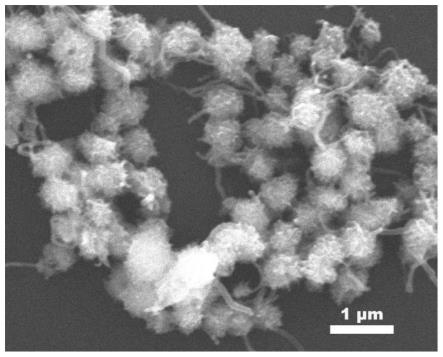
一种葫芦串状cuo/cnt复合催化剂及其制备方法
技术领域
1.本发明涉及一种基于cuo对cnt改性的复合催化材料,还涉及上述复合催化材料的制备方法。
背景技术:2.高级氧化技术(advanced oxidation processes,aops)因其去除速率快、污染小,已成为化学氧化水处理技术中有效去除低浓度有机污染物的重要手段之一。该方法通过产生的活性氧物种,包括:硫酸根自由基(so4·-)、羟基自由基(
·
oh)、单线态氧(1o2)等,可将有机污染物分解为低毒或无毒的中间产物、或直接矿化为co2和h2o。传统的芬顿法(fenton)是以产生羟基自由基(
·
oh)为活性介质用于有机污染物的氧化降解。由于
·
oh的生命周期短(《1微秒),ph应用范围窄(3-5)的特点,使其在中性、碱性环境中降解效率低,降解效果差。近年来,以硫酸根自由基(so4·-)为活化剂的类fenton反应引起国内外研究人员的广泛关注。so4·-具有相比
·
oh更强的氧化电位,长的生命周期(30-40微秒),ph适用范围广(4~10),具有更好的反应选择性。因此,开发简单高效的非均相催化材料使之最大限度地提高过硫酸盐(pms)的活化效率具有重要意义。作为一种p型半导体,cuo具有生物相容性、无毒性与价廉等的特点,在非均相催化中显示出高的电子转移能力、多活性位点暴露等特征。相关的研究表明具有海绵状的多孔氧化铜(sp-cuo)能作为氧化酸橙7的高效活化剂(applied surface science,2020,521:146479.)。然而,由于单一cuo的低电导率和电子转换率等固有特性,进一步提高cuo的本征催化活性仍不理想。
3.碳纳米材料具有超高的导电性和纳米尺寸效应,将其作为基底材料能制备出具有良好性能的铜基催化剂。有研究发现相较于纯的cuo,复合结构的cuo@c降解性能增加了85%以上。然而现有以cnt作为基底的铜基复合催化剂制备相对复杂,合成周期长,容易出现结块或变形。
技术实现要素:4.发明目的:本发明目的旨在提供一种具有高催化活性的葫芦串状cuo/cnt复合催化剂,本发明另一目的是提供上述复合催化剂的制备方法。
5.技术方案:本发明所述的葫芦串状cuo/cnt复合催化剂,由cnt以及生长在cnt上的cuo颗粒组成,多个生长在cnt上的cuo颗粒由cnt串接形成葫芦串状。
6.上述葫芦串状cuo/cnt复合催化剂的制备方法,包括如下步骤:
7.(1)对cnt进行活化处理,活化处理后分散于去离子水中,得到富有含氧基团的cnt分散液;
8.(2)将氯化亚铜溶于乙醇的水溶液中,得到溶液a,将聚环氧乙烷-聚环氧丙烷-聚环氧乙烷三嵌段共聚物(p123)溶于乙醇中,得到溶液b,在室温下混合溶液a和溶液b,得到混合液;
9.(3)向步骤(2)的混合液中加入步骤(1)的cnt浊液均匀分散后,加入一定量的氨
水,观察到迅速有蓝色的cu(oh)2生成,将混合溶液装入单模微波反应器中,反应器设定的温度为125~135℃(相比于其它高温高压反应容器,单模微波反应器多了微波的功能,微波会加快合成反应,这个合成反应只需要5~10min就能得到产物,同时还能降低得到氧化物的温度(高温煅烧得到氧化铜的温度为300℃左右);
10.(4)充分反应后,将所得沉淀经离心洗涤、干燥,得到葫芦串状cuo/cnt复合催化剂。
11.其中,步骤(1)中,cnt的活化过程为:将cnt置于浓硝酸与浓硫酸的混合溶液中,回流加热,将所得溶液用纤维素膜过滤器过滤,清洗至洗出液ph为6~7,离心并干燥,得到活化的cnt粉末。对cnt活化处理的目的是为了提高cnt上的含氧官能团,使cu(oh)2附着沉积在cnt上,通过静电效应将cu(oh)2纳米团簇(混合溶液让表面活性剂定向排列得到cu(oh)2纳米团簇)固定于cnt表面。
12.其中,所述浓硝酸与浓硫酸的混合体积比为1:3,加热温度为100~115℃,纤维素过滤器孔径为0.2~0.3μm。
13.其中,步骤(1)中,cnt分散液中,cnt的质量分数为50%。
14.其中,步骤(2)中,溶液a中,氯化亚铜的浓度为18~22mol/l;溶液b中,p123的质量浓度为8~12g/l;溶液a和溶液b的混合体积比为1:2。
15.其中,步骤(3)中,搅拌速度为600~1000rpm;在微波反应器中反应时长为5~10分钟。
16.有益效果:在cuo/cnt复合催化剂中,虽然cuo为催化pms的活性位点,但单一cuo电导率不足,不利于催化剂的电子传递;通过耦合cnt,形成葫芦串状微观结构,不仅增加了复合催化剂的导电性,且cnt提供了电子转移的通道,促进了cuo之间的电子转移;将本发明的葫芦串状cuo/cnt复合催化剂应用于含四环素(tc)废水的深度处理时,相比于纯cuo微球或cnt,cuo/cnt使氧化反应的反应速率分别提高了1.9和6.5倍,并且在浓度为10ppm的tc,pms浓度为0.2g/l,温度为298k,催化剂投加量为0.2g/l的条件下,在10分钟内催化降解效率可达到100%;本发明复合催化剂的制备方法工艺简单,能够制得相互耦合的葫芦串状的cuo/cnt复合催化剂,cuo与cnt之间的相互协同进一步实现过硫酸盐的高效活化。
附图说明
17.图1为实施例1制得的葫芦串状cuo/cnt的扫描电镜图;
18.图2为实施例1制得的葫芦串状cuo/cnt的透射电镜图;
19.图3为不同氯化亚铜投量的葫芦串状cuo/cnt对tc的降解图;
20.图4为cuo、cnt与cuo/cnt降解tc的效果对比图;
21.图5为葫芦串状cuo/cnt在不同温度下的tc降解效率图;
22.图6为葫芦串状cuo/cnt在不同tc浓度下的降解效率图;
23.图7为在不同cuo/cnt的用量对tc的降解效率图。
具体实施方式
24.实施例1
25.本发明葫芦串状cuo/cnt复合催化剂的制备方法,具体包括如下步骤:
26.(1)取0.5g cnt置于60ml浓硝酸与浓硫酸的混合溶液(1:3,v/v)中,在120℃下加热3个小时,将所得溶液用纤维素膜过滤器(孔径0.25μm)过滤,清洗至洗出液ph为6~7,然后离心并干燥,得到活化的cnt粉末,将所得粉末分散在1ml去离子水中;cnt分散液中,cnt的质量分数为50%;
27.(2)将0.2mol氯化亚铜溶于10ml乙醇的水溶液中,得到溶液a;将0.05g的表面活性剂p123溶于5ml乙醇中,得到溶液b;在室温下按体积比为1:2混合溶液a和溶液b,得到混合液;
28.(3)往步骤(2)混合液中加入0.45ml氨水(质量分数25%~28%),观察到生成蓝色的cu(oh)2;随后在不断搅拌下,往其中加入1ml步骤(1)的分散的cnt浊液(50wt%),将混合溶液倒入密封的反应瓶(30ml),并转移到单模微波反应器中;本发明使用的单模微波反应器型号为单模微波反应器(monowave 300);
29.(4)调节微波反应器温度为130℃,搅拌速度为1000rpm,微波功率设定为反应器自行设定,设定反应时间为5分钟,cnt上的cu(oh)2团簇转化至cuo微球,将所得棕色粉末用乙醇洗涤四次,然后离心并于60℃下干燥12h,得葫芦串状的cuo/cnt复合催化剂粉末。
30.对比例1
31.对比例1与实施例1制备方法基本相同,唯一不同是氯化亚铜投加量改成0.1mol。
32.对比例2
33.对比例2与实施例1制备方法基本相同,唯一不同是氯化亚铜投加量改成0.4mol。
34.根据图1~2所示,实施例1合成的cuo/cnt复合催化剂中cuo微球形貌均一,粒径约为350nm,cuo/cnt复合催化剂具有独特的葫芦串状结构,各cuo微球由cnts相互连接,使cuo转移的电子能在cnt中高效传递,同时,介孔介孔的cuo实现了多活性位点暴露,从而促使有机污染物tc的高效降解。
35.氯化亚铜投加量的改变,对产物的催化性能造成影响。分别将对0.1、0.2和0.4mol的氯化亚铜制得的产物进行催化性能的对比,如图3所示,在相同时间内,0.2mol的氯化亚铜制得cuo/cnt催化剂的活化效率最优,因此,适量比例的cu于cnt复合对催化性能造成影响,0.2mol的氯化亚铜投加量为最佳。
36.选取tc作为目标有机污染物,分别对比cuo、cnts和cuo/cnt复合催化剂活化pms降解tc的性能。如图4所示,在相同时间内,cuo/cnt复合催化剂活化的效率要优于其他催化剂。在10min时tc的去除效率分别为73%、77%和92%。相比之下,cuo/cnt复合催化剂的催化活性要优于cuo和cnt。说明cuo/cnt复合催化剂的催化性能良好。
37.研究不同降解条件对tc降解效率的影响,实验条件为:tc浓度为10ppm,pms浓度为0.2g/l,温度为298k,cuo/cnt复合催化剂投加量为0.2g/l。首先探究温度对cuo/cnt复合催化剂降解效率的影响,如图5所示。在293k、298k和308k三个不同的温度下,tc完全去除的时间分别是30、15和10min,说明温度的升高可以提高cuo/cnt复合催化剂的催化性能。同样,tc和cuo/cnt复合催化剂的浓度也对降解效率有一定的影响。如图6所示,当tc浓度是5、10和20ppm时,降解效率随着tc浓度的增加而递减,tc完全去除的时间分别为6、15和20min,说明tc浓度越高,越难降解。cuo/cnt复合催化剂的浓度对降解效率的影响如图7所示。当cuo/cnt复合催化剂浓度从0.1、0.2到0.35g/l变化时,tc降解了90%所花费时间分别为30、8和6min,表明cuo/cnt复合催化剂浓度的增加可以显著提高对tc的降解效率。