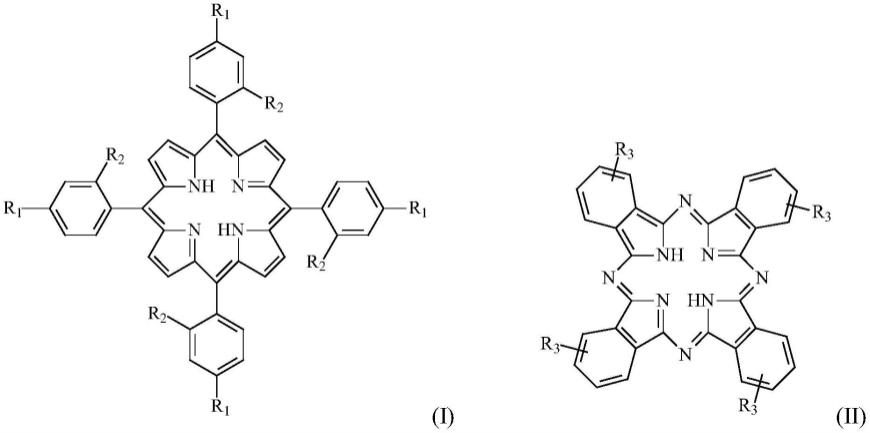
1.本发明涉及废水除氯技术领域,尤其涉及一种铋基吸附除氯材料及其制备方法和应用。
背景技术:2.去除水溶液中含氯盐的方法有离子交换法、难溶盐沉淀法、电化学法、层状氧化物法、真空蒸馏法、膜分离法、热处理法和溶剂萃取法等。这些方法大多存在过程复杂、高耗能、二次污染等缺点和限制条件。沉淀法工艺简单,但去除率低,污泥需要处理;吸附法反应时间较长,易受温度、竞争离子、氯离子浓度等影响,而且吸附剂回收困难;膜分离法工业应用较多,但成本高,易发生堵塞污染问题;电化学法效率高,但耗能大。由于含氯盐存在形态各异,因此不同的除氯技术措施各有其适合应用的场合。
3.氯离子是氯存在的稳定形态,不能被微生物同化或分解,氯化物大多易溶,因此很难除去。氯离子对于工业生产、金属设备以及钢筋混凝土都有着明显的危害。含氯废水改变土壤结构,导致碱化盐渍化,对植物幼苗和农作物的生长具有抑制作用。高浓度的氯化物对人类健康十分不利。淡水资源和废水中的氯离子过高也会对生产生活和经济发展带来损失。由此可见,人民生活、生态环保和国民经济发展需要不同层次和性能指标的除氯技术。针对工业废水处理,为有利于废水回用,避免引入杂质,防止出现氧化还原副反应,本发明提供一种使用简便、耗能低、不引入杂质、没有二次污染的铋基吸附除氯材料及其制备方法。
4.铋基除氯剂在冶金工艺已经获得工业化应用。铋基吸附材料可以有效除去水溶液中的离子型污染物,例如硝酸盐、氟氯离子、砷离子等,因此获得科技界普遍关注,相关文献报道较多。cn110357239a中利用含量大于95%的氧化铋作为含氯溶液的除氯剂,除氯剂的用量为氯离子含量的15-20倍。氧化铋尺寸大,溶出慢,限制了其除氯的效率,而且必须在过量的情况下才能达到有效除氯的的目的。cn104479056b将聚异丁烯丁二酸酐的矿物油溶液在氮气保护下与硝酸铋反应,制备得到高分子有机铋化合物作为除氯剂。但是除氯效率仍不够理想。cn114835233a公开了一种铋基金属有机框架材料用于快速去除废水中氯离子,其实将铋盐、均苯三甲酸,ctab制备得到铋基mofs材料,用于除去废水中的氯。利用了mofs材料较大的比表面积,孔道作为氯离子的穿梭通道,在酸性条件下结构快速坍塌,提高铋和氯离子的反应。该专利方法除氯迅速,1min可以除氯达到78.8%,10min达到85.3%。但是mofs材料制备复杂,成本高昂,不适合工业化的生产和应用。
技术实现要素:5.本发明通过如下技术方案实现:
6.一种铋基吸附除氯材料,为核-壳结构,核为无机微粒,壳为氮掺杂的炭包覆层,铋(氧化铋或者铋盐)均匀分散在氮掺杂的炭包覆层中。
7.进一步地,壳的原料包括含氮配体,含氮助剂,以及铋源,所述含氮配体为原卟啉
或其衍生物,以及酞菁或其衍生物;卟啉的衍生物包括血卟啉、叶绿素,取代的5,10,15,20-四苯基卟啉。
8.优选地,含氮配体,含氮助剂,以及金属铋源的质量比为12-18:5-9:2-4。
9.本发明是通过将含氮配体,含氮助剂,以及金属铋源在一起混合后,再加入无机微粒,混匀后经过预热和烧结,在无机微粒表面形成氮掺杂的碳层,在碳层中均匀分散有铋。
10.更进一步地,所述取代的5,10,15,20-四苯基卟啉结构式如式(i)所示,所述酞菁衍生物结构式如式(ii)所示:
[0011][0012]
r1,r2,r3独立地选自h、nh2、no2、nco、cn、oh。
[0013]
优选地,式(i)化合物中,同一个苯环上的r1,r2中一个为h,另一个选自nh2、no2、oh、nco;式(ii)化合物中,r3不同时为h。
[0014]
更优选地,所述卟啉衍生物选自四(邻氨基苯基)卟啉、四(对氨基苯基)卟啉、四(对氰基苯基)卟啉、四(对硝基苯基)卟啉、四(邻异氰酸酯基苯基)卟啉、四(对异氰酸酯基苯基)卟啉、四(对羟基苯基)卟啉中的至少一种;所述酞菁衍生物选自α-四硝基酞菁、α-四氨基酞菁、β-四氨基酞菁、β-四异氰酸酯基酞菁、α-四羟基酞菁中的至少一种。
[0015]
优选地,所述含氮配体为卟啉或其衍生物,与酞菁或其衍生物按照摩尔比1-3:1-3的复配。更优选地,所述含氮配体为卟啉或其衍生物,与酞菁或其衍生物按照摩尔比1-1.5:1-1.5的复配。卟啉衍生物和酞菁衍生物一起作用,能够形成多层三明治型的多层铋配合的结构,进而使铋更加均匀、稳定地分散,从而达到更好的除氯效果。
[0016]
进一步地,所述含氮助剂选自壳聚糖、三聚氰胺、尿素中的至少一种,所述铋源选自氧化铋、硝酸铋、氢氧化铋中的至少一种。
[0017]
进一步地,所述无机粒子包括活性炭、玻璃颗粒、陶瓷颗粒、石英砂、二氧化钛、膨润土、多孔性二氧化硅、粉煤灰、石灰石粉中的至少一种;无机微粒的粒径为0.5-10mm。活性炭比表面积大,能够在表面形成更多的和氯反应的活性位点,因此除氯效果更好,但是活性炭强度较低;陶瓷颗粒比重大,强度高,适合用于废水处理中流动床,或者层析柱的填料。
[0018]
进一步地,无机微粒和壳的原料(氮配体,含氮助剂,以及铋源的总和)质量比为10-40倍;优选地,当无机微粒为活性炭时,无机微粒和壳的原料质量比为10-15:1;当无机微粒为玻璃颗粒或陶瓷颗粒时,无机微粒和壳的原料质量比为30-40:1。活性炭比表面积
大,能够在较小用量下完成铋基吸附除氯材料的制备。
[0019]
本发明还提供了所述铋基吸附除氯材料的其制备方法,包括以下步骤:
[0020]
将含氮配体溶解或分散在水溶性有机溶剂中,得到第一混合物;将含氮助剂溶解或分散水中,加入铋源,球磨,得到第二混合物;无机微粒和第一混合物,第二混合物混合均匀,取出,干燥,预热,烧结,得到所述铋基吸附除氯材料。
[0021]
进一步地,所述无机微粒依次和第一混合物,第二混合物混合均匀,是先将无机微粒和40-60%的第一混合物混匀,再和40-60%的第二混合物混匀,之后加入剩余第一混合物和第二混合物,继续混匀。分批加入第一混合物和第二混合物,能够使铋源在物料中分散的更加均匀。
[0022]
进一步地,所述水溶性有机溶剂是指乙腈、四氢呋喃、吡啶中的一种。
[0023]
进一步地,所述球磨是在球磨机降物料研磨至4000-10000目,优选5000-6000目。将铋源进行研磨至一定细度后,更有利于其在材料的均匀分散。
[0024]
进一步地,第一混合物中含氮配体的质量浓度为10-30wt%,第二混合物的固含量为20-40%。
[0025]
进一步地,无机微粒依次和第一混合物,第二混合物混合均匀时,是在滚筒中进行;具体是滚筒中加入无机微粒,第一混合物,混合1-2h后,再加入第二混合物,混合1-2h,取出。
[0026]
进一步地,所述干燥是在90-110℃下干燥,或者在60-70℃,0.01-0.1mpa真空干燥;所述预热,是在200-260℃下加热1-3h;所述烧结是在450-600℃下保温烧结6-12h。
[0027]
按照上述方法,铋源分散在混合物中,通过含氮配体的作用,在含氮助剂的存在下,能够均匀分散在混合物中,并且和无机微粒有很好的亲和力,经过烧结后,含氮配体会形成氮掺杂的炭包覆层,并且铋均匀分散在包覆层中,得到铋基吸附除氯材料。将此材料投放到废水中,或者将废水经过填充有该材料的流动柱,经过吸附除氯作用,能够快速有效对废水中的氯进行除去,静态平衡吸附除氯率可以达到85%左右,优选实施例能够达到90%左右;在流动柱处理含氯水时,动态的除氯率在1-2bv/h(即每小时1-2倍的柱体积)流速下能够达到70%左右,显示出快速除氯效果。
[0028]
本发明的有益效果:利用无机微粒形成具有一定粒径和体积的吸附除氯材料,节省材料,降低成本,可以直接用于填料塔,流动柱等已有设备和仪器;卟啉和/或酞菁衍生物在壳聚糖、三聚氰胺、尿素等助剂的作用下,与含铋材料在无机微粒表面形成薄膜状吸附除氯材料;本发明所述铋基吸附除氯材料不引入杂质,不发生氧化还原反应,便于分离回收,不产生二次污染。
具体实施方式
[0029]
以下以具体实施方式对本发明的内容做进一步的解释和说明。
[0030]
本发明实施例中所用试剂均可采购自商业途径。
[0031]
实施例1
[0032]
将8g四(对氨基苯基)卟啉和8gα-四氨基酞菁溶解在100ml乙腈中,得到第一混合物;3g三聚氰胺、3g尿素分散于30ml水中,加入4g硝酸铋,在球磨机中研磨至6000目,得到第二混合物;在滚筒中加入平均粒径为3mm的活性炭颗粒260g,首先加入50%的第一混合物混
匀1h,然后加入50%的第二混合物,混匀1h,105℃下干燥1h,再加入剩余的第一混合物和第二混合物,继续混匀1h,之后取出,105℃下干燥1h,230℃下预热2h后,升温至550℃,保温烧结8小时,即得铋基吸附除氯材料。
[0033]
实施例2
[0034]
将6g四(对氰基苯基)卟啉和6gα-四羟基酞菁溶解在80ml四氢呋喃中,得到第一混合物;5g三聚氰胺、3g尿素溶解于40ml水中,加入4g氧化铋,在球磨机中研磨至5000目,得到第二混合物;在滚筒中加入平均粒径为1.5mm的活性炭颗粒360g,加入40%第一混合物混匀1h,然后加入40%第二混合物,混匀1h,105℃下干燥1h,再加入剩余的第一混合物和第二混合物,继续混匀1h,之后取出,105℃下干燥1h,260℃下预热2h后,升温至600℃,保温烧结1小时,即得铋基吸附除氯材料。
[0035]
实施例3
[0036]
将9g四(对氰基苯基)卟啉和9gβ-四硝基酞菁溶解在100ml乙腈中,得到第一混合物;8g壳聚糖溶解于30ml水中,加入4g氢氧化铋,在球磨机中研磨至6000目,得到第二混合物;在滚筒中加入粒径为2mm的陶瓷颗粒1200g,首先加入60%第一混合物混匀1h,然后加入60%第二混合物混匀1h,105℃下干燥1h,再加入剩余的第一混合物和第二混合物,混匀,105℃下干燥1h,在200℃下预热2h后,升温至450℃,保温烧结12小时后即得铋基吸附除氯材料。
[0037]
实施例4
[0038]
其他条件和实施例1相同,区别在于含氮配体为16g四(对氨基苯基)卟啉,即不加入α-四氨基酞菁。
[0039]
实施例5
[0040]
其他条件和实施例1相同,区别在于含氮配体为16gα-四氨基酞菁,即不加入四(对氨基苯基)卟啉。
[0041]
实施例6
[0042]
其他条件和实施例1相同,区别在于含氮配体为12g四(对氨基苯基)卟啉和4g四(对氨基苯基)卟啉。
[0043]
实施例7
[0044]
其他条件和实施例1相同,区别在于含氮配体为10g四(对氨基苯基)卟啉和6g四(对氨基苯基)卟啉。
[0045]
实施例8
[0046]
将8g四(对氨基苯基)卟啉和8gα-四氨基酞菁溶解在100ml乙腈中,得到第一混合物;3g三聚氰胺、3g尿素分散于20ml水中,加入4g硝酸铋,在球磨机中研磨至1200目,得到第二混合物;在滚筒中加入平均粒径为1.5mm的活性炭颗粒300g,首先加入的第一混合物混匀1h,然后加入第二混合物,混匀1h,105℃下干燥1h,230℃下预热2h后,升温至550℃,保温烧结8小时,即得铋基吸附除氯材料。即和实施例1相比,实施例8中,第一混合物,第二混合物是一批加入,而不是像实施例1分两批加入。
[0047]
实施例9
[0048]
其他条件和实施例1相同,区别在于四(对氨基苯基)卟啉替换为原卟啉。
[0049]
实施例10
[0050]
其他条件和实施例1相同,区别在于α-四氨基酞菁替换为酞菁。
[0051]
实施例11
[0052]
其他条件和实施例1相同,区别在于5g三聚氰胺、3g尿素溶解于40ml水中,加入4g氧化铋,得到第二混合物,即不进行球磨。
[0053]
对比例1
[0054]
将8g四(对氨基苯基)卟啉和8gα-四氨基酞菁溶解在100ml乙腈中,得到第一混合物;将4g硝酸铋分散于20ml水中,在球磨机中研磨至1200目,得到第二混合物;在滚筒中加入平均粒径为1.5mm的活性炭颗粒300g,首先加入50%的第一混合物混匀1h,然后加入50%的第二混合物,混匀1h,105℃下干燥1h,再加入剩余的第一混合物和第二混合物,继续混匀1h,之后取出,105℃下干燥1h,230℃下预热2h后,升温至550℃,保温烧结8小时,即得铋基吸附除氯材料。即和实施例1相比,不加入含氮助剂。
[0055]
应用例1
[0056]
将分析纯nacl溶于去离子水配成500mg/l的氯离子溶液,取该水溶液10ml于烧杯中,分别加入0.65g上述实施例和对比例制备得到铋基吸附除氯材料,常温下搅拌吸附0.5h达到吸附平衡。将悬浊液抽滤,保留滤液,用硝酸银滴定法测定溶液中的氯离子浓度。计算除氯率,结果如下表1所示:
[0057]
表1静态平衡除氯效果
[0058]
除氯剂除氯率实施例191.4%实施例288.7%实施例381.6%实施例488.5%实施例589.1%实施例689.9%实施例790.5%实施例890.7%实施例988.2%实施例1087.8%实施例1188.6%对比例176.5%
[0059]
应用例2
[0060]
分别将上述实施例和对比例所得铋基吸附除氯材料装入125ml的玻璃柱(具砂板,带活塞),填充至100ml,玻璃柱上部注入含0.3%羧甲基纤维素钠的100mg/l的nacl水溶液,控制流速1.5bv/h(即每小时流经1.5倍柱体积),收集流出液,用硝酸银滴定法测定溶液中的氯离子浓度。计算除氯率。结果如下表2所示:
[0061]
表2流动柱动态除氯效果
[0062]
[0063][0064]
通过上述表1,表2的除氯率可以发现,本发明制备得到的铋基吸附除氯材料可以高效对水中氯离子除去,并且在1.5bv/h的流速下,也能达到70%左右的除氯率。
[0065]
通过实施例1和实施例8的比较可以发现,分批加入卟啉/酞菁的第一混合物,以及含n助剂和铋源的第二混合物,能够使铋分散更加均匀,从而达到更好的除氯效果。通过实施例1和实施例9,10的比较可以发现,以苯环上带有取代基的卟啉/酞菁为原料,所得除氯材料的除氯效果更好,可能是因为苯环上带有取代基(nh2、no2、cn、oh、nco等)对铋有更好的分散和亲和的作用,而且增加了物料体系中的氮含量,使的氮掺杂的比例更高。通过实施例1和实施例11的比较,可以得知含有铋源的第二混合物进行球磨至一定粒度,再去制备铋基吸附除氯材料,可以获得更好的除氯效果。