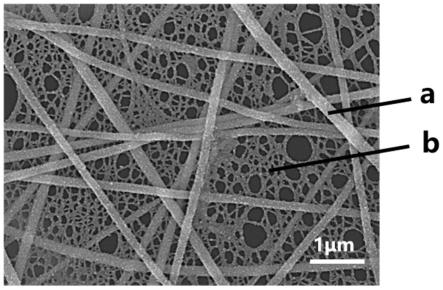
1.本发明涉及纤维膜材料技术领域,尤其是涉及一种单层纳米纤网/静电纺纤维复合膜的制备方法及其制备方法。
背景技术:2.静电纺纤维膜材料具有纤维直径细、孔径小、孔隙率高等特点,在空气过滤、油水分离、防水透湿等领域具有广阔的应用前景。但目前静电纺纤维的直径多在100nm以上,导致其孔径无法进一步降低,对直径1μm以下的亚微米级颗粒污染物难以过滤分离。静电纺纤维膜材料的多孔结构是由纳米纤维层层堆叠而成,导致其厚度大,阻力压降高,限制了其过滤性能的进一步提升。
3.专利cn202010951106.5公开了《一种静电纺纤维基超薄连续纳米蛛网纤维材料及其制备方法》,将聚合物溶液刮涂至静电纺纤维基材表面,通过在非溶剂浴中浸渍相分离的方法得到纳米蛛网复合材料。该方法中的刮涂成膜步骤易使聚合物溶液在毛细作用下渗入静电纺纤维基材内,难以精确调控液膜的连续性与均匀度;并且另一核心步骤非溶剂浴相分离难以控制溶剂与非溶剂双扩散速度,从而无法实现对相分离所形成孔结构的有效调控。
4.专利cn201810555559.9公开了《一种利用冷冻干燥技术制备界面薄层多孔膜的方法》,通过旋涂法在玻璃基底上涂覆液膜,经冷冻干燥后得到薄层多孔膜。该方法通过在玻璃基底上旋涂形成液膜,存在溶液因表面张力难以在玻璃基底上均匀成膜的问题,导致所得多孔膜厚度不匀、孔结构不连续。
5.专利cn201710649234.2公开了《一种细菌纤维素纳米纤维复合滤膜及其制备方法》,将细菌纤维素悬浮液铺于多孔纤维基材表面,去除溶剂,随后交联化处理,得到二维网状结构的细菌纤维素纳米纤维复合滤膜。该方法是基于细菌纤维素短纤间相互搭接而构筑二维网孔结构,在纤维素悬浮液制备过程中,纤维素短纤难以均匀分散,存在纤维素短纤易团簇、成网孔径均匀度差的问题。
技术实现要素:6.本发明的目的就是为了克服上述现有技术存在的缺陷而提供一种单层纳米纤网/静电纺纤维复合膜及其制备方法,以此得到一种连续的、孔径可控的单层二维网状材料,从而显著降低静电纺纳米纤维材料的孔径,并保持原有的高孔隙率和透过性,使复合膜材料具有低过滤阻力。
7.本发明的目的可以通过以下技术方案来实现:
8.本发明第一方面提供一种单层纳米纤网/静电纺纤维复合膜的制备方法,包括以下步骤:
9.s1:将聚合物、表面活性剂加入溶剂中搅拌均匀,获得低表面能聚合物溶液,同时,将无机盐加入非溶剂中搅拌均匀,获得高表面能无机盐溶液;
10.s2:将静电纺纤维基材置于所述高表面能无机盐溶液中浸渍达到饱和状态,得到高表面能静电纺纤维基材;
11.s3:将所述低表面能聚合物溶液多点位滴注于所述高表面能静电纺纤维基材表面,使得低表面能聚合物溶液无渗透地在所述高表面能静电纺纤维基材上自发超铺展,形成连续的超薄聚合物液膜,聚合物液膜与高表面能静电纺纤维基材表面非溶剂接触发生相分离,形成溶剂富集相与聚合物富集相;
12.s4:将s3中得到的材料进行预冷冻,使得溶剂富集相中的冰晶成核生长,使聚合物富集相被冰晶排挤形成二维网孔结构;
13.s5:将预冷冻后的基材进行真空冷冻干燥,去除溶剂与非溶剂,最终获得以静电纺纤维为基材且表面覆盖连续单层纳米纤网的复合材料。
14.进一步地,s4中,通过改变冷冻速率来调控冰晶成核生长过程,从而实现对二维网孔结构的精确调控。
15.进一步地,s1中,所述聚合物选自聚偏氟乙烯、聚丙烯腈、聚酰胺、聚氨酯、聚乙烯醇、聚酰胺酰亚胺、聚醚酰亚胺、聚苯乙烯中的一种或几种,所述聚合物的质量分数为0.1~10wt%。
16.进一步地,s1中,所述低表面能聚合物溶液的表面张力≤35mn/m;
17.所述高表面能非溶剂的表面张力≥50mn/m。
18.进一步地,s1中,所述溶剂选自n,n-二甲基甲酰胺、n,n-二甲基乙酰胺、二甲基亚砜、n-甲基吡咯烷酮、乙醇、异丁醇、正丙醇、乙酸乙酯、丙酮中的一种或几种;
19.所述表面活性剂选自十二烷基硫酸钠、十二烷基苯磺酸钠、十二烷基三甲基溴化铵、月桂基磺化琥珀酸单酯二钠、单月桂基磷酸酯、月桂醇醚磷酸酯钾、脂肪醇聚氧乙烯醚硫酸铵、月桂酰胺丙基甜菜碱、椰油酸单乙醇酰胺、椰油酸二乙醇酰胺中的一种或几种,所述表面活性剂质量分数为0.01~5wt%;
20.所述无机盐选自氯化钠、氯化锂、氯化锌、氯化钙、氯化铜、醋酸钠、苯甲酸钠、硫酸钠、硫酸铝、硫酸锌中的一种或几种,所述无机盐的质量分数为0.001~0.5wt%;
21.所述非溶剂选自水、甲醇、乙醇、丙醇、异丁醇、乙二醇、丙酮、甲酚、环己烷中的一种或几种。
22.进一步地,s2中,所述静电纺纤维基材选自聚酰胺静电纺纳米纤维膜、聚四氟乙烯静电纺纳米纤维膜、聚丙烯静电纺纳米纤维膜、聚酰亚胺静电纺纳米纤维膜、聚对苯二甲酸乙二醇静电纺纳米纤维膜、二氧化硅静电纺纳米纤维中的一种,基材直径为0.2~2μm,孔径为1~10μm,厚度为5~100μm;
23.s2中,浸渍时间为10~60min。
24.进一步地,s3中,所述多点位滴注为利用多个注射器进行微量注射,其中注射器排列形式为:共有a排,每排b个注射器,a≥2,b≥3,注射器间距为1~10cm,注射器针管内径为0.1~5mm,外径为0.3~5.3mm,注射器出液速度为0.1~100μl/s。
25.进一步地,s4中,所述预冷冻温度≤-50℃,降温速率为5~15℃/min,预冷冻时间为3~10h。其中,降温速率可影响冰晶成核生长过程,从而实现对二维网孔结构的调控;降温速率快,更易在溶剂富集相中生成数量多、尺寸小的细晶,使二维网孔径降低,孔隙率增加;反之,降温速率慢,更易生成数量少、尺寸较大冰晶,使二维网孔径增加,孔隙率降低。
26.进一步地,s5中,所述真空冷冻干燥时间为30~60h,真空度为-0.05~-0.1mpa。
27.本发明第二方面提供了一种如上述方法制备的单层纳米纤网/静电纺纤维复合膜,所述单层纳米纤网中纤维直径为10~100nm,单层纳米纤网/静电纺纤维复合膜孔径为0.2~1μm,厚度为5~90μm,孔隙率≥80%。
28.本发明的技术原理如下:
29.本发明的单层纳米纤网/静电纺纤维复合膜,是在静电纺纤维基材上构筑连续超薄聚合物液膜,然后经相分离、预冷冻、真空冷冻干燥得到。通过在聚合物溶液中加入表面活性剂得到低表面能聚合物溶液,在非溶剂中加入无机盐得到高表面能无机盐溶液。通过将静电纺纤维基材在无机盐溶液中浸渍达到饱和,提高基材表面能,从而使溶液表面张力小于基材表面张力,促进聚合物溶液在基材上自发超铺展。首先将聚合物溶液微量滴注于浸渍饱和的基材表面,无机盐溶液填充了基材表面的小孔径,防止聚合物溶液因毛细效应在基材孔道间渗透,表面能作用下聚合物液滴在基材表面超铺展形成连续超薄聚合物液膜;同时,聚合物溶液与基材表面非溶剂接触发生相分离,在聚合物液膜中形成溶剂富集相与聚合物富集相。随后,将覆盖连续超薄液膜的静电纺基材进行预冷冻,液膜溶剂富集相中的冰晶成核生长,使聚合物富集相被冰晶排挤形成二维网孔结构,通过改变冷冻速率调控冰晶成核生长过程,从而实现对二维网孔结构的有效调控。在进行真空冷冻干燥,真空条件下冰晶升华,使得液膜中的溶剂与非溶剂被去除,聚合物富集相形成二维网状结构,实现静电纺纤维膜上单层纳米纤网的构筑。
30.与现有技术相比,本发明具有以下技术优势:
31.(1)本发明的单层纳米纤网可显著降低静电纺纳米纤维材料的孔径,并保持原有的高孔隙率和透过性,使复合膜材料具有低过滤阻力。
32.(2)本发明的单层纳米纤网可通过改变聚合物溶液性质、冷冻参数调控其二维网孔结构,其孔径可调性强,方法通用性强,适用范围广,可满足在多种应用场景下的过滤需求。
附图说明
33.图1为实施例1制得的单层纳米纤网/静电纺纤维复合膜电镜图;图中a为静电纺纤维,b为单层纳米纤网。
具体实施方式
34.本发明中单层纳米纤网/静电纺纤维复合膜及其制备方法,该方法具体为:首先将静电纺纤维基材在高表面能无机盐溶液中浸渍达到饱和状态;再将低表面能聚合物溶液多点位滴注于浸渍饱和的基材表面,液滴自发超铺展形成连续的超薄聚合物液膜,并发生非溶剂诱导相分离,形成溶剂富集相与聚合物富集相;接着将上述材料进行预冷冻,使聚合物富集相被溶剂富集相冰晶成核生长排挤形成二维网孔结构;最后将上述材料进行真空冷冻干燥,去除溶剂与非溶剂,获得在静电纺纤维基材上连续覆盖的单层纳米纤网。
35.本发明所得纳米纤网为单层连续的二维网状结构,直径为10~100nm,所得单层纳米纤网/静电纺纤维复合材料孔径为0.2~1μm,厚度为5~90μm,孔隙率≥80%,在过滤分离领域具有良好的应用前景。
36.下面结合附图和具体实施例对本发明进行详细说明。本技术方案中如未明确说明的制备手段、材料、结构或组成配比等特征,均视为现有技术中公开的常见技术特征。
37.实施例1
38.本实施例中单层纳米纤网/静电纺纤维复合膜及其制备方法,具体步骤如下:
39.第一步:将10g聚丙烯腈溶解在1000gn,n-二甲基乙酰胺中,加入1g十二烷基苯磺酸钠,混合搅拌,得到聚合物溶液;将1g氯化钠溶解于1000g乙醇中,混合搅拌得到无机盐溶液;
40.第二步:选取基材为聚酰胺静电纺纳米纤维膜,纤维直径为0.2μm,孔径为1μm,厚度为5μm,在无机盐溶液中浸渍60min;
41.第三步:将聚合物溶液加入注射器中,设置注射点位共有2排,每排3个,间距5cm,出液速度为20μl/s,进行滴注,在上述基材表面形成连续的超薄聚合物液膜并发生相分离;
42.第四步:将上述材料预冷冻5h,冷冻温度-60℃,降温速率10℃/min;
43.第五步:将上述材料真空冷冻干燥60h,真空度为-0.1mpa,最终得到单层纳米纤网直径为60nm,复合膜孔径为0.3μm,厚度为6μm,孔隙率为90%。图1为实施例1制得的单层纳米纤网/静电纺纤维复合膜电镜图;图中a为静电纺纤维,b为单层纳米纤网。
44.实施例2
45.本实施例中单层纳米纤网/静电纺纤维复合膜及其制备方法,具体步骤如下:
46.第一步:将5g聚偏氟乙烯溶解在1000gn,n-二甲基甲酰胺中,加入0.5g单月桂基磷酸酯,混合搅拌,得到聚合物溶液;将2g氯化锂溶解于1000g水中,混合搅拌得到无机盐溶液;
47.第二步:选取基材为聚酰胺静电纺纳米纤维膜,纤维直径为0.6μm,孔径为5μm,厚度为50μm,在无机盐溶液中浸渍40min;
48.第三步:将聚合物溶液加入注射器中,设置注射点位共有2排,每排5个,间距5cm,出液速度为10μl/s,进行滴注,在上述基材表面形成连续的超薄聚合物液膜并发生相分离;
49.第四步:将上述材料预冷冻3h,冷冻温度-80℃,降温速率15℃/min;
50.第五步:将上述材料真空冷冻干燥40h,真空度为-0.08mpa,最终得到单层纳米纤网直径为40nm,复合膜孔径为1μm,厚度为50μm,孔隙率为85%。
51.实施例3
52.本实施例中单层纳米纤网/静电纺纤维复合膜及其制备方法,具体步骤如下:
53.第一步:将10g聚苯乙烯溶解在800gn,n-二甲基乙酰胺中,加入0.4g单月桂基磷酸酯,混合搅拌,得到聚合物溶液;将18g硫酸钠溶解于800g水中,混合搅拌得到无机盐溶液;
54.第二步:选取基材为聚丙烯静电纺纳米纤维膜,纤维直径为2μm,孔径为8μm,厚度为100μm,在无机盐溶液中浸渍10min;
55.第三步:将聚合物溶液加入注射器中,设置注射点位共有2排,每排5个,间距5cm,出液速度为10μl/s,进行滴注,在上述基材表面形成连续的超薄聚合物液膜并发生相分离;
56.第四步:将上述材料预冷冻6h,冷冻温度-65℃,降温速率8℃/min;
57.第五步:将上述材料真空冷冻干燥45h,真空度为-0.06mpa,最终得到单层纳米纤网直径为100nm,复合膜孔径为0.8μm,厚度为100μm,孔隙率为80%。
58.实施例4
59.本实施例中单层纳米纤网/静电纺纤维复合膜及其制备方法,具体步骤如下:
60.第一步:将10g聚酰胺酰亚胺溶解在1200gn,n-二甲基乙酰胺中,加入2g十二烷基苯磺酸钠,混合搅拌,得到聚合物溶液;将10g氯化铜溶解于600g甲醇中,混合搅拌得到无机盐溶液;
61.第二步:选取基材为二氧化硅静电纺纳米纤维膜,纤维直径为0.4μm,孔径为2μm,厚度为20μm,在无机盐溶液中浸渍20min;
62.第三步:将聚合物溶液加入注射器中,设置注射点位共有3排,每排6个,间距1cm,出液速度为0.1μl/s,进行滴注,在上述基材表面形成连续的超薄聚合物液膜并发生相分离;
63.第四步:将上述材料预冷冻10h,冷冻温度-55℃,降温速率5℃/min;
64.第五步:将上述材料真空冷冻干燥40h,真空度为-0.1mpa,最终得到单层纳米纤网直径为10nm,复合膜孔径为0.2μm,厚度为20μm,孔隙率为95%。
65.实施例5
66.本实施例中单层纳米纤网/静电纺纤维复合膜及其制备方法,具体步骤如下:
67.第一步:将10g聚氨酯溶解在500gn-甲基吡咯烷酮中,加入0.5g十二烷基苯磺酸钠,混合搅拌,得到聚合物溶液;将10g硫酸铝溶解于600g水中,混合搅拌得到无机盐溶液;
68.第二步:选取基材为聚酰亚胺静电纺纳米纤维膜,纤维直径为0.6μm,孔径为3μm,厚度为30μm,在无机盐溶液中浸渍30min;
69.第三步:将聚合物溶液加入注射器中,设置注射点位共有3排,每排4个,间距6cm,出液速度为10μl/s,进行滴注,在上述基材表面形成连续的超薄聚合物液膜并发生相分离;
70.第四步:将上述材料预冷冻6h,冷冻温度-75℃,降温速率10℃/min
71.第五步:将上述材料真空冷冻干燥50h,真空度为-0.05mpa,最终得到单层纳米纤网直径为80nm,复合膜孔径为0.4μm,厚度为30μm,孔隙率为91%。
72.上述的对实施例的描述是为便于该技术领域的普通技术人员能理解和使用发明。熟悉本领域技术的人员显然可以容易地对这些实施例做出各种修改,并把在此说明的一般原理应用到其他实施例中而不必经过创造性的劳动。因此,本发明不限于上述实施例,本领域技术人员根据本发明的揭示,不脱离本发明范畴所做出的改进和修改都应该在本发明的保护范围之内。