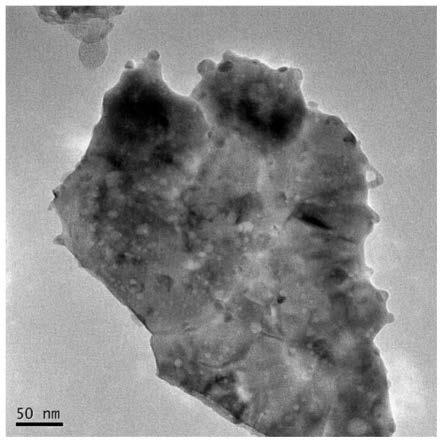
1.本发明涉及高分子材料技术领域,具体涉及一种钙钛矿基甲酸制氢催化剂及其制备方法与应用。
背景技术:2.氢气作为高效清洁可再生能源,是传统化石燃料的理想替代能源。但是氢气的应用面临三大难题:制氢、储氢、广泛经济的应用形式。传统氢气运输采用约20兆帕的高压储氢长管拖车,其氢气装卸过程繁琐:包含加压、装载、运输、卸压等多步过程(单次充/放一车氢气所耗时间约4-5小时),成本十分高昂(运输成本:9-10元/kg氢气/100公里),且储力十分低下(以30吨载重量的长管拖车为例,仅能携带300kg氢气),便捷性差。与传统的压缩储氢及液态储氢法不同,目前以化学物质为氢气载体,在温和条件下完成对氢气的储存与运输,并在需要用氢时将其高效催化分解放出,做到即需即产、即产即用,已成为当下氢能利用发展的主流热点。电解水制氢技术成本高(》100元/kg h2)、本身能耗十分高昂。而甲醇重整制氢一般需要250℃以上的高温及30-50个大气压的高压,该高温高压条件不利于设备的隐藏与反侦察;此外,甲醇制氢纯度较差,含有很高浓度的co(》1%),需对产物进行深度提纯,否则极易使燃料电池中毒,这造成了成本的提升。
3.相比之下,甲酸(hcooh,fa)是最简单的含氢一元有机羧酸, 具有较高的体积储氢量(53 g/l), 在合适的催化剂作用下, 温和条件即可分解释放h2。此外,甲酸毒性较低、常温常压为液态、性质稳定、不易燃烧、运输和储存安全方便, 是一种极具潜力的化学储氢材料。
4.甲酸制氢催化剂主要分为两类,均相液体催化剂和多相固体催化剂。均相催化剂虽然性能较好,但存在回收、分离较为困难等问题。相比之下,多相催化剂因其容易制备、稳定性好,对空气水汽不敏感,容易分离回收等优势受到了广泛关注。中科院长春应用化学研究所邢巍小组发现pd-au/c-ceo2催化剂在92℃的甲酸分解转化频率(tof)为227 h-1
, 且催化剂选择性高,并未检测到co生成(chemistry of materials 2010, 22 (18), 5122-5128.)。中科大傅尧课题组制备了s修饰的pd/sio2催化剂,在85℃时对4m (hcooh-hcoona,9:1)体系的tof为719 h-1
(energy fuels 2011, 25 (8), 3693-3697.)。吉林大学蒋青小组釆用无表面活性剂的溶液共还原的方法制备coaupd/c催化剂,在室温下可催化甲酸分解脱氢,tof转化率为80h-1
(angewandte chemie 2013,125 (16), 4502-4505.)。cn110233271 a公开了一种层状氮化碳基甲酸制氢催化剂及其制备方法,取得了较好的甲酸分解制氢性能。但在上述方法中,大多采用浸渍法将具有甲酸分解制氢活性的pd物种分散于载体之上,但浸渍法步骤复杂,且难以对催化活性物种的形貌尺寸进行控制,金属跟载体的作用力弱,因此导致其活性、稳定性和工艺可操作性仍有待改进。
技术实现要素:5.本发明的主要目的在于提供一种钙钛矿基甲酸制氢催化剂及其制备方法与应用,
从而克服现有技术中的不足。
6.在本发明的实施例中术语钙钛矿是指一类具有通式abo3的特定晶体结构的化合物,其中“a”和“b”是两种尺寸悬殊的阳离子,以及“o”是键合到上述两者上的氧离子。可以使用的阳离子范围很大,“a”位点是具有较大离子半径的金属元素,如稀土或碱土金属元素,a位点与十二个氧配位,主要起稳定钙钛矿结构的作用;“b”位点是具有较小离子半径的金属元素,例如过渡金属元素mn、co、fe、cr、ti、ni和mg等,与六个氧配位,占据八面体中心。abo3钙钛矿型氧化物具有独特的氧化还原催化活性。abo3中a位元素:b位元素:氧离子的比例为1:1:3。
7.本领域技术人员可知,在钙钛矿结构中可实现引入a或b离子取代a或b位点上的金属元素,形成a
1-yayb1-xbx
o3晶体结构的化合物,其中x与y表示原子数量比例,0≤x≤1,0≤y≤1。例如假设b位元素的总和量是1,当x=0.1,y=0时,通式为ab
0.9b0.1
o3,表示b代表的元素占据了b位点的10%(0.1),那么未被占据的b位元素就为90%(0.9)。a取代a位点元素亦是如此。
8.本发明的目的在于提供一种钙钛矿基甲酸制氢催化剂的制备方法,将催化剂采用溶胶凝胶法一步合成后经高温煅烧,预先合成晶格中包含活性组分的钙钛矿晶体,再通过活化处理活性组分从晶格中迁移至催化剂表面,形成活性组分纳米颗粒负载于钙钛矿基体的结构。据相关文献报道,金属在甲酸分解过程中的催化活性顺序为pb>pt≈ru>au>ag,钯(pd)是过渡金属中催化液相甲酸性能最佳的单金属催化剂。具体包括以下步骤:步骤1,按照所需的化学计量比例将含有a元素、b元素、b元素的金属盐完全溶解于水中,得到混合的金属盐溶液。
9.步骤2,在步骤1得到的金属盐溶液中加入柠檬酸,待柠檬酸完全溶解后,将其在恒温下搅拌,直到形成凝胶。
10.步骤3,将步骤2的凝胶干燥、研磨、煅烧,自然冷却后得到晶体粉末。
11.步骤4,将步骤3中的晶体粉末在惰性气体中进行活化处理,待自然冷却至室温后得到表面弥散分布活性组分的钙钛矿基甲酸制氢催化剂。所述惰性气体包括氮气或氦气或两者的混合气体。
12.进一步,步骤1中所述a元素是镧系金属元素镧(la)或铈(ce),或碱土金属元素钙(ca)、锶(sr)、钡(ba)其中一种或多种;b元素是过渡金属元素铁(fe)、钴(co)、镍(ni)、锰(mn)其中一种或多种;b元素是贵金属钯(pd)、钌(ru)、铂(pt) 其中一种或多种。
13.进一步,步骤2中金属盐溶液金属离子总量与柠檬酸的摩尔比为1:2。优选的搅拌温度为60~80℃。
14.进一步,步骤3的干燥温度设为100℃~140℃。
15.进一步,步骤3中煅烧在800~900℃下进行2~10h。其中煅烧温度的升温速率为1~10℃
·
min-1
,优选的煅烧温度为850℃下煅烧2h,优选的升温速率为2℃
·
min-1
。
16.进一步,步骤4活化处理包括以下步骤:将步骤3得到的催化剂粉末置于陶瓷坩埚中,并置于n2气氛中,以一定的升温速率从室温加热至200℃进行预处理。预处理一段时间后,继续升温至750℃~900℃焙烧60~180min。炉体断电待自然冷却至室温后取出粉末晶体即得到催化剂。预处理可以去除样品表面杂质。
17.进一步,当活性组分是钯时,b位元素为铁时,钯含量相对于b位铁元素总量的0.5~
5mol%,钯含量过低导致催化剂催化性能较差,因为活性位数量不足。而过高容易造成材料本身结构的破坏。
18.本发明所制备的钙钛矿基甲酸制氢催化剂可应用于甲酸分解制氢中。
19.本发明与现有技术相比,具有如下有益效果:本发明提出一种新型的甲酸制氢催化剂体系,和新型的甲酸制氢催化剂制备方法,实现pd活性组分在催化剂载体之上的高度分散,解决此前催化剂体系分散度差,不可控的问题。
20.本发明操作流程简单,原料丰富,制备的复合型催化剂有很好制氢效果,有望实现催化剂在低温制氢领域的实际应用。
21.本发明采用一步法制备负载型催化剂,代替原来的浸渍法,简化了工艺流程,节约了生产时间和成本,适用于大规模工业生产。
22.本催化剂在测试过程中,未见co毒化。通过该法合成的催化剂,pd与载体的作用力较强,导致co吸附于pd表面的困难,因此抗co毒化能力提高。
附图说明
23.图1是实施例1制备的钙钛矿基甲酸制氢催化剂的微观形貌图;图2是实施例2所制试样的xrd图。
具体实施方式
24.下面结合具体实施例,对本发明的技术方案进行详细描述。所列举的实施例仅是本发明部分实施例,不是全部的实施例。本发明实施例中所用原料和试剂均市售可得。
25.本发明的目的针对现有技术存在的问题提出了一种钙钛矿基甲酸制氢催化剂及制备方法。该催化剂由含有贵金属的活性组分和具有钙钛矿结构的金属氧化物复合而成,利用一步合成法将具有催化活性的元素掺杂入钙钛矿的体相之中,再经过高温焙烧,预先合成晶格中包含活性组分的钙钛矿晶体,再通过活化处理活性组分从晶格中迁移至催化剂表面,形成活性组分纳米颗粒负载于钙钛矿基体的结构,最终制备出钯负载钙钛矿氧化物的甲酸制氢催化剂。具体包括以下步骤:步骤1,按照所需的化学计量比例将含有a元素、b元素、b元素的金属盐完全溶解于水中,得到混合的金属盐溶液。
26.步骤2,在步骤1得到的金属盐溶液中加入柠檬酸,待柠檬酸完全溶解后,将其在恒温下搅拌,直到形成蜂窝状凝胶。
27.步骤3,将步骤2的凝胶干燥、研磨、煅烧,自然冷却后得到晶体粉末。
28.步骤4,将步骤3中的晶体粉末进行活化处理,即在惰性气氛中升温还原。待自然冷却至室温后得到表面弥散分布活性组分的钙钛矿基甲酸制氢催化剂。
29.进一步,步骤1中所述a元素是镧系金属元素镧(la)或铈(ce),或碱土金属元素钙(ca)、锶(sr)、钡(ba)其中一种或多种;b元素是过渡金属元素铁(fe)、钴(co)、镍(ni)、锰(mn)其中一种或多种;b元素是贵金属钯(pd)、钌(ru)、铂(pt) 其中一种或多种。
30.进一步,步骤2中金属盐溶液金属离子总量与柠檬酸的摩尔比为1:2。搅拌温度为60~80℃。
31.进一步,步骤3的干燥温度设为100℃~140℃,干燥12小时。
32.进一步,步骤3中煅烧在800~900℃下进行2~10h。其中煅烧温度的升温速率为1~10℃
·
min-1
,优选的煅烧温度为850℃下煅烧2h,优选的升温速率为2℃
·
min-1
。
33.进一步,步骤4活化处理包括一下步骤:将步骤3得到的催化剂粉末置于陶瓷坩埚中,并置于n2气氛中,以一定的升温速率从室温加热至200℃进行预处理。预处理一段时间后,继续升温至750~900℃焙烧60~180min。炉体断电待自然冷却至室温后取出粉末晶体即得到催化剂。
34.本发明采用在惰性气氛n2中进行活化处理,并非还原性气氛,是为了制造一个氧分压适中的气氛(不至于像含有氢气的还原性气氛那么低的氧分压),让钙钛矿氧化物上逐渐生成氧空位,进而诱发pd离子向表面的扩散,最后形成pd纳米颗粒。如果使用了还原性气氛,如h2等,则会造成氧分压过低,从而导致材料结构损坏,催化剂性能很低。
35.进一步,当活性组分是钯时,其含量相对于b位元素总量的0.5~5mol%,钯含量过低导致催化剂催化性能较差,因为活性位数量不足。而过高容易造成材料本身结构的破坏。
36.实施例1,制备pd含量为3 mol%的催化剂,以a位点为la元素、b位点为fe元素为例进行说明,采用溶胶凝胶法,钯取代lafeo3晶格中所述fe元素的一部分,制备成lafe
0.97
pd
0.03
o3。
37.步骤(1),称取la(no3)3·
6h2o (macklin,》99%)、fe(no3)3·
9h2o(energy chemical,99%)和(nh3)4pd(no3)2(energy chemical, 99%)完全溶解到去离子水中,配制成0.05mol
·
l-1
的金属盐溶液(下文称溶液i),该溶液中金属离子的摩尔比为la:fe:pd=1:0.97:0.03。
38.步骤(2),在步骤(1)得到的溶液i中加入粉末柠檬酸,搅拌将其完全溶解于溶液i中,得到了溶液ii,该溶液ii中金属离子总量与柠檬酸的摩尔比为1:2。金属离子总量是指镧离子、铁离子、钯粒子的总量。
39.步骤(3),将步骤(2)得到的溶液ii置于恒温80℃下搅拌,直到形成蜂窝状凝胶。
40.步骤(4),将步骤(3)得到的凝胶置于烘箱中干燥一夜,直至完全干燥。烘箱温度设为100℃。
41.步骤(5),将步骤(4)中所得材料用研钵进行精细研磨,粗细约80目,随后将其置于空气中在850℃下煅烧4h形成结晶,自然冷却后,得到棕色粉末。
42.步骤(6),将步骤(5)中制备得到的催化剂在氮气中升温还原,具体过程如下:将催化剂粉末置于陶瓷坩埚中,并置于n2(流速为50 ml
·
min-1
)的气氛中,以5℃
·
min-1
的升温速率从室温加热至200℃。预处理30分钟后,再以3℃
·
min-1
的速率将催化剂加热至850℃进行焙烧。60min后炉体断电待自然冷却至室温后取出粉末晶体即得到催化剂。
43.依照上述步骤所制备的催化剂lafe
0.97
pd
0.03
o3负载有活性组分钯,且钯分散于催化剂载体表面,见图1。图1是本实施例制备的钙钛矿基甲酸制氢催化剂的微观形貌图。可以看到,催化剂表面有大量的纳米pd金属颗粒存在。采用co化学吸附法测得pd单金属的分散度为30.02%,高于浸渍法所制备的催化剂22.16%。
44.另一方面,活性组分的构造(粒径大小、形状、分散度、结晶结构、表面组分等)与催化作用密切相关,而影响活化组分构造的因素有:催化剂载体的结构、干燥方法、焙烧方式、活化温度气流等。本实施例得到催化剂表面钯的平均粒径大小为2~3nm,而通过浸渍法得到
的pd纳米颗粒平均粒径大小为5~15nm[参考applied catalysis b: environmental 273 (2020) 119071]。本发明活性组分钯的颗粒尺寸明显减小。通过stem-edx观测催化剂表面形貌,所有的元素如la, fe, o都均匀分布,未见fe金属颗粒或其他金属的团聚生成颗粒。
[0045]
实施例2按照实施例1的方法步骤,区别在于步骤(6)改变活化处理的温度。如果步骤(6)预处理之后的焙烧温度过高超过900℃,可能会造成材料晶体结构的崩坏,或者pd的纳米颗粒的尺寸增加,使得材料的催化性能下降。而温度过低,难以使pd在材料表面生成pd纳米颗粒。如预处理之后保持200℃不升温,从图2样品的xrd图上未见金属pd的衍射峰。
[0046]
实施例3,传统浸渍法对比例步骤(1),通过采用溶胶凝胶法制备了不含有pd的钙钛矿催化剂lafeo3。首先将摩尔比la:fe=1:1的la(no3)3·
6h2o (麦克林,》99%)、和fe(no3)3·
9h2o (安耐吉,99%)完全溶解到一定量的去离子水中,溶解得到0.05 mol
·
l-1
的金属盐溶液。
[0047]
步骤(2),在步骤(1)得到的金属盐溶液中加入柠檬酸,金属离子总量与柠檬酸的摩尔比为1:2,待柠檬并完全溶解后,将溶液置于恒温80℃下搅拌,直到形成蜂窝状凝胶。
[0048]
步骤(3),将步骤(2)得到的凝胶置于100℃的烘箱中干燥过夜。将所得材料研磨后,置于空气中在800℃下煅烧4h,升温速率为5℃
·
min-1
。自然冷却后,所得的棕色粉末。
[0049]
步骤(4),取一定量的(nh3)4pd(no3)2(安耐吉,99%)溶解到0.5ml去离子水中,待充分溶解后,缓慢滴加到棕色粉末上,使得la:fe:pd的原子比为100:97:3。边滴加边研磨,待充分研磨30min后,置于干燥箱烘干过夜,随后置于马弗炉于800℃下煅烧2h,升温速率为5℃
·
min-1
。自然冷却后,将催化剂粉末置于陶瓷坩埚中,并置于5%h2/n2气氛中,以5℃
·
min-1
的升温速率从室温加热至300℃并维持2h。待自然冷却至室温后取出备用。
[0050]
甲酸制氢催化性能测试:将按照实施例1所述步骤制备好的钙钛矿基甲酸制氢催化剂称取50 mg,分散于10 ml去离子水中。随后加入20 ml含有甲酸和甲酸钠的混合水溶液中。其中,甲酸和甲酸钠的摩尔比例为1:4。反应温度为50℃。通过排水量气法测得甲酸分解制氢所获得的气体体积,最终得制氢活性tof为621 h-1
。其在50-90℃间的反应活化能为50.1 kj/mol。
[0051] 浸渍法合成的对比例采用如上相同的步骤进行性能评价,得制氢活性tof为227 h-1
。其在50-90℃间的反应活化能为88.1 kj/mol。
[0052]
上面结合实施例对本发明作了详细说明,但是本发明不限于上述实施例,在所属技术领域普通技术人员所具备的知识范围内,还可以在不脱离本发明宗旨的前提下作出各种变化。