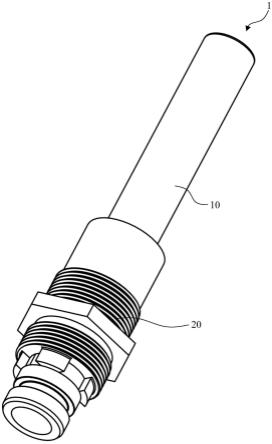
1.本实用新型涉及一种芯棒组件、一种油气分离器以及一种压缩机系统。更具体地,本实用新型涉及一种油气分离器的芯棒组件、具有该芯棒组件的油气分离器以及具有该油气分离器的压缩机系统。
背景技术:2.本部分的内容仅提供了与本实用新型相关的背景信息,其可能并不构成现有技术。
3.在压缩机系统中,从压缩机排出的压缩气体通常会混有油,因此通常在压缩机的排气口的下游设置油气分离器,用以从压缩气体中分离出油。分离出的洁净的压缩气体被排出以供使用,而分离出的油则返回至压缩机中。油气分离器包括分离器本体、底座以及将分离器本体与底座连接的芯棒组件。分离器本体设置有滤芯,用以过滤流入的油气混合气,以使油与压缩气体分离。芯棒组件将分离器本体与底座连接,以使分离出的油和压缩气体分别从设置在底座中的排油通道和排气通道排出。为了确保分离出的油和压缩气体不再混合,分离后的油和压缩气体在芯棒组件和底座中的流动路径必须彼此隔离。因此,芯棒组件中的套筒与芯棒之间的连接以及芯棒组件与底座之间的连接显得尤为重要,在确保连接以实现各通道的导向作用的同时,还需形成可靠的密封,特别是需要在芯棒组件与底座之间形成可靠的密封。
4.在油气分离器的芯棒组件的现有设计中,芯棒组件的套筒与芯棒通常采用固定连接,例如,采用螺纹和密封胶相组合的方式固定连接,或者采用过盈连接。而芯棒组件与底座之间的密封则通过芯棒组件与底座的螺纹接合来密封,或者通过在底座中设置环形沟槽并安装o形环来密封。然而,上述现有设计存在如下不足。对于套筒与芯棒的固定连接,螺纹和密封胶相组合的方式存在不易拆卸以及在密封压力、温度、兼容性方面均存在限制的不足,而过盈连接的方式则存在加工精度要求较高、成本高、周期长以及装配难度高等不足。对于芯棒组件与底座之间的现有密封方式,如果仅通过芯棒组件与底座之间的螺纹接合来实现密封,则对于螺纹的加工和装配要求较高,并且密封效果不佳。如果通过在底座中设置环形内沟槽并安装o形环来实现密封,则一方面,在底座中加工内沟槽的加工难度较高,另一方面,在安装过程中,无法观察底座的内沟槽中的o形环的变形过程,容易安装不到位,并且由于套筒和芯棒的固定连接,芯棒与o形环的密封接合是在套筒与底座螺纹连接的过程中形成的,因此这也对套筒的外螺纹以及芯棒的外圆柱面的加工提出了更高的要求以满足所需的位置度。
5.因此,在油气分离器的芯棒组件及其与底座之间的连接设计方面尚存在改进的空间,以能够提供油气分离器内的油路与气路的可靠的密封隔离,同时简化安装,并降低成本。
技术实现要素:6.本实用新型的一个目的在于解决上述问题中的至少一者。
7.本实用新型的一个方面在于提供一种芯棒组件,芯棒组件用于油气分离器。芯棒组件包括:筒形的芯棒,芯棒包括本体部;以及套筒,套筒套置在芯棒上。芯棒的本体部的第一端部形成有外台肩,外台肩的外径大于芯棒的本体部的外径,外台肩设置成支承套筒的第一端部,并且套筒能够相对于芯棒移动。
8.芯棒的第一端部还设置有环形凹槽,环形凹槽设置成容纳第一密封件。
9.套筒的第一端部形成有周向地间隔开的多个过油孔,过油孔沿套筒的径向贯穿套筒的周壁。
10.外台肩的外径大于套筒的第一端部的内径,并且小于等于套筒的第一端部的外径。
11.本实用新型的另一方面在于提供一种油气分离器,该油气分离器包括根据本实用新型的芯棒组件。
12.在一个实施方式中,油气分离器还包括:分离器本体,分离器本体包括壳体和容置在壳体内的中空的过滤件,在过滤件与壳体的内壁之间形成有第一空间,并且过滤件的内部形成有第二空间;以及底座,底座设置有入口通道、第一出口通道和第二出口通道。底座与分离器本体密封地连接,使得入口通道与第一空间连通。芯棒组件密封地连接在底座与分离器本体之间,使得第二空间经芯棒与第一出口通道连通,并且第二空间经套筒与第二出口通道连通。
13.芯棒的第一端部经第一密封件密封地接合在底座的第一出口通道中,以使第一出口通道与第二出口通道隔离。套筒的第一端部螺纹接合在第一出口通道中,并且套筒的第二端部位于第二空间内。
14.第一出口通道设置有第一内台肩,芯棒的第一端部抵接在第一内台肩上。
15.在一个实施方式中,第一出口通道还设置有第二内台肩,芯棒组件安装成使得套筒的第一端部能够与第二内台肩和/或芯棒的外台肩抵接。
16.优选地,在底座与套筒之间设置有第二密封件。
17.本实用新型的又一方面在于提供一种压缩机系统。压缩机系统包括:压缩机,压缩机包括进气口、排气口以及至少一个回油口;至少一个油气分离器,压缩机的所述排气口连接至该至少一个油气分离器的入口通道,并且该至少一个油气分离器的第二出口通道连接至压缩机的至少一个回油口。该至少一个油气分离器中的至少一者为根据本实用新型的油气分离器。
18.本实用新型提供了一种改进的芯棒组件、具有该芯棒组件的油气分离器以及具有该油气分离器的压缩机系统。通过使芯棒与套筒形成间隙配合,能够简化油气分离器中的芯棒组件的组装与拆卸,并且能够简化加工,并降低对各零部件的加工精度的要求,由此降低制造成本。
附图说明
19.以下将参照附图仅以示例方式描述本实用新型的实施方式。在附图中,相同的特征或部件采用相同的附图标记来表示,并且附图不一定按比例绘制,并且在附图中:
20.图1示出了根据本实用新型的一个实施方式的芯棒组件的立体图;
21.图2和图3分别示出了图1中所示的芯棒组件的芯棒和套筒的立体图;
22.图4示出了图1中所示的芯棒组件的纵向截面图;
23.图5示出了安装有图1所示的芯棒组件的油气分离器的纵向截面图;
24.图6示出了图5的局部放大图;以及
25.图7示出了安装有根据本实用新型的油气分离器的压缩机系统的示意图。
具体实施方式
26.下文的描述本质上仅是示例性的而并非意图限制本实用新型、应用及用途。应当理解,在所有这些附图中,相似的附图标记指示相同的或相似的零件及特征。各个附图仅示意性地表示了本实用新型的实施方式的构思和原理,并不一定示出了本实用新型各个实施方式的具体尺寸及其比例。在特定的附图中的特定部分可能采用夸张的方式来图示本实用新型的实施方式的相关细节或结构。
27.在本实用新型的实施方式的描述中,所采用的与“上”、“下”、“左”、“右”相关的方位术语是以附图中所示出的视图的上、下、左、右位置来描述的。在实际应用中,本文中所使用的“上”、“下”、“左”、“右”的位置关系可以根据实际情况限定,这些关系是可以相互颠倒的。
28.图1示出了根据本实用新型的一个实施方式的芯棒组件1的立体图。如图1所示,芯棒组件1包括芯棒10和套筒20。如图2所示,芯棒10呈筒形,芯棒10的本体部11的第一端部(图2中的下端部)形成有外台肩12,外台肩12的外径大于本体部11的外径。外台肩12设置成用于支承套筒20的端部。另外,芯棒10的本体部11的第一端部还形成有周向的环形凹槽13,用于安装第一密封件s1(图1-4中未示出,仅在图5和图6中示出)。
29.如图3所示,套筒20包括本体部21和形成在本体部21上的凸缘22。在图中所示的示例中,凸缘22的外轮廓呈六边形。然而,本实用新型不限于此,在根据本实用新型的其他示例中,凸缘22的外轮廓可以呈任何其他合适的形状,例如,凸缘22的外轮廓可以呈圆形。并且,在根据本实用新型的其他示例中,甚至可以不设置凸缘22。本体部21的外周形成有彼此间隔开的第一外螺纹23和第二外螺纹24。凸缘22位于第一外螺纹23与第二外螺纹24之间。另外,本体部21的第一端部(图3中的下端部)形成有周向地彼此间隔开的多个过油孔25。过油孔25为在本体部21的第一端部的周壁上等间隔地形成的多个开口,过油孔25贯穿本体部21的第一端部的周壁。
30.芯棒10的本体部11的外径小于套筒20的本体部21的内径,并且芯棒10的外台肩12的外径大于套筒20的本体部21的内径。在图中所示的示例中,芯棒10的外台肩12的外径小于套筒20的本体部21的外径。然而,本实用新型不限于此。在根据本实用新型的其他示例中,芯棒10的外台肩12的外径可以等于套筒20的本体部21的外径。
31.图4示出了组装的芯棒组件1的横截面图。如图4所示,套筒20套置在芯棒10上。套筒20的第一端部(图中的下端部)可以抵靠在芯棒10的外台肩12上。优选地但非必须的,芯棒10的本体部11的轴向长度大于套筒20的轴向长度,使得当套筒20套置在芯棒10上并抵靠芯棒10的外台肩12时,芯棒10的本体部11从套筒20的第二端部(图中的上端部)伸出。由于芯棒10的本体部11的外径小于套筒20的本体部21的内径,因此可以容易地将套筒20套置在
芯棒10上,从而完成芯棒组件1的组装,并且套筒20与芯棒10形成间隙配合,套筒20能够相对于芯棒10移动,而无需将套筒20与芯棒10彼此固定。一方面,这使得芯棒组件1的组装与拆卸均较为容易。另一方面,芯棒10与套筒20之间的这种间隙配合,可以容许一定程度的制造误差以及装配误差,能够降低对各零部件的制造精度的要求,并因此能够降低成本。再者,芯棒10与套筒20之间的这种组装形式,允许套筒20具有一致的内径。与芯棒与套筒之间采用过盈配合而在套筒内壁加工出内台肩的相关设计相比,可以降低加工难度。并且,与芯棒与套筒之间采用螺纹和密封胶的组合而形成固定连接的相关设计相比,能够简化芯棒和套筒的加工。
32.图5示出了安装有芯棒组件1的油气分离器100的纵向截面图,并且图6示出了图5的局部放大图。如图5和图6所示,油气分离器100包括底座30和分离器本体。
33.底座30设置有入口通道31、第一出口通道32以及第二出口通道33。入口通道31大体沿轴向(即,图中的纵向)贯穿底座30。在图中所示的示例中,第一出口通道32包括彼此连接的轴向通道部分321和横向通道部分322。轴向通道部分321自底座30的上表面开口并沿轴向在底座30内延伸,但不贯穿底座30。横向通道部分322自轴向通道部分321的端部横向地延伸至底座30的一个侧面。然而,本实用新型不限于此,在根据本实用新型的其他示例中,第一出口通道32可以不包括横向通道部分322,在此情况下,轴向通道部分321沿轴向贯穿底座30。
34.第二出口通道33的入口端在底座30内与第一出口通道32的轴向通道部分321相通,并且第二出口通道33的出口端延伸至底座30的一个侧面。第二出口通道33的出口端安装有转接头60。
35.分离器本体包括壳体40以及容置在壳体40内的过滤件50。过滤件50分别经上端盖51和下端盖52在壳体40内保持就位,上端盖51经弹性元件53与壳体40的顶部抵接,并且下端盖52抵接在壳体40内的隔板42上。隔板42设置有多个彼此间隔开的通孔421。过滤件50与壳体40的内壁间隙配合,在过滤件50与壳体40的内壁之间形成有第一空间v1。过滤件50呈中空的筒形,内部形成有第二空间v2。
36.底座30与分离器本体密封地连接,使得底座30的入口通道31与第一空间v1连通。
37.芯棒组件1密封地连接在底座30与分离器本体之间,使得分离器本体内的第二空间v2经芯棒10与底座30内的第一出口通道32连通,并且第二空间v2经套筒20与底座30内的第二出口通道33连通。
38.具体地,如图5和图6所示,芯棒组件1的芯棒10的第一端部插入第一出口通道32的轴向通道部分321中。第一密封件s1容置在芯棒10的第一端部的环形凹槽13中,并与第一出口通道32的轴向通道部分321的内壁抵接而形成可靠的密封。通过将第一密封件s1容置在芯棒10的环形凹槽13中,在将芯棒10的第一端部插入底座30内的第一出口通道32的轴向通道部分321的过程中,易于观察第一密封件s1的变形,确保芯棒10在轴向通道部分321内安装就位,以确保第一出口通道32与第二出口通道33之间的可靠密封。
39.如图6中最佳地示出的,轴向通道部分321的内壁设置有第一内台肩3211。当安装就位时,芯棒10的本体部11的第一端部可以抵靠第一内台肩3211。通过芯棒10的第一端部与第一内台肩3211的抵接以及套筒20的第一端部与芯棒10的外台肩12的抵接,可以实现芯棒10在底座30内的定位。
40.套筒20的第一外螺纹23接合轴向通道部分321内的内螺纹,套筒20的过油孔25与底座30内的第二出口通道33连通。优选地,套筒20安装成使得套筒20的第一端部处的过油孔25至少部分地与第二出口通道33对准。
41.在图中所示的示例中,芯棒10的外台肩12的外径小于套筒20的第一端部的外径,相应地,轴向通道部分321的与套筒20接合的部分的内径大于轴向通道部分321的与芯棒10的第一端部接合的部分的内径,从而在轴向通道部分321的内壁上形成有第二内台肩3212。当安装就位时,套筒20的第一端部可以与芯棒10的外台肩12以及轴向通道部分321的第二内台肩3212中的至少一者抵接,从而限定芯棒10的轴向位置。然而,如上文所述,芯棒10的外台肩12的外径可以大体等于套筒20的第一端部的外径,在此情况下,轴向通道部分321的内壁可以不形成上述第二内台肩3212,从而可以简化底座30的加工。当安装就位时,套筒20的第一端部可以与芯棒10的外台肩12抵接。
42.套筒20与底座30的螺纹接合可以提供入口通道31与第二出口通道33之间的密封。并且优选地,在套筒20与底座30之间设置第二密封件s2,从而在入口通道31与轴向通道部分321之间提供更好的密封。套筒20在底座30上可以安装成使得套筒20的凸缘22搁置在底座30的轴向通道部分321的入口端的端面上。第二密封件s2例如可以设置在凸缘22与轴向通道部分321的入口端的端面之间。
43.在此需说明的是,当芯棒组件1在底座30中安装就位时,套筒20的第一端部优选但并非必须与芯棒10的外台肩12抵靠,而是可以允许套筒20的第一端部与芯棒10的外台肩12之间存在一定的轴向间隙。当套筒20安装成使得套筒20的第一端部与芯棒10的外台肩12之间存在轴向间隙时,该轴向间隙即可起到过油孔25的作用,允许套筒20与芯棒11之间的环形空间与第二出口通道33连通。因此,套筒20的第一端部甚至可以不设置过油孔25。因此,轴向通道部分321的第二内台肩3212的轴向高度并无特别的限制,当安装就位时,芯棒10的第一端部抵靠第一内台肩3211,第二内台肩3212优选地低于芯棒10的外台肩12,但也可以与芯棒10的外台肩12齐平或者略高于芯棒10的外台肩12。相应地,套筒20的凸缘22设置成使得当凸缘22搁置在轴向通道部分321的入口端的端面上时,套筒20的第一端部可以抵靠在芯棒10的外台肩12上,或者套筒20的第一端部可以与芯棒10的外台肩12之间存在一定的轴向间隙。
44.如图5和图6所示,套筒20的第二外螺纹24与壳体40内的隔板42的内螺纹接合。并且套筒20的本体部21经第三密封件s3(仅在图5中示出)与下端盖52密封接合,从而密封地接合至过滤件50内的第二空间v2,使得套筒20的第二端部位于第二空间v2内,并且芯棒10的本体部11也伸入第二空间v2内。
45.从压缩机(图中未示出)排出的油气混合气从入口通道31进入油气分离器100,经隔板42的通孔421进入壳体40内的第一空间v1。进入第一空间v1的油气混合气经过滤件50过滤分离,进入过滤件50内的第二空间v2。过滤后的洁净气体从第二空间v2进入芯棒10内,流入第一出口通道32的轴向通道部分321,并从横向通道部分322流出油气分离器100,以供使用。而分离出的油则积聚在第二空间v2的底部,并且一旦第二空间v2内的油的液位超过套筒20的第二端部,则油将进入套筒20与芯棒10之间的环形空间,并经出油孔25流入第二出口通道33,经转接头60流出油气分离器100,例如,可以返回至压缩机中。
46.以上介绍了根据本实用新型的一个实施方式的芯棒组件1以及安装有芯棒组件1
的油气分离器100。芯棒10与套筒20形成间隙配合,不需要进行固定连接,能够简化芯棒组件1的组装与拆卸。另外,与在轴向通道部分321的内壁上设置环形凹槽用以容置密封件的相关技术相比,本技术的芯棒组件1在芯棒10的下端部设置用于容置第一密封件s1的环形凹槽13,一方面,可以简化加工,另一方面,在将芯棒组件1与底座30组装的过程中,易于观察密封件的变形,确保芯棒10的安装就位,以确保第一出口通道32与第二出口通道33之间的密封隔离,防止经分离后的洁净气体与油再次混合。
47.图7示出了根据本实用新型的压缩机系统1000。压缩机系统1000例如可以实施为天然气增压机组。如图7所示,压缩机系统1000包括压缩机200和至少一个油气分离器。在图中所示的示例中,压缩机系统1000包括彼此串联连接的第一油气分离器300以及第二油气分离器400。第一油气分离器300和第二油气分离器400中的至少一者为本实用新型的油气分离器100。然而,本实用新型不限于此,在根据本实用新型的压缩机系统中,可以仅包括一个油气分离器,或者可以包括更多的油气分离器。
48.气体(例如,天然气)从压缩机200的进气口21进入压缩机200,经压缩后从压缩机200的排气口22排出。从压缩机200的排气口22排出的经压缩的油气混合气流向第一油气分离器300,进入第一油气分离器300进行油气分离。经第一油气分离器300分离后的气体流向第二油气分离器400,经第二油气分离器400再次进行油气分离,经第一油气分离器300分离出的油则返回至压缩机200的第一回油口23。
49.经第二油气分离器400分离后的气体流向下游以供使用,而经第二油气分离器400分离后的油则返回至压缩机200的第二回油口24。
50.以上示出了根据本实用新型的优选实施方式的芯棒组件、油气分离器以及压缩机系统。
51.在此,已详细描述了本实用新型的芯棒组件、具有该芯棒组件的油气分离器以及具有该油气分离器的压缩机系统的示例性实施方式,但是应该理解的是,本实用新型并不局限于上文详细描述和示出的具体实施方式。在不偏离本实用新型的主旨和范围的情况下,本领域的技术人员能够对本实用新型进行各种变型和变体。所有这些变型和变体都落入本实用新型的范围内。而且,所有在此描述的构件都可以由其他技术性上等同的构件来代替。