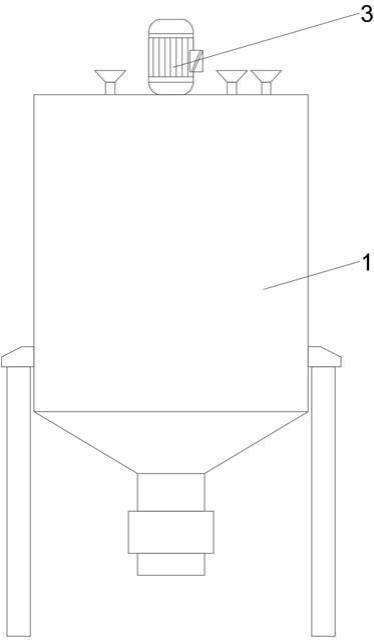
1.本实用新型涉及生产设备技术领域,尤其涉及压裂用助排剂生产设备。
背景技术:2.在石油开采过程中,通常根据大规模体积压裂的模式使用水基压裂液对储层进行改造,从而获得工业油气流,压裂过程结束后,需要将上述压裂液的残液从储层中返排出来,由于地层毛细管阻力的作用,压裂液将无法完全返排至地面,为了帮助压裂液返排,以降低压裂液对储层的伤害,目前通常在压裂液中加入助排剂,大多数助排剂生产设备通过分步将制备剂加入到反应釜中,进行搅拌混合,但是由于不同的制备剂的密度不同,在反应釜中容易产生分层,搅拌叶朝着一个方向转动进行搅拌,搅拌方式单一,同时反应釜底部的制备剂难以与上层进行循环流动,导致混合效果较差。
技术实现要素:3.本实用新型的目的在于:为了解决上述技术的问题,而提出的压裂用助排剂生产设备。
4.为了实现上述目的,本实用新型采用了如下技术方案:
5.压裂用助排剂生产设备,包括反应釜本体,所述反应釜本体上端一侧设有进水管,所述反应釜本体下端设有出液管,所述出液管中部设有阀门,所述反应釜本体内顶面中部转动设有空心搅拌轴,所述反应釜本体上端中部设有驱动电机,所述驱动电机输出端贯穿进反应釜本体内并与空心搅拌轴上端连接,所述空心搅拌轴下端对称设有搅拌叶,所述空心搅拌轴中部设有辅助组件;
6.所述辅助组件包括滑动设于空心搅拌轴中部的活塞板和固定套设于空心搅拌轴中部的伞状导流板,所述活塞板位于伞状导流板正下方且外侧与反应釜本体内壁紧密接触,所述活塞板中部开设有环形出液腔,所述环形出液腔一端贯穿出活塞板外壁,所述活塞板上端开设有多个与环形出液腔相连通的锥形孔,多个所述锥形孔开口较大一端朝上,所述活塞板上端中部设有固定环,所述伞状导流板下端开设有与固定环相配合的凹槽,所述凹槽内壁下端对称设有两个凸块,所述固定环外表面开设有与凸块相配合的波浪形滑槽,所述伞状导流板上端设有导液环,所述导液环下端中部均布开设有多个出液孔,多个所述出液孔呈环形阵列分布。
7.作为上述技术方案的进一步描述:
8.所述反应釜本体内壁开设有与环形出液腔相配合的环形槽,所述环形槽下端面为斜面设置,所述环形槽与环形出液腔的竖直距离小于波浪形滑槽波峰与波谷的竖直距离。
9.作为上述技术方案的进一步描述:
10.所述活塞板上端对称设有两个导向杆,所述反应釜本体内壁对称设有两个分别与导向杆相配合的导向套。
11.作为上述技术方案的进一步描述:
12.所述波浪形滑槽波峰为水平设置。
13.作为上述技术方案的进一步描述:
14.所述反应釜本体上端至少设有两个进液管,两个所述进液管输出端与导液环内部相连通。
15.作为上述技术方案的进一步描述:
16.所述空心搅拌轴侧壁中部对称开设有两个与导液环内部相连通的出液口。
17.综上所述,由于采用了上述技术方案,本实用新型的有益效果是:
18.本实用新型中,通过凸块与波浪形滑槽的相互配合,使得活塞板上下运动,实现将下层液体挤压至活塞板上方,然后在流回至液体上层,使得上下层液体充分混合,进一步提高了混合效果。
附图说明
19.图1示出了根据本实用新型实施例提供的生产设备外观图;
20.图2示出了根据本实用新型实施例提供的生产设备结构示意图;
21.图3示出了根据本实用新型实施例提供的生产设备结构局部正剖示意图。
22.图例说明:1、反应釜本体;2、空心搅拌轴;3、驱动电机;4、搅拌叶;5、活塞板;6、伞状导流板;7、固定环;8、凸块;9、导液环;10、导向杆;11、导向套。
具体实施方式
23.下面将结合本实用新型实施例中的附图,对本实用新型实施例中的技术方案进行清楚、完整地描述,显然,所描述的实施例仅仅是本实用新型一部分实施例,而不是全部的实施例。基于本实用新型中的实施例,本领域普通技术人员在没有作出创造性劳动前提下所获得的所有其它实施例,都属于本实用新型保护的范围。
24.请参阅图1-图3,本实用新型提供一种技术方案:
25.压裂用助排剂生产设备,包括反应釜本体1,反应釜本体1上端一侧设有进水管,反应釜本体1下端设有出液管,出液管中部设有阀门,反应釜本体1内顶面中部转动设有空心搅拌轴2,反应釜本体1上端中部设有驱动电机3,驱动电机3输出端贯穿进反应釜本体1内并与空心搅拌轴2上端连接,空心搅拌轴2下端对称设有搅拌叶4,空心搅拌轴2中部设有辅助组件;
26.辅助组件包括滑动设于空心搅拌轴2中部的活塞板5和固定套设于空心搅拌轴2中部的伞状导流板6,活塞板5位于伞状导流板6正下方且外侧与反应釜本体1内壁紧密接触,活塞板5中部开设有环形出液腔,环形出液腔一端贯穿出活塞板5外壁,活塞板5上端开设有多个与环形出液腔相连通的锥形孔,保证流到活塞板5上方的液体经过锥形孔进入环形出液腔内,多个锥形孔开口较大一端朝上,活塞板5上端中部设有固定环7,伞状导流板6下端开设有与固定环7相配合的凹槽,凹槽内壁下端对称设有两个凸块8,固定环7外表面开设有与凸块8相配合的波浪形滑槽,伞状导流板6上端设有导液环9,导液环9下端中部均布开设有多个出液孔,多个出液孔呈环形阵列分布;伞状导流板6转动过程中,带动导液环9转动,使得液体在离心力作用下,从出液孔分散流出。
27.反应釜本体1内壁开设有与环形出液腔相配合的环形槽,环形槽下端面为斜面设
置,环形槽与环形出液腔的竖直距离小于波浪形滑槽波峰与波谷的竖直距离;使得环形出液腔流出的液体经过斜面贴着反应釜本体1内壁向下滑落,保证液体回流的稳定性,避免产生四溅。
28.活塞板5上端对称设有两个导向杆10,反应釜本体1内壁对称设有两个分别与导向杆10相配合的导向套11;导向杆10沿着导向套11上下滑动,进而保证活塞板5上下运动的稳定性,避免造成活塞板5产生偏转。
29.波浪形滑槽波峰为水平设置;当凸块8滑入波浪形滑槽波峰时,此时不会带动固定环7运动,即保证活塞板5处于稳定状态,保持环形出液腔通过环形槽与反应釜本体1内部下方相连通,使得环形出液腔内的液体回流至反应釜本体1中液体的上层。
30.反应釜本体1上端至少设有两个进液管,两个进液管输出端与导液环9内部相连通;使得液体加入至导液环9内,并经过导液环9的出液孔流出,实现向反应釜本体1内分散加入添加液的效果。
31.空心搅拌轴2侧壁中部对称开设有两个与导液环9内部相连通的出液口。
32.工作原理:使用时,在搅拌过程中,空心搅拌轴2转动带动伞状导流板6转动,伞状导流板6带动凸块8转动,通过凸块8与波浪形滑槽的相互配合,使得固定环7上下运动,进而带动活塞板5上下运动,活塞板5向下运动过程中,由于刚开始环形出液腔与活塞板5下方不连通,挤压使得反应釜本体1下方的液体经过空心搅拌轴2流入活塞板5上方,当凸块8滑到波浪形滑槽波峰时,此时环形出液腔与环形槽相连通,即与活塞板5下方连通,然后活塞板5上方的液体流回反应釜本体1中液体的上层,进而实现上下层液体混合的效果。
33.以上所述,仅为本实用新型较佳的具体实施方式,但本实用新型的保护范围并不局限于此,任何熟悉本技术领域的技术人员在本实用新型揭露的技术范围内,根据本实用新型的技术方案及其实用新型构思加以等同替换或改变,都应涵盖在本实用新型的保护范围之内。