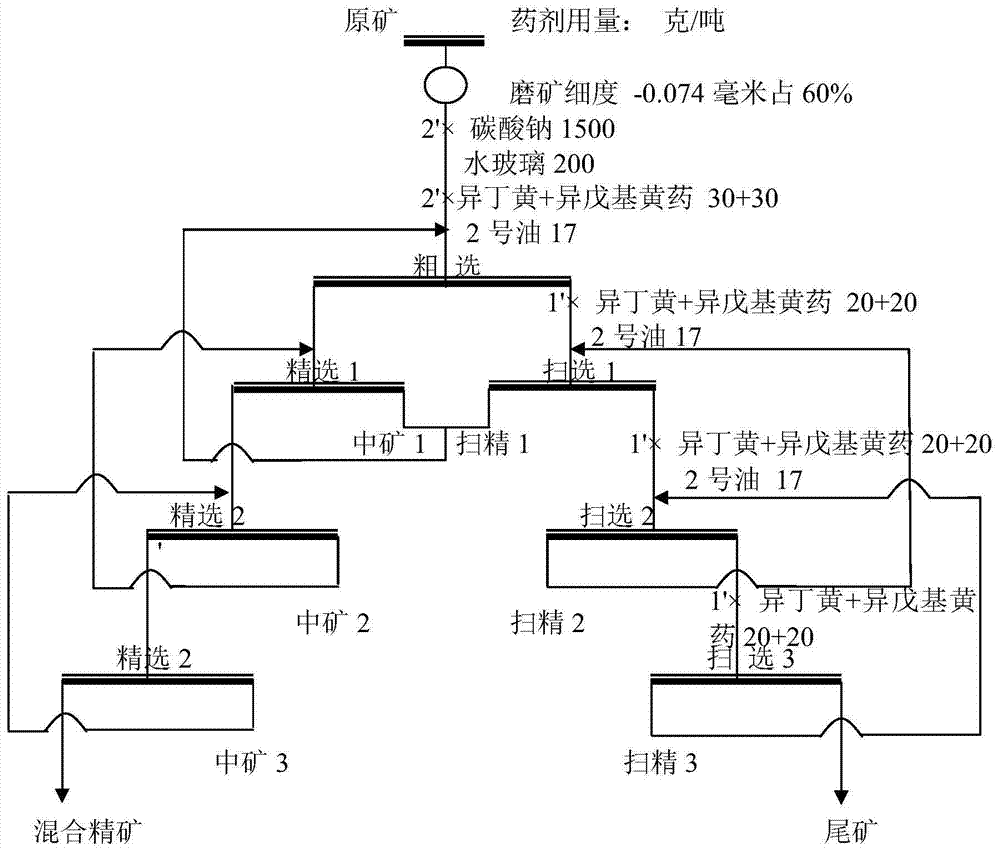
本发明涉及选矿领域,具体涉及一种能从金精矿中回收铅的方法。
背景技术:金矿石常采用原矿磨矿-浮选得金精矿-金精矿细磨-氰化浸出工艺获取成品金。而大部分金矿中含有低品位的有色金属元素,如铅等。其价值大约是金价值的10%左右,而采用上述工艺不能回收这些有价元素,导致了原料的浪费。而企业不愿综合回收这些有价元素的主要原因有两方面:1.在金价高位运行时期,企业重视金产量,忽视铅等伴生元素的回收研究工作,不愿投入时间精力研发、改造。2.在金价低迷时期,企业又无力进行流程优化、改进,因此造成了资源的极大浪费。从目前经济和技术分析,要回收伴生的铅元素,存在以下技术问题:1.若从原矿直接分离金、铅,生产成本高于综合回收铅的产值,成本太高导致经济上不允许此类回收方式;2.若从氰化浸渣中回收铅,由于浸金需要的磨矿细度极细,通常在45微米以下,此时方铅矿已严重泥化,选矿工艺难以回收。3.混合精矿(即浮选金矿)可在粒度相对较粗时实现金、铅分离,但势必使一部分金进入铅精矿中,此时铅精矿中的金以较低的系数计价,这部分金与铅精矿价值低于单得成品金所获效益。
技术实现要素:本发明的目的是针对上述现有技术的不足,提供一种浮选金精矿氰化浸出过程中铅的综合回收方法,能够降低成本,回收金矿中的铅。本发明的技术方案是这样实现的:一种浮选金精矿氰化浸出过程中铅的综合回收方法,是按照下述步骤进行的:步骤(1),原矿磨矿,将原矿磨矿至细度为-0.074mm含量60%;步骤(2),浮选得混合精矿,在步骤(1)中得到的每吨原矿矿粒中加入调整剂1500g和分散剂200g混合2~6min,之后再加入捕收剂60g和起泡剂17g混合2~6min后经过一粗三精三扫中矿顺序返回后,得到混合精矿和尾矿,三扫中每次加入捕收剂40g和起泡剂17g混合1~3min;步骤(3),混合精矿金铅分离,得到硫精矿和含金铅精矿,在步骤(2)中得到的每吨混合精矿中加入脱药剂6000g混合4~12min,加入抑制剂2000g混合2~6min,加入乙硫氮20g、丙黄20g和丁铵10g混合2~6min,经过一粗五精两扫中矿顺序返回后,得到含金铅精矿和硫精矿;步骤(4),硫精矿经过细磨、氰化浸出后得到尾渣和含金贵液,将步骤(3)中得到的硫精矿再磨至颗粒细度为-0.030mm含量95%,之后浸入氰化钠液中48h,固液分离后得到贵液1和浸渣1;步骤(5),含金铅精矿经过细磨、氰化浸出后得到铅精矿和含金贵液,将步骤(3)得到的含金铅精矿再磨至颗粒细度为-0.030mm含量95%,之后浸入氰化钠液中24h,固液分离后得到贵液2和浸渣2。所述步骤(3)中两次扫选是指在待扫选颗粒中加入乙硫氮10g、丙黄10g和丁铵5g混合2~6min后扫选、再次加入乙硫氮10g、丙黄10g和丁铵5g混合1~3min扫选。所述调整剂是碳酸钠;所述分散剂是水玻璃,所述捕收剂是异丁黄和/或异戊基黄药;所述起泡剂是2号油。与现有技术相比,本发明具有以下优点:1.从混合精矿进行金、铅分离,解决了从原矿金、铅分离生产成本高的问题。2.混合精矿先分离后再磨解决了先再磨后分离造成的方铅矿泥化回收难的问题。3.铅精矿再磨浸出,避免了部分金进入铅精矿中导致金回收率低的问题。附图说明为了更清楚地说明本发明实施例或现有技术中的技术方案,下面将对实施例或现有技术描述中所需要使用的附图作简单地介绍,显而易见地,下面描述中的附图仅仅是本发明的一些实施例,对于本领域普通技术人员来讲,在不付出创造性劳动的前提下,还可以根据这些附图获得其他的附图。图1为本发明的工艺流程图。图2为原矿浮选工艺流程图。图3为混合精矿铅硫分离-含金铅精矿、硫精矿分别再磨浸出工艺流程图。图2和图3中t代表该步骤中的混合搅拌时间,这两幅图中显示的时间是实验室中选矿的混合搅拌时间,在工业选矿中,对应步骤的混合搅拌时间是图中显示的2~3倍。具体实施方式下面将结合本发明实施例中的附图,对本发明实施例中的技术方案进行清楚、完整地描述,显然,所描述的实施例仅仅是本发明一部分实施例,而不是全部的实施例。基于本发明中的实施例,本领域普通技术人员在没有付出创造性劳动前提下所获得的所有其他实施例,都属于本发明保护的范围。如图1~3所示,一种浮选金精矿氰化浸出过程中铅的综合回收方法,是按照下述步骤进行的:步骤(1),原矿磨矿,将原矿磨矿至细度为-0.074mm含量60%;步骤(2),浮选得混合精矿,在步骤(1)中得到的每吨原矿矿粒中加入调整剂1500g和分散剂200g混合2~6min,之后再加入捕收剂60g和起泡剂17g混合2~6min后经过一粗三精三扫中矿顺序返回后,得到混合精矿和尾矿,三扫中每次加入捕收剂40g和起泡剂17g混合1~3min;所述一粗三精三扫中矿顺序返回是指经过一次粗选、三次精选、三次扫选,中矿返回重新返回至上一作业,其中,所用调整剂是碳酸钠;所述分散剂是水玻璃,所述捕收剂是异丁黄和异戊基黄药各20g;所述起泡剂是2号油。异戊基黄药也可以用MB替代。在原矿浮选金精矿的过程中,三次精选过程得到混合精矿,混合精矿含铅,精选过程可以提高金的品位,而扫选得到尾矿,扫选则主要是提高金的回收率。步骤(3),混合精矿金铅分离,得到硫精矿(硫精矿含金,又称为硫(金)精矿)和含金铅精矿,在步骤(2)中得到的每吨混合精矿中加入脱药剂6000g混合4~12min,加入抑制剂2000g混合2~6min,加入乙硫氮20g、丙黄20g和丁铵10g混合2~6min,经过一粗五精两扫中矿顺序返回后,得到含金铅精矿和硫精矿;所述脱药剂是硫化钠,所述抑制剂是石灰,石灰可以抑制黄铁矿;而乙硫氮、丙黄和丁铵则是作为捕收剂。步骤(4),硫精矿经过细磨、氰化浸出后得到尾渣和含金贵液,将步骤(3)中得到的硫精矿再磨至颗粒细度为-0.030mm含量95%,之后浸入氰化钠液中48h,固液分离后得到贵液1和浸渣1;其中浸渣1的主要成分是黄铁矿,贵液1为含金溶液。氰化钠浸渍的条件为:浸渍时间48h,加入石灰2000g左右调节pH值为11,氰化钠的加入量为5000g左右,硫精矿的液固比为2:1,其中石灰和氰化钠的加入量是指每吨混合精矿中的用量。步骤(5),含金铅精矿经过细磨、氰化浸出后得到铅精矿和含金贵液,将步骤(3)得到的含金铅精矿再磨至颗粒细度为-0.030mm含量95%,之后浸入氰化钠液中24h,固液分离后得到贵液2和浸渣2。其中浸渣2的主要有效成分是方铅矿,而贵液2含金溶液。氰化钠浸渍条件为:浸出时间24h,加入石灰2000g左右至pH值为11,加入氰化钠5000g左右,其中含金铅精矿的固液比为2:1(质量比)。上述石灰和氰化钠的加入量是指每吨混合精矿中的用量。其中,步骤(3)中五次精选过程如下(这个过程加入的药剂量是每吨混合精矿中需要的用量):第一步精选是将待精选矿中加入石灰800g混合2~6min后分选,符合要求的颗粒进入二级精选、其余的再次进行初级精选,其中二级精选是加入石灰500g混合2~6min后分选,符合要求的颗粒进入三级精选,其余的再次进行初级精选;三级精选是加入石灰500g混合2~6min后分选,符合要求的颗粒进入四级精选,其余的再次进行初级精选;五级精选和四级精选相同,五级精选后符合要求的为含金铅精矿。所述步骤(3)中扫选步骤是在待扫选颗粒中加入乙硫氮10g、丙黄10g和丁铵5g混合2~6min后分选,符合要求颗粒再次加入乙硫氮10g、丙黄10g和丁铵5g混合1~3min,符合要求的颗粒是硫精矿,其余的重新进入扫选流程。现有技术中,浮选后的混合精矿直接经过再磨、浸液步骤,矿粒太小,无法回收方铅矿。而本申请中,浮选后的混合精矿再经过粗选后的颗粒分为两部分,加入石灰做抑制剂,可以抑制黄铁矿,浮选方铅矿。而扫选得到硫精矿的过程,其目的主要是提高铅回收率。下面结合具体实施方式说明本发明的实施过程和效果:表1矿石中主要矿物的相对含量(%)非金属矿物石英钾长石斜长石绢云母黑云母含量25.229.33.45.65.1非金属矿物方解石白云石绿泥石萤石含量4.212.910.21.7非金属矿物黄铁矿方铅矿黄铜矿闪锌矿含量1.90.2少量少量本发明所选择的原矿经过测量,主要含量如表1所示,其中金赋存于黄铁矿中,是主要回收的矿物。另方铅矿含量0.2%,可综合回收。原矿磨矿之后浮选得到混合精矿,浮选结果如下:表2原矿浮选结果混合精矿后经过步骤(3)得到含金铅精矿和硫精矿,具体结果如表3所示。表3金铅分离闭路结果含金铅精矿、硫精矿氰化浸出后结果如表4所示。表4金精矿、铅精矿分别氰化浸出结果注:金总回收率为39.16+2.72+52.67=94.55%。从表1~4可以看出,与现有技术变比,本发明具有以下特点:1、本申请工艺与原有工艺实验室选矿指标对比表明,除综合回收了方铅矿外,还可较大幅度提高金银回收率:可获得产率4.59%,铅品位56.73%,铅回收率79.83%的铅精矿,金总回收率为94.55%,银总回收率为91.67%,高出原有工艺3.85%、9.42%。2、由于浮选混合精矿产率较小,金、铅分离及铅细磨浸出工艺生产成本增加有限,远低于所获铅精矿以及金、银增加回收率所增效益。针对一个原矿金品位1.5克/吨,铅品位0.3%,日处理500吨的金选厂,项目改造后年增加效益五百余万元,占主产品金产值的14%,半年可收回基建投资。3、本发明可分阶段实施,在不影响正常生产进度的前提下,对原有工艺流程改动少,改造工程量小,切实可行,项目改造投资回收期短。4、本发明的工艺方法有助于增加企业效益,提高我国伴生资源综合利用率。目前金价处于低迷期,本发明的工艺有利于原矿品位低的金矿企业注重这部分有价元素的回收。以上所述仅为本发明的较佳实施例而已,并不用以限制本发明,凡在本发明的精神和原则之内,所作的任何修改、等同替换、改进等,均应包含在本发明的保护范围之内。