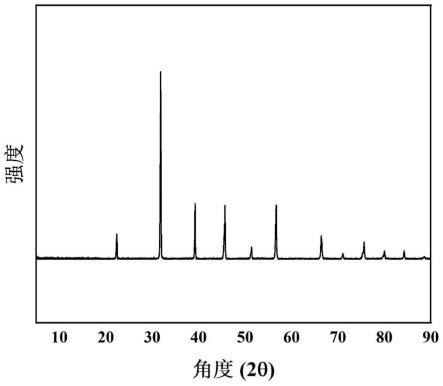
1.本发明涉及一种取向多孔压电陶瓷催化剂及其制备方法及应用,属于催化剂制备技术领域。
背景技术:2.近年来,利用压电材料驱动热力学禁阻化学反应成为一种低碳环保的新手段,比如它可以收集低品位机械能用来催化水和二氧化碳等物质转化成对人体有利的物质,从而实现了机械能向电能的转换。因此,在分解水制氢领域,压电材料具有巨大潜力。
3.专利cn202111367520公开了一种锡、铈-钛酸锶固溶体压电制氢催化剂及其制备方法与应用,其提供的压电陶瓷为固溶体粉体材料。随着与环境保护相关的法律法规不断完善,压电陶瓷粉体作为催化剂分解水产氢往往存在难以回收的问题而造成二次污染,因此利用块材作为催化剂成为未来的趋势。除此之外,块体材料也可以通过多种改性方式来提高其产氢效率。专利cn202110118320公开了一种p-n-batio3/nio异质结压电陶瓷、其制法与自供能高效制氢中的应用,其提供的其催化剂为致密陶瓷块材,具有可回收性,但比表面积仍有待提高。
4.现有技术还未有多孔压电陶瓷分解水制氢的报道。
技术实现要素:5.针对现有技术的不足,本发明的目的在于提供一种取向多孔压电陶瓷催化剂及其制备方法和应用,本发明制备的取向多孔压电陶瓷催化剂具有可回收性、高比表面积、高孔道连通性、固液分离能力。
6.为达到上述目的,本方案采取如下技术方案:
7.本发明一种取向多孔压电陶瓷催化剂,所述压电陶瓷催化剂为取向多孔结构,取向多孔结构是由宽度为10~80μm平行排列的陶瓷片层构成,所述陶瓷片层之间的孔道宽度为20~70μm。
8.本发明所提供的取向多孔压电陶瓷催化剂,取向多孔结构是由宽度为10~80μm平行排列的陶瓷片层构成,孔道从靠近样品底部的部分贯通至样品顶部,片层之间充满空气,片层之间连通性高,可以实现和外界环境的物质交换和能量交换,反应物水分子进入孔道参与催化反应,可以大幅提升分解水产氢速率。
9.当然要获得优异的分解水产氢速率,无论是陶瓷片层的厚度以及孔道的宽度都需要有效的控制,陶瓷片层过窄,则样品的孔隙率高,力学强度下降,压电陶瓷相也会减少;陶瓷片层过厚,孔道变少,不利于反应物和产物的物质交换,产氢效率降低,而若孔道宽度孔道过大,则样品的孔隙率高,力学强度下降,压电陶瓷相会减少;孔道过小,不利于反应物和产物的物质交换,产氢效率降低。
10.优选的方案,所述取向多孔压电陶瓷催化剂的体积孔隙率为30~50%,优选为30~40%,进一步优选为40%。
11.在本发明中,通过将取向多孔压电陶瓷催化剂的体积孔隙率控制在上述范围内,最终材料的产氢速率最佳,而孔隙率过大过小,都会降低产氢效率,因为孔隙率过大,力学强度下降,压电陶瓷相的含量也相应减少,及催化剂中有效部分的含量降低,产氢效率下降,而孔隙率过小,则没有办法提供足够的空间供反应物的消耗与产物的释放,不利于催化过程中的物质交换,同样会造成产氢效率下降。
12.优选的方案,所述取向多孔压电陶瓷催化剂的厚度为1~1.5mm。
13.本发明中,对于取向多孔压电陶瓷催化剂中的压电陶瓷的具体成份,没有过多的限制,在上述设定的结构下的取向多孔压电陶瓷催化剂都具有很好的产氢效果。
14.优选的方案,所述压电陶瓷催化剂中的陶瓷,选自钛酸锶钡、钛酸钡、锆钛酸钙钡中的至少一种,优选为钛酸锶钡。采用该优选方案的陶瓷,最终所得取向多孔压电陶瓷催化剂的产氢效率最优。
15.优选的方案,所述取向多孔压电陶瓷催化剂的产氢速率≥100nmol/h,优选为400nmol/h。
16.本发明一种取向多孔压电陶瓷催化剂的制备方法:将钛酸锶钡陶瓷粉体、水、分散剂、粘接剂混合获得陶瓷浆料,将陶瓷浆料置于模具中,然后将模具以5~20℃/min的降温速率下降至-90~-20℃,冷冻15~30min,然后再于-50~0℃,1~100pa的环境下干燥,获得取向多孔结构的坯料,将坯料烧结即得取向多孔压电陶瓷催化剂。
17.本发明的取向多孔压电陶瓷催化剂,通过配取陶瓷浆料后,将陶瓷浆料倒入模具,在温度梯度下将浆料转变为取向多孔结构的原料坯体,将原料坯体置于马弗炉内,在受控的反应环境下进行高温合成,而后经切割后即得取向多孔压电陶瓷催化剂,发明人发现,在本发明中,需要有效的控制冷冻的过程,若冷冻温度较高时,过冷度小,固化晶体的生长速率大于其成核速率,更有利于固化晶体的生长,从而多孔陶瓷的孔径较大;反之孔径更小,因此需要降温速度以及最终的冷冻速度控制在本发明范围内,避免多孔陶瓷的孔径过大或过小。
18.优选的方案,所述钛酸锶钡陶瓷粉体的粒径为1~3μm。
19.将钛酸锶钡陶瓷粉体的粒径控制在上述范围内,最终多孔压电陶瓷催化剂的性能最优,若粒径过大,颗粒之间接触不充分,填充不均匀,烧结后容易产生晶粒结合不够紧密;过细的颗粒容易吸附大量气体,妨碍颗粒间的接触,同样阻碍烧结。
20.优选的方案,所述钛酸锶钡陶瓷粉体的制备过程为:配取碳酸锶、碳酸钡、二氧化钛获得混合粉,将混合粉进行第一次湿法球磨,获得悬浮液,悬浮液烘干后,进行固相反应,获得粉体a,将粉体a进行第二次湿法球磨,获得粉体b,粉体b经烘干、过筛即得钛酸锶钡陶瓷粉体。
21.进一步的优选,混合粉中,按摩尔比计,ba:sr:ti:o=ba:sr:ti:o=x:(1-x):1:3。
22.更进一步的优选,所述混合粉中,按摩尔比计,碳酸锶:碳酸钡:二氧化钛=3:1:12。
23.进一步的优选,所述第一次湿法球磨的介质为无水乙醇。
24.进一步的优选,所述固相反应的温度为1200~1320℃,固相反应的时间为2~4h。
25.进一步的优选,所述第二次湿法球磨的介质为无水乙醇。
26.进一步的优选,所述第二次湿法球磨的转速为250~350r/min,第二次湿法球磨的
时间为36~72h。
27.优选的方案,所述分散剂选自柠檬酸铵、四甲基氢氧化铵、聚丙烯酸铵、聚丙烯酸酯中的至少一种。
28.优选的方案,所述粘接剂选自聚乙烯醇、聚乙烯吡咯烷酮、聚乙烯醇缩丁醛、羧甲基纤维素中的至少一种。
29.优选的方案,所述陶瓷浆料中,钛酸锶钡陶瓷粉体的体积分数为30vol.%~50vol.%。
30.发明人发现,钛酸锶钡陶瓷粉体的体积分数,对最终形成的取向多孔压电陶瓷催化剂的结构有较大的影响,控制在本发明范围内,才能获得本发明所需的结构,最终获得理想的产氢效率,而若固含量过高,浆料粘度大,冰晶生长需要克服的阻力就越大,陶瓷层厚度增加而孔道的宽度减小,孔隙率会变小;此外固含量过大还使得浆料无法在悬浮液中获得良好分散性,而若固含量过低,浆料粘度低,陶瓷层厚度减小而孔道的宽度增加,孔隙率增大。
31.优选的方案,所述分散剂的加入量为钛酸锶钡陶瓷粉体质量的0.5~2%。
32.优选的方案,所述粘接剂的加入量为钛酸锶钡陶瓷粉体质量的0.5~2%。
33.优选的方案,所述烧结的过程为,先以1~3℃/min的升温速率升温至550~650℃保温2~4h,然后再以3~5℃/min的升温速率升温至1200~1320℃保温2~4h。
34.在本发明的烧结过程,在第一阶段采用较慢的升温速率,并通过在550~650℃进行保温,使有机添加剂均匀、完全的脱除,然后升温至1200~1320℃,烧结获得取向多孔压电陶瓷催化剂,当然最后的烧结温度也需有有效控制,若烧结温度过高过低,都会降低陶瓷催化剂的性能。
35.本发明一种取向多孔压电陶瓷催化剂的应用,将所述取向多孔压电陶瓷催化剂应用于催化分解水产氢。
36.优选的方案,应用过程为:将取向多孔压电陶瓷催化剂置于纯水中,于超声条件下,催化分解产氢。
37.有益效果
38.本发明提供了一种取向多孔压电陶瓷催化剂,取向多孔结构是由宽度为10~80μm平行排列的陶瓷片层构成,孔道从靠近样品底部的部分贯通至样品顶部,片层之间充满空气,比表面积大、片层之间连通性高,可以实现和外界环境的物质交换和能量交换,反应物水分子进入孔道参与催化反应,可以大幅提升分解水产氢速率。
39.本发明通过以冰作为造孔模板,在低温低压的条件下制备得到钛酸锶钡压电陶瓷生坯,经过高温烧结后得到具有取向多孔压电陶瓷催化剂。本发明所述制备方法具有安全环保、价格低廉的特点,该取向多孔压电陶瓷催化剂在超声振动作用下,表现出较高的分解水产氢性能。
40.在优选方案中,本发明所提供的多孔取向的压电陶瓷催化剂的产氢速率≧400nmol/h。
附图说明
41.图1为实施例1中的方法制备的钛酸锶钡陶瓷粉体的xrd图。
42.图2为实施例1中的方法制备的取向多孔压电陶瓷催化剂的sem图。
43.图3为实施例1-3中的方法制备的取向多孔压电陶瓷催化剂产氢效果对比图。
具体实施方式
44.实施例1
45.将26.8克碳酸锶、6.7克碳酸钡、14.5克二氧化钛和70毫升加入球磨罐,球磨24小时后得陶瓷粉原料悬浮液;将悬浮液烘干后,将干燥后的粉体置于马弗炉内,以3℃/min升至1200℃,保温3小时进行固相反应后,得到粉体a;以酒精为介质,将粉体a加入球磨罐,行星破碎48小时后得到粉体b;粉体b烘干后,经200目和400目筛网过筛后,得钛酸锶钡陶瓷粉体。
46.在120毫升聚丙烯瓶中,加入适量锆球,并加入46.4克钛酸锶钡陶瓷粉,12毫升去离子水,0.464克聚丙烯酸酯,球磨12小时后,加入4.64克质量分数为5%的聚乙烯醇水溶液,混合2小时后,将浆料倒入模具,在10℃/min的降温速率下降至-90℃,冷冻20分钟,冷冻后的样品进行脱模,脱模样品在-50℃,10帕的条件下进行干燥,干燥后的生坯先以1℃/min升至600℃脱出有机物,再以3℃/min升至1320℃进行烧结,得到取向多孔压电钛酸锶钡陶瓷。
47.图1为实施例1中的方法制备的钛酸锶钡陶瓷粉体的xrd图。图2为实施例1中的方法制备的取向多孔压电陶瓷催化剂的sem图。从xrd图可以看出,制备的粉体物相准确;sem图显示具有片层状取向孔结构的压电陶瓷催化剂已经成功制备得到,孔道具有良好的连通性,陶瓷片层厚度约为25μm,孔间距约为30μm。
48.钛酸锶钡陶瓷切割后得到厚度为1.5毫米、孔隙率为40%的取向多孔压电陶瓷催化剂,置于装有30毫升纯水的密闭反应器中,在功率为80瓦的超声条件下,得到分解水产氢速率为442nmol/h。
49.实施例2
50.将26.8克碳酸锶、6.7克碳酸钡、14.5克二氧化钛和70毫升加入球磨罐,球磨24小时后得陶瓷粉原料悬浮液;将悬浮液烘干后,将干燥后的粉体置于马弗炉内,以3℃/min升至1200℃,保温3小时进行固相反应后,得到粉体a;以酒精为介质,将粉体a加入球磨罐,行星破碎48小时后得到粉体b;粉体b烘干后,经200目和400目筛网过筛后,得钛酸锶钡陶瓷粉体。
51.在120毫升聚丙烯瓶中,加入适量锆球,并加入34.8克钛酸锶钡陶瓷粉,12毫升去离子水,0.464克聚丙烯酸酯,球磨12小时后,加入3.48克质量分数为5%的聚乙烯醇水溶液,混合2小时后,将浆料倒入模具,在10℃/min的降温速率下降至-90℃,冷冻20分钟,冷冻后的样品进行脱模,脱模样品在-50℃,10帕的条件下进行干燥,干燥后的生坯先以1℃/min升至600℃脱出有机物,再以3℃/min升至1320℃进行烧结,得到取向多孔压电钛酸锶钡陶瓷。
52.钛酸锶钡陶瓷切割后得到厚度为1.5毫米、孔隙率为50%的取向多孔压电陶瓷催化剂,置于装有30毫升纯水的密闭反应器中,在功率为80瓦的超声条件下,得到分解水产氢速率为112nmol/h。
53.实施例3
54.将26.8克碳酸锶、6.7克碳酸钡、14.5克二氧化钛和70毫升加入球磨罐,球磨24小时后得陶瓷粉原料悬浮液;将悬浮液烘干后,将干燥后的粉体置于马弗炉内,以3℃/min升至1200℃,保温3小时进行固相反应后,得到粉体a;以酒精为介质,将粉体a加入球磨罐,行星破碎48小时后得到粉体b;粉体b烘干后,经200目和400目筛网过筛后,得钛酸锶钡陶瓷粉体。
55.在120毫升聚丙烯瓶中,加入适量锆球,并加入58克钛酸锶钡陶瓷粉,12毫升去离子水,0.464克聚丙烯酸酯,球磨12小时后,加入5.8克质量分数为5%的聚乙烯醇水溶液,混合2小时后,将浆料倒入模具,在10℃/min的降温速率下降至-90℃,冷冻20分钟,冷冻后的样品进行脱模,脱模样品在-50℃,10帕的条件下进行干燥,干燥后的生坯先以1℃/min升至600℃脱出有机物,再以3℃/min升至1320℃进行烧结,得到取向多孔压电钛酸锶钡陶瓷。
56.钛酸锶钡陶瓷切割后得到厚度为1.5毫米、孔隙率为30%的取向多孔压电陶瓷催化剂,置于装有30毫升纯水的密闭反应器中,在功率为80瓦的超声条件下,得到分解水产氢速率为237nmol/h。
57.对比例1
58.其他条件与实施例1相同,仅是加入23.2克钛酸锶钡陶瓷粉,其力学强度已经不足以支撑超声条件下的测试,取向多孔压电陶瓷催化剂在超声条件下会破碎,并伴有大量陶瓷粉体脱落,不能实现多孔压电陶瓷催化剂可回收的优势。