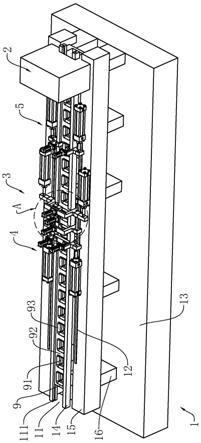
一种载带ccd检测及修复设备
技术领域
1.本技术涉及载带质量检测的领域,尤其是涉及一种载带ccd检测及修复设备。
背景技术:2.载带主要应用于电气元器件贴装工业,是一种带状产品,在长度方向上等距分布着用于盛放电器元器件的孔穴。载带通常和盖带一起配合使用,电子元器件放置在孔穴内之后,盖带会盖设在载带的上方,形成闭合式的包装,用于保护电子元器件。
3.在生产载带的过程中,通常使用载带生产设备,包括工作台、成型装置和输送装置,工作台放置在地面上,成型装置和输送装置设置在工作台上,成型装置为热塑模压成型。原材料为具有特定厚度的带状塑料,原料带在输送装置的作用下在工作台上方沿原料带的长度方向进行步进式移动,在原料带步进式移动停歇的过程中,利用成型装置对原料带进行热塑模压成型,在原料带的中间部位成型孔穴。
4.在成型后,需要对载带进行检测,检测载带中孔穴的成型形状、质量是否达标,检测孔穴之间的间距是否在允许范围内,以及孔穴与载带侧边的距离是否达标。目前的检测方式仍采用人工检测或者工业相机检测,一旦检测到存在质量不合格的部位,通常都只能停机,将不合格部位切断后重新上料,造成生产不连续,各个装置的生产条件都会有所波动,尤其是定位和成型装置的温度变化,从而更加容易产生产品质量不合格的情况。
技术实现要素:5.为了解决检测质量缺陷的产品后会造成生产不连续的问题,本技术的目的是提供了一种载带ccd检测及修复设备。
6.本技术提供的一种载带ccd检测及修复设备,采用如下的技术方案:一种载带ccd检测及修复设备,包括工作台、ccd拍照检测装置、切断装置、热熔装置和输送装置,工作台水平放置,工作台上表面开设有用于容置和支撑载带的容置槽,ccd拍照检测装置用于拍照并对比分析检测载带质量,输送装置、切断装置和热熔装置均安装在工作台上,输送装置并且用于驱动载带沿载带的长度方向步进式移动,经过输送装置驱动的载带依次经过切断装置和热熔装置,所述切断装置能够通过两次切断将载带不合格部位切除,输送装置驱动载带移动后能够将载带的两个断面重合,热熔装置能够热熔接合载带断面重合部位。
7.通过采用上述技术方案,输送装置能够持续将载带向前输送,当ccd拍照检测装置检测到产品有缺陷时,标记产品缺陷位置,当被标记的产品缺陷处移动至切断装置处之后,启动切断装置将标记产品位置的段位切除,随后输送装置能够将切除处段位载带前的载带继续向后输送,使得切除段位载带前、后处的载带对齐,此时使用热熔装置对载带对接处进行热熔,使载带恢复到连续的带状结构,从而利用输送装置继续输送载带,中间没有任何的停机作业,保持载带生产的连续性。
8.优选的,所述切断装置包括切断机构,所述切断机构包括上固定架、下固定架、上
推缸、下推缸、上切刀和下切刀,上固定架、上推缸和上切刀位于工作台上方,下固定架、下推缸和下切刀位于工作台下方,上推缸的缸体与上固定架固定,上推缸的推杆与上切刀固定,下推缸的缸体与下固定架固定,下推缸的推杆与下切刀固定,上切刀和下切刀依次位于容置槽的上方和下方,上推缸能够推动上切刀上下移动,下推缸能推动下切刀上下移动。
9.通过采用上述技术方案,在进行切断作业时,同时启动上推缸和下推缸伸出,同时带动上切刀向下移动和下切刀向上移动,对位于容置槽内的载带进行切断,经过两次切断后,将被标记的缺陷载带段切除。
10.优选的,所述切断机构包括两组,两组切断机构的上推缸的伸缩杆端部固定设置有联动板,两组上切刀固定连接在联动板的下方。
11.通过采用上述技术方案,当两组切断机构通过联动板同时进行切断作业时,就能够一次性切除被标记的载带段,提升效率。
12.优选的,联动板的上方设置有卸料气缸,卸料气缸的缸体固定连接在联动板上方,卸料气缸的伸缩杆从上往下穿过联动板。
13.通过采用上述技术方案,当利用切断机构对被标记的载带段进行切断之后,启动卸料气缸,卸料气缸的伸缩杆能够伸出联动板,将切除后的载带段从容置槽内顶出,从而保证载带段能够顺畅地在容置槽内继续输送,以确保载带的断面处能够对齐。
14.优选的,工作台上设置有导轨,导轨与载带长度方向平行,所述切断装置还包括驱动结构和第一滑块,第一滑块与导轨滑动连接,上固定架和下固定架与滑块固定连接,驱动结构与工作台连接且能够驱动滑块沿导轨往复移动。
15.通过采用上述技术方案,能够通过驱动结构带动滑块移动,从而将载带的切段位让出,以便于热熔装置对载带的断面处进行热熔,降低切断装置与热熔装置互相干涉的可能性。
16.优选的,所述热熔装置包括上热熔板、下热熔板、第二上推缸和第二下推缸,第二上推缸的缸体和第二下推缸的缸体均与工作台连接,上热熔板固定连接在第二上推缸推杆的下端,下热熔板固定连接在第二下推缸推杆的上端,上热熔板和下热熔板依次位于容置槽的上方和下方。
17.通过采用上述技术方案,当需要对载带进行热熔连接时,启动第二上推缸和第二下推缸伸出,带动上热熔板下移,同时带动下热熔板上移,利用上热熔板和下热熔板挤压载带的断面处,将载带的断面处熔化粘合,保证载带的连续性。
18.优选的,所述热熔装置还包括第二驱动结构和第二滑块,第二上推缸的缸体和第二下推缸的缸体均通过连接板与第二滑块固定连接,第二滑块与导轨滑动配合,第二驱动结构与工作台连接且能够驱动第二滑块沿导轨往复移动。
19.通过采用上述技术方案,第二驱动结构能够带动第二滑块在导轨上移动,从而带动上热熔板和下热熔板随第二滑块移动,在需要热熔时利用第二驱动结构带动第二滑块移动,从而将热熔工位移动至载带的断面接合处,降低热熔装置与切断装置互相产生干涉的可能性。
20.优选的,所述切断装置切断载带的长度小于输送装置单次步进移动载带的长度。
21.通过采用上述技术方案,当输送装置再次对载带进行输送时,由于切断的长度比载带每次步进的长度小,因此在载带的断面接合处会有部分的载带重合,从而有助于该部
分的载带热熔后稳定接合,提升载带热熔接合的成功率。
22.优选的,所述ccd检测及修复设备还包括位移微调机构,所述位移微调机构能够带动被切断装置切断后靠近热熔装置处的载带朝向切断装置移动。
23.通过采用上述技术方案,能够利用位移微调机构,将切断后尾部的载带朝向切断装置移动一小段距离,保证在载带的断面接合部位始终有叠加重合的部分,提升载带热熔接合的成功率。
24.优选的,所述位移微调机构包括第三滑块、第三驱动结构、下夹块、上夹块和第三上推缸,第三滑块与导轨滑动配合,所述第三驱动结构能够驱动第三滑块沿导轨往复移动,下夹块和第三上推缸与第三滑块连接,下夹块位于容置槽边缘部位的下方,上夹块位于下夹块和容置槽的上方,所述第三上推缸能够驱动上夹块向下抵接下夹块。
25.通过采用上述技术方案,首先启动第三上推缸,第三上推缸能够带动上夹块向下移动,之后上夹块与下夹块抵接夹紧载带的侧边边缘处,随后启动第三驱动结构,第三驱动结构带动第三滑块移动,从而带动上夹块和下夹块同步移动,最终带动载带移动。
26.综上所述,本技术具有以下技术效果:1、通过设置切断装置和热熔装置,达到了不停机去除缺陷载带的效果;2、通过设置切除载带的长度小于载带步进的长度,达到了提升热熔接合成功率的效果;3、通过设置位移微调装置,达到了提升热熔接合成功率的效果。
附图说明
27.图1是实施例一的整体结构示意图。
28.图2是图1中的局部a处放大图。
29.图3是实施例一中突出显示切断装置结构的剖面示意图。
30.图4是实施例一中突出显示热熔装置结构的剖面示意图。
31.图5是实施例一中突出显示输送装置结构的剖面示意图。
32.图6是实施例二的整体结构示意图。
33.图7是实施例二中突出显示位移微调机构结构的剖面示意图。
34.附图标记说明:1、工作台;11、容置槽;111、支撑槽;12、导轨;13、基台;14、支撑台;141、刀槽;142、热熔口;15、滑动台;16、支撑板;2、ccd拍照检测装置;3、切断装置;31、驱动结构;32、第一滑块;33、切断机构;331、上固定架;332、下固定架;333、上推缸;334、下推缸;335、上切刀;336、下切刀;337、联动板;338、卸料气缸;4、热熔装置;41、第二驱动结构;42、第二滑块;43、第二上推缸;44、第二下推缸;45、上热熔板;46、下热熔板;5、输送装置;51、第三滑块;52、第三驱动结构;53、第二下夹块;54、第二上夹块;55、第三上推缸;6、位移微调机构;61、第四滑块;62、第四驱动结构;63、下夹块;64、上夹块;65、第四上推缸;9、载带;91、孔穴;92、连接部;93、支撑部。
具体实施方式
35.实施例一如图1所示,本实施例介绍了一种载带cdd检测及修复设备,包括工作台1、ccd拍照
检测装置2、切断装置3、热熔装置4和输送装置5,工作台1放置在地面上,载带9则放置在工作台1的上方,沿着载带9的移动方向,ccd拍照检测装置2、输送装置5、切断装置3和热熔装置4依次顺序设置。输送装置5用于步进式输送载带9向前移动,ccd拍照检测装置2用于拍摄载带9,并且将拍摄的照片与数据库进行对比,分析检测具有缺陷的载带9部位,当检测载带9具有缺陷时,会对具有缺陷那段的载带9进行标记,被标记的那段载带9长度通常为每次步进移动的载带9的长度。当载带9被标记的部分移动至切断装置3处,切断装置3会对载带9进行两次切断,从而将被标记的那段载带9切除,之后输送装置5继续将载带9向后移动,此时载带9在断面处对齐,再利用热熔装置4对载带9断面处进行热熔接合,保证载带9的连续性,同时生产能够继续连续进行。
36.在工作的过程中,由于切断装置3的其中一个切断处与热熔装置4的热熔接合处位置是相同的,因此在设置切断装置3和热熔装置4时应当注意避免两个装置之间互相产生干涉。在本实施例中,切断装置3和热熔装置4均设置为相对工作台1滑动连接。
37.如图1所示,载带9上设置有多个孔穴91,多个孔穴91均匀间隔排列,孔穴91之间的部位称为连接部92,孔穴91与载带9侧边之间的部位称为支撑部93。切断装置3和热熔装置4均作用在连接部92上。
38.如图1所示,工作台1包括基台13、支撑台14和滑动台15,基台13放置在地面上,支撑台14和滑动台15位于基台13的上方,滑动台15位于支撑台14的两侧,滑动台15和支撑台14均通过多个竖直的支撑板16与基台13固定连接。支撑台14的中间部位开设有容置槽11,所述容置槽11上下贯穿支撑台14,容置槽11将支撑台14分隔成两块板,支撑台14的两块板均通过支撑板16与基台13固定连接,支撑台14靠近容置槽11的内侧壁向内开设有支撑槽111,当载带9放置在支撑台14上时,载带9的支撑部93的边缘部位位于支撑槽111内,孔穴91位于容置槽11内,通过将支撑部93搭接在支撑槽111内,实现了支撑台14对载带9的支撑。滑动台15上固定设置有导轨12,导轨12的长度方向与载带9的长度方向相同。
39.如图2和图3所示,切断装置3包括驱动结构31、第一滑块32和切断机构33,第一滑块32与导轨12滑动配合,切断机构33与第一滑块32固定连接,驱动结构31连接在滑动台15上,并且能够带动第一滑块32往复移动。驱动结构31在本实施例中选用为气缸,当然也可以选用丝杆滑块机构或者曲柄滑块机构等能够实现往复移动的机构。切断机构33包括上固定架331、下固定架332、上推缸333、下推缸334、上切刀335和下切刀336,上固定架331、上推缸333和上切刀335位于工作台1上方,下固定架332、下推缸334和下切刀336位于工作台1下方,上推缸333的缸体与上固定架331固定,上推缸333的推杆与上切刀335固定,下推缸334的缸体与下固定架332固定,下推缸334的推杆与下切刀336固定,上切刀335和下切刀336依次位于容置槽11的上方和下方,上推缸333能够推动上切刀335上下移动,下推缸334能推动下切刀336上下移动,上切刀335和下切刀336为交错设置。支撑台14在上切刀335和下切刀336所在的位置处开设有刀槽141,以供上切刀335和下切刀336穿过来切断载带9。切断机构33启动时,同时启动上推缸333和下推缸334,带动上切刀335向下移动,同时带动下切刀336向上移动,通过上切刀335和下切刀336的交错作用,将载带9切断。
40.当切断机构33设置为一组时,需要使用一组切断机构33进行两次切断作业。切断装置3使用时,首先启动切断机构33对载带9进行一次切断作业,之后启动驱动结构31,将第一滑块32推动至第二工位,再次启动切断机构33对载带9进行第二次切断作业,实现对被标
记的载带9进行切除。最后,再启动驱动机构31,将第一滑块32和切断机构33复位,确保切断机构33不会与热熔装置4干涉。
41.如图2所示,当切断机构33为两组时,只需同时启动多组切断机构33即可完成对标记段载带9的切除。此时,驱动结构31带动第一滑块32和切断机构33滑动时,是为了移动切断机构33,将切断机构33移出载带9切断的断面处,确保与热熔装置4不会产生干涉。
42.如图2所示,当切断机构33为两组时,两组切断机构33的上推缸333的伸缩杆端部固定设置有联动板337,两组上切刀335固定连接在联动板337的下方,联动板337的上方设置有卸料气缸338,卸料气缸338的缸体固定连接在联动板337上方,卸料气缸338的伸缩杆从上往下穿过联动板337。利用两组切断机构33联动切断被标记段载带9后,再启动卸料气缸338,利用卸料气缸338的推杆向下推动被标记段载带9,能够将被标记段载带9推出容置槽11,从而便于前方的载带9能够在输送装置5的作用下继续向前输送。
43.如图4所示,热熔装置4包括第二驱动结构41、第二滑块42和热熔机构,第二滑块42与导轨12滑动配合,热熔机构固定连接在第二滑块42上,第二驱动结构41固定在滑动台15上并且能够带动第二滑块42进行往复移动。第二驱动结构41在本实施例中选用为气缸,当然也可以选用丝杆滑块机构或者曲柄滑块机构等能够实现往复移动的机构。热熔机构包括上热熔板45、下热熔板46、第二上推缸43和第二下推缸44,第二上推缸43的缸体和第二下推缸44的缸体均通过连接板与第二滑块42固定连接,上热熔板45固定连接在第二上推缸43推杆的下端,下热熔板46固定连接在第二下推缸44推杆的上端,上热熔板45和下热熔板46依次位于容置槽11的上方和下方。支撑台14上开设有用于避让上热熔板45和下热熔板46的热熔口142,其中,热熔口142可以与靠近热熔装置4的刀槽141重合。
44.启动热熔装置4时,首先启动第二驱动结构41,带动第二滑块42移动,使上热熔板45和下热熔板46处于热熔口142处,之后启动第二上推缸43和第二下推缸44,带动上热熔板45下移,同时带动下热熔板46上移,对热熔口142处的载带9进行热熔接合。
45.为了提升热熔接合的成功率,载带9在断面互相对齐后,前段载带9和后段载带9之间最好能够有部分重合叠络,这样通过热熔装置4进行热熔之后,能够将载带9叠络的部分熔化粘合,降低因载带9结合处因载带9断面相距过远而产生热熔失败的可能性,从而大大提升载带9的热熔接合成功率。未达到该效果,在利用切断装置3对载带9的被标记段载带9进行切除时,可以将切除的载带9长度调整为小于载带9每次步进位移的长度,一般为2
‑
4mm,此时当载带9被切除之后,由于剩余载带9长度略大于载带9的步进位移长度,因此当载带9的断面处对齐时,一定会有部分载带9是处于重合叠络状态,确保热熔接合的成功率。
46.如图5所示,输送装置5包括第三滑块51、第三驱动结构52、第二下夹块53、第二上夹块54和第三上推缸55,第三滑块51与导轨12滑动配合,所述第三驱动结构52能够驱动第三滑块51沿导轨12往复移动,第二下夹块53和第三上推缸55均通过连接板与第三滑块51固定连接,第二下夹块53位于容置槽11边缘部位的下方,第二上夹块54位于第二下夹块53和容置槽11的上方,第三上推缸55能够驱动第二上夹块54向下抵接第二下夹块53。启动输送装置5时,首先启动第三上推缸55,第三上推缸55能够带动第二上夹块54向下移动,之后第二上夹块54与第二下夹块53抵接夹紧载带9的支撑部93,随后启动第三驱动结构52,第三驱动结构52带动第三滑块51移动,从而带动第二上夹块54和第二下夹块53同步移动,最终带动载带9移动。之后,启动第三上推缸55收缩复位,此时第二上夹块54和第二下夹块53互相
脱离,松开载带9,再启动第三驱动结构52带动第三滑块51收缩复位,持续往复运动,实现带动载带9步进式移动,每次步进的距离为第三驱动结构52带动第三滑块51移动的距离。第三驱动结构52在本实施例中为气缸,当然也可以选用丝杆滑块机构或者曲柄滑块机构等能够实现往复移动的机构。
47.本实施例的工作过程为:随着输送装置5带动载带9进行步进式输送,ccd拍照检测装置2能对每个输送段的载带9进行拍照检测,当检测到单个输送段载带9上具有缺陷时,标记该段载带9,当被标记段载带9移动至切断装置3时,启动驱动结构31推动第一滑块32滑动,从而使切断机构33对准支撑台14上的刀槽141,之后利用切断机构33切除被标记段载带9,切断完成之后,再利用卸料气缸338将被切断的被标记段载带9推出容置槽11,随后启动驱动结构31,带动第一滑块32和切断机构33复位。
48.随着输送装置5的再次启动,能够继续将载带9向下游输送,从而将上游的载带9断面处向下输送至与下游的载带9断面处对齐,载带9的断面对齐处在热熔口142处。随后启动第二驱动结构41,利用第二驱动结构41推动第二滑块42滑动,将热熔机构上的上热熔板45和下热熔板46与热熔口142对齐,启动热熔机构后,利用上热熔板45和下热熔板46对载带9的断面处进行热熔接合,之后被切断的载带9接合成一个整体,随着输送装置5的继续作用,能够持续将整个载带9向前输送,确保生产的连续性。
49.实施例二如图6和图7所示,与实施例一的区别之处在于,本实施例还包括位移微调机构6,包括第四滑块61、第四驱动结构62、下夹块63、上夹块64和第四上推缸65,第四滑块61与导轨12滑动配合,所述第四驱动结构62能够驱动第四滑块61沿导轨12往复移动,下夹块63和第四上推缸65均通过连接板与第四滑块61固定连接,下夹块63位于容置槽11边缘部位的下方,上夹块64位于下夹块63和容置槽11的上方,所述第四上推缸65能够驱动上夹块64向下抵接下夹块63。
50.当切断装置3进行切断作业并且复位之后,启动第四上推缸65,第四上推缸65能够带动上夹块64向下移动,之后上夹块64与下夹块63抵接夹紧载带9的支撑部93,随后启动第四驱动结构62,第四驱动结构62带动第四滑块61移动,从而带动上夹块64和下夹块63同步移动,最终带动载带9向载带9输送的上游方向移动。之后,启动第四上推缸65收缩,上夹块64和下夹块63互相分离,此时上夹块64和下夹块63脱离载带9,再启动第四驱动结构62收缩,从而带动上夹块64和下夹块63复位。经过上述的动作,位移微调机构6能够将下游被切断的载带9向上游的方向移动一小段距离,从而保证载带9在断面对齐处一定有部分的重合,从而提升载带9热熔接合的成功率。
51.本具体实施方式的实施例均为本技术的较佳实施例,并非依此限制本技术的保护范围,故:凡依本技术的结构、形状、原理所做的等效变化,均应涵盖于本技术的保护范围之内。