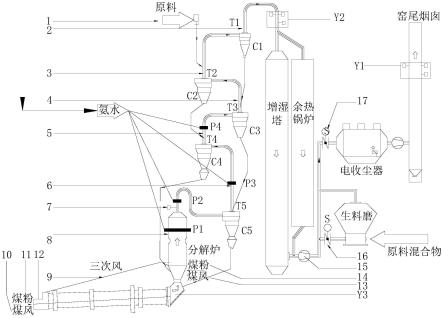
基于预测控制模型的水泥窑烟气isncr控制方法
技术领域
1.本技术涉及环境保护与工业智能化领域,特别是涉及一种基于预测控制模型的水泥窑烟气isncr控制方法。
背景技术:2.基于现行《水泥工业大气污染物排放标准(gb4915-2013)》控制要求,采用基于化学计量比控制的传统sncr脱硝技术,是目前应用最为广泛的技术。在日渐严格的环保标准态势下,需优化控制方法对排放nox浓度进行有效控制。
3.公开号为cn203862137u的中国专利公开了一种水泥熟料生产线sncr烟气脱硝的还原剂计量与控制系统,该方案通过温度修正参数k1、氨逃逸修正参数k2、论脱硝率k3和实际脱硝率的比值系统自动生成(e/f)来进行调整。但是其本质是基于精确测量、辅以改良修正参数进行控制,所选取的核心信号来自c1级预热器出口第一cems和第一氨表,存在选型难、造价高、运维维护费用高,否则数据可信度不高。并且,其初始赋值nox不能随生产实时调控,但水泥熟料生产由于燃原料和生产负荷的调整,会出现偶发性nox浓度远远超出设计范围,历史曲线表明会出现调控失灵现象:当nox排放浓度已经低于设定目标值,计算氨水流量理应小于实际喷氨量,以指导系统减少氨水喷射量,但是会出现计算氨水流量高于实际氨水流量的现象。
4.上述传统sncr脱硝工艺,难以解决在原料和生产负荷进行调整、或生产工况突破边界条件等情况下,脱硝过程中出现的喷氨量调节不足或调节过量问题。
技术实现要素:5.基于此,有必要针对上述技术问题,提供一种基于预测控制模型的水泥窑烟气isncr控制方法。
6.本技术基于预测控制模型的水泥窑烟气isncr控制方法,向待处理的烟气混入氨水进行脱硝处理,采集处理后的烟气参数作为窑尾烟囱烟气数据集,输入到预测控制模型输出氨水分配数据集,用于控制氨水的混入,所述预测控制模型基于神经网络构建预先训练获得,训练过程包括:
7.获得历史数据集,将所述历史数据集划分为因变量数据集和果变量数据集,所述氨水分配数据集属于所述因变量数据集,所述窑尾烟囱烟气数据集属于所述果变量数据集;
8.获得所述因变量数据集和所述果变量数据集的特征相关度,将所述因变量数据集划分为特征相关度超过第一阈值的主因子数据集和相关度小于或等于第一阈值的多元数据集;
9.根据所述主因子数据集和所述多元数据集,获得基于因变量数据集的输入变量矩阵和基于果变量数据集的输出变量矩阵;
10.根据输入变量矩阵和输出变量矩阵训练获得基于神经网络构建的预测控制模型。
11.可选的,所述第一阈值为0.3~0.5。
12.可选的,因变量数据集和果变量数据集的特征相关度利用皮尔逊系数排列获得。
13.可选的,获得基于因变量数据集的输入变量矩阵和基于果变量数据集的输出变量矩阵,具体包括:
14.利用偏最小二乘法结合进行主成分回归分析和多元线性回归分析,获得基于因变量数据集的输入变量矩阵和基于果变量数据集的输出变量矩阵。
15.可选的,还包括获得测试数据集,所述测试数据集和历史数据集的类型相同,在预测控制模型训练完成后,所述测试数据集用于验证所述预测控制模型的训练结果。
16.可选的,所述预测控制模型随使用过程进行自优化,自优化的过程包括:
17.获得实时数据集,将实时数据集划分为因变量数据集和果变量数据集,因变量数据集包括实时的氨水分配数据集,果变量数据集包括实时的氮氧化物浓度实测值;
18.将实时数据集转化为输入变量矩阵和输出变量矩阵,利用滑动窗口法根据实时数据集更新输入变量矩阵和输出变量矩阵,更新所述预测控制模型。
19.可选的,从控制氨水的混入到改变窑尾烟囱烟气数据集存在时滞时间;
20.所述氮氧化物浓度实测值相应滞后于所述氨水分配数据集,所述输出变量矩阵相应滞后于所述输入变量矩阵。
21.可选的,更新预测控制模型的方式包括:获得实时数据集,丢失历史数据集中距当前时刻最远的数据。
22.可选的,所述基于预测控制模型的水泥窑烟气isncr控制方法实施于水泥熟料煅烧系统,所述水泥熟料煅烧系统按照烟气流向依次包括分解炉、五级预热器和窑尾烟囱,氨水通过用于喷射氨水的喷枪混入,喷枪设置于分解炉和五级预热器的相应部分,所述氨水分配数据集用于控制各喷枪。
23.可选的,所述喷枪设置于不同的喷氨点位,所述喷氨点位包括:所述分解炉的中上部、分解炉出口、c5级旋风预热器出口、c4级旋风预热器出口。
24.本技术还提供一种基于预测控制模型的水泥窑烟气isncr控制方法,向待处理的烟气混入氨水进行脱硝处理,采集处理后的烟气参数作为窑尾烟囱烟气数据集,输入到预测控制模型输出氨水分配数据集,用于控制氨水的混入,所述基于预测控制模型的水泥窑烟气isncr控制方法包括:
25.设定氮氧化物浓度目标值,获得t1时刻的氨水分配数据集和t1时刻的氮氧化物浓度实测值,利用所述预测控制模型预测t2时刻的氮氧化物浓度,获得t2时刻的氮氧化物浓度预估值,t2时刻滞后于t1时刻;
26.获得t2时刻的氮氧化物浓度实测值,比较t2时刻的氮氧化物浓度实测值和t2时刻的氮氧化物浓度预估值,获得二者的偏差;
27.利用所述偏差优化所述预测控制模型。
28.可选的,所述基于预测控制模型的水泥窑烟气isncr控制方法还包括:循环进行上述流程,利用所述偏差实时地优化所述预测控制模型。
29.可选的,所述基于预测控制模型的水泥窑烟气isncr控制方法还包括:根据优化后的预测控制模型和氮氧化物浓度目标值调节下一次循环中的氮氧化物浓度预估值。
30.可选的,所述预测控制模型基于神经网络构建预先训练获得,所述基于神经网络
构建的预测控制模型的训练过程包括:
31.获得历史数据集,将历史数据集划分为因变量数据集和果变量数据集,所述因变量数据集包括所述氨水分配数据集,果变量数据集包括所述窑尾烟囱烟气数据集;
32.根据所述因变量数据集和所述果变量数据集,获得基于因变量数据集的输入变量矩阵和基于果变量数据集的输出变量矩阵;
33.根据所述输入变量矩阵和所述输出变量矩阵获得基于神经网络构建的预测控制模型。
34.可选的,所述因变量数据集包括t3时刻的氨水分配数据集,所述果变量数据集包括t4时刻的氮氧化物浓度实测值,t4时刻滞后于t3时刻;
35.所述果变量数据集滞后于所述氨水分配数据集,所述输出变量矩阵滞后于所述输入变量矩阵。
36.可选的,所述果变量数据集滞后于所述氨水分配数据集的时滞时间为预先设定,或在训练过程中根据因变量数据集和果变量数据集分析获得。
37.可选的,所述预测控制模型随使用过程进行自优化,自优化的过程包括:
38.获得实时数据集,将实时数据集划分为因变量数据集和果变量数据集,因变量数据集包括实时的氨水分配数据集,果变量数据集包括实时的氮氧化物浓度实测值;
39.将实时数据集转化为输入变量矩阵和输出变量矩阵,利用滑动窗口法根据实时数据集更新输入变量矩阵和输出变量矩阵,更新预测控制模型。
40.可选的,更新预测控制模型的方式包括:获得实时数据集,丢弃历史数据集中距当前时刻最远的数据。
41.可选的,利用滑动窗口法根据实时数据集更新输入变量矩阵和输出变量矩阵,具体包括:将t1时刻的氨水分配数据集转化为输入变量矩阵,将t2时刻的氮氧化物浓度实测值转化输出变量矩阵。
42.本技术基于预测控制模型的水泥窑烟气isncr控制方法至少具有以下技术效果之一:
43.本技术通过预测控制模型实现对氨水分配数据集的调节,通过因变量数据集和果变量数据集训练获得预测控制模型,通过因变量数据集和所述果变量数据集的特征相关度,加快了预测控制模型的训练速度,提高了预测控制模型的控制精度,解决了对氨水分配数据集的调节过程中,因变量数据集之间存在的耦合问题。
44.本技术通过预测控制模型在t1时刻预测t2时刻的氮氧化物浓度,获得t2时刻的氮氧化物浓度预估值,在t2时刻用氮氧化物浓度预估值比较氮氧化物浓度实测值获得二者的偏差,利用该偏差不断优化预测控制模型,使得预测控制模型能够进行实时更新。在某个时刻由于工况变化而使偏差增大时,预测控制模型能够适应工况的变化,保持控制的稳定性和可靠性。
附图说明
45.图1为本技术一实施例中水泥熟料煅烧系统的脱硝场景示意图;
46.图2为本技术一实施例中基于预测控制模型的水泥窑烟气isncr控制方法中预测控制模型的训练流程图;
47.图3为本技术一实施例中基于预测控制模型的水泥窑烟气isncr控制方法的控制流程图;
48.图4为本技术一实施例中预测控制模型的优化过程示意图。
具体实施方式
49.下面将结合本技术实施例中的附图,对本技术实施例中的技术方案进行清楚、完整地描述,显然,所描述的实施例仅是本技术一部分实施例,而不是全部的实施例。基于本技术中的实施例,本领域普通技术人员在没有做出创造性劳动前提下所获得的所有其他实施例,都属于本技术保护的范围。
50.除非另有定义,本文所使用的所有的技术和科学术语与属于本技术的技术领域的技术人员通常理解的含义相同。本文中在本技术的说明书中所使用的术语只是为了描述具体的实施例的目的,不是在于限制本技术。本文所使用的术语“和/或”包括一个或多个相关的所列项目的任意的和所有的组合。
51.本技术中,术语“包括”和“具有”以及他们的任何变形,意图在于覆盖不排他的包含,例如,包含了一系列单元的系统、产品或设备不必限于清楚地列出的那些单元,而是可包括没有清楚地列出的或对于这些产品或设备固有的其它单元。
52.参见图1,在一个实施例中,提供一种水泥熟料煅烧isncr脱硝系统包括依次连接的回转窑、分解炉、五级预热器、增湿塔、生料磨、电吸尘器和窑尾烟囱。使用时,烟气与物料呈逆流运行,依烟气流向,依次经过从窑头喷入煤粉燃烧到回转窑高温烧成,经回转窑的窑尾烟室进入分解炉,分解炉底部再次喷入煤粉燃烧,依次经c5、c4、c3、c2、c1级预热器经预热锅炉、生料磨、窑尾布袋除尘器后经窑尾烟囱排放。isncr脱硝系统,是基于智能选择性非催化还原isncr(intelligent selective non-catalytic reduction)作为烟气脱硝的还原剂计量标准,包括计算水泥熟料煅烧isncr脱硝系统各部分的喷氨量,用于调整喷氨量的喷氨点通常布置在分解炉中上部至c5级预热器区段。
53.水泥熟料煅烧isncr脱硝系统包括控制单元、以及受控于控制单元的喷射单元。喷射单元包括氨水分配模块、压缩空气分配模块,氨水分配模块用于调节喷氨量(氨水分配数据集),压缩空气分配模块用于调节压缩空气量(压缩空气分配数据集)。具体地,控制单元指导调整布置于分解炉预热器800~1000℃温度窗口区间的喷枪模块的氨水喷入量喷射压力和压缩空气的喷入量和喷射压力。
54.控制单元包括基于神经网络构建的预测控制模型,该预测控制模型根据生产数据集预先训练获得。从时间上划分,生产数据集包括历史数据集和实时数据集。从类别上划分,生产数据集包括因变量数据集和果变量数据集。果变量数据集包括窑尾烟囱烟气数据集,至少包括烟气中nox的浓度。因变量数据集即影响果变量数据集的原因,包括氨水分配数据集和压缩空气分配数据集。控制单元例如可以通过信号采集模块完成对生产数据集的采集。
55.本技术硬件和软件上对传统sncr脱硝系统进行全面升级,生产数据集更丰富,参见表1:
56.表1本技术生产数据集和传统sncr脱硝生产数据集对比一览表
[0057][0058][0059]
参见表2,为配合水泥熟料煅烧isncr脱硝系统中喷射单元导出的喷射参数的适时调整,氨水分配模块和压缩空气分配模块的各分配支路配套有流量计、调节阀和减压阀,通过控制各分配支路的氨水流量、压力,压缩空气流量和压力调整,实现喷枪喷入量的调整。
[0060]
表2本技术烟气脱硝系统和传统sncr脱硝系统氨水分配模块和压缩空气分配模块的对比一览表
[0061][0062]
氨水分配模块用于改变水泥熟料煅烧isncr脱硝系统中的喷氨量,压缩空气分配模块用于改变水泥熟料煅烧isncr脱硝系统中的压缩空气量。喷氨量和压缩空气量是指水泥窑工作过程不同位置相应需要的喷氨量和压缩空气量,具体通过氨水分配数据集和压缩空气分配数据集表示该含义。各数据集可参见现有技术中的常规方式或者下文各实施例。
[0063]
氨水分配模块设置8-12个分配支路,各分配支路设置有调节阀、流量计和减压阀,可以控制1-2只喷枪喷射量和喷射压力。相关信号作为生产数据集,详见表3。
[0064]
在氨水分配模块的喷枪布置方案上,本技术将传统sncr脱硝常规配置的2层偏平面化的喷射单元,调整为3-4层喷射单元,喷射层呈立体化布置。对于氨水分配模块,喷枪依烟气流向分别布置在分解炉中上部、分解炉出口、c5级旋风预热器出口、c4级旋风器出口处。通过选择合适的点位,最末级喷射层下游不再有烟气再燃区域;喷射区域能覆盖熟料生产流程上整个适宜sncr脱硝反应的温度窗口。
[0065]
压缩空气分配模块设置2-4个分配支路各分配支路,各分配支路设置有调节阀、流量计和减压阀,可实现控制一层喷淋的压缩空气量和压力,常规1层布置3-8只喷枪。
[0066]
压缩空气分配模块调整各阀门开度,其核心目标是作用于布置在水泥窑分解炉到预热器的喷枪模块。喷枪喷射点位沿烟气流向呈立体化布置,依烟气流向,主要分布在分解炉中上部、分解炉出口、c5级旋风预热器出口、c4级旋风预热器出口,依烟道截面面积每层布置3-4只,沿烟道截面均匀布置。喷射点位处于温度800~1000℃温度区间,为适宜sncr反应的温度窗口区间。
[0067]
压缩空气分配模块配置有3只分配支路,各分配支路对应控制分布在同一烟道截面一层喷枪,均配置有开关阀、调节阀、流量计、减压阀和压力表。相关信号作为生产数据集,详见表3。
[0068]
参见图1,硬件配置方面,本技术将现有传统sncr脱硝系统配置的8只喷枪,改造调整为16支;在喷枪的布置方式上,将现有传统sncr脱硝系统沿烟气流向设2层喷射系统,分别布置在分解炉中上部和分解炉出口至c5级旋风筒,改造调整为3-4层喷射系统,新增的2个喷射层布置在分解炉出口至c4级旋风预热器出口。
[0069]
在生产数据集方面:现有传统sncr脱硝生产数据集参见表2,本技术生产数据集参见图1、表2和表3,可见本技术水泥熟料煅烧isncr脱硝系统从生产参数、烟气参数和脱硝控
制参数方面增加大量参数。
[0070]
表3本技术水泥熟料煅烧isncr脱硝系统的生产数据集
[0071]
[0072][0073][0074]
水泥熟料煅烧isncr脱硝系统按照烟气流向依次包括分解炉、五级预热器和窑尾
烟囱。氨水通过用于喷射氨水的喷枪混入,喷枪设置于分解炉和五级预热器的相应部分,氨水分配数据集用于控制各喷枪。可以理解,c4、c5两级预热器具有适用于sncr脱硝反应的温度窗口区间,可以作为喷枪的设置位置。
[0075]
现有技术中sncr烟气脱硝的nox排放浓度难以达到<100mg/m3的超低排放指标,氨水利用率低,系统运行稳定性和灵敏性欠佳。在整个水泥熟料煅烧isncr脱硝系统中,需要控制的参数包括喷煤量、压缩空气流量和喷氨量等等,详见下文各实施例。就喷氨量而言,存在不同喷氨点及喷氨点的喷氨量综合调整问题,不同喷氨点之间、以及喷氨量与其他控制参数之间存在着密切的影响,存在着强耦合。而从喷入氨水到窑尾烟囱的烟气连续监测系统(cems)获取数据,又存在着大时滞(即改变喷氨量后影响窑尾烟囱的烟气结果需要的时间延迟),这对控制的有效性和稳定性提出了更高要求。
[0076]
预测控制模型通过历史数据集预先训练获得,即水泥窑烟气isncr脱硝预测控制模型的训练,训练过程包括:
[0077]
步骤s100,获得历史数据集,将历史数据集划分为因变量数据集和果变量数据集,因变量数据集包括氨水分配数据集,果变量数据集包括窑尾烟囱烟气数据集;
[0078]
氨水分配数据集即水泥熟料煅烧isncr脱硝系统中设置在不同喷氨点的喷氨量数据,包括喷氨点位、喷氨流量等,预测控制模型可对其进行调节。窑尾烟囱烟气数据集包括氮氧化物浓度(实测排放浓度)。
[0079]
获得历史数据集包括,将t1时刻采集的生产数据集记为x1。x1={x1,x2,.....xm}(m为表3中烟气脱硝采集生产数据数量,允许部分非核心数据缺省,以实际采集量为准,通常m=30-50)。
[0080]
步骤s200,获得因变量数据集和果变量数据集内不同数据的时滞时间;
[0081]
步骤s200中,即可以通过因变量数据集和果变量数据集相互影响的内部联系确认时滞时间,也可以通过日常生产从投料到窑尾烟气产生变化的经验确认时滞时间。实际氨水分配数据集对氮氧化物浓度影响的时滞时间一般为4min。
[0082]
步骤s300,获得因变量数据集和果变量数据集的特征相关度,将因变量数据集划分为特征相关度超过第一阈值的主因子数据集和相关度小于或等于第一阈值的多元数据集;
[0083]
因变量数据集和果变量数据集的特征相关度利用皮尔逊系数排列获得。特征相关度广义上是指因变量数据集中,对某一种果变量数据集起主导影响的数据。狭义上是指不同位置的喷氨点位(p0、p1、p2、p3、p4)对氮氧化物浓度起主导影响的喷氨量。第一阈值例如可以是特征相关度为0.3,适当的阈值大小能够兼顾精度和计算量。
[0084]
在步骤s200~步骤s300中,生产数据集如分解炉中部温度、分解炉出口温度、c5级预热器出口温度、c4级预热器出口温度、总风量、总喷氨流量、各分配支路氨水流量、压力等运行参数。用时滞时间进行时间平移后,利用式(1)计算各变量与nox实测排放浓度之间的相关程度,记录各变量获得最大相关度的大小。
[0085][0086]
式中:r为皮尔逊系数;xi为第i个输入样本数据,为输入样本数据的均值;yi为第i个输出样本数据,包括no
x
排放浓度实测值;为输出样本数据的均值;n为样本数据的总量。输入样本数据即因变量数据集,输出样本数据即果变量数据集。
[0087]
步骤s400,根据主因子数据集和多元数据集,获得基于因变量数据集的输入变量矩阵和基于果变量数据集的输出变量矩阵,例如可以利用偏最小二乘法结合进行主成分回归分析和多元线性回归分析获得;
[0088]
在步骤s100~步骤s400中,因变量数据集包括t3时刻的氨水分配数据集,果变量数据集包括t4时刻的氮氧化物浓度实测值,t4时刻滞后于t3时刻;果变量数据集滞后于氨水分配数据集,输出变量矩阵滞后于输入变量矩阵。
[0089]
可以理解,由于因果变量数据集之间存在时滞时间,在训练过程中需要相应地进行考虑。时滞时间可以是预先设定,或在训练过程中根据因变量数据集和果变量数据集分析获得。t4时刻和t3时刻并不指代具体的时间节点,而应当理解为一种滞后关系,输入变量矩阵和输出变量矩阵之间存在该种滞后关系,以保证模型的有效性。
[0090]
步骤s400中,还包括(1)数据预处理和(2)数据归一化。
[0091]
(1)数据预处理:由于数据本身的可变性、检测设备故障或人为操作失误等原因,运行数据中会存在一些异常值。这类异常值会将错误信息引入数据样本,导致样本特性偏离实际情况,因此需要从建模数据中剔除异常值,采用3σ准则来剔除异常值。
[0092]
(2)数据归一化:采用z-score标准化对特征变量进行归一化,将有量纲数据经过转换公式转化为无量纲数据,避免不同物理意义的变量由于量纲的差别,造成各个量之间标度差不同,进而提高预测模型的稳定性与收敛性。
[0093]
步骤s500,根据输入变量矩阵和输出变量矩阵获得基于神经网络构建的预测控制模型。
[0094]
采用偏最小二乘法(partial least squares,pls),将主成分回归分析和多元线性回归结合起来,通过逐步分解得到输入变量矩阵和输出变量矩阵,综合评价提取的主成分对输入变量和输出变量矩阵的解释能力,直到提取的主成分贡献率之和满足精度要求。本技术通过持续采集生产数据集对生产工况实时跟踪,基于长时间数据积累获得大数据和模糊控制理论建立预测控制模型,保证使用效果。
[0095]
具体地,步骤s100~步骤s500具体通过以下方式实现:
[0096]
利用t1时刻的输入参数集x以及nox排放浓度和4min前的氨水分配数据集,采用偏最小二乘法建立并训练未来4min时刻的nox排放浓度预测模型,获得系数矩阵w和负载矩阵a。具体如下:
[0097]
假设原始n组样本x=[x1,...,xm]∈rn×m和给定输出y∈rn×1,m表示原始样本输入变量个数。通过对原始样本x不断提取由线性表示的正交主成分[t1,
…
,tk],在提取过程中,
通过循环计算使主成分尽可能多的携带x的信息,同时与y的相关性达到最大。具体计算步骤如下。
[0098]
步骤s510,对原始样本x和y进行归一化,得到标准矩阵e0和f0,标准化计算公式为:
[0099][0100]
式中:分别表示样本x、y中对应列向量的均值;si、sy分别表示样本x、y对应的方差。
[0101]
构成标准矩阵e0=[x1,
…
,xm],f0=[y]。
[0102]
步骤s520,先计算矩阵e
0t
f0f
0t
e0最大特征值对应的特征向量w1,并归一化w1=w1/||w1||,计算成分得分向量t1和残差矩阵e1:
[0103]
得分向量t1=e0.w1ꢀꢀꢀ
式(3)
[0104]
残差矩阵e1=e
0-t1ɑ
1t
ꢀꢀꢀ
式(4)
[0105]
其中负载向量α1为
[0106]
α1=e
0t
t1/||t1||2ꢀꢀꢀ
式(5)
[0107]
步骤s530,将e1代替e0代入步骤2中循环计算,直至计算到第k步,得到成分得分向量tk、残差矩阵ek和负载向量αk:
[0108]
tk=e
k-1
ωk[0109][0110][0111]
式中,e
rss
表示统计平方公差矩阵。
[0112]
步骤s540,选择k满足精度要求,得到t=[t1,
…
,tk]为得分矩阵,也即样本主成分;a=[α1,
…
,αk]为负载矩阵;w=[w1,
…
,wk]为系数矩阵。
[0113]
步骤s550,预测模型输出表达为:
[0114][0115]
式(7)和式(8)中,各参数的含义如下:
[0116]
cpre1:nox浓度模型预测值;
[0117]
a:负载矩阵;
[0118]
xi:序列i对应的指标向量;
[0119]
wi:各指标权重系数矩阵。
[0120]
反归一化:将归一化公式代入式(7)中,合并各项系数可得反归一化后的预测模型输出表达为:
[0121][0122]
cpre1:nox浓度模型预测值;
[0123]
b:反归一化后负载矩阵;
[0124]
xi:反归一化后输入参数集矩阵;
[0125]
βi:各指标权重系数向量;
[0126]
步骤s550,获得测试数据集,测试数据集和历史数据集的类型相同,用于验证预测控制模型的训练结果。
[0127]
步骤s550通过加大建模数据量的方法,有效保证所建立的预测模型在稳态和非稳态工况下保持较强的预测能力。即采集水泥熟料线连续15日的运行数据,每30s采集一个数据,经数据预处理和优选,最终选择40000组数据进行建模预测,其中35000组数据作为训练集,5000组数据作为测试集。经验证,基于神经网络构建的预测控制模型与测试集的数据变化趋势大致吻合,其与实际值的皮尔逊关系数为>0.8,认为满足工业控制的需求。
[0128]
由于生料特性、煅烧工况和烟气成分复杂变化,运行参数与nox排放浓度往往存在较大的线性关系,同时运行工况的不断变化,造成线性预测模型的预测精度和稳定性难以长久保证。
[0129]
为有效提高模型在全工况下的预测精度,强化模型预测前馈控制能力,在一个实施例中,提供一种基于预测控制模型的水泥窑烟气isncr控制方法,采集处理后的烟气参数作为窑尾烟囱烟气数据集,输入到预测控制模型输出氨水分配数据集,用于控制氨水的混入,预测控制模型基于神经网络构建预先训练获得,即利用上述步骤s100~s500训练完成的预测控制模型实现。可以理解,预测控制模型的输入的窑尾烟囱烟气数据集、以及输出的氨水分配数据集,二者均属于生产数据集。
[0130]
基于预测控制模型的水泥窑烟气isncr控制方法包括:
[0131]
步骤s600,设定氮氧化物浓度目标值,获得t1时刻的氨水分配数据集和t1时刻的氮氧化物浓度实测值,利用预测控制模型预测t2时刻的氮氧化物浓度,获得t2时刻的氮氧化物浓度预估值,t2时刻滞后于t1时刻;
[0132]
步骤s700,获得t2时刻的氮氧化物浓度实测值,比较t2时刻的氮氧化物浓度实测值和t2时刻的氮氧化物浓度预估值,获得二者的偏差;
[0133]
步骤s800,利用偏差优化预测控制模型。
[0134]
本实施例中,t2时刻滞后于t1时刻一个时滞时间。步骤s800中还包括循环进行上述流程,利用偏差实时地优化预测控制模型。t2时刻和t1时刻并不完全限定为时间轴上的两个时间点,而是相对性的时间概念。
[0135]
具体地,步骤s700和步骤s800可根据式(9)和式(10)进一步理解。
[0136]
δ=(c
s-c
pre2
)/csꢀꢀꢀ
式(9)
[0137]cs
为氮氧化物浓度实测值;
[0138]cpre2
氮氧化物浓度预估值;
[0139]
δ为氮氧化物浓度实测值和氮氧化物浓度预估值的偏差。
[0140]
可以理解,优化后的预测控制模型能够提高氮氧化物浓度预估值的准确性,使之
趋近于氮氧化物浓度目标值。调节氨水分配数据集,具体为改变氨水分配模块最终的喷氨量,此过程可以通过pid积分微分控制完成。可以理解,氮氧化物浓度目标值和氮氧化物浓度预估值的偏差属于果变量数据集的偏差。本技术预测控制模型经过训练后内部形成了氨水分配数据集和氮氧化物浓度特征相关度逻辑(步骤s300和步骤s400),即因果变量数据集之间在输入变量矩阵和输出变量矩阵形成的关联。本技术预测控制模型能够对达到氮氧化物浓度目标值所需要的喷氨量进行计算。由于水泥熟料煅烧isncr脱硝系统在使用时控制参数会受到扰动,通过预测控制模型的持续优化,具体通过,调节氨水分配数据集,使氮氧化物浓度实测值趋近于氮氧化物浓度目标值。
[0141]
从另一个角度来讲,步骤s800也是一种预测控制模型的训练过程,每次循环距离上一次循环相差一个时滞时间。在预测控制模型自优化的过程中,其内部对于输入变量矩阵和输出变量矩阵的耦合关系不断调整。
[0142]
本技术基于预测控制模型的水泥窑烟气isncr控制方法,通过氨水分配模块的自动寻优,改变氨水分配数据集,灵活调配投入的喷枪点位、各路喷枪的流量、压力,以及压缩空气的流量和压力,实现精准喷氨,进而实现水泥窑烟气nox超低排放。与最优喷射参数集对应,对现有传统sncr脱硝系统喷枪点位进行优化,扩大喷射层能覆盖的温度流程,采用分层级安装可独立控制的喷枪组,实时调整并分别控制各路喷枪喷射位置、氨水及压缩空气喷射量和压力。
[0143]
基于预测控制模型的水泥窑烟气isncr控制方法以传统串级pid控制为基础,将窑尾烟气nox的预测方法引入基于预测控制模型的水泥窑烟气isncr控制方法中,获得偏差后根据pid调节控制氨水分配模块,调节氨水分配数据集喷氨量,使时滞时间后的氮氧化物浓度实测值小于50mg/m3,实现氨水消耗量的节省,优化模型充分利用初始模型中的有用信息。调节当前氨水分配数据集可以是通过预测控制模型调节各点位喷枪随工况变化实时调整喷射状态。喷射单元可实现导入生产参数集导出最优喷射方案对应的氨水分配数据集,并指导各点位喷枪调整。
[0144]
步骤s700中,氮氧化物浓度目标值和当前时刻氮氧化物浓度实测值的偏差作为分段函数输入,计算得到氨水分配数据集的调节量。其中,分段函数的各分界点可由基于预测控制模型的水泥窑烟气isncr控制方法在线调试获得。为提高稳定性,对各变量进行一定的滞后处理,即滞后获得生产数据集,滞后时间例如可以是30s。利用在线调试方法对pid参数和各分段函数的分界点进行调试和确定。
[0145]
具体地,选择分解炉中上部温度,c5、c4级旋风预热筒温度作为第1关键变量,进行前馈调节。总烟气量既是计量氨水耗量的关键参数,也能在一定程度上反应燃烧工况的变化,因此选择烟气量作为第2关键变量,进行前馈调节。获取当前时刻的分解炉中上部,c5、c4级旋风预热筒温度数据,并计算各自均值,最后作为分段函数的输入,计算得到预热器变化前馈调节量和窑尾烟气排放量变化调节量。获取当前时刻的总烟气量值,基于分段函数计算得到总烟气量。基于预测控制模型的水泥窑烟气isncr控制方法以传统串级pid(proportion integratio differentiation,pid)控制为基础,同时将nox排放浓度模型预测前馈和烟气量变化前馈引入烟气脱硝控制方法中,以有效解决水泥生产复杂变化和脱硝过程具有的大延迟、大滞后等问题。
[0146]
水泥熟料线运行参数特性会实时变化,主要由两方面因素引起:一是由于生产负
荷变化引起的运行参数调整,从而导致设备运行在新的工况状态下。这种变化是可逆的,负荷指令会不断改变,运行工况也会随之不断变化,设备的运行状态有可能恢复到历史工况中已有的状态。二是在运行过程中,由于技改、系统处置固体废物的变化等原因,导致生产运行特性发生变化。这种变化是不可逆的,设备发生这种变化后会进入新的运行状态并且不会再恢复到以前的状态。两种情况时,根据原有运行状态建立的设备模型会出现模型失效的现象,导致模型的计算精度下降,有可能对水泥窑烟气稳定可靠运行造成不利影响。
[0147]
在一个实施例中,在基于预测控制模型的水泥窑烟气isncr控制方法中,预测控制模型随使用过程进行自优化,即水泥窑烟气isncr脱硝预测控制模型的优化,自优化的过程包括:
[0148]
步骤s910,获得实时数据集,将实时数据集划分为因变量数据集和果变量数据集,因变量数据集包括实时的氨水分配数据集,果变量数据集包括实时的氮氧化物浓度实测值;
[0149]
步骤s920,将实时数据集转化为输入变量矩阵和输出变量矩阵,利用滑动窗口法根据实时数据集更新输入变量矩阵和输出变量矩阵,更新预测控制模型。
[0150]
步骤s920具体包括,将t1时刻的氨水分配数据集转化为输入变量矩阵,将t2时刻的氮氧化物浓度实测值转化输出变量矩阵。关于t1时刻和t2时刻的解释参见上述相关实施例。
[0151]
步骤s910和步骤920,从控制氨水的混入到改变窑尾烟囱烟气数据集存在时滞时间;氮氧化物浓度实测值相应滞后于氨水分配数据集,输出变量矩阵相应滞后于输入变量矩阵。本实施例结合滑动窗口法提出一种自适应模型更新策略,在保证模型有效性的同时减少了计算量和更新耗时自优化模型通过长时间序列下历史数据集和各生产工况对应的大量nox预测值和nox实测值比对实现曲线拟合,形成新的优先级曲线,通过系统的自动学习,实现预测控制模型的不断优化。
[0152]
可以理解,基于预测控制模型的水泥窑烟气isncr控制方法中周期性地当前时刻氮氧化物浓度实测值,可视为实时数据集。与此同时,预测控制模型还周期性地获得氨水分配数据集,检测的周期例如可以是时滞时间。将实时数据集转化为输入变量矩阵和输出变量矩阵的方式,可参见步骤s300~步骤s400中,将历史数据集转化为输入变量矩阵和输出变量矩阵的方式。
[0153]
具体地,对步骤s910和步骤s920详细展开表述如下。采用滑动窗口法设定固定长度的样本作为训练样本,并使窗口随着新样本的采集不断向前滑动,在舍弃旧样本的同时添加新样本,从而实现模型的更新。pls模型更新是为了更新核矩阵中的元素,采用自适应模型更新策略,更新过程中只需改变部分元素的位置并计算少量新元素,不必重构模型需重新计算整个矩阵进行大量重复计算。
[0154]
更新预测控制模型的方式包括:获得实时数据集,丢失历史数据集中距当前时刻最远的数据。具体流程如下。模型更新策略的实时过程可以分为两部分,删除旧样本和增加新样本。设样本更新窗口长度为m,则对于建模对象当前的运行状态,前m组样本为没有价值的旧样本点,应删除核矩阵中包含x1~xm的元素,删除相应元素以后的核矩阵记为kn×
n,
针对变量x∈rn,核矩阵kn×n的表达式为
[0155][0156]
设样本更新窗口长度为m,则对于建模对象当前的运行状态,前m组样本为没有价值的旧样本点,应删除核矩阵中包含x1~xm的元素,删除相应元素以后的核矩阵记为k
(n-m)
×
(n-m)
[0157][0158]
删除旧样本后,为了保持核矩阵的阶次,需要增加相同数量的新样本。由于模型更新采用时序更新策略,新添加的矩阵元素需要考虑样本时序,添加新元素后的核矩阵记k’n
×n。
[0159][0160]
本技术各实施例中,通过步骤s100~s500训练完成的预测控制模型实现nox预测。通过训练完成的预测控制模型调节氨水分配数据集,实时精准分配喷氨系数,实现精准喷氨。通过预测控制模型随使用过程进行的自优化,保证预测控制模型的使用效果,具体通过持续数据积累完成数据训练,对算法模型持续优化。
[0161]
本技术各实施例通过训练获得预测控制模型应用于水泥熟料煅烧isncr脱硝系统,实现nox初始浓度的预测、精准喷氨、自动寻优,控制水泥窑烟气中nox超低排放,可控制窑尾烟囱烟气nox排放浓度小于50mg/m3。本技术各实施例的基本原理是sncr脱硝,通过工业智能化的手段,通过预测控制模型对喷射单元的控制,在技术指标可达的基础上,建设成本和运行成本都大幅降低,具有可操作性。
[0162]
本技术解决了传统sncr脱硝通过pid线性控制存在调控滞后、稳定性欠佳的问题,基于大数据和模糊控制理论实现nox稳定可靠超低排放,是将大数据技术应用于水泥窑烟气脱硝的技术先导。与传统sncr脱硝技术相比,本发明的有益效果,具体表现在以下四个方面:
[0163]
第一,将nox排放浓度模型预测前馈和烟气量变化前馈引入sncr脱硝控制中,以有效解决水泥要特性复杂变化和脱硝过程具有的大延迟、大滞后等问题。
[0164]
第二,通过皮尔逊系数确定的相关性关系找到主因子数据集作为输入参数集进行预测、控制,解决了传统控制原理基于基于精准测量的pid控制与实际难以实现精准测量的难题,通过还消除了测量误差,通常可以实现提前4min预测参数作为前馈,弥补反馈控制策略喷射参数到窑尾烟囱烟气检测结果的时滞。
[0165]
第三,实时导入生产数据集即可导出对应工况下的最优喷射参数,喷射参数即喷射单元的控制参数包括氨水分配数据集。通过调整氨水分配数据集灵活调配各点位的喷枪的投用和退出,各路喷枪氨水和压缩空气的流量和压力,实现精准喷氨。
[0166]
第四,对生产数据集、氨水分配数据集和氮氧化物浓度实测值,进行实时监测和积累。利用最接近目标nox浓度和最小喷氨量作为目标函数,通过曲线拟合完成数据训练和自动寻优,实现预测模型和喷射模型的自优化。
[0167]
参见表4,采用本技术各实施例提供的水泥熟料煅烧isncr脱硝系统和控制方法效果良好,改造前后对比数据如下。
[0168]
表4利用本技术烟气脱硝控制方法改造前后技术经济指标对比表
[0169]
[0170][0171]
表中可见:
[0172]
(1)烟气脱硝适宜的控制区间为将nox控制在100mg/m3以下,满足水泥窑nox超低排放要求;
[0173]
(2)基于现行控制标准,将nox同等控制在320mg/m3,烟气脱硝系统氨水消耗量比传统sncr脱硝系统节省氨水消耗量,氨水节省量高于35%;
[0174]
(3)烟气脱硝系统稳定性更好,nox小时均值波动幅度在30mg/m3以下,日均值波动幅度小于1mg/m3,远低于传统sncr脱硝nox波动幅度。统计nox瞬时值达标率,传统sncr脱硝达标率95%,烟气脱硝可以严格控制达标率在99%以上,也说明烟气脱硝更稳定。
[0175]
(4)通过投入运行0-10天、10-20天和投入运行20-30天的数据对比,可以看到,本技术预测控制模型具有智能学习和自优化功能,通过数据持续积累完成了数据训练和预测模型和喷射模型的自优化,系统运行稳定性、灵敏性和可靠性更高。
[0176]
以上实施例的各技术特征可以进行任意的组合,为使描述简洁,未对上述实施例中的各技术特征所有可能的组合都进行描述,然而,只要这些技术特征的组合不存在矛盾,都应当认为是本说明书记载的范围。不同实施例中的技术特征体现在同一附图中时,可视为该附图也同时披露了所涉及的各个实施例的组合例。
[0177]
以上实施例仅表达了本技术的几种实施方式,其描述较为具体和详细,但并不能因此而理解为对申请专利范围的限制。应当指出的是,对于本领域的普通技术人员来说,在不脱离本技术构思的前提下,还可以做出若干变形和改进,这些都属于本技术的保护范围。