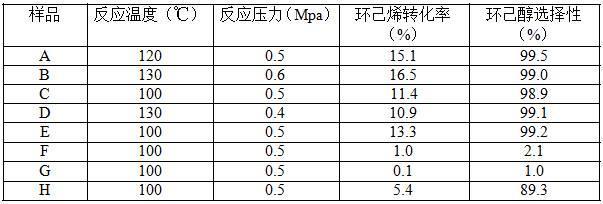
1.本发明涉及一种用于环己烯直接水合反应的催化剂及其制备方法,属于催化剂及其制备技术领域。
背景技术:2.环己醇是一种重要的有机化学中间体,主要用于纺织品、工程塑料和洗涤剂等领域。目前环己醇生产工艺主要有苯酚加氢法、环己烷氧化法和环己烯水合法。随着环己醇下游产品环己酮、己内酰胺、己二酸、尼龙6、尼龙66等需求逐年递增,环己烯水合制备环己醇工艺因其成本低、节能高效、环境友好等优势而受到众多研究者广泛关注。环己烯水合制备环己醇催化技术对支撑尼龙化工、材料化工和纺织行业高质量发展具有重要的现实意义。
3.虽然环己烯间接水合工艺过程中环己烯单程收率高于环己烯直接水合工艺,但是环己烯间接水合催化过程需经过两步反应,同时存在工艺过程复杂和环己醇选择性低的问题,因此设计并开发高效环己烯直接水合催化剂具有重要的现实意义。
4.申武等(申武, 林清香, 朱明乔. 环己烯水合制环己醇研究进展[j]. 合成纤维工业, 2009, 32(2):3.)综合评价了离子交换树脂和分子筛类催化剂在环己烯水合催化反应中的性能,其中amberlyst-36强酸性离子交换树脂和hzsm-5分子筛具有优异的催化性能。在相同的催化条件下,amberlyst-36 离子交换树脂作催化剂的环己烯转化率最大值为12.38%,其高于hzsm-5分子筛(9.84%)。离子交换树脂存在溶胀现象及在高温下易分解的性质,其限制了阳离子交换树脂在环己烯水合反应中的应用,因此hzsm-5分子筛在环己烯直接水合反应中的应用成为了重要研究课题。
[0005]
基于环己烯直接水合工艺,wang 等(wang q, zhang f, huang r, et al. multiphase flow and multicomponent reactive transport study in the catalyst layer of structured catalytic packings for the direct hydration of cyclohexene[j]. chemical engineering and processing-process intensification, 2020, 158: 108199.)建立了催化剂层中的多相流和多组分反应传质模型,通过运算发现增加催化剂表层亲水性和降低水/环己烯体积比能有效提升催化剂表层催化效率。中国专利cn111450875a公开了一种环己烯水合液-液两亲性催化剂的制备方法,通过正辛基三甲氧基硅烷对hzsm-5分子筛进行改性,提供一种相界面催化剂,使得固体催化剂处于油相与水相之间,提高催化剂接触面积,进而提高环己烯的收率,其中环己烯转化率最大值为13.6%。此外,马丙丽等((马丙丽, 淳远, 须沁华,等. 不同孔结构两亲性沸石的制备及其对相界面反应的催化性能 [j]. 催化学报, 2006, 27 (8): 737-742.)通过液相回流的方法,使用环己基三氯硅烷对hzsm-5分子筛进行了修饰改性,改性后的催化剂具有了疏水性质,这使得该催化剂的催化活性得到提高,从而使环己烯的转化率也得到了提高,而且该催化剂还可以明显抑制副产物二环己基醚的生成。张大治等(张大治, 黄声骏, 焦雨桐. 一种环己烯水合制备环己醇的方法:cn201811454101.0[p]. 2020-06-09.)将微孔zsm-5骨架拓扑结构和中控孔道的硅铝酸盐材料用于催化环己烯直接水合制备环己醇反应过程,其中
环己烯转化率最大值为16.5%,环己醇选择性为99.7%。为了进一步降催化剂合成成本,姚旭婷等(姚旭婷, 黄鑫, 林玉霞,等. 失活ts-1高效催化环己烯水合生成环己醇的研究[j]. 化学学报, 2020, 78(10):9.)研究发现失活ts-1是高效催化剂,在优化的反应条件下可得到11.0%的环己醇收率和99.8%的环己醇选择性,进一步研究发现,失活ts-1中含有两种br
ø
nsted 酸中心,而催化环己烯水合反应的高效活性中心为与钛羟基相邻的硅羟基(si-oh(ti))。该br
ø
nsted 酸中心的结构完全不同于zsm-5分子筛中的骨架桥式br
ø
nsted酸中心(si-(oh)-al),且表现出相对较弱的酸强度特征,因而促进了环己烯水合反应中生成环己醇的主反应路径,抑制了环己烯异构化的副反应路径,表现出高环己醇选择性的特性。因此开发催化性能优异的固体酸催化剂具有重要的意义。
技术实现要素:[0006]
本发明旨在提供一种用于环己烯直接水合反应的催化剂及其制备方法,具有制备方法简单,合成成本低,合成过程无污染的特点。本发明合成的催化剂具体为一种锡碳基负载型催化剂,将该催化剂用在环己烯直接水合反应中,该催化剂表现出了优异的催化剂活性和选择性。
[0007]
本发明提供了一种用于环己烯直接水合反应的催化剂,由以下原料制成:含锡化合物、有机配体、碱和碳载体;其中:含锡化合物、有机配体、碱和碳载体的质量比为1:1-35:1-35:1-70;进一步地,含锡化合物包括:氯化亚锡、硫酸亚锡、磺酸亚锡、草酸亚锡、氟化亚锡、溴化亚锡中的一种或几种;碳载体包括:椰壳活性炭、煤基活性炭、沥青基球形活性炭、柱状活性炭、碳纳米管、石墨烯中的一种。
[0008]
碱包括:氢氧化钠、氢氧化钾、氢氧化钙、氢氧化钡、氨水中的一种。
[0009]
所述有机配体为苯甲酸、邻苯二甲酸、对苯二甲酸、间苯二甲酸、均三苯甲酸、联苯二甲酸、2-甲基咪唑中的一种。
[0010]
本发明提供了上述用于环己烯直接水合反应的催化剂的制备方法,包括以下步骤:(1)将碳载体与溶剂在敞口容器中搅拌,其中碳载体与溶剂的质量比为1-35:70;(2)在60℃-90℃水浴条件下,将含锡化合物,碱和有机配体混合溶于步骤(1)制备的溶液中,在敞口容器中搅拌5-120min制备催化剂前驱体,其中制成的前驱体中含锡化合物质量百分浓度为1%-45%,有机配体化合物质量百分浓度为1%-45%。得到的混合物进行洗涤、干燥、焙烧,最终获得催化剂。
[0011]
进一步地,所述步骤(1)中的溶剂为甲醇、乙醇、丙酮、乙醚中的一种。
[0012]
进一步地,所述碳载体与溶剂在敞口容器中搅拌是指:60℃-90℃ 条件下,溶剂与载体混合敞口浸渍1h-24h;含锡化合物与载体质量比为1-100:10,有机配体与载体质量比为1-100:10。
[0013]
进一步地,所述的洗涤是指:使用溶剂(甲醇、乙醇、丙酮、乙醚中的一种)对混合物进行洗涤。
[0014]
所述的干燥是指:将混合物放置在90℃-120℃的烘箱中进行干燥6h-24h;
所述的焙烧是指:在氮气氛围下,按升温速率1℃/min-20℃/min升温至150℃-650℃保持4h以上,自然冷却至室温,最终获得锡碳基负载型催化剂。
[0015]
本发明提供了上述锡碳基负载型催化剂在环己烯直接水合反应中的应用。
[0016]
上述应用中,催化剂:环己烯:水的质量比为1:2-20:2-20,反应温度为80-180℃,反应时间为0.5-3.0h,然后采样,在气相色谱中进行分析。
[0017]
本发明提供的催化剂用于环己烯直接水合制备环己醇反应中,环己烯的转化率最高达到16.5%,环己醇的选择性最高能达到大于99.0%。
[0018]
本发明的有益效果:()本发明提供的催化剂合成过程简单环保,合成成本低;(2)在环己烯直接水合制备环己醇过程中,本发明制备的催化剂的活性和选择性表现优异,特别是环己烯的转化率,与现有技术中hzsm-5用于催化环己烯直接水合制备环己醇的工艺(环己烯的转化率最高达到9.8%)相比,环己烯转化率有了显著提高。
具体实施方式
[0019]
下面通过实施例来进一步说明本发明,但不局限于以下实施例。
[0020]
实施例1:在200ml烧杯中加入10g甲醇、2g氯化亚锡、5g邻苯二甲酸、0.6g氢氧化钠和5g煤基活性炭搅拌均匀,然后浸渍搅拌2h。将烧杯中产物取出,洗涤,120℃干燥12h,烘干后在氮气氛下400℃焙烧8h,升温速率为8℃/min。记为催化剂a。在50ml的高压反应釜中加入0.6g催化剂a、12g环己烯和12g去离子水,然后密封。通入高纯氮气置换反应釜中的空气,共计置换3次。将反应釜温度升至120℃,反应压力升至0 .5mpa,搅拌桨转速600r/min,反应2h后,将反应釜温度用水急冷至室温。打开反应釜取出物料离心分离,用气相色谱分析上层溶液。
[0021]
催化剂a的催化性能见表1。
[0022]
实施例2在200ml烧杯中加入10g乙醇、4g草酸亚锡、5g均苯三甲酸、0.8g氢氧化钠和6g沥青基活性炭搅拌均匀,然后浸渍搅拌2h。将烧杯中产物取出,洗涤,100℃干燥10h,烘干后在氮气氛下500℃焙烧8h,升温速率为10℃/min。记为催化剂b。在50ml的高压反应釜中加入0.6g催化剂b、12g环己烯和10g去离子水,然后密封。通入高纯氮气置换反应釜中的空气,共计置换3次。将反应釜温度升至130℃,反应压力升至0 .6mpa,搅拌桨转速900r/min,反应3h后,将反应釜温度用水急冷至室温。打开反应釜取出物料离心分离,用气相色谱分析上层溶液。
[0023]
催化剂b的催化性能见表1。
[0024]
实施例3在200ml烧杯中加入10g丙酮、3g硫酸亚锡、5g间苯二甲酸、0.4g氢氧化钠和9g碳纳米管搅拌均匀,然后浸渍搅拌2h。将烧杯中产物取出,洗涤,100℃干燥24h,烘干后在氮气氛下550℃焙烧8h,升温速率为15℃/min。记为催化剂c。在50ml的高压反应釜中加入0.6g催化剂c、12g环己烯和12g去离子水,然后密封。通入高纯氮气置换反应釜中的空气,共计置换3次。将反应釜温度升至100℃,反应压力升至0 .5mpa,搅拌桨转速600r/min,反应2h后,将反应釜温度用水急冷至室温。打开反应釜取出物料离心分离,用气相色谱分析上层溶液。
[0025]
催化剂c的催化性能见表1。
[0026]
实施例4在200ml烧杯中加入10g甲醇、2g氯化亚锡、10g联苯二甲酸、0.7g氢氧化钠和4g石墨烯搅拌均匀,然后浸渍搅拌2h。将烧杯中产物取出,洗涤,100℃干燥12h,烘干后在氮气氛下600℃焙烧4h,升温速率为12℃/min。记为催化剂d。在50ml的高压反应釜中加入0.6g催化剂d、12g环己烯和14g去离子水,然后密封。通入高纯氮气置换反应釜中的空气,共计置换3次。将反应釜温度升至130℃,反应压力升至0 .4mpa,搅拌桨转速1000r/min,反应2h后,将反应釜温度用水急冷至室温。打开反应釜取出物料离心分离,用气相色谱分析上层溶液。
[0027]
催化剂d的催化性能见表1。
[0028]
实施例5在200ml烧杯中加入10g乙醚、2g磺酸亚锡、5g邻苯二甲酸、0.6g氢氧化钠和5g煤基活性炭搅拌均匀,然后浸渍搅拌2h。将烧杯中产物取出,洗涤,120℃干燥12h,烘干后在氮气氛下650℃焙烧7h,升温速率为20℃/min。记为催化剂e。在50ml的高压反应釜中加入0.6g催化剂e、12g环己烯和7g去离子水,然后密封。通入高纯氮气置换反应釜中的空气,共计置换3次。将反应釜温度升至100℃,反应压力升至0 .5mpa,搅拌桨转速800r/min,反应2h后,将反应釜温度用水急冷至室温。打开反应釜取出物料离心分离,用气相色谱分析上层溶液。
[0029]
催化剂e的催化性能见表1。
[0030]
对比实施例1在200ml烧杯中加入10g乙醚、2g磺酸亚锡、0.6g氢氧化钠和5g煤基活性炭搅拌均匀,然后浸渍搅拌2h。将烧杯中产物取出,洗涤,120℃干燥12h,烘干后在氮气氛下650℃焙烧7h,升温速率为20℃/min。记为催化剂f。在50ml的高压反应釜中加入0.6g催化剂f、12g环己烯和7g去离子水,然后密封。通入高纯氮气置换反应釜中的空气,共计置换3次。将反应釜温度升至100℃,反应压力升至0 .5mpa,搅拌桨转速800r/min,反应2h后,将反应釜温度用水急冷至室温。打开反应釜取出物料离心分离,用气相色谱分析上层溶液。
[0031]
催化剂f的催化性能见表1。
[0032]
对比实施例2在200ml烧杯中加入10g乙醚、5g邻苯二甲酸、0.6g氢氧化钠和5g煤基活性炭搅拌均匀,然后浸渍搅拌2h。将烧杯中产物取出,洗涤,120℃干燥12h,烘干后在氮气氛下650℃焙烧7h,升温速率为20℃/min。记为催化剂g。在50ml的高压反应釜中加入0.6g催化剂g、12g环己烯和7g去离子水,然后密封。通入高纯氮气置换反应釜中的空气,共计置换3次。将反应釜温度升至100℃,反应压力升至0 .5mpa,搅拌桨转速800r/min,反应2h后,将反应釜温度用水急冷至室温。打开反应釜取出物料离心分离,用气相色谱分析上层溶液。
[0033]
催化剂g的催化性能见表1。
[0034]
对比实施例3在200ml烧杯中加入10g乙醚、2g磺酸亚锡、5g邻苯二甲酸、0.6g氢氧化钠和5g煤基活性炭搅拌均匀,然后浸渍搅拌2h。将烧杯中产物取出,洗涤,120℃干燥12h,烘干。记为催化剂h。在50ml的高压反应釜中加入0.6g催化剂h、12g环己烯和7g去离子水,然后密封。通入高纯氮气置换反应釜中的空气,共计置换3次。将反应釜温度升至100℃,反应压力升至0.5mpa,搅拌桨转速800r/min,反应2h后,将反应釜温度用水急冷至室温。打开反应釜取出物料离心分离,用气相色谱分析上层溶液。
[0035]
催化剂h的催化性能见表1。
[0036]
表 1 催化剂在环己烯直接水合催化反应中的性能对比实施例1:与实施例5对比,原料合成过程未加入邻苯二甲酸,催化剂的环己烯转化率为1.0%,环己醇选择性为2.1%,说明邻苯二甲酸与磺酸亚锡协同作用的催化性能最佳。
[0037]
对比实施例2:与实施例5对比,原料合成过程未加入磺酸亚锡,催化剂的环己烯转化率为0.1%,环己醇选择性为1.0%,说明邻苯二甲酸与磺酸亚锡协同作用的催化性能最佳。
[0038]
对比实施例3:与实施例5对比,催化剂前驱体未经过高温焙烧。催化剂的环己烯转化率为5.4%,环己醇选择性为89.3%,说明经碳化后,催化剂表面出现多级孔,实现二次造孔,从而提升传质效率,进而提升催化活性。