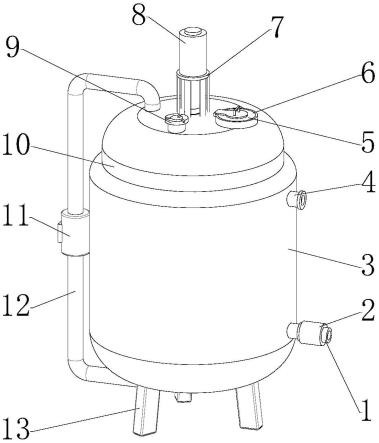
1.本实用新型涉及化工生产设备技术领域,具体涉及一种循环式化工反应釜。
背景技术:2.聚酰胺树脂具有良好的综合性能,广泛应用于各种领域,在聚酰胺树脂的生产过程中,通常需要利用反应釜对化工原料进行生产,但是现有反应釜在使用过程中存在一定问题,主要在于化学反应过程中的气体反应物和催化剂需要与液态或固态反应物充分接触,传动的加工方式多采用电机进行搅拌混合,在于液态或固态原材料接触时的效率较低,进而影响化工反应的效率,不能够满足现阶段的使用需求。
技术实现要素:3.本实用新型的目的就在于为了解决上述问题而提供一种循环式化工反应釜,以解决现有技术中反应釜采用搅拌混合的方式进行加工,在于液态或固态原材料接触时的效率较低,进而影响化工反应的效率,不能够满足现阶段的使用需求的技术问题。本实用新型提供的诸多技术方案中优选的技术方案中采用回流管配合回流泵,将反应釜本体内部的物料循环导入至反应釜本体内,并通过积料盘与刮板的配合,使得物料平铺展开,能够增加物料与气体反应物之间的接触几率,进而提升化工反应的速率的技术效果,详见下文阐述。
4.为实现上述目的,本实用新型提供了以下技术方案:
5.本实用新型提供的循环式化工反应釜,包括:
6.反应釜本体,用于进行化工反应;
7.积料盘,水平布置在反应釜本体内,所述积料盘上贯穿开设有下料孔;
8.传动杆,竖向布置在反应釜本体内,所述传动杆的外壁上设有推送物料进入下料孔的刮板;
9.旋转电机,设置在反应釜本体的顶部中心处,用于带动传动杆旋转;
10.回流管,设置在反应釜本体的一侧,所述回流管的两端分别与反应釜本体的底部和顶部相连通;
11.循环泵,设置在回流管上,用于带动反应釜内部物料导入回流管内循环;
12.排料管,设置在反应釜本体的底部,用于将反应釜本体内部的制成品排出;
13.所述反应釜本体的顶部设有主进料管和副进料管,所述主进料管位于副进料管的一侧,所述主进料管和副进料管上设有可翻转的密封盖。
14.作为优选,所述刮板沿传动杆中心呈对称结构布置,且刮板与积料盘之间设有30
°
的倾角。
15.作为优选,所述反应釜本体的外壁上设有换热夹层,所述换热夹层的侧壁上设有进液管和出液管,所述进液管位于出液管的下方。
16.作为优选,所述副进料管上设有节流阀。
17.作为优选,所述反应釜本体的顶部设有用于安装旋转电机的承托支架。
18.作为优选,所述反应釜本体的底部设有底架。
19.作为优选,所述排料管上设有下料阀。
20.有益效果在于:
21.1、采用回流管配合回流泵,将反应釜本体内部的物料循环导入至反应釜本体内,并通过积料盘与刮板的配合,使得物料平铺展开,能够增加物料与气体反应物之间的接触几率,进而提升化工反应的速率;
22.2、采用倾角结构设计,能够便于利用刮板对物料进行推送移动,提升下料和循环的效率;
23.3、通过导热液在换热夹层内部进行循环流动,从而使得反应釜本体内部的温度状态保持在合适区间,进而提升化工反应的效率;
24.4、通过节流阀能够控制导热液循环进入装置内部,进而能够通过控制导热液的流动来调节反应釜本体内部的温度状态,以便于适配不同的化工反应;
25.5、采用主进料管和副进料管的结构设计,能够根据实际的生产需要将不同种类的物料通过主进料管和副进料管分别进行添加,在保证添加效率的同时,减少混料的几率,便于后续进行清洁;
26.6、通过下料阀的设计,能够自动控制排料,提升生产的自动化程度。
附图说明
27.为了更清楚地说明本实用新型实施例或现有技术中的技术方案,下面将对实施例或现有技术描述中所需要使用的附图作简单地介绍,显而易见地,下面描述中的附图仅仅是本实用新型的一些实施例,对于本领域普通技术人员来讲,在不付出创造性劳动的前提下,还可以根据这些附图获得其他的附图。
28.图1是本实用新型的立体结构视图一;
29.图2是本实用新型的主视图;
30.图3是本实用新型的俯视图;
31.图4是本实用新型的内部结构视图;
32.图5是本实用新型的立体结构视图二。
33.附图标记说明如下:
34.1、进液管;2、节流阀;3、换热夹层;4、出液管;5、密封盖; 6、主进料管;7、承托支架;8、旋转电机;9、副进料管;10、反应釜本体;11、循环泵;12、回流管;13、底架;14、排料管;15、积料盘;16、刮板;17、传动杆;18、下料阀;19、下料孔。
具体实施方式
35.为使本实用新型的目的、技术方案和优点更加清楚,下面将对本实用新型的技术方案进行详细的描述。显然,所描述的实施例仅仅是本实用新型一部分实施例,而不是全部的实施例。基于本实用新型中的实施例,本领域普通技术人员在没有做出创造性劳动的前提下所得到的所有其它实施方式,都属于本实用新型所保护的范围。
36.参见图1-图5所示,本实用新型提供了循环式化工反应釜,包括:
37.反应釜本体10,用于进行化工反应,反应釜本体10为竖向布置的圆筒状结构,内部
用于盛放用于化学反应的原料进行反应;
38.积料盘15,水平布置在反应釜本体10内,积料盘15用于盛放投入反应釜本体10内部的物料,进而便于物料平铺展开,增加与气体反应物的接触几率,进而提升化工生产的效率,积料盘15的数量有两个,上下平行布置,能够增加铺设面积,进一步增加反应物的接触几率,且积料盘15和刮板16的数量可以根据使用需求进行调节,积料盘15上贯穿开设有下料孔19,下料孔19均匀布置在积料盘15 上,用于供物料穿过;
39.传动杆17,竖向布置在反应釜本体10内,传动杆17的外壁上设有推送物料进入下料孔19的刮板16,每个积料盘15上设有两个呈中心对称结构布置的刮板16,刮板16通过螺钉进行安装固定安装在传动杆17上,其中一个刮板16与积料盘15之间预留有间隙,该间隙可以通过调节刮板16的安装高度进行调节,通常为10mm,而另外一个刮板16贴紧积料盘15的表面,用于将积料盘15上的刮板16 推送至下料孔19内,能够在使用时,通过传动杆17旋转带动刮板 16移动,进而使得刮板16将积料盘15上的物料逐渐刮平,从而使得物料平铺展开,增加与气体反应物的接触面积;
40.旋转电机8,设置在反应釜本体10的顶部中心处,用于带动传动杆17旋转,旋转电机8倒置安装在反应釜本体10的顶面中心处,其底部的传动轴与传动杆17通过联轴器传动连接,以便于旋转电机 8带动传动杆17旋转;
41.回流管12,设置在反应釜本体10的一侧,回流管12的两端分别与反应釜本体10的底部和顶部相连通,采用此种结构设计,能够使得回流管12在输送过程中,将物料由反应釜本体10底部重新导入至反应釜本体10顶部,进而能够使得物料不断循环,提升化工材料制备时的效率;
42.循环泵11,设置在回流管12上,用于带动反应釜内部物料导入回流管12内循环,用于提供输送的动力。
43.排料管14,设置在反应釜本体10的底部,用于将反应釜本体10 内部的制成品排出;
44.反应釜本体10的顶部设有主进料管6和副进料管9,主进料管6 位于副进料管9的一侧,进料管上设有可翻转的密封盖5,采用主进料管6和副进料管9的结构设计,能够根据实际的生产需要将不同种类的物料通过主进料管6和副进料管9分别进行添加,在保证添加效率的同时,减少混料的几率,便于后续进行清洁;
45.使用时,向反应釜本体10内部投入液态或固态反应物,同时投入气态反应物,而液态或固态反应物会落在积料盘15上进行堆放,此时旋转电机8工作带动传动杆17不断旋转,进而使得传动杆17外壁上的刮板16带动物料平铺展开在积料盘15上,进而能够增加物料与气体反应物的接触几率,而在此过程中,多余物料会穿过积料盘 15表面的下料孔19,并最终落入在反应釜本体10的底部,而循环泵 11工作,将反应釜本体10底部的物料泵入回流管12内,从而重新输送至反应釜本体10的顶部进行重新投放,循环反复能够使得反应釜本体10内部物料充分与液体进行循环接触,以提升化工反应的效率,确保反应的完成度,减少原材料的浪费。
46.在另外一个实施例中,刮板16沿传动杆17中心呈对称结构布置,且刮板16与积料盘15之间设有30
°
的倾角,采用倾斜布置的刮板 16结构,能够使得刮板16在跟随传动杆17旋转的过程中,压动物料在积料盘15上不断移动,进而送入至下料孔19内部,从而提升输送
和循环的效率。
47.在另外一个实施例中,反应釜本体10的外壁上设有换热夹层3,换热夹层3环绕包覆在反应釜本体10的侧壁及底部,换热夹层3的侧壁上设有进液管1和出液管4,进液管1位于出液管4的下方,使用时,导热液从进液管1导入至换热夹层3内部,并从出液管4导出,从而使得反应釜本体10内部的温度状态保持在合适区间,进而提升化工反应的效率。
48.在另外一个实施例中,进液管1上设有节流阀2,通过节流阀2 的设计能够控制导热液循环进入装置内部,进而能够通过控制导热液的流动来调节反应釜本体10内部的温度状态,以便于适配不同的化工反应。
49.在另外一个实施例中,反应釜本体10的顶部设有用于安装旋转电机8的承托支架7,承托支架7由多根竖向布置的支撑杆和设置在各个支撑杆顶部的圆盘组成,旋转电机8倒置安装在圆盘上,用以提供承托支架7进行安装。
50.在另外一个实施例中,反应釜本体10的底部设有底架13,底架13由三个圆周阵列布置的支撑杆组成,用于将反应釜撑起,以便于收集底部物料。
51.在另外一个实施例中,排料管14上设有下料阀18,通过下料阀 18的设计,能够自动控制排料,提升生产的自动化程度。
52.以上,仅为本实用新型的具体实施方式,但本实用新型的保护范围并不局限于此,任何熟悉本技术领域的技术人员在本实用新型揭露的技术范围内,可轻易想到变化或替换,都应涵盖在本实用新型的保护范围之内。因此,本实用新型的保护范围应以权利要求的保护范围为准。