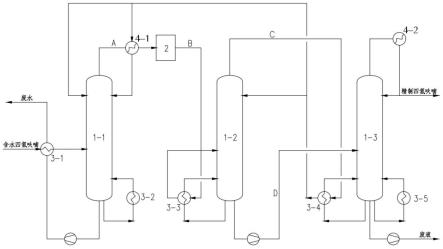
1.本技术属于化工分离技术领域,具体涉及一种塔膜一体化脱水的四氢呋喃精制装置及精制方法。
背景技术:2.四氢呋喃(thf)是一个杂环有机化合物,分子式为c4h8o,属于醚类,是呋喃的完全氢化产物,是一种无色、可与水混溶、在常温常压下有较小粘稠度的有机液体。thf常压下的沸点66℃,闭杯闪点-14℃,爆炸范围为1.8%~18%,具有爆炸危险性。thf具有广泛的用途:(1)thf是一种重要的有机合成原料且是性能优良的溶剂,特别适用于溶解pvc、聚偏氯乙烯和丁苯胺,广泛用作表面涂料、防腐涂料、印刷油墨、磁带和薄膜涂料的溶剂,并用作反应溶剂,用于电镀铝液时可任意控制铝层厚度且光亮;(2)thf自身可缩聚成聚四亚甲基醚二醇(ptmeg),也称四氢呋喃均聚醚;(3)在医药工业方面,thf用于合成咳必清、利复霉素、黄体酮和一些激素药;(4)thf经硫化氢处理生成四氢硫酚,可作燃料气中的臭味剂(识别添加剂);(5)thf还可用做合成革的表面处理剂。
3.thf与水会形成混合物,其共沸组成随压力不同而变化。无论是ptmeg生产中的原料thf还是pbat副产的thf,均通过变压精馏精制得到。现有相关技术中,对于四氢呋喃-水体系的变压精馏分离,通常由一个常压塔(低压塔)与一个高压塔串联而成,原料进入常压塔,塔底脱出部分水分,塔顶产物为thf-水共沸物,经加压进入高压塔。此时因为压力的改变使得共沸点发生了变化,故可在高压塔中进行分离得到纯的thf。
4.但是,传统的变压精馏工艺的四氢呋喃-水混合物循环处理量大、蒸汽消耗量大,寻找一种节能的thf脱水精制工艺,成为thf生产行业迫切需要解决的课题。
技术实现要素:5.本技术提供一种塔膜一体化脱水的四氢呋喃精制装置及精制方法,以解决传统的四氢呋喃脱水工艺能耗高的问题。
6.本技术的第一方面,提供一种塔膜一体化脱水的四氢呋喃精制装置,包括按进料方向串联的第一精馏塔、第二精馏塔以及第三精馏塔,在第一精馏塔塔顶连接有膜脱水装置,所述膜脱水装置还与设置在第二精馏塔塔底的第二再沸器连接,第二精馏塔塔顶与设置在第三精馏塔塔底的第三再沸器连接。
7.可选的,所述第一精馏塔的塔顶连接有第一冷凝器,所述第一冷凝器与膜脱水装置连接,并与第三精馏塔塔底的第三再沸器连接。
8.本技术的第二方面,提供一种塔膜一体化脱水的四氢呋喃精制方法,包括以下步骤:
9.将待处理的四氢呋喃料液经预热器升温后送入第一精馏塔处理,从塔顶得到气相四氢呋喃和水混合物;将第一精馏塔塔顶得到的气相四氢呋喃和水的混合物送入膜脱水装置,膜脱水装置的渗透物送回第一精馏塔再处理,膜脱水装置的渗余物送入第二精馏塔处
理;从第二精馏塔塔顶得到的气相四氢呋喃和水的混合物送回第一精馏塔或者膜脱水装置处理,从第二精馏塔塔底得到的四氢呋喃粗液送入第三精馏塔处理;从第三精馏塔塔顶采出四氢呋喃产品,从第三精馏塔塔底间歇排放重组分杂质;
10.其中,第一精馏塔塔顶操作压力高于第二精馏塔塔顶操作压力,第二精馏塔塔顶操作压力高于第三精馏塔塔顶操作压力。
11.可选的,所述膜脱水装置的渗余物,在送入第二精馏塔处理之前,送入第二精馏塔塔底的第二再沸器壳程换热,加热第二精馏塔釜液,再送入第二精馏塔处理;所述从第二精馏塔塔顶得到的气相四氢呋喃和水的混合物,在送回第一精馏塔或者膜脱水装置处理之前,送入第三精馏塔塔底的第三再沸器壳程换热,加热第三精馏塔釜液,再送入第一精馏塔或者膜脱水装置处理;
12.可选的,第一精馏塔塔顶得到的气相四氢呋喃和水的混合物送入膜脱水装置之前,通过第一精馏塔塔顶的冷凝器换热后,气相再送入膜脱水装置;第二精馏塔塔顶得到的气相四氢呋喃和水的混合物通过第三精馏塔的第三再沸器壳程换热后,通过第一精馏塔塔顶的冷凝器换热,气相再进入膜脱水装置继续下一流程。
13.可选的,所述第一精馏塔塔顶操作压力0.3~0.5mpa,第二精馏塔塔顶操作压力0.2~0.3mpa,第三精馏塔塔顶操作压力为常压。
14.可选的,所述膜脱水装置为沸石膜脱水装置或有机膜脱水装置,膜脱水装置原料侧的压力控制在0.3~0.5mpa。
15.可选的,第三精馏塔的塔釜温度控制在110℃以下。
16.可选的,待处理的四氢呋喃料液含水20%~30%。
17.可选的,待处理的四氢呋喃料液含水22%~92%;其脱水精制步骤具体为:
18.(1)将含水22%~92%的四氢呋喃料液经预热器升温后送入第一精馏塔处理,从塔顶得到含量89%~96%的气相四氢呋喃和水混合物;
19.(2)将步骤(1)得到的含量89%~96%的四氢呋喃和水的混合物送入膜脱水装置,渗透物为含少量四氢呋喃的水溶液,送回第二精馏塔再处理;渗余物为水含量0.5%~2%的四氢呋喃;
20.(3)将步骤(2)得到的水含量0.5%~2%的四氢呋喃送入第二精馏塔第二再沸器换热后再送入第二精馏塔处理;塔顶得到含量91%~96%的四氢呋喃和水混合物,塔底得到水含量小于100ppm的四氢呋喃;
21.(4)将步骤(3)得到的含量91%~96%的四氢呋喃和水混合物送入第三精馏塔第三再沸器换热后再送入第一精馏塔或膜脱水装置处理;
22.(5)将步骤(3)得到的水含量小于100ppm的四氢呋喃送入第三精馏塔处理,从塔顶采出纯度大于99.9%的四氢呋喃,塔底间歇排放少量重组分杂质。
23.本技术的技术方案,构建了不同于传统工艺的新的四氢呋喃精馏脱水工艺,提供了工艺方法以及与工艺流程相对应的整套精馏装置。在本工艺中,除了膜脱水装置的引入而形成的塔膜一体化工艺,使得系统精馏脱水负荷大幅降低以外,还将三塔的操作压力由高到低依次递减,相应形成的温度梯度带来了不同于传统工艺的换热方式,使前塔塔顶蒸汽能用于后塔的再沸器加热,能耗由此进一步降低。
24.与传统的精馏脱水精制工艺相比,本技术的四氢呋喃脱水精制工艺具有如下优
势:
25.1.本发明工艺采用了塔膜一体化的脱水方式,膜脱水装置的引入,使系统的精馏脱水负荷大幅降低,降低了能耗;
26.2.本技术的精制工艺方法,顺着工艺流程的各塔操作压力由高到低,层层递减,形成压力梯度,从而构建出温度梯度,前塔温度大于后塔温度,使前塔塔顶蒸汽能用于后塔的再沸器加热,形成不同于传统工艺的换热方式,充分利用了塔顶气体的液化潜热,进而节约能耗;综合能耗降低15%~40%;
27.3.本发明工艺的系统最高操作压力低于传统工艺的系统最高操作压力,相应系统操作温度也低于传统工艺的系统操作温度,不易产生杂质,thf产品质量更高,回收率也更高;
28.4.本发明工艺的设备规格更小,节约投资,减小占地;操作弹性更大,对进料要求更低,更有利于装置的稳定运行;
29.5.本发明工艺产生的废水cod含量更低,减少了后续污水处理单元的负荷。
附图说明
30.为了更清楚地说明本技术的技术方案,下面将对实施例中所需要使用的附图作简单地介绍,显而易见地,对于本领域普通技术人员而言,在不付出创造性劳动的前提下,还可以根据这些附图获得其他的附图。
31.图1为本技术实施例的四氢呋喃脱水精制装置及工艺流程示意图。
32.图中,1-1是第一精馏塔,1-2是第二精馏塔,1-3第三精馏塔,2是膜脱水装置,3-1是进料预热器,3-2是第二再沸器,3-3是第三再沸器,3-4是第四再沸器,4-1是第一冷凝器,4-2是第二冷凝器;
33.物流a是从第一精馏塔塔顶采出的四氢呋喃和水的混合物,物流b是膜脱水装置过滤后的渗余物,物流c是从第二精馏塔塔顶采出的四氢呋喃和水的混合物,物流d是从第二精馏塔塔底采出的四氢呋喃粗液。
具体实施方式
34.为了使本技术的上述目的、特征和优点能够更加明显易懂,下面结合附图和实施例对本技术进行详细说明。
35.本技术提供一种塔膜一体化脱水的四氢呋喃精制装置以及四氢呋喃脱水精制方法。在本技术具体实施方式的说明中,四氢呋喃脱水精制方法可利用本实施例中的装置进行。
36.实施例1
37.如图1所示,本技术的塔膜一体化脱水的四氢呋喃精制装置包括按进料方向总体依次串联的第一精馏塔1-1,第二精馏塔1-2,第三精馏塔1-3。其中,在第一精馏塔1-1、第二精馏塔1-2、第三精馏塔1-3的塔釜均设置再沸器,用于回流加热釜液,参照图1,分别为第一再沸器3-2,第二再沸器3-3,第三再沸器3-4和第四再沸器3-5(本实施例中第三精馏塔塔釜设置2个再沸器)。在第一精馏塔1-1和第三精馏塔1-3的塔顶还设置有第一冷凝器4-1和第二冷凝器4-2,用于塔顶物流冷凝换热以及循环回流。
38.在第一精馏塔1-1的进料口设置进料预热器3-1,用于加热待处理的进料四氢呋喃料液;第一精馏塔1-1塔顶的第一冷凝器4-1还与第三精馏塔1-3塔底的第三再沸器3-4连接,用于承接来自第三再沸器的物流c换热后待回流进入膜脱水装置的物流。
39.在第一精馏塔塔顶连接有膜脱水装置2,在具体实施时,膜脱水装置2中的膜可为沸石膜或有机膜。第一精馏塔塔顶采出物流a通过冷凝器4-1进入膜脱水装置2中,通过膜脱水装置2的膜过滤后,渗透物返回第一精馏塔1-1。所述膜脱水装置2还与第二精馏塔1-2塔底的第二再沸器3-3连接,用于膜脱水装置2的渗余物通入第二再沸器3-3而与第二精馏塔塔釜液换热后,再进入第二精馏塔1-2进一步处理。
40.第二精馏塔1-2塔顶与第三精馏塔1-3塔底的第三再沸器3-4连接,用于使第二精馏塔塔顶采出的物流c通入第三再沸器3-4而与第三精馏塔1-3塔底釜液换热后,再回到第一精馏塔1-1塔顶的冷凝器4-1内从而进入膜脱水装置2,或者直接进入第一精馏塔1-1,并部分回流至第二精馏塔1-2。
41.第二精馏塔1-2塔底与第三精馏塔1-3进料口连接,使第二精馏塔1-2塔底的釜液物流d进入第三精馏塔1-3进一步处理,在第三精馏塔1-3塔顶设置有第二冷凝器4-2用于冷凝回流,并在塔顶采出高纯度的四氢呋喃产品。
42.实施例2
43.可知的是,本技术的方法可以但不限于利用实施例1所述的四氢呋喃精制装置。为方便说明,在本实施例中,本技术所述的精制方法利用实施例1所述的四氢呋喃精制装置进行说明,如图1所示,具体包括以下步骤:
44.将待处理的含水四氢呋喃料液经预热器3-1升温后送入第一精馏塔1-1处理,从塔顶得到气相四氢呋喃和水混合物(物流a);将第一精馏塔1-1塔顶得到的气相四氢呋喃和水的混合物a送入膜脱水装置2,作为优选实施方式,物流a被送入膜脱水装置2之前,通过第一精馏塔塔顶的冷凝器4-1换热后,气相再进入膜脱水装置2;膜脱水装置2的渗透物送回第一精馏塔1-1再处理,膜脱水装置2的渗余物送入第二精馏塔1-2的第二再沸器3-3壳程换热,加热第二精馏塔1-2塔底釜液,再送入第二精馏塔1-2处理;从第二精馏塔1-2塔顶得到的气相四氢呋喃和水的混合物(物流c)送入第三精馏塔1-3的第三再沸器3-4壳程换热,加热第三精馏塔1-3塔底釜液,再送入第一精馏塔1-1或者膜脱水装置2处理,作为优选实施方式,送入膜脱水装置2处理时,通过第一精馏塔塔顶的冷凝器4-1换热,气相再进入膜脱水装置2,继续下一流程。从第二精馏塔1-2塔底得到的四氢呋喃粗液(物流d)送入第三精馏塔1-3处理。从第三精馏塔1-3塔顶采出四氢呋喃产品,从第三精馏塔1-3塔底间歇排放重组分杂质。
45.在本工艺方法中,第一精馏塔塔顶操作压力高于第二精馏塔塔顶操作压力,第二精馏塔塔顶操作压力高于第三精馏塔塔顶操作压力。
46.作为优选实施方式,所述的膜脱水装置为沸石膜脱水装置或有机膜脱水装置,膜脱水装置原料侧的压力控制在0.3~0.5mpa。
47.作为优选实施方式,所述第一精馏塔塔顶操作压力0.3~0.5mpa,第二精馏塔塔顶操作压力0.2~0.3mpa,第三精馏塔塔顶操作压力为常压。第三精馏塔的塔釜温度控制在110℃以下。
48.具体地,本技术的精制工艺方法,顺着工艺流程的各塔操作压力由高到低,层层递
减,形成压力梯度,从而构建出温度梯度,前塔温度大于后塔温度,使前塔塔顶蒸汽能用于后塔的再沸器加热,形成不同于传统工艺的换热方式,充分利用了塔顶气体的液化潜热,进而节约能耗;综合能耗降低15%~40%。此外,系统最高操作压力低于传统工艺的系统最高操作压力,相应系统操作温度也低于传统工艺的系统操作温度,从而不易产生杂质,thf产品质量更高,回收率也更高。
49.以本方法适用的四氢呋喃料液含水22%~92%为例,进一步说明脱水精制方法步骤以及各流程的物流情况:
50.(1)将含水22%~92%的四氢呋喃料液经预热器升温后送入第一精馏塔处理,从塔顶得到含量89%~96%的气相四氢呋喃和水混合物;
51.(2)将步骤(1)得到的含量89%~96%的四氢呋喃和水的混合物送入膜脱水装置,渗透物为含少量四氢呋喃的水溶液,送回第二精馏塔再处理;渗余物为水含量0.5%~2%的四氢呋喃;
52.(3)将步骤(2)得到的水含量0.5%~2%的四氢呋喃送入第二精馏塔第二再沸器换热后再送入第二精馏塔处理;塔顶得到含量91%~96%的四氢呋喃和水混合物,塔底得到水含量小于100ppm的四氢呋喃;
53.(4)将步骤(3)得到的含量91%~96%的四氢呋喃和水混合物送入第三精馏塔第三再沸器换热后再送入第一精馏塔或膜脱水装置处理;
54.(5)将步骤(3)得到的水含量小于100ppm的四氢呋喃送入第三精馏塔处理,从塔顶采出纯度大于99.9%的四氢呋喃,塔底间歇排放少量重组分杂质。
55.本技术的精制工艺方法脱水效率和精度高,适用于含水率低的四氢呋喃料液的精制。可用于ptmeg生产中的四氢呋喃脱水精制,其待处理的四氢呋喃料液含水约20%~30%。
56.以下实施例以1000kg的四氢呋喃料液处理量为例进一步说明本技术的技术方案。
57.实施例3
58.(1)将含水22%的四氢呋喃料液预热后送入第一精馏塔。第一精馏塔操作压力0.3mpa,塔底采出含thf约100ppm的220kg废水,塔顶采出含量91%的四氢呋喃和水混合物气体a(物流a,下同)920kg。
59.(2)将步骤(1)得到的气体a直接送入沸石脱水膜处理,大部分水和少量四氢呋喃透过沸石膜,得到含四氢呋喃9.6%的废水88kg,送回第一精馏塔处理以回收四氢呋喃。四氢呋喃和少量水留在进料侧,得到约115℃、含水0.5%的四氢呋喃气体b(物流b,下同)835kg。
60.(3)将步骤(2)得到的气体b送入第二精馏塔再沸器壳程加热釜液,50%的气体b被冷凝,与未冷凝气体一起送入第二精馏塔处理。第二精馏塔操作压力0.2mpa,从塔顶采出约98℃、含量92.6%的四氢呋喃和水混合物气体c(物流c,下同)330kg,从塔底采出含水100ppm的四氢呋喃液体d(物流d,下同)780kg。
61.(4)将步骤(3)得到的气体c送入第三精馏塔再沸壳程加热釜液,自身全部被冷凝,其中55kg返回第一精馏塔处理,275kg回流至第二精馏塔顶部。从步骤(3)得到的液体d送入第三精馏塔精制处理。第三精馏塔操作压力10kpa,从塔顶采出约70℃、含量99.9%的四氢呋喃液体764kg。塔底间歇采出杂质16kg。
62.实施例4
63.(1)将含水78%的四氢呋喃料液预热后送入第一精馏塔。第一精馏塔操作压力0.5mpa,塔底采出含thf约100ppm的780kg废水,塔顶采出含量89%的四氢呋喃和水的混合物气体a265kg。
64.(2)将步骤(1)得到的气体a直接送入有机脱水膜处理,大部分水和少量四氢呋喃透过有机膜,得到含四氢呋喃8.6%的废水29kg,送回第一精馏塔处理回收四氢呋喃。四氢呋喃和少量水留在进料侧,得到约132℃、含水1.2%的四氢呋喃气体b 253kg。
65.(3)将步骤(2)得到的气体b送入第二精馏塔再沸器壳程加热釜液,自身全部被冷凝后送入第二精馏塔处理。第二精馏塔操作压力0.3mpa,从塔顶采出约108℃、含量91%的四氢呋喃和水的混合物气体c 210kg,从塔底采出含水100ppm的四氢呋喃液体d 220kg。
66.(4)将步骤(3)得到的气体c送入第三精馏塔再沸壳程加热釜液,自身全部被冷凝,其中35kg返回第一精馏塔处理,175kg回流至第二精馏塔顶部。从步骤(3)得到的液体d送入第三精馏塔精制处理。第三精馏塔操作压力30kpa,从塔顶采出约75℃、含量99.9%的四氢呋喃液体216kg。塔底间歇采出约77℃杂质4kg。
67.实施例5
68.(1)将含水60%的四氢呋喃料液预热后送入第一精馏塔。第一精馏塔操作压力0.5mpa,塔底采出含thf约100ppm的600kg废水,塔顶采出含量89%的四氢呋喃和水混合物气体a521kg。
69.(2)将步骤(1)得到的气体a直接送入沸石膜处理,大部分水和少量四氢呋喃透过有机膜,得到含四氢呋喃8.5%的废水55kg,送回第一精馏塔处理回收四氢呋喃。四氢呋喃和少量水留在进料侧,得到约132℃、含水0.9%的四氢呋喃气体b 466kg。
70.(3)将步骤(2)得到的气体b送入第二精馏塔再沸器壳程加热釜液,自身全部被冷凝后送入第二精馏塔处理。第二精馏塔操作压力0.1mpa,从塔顶采出约85℃、含量93%的四氢呋喃和水的混合物气体c 396kg,从塔底采出含水100ppm的四氢呋喃液体d 400kg。
71.(4)将步骤(3)得到的气体c送入第三精馏塔再沸壳程加热釜液,自身全部被冷凝,其中66kg返回第一精馏塔处理,330kg回流至第二精馏塔顶部。从步骤(3)得到的液体d送入第三精馏塔精制处理。第三精馏塔操作压力0kpa,从塔顶采出约66℃、含量99.9%的四氢呋喃液体392kg。塔底间歇采出约70℃杂质8kg。
72.以上结合具体实施方式和范例性实例对本技术进行了详细说明,不过这些说明并不能理解为对本技术的限制。本领域技术人员理解,在不偏离本技术精神和范围的情况下,可以对本技术技术方案及其实施方式进行多种等价替换、修饰或改进,这些均落入本技术的范围内。本技术的保护范围以所附权利要求为准。