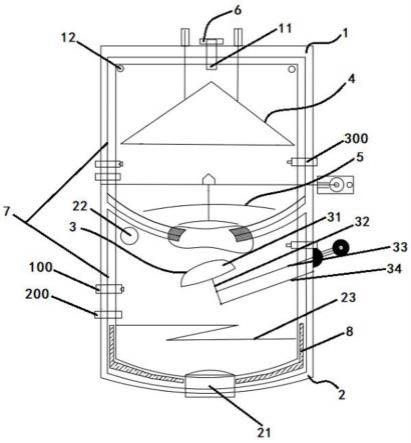
1.本发明涉及碳素行业中多种不同粒径物料均匀混合的设备及混捏工艺,具体是一种新型混捏锅及混捏工艺。
背景技术:2.目前物料混合、混捏过程普遍采用导热油加热方式,此方法主要是通过热传导的热传递方式提升物料温度,加热效率低、耗时长,虽然不断地进行搅拌混合,但是否接触导热油管路对物料温度影响明显,不同区域处物料温度差异大,物料升温耗时一般都大于半小时,长时间的搅拌会改变物料粒径,导致实际物料粒径配比与工艺配方存在明显差异,进而影响工艺稳定性,物料搅拌混合过程中为了防止飘尘外溢,负压除尘设备一直保持稼动状态,更加重了微细粉料的流失,对物料粒径配比的失真更是雪上加霜,而且提高了生产能耗、增加了生产成本;另外现有搅拌刀的搅拌形式及搅拌工艺比较单一,搅拌过程中不同粒径物料混合不够充分,不能达到快速均匀混合的目的,在物料搅拌过程中,刀轴温度升高很容易导致密封失效,刀轴处润滑油泄露,致使物料不纯,严重影响产品质量。
3.现有技术中在添加物料及搅拌混合的过程中,极易发生飘尘外溢,严重影响劳动环境甚至危害员工健康、对行业形象起到极大的负面效应,目前行业内普遍采用大口径、高功率吸尘设备解决飘尘问题,但设备整体智能化低,设备能耗大,且极易将粉料抽走,改变了配方中各粒径比例、降低了配方可靠性,工艺及产品质量稳定性差。
4.因此,急需寻找一种能够降低生产时间,提高搅拌效果和混捏质量的混捏设备及混捏工艺。
技术实现要素:5.本发明的目的是提供一种新型混捏锅及混捏工艺,通过改进混捏锅的结构克服目前工艺缺陷,采用射频加热实现物料的均匀、快速加热,降低物料混合时间,降低物料粒径变化范围、保障了各粒径物料配方比例,提升了实际物料组分与理论配方的契合度,增加了工艺稳定性进而保障了产品质量的稳定性;通过粉料搅拌组件的设计,能够更有效的将各粒径物料均匀搅拌混合,降低飘尘、提升了配方中细粉料比例的稳定性;通过计算物料体积,按比例提前对锅体内进行抽气降压,不仅能够有效降低搅拌混合过程中的飘尘而且能够降低除尘负荷,还可以避免高功率除尘将配方中细颗粒物料抽走带来的配方变化,有效保障了配方稳定性,进而保障了工艺及产品质量的稳定。通过控制糊料混捏锅内的压力先负压再加压后常压,并在压力变化过程中配合超声波发生器产生超声波,利用超声波在液态传播时产生的空化效应及共振效应,促使黏结剂更好的浸入到物料的毛细微孔中,有效的提升浸润、混捏效果,提高了产品密实度。
6.为解决上述技术问题,本发明提供了一种新型混捏锅,包括从上至下依次设置的粉料混合锅体和糊料混捏锅体,所述粉料混合锅体的顶部设有第一进料口,所述第一进料口的下方设有辅助进料组件,所述辅助进料组件的下方设有粉料搅拌组件,所述粉料混合
锅体的外侧设有粉尘吸收装置,所述粉料混合锅体上设有油料喷射孔,所述粉料混合锅体和所述糊料混捏锅体的内外层锅体之间均设有射频加热件,所述糊料混捏锅体的底部内外层锅体之间设有超声波发生器,所述粉料混合锅体的底部设有第一出料口,所述糊料混捏锅体的顶部设有第二进料口,所述第一出料口与所述第二进料口之间设有排料组件,所述糊料混捏锅体的底部设有第二出料口。
7.进一步的,所述辅助进料组件包括电动推杆和伞形分料器,所述电动推杆至少具有两个,所述电动推杆的下端与所述伞形分料器固定,上端伸出所述粉料混合锅体外连接有驱动机构。
8.进一步的,所述粉料搅拌组件包括齿轮箱、设置在齿轮箱内的伞齿轮组件、同轴设置的传动轴和固定杆,所述伞齿轮组件包括第一伞齿轮、第二伞齿轮和第三伞齿轮,所述第二伞齿轮和所述第三伞齿轮上下同轴对称设置在所述齿轮箱内,且分别与所述第一伞齿轮啮合,远离所述齿轮箱的所述固定杆一端固定在所述粉料混合锅体的内壁,所述传动轴的一端穿出所述粉料混合锅体外连接有电机输出端,另一端穿设在所述齿轮箱内与所述第一伞齿轮连接,所述第二伞齿轮上连接有第一刀轴,所述第一刀轴的端部设有第一搅拌刀,所述第三伞齿轮上连接有第二刀轴,所述第二刀轴套设在所述第一刀轴的外侧,所述第二刀轴的端部设有第二搅拌刀。
9.进一步的,所述排料组件包括排料塞、支撑杆和移动杆,所述排料塞与所述支撑杆固定连接,所述移动杆的一端与所述支撑杆固定连接,另一端穿出所述糊料混捏锅体外连接有驱动机构。
10.进一步的,所述糊料混捏锅体上设有黏结剂添加孔,所述糊料混捏锅体内设有糊料搅拌组件,所述糊料搅拌组件包括z字型搅拌刀,所述糊料混捏锅体和所述粉料混合锅体上均设有视频探头、温度感知探头和气压调节口。
11.进一步的,所述齿轮箱的顶部呈锥状,所述第二伞齿轮和所述第三伞齿轮通过轴承与所述齿轮箱的上下内壁固定。
12.进一步的,所述支撑杆的下端连接有第二移动杆,所述第二移动杆的一端嵌设在所述糊料混捏锅体的内外层锅体之间。
13.另一方面,本发明还提供了一种新型混捏锅的混捏工艺,采用上述的新型混捏锅进行加工,所述工艺如下:
14.s1、根据所加物料的体积大小,调节粉料混合锅体和糊料混捏锅体内的气压;根据物料的体积大小与锅体的实际体积,通过外接计算机按高度计算公式计算出伞形分料器距离锅底的高度并控制电动推杆带动伞形分料器实现位置变更;控制射频加热件对粉料混合锅体和糊料混捏锅体内进行预热。
15.s2、打开粉料搅拌组件,使得第一搅拌刀和第二搅拌刀旋转,然后将按照配方称重后的物料从第一进料口经过辅助进料组件进入粉料混合锅体内;混合过程中,通过温度感知探头及时了解物料温度,并将信号反馈给计算机,计算机根据物料量及探测温度调整加热频率,保持粉料混合锅体的锅内温度90~140℃,气压调节口不断调整锅内气压,将蒸发的水分等挥发分分离,向油料喷射孔内喷射雾化油料,使得油料与物料在搅拌的作用下快速进行混合;通过视频探头及时了解锅体内生产情况,待物料温度及混合情况达到工艺要求后通过排料口排至糊料混捏锅内。其中,粉料混合锅体的锅内温度优选为110~130℃。
16.s3、打开糊料搅拌组件,根据生产实际情况由黏结剂添加孔向锅体内采用先喷雾式喷入后流淌式注入黏结剂,然后通过控制糊料混捏锅内的压力先负压再正压后常压,利于黏结剂浸入到物料的毛细孔径中,提升糊料混捏质量,降低糊料气孔率,提升产品密实度;而且在压力变化过程中配合超声波发生器产生的超声波,利用超声波在液态中传播时产生的空化效应及共振效应,使黏结剂更好的浸入到物料的毛细微孔中;混捏过程中,通过温度感知探头及时了解锅体内物料温度,并将信号反馈给计算机,计算机根据物料量及探测的温度实时改变加热频率,保持糊料混捏锅的锅内温度110~160℃,混捏结束后通过第二出料口排出物料。其中,通过视频探头及时了解生产情况,根据实际情况调整黏结剂用量。
17.进一步的,所述s1中按物料体积的1.1~1.3倍进行抽气降压,优选为1.2倍,其中物料体积可以将实际生产所需的物料测量平均密度后,由重量除以平均密度获得理论值,或者直接称取物料后现场测量体积获得经验值,或者上述理论值与实际值取平均值;所述高度计算公式为h
距离锅底高度
=kv
物料体积
/s
混捏锅截面积
,其中升高系数k取值为1.05~1.45,优选值为1.25;控制射频加热件对粉料混合锅体和糊料混捏锅体内进行预热的温度为100~120℃。
18.进一步的,所述s3中糊料混捏锅的锅内温度为140~150℃。
19.本发明的有益效果是:
20.1.通过射频加热方式能够使物料得到快速、均匀的加热,缩短了生产时间,提高了设备的利用率,解决了当前加热慢、物料温度不均匀、搅拌时间长的问题;物料混合搅拌过程时间长会导致物料粒径变化,引起实际物料配比与配方不一致,进而导致工艺及产品质量稳定性差,采用射频加热的方式,可以有效提升加热均匀性,降低搅拌时间、保障配方中各物料粒度配比,提升实际物料配比与配方物料配比的契合度,进而提升工艺及产品稳定性;粉料混合锅体和糊料混捏锅体均采用可透过射频及超声波的碳纤维材质制造,粉料混合锅体和糊料混捏锅体均设有检修口,既实现了设备的轻质化,又能方便的进行维护、维修。
21.2.通过辅助进料组件的设计,既保证了物料均匀搅拌的混合空间,又降低了飘尘扩散的空间;结合粉尘吸收装置的设计,能够降低或杜绝物料添加及搅拌混合过程中的飘尘外溢问题,不仅降低了微细物料丢失的几率,还优化了生产环境,对一线工人的身心健康大有裨益,能够有效提升产业形象。
22.3.通过粉料搅拌组件的设计,两个转动方向搅拌物料,提高物料混合均匀性,提高设备搅拌效率,提高了生产效率;
23.4.通过设计的“先喷雾式喷入,后流淌式注入”的黏结剂加入方式,不但可以有效降低飘尘、保证配方稳定可靠,而且还增强了配方中微细物料对黏结剂吸收的均匀性,又可以减少黏结剂添加过程中的混捏阻力,预防混捏外接电动机超负荷运行,防止动力电源电压剧烈波动。
24.5.本发明的混捏工艺中,通过控制糊料混捏锅内的压力先负压再加压后常压,压力变化过程中辅助以超声波振荡的工艺方法,利用超声波在液态中传播时产生的空化效应及共振效应,使黏结剂更好的浸入到物料的毛细微孔中,提高了物料微孔填充率及混捏的均匀性,提高了混捏质量及产品的密实度。
25.6.通过视频探头、温度感知探头能够及时了解生产情况,根据实际情况调整黏结
剂用量、控制射频加热温度,无需打开混捏腔体查看生产情况,杜绝了混捏过程中有毒挥发物质及粉尘的逸出,优化了劳动环境,降低了职业病患病概率,有效提升产业形象。
26.7.第一搅拌刀和第二搅拌刀的刀体采用碳纤维材质,第一刀轴和第二刀轴采用金属材质,如此便可实现:射频加热件可以加热刀体而不加热刀轴,能够有效避免刀轴温度升高导致的密封失效、润滑油泄露、润滑失效,刀轴损坏的问题,能够有效的解决现有技术中采用导热油加热搅拌刀,刀轴不便于冷却的问题,能够有效避免刀轴密封失效,导致的润滑油泄露污染物料的问题;而且纤维搅拌刀自身重量小,可以有效降低能耗,纤维刀体在加热的过程中,与物料温差小,更利于物料升温,更利于搅拌、混捏的稳定性及均匀性。
附图说明
27.为了更清楚地说明本发明的技术方案,下面将对实施例或现有技术描述中所需要使用的附图作简单地介绍,显而易见地,下面描述中的附图仅仅是本发明的一些实施例,对于本领域普通技术人员来讲,在不付出创造性劳动的前提下,还可以根据这些附图获得其它附图。
28.图1是本发明的新型混捏锅的结构示意图;
29.图2是本发明的新型混捏锅的辅助进料组件的结构示意图;
30.图3是本发明的新型混捏锅的粉料搅拌组件的结构示意图;
31.图4是本发明的新型混捏锅的伞齿轮组件的局部示意图;
32.图中:1-粉料混合锅体,2-糊料混捏锅体,3-排料组件连接,4-辅助进料组件,5-粉料搅拌组件,6-粉尘吸收装置,7-射频加热件,8-超声波发生器,11-第一进料口,12-油料喷射孔,21-第二出料口,22-黏结剂添加孔,23-糊料搅拌组件,31-排料塞,32-支撑杆,33-移动杆,34-第二移动杆,41-电动推杆,42-伞形分料器,51-齿轮箱,52-伞齿轮组件,53-传动轴,54-固定杆,521-第一伞齿轮,522-第二伞齿轮,523-第三伞齿轮,524-第一刀轴,525-第一搅拌刀,526-第二刀轴,527-第二搅拌刀,528-轴承,100-视频探头,200-温度感知探头,300-气压调节口。
具体实施方式
33.下面将结合本发明说明书附图,对本发明实施例中的技术方案进行清楚、完整地描述,显然,所描述的实施例仅仅是本发明一部分实施例,而不是全部的实施例。基于本发明中的实施例,本领域普通技术人员在没有做出创造性劳动的前提下所获得的所有其他实施例,都属于本发明保护的范围。
34.在本发明的一个具体实施例中,如图1所示,一种新型混捏锅,包括从上至下依次设置的粉料混合锅体1和糊料混捏锅体2,粉料混合锅体1的顶部设有第一进料口11,第一进料口11的下方设有辅助进料组件4,不但可以有效降低飘尘、减少物料损失防止配方失真,而且可以有效提升物料混合均匀性;辅助进料组件4的下方设有粉料搅拌组件5,粉料混合锅体1的外侧设有粉尘吸收装置6,粉料混合锅体1上设有油料喷射孔12,喷射孔的喷射角度可以调整,通过喷射蒽油、煤油等物料,不仅可以降低飘尘而且能够在物料微孔内形成一层浸润油膜,可以有效的提升配方料中物料的浸润效果,增加制品的机械性能,提高残碳率进而提升制品密实度;
35.粉料混合锅体1和糊料混捏锅体2的内层锅体均采用碳纤维材质,粉料混合锅体1和糊料混捏锅体2的内外层锅体之间均设有射频加热件7,能够对粉料混合锅体1和糊料混捏锅体2内的物料进行均匀快速的加热,此过程中配合压强变化能够有效的分离水分,提升物料纯度,便于混捏过程的进行,提高产品的密实度;
36.糊料混捏锅体2的底部内外层锅体之间设有超声波发生器8,粉料混合锅体1的底部设有第一出料口,糊料混捏锅体2的顶部设有第二进料口,第一出料口与第二进料口之间设有排料组件3,糊料混捏锅体2的底部设有第二出料口21,糊料混捏锅体2上设有黏结剂添加孔22,糊料混捏锅体2内设有糊料搅拌组件23,糊料搅拌组件23包括z字型搅拌刀,糊料混捏锅体2和粉料混合锅体1上均设有视频探头100、温度感知探头200和气压调节口300,其中,射频加热件7、粉料搅拌组件5、超声波发生器8、糊料搅拌组件23均由计算机控制系统控制。
37.排料组件3包括排料塞31、支撑杆32和移动杆33,排料塞31与支撑杆32固定连接,移动杆33的一端与支撑杆32固定连接,另一端穿出糊料混捏锅体2外连接有驱动机构,支撑杆32的下端连接有第二移动杆34,第二移动杆34的一端嵌设在糊料混捏锅体2的内外层锅体之间。
38.驱动机构驱动移动杆33作下压或抬起运动,实现粉料混合锅体1的关闭或排料动作,排料组件3排料过程:粉料混合锅体1内物料搅拌混合结束后,驱动机构驱动移动杆33作抬起运动,具体的,移动杆33以与糊料混捏锅体2接触部为支点转动,带动支撑杆32以与移动杆33的连接点转动,使得排料塞31从第一出料口与第二进料口之间转动出来,形成料口,便于物料进入糊料混捏锅体2进行下一步糊料混捏操作。其中,第二移动杆34以与糊料混捏锅体2接触部为支点转动,提高转动过程中的稳定性。
39.如图2,辅助进料组件4包括电动推杆41和伞形分料器42,电动推杆41具有四个且呈圆周等距分布,电动推杆41的下端与伞形分料器42固定,上端伸出粉料混合锅体1外连接有驱动机构,电动推杆41带动伞形分料器42可以进行上下距离调整,既保证物料均匀搅拌混合空间,又降低飘尘扩散空间,减少配方中微细粉料的丢失,提升实际物料配比与配方物料配比的契合度,进而提升工艺及产品稳定性。
40.如图3-4,粉料搅拌组件5包括齿轮箱51、设置在齿轮箱51内的伞齿轮组件52、同轴设置的传动轴53和固定杆54,伞齿轮组件52包括第一伞齿轮521、第二伞齿轮522和第三伞齿轮523,齿轮箱51的顶部呈锥型,第二伞齿轮522和第三伞齿轮523上下同轴对称设置在齿轮箱51内,且分别与第一伞齿轮521啮合,远离齿轮箱51的固定杆54一端固定在粉料混合锅体1的内壁,传动轴53的一端穿出粉料混合锅体1外连接有电机输出端,另一端穿设在齿轮箱51内与第一伞齿轮521连接,第二伞齿轮522上连接有第一刀轴524,第一刀轴524的端部设有第一搅拌刀525,第三伞齿轮523上连接有第二刀轴526,第二刀轴526套设在第一刀轴524的外侧,第二刀轴526的端部设有第二搅拌刀527,第二伞齿轮522和第三伞齿轮523通过轴承528与齿轮箱51的上下内壁固定。
41.电机输出端驱动传动轴53转动,带动第一伞齿轮521转动,从而带动第二伞齿轮522和第三伞齿轮523转动,间接带动第一搅拌刀525和第二搅拌刀527转动,两个方向进行物料搅拌,提高了物料混合的均匀性,提高了搅拌速率及生产效率。
42.其中,第一搅拌刀525和第二搅拌刀527及z字型搅拌刀的刀体采用碳纤维材质,第
一刀轴524和第二刀轴526采用金属材质,这样射频加热件7可以加热刀体而不加热刀轴,防止刀轴温度升高导致润滑油失效,刀轴损坏的状况发生,能够有效的解决现有技术中导热油加热搅拌刀过程中刀轴不方便冷却的问题;杜绝刀轴密封损坏,润滑油泄露导致糊料不纯,严重影响产品混捏质量的状况发生;而且纤维搅拌刀自身重量小,碳纤维刀体加热速率快且升温均匀,与物料、黏结剂之间的温差小,更利于物料搅拌、混捏的均匀性,可以有效地降低生产能耗。
43.另一方面,本发明还提供了一种新型混捏锅的混捏工艺,采用新型混捏锅进行加工,工艺步骤如下:
44.s1、按物料体积的1.1~1.3倍进行抽气,调节粉料混合锅体内的气压,防止物料中的微细粉料飘尘外溢,与现有技术采用大功率负压吸尘不同,可以有效地避免微细物料损失、提高实际物料配比与配方的契合度,提高工艺稳定性;根据物料的体积大小与锅体的实际体积,通过外接计算机按h
距离锅底高度
=1.25v
物料体积
/s
混捏锅截面积
计算出伞形分料器距离锅底的高度并控制电动推杆带动伞形分料器实现位置变更;既保证了物料均匀搅拌的混合空间,又降低了飘尘的扩散空间;控制射频加热件对粉料混合锅体和糊料混捏锅体内进行预热的温度为100~120℃。
45.s2、打开粉料搅拌组件,使得第一搅拌刀和第二搅拌刀快速旋转,然后将按照配方称重后的物料从第一进料口经过辅助进料组件进入粉料混合锅体内,气压调节口不断调整锅内气压,将蒸发的水分等挥发分分离,向油料喷射孔内喷射油料,降低飘尘,提高物料对油料的均匀吸附性,使得油料与物料在搅拌的作用下快速进行混合;混合过程中,通过温度感知探头及时了解物料温度,调整射频加热频率,保持粉料混合锅体的锅内温度100~120℃,通过视频探头及时了解生产情况,待物料混合均匀后通过第一排料口排至糊料混捏锅内。
46.s3、打开糊料搅拌组件,通过控制糊料混捏锅内的压力先负压,然后向黏结剂添加孔内喷入经过雾化后的黏结剂,搅拌过程中再控制气压进行加压后常压,能够有效的提升沥青等黏结剂对物料的浸润,降低物料中空隙的比率,且在压力变化过程中配合超声波发生器产生的超声波,利用超声波在液态中传播时产生的空化效应及共振效应,使黏结剂更好的浸入到物料的毛细微孔中;混捏过程中,通过可以自由调整角度的温度感知探头,及时了解物料温度,调整射频加热频率,保持糊料混捏锅的锅内温度140~150℃,结束后通过第二出料口排出物料。
47.其中,混合搅拌后的物料加入到糊料混捏锅,此过程中黏结剂采用喷雾式喷入,通过视频探头观察锅体内飘尘基本得到抑制时改为流淌式注入,此过程采用计算机控制时间参数或者黏结剂用量,实现先喷雾后流淌的功能,视频探头开始时用来确定黏结剂配方用量,配方确定后起到监控作业过程的作用。
48.以上所揭露的仅为本发明的一种较佳实施例而已,当然不能以此来限定本发明之权利范围,因此依本发明权利要求所作的等同变化,仍属本发明所涵盖的范围。