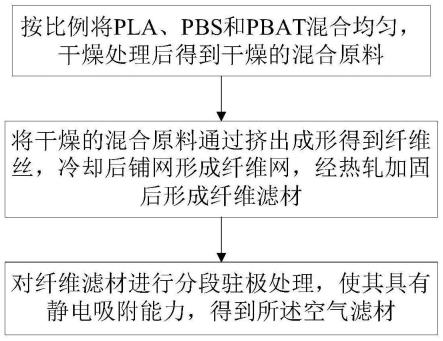
1.本发明属于过滤及分离技术领域,更具体地,涉及一种可生物降解的空气滤材及其制备方法。
背景技术:2.随着我国经济飞速发展,无论在工业领域还是民用领域,空气滤芯作为一次性消耗品的用量越来越大。据保守统计,我国每年空气滤芯消耗量超数十亿支。如此巨大的滤芯消耗量随之带来的棘手问题就是废弃滤芯的处理。由于空气滤芯组成部分多为不可降解材料,如pp、pet、pe塑料,玻璃纤维和热固性树脂等,且由于使用后的滤芯上附着了各类污染物杂质,因此难以对pp、pet、pe、玻璃纤维等进行单独回收再利用。以往常见的处理方式是破碎后焚烧或填埋,这两种方式都会对环境产生危害,焚烧会增加二氧化碳、二氧化硫、氮氧化物以及烟尘等污染物的排放,填埋则会增加土壤污染负荷,pp、pet、pe等的降解周期是数百年,玻璃降解周期更是达数百万年。
3.随着建立健全绿色低碳循环发展经济体系战略的提出,以及确保2030年实现碳达峰目标,多个省份相继提出禁止生产、销售、使用不可降解塑料制品。大力推广应用可生物降解材料。
4.如何提供一种可生物降解的空气滤材及其制备方法,使其具有高效率、低阻力、良好耐温性和强度,是本领域亟待解决的问题。
技术实现要素:5.针对现有技术的缺陷,本发明提供了一种可生物降解的空气滤材及其制备方法,通过采用三种可生物降解原材料pla、pbs和pbat,制成纤维后配合特定的分段驻极处理步骤,解决现有技术缺乏综合性能优异的可生物降解空气滤材等的技术问题。
6.为实现上述目的,本发明提供了一种可生物降解的空气滤材的制备方法,包括如下步骤:
7.(1)按比例将pla、pbs和pbat混合均匀,干燥处理后得到干燥的混合原料;所述pla、pbs和pbat的质量比为(40-60):(20-30):(20-30);
8.(2)将步骤(1)所述干燥的混合原料通过挤出成形得到纤维丝,冷却后铺网形成纤维网,经热轧加固后形成纤维滤材;
9.(3)对步骤(2)所述纤维滤材进行分段驻极处理,使其具有静电吸附能力,得到所述空气滤材。
10.优选地,所述pla的熔点为170-180℃,熔融指数为60-100g/10min,分子量为4
×
10
4-6
×
104,密度为1.20-1.25g/cm3。
11.优选地,所述pbs的熔点为110-116℃,熔融指数为15-30g/10min,分子量为6
×
10
4-8
×
104,密度为1.25-1.3g/cm3。
12.优选地,所述pbat的熔点为120-130℃,熔融指数为10-15g/min,分子量为1.8
×
10
5-2
×
105,密度为1.18-1.3g/cm3。
13.优选地,步骤(1)所述干燥处理在真空干燥箱中进行,干燥温度为80-90℃,时间为8-12h。
14.优选地,步骤(2)所述挤出成形,其熔体温度为200-220℃,热风温度为240-260℃。
15.优选地,步骤(2)通过挤出成形得到直径为2μm-5μm的纤维丝。
16.优选地,步骤(3)所述分段驻极处理具体为:
17.(i)第一阶段驻极电压为10kv-12kv,驻极时间5s-10s,驻极距离为35-45mm;
18.(ii)第二阶段驻极电压为13kv-15kv,驻极时间2s-4s,驻极距离为45-55mm。
19.按照本发明的另一个方面,提供了一种可生物降解的空气滤材,按照质量份计,其包括40-60份的pla,20-30份的pbs和20-30份的pbat;其为将pla、pbs和pbat按比例共混后制成纤维,然后经过分段驻极处理得到所述空气滤材。
20.优选地,所述分段驻极处理具体为:
21.(i)第一阶段驻极电压为10kv-12kv,驻极时间5s-10s,驻极距离为35-45mm;
22.(ii)第二阶段驻极电压为13kv-15kv,驻极时间2s-4s,驻极距离为45-55mm。
23.总体而言,通过本发明所构思的以上技术方案与现有技术相比,具有以下有益效果:
24.(1)本发明将pla、pbs和pbat按比例共混后制成纤维,然后经过分段驻极处理得到所述空气滤材。本发明提供的空气滤材包含pla、pbs和pbat三种可生物降解原材料,相比单一可生物降解原材料制成的滤材,不仅耐热性能好,且具有良好的力学性能和机械性能,在滤材打褶过程中,纤维不易断裂,在实际过滤过程中,可以耐受较高风压。
25.(2)本发明的空气滤材包含多种不同的可生物降解原材料,实验发现制备过程中传统的一步驻极处理不能达到较好的过滤效果,采用分段驻极处理,才使得初次过滤效率达到99.95%,相对于一步驻极处理过滤效率提高了15%以上。本发明可生物降解的空气滤材具备高效率、低阻力、高耐温性和高强度的综合优良特性。
附图说明
26.图1为本发明可生物降解的空气滤材制备流程示意图。
27.图2为本发明一些实施例中制备空气滤材的装置示意图。
具体实施方式
28.为了使本发明的目的、技术方案及优点更加清楚明白,以下结合附图及实施例,对本发明进行进一步详细说明。应当理解,此处所描述的具体实施例仅仅用以解释本发明,并不用于限定本发明。
29.常见的可生物降解材料有pla、pbs、pbat、pga、pcl、pha等等,但每种材料都有各自优缺点,例如pbs韧性较好,易于加工,但机械性能较差;pla硬度和强度较好,但脆性大;pbat具有较好的抗冲击性,但强度性能差。对于高效空气滤材,不仅要求效率高、阻力低,还要求具有良好耐温性和强度。目前未见同时能够满足以上性能要求的可生物降解空气滤材。
30.为此,本发明提供了一种可生物降解的空气滤材的制备方法,包括如下步骤:
31.(1)按比例将pla、pbs和pbat混合均匀,干燥处理后得到干燥的混合原料;所述pla、pbs和pbat的质量比为(40-60):(20-30):(20-30);
32.(2)将步骤(1)所述干燥的混合原料通过挤出成形得到纤维丝,冷却后铺网形成纤维网,经热轧加固后形成纤维滤材;
33.(3)对步骤(2)所述纤维滤材进行分段驻极处理,使其具有静电吸附能力,得到所述空气滤材。
34.一些实施例中,所述pla的熔点为170-180℃,熔融指数为60-100g/10min,分子量为4
×
10
4-6
×
104,密度为1.20-1.25g/cm3。所述pbs的熔点为110-116℃,熔融指数为15-30g/10min,分子量为6
×
10
4-8
×
104,密度为1.25-1.3g/cm3。所述pbat的熔点为120-130℃,熔融指数为10-15g/min,分子量为1.8
×
10
5-2
×
105,密度为1.18-1.3g/cm3。在这些参数范围内,更有利于共混熔融,纺出的丝均匀性更好。
35.一些实施例中,步骤(1)所述干燥处理在真空干燥箱中进行,干燥温度为80-90℃,时间为8-12h。
36.一些实施例中,步骤(2)将干燥的混合原料送入螺杆挤出机中挤出成形,其熔体温度为200-220℃,热风温度为240-260℃。熔体从喷丝模头孔中挤出形成2μm-5μm直径的长丝,利用空气冷却后在铺网机上形成纤维网,纤维网经过热轧机加固后形成纤维滤材。通过调控热轧温度及压力,可以在一定范围内调节滤材孔隙及厚度,热轧温度越高,热轧压力越大,孔隙和厚度越小,反之越大。
37.一些实施例中,步骤(3)所述分段驻极处理具体为:
38.(i)第一阶段驻极电压为10kv-12kv,驻极时间5s-10s,驻极距离为35-45mm;
39.(ii)第二阶段驻极电压为13kv-15kv,驻极时间2s-4s,驻极距离为45-55mm。
40.本发明提供的一种可生物降解的空气滤材,按照质量份计,其包括40-60份的pla(聚乳酸),20-30份的pbs(聚丁二酸丁二醇酯)和20-30份的pbat(聚对苯二甲酸-己二酸丁二醇酯);其为将pla、pbs和pbat按比例共混后制成纤维,然后经过上述分段驻极处理方式得到所述空气滤材。
41.pla、pbs和pbat本身微观结构差异很大,这几种可生物降解材料本身是否具有可驻极性未知,本发明实验过程中首先采用传统的一步驻极方式进行驻极处理,无论怎样调节驻极电压和驻极时间以及驻极距离参数,都未能获得理想的驻极效果,制备得到的滤材过滤效率较低。偶然地,本发明通过对由pla、pbs和pbat混合制成的纤维网进行分段驻极处理,配合特定的驻极工艺参数,制备得到的空气滤材具有高达99.95%的初次过滤效率,且相对于单一软化点较低的材料,如pbs,多种材料共混后,由于加入了软化点较高的成分,如pla,因此,整体材料软化点提高。同样,相对于单一强度较低的材料,如pbat,多种材料共混后,由于加入了强度性能好的材料,如pla,因此,整体材料耐破度提高。
42.本发明提供的一种空气滤材可用于电厂、冶金、石化、工程机械等行业的空气净化及室内空调等的滤膜芯材中。
43.以下为实施例:
44.实施例1
45.本实施例的可生物降解的空气滤材包括pla、pbs和pbat三种可生物降解原材料。本实施例中,pla质量占比55%;pbs占比20%;pbat占比25%。本实施例中,pla熔点为175
℃,熔融指数为75g/10min,分子量为4.8
×
104,密度为1.25g/cm3。pbs熔点为115℃,熔融指数为20g/10min,分子量为6.5
×
104,密度为1.26g/cm3。pbat熔点为125℃,熔融指数为15g/min,分子量为1.8
×
105,密度为1.25g/cm3。
46.如图1所示,本实施例还提供了上述可生物降解空气滤材的制备方法,具体包括以下步骤:
47.(1)按上述比例将pla、pbs和pbat三种可生物降解原材料混合均匀,并在真空干燥箱中进行干燥,干燥温度为90℃,时间为10h。
48.(2)将干燥后的原料颗粒从图2中料斗1进入螺杆挤出机2中,熔体温度为210℃,热风温度为245℃;
49.(3)熔体从喷丝模头3孔中挤出形成2.5μm直径的长丝,利用空气冷却后在铺网机4上形成定量为60
±
5g/m2的纤维网,纤维网经过热轧机加固后形成纤维滤材,热轧温度为120℃,热轧压力为1.5bar;
50.(4)纤维滤材经过高压静电装置5驻极整理,第一阶段驻极电压为10kv,驻极时间5s,驻极距离为35mm;第二阶段驻极电压为15kv,驻极时间2s,驻极距离为45mm。
51.实施例2
52.其他条件同实施例1,不同的是步骤(4)中纤维滤材经过高压静电装置驻极整理,第一阶段驻极电压为12kv,驻极时间5s,驻极距离为40mm;第二阶段驻极电压为14kv,驻极时间4s,驻极距离为42mm。
53.对比例1
54.其他条件同实施例1,不同的是,对比例1的空气滤材仅含有pbs一种可生物降解原材料。pbs熔点为115℃,熔融指数为20g/10min。
55.对比例2
56.其他条件同实施例1,不同的是步骤(4)中纤维滤材经过高压静电装置一步驻极整理,驻极电压为20kv,驻极时间5s。
57.对比例3
58.其他条件同实施例1,不同的是步骤(4)中纤维滤材经过高压静电装置一步驻极整理,驻极电压为10kv,驻极时间10s。
59.对比例4
60.其他条件同实施例1,不同的是步骤(4)中纤维滤材经过高压静电装置驻极整理,驻极电压为15kv,驻极时间6s。
61.对实施例1、实施例2、对比例1、对比例2、对比例3和对比例4得到的空气滤材进行测试,测试项目及方法分别为:
62.(1)软化点:按照测试标准:astm e793-2001;
63.(2)耐破度:按照测试标准:gb/t454-2002;
64.(3)初始过滤效率:按照测试标准:en1822-2009。
65.测试结果见表1。
66.表1测试结果
[0067] 软化点耐破度初始过滤效果实施例1120℃300kpa(99.95%,0.3μm)
实施例2120℃300kpa(99.92%,0.3μm)对比例190℃150kpa(74.56%,0.3μm)对比例2120℃300kpa(80.66%,0.3μm)对比例3120℃300kpa(84.32%,0.3μm)对比例4120℃300kpa(82.15%,0.3μm)
[0068]
从表1结果不难看出,对比例1仅采用一种可生物降解材料pbs制备空气滤材,由于单一pbs材料强度低,导致最终制备得到的滤材软化点和耐破度均很低,其耐破度仅为实施例1和实施例2滤材的一半;实施例1将三种可生物降解材料按照一定的比例复配,提高了最终滤材的耐温性,强度和韧性也提高,因此耐坡度也有明显的提高。
[0069]
实施例1与对比例2、对比例3和对比例4相比,采用分段驻极处理较一步驻极处理,无论是高电压下的一步驻极整理,还是低电压下的一步驻极整理,其过滤效率都明显低于实施例1滤材的过滤效率,分段驻极处理相对于一步驻极处理其初始过滤效率提升了15%以上,可能的原因是驻极体材料的电荷存储能力决定于材料中的电荷陷阱密度,而陷阱的产生与材料的微观结构尤其是晶向结构密切相关。本发明实施例1材料是由三种可生物降解材料组成,每种材料晶向结构差距较大,采用传统的一步驻极处理,实验证明不能得到较好的驻极效果;采用分段驻极,可能能够保证各种材料都充分驻极,使过滤材料获得较高的表面电位,在过滤过程中,可以捕捉更小的颗粒,从而使得滤材最终的过滤效率可高达99.95%。
[0070]
本领域的技术人员容易理解,以上所述仅为本发明的较佳实施例而已,并不用以限制本发明,凡在本发明的精神和原则之内所作的任何修改、等同替换和改进等,均应包含在本发明的保护范围之内。