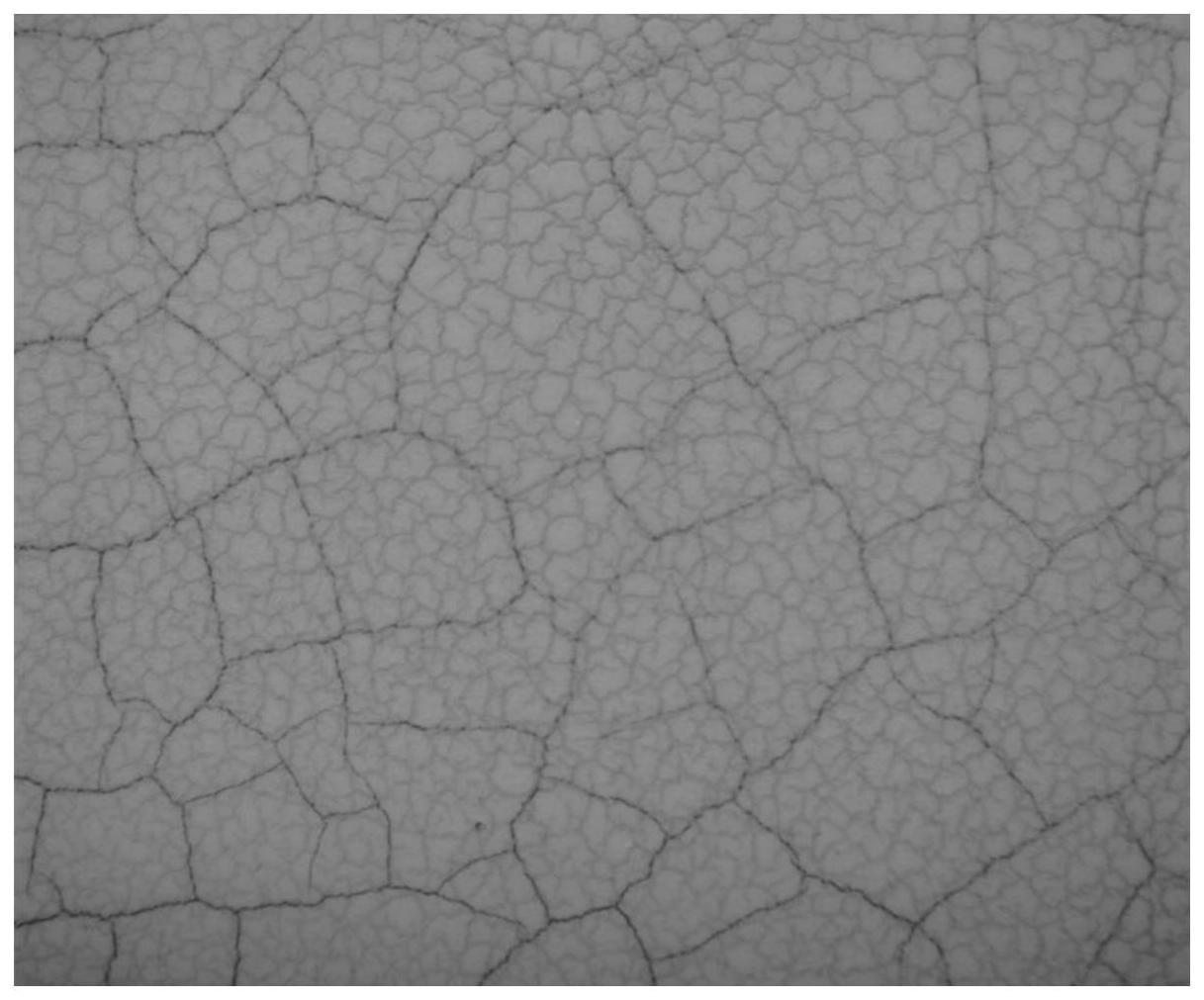
1.本发明涉及涂料技术领域,尤其涉及一种可控裂纹涂层及其制备方法。
背景技术:2.哥窑的主要特点是瓷器釉面开裂,系利用胎和釉的热胀冷缩的不同性能在焙烧后冷却时形成或大或小的开片。
3.哥窑瓷器中,以“金丝铁线”为贵,即大开片如冰裂状、裂纹处为铁黑色,所谓“铁线”;小开片如鱼籽状,裂纹处为金黄色,所谓“金丝”。其大裂纹嵌套小裂纹、大小裂纹相互交织,形成一种错落有致的立体美感。
4.用涂料的配套涂层技术解决方案来实现类似哥窑瓷器的金丝铁线效果,尚未见有报道。
5.cn104260503a公开了一种低质材改性杨木家具表面特种涂装涂层及涂饰方法,其结构是包括低质材改性杨木基材和多层涂层,其中多层涂层在低质材改性杨木基材上;所述的多层涂层由封闭底漆层、聚氨酯(pu)黄底漆层、局部填灰、pu白底漆层、白色裂纹漆层、格丽斯涂层、硝基清面漆层从下到上依次堆放而成。其涂饰方法,包括如下工艺步骤:1)白坯处理,2)封闭底漆,3)第一次涂层砂磨,4)头度底漆,5)第二次涂层砂磨,6)局部填灰,7)二度底漆,8)挖灰打磨,9)喷裂纹漆,10)做仿古漆,11)清面漆。其公开的方法拓宽了实木家具用低质材提质加工表面装饰技术的新领域,但其裂纹层次及效果远不及哥窑。
6.cn112371466a公开了一种立体裂纹涂层的制备方法、立体裂纹涂层、灯具配件和灯具。其公开的制备方法包括:在基底上涂敷底漆;对底漆进行第一次干燥;在底漆上涂敷面漆,底漆与面漆的收缩率比大于或等于200;对面漆进行第二次干燥,得到基底上的立体裂纹涂层。通过利用底漆和面漆的不同收缩率,在干燥后,面漆裂开形成不同形状的自然裂纹纹理,从而得到立体裂纹涂层。其公开的制备方法制备的涂层具有自然、多样的纹理,立体效果好,质感强。但其裂纹效果如大裂纹过于粗大、裂纹边缘不整齐、裂纹中间残存细碎漆片即存在“孤岛”现象,而其小裂纹比较短小、似裂未裂不够清晰,离哥窑“金丝铁线”的裂纹效果差距很远。
[0007]“金丝铁线”的哥窑磁器至少要经两次一千多度高温烧结,以便分别形成均匀的粗裂纹和细裂纹,工艺繁复,能耗很高,且胎体仅仅限于陶瓷;“金丝铁线”的艺术风格如果要体现在竹木家具/工艺品、混凝土墙面、金属构件等表面,并避免上述缺点,显然需要开发常温干燥的可控裂纹涂层及工艺才能匹配。
[0008]
综上所述,开发能满足不同基底的可控裂纹涂层的制备方法至关重要。
技术实现要素:[0009]
针对现有技术的不足,本发明的目的在于提供一种可控裂纹涂层及其制备方法,所述制备方法利于形成可控裂纹涂层,尤其是在多种基底上形成具有仿哥窑“金丝铁线”陶瓷开片效果的裂纹涂层。
[0010]
为达此目的,本发明采用以下技术方案:
[0011]
第一方面,本发明提供一种可控裂纹涂层的制备方法,所述制备方法包括如下步骤:
[0012]
(1)在基材上喷涂至少一道(例如一道喷一个十字、两道两个十字、三道三个十字、四道四个十字等)反应固化型有色底漆,干燥,形成第一底漆层;
[0013]
(2)在所述第一底漆层上喷涂第一单组分有色裂纹涂料,干燥,形成第一裂纹涂层;
[0014]
(3)在所述第一裂纹涂层上喷涂一至两道(例如一道喷一个十字、两道两个十字等)反应固化型透明底漆,干燥,形成第二底漆层;
[0015]
(4)在所述第二底漆层上喷涂第二单组分透明裂纹涂料,干燥,形成第二裂纹涂层;
[0016]
(5)采用着色剂擦拭第二裂纹涂层表面,并使第二裂纹涂层的裂缝处着床有着色剂,同时将第二裂纹涂层之上的多余的着色剂擦拭干净,干燥后喷涂一道聚氨酯清漆,进一步干燥,得到所述可控精细裂纹涂层。
[0017]
本发明中,所得到的可控裂纹涂层具有类似哥窑金丝铁线效果。
[0018]
优选地,所述步骤(1)中,还包括测试所述反应固化型有色底漆的表干时间和实干时间。
[0019]
本发明中,所述表干时间的测试方法按照gb/t 1728-2020表面干燥时间的乙法进行;所述实干时间按照gb/t 1728-2020实际干燥时间的甲法进行。
[0020]
优选地,所述步骤(1)中,所述干燥的温度为5-35℃,例如10℃、15℃、20℃、25℃、30℃等。
[0021]
优选地,所述干燥的湿度为30%-75%,例如35%、40%、45%、50%、55%、60%、65%、70%等。
[0022]
优选地,所述干燥的时间≥所述表干时间的1.5-2.5倍,例如1.6倍、1.7倍、1.8倍、1.9倍、2.0倍、2.1倍、2.2倍、2.3倍、2.4倍等,进一步优选2倍;
[0023]
所述干燥的时间≤所述实干时间的35%-45%,例如36%、37%、38%、39%、40%、41%、42%、43%、44%等,进一步优选40%。
[0024]
本发明中,控制反应固化型有色底漆的干燥时间在所述范围内,是产生可控裂纹的窗口期,干燥时间太短,会造成后道裂纹漆开裂过于粗大、裂纹不够精细;干燥时间太长,会造成后道裂纹漆开裂不充分或无法开裂。
[0025]
优选地,所述步骤(1)中,所述反应固化型有色底漆包括反应固化型黑色底漆,除黑色外也可选灰色、深啡色、棕褐色等。
[0026]
优选地,所述反应固化型黑色底漆包括双组份聚氨酯黑色底漆、单组分潮气固化聚氨酯黑色底漆、单组分黑色醇酸磁漆或双组份环氧黑色底漆中的任意一种,其中典型但非限制性的选择包括:双组份聚氨酯黑色底漆,单组分黑色醇酸磁漆、双组份环氧黑色底漆等,这些漆液固化反应温和,利于控制后道裂纹漆开裂;反之,较剧烈反应的双组分不饱和聚酯底漆及紫外光uv固化底漆不适用,因其漆膜在实干前有较剧烈收缩导致上层裂纹涂层无法实现可控开裂。
[0027]
优选地,所述基材的材质包括竹木、混凝土或金属中的任意一种或至少两种的组
合,其中典型但非限制性的组合包括:竹木和混凝土的组合,混凝土和金属的组合,竹木、混凝土和金属的组合等;基材不同所选的底漆品种也应不同,如竹木可优选聚氨酯类底漆、混凝土和金属可优选环氧类底漆等。
[0028]
优选地,所述步骤(2)中,所述第一单组分有色裂纹涂料的涂布量为6-8m2/kg,例如6.2m2/kg、6.4m2/kg、6.6m2/kg、6.8m2/kg、7.0m2/kg、7.2m2/kg、7.4m2/kg、7.6m2/kg、7.8m2/kg等。
[0029]
本发明中,所述第一单组分有色裂纹涂料在6-8m2/kg范围内,控制在此范围的原因在于易形成合适的“冰裂纹”板块开片;涂布量过高,会造成开片过大、裂纹过粗,不美观;涂布量过低,会造成细碎开片、达不到“铁线”效果。
[0030]
优选地,所述第一裂纹涂层的厚度为30-40μm,例如32μm、34μm、36μm、38μm等。
[0031]
本发明中,所述第一裂纹涂层的厚度为30-40μm,控制在此范围的原因在于易形成合适的“冰裂纹”板块开片;厚度过厚,会造成开片过大、裂纹过粗,不美观;厚度过薄,会造成细碎开片、达不到“铁线”效果。
[0032]
优选地,所述步骤(2)中,所述干燥为至所述第一单组分有色裂纹涂料实干后。
[0033]
优选地,所述第一裂纹涂层呈现冰裂状大开片,所述冰裂状大开片的宽度为0.3-0.8mm,例如0.4mm、0.5mm、0.6mm、0.7mm等。
[0034]
优选地,所述第一裂纹涂层的裂缝呈现底漆层的颜色。
[0035]
优选地,所述第一单组分有色裂纹涂料包括单组分白色裂纹涂料,除白色外也可选浅灰白色、浅绿色、浅粉色等。
[0036]
优选地,所述单组分白色裂纹涂料包括白色硝基裂纹漆和/或白色丙烯酸裂纹漆。
[0037]
优选地,所述步骤(3)中,还包括测试所述反应固化型透明底漆的表干时间和实干时间。
[0038]
本发明中,所述表干时间的测试方法按照gb/t 1728-2020表面干燥时间的乙法进行;所述实干时间按照gb/t 1728-2020实际干燥时间的甲法进行。
[0039]
优选地,所述步骤(3)中,所述干燥的温度为5-35℃,例如10℃、15℃、20℃、25℃、30℃等。
[0040]
优选地,所述干燥的湿度为30%-75%,例如35%、40%、45%、50%、55%、60%、65%、70%等。
[0041]
优选地,所述干燥的时间≥所述表干时间的1.5-2.5倍,例如1.6倍、1.7倍、1.8倍、1.9倍、2.0倍、2.1倍、2.2倍、2.3倍、2.4倍等,进一步优选2倍;
[0042]
所述干燥的时间≤所述实干时间的35%-45%,例如36%、37%、38%、39%、40%、41%、42%、43%、44%等,进一步优选40%。
[0043]
本发明中,控制反应固化型透明底漆的干燥时间在所述范围内,是产生可控裂纹的窗口期,干燥时间太短,会造成后道裂纹漆开裂过于粗大、裂纹不够精细;干燥时间太长,会造成后道裂纹漆开裂不充分或无法开裂。
[0044]
优选地,所述步骤(3)中,所述反应固化型透明底漆包括双组份聚氨酯透明底漆、单组分潮气固化聚氨酯透明底漆、单组分醇酸透明底漆或双组份环氧透明底漆中的任意一种或至少两种的组合,其中典型但非限制性的选择包括:双组份聚氨酯透明底漆,单组分醇酸透明底漆、双组份环氧透明底漆等,这些漆液固化反应温和,利于控制后道裂纹漆开裂;
反之,较剧烈反应的双组分不饱和聚酯透明底漆及紫外光uv固化透明底漆不适用,因其漆膜在实干前有较剧烈收缩导致上层裂纹涂层无法实现可控开裂。
[0045]
优选地,所述步骤(4)中,所述第二单组分透明裂纹涂料的涂布量为12-15m2/kg,例如12.5m2/kg、13m2/kg、13.5m2/kg、14m2/kg、14.5m2/kg等。
[0046]
本发明中,所述第二单组分透明裂纹涂料在12-15m2/kg范围内,控制在此范围的原因在于易形成合适的“鱼籽状裂纹”板块开片;涂布量过低,会造成极细碎开片,不美观;涂布量过高,会造成开片过大、裂纹过粗,达不到“金丝”效果。
[0047]
优选地,所述第二裂纹涂层的厚度为15-25μm,例如16μm、18μm、20μm、22μm、24μm、25μm等。
[0048]
本发明中,所述第二裂纹涂层的厚度为15-25μm,控制在此范围的原因在于易形成合适的“鱼籽状裂纹”板块开片;涂布量过低,会造成极细碎开片,不美观;涂布量过高,会造成开片过大、裂纹过粗,达不到“金丝”效果。
[0049]
优选地,所述步骤(4)中,所述干燥至所述第二单组分透明裂纹涂料实干后。
[0050]
优选地,所述第二裂纹涂层呈现鱼籽状小开片,所述鱼籽状小开片的宽度为0.05-0.2mm,例如0.06mm、0.08mm、0.10mm、0.12mm、0.14mm、0.16mm、0.18mm等。
[0051]
优选地,所述单组分透明裂纹涂料包括硝基透明裂纹漆和/或丙烯酸透明裂纹漆。
[0052]
优选地,所述步骤(5)中,所述着色剂包括黄色着色剂。
[0053]
优选地,所述黄色着色剂包括金属络合油溶黄色染料和/或氧化铁黄色安巴粉格丽斯。
[0054]
优选地,所述聚氨酯清漆包括双组分聚氨酯清漆。
[0055]
作为优选的技术方案,所述制备方法包括如下步骤:
[0056]
(1)在基材上喷涂至少一层黑色反应固化型双组分聚氨酯底漆,干燥,控制干燥的时间在所述表干时间的1.5-2.5倍至实干时间的35%-45%之间,形成第一底漆层;
[0057]
(2)在所述第一底漆层上按照涂布量为6-8m2/kg喷涂单组分白色裂纹涂料,干燥至所述单组分白色裂纹涂料实干,形成厚度为30-40μm的第一裂纹涂层,所述第一裂纹涂层呈现冰裂状大开片,所述冰裂状大开片的宽度为0.3-0.8mm,裂纹颜色为黑色;
[0058]
(3)在所述第一裂纹涂层上喷涂一至两道反应固化型双组分聚氨酯透明底漆,干燥,控制干燥的时间在所述表干时间的1.5-2.5倍至实干时间的35%-45%之间,形成第二底漆层;
[0059]
(4)在所述第二底漆涂层上按照涂布量为12-15m2/kg喷涂单组分透明裂纹涂料,干燥至单组分透明裂纹涂料实干,形成厚度为15-25μm第二裂纹涂层,所述第二裂纹涂层呈现鱼籽状小开片,所述鱼籽状小开片的宽度为0.05-0.2mm;
[0060]
(5)采用黄色着色剂擦拭第二裂纹涂层表面,并使第二裂纹涂层的裂缝处着床有黄色着色剂,擦净非裂纹处涂层表面的多余黄色着色剂,干燥后喷涂聚氨酯清漆,进一步干燥至聚氨酯清漆实干,得到所述可控裂纹涂层。
[0061]
第二方面,本发明提供一种可控裂纹涂层,所述可控裂纹涂层由第一方面所述的方法制备;
[0062]
所述可控裂纹涂层具有哥窑金丝铁线效果。
[0063]
本发明中,所述制备方法利于形成可控裂纹涂层,尤其是在多种基底上形成具有
仿哥窑“金丝铁线”陶瓷开片效果的裂纹涂层。在步骤(1)中,通过反应固化型底漆的反应固化,利用其自表干至实干之间的最优时间段内漆膜有序有限的半固化收缩、以及该半固化漆膜底层为后道裂纹漆所有限溶胀,为后道裂纹漆提供有限度的“板块漂移”、为受控精细裂纹的形成提供基础,避免了选用其他热塑性单组分自干底漆对后道裂纹漆的非受控开裂,参见图1a和图1b;步骤(2)中,选择单组分裂纹涂料及适度厚涂,避免了双组份反应型裂纹涂料的不受控开裂或无法开裂问题,更利于形成板块相对较大的裂纹,以形成“铁线”效果;类似的,步骤(3)、(4)、(5)中,选择反应固化型底漆自表干至实干之间的最优时间段内获得半干燥固化的漆膜、选择单组分裂纹涂料薄涂、以及选择着色剂对细裂纹进行着色,利于形成可控的、板块相对较小的裂纹,以形成“金丝”效果,参见图2。
[0064]
相对于现有技术,本发明具有以下有益效果:
[0065]
本发明所述方法更利于形成可控裂纹涂层,尤其是在多种基底上形成具有仿哥窑“金丝铁线”陶瓷开片效果的裂纹涂层;也可在陶坯烧成后替代瓷釉制做仿哥窑瓷器和工艺品而无需高温烧结,可应用于木器家具或铁艺的仿哥窑风格,可应用于墙面仿哥窑艺术涂装效果。
附图说明
[0066]
图1a是可控精细裂纹涂层的形貌示意图;
[0067]
图1b是不可控裂纹涂层的形貌示意图;
[0068]
图2是实施例1所述可控裂纹涂层的形貌示意图。
具体实施方式
[0069]
为便于理解本发明,本发明列举实施例如下。本领域技术人员应该明了,所述实施例仅仅是帮助理解本发明,不应视为对本发明的具体限制。
[0070]
实施例1
[0071]
本实施例提供一种可控裂纹涂层,其形貌示意图如图2所示,所述可控裂纹涂层由如下方法制备:
[0072]
(1)在已处理的木器家具表面,喷涂一道紫荆花净味聚氨酯黑色底漆(购于紫荆花,型号为zjp4310-10398n),测得其表干时间为13分钟、实干时间为2.5h,在温度25℃、湿度55%条件下自干30分钟后,形成第一底漆层;
[0073]
(2)按7m2/kg的平均涂布量,误差在0.5m2/kg内,喷涂紫荆花硝基裂纹白漆(购于紫荆花,型号为691-01a),数十秒后即出现裂纹平均宽度为0.7mm的大裂纹,波动幅度在0.05mm范围内,裂缝颜色为黑色,待12小时实干后,形成第一裂纹涂层;
[0074]
(3)在所述第一裂纹涂层上喷涂一道紫荆花净味聚氨酯特清透明底漆(购于紫荆花,型号为zjp3312n),干燥,测得其表干时间为15分钟、实干时间为2.5h,在温度25℃、湿度55%条件下自干30分钟后,形成第二底漆层;
[0075]
(4)按13m2/kg的涂布量,误差在0.5m2/kg内,喷涂紫荆花硝基透明裂纹清漆(购于紫荆花,型号为lw-99),数十秒后即出现裂纹宽度为0.1mm的细小裂纹,波动幅度在0.02mm范围内,待4小时实干后,形成第二裂纹涂层;
[0076]
(5)以棉布蘸取紫荆花高浓度黄色色精(购于紫荆花,型号为694-002)擦拭表面,
细小裂纹处着满黄色后将漆面多余色精清理干净,最后喷涂一道紫荆花高耐黄变聚氨酯清面漆(购于紫荆花,型号为zjp6697f7)罩面至实干,得到所述仿哥窑金丝铁线效果可控裂纹涂层。
[0077]
实施例2
[0078]
本实施例提供一种可控裂纹涂层,所述可控裂纹涂层由如下方法制备:
[0079]
(1)在已处理的竹器家具表面,喷涂一道紫荆花潮固化聚氨酯黑色底漆(购于紫荆花,型号为d899-88),其表干时间为15分钟,实干时间为4小时10分钟,在温度25℃、湿度55%条件下自干40分钟后,形成第一底漆层;
[0080]
(2)按7.5m2/kg的平均涂布量,误差在0.5m2/kg内,喷涂紫荆花硝基裂纹白漆(购于紫荆花,型号为691-01a),数十秒后即出现裂纹平均宽度为0.6mm的大裂纹,波动幅度在0.05mm范围内,裂缝颜色为黑色,待12小时实干后,形成第一裂纹涂层;
[0081]
(3)在所述第一裂纹涂层上喷涂一道紫荆花潮固化聚氨酯清漆(购于紫荆花,型号为d899),其表干时间为15分钟,实干时间为4小时,在温度25℃、湿度55%条件下自干30分钟后,形成第二底漆层;
[0082]
(4)按13.5m2/kg的涂布量,误差在0.5m2/kg内,喷涂紫荆花硝基透明裂纹清漆(购于紫荆花,型号为lw-99),数十秒后即出现裂纹宽度为0.1mm的细小裂纹,波动幅度在0.02mm范围内,待4小时实干后,形成第二裂纹涂层;
[0083]
(5)以棉布蘸取紫荆花鲜黄色格丽斯(购于紫荆花,型号为zjcb32a)擦拭表面,细小裂纹处着满黄色后将漆面多余色黄色格丽斯清理干净,最后喷涂一道紫荆花高耐黄变聚氨酯清面漆(购于紫荆花,型号为zjp6697f7)罩面至实干,得到所述仿哥窑金丝铁线效果可控裂纹涂层。
[0084]
实施例3
[0085]
本实施例提供一种可控裂纹涂层,所述可控裂纹涂层由如下方法制备:
[0086]
(1)在已处理的混凝土墙面,喷涂一道紫荆花黑色醇酸磁漆(购于紫荆花,型号为zipc10t-88),测得其表干时间为40分钟,实干时间为5小时,在温度25℃、湿度55%条件下自干1小时后,形成第一底漆层;
[0087]
(2)按7.5m2/kg的平均涂布量,误差在0.5m2/kg内,喷涂紫荆花水性丙烯酸裂纹白漆(购于紫荆花,型号为zjw4320f0),数十秒后即出现裂纹平均宽度为0.5mm的大裂纹,波动幅度在0.05mm范围内,裂缝颜色为黑色,待24小时实干后,形成第一裂纹涂层;
[0088]
(3)在所述第一裂纹涂层上喷涂一道紫荆花醇酸清漆(购于紫荆花,型号为zipc10t-99),测得其表干时间为40分钟,实干时间为5小时,在温度25℃、湿度55%条件下自干1小时后,形成第二底漆层;
[0089]
(4)按14.5m2/kg的涂布量,误差在0.5m2/kg内,喷涂紫荆花水性丙烯酸裂纹清漆(购于紫荆花,型号为zjw4329),数十秒后即出现裂纹平均宽度为0.1mm的细小裂纹,波动幅度在0.02mm范围内,待12小时实干后,形成第二裂纹涂层;
[0090]
(5)以棉布蘸取紫荆花鲜黄色格丽斯(购于紫荆花,型号为zjcb32a)擦拭表面,细小裂纹处着满黄色后将漆面多余色黄色格丽斯清理干净,最后喷涂一道紫荆花高耐黄变聚氨酯清面漆(购于紫荆花,型号为zjp6697f7)罩面至实干,得到所述仿哥窑金丝铁线效果可控裂纹涂层。
[0091]
实施例4
[0092]
本实施例提供一种可控裂纹涂层,所述可控裂纹涂层由如下方法制备:
[0093]
(1)在已处理的金属工件表面,喷涂一道紫荆花双组分灰色环氧底漆(购于紫荆花,牌号为zipc20p-204),测得其表干时间为20分钟、实干时间为6h,在温度25℃、湿度55%条件下自干50分钟后,形成第一底漆层;
[0094]
(2)按6.5m2/kg的平均涂布量,误差在0.5m2/kg内,喷涂紫荆花硝基裂纹白漆(购于紫荆花,型号为691-01a),数十秒后即出现裂纹平均宽度为0.6mm的大裂纹,波动幅度在0.05mm范围内,裂缝颜色为灰色,待12小时实干后,形成第一裂纹涂层;
[0095]
(3)在所述第一裂纹涂层上喷涂一道紫荆花双组分环氧透明底漆(购于紫荆花,牌号为zipc20p-101),测得其表干时间为25分钟,实干时间为6小时,在温度25℃、湿度55%条件下自干50分钟后,形成第二底漆层;
[0096]
(4)按14.5m2/kg的涂布量,误差在0.5m2/kg内,喷涂紫荆花硝基透明裂纹清漆(购于紫荆花,型号为lw-99),数十秒后即出现裂纹宽度为0.09mm的细小裂纹,波动幅度在0.02mm范围内,待4小时实干后,形成第二裂纹涂层;
[0097]
(5)以棉布蘸取紫荆花高浓度黄色色精(购于紫荆花,型号为694-002)擦拭表面,细小裂纹处着满黄色后将漆面多余色精清理干净,最后喷涂一道紫荆花高耐黄变聚氨酯清面漆(购于紫荆花,型号为zjp6697f7)罩面至实干,得到所述仿哥窑金丝铁线效果可控裂纹涂层。
[0098]
实施例5-8
[0099]
本实施例与实施例1的区别在于步骤(1)中所述自干时间分别为26min(实施例5)、1h(实施例6)、18min(实施例7)和1.3h(实施例8),其余均与实施例1相同。
[0100]
对比例1
[0101]
本对比例与实施例1的区别在于将所述紫荆花硝基裂纹白漆替换为双组份聚氨酯白色裂纹漆,所述双组份聚氨酯白色裂纹漆按cn102604519a发明专利公开的pu裂纹涂料配方及工艺制作而成。
[0102]
对比例2
[0103]
本对比例与实施例1的区别在于将所述紫荆花硝基透明裂纹清漆替换为双组份聚氨酯透明裂纹漆,所述双组份聚氨酯透明裂纹漆按cn102604519a发明专利公开的pu裂纹涂料配方(不添加钛白粉等颜料)及工艺制作而成。
[0104]
性能测试:
[0105]
将实施例1-8和对比例1-2所述方法制备的可控裂纹涂层进行如下测试:
[0106]
观察可控裂纹涂层在制备中第一裂纹涂层裂缝形貌和第二裂纹涂层裂缝形貌,第一裂纹涂层裂缝形貌按照裂纹形貌的分布均匀性和宽度的合理性(在0.3-0.8mm为佳)依次分为ⅰ级、ⅱ级、ⅲ级、ⅳ级,其中,ⅰ级裂纹分布均匀、裂纹宽度在0.6-0.8mm之间,ⅱ级裂纹分布均匀、宽度在0.5-0.6mm之间,ⅲ级裂纹分布均匀、宽度在0.3-0.5mm之间,ⅳ级无裂纹分布、宽度0mm(不开裂);第二裂纹涂层裂纹分为ⅰ级、ⅳ级,其中ⅰ级裂纹分布均匀、裂纹宽度为0.08-0.2mm(因裂纹细小,不再分ⅱ级、ⅲ级),ⅳ级无裂纹分布、宽度0mm(不开裂)。
[0107]
测试结果汇总于表1中。
[0108]
表1
[0109][0110]
分析表1可知,本发明所述方法更利于形成可控裂纹涂层,尤其是在多种基底上形成具有仿哥窑“金丝铁线”陶瓷开片效果的裂纹涂层,图2中显示出此效果。
[0111]
分析对比例1与实施例1可知,对比例1性能不如实施例1,证明以双组份裂纹涂料代替第一单组分裂纹涂料不利于形成可控裂纹涂层。
[0112]
分析对比例2与实施例1可知,对比例2性能不如实施例1,证明以双组份裂纹涂料代替第二单组分裂纹涂料不利于形成可控裂纹涂层。
[0113]
分析实施例5-8与实施例1可知,实施例7-8性能不如实施例5-6,证明在形成底漆层时,控制干燥的时间在表干时间的1.5-2.5倍至实干时间的35%-45%之间,更利于形成可控裂纹涂层,尤其是控制在表干时间的2倍至实干时间的40%之间。
[0114]
申请人声明,本发明通过上述实施例来说明本发明的详细方法,但本发明并不局限于上述详细方法,即不意味着本发明必须依赖上述详细方法才能实施。所属技术领域的技术人员应该明了,对本发明的任何改进,对本发明产品各原料的等效替换及辅助成分的添加、具体方式的选择等,均落在本发明的保护范围和公开范围之内。