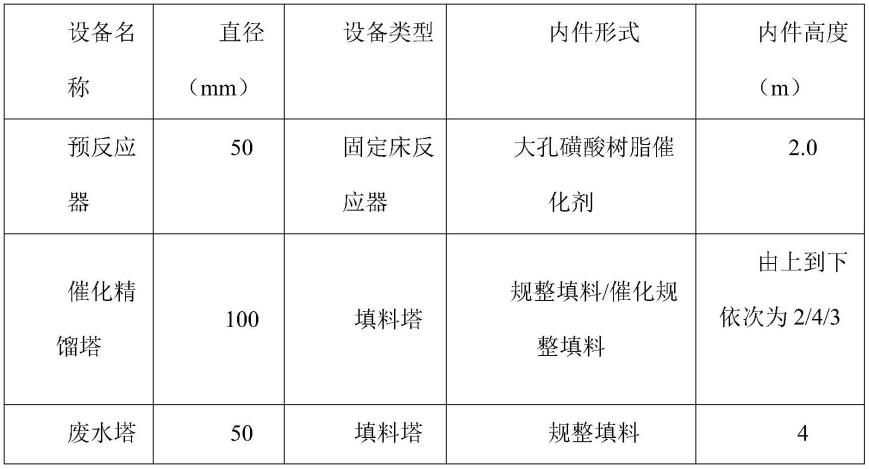
1.本实用新型涉及化学反应装置领域,更具体地说,涉及一种制备邻苯基苯酚中间体的装置。
背景技术:2.邻苯基苯酚(简称opp)是重要的精细化工产品和有机中间体,广泛应用于杀菌防腐、印染助剂和表面活性剂,还用于合成新型塑料、树脂和高分子材料的稳定剂和阻燃剂等领域。目前世界上关于opp的生产和研究主要集中在以环己酮为原料制备opp,即以环己酮为原料,在酸催化下缩合脱水得到中间体2-(1-环己烯基)环己酮和2-环己亚烷基环己酮,再经脱氢合成邻苯基苯酚。
3.其中环己酮缩合反应是在酸催化剂作用下的二聚反应,脱水后得到两种异构体,其中环己亚甲基环己酮含量较多。所得中间体经分离提纯后在高温下催化脱氢、精馏、结晶,得到高品质的邻苯基苯酚。
4.环己酮缩合反应式如下:
[0005][0006]
专利cn1371897a公开了一种用环己酮合成邻苯基苯酚的方法,合成中间体二聚体的步骤为原料环己酮经硫酸催化反应,然后经中和、分离、脱水、精馏后得到二聚体中间体。在实际生产过程中,随着反应的进行,环己酮缩合产生的二聚体浓度增大,与催化剂接触后会继续发生多聚反应,使得二聚产物的收率降低。只能通过控制反应转化率的方式抑制副反应。从反应器出来的混合物进入分离工段,将产物和未反应的环己酮进行分离,产物进入下一工段,未反应的环己酮循环回反应器。如此操作造成了大量的反应物循环,使得过程的能耗提高,设备尺寸增大。
[0007]
专利cn101544553a公开了一种连续催化反应精馏合成环己酮二聚体的方法,催化精馏塔上段为精馏段,内部装填催化剂,环己酮从塔中部即反应段下部进入。环己酮的缩合反应为液相反应,进料环己酮需要变成气相才能进入上部反应段,然后冷凝之后进入催化剂反应。原料需要经历气化冷凝过程才能进行反应,使得整个过程的能耗偏高。
[0008]
以上两个公开的专利均未提出反应废水的处理方法,由于环己酮和水有一定的互溶度,环己酮和水分层后的水层中含有一定量的环己酮,不能直接排放。
技术实现要素:[0009]
针对现有技术中存在的问题,本实用新型的目的在于提供一种制备邻苯基苯酚中间体的装置,它可以实现同时集成了废水处理装置,将反应和分离进行耦合,减少副反应的发生,并简化了生产流程,同时减少了原料的循环,降低了过程能耗。
[0010]
为解决上述问题,本实用新型采用如下的技术方案。
[0011]
一种制备邻苯基苯酚中间体的装置,包括预反应器、催化精馏塔、催化精馏塔再沸器、催化精馏塔冷凝器、分水器、废水塔、废水塔再沸器、废水塔冷凝器和连接管路,进料管路的一端与预反应器的底端管路连接,预反应器的顶端与催化精馏塔中上端管路连接,催化精馏塔的底端管路连接着催化精馏塔再沸器的底端,并管路回连至催化精馏塔的底端,催化精馏塔的顶端与催化精馏塔冷凝器的左端管路连接,催化精馏塔冷凝器的右端与分水器的上端管路连接,分水器的下端与催化精馏塔的顶端管路连接,分水器的下端与废水塔的中端管路连接,废水塔的底端管路连接着废水塔再沸器的底端,并管路回连至废水塔的底端,废水塔的顶端与废水塔冷凝器的右端管路连接,废水塔冷凝器的左端与分水器的上端管路连接;可以实现同时集成了废水处理装置,将反应和分离进行耦合,减少副反应的发生,并简化了生产流程,同时减少了原料的循环,降低了过程能耗。
[0012]
进一步的,催化精馏塔内部包括精馏段、反应段和提馏段,反应段位于精馏段和提馏段之间,精馏段位于反应段的上侧,提馏段位于反应段的下侧,精馏段和反应段之间的位置管路连接着预反应器的顶端;预反应后的环己酮和二聚体由反应段上部进入催化精馏塔,未反应的环己酮在反应段发生缩合反应生成二聚体,由于塔的分离作用,反应生成水和环己酮形成共沸物,向塔顶富集,产物二聚体为重组分,向塔釜富集。
[0013]
进一步的,预反应器为固定床反应器,装填大孔磺酸树脂催化剂;预反应器控制其内部的催化剂装填量,可以使原料在预反应器中的转化率低于50%,相比催化精馏塔内的催化剂更换,固定床反应器的催化剂更换更易操作,所以本装置的预反应器可以保护催化精馏塔内的催化剂,延长其使用寿命,减少更换周期。
[0014]
进一步的,预反应器的操作温度范围为80-120℃;可以使原料在预反应器中的转化率低于50%。
[0015]
进一步的,催化精馏塔、催化精馏塔再沸器、催化精馏塔冷凝器、分水器、废水塔、废水塔再沸器和废水塔冷凝器的操作压力范围均为-0.095~-0.08mpa;可以使催化精馏塔塔釜采出物料邻苯基苯酚中间体含量超过95%,未反应的环己酮含量低于4%。
[0016]
进一步的,预反应器的操作温度为80℃;可以使原料在预反应器中的转化率更低。
[0017]
进一步的,催化精馏塔、催化精馏塔再沸器、催化精馏塔冷凝器、分水器、废水塔、废水塔再沸器和废水塔冷凝器的操作压力均为-0.093mpa;可以使催化精馏塔塔釜采出物料邻苯基苯酚中间体含量超过95%,未反应的环己酮含量低于4%。
[0018]
进一步的,反应段装填大孔磺酸树脂催化剂和分离填料的复合模块。
[0019]
相比于现有技术,本实用新型的优点在于:
[0020]
(1)本方案以实现同时集成了废水处理装置,将反应和分离进行耦合,减少副反应的发生,并简化了生产流程,同时减少了原料的循环,降低了过程能耗。
[0021]
(2)本方案可以实现预反应后的环己酮和二聚体由反应段上部进入催化精馏塔,未反应的环己酮在反应段发生缩合反应生成二聚体,由于塔的分离作用,反应生成水和环己酮形成共沸物,向塔顶富集,产物二聚体为重组分,向塔釜富集。
[0022]
(3)本方案可以使原料在预反应器中的转化率低于50%,相比催化精馏塔内的催化剂更换,固定床反应器的催化剂更换更易操作,所以本装置的预反应器可以保护催化精馏塔内的催化剂,延长其使用寿命,减少更换周期,降低工作人员的工作强度。
[0023]
(4)本方案可以实现环己酮的转化率可达到95%以上,塔釜二聚体含量超过95%,
提升环己酮的利用率,节约原料。
[0024]
(5)本方案的设备少、投资低,同时又节约能耗,可广泛应用于邻苯基苯酚中间体的制备过程。
附图说明
[0025]
图1为本实用新型催化精馏制备邻苯基苯酚中间体及其废水处理装置的结构示意图。
[0026]
图中标号说明:
[0027]
e1催化精馏塔再沸器、e2催化精馏塔冷凝器、e3废水塔再沸器、e4废水塔冷凝器、r1预反应器、t1催化精馏塔、t2废水塔、v1分水器、a精馏段、b反应段、c提馏段、1原料环己酮、2邻苯基苯酚中间体、3回流环己酮、4待处理废水、5处理后废水。
具体实施方式
[0028]
实施例1:
[0029]
请参阅图1,一种制备邻苯基苯酚中间体的装置,包括预反应器r1、催化精馏塔t1、催化精馏塔再沸器e1、催化精馏塔冷凝器e2、分水器v1、废水塔t2、废水塔再沸器e3、废水塔冷凝器e4和连接管路,进料管路的一端与预反应器r1的底端管路连接,预反应器r1的顶端与催化精馏塔t1中上端管路连接,催化精馏塔t1的底端管路连接着催化精馏塔再沸器e1的底端,并管路回连至催化精馏塔t1的底端,催化精馏塔t1的顶端与催化精馏塔冷凝器e2的左端管路连接,催化精馏塔冷凝器e2的右端与分水器v1的上端管路连接,分水器v1的下端与催化精馏塔t1的顶端管路连接,分水器v1的下端与废水塔t2的中端管路连接,废水塔t2的底端管路连接着废水塔再沸器e3的底端,并管路回连至废水塔t2的底端,废水塔t2的顶端与废水塔冷凝器e4的右端管路连接,废水塔冷凝器e4的左端与分水器v1的上端管路连接;可以实现同时集成了废水处理装置,将反应和分离进行耦合,减少副反应的发生,并简化了生产流程,同时减少了原料的循环,降低了过程能耗。
[0030]
催化精馏塔t1内部包括精馏段a、反应段b和提馏段c,反应段b位于精馏段a和提馏段c之间,精馏段a位于反应段b的上侧,提馏段c位于反应段b的下侧,精馏段a和反应段b之间的位置管路连接着预反应器r1的顶端;预反应后的环己酮和二聚体由反应段b上部进入催化精馏塔t1,未反应的环己酮在反应段b发生缩合反应生成二聚体,由于塔的分离作用,反应生成水和环己酮形成共沸物,向塔顶富集,产物二聚体为重组分,向塔釜富集。
[0031]
预反应器r1为固定床反应器,装填大孔磺酸树脂催化剂;预反应器r1控制其内部的催化剂装填量,可以使原料在预反应器r1中的转化率低于50%,相比催化精馏塔t1内的催化剂更换,固定床反应器的催化剂更换更易操作,所以本装置的预反应器r1可以保护催化精馏塔内的催化剂,延长其使用寿命,减少更换周期。
[0032]
催化精馏塔t1、催化精馏塔再沸器e1、催化精馏塔冷凝器e2、分水器v1、废水塔t2、废水塔再沸器e3、废水塔冷凝器e4的操作压力为-0.095~-0.08mpa;可以使催化精馏塔t1塔釜采出物料邻苯基苯酚中间体含量超过95%,未反应的环己酮含量低于4%。
[0033]
预反应器r1的操作温度为80-120℃;可以使原料在预反应器中的转化率低于50%。
[0034]
反应段b装填大孔磺酸树脂催化剂和分离填料的复合模块。
[0035]
一种制备邻苯基苯酚中间体的装置的主要设备及内件参数见表1。
[0036]
表1实施例1主要设备及内件参数
[0037][0038]
原料环己酮以10kg/h的流量由预反应器r1底部进入,预反应器r1常压操作,预反应温度为80℃,预反应环己酮转化率为25%。预反应后的物料从预反应器顶部排出,进入催化精馏塔t1中上部。催化精馏塔t1和废水塔t2真空操作,操作压力为-0.088mpa。稳定运行后,催化精馏塔t1塔釜采出物料邻苯基苯酚中间体含量为95%,未反应的环己酮含量为3%,其余为杂质。废水塔t2塔釜采出废水中不含环己酮。
[0039]
实施例2:
[0040]
一种制备邻苯基苯酚中间体的装置的主要设备及内件参数见表2。
[0041]
表2实施例2主要设备及内件参数
[0042]
[0043]
原料环己酮以800kg/h的流量由预反应器r1底部进入,预反应器r1常压操作,预反应温度为120℃,预反应环己酮转化率为40%。预反应后的物料从预反应器r1顶部排出,进入催化精馏塔t1中上部。催化精馏塔t1和废水塔t2真空操作,操作压力为-0.093mpa。稳定运行后,催化精馏塔t1塔釜采出物料邻苯基苯酚中间体含量为97%,未反应的环己酮含量为0.5%,其余为杂质。废水塔t2塔釜采出废水中不含环己酮。
[0044]
以上所述实例仅是充分说明本实用新型而所举的较佳的实施例,本实用新型的保护范围不限于此。本技术领域的技术人员在本实用新型基础上所作的等同替代或变换,均在本实用新型的保护范围之内。
[0045]
工作原理:原料环己酮1由预反应器r1底部进入,预反应器r1内部装填大孔磺酸树脂催化剂,预反应后的物料由预反应器r1顶部采出。催化精馏塔t1内部由上到下依次设置精馏段a、反应段b和提馏段c,其中反应段b装填大孔磺酸树脂催化剂和分离填料的复合模块。预反应后的物料由反应段b顶部进入催化精馏塔t1。催化精馏塔t1底部设有催化精馏塔再沸器e1,顶部设有催化精馏塔冷凝器e2。反应混合物继续在催化精馏塔t1内部反应、分离,缩合反应产生的水与环己酮共沸,由催化精馏塔t1顶部进入催化精馏塔冷凝器e2,冷凝后进入分水器v1,环己酮和水在分水器v1中分层,油相环己酮作为回流返回催化精馏塔t1水相为溶解了少量环己酮的废水,进入废水塔t2中部。催化精馏塔t1塔底采出含少量未反应的环己酮的二聚体。废水塔t2底部设有废水塔再沸器e3,顶部设有废水塔冷凝器e4。废水塔t2塔顶蒸出少量环己酮和水的共沸物,经废水塔冷凝器e4冷凝后进入与催化精馏塔t1共用的分水器中,完成油水两相分层操作。废水塔t2塔塔釜采出不含环己酮的废水;可以实现环己酮的转化率可达到95%以上,塔釜二聚体含量超过95%,本装置设备少、投资低,同时又节约能耗,可广泛应用于邻苯基苯酚中间体的制备过程。