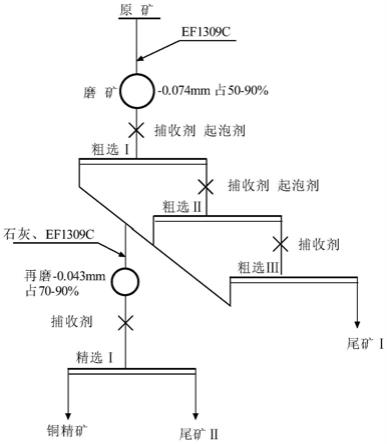
1.本发明涉及矿物冶金加工技术领域,特别是涉及一种含水溶性铜的硫化铜矿铜硫分离用组合抑制剂及方法。
背景技术:2.铜硫矿资源作为重要战略资源,在世界矿产资源中占有重要地位。铜硫共生是硫化铜石中最为常见的类型,而此类矿石中有时存在着水溶性铜矿物,如胆矾是一种天然含有结晶水的硫酸铜,分布情况很广,亦称其蓝矾或铜矾,其化学式为cuso4·
5h2o,容易溶解,造成矿浆中出现大量的cu
2+
活化硫铁矿(包括黄铁矿、磁黄铁矿、白铁矿等)使得铜硫分离变得更加困难。虽然近年来在含水溶性的硫化铜矿石选矿技术上有一定的发展,但其适应性较差,选矿技术指标参差不齐,存在诸多弊端。
3.铜硫分离的实质就是将铜矿物与硫矿物分离,铜硫分离过程中涉及到铜矿物有黄铜矿、辉铜矿、斑铜矿、铜蓝等,硫矿物主要有黄铁矿、磁黄铁矿和白铁矿等。目前生产中最为常见的浮选工艺就是“抑硫浮铜”工艺和“铜硫混浮
‑
铜硫分离”工艺。常在高碱条件下把石灰作为抑制剂实现铜硫分离,石灰用量过大时对黄铜矿、斑铜矿等铜矿物有一定程度的抑制,并且随着石灰用量的增大,出现管道堵塞、结垢、腐蚀设备,造成选矿废水因为ph值过高不达标,铜精矿品位低等现象。
4.现有传统方法的缺点是,(1)加入硫化钠沉淀cu
2+
,硫化钠的用量难易控制,过量对铜矿物有明显的抑制作用;另外,硫化钠对环境有明显的负面影响。(2)加入大量的石灰抑制硫铁矿,浮选铜矿物。第一,矿浆中的石灰能够促进粘土矿物颗粒与硫化铜矿物颗粒异相凝聚,不利于矿物颗粒的分散与浮选分离;第二,大量的石灰对黄铜矿、斑铜矿等铜矿物有的可浮性有较大影响;第三,石灰用量大,出现管道堵塞、结垢、腐蚀设备,尤其是当石灰造成矿山废水因ph值过高不达标等现象。第四,石灰用量大,不利于矿石中金银矿物的综合回收。第五,采用亚硫酸钠、腐殖酸钠、焦亚硫酸钠、木质素、氰化物等辅助抑制剂与石灰组合作铜硫分离的抑制剂的情况,也存在诸多弊端,如石灰的用量难以大幅度降低,辅助抑制的用量较大且效果不明显或者对环境有一定的污染,铜硫分离效果不理想。
5.因此,研究含水溶性铜矿物的铜硫分离的高效、环保的铜硫分离技术,既符合当前节能环保的国家政策,也可促进矿产资源高效综合回收利用,为企业创造更多的经济效益。
技术实现要素:6.本发明的目的在于提供一种含水溶性铜的硫化铜矿铜硫分离用组合抑制剂及方法,以克服因为水溶性铜矿物的存在,导致铜硫矿中铜硫分离困难,选矿药剂用量大、药剂成本高、铜精矿品位低,且铜选矿尾矿水因ph值过高带来的环保问题;该方法具有分离效果好、操作使用简单、适应能力强、技术指标良好且稳定、药剂绿色环保等特点。
7.本发明的上述目的是通过以下技术方案实现的:
8.根据本发明的一个方面,本发明提供的一种含水溶性铜的硫化铜矿铜硫分离用组
合抑制剂,所述组合抑制剂包括:第一抑制剂和第二抑制剂,所述组合抑制剂在常温常压下,按质量比为(60.0~90.0)∶(10.0~40.0)配比混合,搅拌30~60min制备得到;其中,所述第一抑制剂包括过碳酸钠、过碳酸钾以及过硫酸氢钾中的一种或多种的混合物;所述第二抑制剂包括腐殖酸钙盐、腐殖酸钠盐、腐殖酸铵盐以及腐殖酸钾盐中的一种或多种的混合物。
9.根据本发明的另一个方面,本发明提供的一种含水溶性铜的硫化铜矿铜硫分离方法,包括:
10.向硫化铜矿中加入如权利要求1所述的组合抑制剂进行磨矿,调节矿浆质量浓度为15~45%,矿浆ph为7~8.5;加入捕收剂和起泡剂进行至少三次铜硫分离粗选,得到混合粗精矿和粗选尾矿;
11.对所述混合粗精矿分级后进行再磨处理,再磨处理时添加石灰和所述组合抑制剂,调节矿浆质量浓度为25~30%,控制矿浆ph值为9~11.5;对再磨矿后矿浆进行铜硫分离精选。
12.可选地,磨矿处理时,所述组合抑制剂加入量与矿浆质量比为(0.01~0.2):1000。
13.可选地,再磨矿处理时,所述组合抑制剂加入量与矿浆质量比为(0.01~0.4):1000。
14.可选地,磨矿处理时,所述组合抑制剂加入量与矿浆质量比为(0.1~0.2):1000。
15.可选地,再磨矿处理时,所述组合抑制剂加入量与矿浆质量比为(0.1~0.4):1000。
16.可选地,磨矿处理时,磨矿至细度
‑
0.074mm占50%~90%。
17.可选地,再磨矿处理时,磨矿至细度
‑
0.043mm占70~90%。进一步地,再磨矿处理,磨矿至细度
‑
0.038mm占70~90%。
18.可选地,磨矿处理时,搅拌反应时间为2min~6min。
19.可选地,再磨矿处理时,搅拌反应时间为3min~20min。
20.下面对本发明的作用机理进行如下描述:
21.本发明中组合抑制剂中的腐殖酸盐分子中含有
‑
oh、
‑
ch2o、
‑
cooh、
‑
nh2等大量的极性基团,在水中可以与多种金属离子形成金属螯合物,如与fe
3+
、fe
2+
、cu
2+
、zn
2+
、mn
2+
、ni
2+
等,减少了矿浆中对硫铁矿物有活化能力的离子浓度,从而消除cu
2+
等对硫铁矿的活化作用。
22.本发明组合抑制剂中的过碳酸钠(钾)、过硫酸氢钾,在矿浆中与水发生如下反应:
23.过碳酸钠发生如下反应:
24.na2co4+h2o=na2co3+h2o225.2h2o2+3fe
2+
=2h2o+2fe
3+
+o2↑
26.fe
3+
+3oh
‑
=fe(oh)3↓
27.过硫酸氢钾发生如下反应:
28.2hso
‑5+h2o
→
2so
‑4+h2o229.2so
‑4·
+h2o
→
2so2‑4+h
+
+h2o
·
30.过碳酸钠(过碳酸钾与过碳酸钠类似)与水反应生成的h2o2,以及过硫酸氢钾与水反应生成的so4‑
·
和ho
·
是强氧化剂,一方面通过氧化作用调节矿浆的电位,使硫铁矿物
表面在氧化作用下生成亲水物质,以达到抑制硫铁矿物的作用;另一方面,将矿浆中的fe
2+
氧化成fe
3+
,在碱性矿浆中更容易生fe(oh)3沉淀,从而消除fe
2+
对硫矿物的活化作用。
31.石灰能提高矿浆的ph值,造成硫铁矿的可浮性迅速下降,另外,ca
2+
和[caoh]
+
能选择地吸附于硫矿物表面,改变其表面电性和增强亲水性,从而可浮性降低。
[0032]
本发明组合抑制剂中各组分在浮选过程中,既发挥自身的优势又互相协同作用,功能互补,强化了对硫铁矿的抑制作用;本发明所采用的组合抑制剂ef1309c浮选含水溶性铜的硫化铜矿物,可在较低的矿浆ph值下抑制黄硫铁矿,实现了含水溶性铜的铜硫矿低碱度下清洁分离,为硫化铜矿物选矿指标的提高和选矿废水达标排放提供了很好的技术支撑,这一创造性的思想和组合使用的各种药剂及成套技术形成一种适应能力强、回收指标高、环保清洁的含水溶性铜的铜硫矿的选矿新方法。
[0033]
与现有技术相比,本发明含水溶性铜的硫化铜矿铜硫分离用组合抑制剂及方法,针对含水溶性铜的硫化铜矿石,通过添加组合抑制剂ef1309c消除了次生铜的影响,抑制了硫铁矿,达到了低碱度下铜硫高效分离,并取得较好的技术指标。
[0034]
具体地,本发明主要通过组合抑制剂ef1309c强化对硫铁矿物的抑制,消除矿浆中cu
2+
对硫铁矿物的活化,促使硫铁矿物表面生成亲水物质,通过捕收剂(如异丁基钠黑药)选择性对硫化铜矿物的捕收。同时,铜硫分离浮选前不需要采用生石灰将矿浆ph调整到强碱性,该组合抑制剂的添加能有效地螯合铜离子、铁离子、亚铁离子等,消除这些离子对硫铁矿物的活化作用,从而实现硫化铜矿物与硫铁矿物的高效分离,实现了低碱度清洁分离。
[0035]
本发明具有分离效果好、选矿指标稳定、药剂消耗量少、组合抑制剂较传统抑制剂清洁环保,操作简便、易于现场操作管理的特点,适合复杂难选铜硫矿选矿的新方法,适于推广应用。
附图说明
[0036]
图1是对比例中的铜硫分离方法的流程图;
[0037]
图2是本发明实施例中含水溶性铜的硫化铜矿铜硫分离方法的流程图。
具体实施方式
[0038]
下面将结合本发明实施例中的附图,对本发明实施例中的技术方案进行清楚、完整地描述,显然,所描述的实施例仅仅是本发明一部分实施例,而不是全部的实施例。以下对至少一个示例性实施例的描述实际上仅仅是说明性的,决不作为对本发明及其应用或使用的任何限制。基于本发明中的实施例,本领域普通技术人员在没有作出创造性劳动前提下所获得的所有其他实施例,都属于本发明保护的范围。
[0039]
本发明提供一种含水溶性铜的硫化铜矿铜硫分离用的组合抑制剂,包括:第一抑制剂和第二抑制剂,其中,所述第一抑制剂包括过碳酸钠、过碳酸钾以及过硫酸氢钾中的一种或多种的混合物;所述第二抑制剂包括腐殖酸钙盐、腐殖酸钠盐、腐殖酸铵盐以及腐殖酸钾盐中的一种或多种的混合物。进一步地,所述组合抑制剂是在常温常压下,按质量比为(60.0~90.0)∶(10.0~40.0)配比混合,搅拌30~60min制备得到。进一步地,质量比可以为(70.0~80.0)∶(20.0~30.0)。
[0040]
图1示意性地示出了实施例中含水溶性铜的硫化铜矿铜硫分离方法的流程。如图1
所示,含水溶性铜的硫化铜矿铜硫分离方法可以包括对铜硫矿原矿进行破碎、磨矿、调浆、铜硫矿粗扫选、粗选精矿再磨后精选等步骤。
[0041]
本发明提供的所述含水溶性铜的硫化铜矿铜硫分离方法,具体地可以包括以下步骤:
[0042]
(1)、将原矿破碎、磨矿,使铜硫矿中的有用矿物与脉石矿物较好单体解离,磨矿至粒度
‑
0.074mm占50~90%;磨矿时加入本发明组合抑制剂ef1309c,用量为20~200g/t,搅拌,进行硫铁矿的抑制及cu
2+
的消除反应,反应时间为2
‑
6min,将磨矿后的矿石调浆至质量浓度为15%~45%,矿浆的ph值为7~8.5。该步骤中添加组合抑制剂,在磨矿的过程中充分与cu2+作用并且氧化硫矿物表面使其失去可浮性。
[0043]
(2)、往步骤(1)磨矿后的矿浆中按20~100g/t加入捕收剂异丁基钠黑药,搅拌2
‑
3min;按10~80g/t加入起泡剂甲基异丁基甲醇,搅拌2
‑
3min,进行第一次铜硫混合粗选,粗选时间为4
‑
8min,获得铜硫混合粗精矿ⅰ和第一次粗选尾矿。本发明中捕收剂不限于此,例如还可以为乙硫氨酯、异丁基钠黑药、丁基黄药等中的一种或几种,起泡剂为甲基异丁基甲醇,浮选5
‑
10min。
[0044]
(3)、往步骤(2)得到的第一次粗选尾矿中,按10~100g/t加入捕收剂丁基黄药,搅拌2
‑
3min;按5~30g/t加入起泡剂甲基异丁基甲醇,搅拌2
‑
3min,进行第二次铜硫混合粗选,粗选时间为4
‑
6min,获得铜硫混合粗精矿ⅱ和第二次粗选尾矿;
[0045]
(4)、往步骤(3)得到的第二次粗选尾矿中按5~20g/t加入捕收剂丁基黄药,搅拌2
‑
3min,进行第三次铜硫混合粗选,粗选时间为2
‑
4min,获得铜硫混合粗选精矿ⅲ和全流程浮选尾矿ⅰ;
[0046]
(5)、将步骤(2)、(3)、(4)中得到的铜硫混合粗选精矿进行分级,分级粒度为0.038mm,
‑
0.038mm直接进入铜硫分离作业,+0.038mm进入球磨机再磨,再磨时添加石灰100~500g/t、ef1309c 30~400g/t,搅拌3
‑
20min,控制矿浆ph值为9~11.5。再磨至
‑
0.038mm占70~90%,旋流器溢流调浆至矿浆质量浓度为25~30%。该步骤再磨时加入组合抑制剂以进行cu
2+
、fe
2+
、fe
3+
的消除反应硫铁矿表面氧化反应,充分与cu
2+
作用并且氧化硫矿物表面使其失去可浮性。
[0047]
(6)、将步骤(5)中再磨后的铜硫混合粗精矿进入铜硫分离作业;按5~30g/t加入捕收剂异丁基钠黑药,搅拌2
‑
3min分钟,进行浮选,浮选时间为6
‑
8min,获得铜硫分离一次精矿和铜硫分离粗选尾矿;
[0048]
(7)、将步骤(6)中的铜硫分离一次精矿进行铜硫分离精选,添加抑制剂石灰50~500g/t,搅拌3
‑
10min,进行浮选,浮选时间为4
‑
6min,获得铜精矿和精选中矿;铜硫分离粗选尾矿按5~20g/t添加捕收剂丁基黄药,搅拌2
‑
3min,进行两次扫选,获得扫选中矿和全流程浮选尾矿ⅱ;
[0049]
(8)、将步骤(7)中的铜硫分离精选中矿和铜硫分离扫选中矿按顺序返回上道作业,形成闭路循环。
[0050]
本发明中,上述铜硫矿中硫化铜矿物以黄铜矿、辉铜矿、斑铜矿为主另外还有水溶性铜矿物,黄铜矿、辉铜矿、斑铜矿的质量百分数分别在0.5~6%、0.2
‑
4%、0.1~1.5%之间,另外含有质量百分数为0.02~0.2%的水溶性铜矿物;硫铁矿矿物为黄铁矿、磁黄铁矿和白铁矿,其中含硫矿物的质量百分数在2~30%之间。其中,在铜硫混合粗选、铜硫分离粗
选和铜硫分离扫选中,可以采用异丁基钠黑药或丁基黄药为捕收剂,采用甲基异丁基甲醇为起泡剂;铜硫分离粗选和铜硫分离精选中,组合抑制剂ef1309c可以为过碳酸钠(钾)或过硫酸氢钾、与腐殖酸盐(含钙盐、钠盐、铵盐、钾盐等可溶性盐)的组合物。
[0051]
下面结合具体实施例和对比例对本发明的技术方案进行说明:
[0052]
实施例一
[0053]
原矿品位为cu 0.67%、s 5.22%,水溶性铜矿物含铜占铜矿物的12%,金属矿物有辉铜矿、铜蓝、黄铜矿、胆矾、黄铁矿、磁黄铁矿、褐铁矿等。脉石矿物以石英为主,其次为高岭石、云母、钾长岩、绿泥石等。铜矿物嵌布比较复杂,多与黄铁矿和水高岭石连生,其嵌布粒度较细,单体解离度差。
[0054]
该实施例1的步骤1)、3)中加入的组合抑制剂的组分都相同,具体为过碳酸钠和腐殖酸钠;两者比例为过碳酸钠:腐殖酸钠=70:30。
[0055]
工艺流程的具体步骤为:
[0056]
1)将原矿破碎、磨矿,使铜硫矿中的有用矿物与脉石矿物单体解离,磨矿至铜硫矿粒度
‑
0.074mm占65%;磨矿时加入ef1309c 100g/t作为矿浆ph调整剂和抑制剂,加水调浆至矿浆质量浓度为33%,矿浆的ph值为8.3;
[0057]
2)往步骤1)磨矿后的矿浆中加入捕收剂丁基钠黑药、丁基黄药和起泡剂甲基异丁基甲醇,进行三次铜硫混合粗选获得铜硫混合粗精矿和全流程浮选尾矿ⅰ;
[0058]
3)将步骤2)中得到的铜硫混合粗精矿进行再磨,再磨时添加抑制剂ef1309c 180g/t,石灰600g/t,再磨至
‑
0.038mm占89%,加水调降至矿浆质量浓度为25%;
[0059]
4)将步骤5)中再磨后的铜硫混合粗精矿进入铜硫分离作业,矿浆ph值为10.5,搅拌3min,加入捕收剂丁基钠黑药10g/t,搅拌2min分钟,进行浮选,浮选时间为6min,获得铜硫分离一次铜精矿和分离粗选尾矿;
[0060]
5)将步骤5)中的铜硫分离一次精矿进行铜硫分离精选,添加抑制剂石灰200g/t,搅拌3min,进行浮选,浮选时间为6min,获得铜精矿和精选中矿;铜硫分离粗选尾矿添加捕收剂丁基黄药为20g/t,搅拌3min,进行两次扫选,获得扫选中矿和全流程浮选尾矿ⅱ;
[0061]
6)将步骤6)中的铜硫分离精选中矿和铜硫分离扫选中矿按顺序返回上道作业,形成闭路循环。
[0062]
对比例一
[0063]
具体分离流程如图1所示,磨矿时添加石灰2000g/t,辅助抑制剂为亚硫酸钠,用量为500g/t;再磨阶段,加入硫化钠用量50g/t,石灰2000g/t,辅助抑制剂为亚硫酸钠,用量为200g/t;其他流程与实施例一类似。
[0064]
实施例一与对比例一选矿指标见表1。
[0065]
表1实施例一与对比例一选矿指标
[0066][0067]
实施例二
[0068]
原矿品位为cu 0.90%、s 12.6%。该矿石矿物组成较复杂,金属矿物有黄铜矿、辉铜矿、斑铜矿、胆矾、磁黄铁矿、黄铁矿、白铁矿等,胆矾含铜占铜矿物的11.5%。脉石矿物以石英、石榴石为主。
[0069]
该实施例1的步骤1)、3)中加入的组合抑制剂的组分都相同,具体为过碳酸钾和腐殖酸钙;两者比例为过碳酸钾:腐殖酸钙=75:25。
[0070]
工艺流程的具体步骤为:
[0071]
1)将原矿破碎、磨矿,磨矿至铜硫矿粒度
‑
0.074mm占70%;磨矿时加入ef1309c 120g/t作为矿浆ph调整剂和抑制剂,加水调浆至矿浆质量浓度为33%,矿浆的ph值为8.0;
[0072]
2)往步骤1)磨矿后的矿浆中加入捕收剂丁基钠黑药为40g/t,搅拌3min,加入起泡剂甲基异丁基甲醇30g/t,搅拌2min,进行第一次铜硫混合粗选,粗选时间为6min,获得铜硫混合粗精矿ⅰ和第一次粗选尾矿;
[0073]
3)往步骤2)得到的粗选尾矿中加入捕收剂丁基黄药为30g/t,搅拌3min,加入起泡剂甲基异丁基甲醇20g/t,搅拌2min,进行第二次铜硫混合粗选,粗选时间为5min,获得铜硫混合粗精矿ⅱ和第二次粗选尾矿;
[0074]
4)往步骤3)得到的粗选尾矿加入捕收剂丁基黄药为15g/t,搅拌3min,进行第三次铜硫混合粗选,粗选时间为3min,获得铜硫混合粗选精矿ⅲ和全流程浮选尾矿ⅰ;
[0075]
5)将步骤2)、3)、4)、中得到的铜硫粗选混合精矿合并进行再磨,再磨时加入石灰400g/t,ef1309c 360g/t。再磨至
‑
0.038mm占85%,加水调降至矿浆质量浓度为25%;
[0076]
6)将步骤5)中再磨后的铜硫混合粗精矿进入铜硫分离作业,矿浆ph值为10.8,搅拌3min,加入捕收剂丁基钠黑药10g/t,搅拌2min分钟,进行浮选,浮选时间为6min,获得铜硫分离一次铜精矿和分离粗选尾矿;
[0077]
7)将步骤6)中的铜硫分离一次精矿进行铜硫分离精选,添加抑制剂石灰200,搅拌3min,进行浮选,浮选时间为6min,获得铜精矿和精选中矿;铜硫分离粗选尾矿添加捕收剂丁基黄药为15g/t,搅拌3min,进行两次扫选,获得扫选中矿和全流程浮选尾矿ⅱ;
[0078]
8)将步骤7)中的铜硫分离精选中矿和铜硫分离扫选中矿按顺序返回上道作业,形成闭路循环。
[0079]
对比例二
[0080]
具体分离流程如图1所示,磨矿时添加石灰2000g/t,辅助抑制剂为亚硫酸钠,用量为500g/t;再磨阶段,加入硫化钠用量60g/t,石灰2000g/t,辅助抑制剂为亚硫酸钠,用量为300g/t;其他流程与实施例二类似。
[0081]
实施例二与对比例二选矿指标见表2。
[0082]
表2实施例二与对比例二选矿指标
[0083][0084]
由上可知,本发明采用组合抑制剂通过其与铜离子等螯合物作用,对硫铁矿的氧化作用,调节矿浆的电位的作用,消除矿浆中的铜离子对硫铁矿物的活化作用,实现了低碱
度有效清洁分离,并取得较好的技术指标。
[0085]
具体地,具有以下优点:
[0086]
1、该技术大幅度降低石灰的用量。石灰的用量减少75%以上,降低了选矿废水的ph值。选矿废水ph值由石灰工艺的11.3以上降低至9.0以下。
[0087]
2、提高铜硫分离的技术指标。铜品位可提高5个百分点以上,铜回收率可提高5个百分点以上。
[0088]
3、有利于矿石中金银的综合回收。高碱度下进行铜硫分离,金银的矿物受到明显的抑制,而新工艺下,金的回收率可提高10个百分点以上。
[0089]
4、该抑制剂环境友好。组合抑制剂无毒、环保,对环境几乎无不利影响,易降解。
[0090]
本发明的描述是为了示例和描述起见而给出的,而并不是无遗漏的或者将本发明限于所公开的形式。很多修改和变化对于本领域的普通技术人员而言是显然的。选择和描述实施例是为了更好说明本发明的原理和实际应用,并且使本领域的普通技术人员能够理解本发明从而设计适于特定用途的带有各种修改的各种实施例。