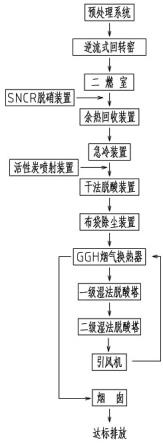
1.本发明涉及废活性炭利用处置技术领域,具体涉及一种颗粒状废活性炭逆流式回转窑热解再生工艺。
背景技术:2.活性炭由于其优异的吸附性能而广泛应用于石化、化工、医药、染料、黄金冶炼、半导体、生物工程、核电、食品、调味品、饮料、自来水净化、废水处理、空气净化、烟气净化、溶剂回收、土壤修复、贵金属碳基催化剂、超级电容器、纳米材料等领域。活性炭使用一段时间后,其孔隙结构被吸附质堵塞,吸附能力显著下降或完全丧失,不再满足其使用工艺要求而成为废活性炭。废活性炭是一种有毒有害物富集体,具有有毒有害、易燃等危险特性,若处理不当极易造成地下水、土壤污染,影响人体健康和生产生活,因此被纳入一般固废或危险废物管理范畴。若将废活性炭直接焚烧填埋,不仅会造成资源的大量浪费,还会造成严重的环境污染。
3.废活性炭由于吸附了各种有机物、无机物及重金属等杂质,不能直接回用于原有使用领域,需再生处理后才能循环使用。废活性炭的再生方法很多,常见的有热再生法、微波再生法、超声再生法、生物再生法、化学再生法、溶剂再生法、电化学再生法、芬顿氧化法、湿式氧化法、超临界氧化法、催化氧化法和光催化再生法等。热再生法由于适应性强已成为应用最为广泛的废活性炭再生技术。其他再生方法由于物料普适性差,再生机理不明、工艺技术不完善等原因,并未得到广泛的工业化应用。
4.废活性炭热解再生作为热再生法中的一种最为重要的技术,是国内外废活性炭再生工业化应用最广泛、最成熟的主流技术。废活性炭热解再生大多采用回转窑、多膛炉作为热解反应器,多膛炉由于内部机械转动结构复杂、故障率高、活性炭机械磨损大等原因,目前主要应用于大型污水处理厂的生物活性炭再生。回转窑热解炉在国内废活性炭再生应用中得到了一定程度的发展,但多种类废活性炭的综合热解再生反应机理研究薄弱,对回转窑热解再生技术、装备和工程应用的理论支撑不足。国内回转窑热解再生废活性炭在原位再生、集中再生应用实践中,尚存在较多的技术和工程应用缺陷,废活性炭回转窑热解的工艺设计漏项和缺陷多,回转窑热解反应器的结构不合理,回转窑和其他主设备的选型计算不合理,余热回收和烟气净化系统的设计依据和标准引用混乱等,导致再生活性炭的吸附性能下降,再生活性炭的强度低、循环使用次数低,活性炭再生过程炭基质损失大,再生能耗高,装备的实际再生能力小,再生烟气排放超标等问题。
技术实现要素:5.本发明的目的在于针对现有废活性炭热解再生技术的缺陷和不足,提供一种颗粒状废活性炭逆流式回转窑热解再生工艺,以解决现有颗粒状废活性炭热解再生技术中再生效率低、炭基质损失大、耗能高、强度、碘值达不到相关标准要求,以及难以彻底净化再生烟气等技术问题。
6.为实现上述目的,本发明采用以下技术方案是:一种颗粒状废活性炭逆流式回转窑热解再生工艺,它包含以下步骤:步骤1:对来自不同行业、不同产废企业的废活性炭,按原生活性炭的种类、形态、粒径及废活性炭的产生工艺进行综合分类,如煤质破碎活性炭、颗粒状活性炭、柱状活性炭、挥发性有机物vocs治理活性炭、污水处理生物活性炭、净水活性炭、催化剂载体活性炭等;步骤2:对来自不同产废企业、不同产废工艺工序的颗粒状废活性炭进行化验分析,检测含水量、挥发份、灰份、固定碳、挥发性有机氯含量、硫含量、重金属等项目,建立颗粒状废活性炭的工业分析和污染特性数据库,为后续工艺配伍和再生运行工艺提供基础数据;步骤3:对相同或类似种类、形态、粒径、产废工艺的颗粒状废活性炭进行综合配伍,确定需再生的颗粒状废活性炭的批次和数量,均化废活性炭的热解特性、酸性污染物及重金属含量,初步确定热解再生工艺条件和运行参数,提高废活性炭的再生效果和再生活性炭的品质,便于再生活性炭的定向销售和回用;步骤4:颗粒状废活性炭通过机械筛分设备去除金属、塑料、石块、混凝土等杂物,再经磁选设备进一步去除小颗粒的金属机械杂质;步骤5:启动逆流式回转窑辅助燃烧器(包括辅助燃烧器助燃风机),逆流式回转窑开始升温;当逆流式回转窑窑头温度达到1000℃时,调整辅助燃烧器功率(辅助燃料流量和燃烧器助燃风流量),使窑头温度维持在1000℃;步骤6:启动二燃室辅助燃烧器(包括辅助燃烧器助燃风机),二燃室开始升温;当二燃室温度达到1100℃时,调整二燃室辅助燃烧器功率(辅助燃料流量和燃烧器助燃风流量),使二燃室温度维持在1100℃;步骤7:预处理后的颗粒状废活性炭经螺旋进料装置匀速输送至逆流式回转窑进行热解再生,颗粒状废活性炭在不同的时间和空间上依次经历低温干燥、中低温热解、高温热解和高温气化等四个阶段;干燥阶段主要去除废活性炭吸附的水分;各种性质不同的有机物吸附质在窑内的不同部位和温度区间受热发生中低温热解、高温热解,产生气体小分子有机物、co2、co和h2o而形成再生烟气,热解阶段使得废活性炭恢复部分吸附性能;有机物吸附质的热解阶段同时会缩聚产生固体半焦而残留在废活性炭孔隙中,成为影响废活性炭孔隙结构和再生吸附性能的关键因素;废活性炭孔隙中的热解半焦经水蒸气高温气化而去除,实现废活性炭孔隙结构的彻底清理和部分再造;步骤8:启动二燃室助燃风机,调整二燃室助燃风的流量,平衡调整二燃室辅助燃烧器,以维持二燃室温度≥1100℃,二燃室出口烟气的氧含量维持在6%~10%,确保逆流式回转窑热解再生过程产生的烟气在二燃室内完全燃烧,废活性炭热解再生过程无二噁英产生;步骤9:随着逆流式回转窑的转动,颗粒状废活性炭沿回转窑轴线方向不断前进;当废活性炭运动至回转窑中部位置时,启动双流体喷枪向逆流式回转窑内喷入雾化水;雾化水在1000℃高温条件下瞬间汽化成水蒸气,水蒸气与残留在活性炭孔隙中的热解半焦发生气化反应,从而实现热解半焦的彻底去除和活性炭孔隙结构的部分再造,全面恢复活性炭的吸附性能;
步骤10:启动水冷螺旋出料装置,保证再生活性炭及时从逆流式回转窑的窑头罩处排出;步骤11:启动机械筛分装置,再生活性炭按粒径大小进行分类,同步检测再生活性炭的碘值和强度,满足标准后对不同类别的再生活性炭进行分类包装;步骤12:二燃室出口的1100℃高温烟气经余热回收(含sncr脱硝)、急冷降温、干法脱酸、活性炭吸附、布袋除尘、两级湿法脱酸、ggh烟气换热后,由引风机加压经烟囱排入大气;步骤13:缓慢平稳调整螺旋进料装置的运行频率,提高进料速率,提高逆流式回转窑的再生负荷;同步调整逆流式回转窑的其他工艺参数,使再生过程始终保持在稳定状态;步骤14:根据螺旋进料装置的运行频率(即进料速率),平稳调整逆流式回转窑的辅助燃烧器(辅助燃料流量和燃烧器助燃风流量),使逆流式回转窑的运行温度满足不同种类、来源的活性炭的再生温度要求,使逆流式回转窑的热解再生烟气的氧含量、co含量和ch4含量分别控制在0.1%~0.5%、5%~12%、1%以内;步骤15:根据螺旋进料装置的运行频率(即进料速率),平稳调整逆流式回转窑的驱动变频电机的运行频率(即调整回转窑转速),满足不同成分、不同热解特性的有机物吸附质的热解时间要求,彻底去除有机吸附质,提高再生活性炭的吸附性能;步骤16:根据螺旋进料装置的运行频率(即进料速率),平稳调整窑头罩处双流体喷枪的雾化水流量,确保废活性炭孔隙中残留的热解半焦完全气化去除,同时实现废活性炭孔隙结构的部分再造,从而全面恢复废活性炭的吸附性能;步骤17:综合考虑不同种类、来源的废活性炭、有机吸附质的热解特性及废活性炭的挥发份检测数据,优化确定双流体喷枪的雾化水流量,从而平衡废活性炭再生后的吸附性能和再生过程所需的能耗;步骤18:根据废活性炭的种类、热解特性、化验分析数据,结合再生活性炭的吸能性能、炭损失及强度等检测数据,不断优化废活性炭的热解再生温度、逆流式回转窑燃烧器的辅助燃料流量、逆流式回转窑燃烧器的助燃风流量、逆流式回转窑驱动电机的运行频率(热解再生时间)、热解再生烟气的氧含量、废活性炭的进料频率(进料速率)、雾化水流量、热解再生烟气的co含量、热解再生烟气的ch4含量等工艺条件和运行参数,实现再生效率与吸附性能、强度之间的最佳平衡。
7.进一步地,所述步骤3中的配伍指标为水份~30%、挥发份~15%、固定碳~60%、灰份~10%、有机氯~4%、总硫~4%。
8.进一步地,所述步骤5中的辅助燃烧器设置在逆流式回转窑的窑头罩,采用分体式结构;所述步骤5中的燃烧器助燃风机采用变频控制;所述步骤5中的辅助燃料设置远程流量计和流量调节阀;所述步骤5中的燃烧器助燃风设置远程流量计和流量调节阀。
9.进一步地,所述步骤5中的逆流式回转窑的窑头温度为窑头罩远程热电偶温度计的测量值。
10.进一步地,所述步骤6中的二燃室辅助燃烧器设置在二燃室1100℃高温段的底部,采用分体式结构;所述步骤6中的燃烧器助燃风机采用变频控制;所述步骤6中的燃烧器辅助燃料设置远程流量计和流量调节阀;所述步骤6中的燃烧器助燃风设置远程流量计和流量调节阀。
11.进一步地,所述步骤6中的二燃室温度为二燃室高温段的上断面远程热电偶温度计的测量值、二燃室高温段的下断面远程热电偶温度计的测量值,且上断面和下断面的温度均≥1100℃时即可判定为二燃室温度达到1100℃。
12.进一步地,所述步骤7中的螺旋进料装置采用无轴螺旋结构,螺旋进料装置设置在线自动计量秤,螺旋进料装置的驱动电机采用变频控制,实现颗粒状废活性炭的进料速率调整。
13.进一步地,所述步骤7中的螺旋进料装置与逆流式回转窑的窑尾罩连接。
14.进一步地,所述步骤7中的逆流式回转窑的中轴线与水平线的夹角为1
°
~5
°
。
15.进一步地,所述步骤7中的低温干燥温度范围在150℃以内,中低温热解温度范围在150℃~600℃,高温热解温度范围在600℃~800℃,高温气化温度范围在800℃~1000℃。
16.进一步地,所述步骤7中的再生烟气经逆流式回转窑的窑尾罩的烟气出口管道排出。
17.进一步地,所述步骤8中的二燃室为立式圆筒形结构。
18.进一步地,所述步骤8中的二燃室助燃风机采用变频控制;所述步骤8中的二燃室助燃风设置远程流量计和流量调节阀。
19.进一步地,所述步骤8中的二燃室出口烟气的氧含量为远程氧化锆型氧气测量仪的测量值,远程氧化锆型氧气测量仪位于二燃室烟气出口的水平段烟道上。
20.进一步地,所述步骤8中的逆流式回转窑的再生烟气从二燃室底部的烟气进口进入。
21.进一步地,所述步骤9中的双流体喷枪采用压缩空气雾化的脱盐水喷枪,脱盐水的电导率<1μs/cm。
22.进一步地,所述步骤9中的双流体喷枪设置压缩空气远程压力表、压力调节阀和远程流量计。
23.进一步地,所述步骤9中的双流体喷枪设置脱盐水远程压力表,远程流量计和流量调节阀。
24.进一步地,所述步骤9中的雾化水的粒径为30μm。
25.进一步地,所述步骤10中的水冷螺旋出料装置设置循环冷却水夹套结构;所述步骤10中的水冷螺旋出料装置通过两级气动插板阀与逆流式回转窑的窑头罩底部连接。
26.进一步地,所述步骤10中的机械筛分装置配置不同目数的筛网,实现不同粒径的再生活性炭的分离。
27.进一步地,所述步骤14中的颗粒状废活性炭逆流式回转窑的热解再生烟气中的氧含量、co含量和ch4含量分别为氧量仪、co测量仪、ch4测量仪对应的在线测量值,氧量仪、co测量仪、ch4测量仪设置在逆流式回转窑烟气出口管道的水平段上。
28.进一步地,所述步骤15中的逆流式回转窑的驱动变频电机可调整逆流室回转窑的转速,逆流室回转窑的转速范围为0.4~4rpm,使颗粒状废活性炭再生时间控制在60min~90min。
29.进一步地,所述步骤16中的双流体喷枪的雾化水流量为0.1kg~0.5kg脱盐水/1kg颗粒状废活性炭。
30.进一步地,所述步骤18中的再生效率为0.4kg~0.6kg再生活性炭/1kg颗粒状废活
性炭。
31.进一步地,所述步骤18中的吸附性能为经再生后活性炭的碘值≥800mg/g。
32.进一步地,所述步骤18中的强度为再生后活性炭的强度≥80%。
33.本发明的工作原理:本发明使用时,逆流式回转窑呈卧式倾斜布置,颗粒状废活性炭经机械筛分设备去除金属、塑料、石块、混凝土等杂物,再经磁选设备进一步去除小颗粒的金属机械杂质后,由螺旋进料装置将颗粒状废活性炭匀速输送至逆流式回转窑热解再生炉;在回转窑内废活性炭与高温水蒸气、co2等气化剂逆流接触,实现有机物吸附质的热解气化,去除活性炭孔隙结构表面和孔隙内部的有机物,达到恢复废活性炭孔隙结构和吸附性能的目的。在逆流式回转窑辅助燃烧器的辅助加热作用下,沿回转窑轴线方向运动的废活性炭依次经历干燥、中低温热解、高温热解、高温气化等四个阶段,分别去除活性炭吸附的水分、挥发性有机物、低沸点有机物、高沸点有机物、难分解有机物及挥发性重金属;有机物吸附质的中低温和高温热解阶段会缩聚产生固体半焦而残留在活性炭孔隙中,成为影响再生活性炭孔隙结构和吸附性能的关键因素;在废活性炭热解再生过程中,通过逆流式回转窑窑头罩的双流体喷枪向炉内喷入30μm雾化状水颗粒,颗粒水在高温作用下急速汽化成水蒸汽,残留在活性炭孔隙中的热解半焦由于水蒸气的气化作用而得以去除,从而实现废活性炭孔隙结构的彻底清理和部分再造,全面恢复活性炭的吸附性能,同时避免活性炭基质的高温氧化烧蚀,降低活性炭的炭基质损失,减轻活性炭强度的下降。再生活性炭经水冷螺旋装置冷却输送至炉外,经机械筛分、检测、包装后外售。废活性炭在逆流式回转窑热解再生过程产生的烟气经二燃室充分燃烧后,依次经余热回收、sncr脱硝、急冷降温、干法脱酸、活性炭吸附、布袋除尘、两级湿法脱酸、ggh烟气换热等烟气净化处理后,由引风机排入大气。
34.采用上述技术工艺方案后,本发明得到的显著效果是:1、本发明适合再生利用的颗粒状废活性炭的物料范围广,除粉末状、蜂窝状废活性炭外,均可采用本发明进行再生循环利用;2、本发明可现实不同种类、来源的颗粒状废活性炭再生的吸附性能、再生效率和再生强度的平衡,其再生活性炭的吸附性能(如碘值)、再生效率和强度,显著优于目前已有的活性炭热再生技术的再生效果;3、本发明提供的颗粒状废活性炭热解再生技术的过程调控强,工艺控制方案完善,自动化程度高,再生作业率高;4、本发明提供的颗粒状废活性炭热解再生的技术机理清晰,有利于颗粒状废活性炭热解再生装备的大型化应用和推广,有利于种类多、数量少、来源广的颗粒状废活性炭的集中再生利用,提高活性炭的循环使用效率、环境效益和经济效益,进一步推动活性炭的普及应用和产业绿色发展,满足国家减污降碳的政策要求。
附图说明
35.为了更清楚地说明本发明实施例或现有技术中的技术方案,下面将对实施例或现有技术描述中所需要使用的附图作简单地介绍,显而易见地,下面描述中的附图仅仅是本发明的一些实施例,对于本领域普通技术人员来讲,在不付出创造性劳动性的前提下,还可以根据这些附图获得其他的附图。
36.图1为本发明提供的一种颗粒状废活性炭逆流式回转窑热解再生工艺的一种具体实施的原理结构图。
37.图2为本发明提供的一种颗粒状废活性炭逆流式回转窑热解再生工艺的工艺流程示意图。
38.图中:1-逆流式回窑、101-窑头罩、102-窑尾罩、2-螺旋进料装置、3-烟气出口管道、4-ch4测量仪、5-co测量仪、6-氧量仪、7-辅助燃烧器、701-燃烧器助燃风机、8-双流体喷枪、9-两级气动插板阀、10-水冷螺旋出料装置。
具体实施方式
39.为使本发明的目的、技术方案和优点更加清楚,下面将对本发明的技术方案进行详细的描述。显然,所描述的实施例仅仅是本发明一部分实施例,而不是全部的实施例。基于本发明中的实施例,本领域普通技术人员在没有做出创造性劳动的前提下所得到的所有其它实施方式,都属于本发明所保护的范围。
40.参考图1、图2所示,本具体实施方式采用的技术方案是:它包含以下步骤:步骤1:对来自不同产废企业的废活性炭,按原生活性炭的种类、形态、尺寸及废活性炭的产生工艺进行综合分类,如煤质破碎活性炭、颗粒状活性炭、柱状活性炭、挥发性有机物vocs治理活性炭、污水处理生物活性炭、净水活性炭、催化剂载体活性炭等;步骤2:对来自不同产废企业、不同产废工艺工序的颗粒状废活性炭进行化验分析,检测含水量、挥发份、灰份、固定碳、挥发性有机氯含量、硫含量、重金属等项目,建立颗粒状废活性炭的工业分析和污染特性数据库,为后续配伍和再生运行工艺提供基础数据;颗粒状废活性炭的化验分析数据有利于提高配伍的调节均化效果,能有效提高逆流式回转窑热解再生的工艺条件和运行参数的稳定性,能有效提高再生烟气净化系统的工况稳定性,有助于延长整体设施的运行使用寿命;步骤3:对相同或类似种类、形态、粒径、产废工艺的颗粒状废活性炭进行综合配伍,确定需再生的颗粒状废活性炭的批次和数量,均化废活性炭吸附的有机物种类和热解特性、酸性污染物及重金属含量,初步确定热解再生工艺条件和运行参数,提高废活性炭的再生效果和再生活性炭的品质,便于再生活性炭的定向销售和回用;优先对相同或相近来源、工艺、规格的颗粒状废活性炭进行同批次处理,使热解再生工艺条件和工艺参数趋于稳定,提高再生活性炭的品质;步骤4:颗粒状废活性炭通过机械筛分设备去除金属、塑料、石块、混凝土等杂物,再经磁选设备进一步去除小颗粒的金属机械杂质;经过机械筛分和磁选,去除绝大部分与颗粒状废活性炭混合的杂质,提高逆流式回转窑热解再生的设备稳定性和效率;步骤5:启动逆流式回转窑1窑头罩101处的辅助燃烧器7(包括燃烧器助燃风机701),逆流式回转窑1开始升温;当逆流式回转窑1窑头温度达到1000℃时,调整辅助燃烧器7功率(调整辅助燃料流量和燃烧器助燃风流量),使窑头温度维持在1000℃;步骤6:启动二燃室辅助燃烧器(包括燃烧器助燃风机),二燃室开始升温;当二燃室温度达到1100℃时,调整二燃室辅助燃烧器功率(调整辅助燃料流量和燃烧器助燃风流量),使二燃室温度维持在1100℃;逆流式回转窑产生的烟气在二燃室1100℃高温段的有效停留时间大于2秒,保证热解再生过程无二噁英产生;
步骤7:预处理后的颗粒状废活性炭经螺旋进料装置2匀速输送,由窑尾罩102进入逆流式回转窑1进行热解再生;废活性炭在逆流式回转窑内部不同的时间和空间顺序上,依次经历低温干燥、中低温热解、高温热解和高温气化等四个阶段;干燥阶段主要去除废活性炭吸附的自由基水分;各种性质不同的有机物吸附质在窑内的不同部位和温度区间受热发生中低温热解、高温热解,产生气体小分子有机物、co2、co和h2o而形成再生烟气,热解阶段使得废活性炭恢复部分吸附性能;有机物吸附质的热解阶段同时会缩聚产生固体半焦而残留在活性炭孔隙中,成为影响废活性炭孔隙结构和再生吸附性能的关键因素;废活性炭孔隙中的热解半焦经水蒸气高温气化而去除,实现废活性炭孔隙结构的清理和部分再造;步骤8:启动二燃室助燃风机,调整二燃室助燃风风量,平衡调整二燃室辅助燃烧器,以维持二燃室温度≥1100℃,二燃室出口烟气的氧含量保持在6%~10%,确保逆流式回转窑热解再生过程产生的烟气在二燃室内完全燃烧,废活性炭热解再生过程无二噁英产生;步骤9:随着逆流式回转窑的转动,颗粒状废活性炭沿回转窑轴线方向不断前进;当废活性炭运动至回转窑1中部位置时,启动窑头罩101处的双流体喷枪8向逆流式回转窑1内喷入雾化水,雾化水在1000℃高温条件下瞬间汽化成水蒸气,水蒸气与在步骤7废活性炭孔隙中的热解半焦发生高温气化反应,从而实现热解半焦的彻底去除和活性炭孔隙结构的部分再造,全面恢复活性炭的吸附性能;窑头温度(即1000℃热解再生温度)通过与窑头罩101处的辅助燃烧器7的双回路控制(温度和辅助燃料流量两个控制回路),实现自动控制调整;步骤10:启动水冷螺旋装置10,保证再生活性炭及时从逆流式回转窑1窑头罩101处排出;水冷螺旋装置通过两级气动插板阀9与逆流式回转窑1窑头罩101底部连接;步骤11:启动机械筛分装置,按粒径大小进行分类,同步检测再生活性炭的碘值和强度,满足标准后对不同类别的再生活性炭进行分别包装;根据粒径大小、检测的碘值及强度值,按不同行业及客户需求的活性炭性能参数进行匹配、分类和包装,针对性地开展再生活性炭的销售;步骤12:二燃室出口的1100℃高温烟气经余热回收(含sncr脱硝)、急冷降温、干法脱酸、活性炭吸附、布袋除尘、两级湿法脱酸、ggh烟气换热后,由引风机加压经烟囱排入大气;1100℃高温烟气自二燃室出口进入全膜式壁余热锅炉进行余热回收利用(蒸气生产及蒸汽发电);在全膜式壁余热锅炉高温段(850℃-1100℃)设置sncr脱硝装置,通过双流体喷枪计量喷射10%尿素溶液,使烟气中的no
x
被选择性非催化还原为n2,脱硝效率不低于40%;经余热回收后的烟气降温至~550℃,550℃烟气进入急冷装置进行急冷降温处理,急冷水经泵送至急冷塔顶部的双流体喷枪,急冷水经压缩空气雾化成30μm的小颗粒雾状水后喷入急冷塔内,与急冷塔顶部进入的烟气顺流接触、换热和汽化,使雾状水在1秒钟内完全汽化成水蒸气,使烟气在1秒内快速降温至200℃,从而使烟气避开二噁英再合成的温度区间(500℃~200℃),防止二噁英的再合成;急冷后的烟气进入干法脱酸装置,烟气中的hcl、so2、hf等酸性气体与消石灰喷射装置喷射的消石灰发生中和反应,酸性气体去除率不小于20%,活性炭喷射装置喷射的粉末状活性炭吸附去除烟气中的二噁英及部分挥发性重金属;烟气经干法脱酸后进入布袋除尘装置,烟气中的颗粒物经ptfe+ptfe覆膜的滤袋的截留过滤而去除,大部分难挥发性重金属在300℃以下以固体形式存在,与颗粒物凝聚在一起而被布袋除尘装置去除,经布袋除尘后烟气的颗粒物含量小于10mg/m3;布袋除尘装置烟气出口温度约170
℃~180℃,为充分利用烟气余热,采用ggh烟气换热器实现高温烟气和低温烟气换热,除尘后的高温原烟气进入ggh烟气换热器的管程,两级湿法脱酸后的低温净烟气经引风机加压进入ggh烟气换热器的壳程,使得高温原烟气得以降温(降至~100℃)从而满足湿法脱酸的温度要求,低温净烟气得以升温(升至~140℃)从而满足烟气“消白”目的;经ggh烟气换热器降温的原烟气依次进入一级湿法脱酸塔和二级湿法脱酸塔,烟气自下而上与湿法脱酸塔顶部喷淋的循环碱液逆流接触并发生中和反应,使得烟气中的绝大部分酸性气体得以去除,湿法脱酸效率可达99%;大部分汞等饱和蒸汽压较高的挥发性重金属以气态形式存在于烟气中,烟气中的汞可与hcl反应,80%~90%转化为hgcl2,hgcl2为水溶性化合物,在湿法脱酸过程中hgcl2与循环碱液反应而去除,满足《危险废物焚烧污染控制标准》(gb18484)的排放限值要求;两级湿法脱酸后的低温净烟气(~70℃)经引风机加压进入ggh换热器加热消白,再经烟囱排入大气;步骤13:缓慢平稳调整螺旋进料装置2的运行频率,提高进料速率,提高逆流式回转窑的再生负荷;同步调整逆流式回转窑1的其他工艺参数,使再生过程始终保持在稳定状态;步骤14:根据螺旋进料装置2的运行频率(即进料速率),平稳调整逆流式回转窑1窑头罩101处的辅助燃烧器7的功率(辅助燃料流量和燃烧器助燃风流量),使逆流式回转窑1的运行温度满足不同种类、来源的颗粒状废活性炭的热解再生温度要求,使逆流式回转窑1烟气出口管道3处的氧量仪6、co测量仪5、ch4测量仪4的实时检测值别控制在0.1%~0.5%、5%~12%、1%以内,最大程度降低活性炭基质的氧化烧蚀,提高再生活性炭的强度,提高逆流式回转窑在热解工艺条件下的可靠性;步骤15:根据螺旋进料装置2的运行频率(即进料速率),平稳调整逆流式回转窑1驱动变频电机的频率(即调整回转窑转速),满足不同种类、来源的颗粒状废活性炭的再生时间要求,满足不同成分、不同热解特性的有机物吸附质的热解时间要求,彻底去除有机吸附质,提高再生活性炭的吸附性能;步骤16:根据螺旋进料装置2的运行频率(即进料速率),平稳调整逆流式回转窑1窑头罩101处双流体喷枪7的雾化水流量,确保废活性炭孔隙中残留的热解半焦完全气化去除,同时实现废活性炭孔隙结构的部分再造,从而全面恢复废活性炭的吸附性能;步骤17:综合考虑不同种类、来源的废活性炭、有机吸附质的热解特性及废活性炭的挥发份检测数据,优化双流体喷枪8的雾化水流量,从而平衡废活性炭再生后的吸附性能和再生过程所需的能耗;步骤18:根据废活性炭的种类、热解特性、化验分析数据,结合再生活性炭的吸能性能、炭损失及强度等检测数据,不断优化颗粒状废活性炭的螺旋进料装置2的运行频率(即进料速率)、热解再生温度、辅助燃烧器7功率(辅助燃料流量、助燃风流量)、逆流式回转窑1驱动变频电机的频率(再生时间)、双流体喷枪8的雾化水流量、氧量仪6的烟气氧含量、co测量仪5的烟气co含量、ch4测量仪4的ch4含量等工艺条件和运行参数,实现再生效率与吸附性能、强度之间的最佳平衡。
41.所述步骤3中的配伍指标为水份≤30%、挥发份≤15%、固定碳≤60%、灰份≤10%、有机氯≤4%、总硫≤4%。
42.所述步骤5中的辅助燃烧器7设置在逆流式回转窑1的窑头罩101,采用分体式结
构;所述步骤5中的燃烧器助燃风机701采用变频控制;所述步骤5中的辅助燃料设置远程流量计和流量调节阀;所述步骤5中的燃烧器助燃风设置远程流量计和流量调节阀。
43.所述步骤5中的逆流式回转窑1的窑头温度为窑头罩101远程热电偶温度计的测量值,通过此温度与窑头辅助燃烧器7的辅助燃料流量形成双回路控制;所述步骤5中的窑头辅助燃烧器7设置辅助燃料流量控制回路、助燃风流量控制回路;所述步骤5中的辅助燃料流量与助燃风流量设置比例控制回路;提高热解再生温度控制的精确度和稳定性,确保逆流式回转窑1的窑头温度(即热解再生温度)满足不同种类、来源活性炭的热解再生温度要求。
44.所述步骤6中的二燃室辅助燃烧器设置在二燃室1100℃高温段的底部,采用分体式结构;所述步骤6中的燃烧器助燃风机采用变频控制;所述步骤6中的辅助燃料设置远程流量计和流量调节阀;所述步骤6中的燃烧器助燃风设置远程流量计和流量调节阀。
45.所述步骤6中的二燃室温度为二燃室高温段的上断面远程热电偶温度计的测量值、二燃室高温段的下断面远程热电偶温度计的测量值,且上断面和下断面的温度均≥1100℃时即可判定为二燃室温度达到1100℃,满足《危险废物焚烧污染控制标准》(gb18484)的要求,确保无二噁英产生。
46.所述步骤7中的螺旋进料装置2采用无轴螺旋结构,螺旋进料装置2设置在线自动计量秤,螺旋进料装置2的驱动电机采用变频控制,实现颗粒状废活性炭的进料速率调整,确保逆流式回转窑1内热解再生工艺的稳定运行。
47.所述步骤7中的螺旋进料装置2与逆流式回转窑1窑尾罩102连接。
48.所述步骤7中的逆流式回转窑1的中轴线与水平线的夹角为3
°
。
49.所述步骤7中的低温干燥温度范围在150℃以内,中低温热解温度范围在150℃~600℃,高温热解温度范围在600℃~800℃,高温气化温度范围在800℃~1000℃。
50.所述步骤7中的再生烟气经逆流式回转窑1窑尾罩102的烟气出口管道3排出。
51.所述步骤8中的二燃室为立式圆筒形结构。
52.所述步骤8中的二燃室助燃风机采用变频控制;所述步骤8中的二燃室助燃风设置远程流量计和流量调节阀。
53.所述步骤8中的二燃室出口烟气的氧含量为远程氧化锆型氧气测量仪的测量值,远程氧化锆型氧气测量仪位于二燃室烟气出口的水平段烟道上。
54.所述步骤8中的逆流式回转窑1的再生烟气从二燃室底部的烟气进口进入。
55.所述步骤9中的双流体喷枪8采用压缩空气雾化的脱盐水喷枪,其中脱盐水的电导率<1μs/cm,可以最大限度地降低钙、镁离子的浓度,进而降低水的硬度,防止喷枪堵塞,降低检修频率;同时降低废活性炭热解再生过程中盐分对炭基质的催化烧蚀,减少再生活性炭的杂质污染。
56.所述步骤9中的双流体喷枪8设置压缩空气远程压力表、压力调节阀和远程流量计。
57.所述步骤9中的双流体喷枪8设置脱盐水远程流量计、流量调节阀和远程压力表。
58.所述步骤9中的雾化水的粒径为30μm。
59.所述步骤10中的水冷螺旋出料装置9设置循环冷却水夹套结构,循环冷却水的进水温度≤40℃;所述步骤10中的水冷螺旋出料装置9通过两级气动插板阀10与逆流式回转
窑1的窑头罩101底部连接,方便拆卸及检修。
60.所述步骤10中的机械筛分装置配置不同目数的筛网,实现不同粒径再生活性炭的分类,满足不同行业及用户的活性炭使用规格要求。
61.所述步骤14中的氧、co和ch4含量分别为氧量仪6、co测量仪5、ch4测量仪4对应的实现在线测量值,氧量仪6、co测量仪5、ch4测量仪4设置在逆流式回转窑1烟气出口管道3的水平段上;通过检测烟气中的氧含量、co含量和ch4含量,可优化调整逆流式回转窑1的热解再生温度、逆流式回转窑1辅助燃烧器7的助燃风流量,提高再生活性炭的吸附性能,降低炭基质损失和再生能耗。
62.所述步骤15中的逆流式回转窑1驱动变频电机为调整逆流室回转窑的转速,逆流室回转窑1转速范围为0.4~4rpm,使颗粒状废活性炭再生时间控制在60min~90min。
63.所述步骤16中的双流体喷枪8的雾化水流量为0.1kg~0.5kg脱盐水/1kg废活性炭。
64.所述步骤18中的再生效率为0.4kg~0.6kg再生活性炭/1kg废活性炭。
65.所述步骤18中的吸附性能为经再生后活性炭的碘值≥800mg/g。
66.所述步骤18中的强度为再生后活性炭的强度≥80%。
67.本实施例的工作原理:本发明使用时,逆流式回转窑呈倾斜布置,颗粒状废活性炭经机械筛分设备去除金属、塑料、石块、混凝土等杂物,再经磁选设备进一步去除小颗粒的金属机械杂质后,由螺旋进料装置将颗粒状废活性炭匀速输送至逆流式回转窑再生炉;在回转窑内废活性炭与高温水蒸气、co2等气化剂逆流接触,实现有机物吸附质的热解气化,去除活性炭孔隙结构表面和孔隙内部的有机物,达到恢复废活性炭孔隙结构和吸附性能的目的。在逆流式回转窑的窑头燃烧器的辅助加热作用下,沿回转窑轴线方向运动的废活性炭依次经历干燥、中低温热解、高温热解、高温气化等四个阶段,分别去除活性炭吸附的水分、挥发性有机物、低沸点有机物、高沸点有机物、难分解有机物及挥发性重金属;有机物吸附质的中低温和高温热解阶段会缩聚产生固体半焦而残留在活性炭孔隙中,成为影响再生活性炭孔隙结构和吸附性能的关键因素;在废活性炭热解再生过程中,通过逆流式回转窑窑头罩的双流体喷枪向炉内喷入30μm雾化状水颗粒,颗粒水在高温作用下急速汽化成水蒸汽,残留在活性炭孔隙中的热解半焦由于水蒸气的气化作用而得以去除,从而实现废活性炭孔隙结构的彻底清理和部分再造,全面恢复活性炭的吸附性能,同时避免活性炭基质的高温氧化烧蚀,降低活性炭的炭基质损失,减轻活性炭强度的下降。再生活性炭经水冷螺旋装置冷却输送至炉外,经机械筛分、检测、包装后外售。废活性炭再生过程产生的烟气经二燃室充分燃烧后依次经余热回收、sncr脱硝、急冷降温、干法脱酸、活性炭吸附、布袋除尘、两级湿法脱酸、ggh烟气换热等烟气净化处理后,由引风机排入大气。
68.采用上述技术方案后,本实施例有益效果为:1、本发明适合再生利用的颗粒状废活性炭的物料范围广,除粉末状、蜂窝状废活性炭外,其他颗粒状废活性炭均可采用本发明进行再生循环利用;2、本发明可现实不同种类、来源的废活性炭再生的吸附性能、再生效率和再生强度的平衡,其再生活性炭的吸附性能(如碘值)、收率和强度,显著优于目前已有的活性炭热解再生技术的再生效果;3、本发明提供的废活性炭热解再生技术的过程调控强,工艺控制方案完善,自动
化程度高,再生作业率高;4、本发明提供的废活性炭热解再生技术的再生反应机理清晰,有利于废活性炭热解再生装备的大型化应用和推广,有利于种类多、数量少、来源广的废活性炭的集中再生利用,提高活性炭的循环使用效率、环境效益和经济效益,进一步推动活性炭的普及应用和产业绿色发展,满足国家减污降碳的政策要求。
69.以上所述,仅用以说明本发明的技术方案而非限制,本领域普通技术人员对本发明的技术方案所做的其它修改或者等同替换,只要不脱离本发明技术方案的精神和范围,均应涵盖在本发明的权利要求范围当中。