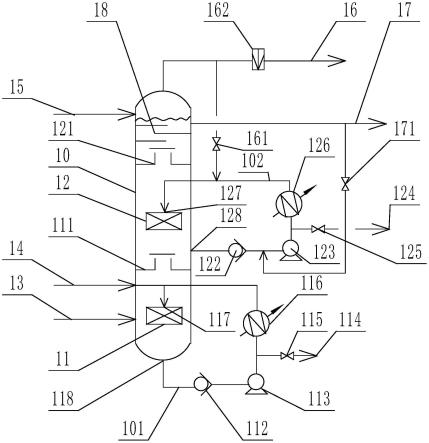
1.本实用新型属于高分子聚合物技术领域,具体而言,涉及一种利用环状化合物对多元醇缩聚的装置。
背景技术:2.缩合聚合反应,简称缩聚反应,是指由一种或多种单体相互缩合生成高分子的反应,其主产物称为缩聚物。缩合聚合反应的单体为带有2个(或以上)反应官能团的化合物聚合时脱去小分子形成聚合物,故聚合物的重复结构单元分子量比单体小。
3.现有的缩聚反应大多使用搅拌釜式反应器,该反应器结构紧凑,设备简单,工艺操作灵活性大,搅拌功率大,适合高分子量聚醚的生产等优点。但这种反应器也存在明显缺点,反应过程中搅拌破碎气泡效果不佳,反应釜内部气液混合不均匀易产生浓度和温度梯度,导致传质和反应速率低;蛇管式换热器的存在减少了釜的有效容积,使反应器生产能力减小,且检修和更换困难;搅拌器的存在易使气相环状化合物产生局部热点,产生爆炸的危险(在搅拌器和反应器器壁间形成电偶极,并使机械密封装置过热)。此外,如果机械密封装置被损坏或失效,氧化物可能会从反应器内溢出,外部的物质也可能进入反应器,引发反应器安全性问题。
4.有鉴于此,特提出本实用新型。
技术实现要素:5.本实用新型的目的在于提供一种利用环状化合物对多元醇缩聚的装置,解决了搅拌釜式反应器气液接触面较小,气体的分散性能差,传质效率低,产品的分子量分布较宽的问题,本实用新型通过应用微界面强化反应技术,在反应器内形成微界面体系,以数十倍地增加气液接触面积,大幅强化气液传质效率,希冀获得窄分子量分布的产品,并且通过应用微界面强化反应技术,可大幅加快环状化合物气体的消耗速率,有效降低气相中环状化合物的分压,大大提高设备的本质安全性。
6.为了实现上述技术目的,本实用新型提供了以下技术方案:
7.本实用新型提供了一种利用环状化合物对多元醇缩聚的装置,包括反应釜,所述反应釜的内部底层设置有第一微界面发生器,所述反应釜的内部中层设置有第二微界面发生器,所述第一微界面发生器与所述第二微界面发生器的中间设置有用以防止物料逆流的第一单向通道,所述第二微界面发生器的上方设置有第二单向通道,所述反应釜的底部侧边开设有多元醇管道以及环状化合物管道,所述第一微界面发生器连接有所述环状化合物管道以用于将汽化的环状化合物引入进行分散破碎,所述反应釜的顶部设置有缩聚产物管道。
8.现有技术中大多使用搅拌釜式反应器具有结构紧凑,设备简单,工艺操作灵活性大,搅拌功率大,适合高分子量聚醚的生产等优点,但这种搅拌釜式反应器也存在明显缺点,反应过程中搅拌破碎气泡效果不佳,反应釜内部气液混合不均匀易产生浓度和温度梯
度,导致传质和反应速率低;换热蛇管的存在减少了釜的有效容积,使搅拌釜式反应器生产能力减小,且检修和更换困难;搅拌釜式反应器的存在易使气相环状化合物产生局部热点,产生爆炸的危险(在搅拌器和反应器器壁间形成电偶极,并使机械密封装置过热),此外,如果机械密封装置被损坏或失效,氧化物可能会从搅拌釜式反应器内溢出,外部的物质也可能进入搅拌釜式反应器,引发反应器安全性问题。
9.本实用新型通过在反应釜的底部设置了第一微界面发生器,将环状化合物破碎分散为环状化合物微气泡,这增大了环状化合物与多元醇的相界传质面积,大幅强化气液传质效率,提高了缩聚反应的效率。之所以将第一微界面发生器设置在反应釜的底部,且最好置于反应釜的中线上。首先,微气泡是向上方跑的,将第一微界面发生器放置在最下边就可以让微气泡与多元醇反应时间更长,这也会提高缩聚反应的效率。其次,在反应釜的中线上是因为这样可以使气泡更均匀的分布在反应釜的里边。如果将第一微界面发生器置于反应釜的一侧,那么离第一微界面发生器远的地方微气泡肯定就更少,反应效率肯定就不高了。
10.第一微界面发生器的上方还设置了第一单向通道,这使得物料只能从下往上走,上边的物料并不能回流。下边的缩聚反应完成后通过第一单向通道后进入反应釜的中部继续在第二微界面发生器中反应,这样反应釜中部出来的产物肯定要比底部出来的产物纯度更高,为了防止高纯度的产物和低纯度的产物混杂在一起,所以才设置了第一单向通道来阻断反应釜的底部与中部。
11.第二微界面发生器的上方还设置有第二单向通道,第二单向通道的作用与第一单向通道的作用相同,从第一单向通道出来的产物就可以通过缩聚产物管道被排出收集了,这样可以进一步的保证缩聚产物的纯度。
12.优选的,所述第二微界面发生器连通有第二外循环通道,所述第二外循环通道的出口设置在所述第一单向通道和所述第二微界面发生器的中间,所述第二外循环通道的出口依次连接有第二单向阀、第二循环泵和第二换热器,所述第二外循环的回流口连通于所述第二微界面发生器的顶部。第二微界面发生器的侧边,反应釜的外边设置有第二外循环通道,这个第二外循环通道的出口设置在第一单向通道的上方靠近第一单向通道,这样从第一单向通道出来的未反应完全的液相和气相物料直接被卷吸进第二外循环通道,经过加热升温后送往第二微界面发生器再次破碎分散,这一过程再次提高气液之间的传质效率,提高了缩聚反应的效率。
13.优选的,所述第一微界面发生器连通有第一外循环通道,所述第一外循环通道的出口设置在所述反应釜的底部,所述第一外循环通道的出口依次连接有第一单向阀、第一循环泵和第一换热器,所述第一外循环的回流口连通于所述第一微界面发生器的顶部。第一微界面发生器的侧边,反应釜的外边连通有第一外循环通道,第一外循环通道的出口之所以设置在反应釜的底部,是可以将反应釜底部的物料卷回第一微界面发生器,这样可以有效利用反应物料。第一外循环通道设置有第一单向阀可以防止物料从第一外循环通道逆流,再通过循环泵提供动力,再通过换热器进行加热,将物料加热到反应温度后返回至第一微界面发生器。
14.优选的,所述反应釜的顶部设置有筛板用以减缓物料的流速。
15.优选的,所述反应釜的顶部连接有氮气进气管道。之所以在反应釜的顶部设置氮气进气管道,一是将氮气作为吹扫气吹扫反应釜的顶部,二是可以控制反应釜内部的压力。
16.优选的,所述反应釜的顶部开设有尾气管道,所述尾气管道分为两条管道,其中一条管道连接有第二外循环通道,另一条管道用于运输经过用以收集环状化合物的冷井后被排出。这里设置冷井的目的是在于将环状化合物液化后收集保存,防止环状化合物污染空气。
17.优选的,所述产物管道分为两条管道,一条管道将产物送回至所述第二外循环通道,另一条管道将产物排出收集。
18.优选的,所述第二外循环通道上设置有用以排出产物的第二产物出口。第二产物出口产出的缩聚产物要比第一产物出口产出的缩聚产物纯度要高一点,这些可以进行排出收集。
19.优选的,所述第一外循环通道上设置有用以排出产物的第一产物出口。通过第一微界面发生器处理后也可以得到纯度不高的缩聚产物,这些缩聚产物通过第一产物出口被排出收集。
20.与现有技术相比,本实用新型的优点在于:
21.(1)大幅提升气液两相传质效率,改善产品分子量分布。
22.乙氧基化反应器为典型的汽液相反应器,在反应器中,汽相环状化合物以扩散的方式进入液相进行反应,受化学反应和界面传质控制,其中气液物料的混合和传质是影响反应器反应性能、生产能力和技术先进性的重要因素。传质效率高低是衡量乙氧基化装置技术水平的重要指标,强化传质是所有乙氧基化工艺努力改进的重要方向。搅拌釜式反应器气液接触面较小,气体的分散性能差,传质效率低,产品的分子量分布较宽。本实用新型通过应用微界面强化反应技术,在反应器内形成微界面体系,以数十倍地增加气液接触面积,大幅强化气液传质效率,希冀获得窄分子量分布的产品。
23.(2)提高设备的本质安全性能。
24.釜式反应器上方气相空间有环状化合物气相聚集,搅拌桨的动密封易泄漏、产生静电,引起中毒、爆炸等安全事故。通过应用微界面强化反应技术,可大幅加快环状化合物的消耗速率,有效降低气相中环状化合物的分压,大大提高设备的本质安全性。
附图说明
25.通过阅读下文优选实施方式的详细描述,各种其他的优点和益处对于本领域普通技术人员将变得清楚明了。附图仅用于示出优选实施方式的目的,而并不认为是对本实用新型的限制。而且在整个附图中,用相同的参考符号表示相同的部件。在附图中:
26.附图1为本实施例提供的一种利用环状化合物对多元醇缩聚的装置的结构示意图。
27.其中:
28.10-反应釜;
ꢀꢀꢀꢀꢀꢀꢀꢀꢀꢀꢀꢀꢀꢀꢀꢀꢀꢀꢀꢀꢀꢀꢀꢀ
11-第一微界面发生器;
29.12-第二微界面发生器;
ꢀꢀꢀꢀꢀꢀꢀꢀꢀꢀꢀꢀꢀꢀ
111-第一单向通道;
30.121-第二单向通道;
ꢀꢀꢀꢀꢀꢀꢀꢀꢀꢀꢀꢀꢀꢀꢀꢀꢀ
13-多元醇管道;
31.14-环状化合物管道;
ꢀꢀꢀꢀꢀꢀꢀꢀꢀꢀꢀꢀꢀꢀꢀꢀ
17-缩聚产物管道;
32.102-第二外循环通道;
ꢀꢀꢀꢀꢀꢀꢀꢀꢀꢀꢀꢀꢀꢀꢀ
128-第二外循环通道的出口;
33.122-第二单向阀;
ꢀꢀꢀꢀꢀꢀꢀꢀꢀꢀꢀꢀꢀꢀꢀꢀꢀꢀꢀ
123-第二循环泵;
34.124-第二产物出口;
ꢀꢀꢀꢀꢀꢀꢀꢀꢀꢀꢀꢀꢀꢀꢀꢀꢀ
125-第二阀门;
35.126-第二换热器;
ꢀꢀꢀꢀꢀꢀꢀꢀꢀꢀꢀꢀꢀꢀꢀꢀꢀꢀꢀ
127-第二外循环的回流口;
36.101-第一外循环通道;
ꢀꢀꢀꢀꢀꢀꢀꢀꢀꢀꢀꢀꢀꢀꢀ
118-第一外循环通道的出口;
37.112-第一单向阀;
ꢀꢀꢀꢀꢀꢀꢀꢀꢀꢀꢀꢀꢀꢀꢀꢀꢀꢀꢀ
113-第一循环泵;
38.114-第一产物出口;
ꢀꢀꢀꢀꢀꢀꢀꢀꢀꢀꢀꢀꢀꢀꢀꢀ
115-第一阀门;
39.116-第一换热器;
ꢀꢀꢀꢀꢀꢀꢀꢀꢀꢀꢀꢀꢀꢀꢀꢀꢀꢀ
117-第一外循环的回流口;
40.15-氮气进气管道;
ꢀꢀꢀꢀꢀꢀꢀꢀꢀꢀꢀꢀꢀꢀꢀꢀꢀ
16-尾气管道;
41.161-回流阀门;
ꢀꢀꢀꢀꢀꢀꢀꢀꢀꢀꢀꢀꢀꢀꢀꢀꢀꢀꢀꢀ
162-冷井;
42.171-第三阀门;
ꢀꢀꢀꢀꢀꢀꢀꢀꢀꢀꢀꢀꢀꢀꢀꢀꢀꢀꢀꢀ
18-筛板。
具体实施方式
43.下面将结合附图和具体实施方式对本实用新型的技术方案进行清楚、完整地描述,但是本领域技术人员将会理解,下列所描述的实施例是本实用新型一部分实施例,而不是全部的实施例,仅用于说明本实用新型,而不应视为限制本实用新型的范围。基于本实用新型中的实施例,本领域普通技术人员在没有做出创造性劳动前提下所获得的所有其他实施例,都属于本实用新型保护的范围。实施例中未注明具体条件者,按照常规条件或制造商建议的条件进行。所用试剂或仪器未注明生产厂商者,均为可以通过市售购买获得的常规产品。
44.在本实用新型的描述中,需要说明的是,术语“中心”、“上”、“下”、“左”、“右”、“竖直”、“水平”、“内”、“外”等指示的方位或位置关系为基于附图所示的方位或位置关系,仅是为了便于描述本实用新型和简化描述,而不是指示或暗示所指的装置或元件必须具有特定的方位、以特定的方位构造和操作,因此不能理解为对本实用新型的限制。此外,术语“第一”、“第二”、“第三”仅用于描述目的,而不能理解为指示或暗示相对重要性。
45.在本实用新型的描述中,需要说明的是,除非另有明确的规定和限定,术语“安装”、“相连”、“连接”应做广义理解,例如,可以是固定连接,也可以是可拆卸连接,或一体地连接;可以是机械连接,也可以是电连接;可以是直接相连,也可以通过中间媒介间接相连,可以是两个元件内部的连通。对于本领域的普通技术人员而言,可以具体情况理解上述术语在本实用新型中的具体含义。
46.为了更加清晰的对本实用新型中的技术方案进行阐述,下面以具体实施例的形式进行说明。
47.实施例
48.参阅图1所示,为本实用新型提供的一种利用环状化合物对多元醇缩聚的装置的结构示意图。本装置包括反应釜10,反应釜10分为底部、中部和顶部三个部分,底部和中部通过通过第一单向通道111进行分隔,中部和顶部通过第二单向通道121进行分隔。本实施例中环状化合物选为环氧丙烷,多元醇为乙二醇。
49.首先,反应釜10的底部设置有第一微界面发生器11。第一微界面发生器11设置在反应釜10的中线上。多元醇管道13通过反应釜10底部的侧壁进入到反应釜10中,将乙二醇通入反应釜10中,环状化合物管道14同样穿过反应釜10底部的侧壁进入反应釜10中并且连通于第一微界面发生器11的顶部。环氧丙烷当进入反应釜10中就瞬间被汽化,因为反应釜
10的工作温度会使得环氧丙烷汽化。围绕着第一微界面发生器11还设置有第一外循环通道101,反应釜10的底部开设有第一外循环通道的出口118。第一外循环通道的出口118将反应釜10底部的物料通过第一单向阀112被第一循环泵113抽吸循环,之后经过第一换热器116后被返回至第一微界面发生器11,即第一外循环通道101通过第一外循环的回流口117将物料返回至第一微界面发生器11。第一外循环通道101上还有分出来一条通道,这条通道设置在第一循环泵113和第一换热器116的中间,并且这条通道上还设置有第一阀门115,第一阀门115后边跟着第一产物出口114,第一产物出口114可以收集一些纯度不是太高的聚乙二醇。
50.其次,反应釜10的中段设置有第二微界面发生器12。第二微界面发生器12也设置在反应釜10的中线上,处于第一微界面发生器11的正上方。反应釜10的中段,靠近第一单向通道111出开设有第二外循环通道的出口128,从第二外循环通道的出口128处出来的物料依次穿过第二单向阀122、第二循环泵123和第二换热器126后从第二外循环的回流口127回到第二微界面发生器12里。这样从反应釜10底部出来的未反应完全的环状化合物微气泡被卷吸进入第二微界面发生器12进行二次破碎分散。第二外循环通道102处也分出来一条通道,通道上设置有第二阀门125和第二产物出口124用以收集纯度比较高的聚乙二醇。
51.最后,反应釜10的顶端设置有筛板18,这些筛板18减缓了气泡的上升速度。在反应釜10顶部的液面上还开设有氮气进气管道15用以吹扫反应釜10顶端的未反应完全的环氧丙烷气体。这些环环氧丙烷气体一部分经过冷井162被冷却后回收,然后剩余的尾气通过尾气管道16进行排除;另一部分通过回流阀门161回到第二外循环通道102中继续反应,这样提高了物料的利用率。在反应釜10顶部的筛板18上方开设有缩聚产物管道17,聚乙二醇一部分被收集保存,另一部分也是返回至第二外循环通道102进行重复利用。
52.应用上述装置生产聚乙二醇,反应开始在反应釜10中加入乙二醇150l,并对反应釜10进行氮气置换,通入氮气至压力为140kpa。启动第一微界面发生器和第二微界面发生器并将反应釜10升温至100℃,形成液态均相溶液。在第一微界面发生器11内连续加入液态环氧丙烷,加料速度为100-160kg/h,液态环氧丙烷在进入反应釜10的瞬间就被汽化变成气态环氧丙烷通入第一微界面发生器11中,反应过程中利用第一换热器和第二换热器控制反应温度在130-140℃左右。
53.对比例
54.对比例采用搅拌釜式反应器,首先反应开始在釜中加入起始剂150l,并对反应釜进行氮气置换,通入氮气至压力为150kpa;启动搅拌将反应釜内物料升温至100℃,形成液态均相溶液;在反应器底部进料口连续加入液态环氧乙烷,加料速度为100-150kg/h;反应过程中利用反应器的外置夹套加热和内部的冷却盘管冷却以准确控制反应温度在130~150℃,反应压力最高为550kpa;加料结束后继续保温熟化,加料时间为3小时,熟化时间为0.5-1h;当进料管线与釜内压力差小于150kpa、釜内压力超过550kpa、釜内温度超过190℃时,联锁启动自动切断eo进料。
55.根据上述实施例生产聚乙二醇,得到如下数据:
56.反应罐内参数实施例对比例初期反应压力(kpa)140150末期反应压力(kpa)530550
反应温度(℃)130150末期反应粘稠度(cp)8595环氧丙烷加入速率(kg/h)150120
57.从上述实验数据中可以看出,对比例采用的搅拌釜式反应器虽然具有结构紧凑,设备简单,工艺操作灵活性大,搅拌功率大,适合高分子量聚醚的生产等优点。但这种反应器也存在明显缺点,反应过程中搅拌破碎气泡效果不佳,反应釜内部气液混合不均匀易产生浓度和温度梯度,导致传质和反应速率低;蛇管的存在减少了釜的有效容积,使反应器生产能力减小,且检修和更换困难;搅拌器的存在易使气相环氧乙烷产生局部热点,产生爆炸的危险。此外,如果机械密封装置被损坏或失效,氧化物可能会从反应器内溢出,外部的物质也可能进入反应器,引发反应器安全性问题。本实用新型的实施例在反应釜内形成微界面体系,以数十倍地增加气液接触面积,大幅强化气液传质效率,有效降低了反应压力和反应温度。还通过应用微界面强化反应技术,大幅加快环氧乙烷的消耗速率,有效降低气相中环氧乙烷的分压,大大提高设备的本质安全性。
58.最后应说明的是:以上各实施例仅用以说明本实用新型的技术方案,而非对其限制;尽管参照前述各实施例对本实用新型进行了详细的说明,本领域的普通技术人员应当理解:其依然可以对前述各实施例所记载的技术方案进行修改,或者对其中部分或者全部技术特征进行等同替换;而这些修改或者替换,并不使相应技术方案的本质脱离本实用新型各实施例技术方案的范围。