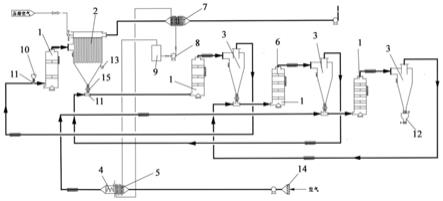
1.本发明属于脱酸工艺技术领域,具体涉及一种用于超细粉体脱酸的系统及工艺。
背景技术:2.当前,高新技术与材料行业飞速发展,超细粉体工业日新月异。超细化后的粉体具有比分散性好、磁性强、活性与热导性能好等特性,已成为各国研究的热点,但制备超细粉体一般由氯化物气相燃烧水解得到,伴随目标产物的生成,同时有hcl产生,由于超细粉体具有较大的比表面积,会使其吸附微量的hcl。在超细粉体的应用场合,对超细粉体吸附的hcl量有严格要求,其中ph值是衡量产品质量的一个重要指标。为了满足各种应用场合的要求,需要把所含hcl脱除,以达到规定的产品质量标准。
3.关于超细粉体脱酸,在《气相纳米tio2流化床脱酸及其机理研究》(刘杰、李春忠、胡彦杰等;中国粉体技术;2007.)、《纳米氧化铝粉体脱酸工艺研究》(石进、颜卫卫、刘国栋;化工时刊;2020)等文献中讲述,传统的脱酸方式为干热空气脱酸、湿热空气脱酸。传统的并流脱酸过程中温度需要一直控制在500℃以上,能耗比较高,且停留时间过长,超细粉体容易团聚。而脱酸装置也多为流化床或脱酸炉,设备占地面积比较大,脱酸后的ph也基本在4左右甚至4以下。
技术实现要素:4.为解决上述问题,本发明的目的在于提供一种用于超细粉体脱酸的系统及工艺。
5.为达到上述目的,提出以下技术方案:
6.一种用于超细粉体脱酸的系统,包括超细粉体进料器、进气系统、初级脱酸系统、多级气固逆流脱酸模组和能量回收系统,初级脱酸系统与多级气固逆流脱酸模组循环连接构成回路,超细粉体进料器设于初级脱酸系统的进料管路上,进气系统连接多级气固逆流脱酸模组,能量回收系统用于回收利用废气热量。
7.进一步地,所述的初级脱酸系统包括旋流器、布袋分离器、星型出料器和文丘里输送器,旋流器的顶部出口与布袋分离器的侧边入口连接,星型出料器和文丘里输送器依次设于布袋分离器的下方出料口,多级气固逆流脱酸模组与布袋分离器连接构成回路,多级气固逆流脱酸模组依次与旋流器和布袋分离器连接构成回路;所述的气固逆流脱酸模组包括旋流器、旋风分离器、星型出料器和文丘里输送器,旋流器的顶部出口与旋风分离器的侧边入口连接,旋风分离器的下方依次设有星型出料器和文丘里输送器或出料装置,n个气固逆流脱酸模组依次连接构成回路,n的取值为1~5。
8.进一步地,进气系统包括过滤器、电加热和鼓风机,过滤器、鼓风机和电加热依次管路连接,电加热管路连接多级气固逆流脱酸模组。
9.进一步地,所述的超细粉体进料器包括料斗和文丘里输送器,文丘里输送器设于初级脱酸系统与多级气固逆流脱酸模组循环连接的管路上。
10.进一步地,能量回收系统包括预热器、冷却器、循环泵和换热介质循环槽,所述预
热器设于电加热的入口前端,冷却器设于布袋分离器的上方出气管路上,预热器与冷却器连接成回路实现热量置换,换热介质循环槽和循环泵设于回路上。
11.进一步地,所述的旋流器的内部设有2
‑
20块旋流板,所述旋流板包括内旋旋流板和外旋旋流板,内旋旋流板和外旋旋流板上下交替分布,旋流板通过设置多块分隔板分隔成多区域,每个区域内均倾斜设置有旋流片,外旋旋流板的旋流片向中心点向下倾斜,内旋旋流板的旋流片向中心点向上倾斜。
12.进一步地,所述的旋流片呈百叶窗式整齐排列,外旋旋流板的旋流片的倾斜角度范围为10~30
°
,内旋旋流板的旋流片的倾斜角度范围为35~70
°
,旋流片之间的距离e设置为d为旋流板直径,d为旋流片的厚度,m为每一块旋流板的旋流片的总片数,θ为旋流片的倾斜角度。
13.进一步地,第n级的旋风分离器下方的出料装置为双蝶阀出料器,用于最后产品的收集;布袋分离器的外部还设有振动器。
14.一种用于超细粉体脱酸的工艺,包括如下步骤:
15.1)开启鼓风机、电加热和循环泵,使热空气依次经过多级气固逆流脱酸模组和初级脱酸系统中,在换热介质循环槽中加入换热介质,使能量回收系统循环;
16.2)温度稳定后,将超细粉体物料通过超细粉体进料器加入初级脱酸系统的旋流器中进行初级脱酸,脱酸后进入布袋分离器进行气固分离,气体从布袋分离器的上方经冷却后吹出,固体进入多级气固逆流脱酸模组进行多级脱酸,脱酸完成后进行收集。
17.进一步地,当初级脱酸后的热空气温度小于100℃时,换热介质循环槽里面的换热介质为水,当一级脱酸后的热空气温度大于100℃时,换热介质循环槽里面的换热介质为导热油,被冷却器冷却后的废气温度约为50℃—80℃,之后由引风机排出体系。
18.本发明的有益效果在于:
19.1)旋流器中的旋流板采用内外旋上下交替排布,被分隔板隔开的每部分旋流片采用百叶窗式的排布方法整齐分布,增强了颗粒之间的破碎,减少团聚体的形成,使得超细粉体更好地进行传热传质;
20.2)当超细粉体在旋流片上随气流旋转,如果旋流片间距太大,传热效果可能不好,旋流片间距离过小,流体阻力过大,粉体在旋流片上旋转时会集聚在一起,精确设置了旋流片间距的计算,合适的距离使气固之间更好地传热传质,减少了超细粉体的团聚与积粉,使得旋流板达到最佳的有益效果;
21.3)本工艺设置了循环回收利用热能系统,以换热介质循环槽、循环泵、冷却器和预热器为基础,进行热量的循环利用,预热器的冷空气至换热介质循环槽,换热介质则通过循环泵进入冷却器与热空气换热升温,换热后的热空气经过预热器与冷空气换热降温,降温后进入换热介质循环槽再次循环,对热量进行了有效利用;
22.4)本工艺采用多级旋流脱酸装置进行多级气固逆流脱酸,得到脱酸产品,通过多级脱酸,有效提高超细粉体脱酸的效果。
附图说明
23.图1为本发明的流程示意图;
24.图2为外旋旋流板的立体结构示意图;
25.图3为内旋旋流板的立体结构示意图;
26.图4为采用不同级数的气固逆流脱酸模组时的ph值;
27.图5为采用不同内旋旋流板旋流片倾斜角度时的ph值;
28.图6为采用不同外旋旋流板旋流片倾斜角度时的ph值;
29.图7为采用不同内旋旋流板旋流片之间距离时的ph值;
30.图8为采用不同外旋旋流板旋流片之间距离时的ph值。
31.图中:1、旋流器;2、布袋分离器;3、旋风分离器;4、电加热;5、预热器;6、旋流板;7、冷却器;8、循环泵;9、换热介质循环槽;10、料斗;11、文丘里输送器;12、双蝶阀出料器;13、振动器;14、过滤器;15、星型出料器;61、分隔板;62、旋流片。
具体实施方式
32.下面结合说明书附图和实施例对本发明做进一步地说明,但本发明的保护范围并不仅限于此。
33.如图1所示,为n取值为3时的一种用于超细粉体脱酸的系统,包括4个旋流器1、1个布袋分离器2、3个旋风分离器3、电加热4、预热器5、冷却器7、循环泵8、换热介质循环槽9、料斗10、4个文丘里输送器11、双蝶阀出料器12、振动器13、过滤器14和3个星型出料器15;第一个旋流器1作为初级脱酸器,其顶部出口与布袋分离器2的侧边入口连接,布袋分离器2的下方出料口依次设有星型出料器15和文丘里输送器11,该文丘里输送器11的一端通过管路与第二个旋流器1的进料口连接,第二个旋流器1的顶部出口与第一个旋风分离器3的侧边入口连接,第一个旋风分离器3的下方出料口依次设有星型出料器15和文丘里输送器11,该文丘里输送器11的一端通过管路与第二个旋流器1的进料口连接,第三个旋流器1、第二个旋风分离器3、第四个旋流器1和第三个旋风分离器3通过与前面相同的连接方式依次连接,第三个旋风分离器2的下方出料口设有双蝶阀出料器12,第一个旋风分离器3的上方出风口通过管路与第一个旋流器1的进料口连接构成回路,连接的管路上设有文丘里输送器11,该文丘里输送器11的上方设有料斗10,第二个旋风分离器3的上方出风口通过管路与布袋分离器2下方的文丘里输送器11的另一端连接构成回路,第三个旋风分离器3的上方出风口通过管路与第一个旋风分离器3下方的文丘里输送器11的另一端连接构成回路,过滤器14依次连接鼓风机、预热器5和电加热4,预热器5设于电加热4的入口端,电加热4通过管路与第二个旋风分离器3下方的文丘里输送器11连接,布袋分离器2的上方出风口的管路上设有冷却器7,冷却器7通过管路与预热器5连接构成循环回路,回路上设有循环泵8和换热介质循环槽9。
34.旋流器1内部都设有旋流板6,旋流板6包括如图2所示的外旋旋流板和如图3所示的内旋旋流板,外旋旋流板和内旋旋流板上下交替设置,旋流板6由多块分隔板61分隔成多区域,每区域内均设有倾斜设置的旋流片62,外旋旋流板的旋流片62向中心点向下倾斜,内旋旋流板的旋流片62向中心点向上倾斜,外旋旋流板的旋流片62的倾斜角度范围为10~30
°
,内旋旋流板的旋流片62的倾斜角度范围为35~70
°
;冷却器7的出风口依次连接有引风机和消音器,布袋分离器2外设有振动器13。
35.实施例1
36.本实施例采用的方案是:所述的内旋旋流板,倾斜角度为45
°
,外旋旋流板,倾斜的角度为15
°
,旋流板6的直径为1m,旋流片62厚约为0.5mm,内旋旋流板用分隔板61分成四个区域,每个区域旋流片62设置为11片,外旋旋流板用分隔板61分成四个区域,每个区域旋流片62设置为8片,内旋旋流板的旋流片62每两片间隔距离约为5
㎝
,外旋旋流板的旋流片62每两片间隔距离约为3
㎝
,实验控制旋流脱酸总时间约为30分钟,采用三级逆流脱酸时,即n为3时,初级脱酸处的旋流器1内部的旋流板6数为2,第二个旋流器1内部的旋流板6数为3,第三个旋流器1内部的旋流板6数为3,第四个旋流器1内部的旋流板6数为3,总旋流板6数为11块。
37.具体过程如下:实验前先检查设备、控制阀、开关等是否正常运作,查看换热介质循环槽9,保证导热油体积占换热介质循环槽9体积的检查完毕后开启过滤器14、鼓风机、预热器5、电加热4,电加热4温度设定为500℃,加热管路都设有保温棉进行保温,防止热量的散失,温度上升至稳定状态,开启冷却器7、循环泵8开关进行能量的回收利用,待系统稳定之后开启压缩空气控制阀,振动器13、引风机、消音器、关风机,关风机频率调至15赫兹,物料选用初始ph约为2.8的超细氧化铝,进料量约为125
㎏
/h,风速设为0.5m/s,2分钟后,超细氧化铝倒入料斗10中,经过关风机,进入文丘里输送器11,随热空气进入到初级脱酸的旋流器1中进行脱酸,超细氧化铝进入旋流器1时,在底部导流板的作用下随气体一起在旋流板6上做不同方向的旋流,最大化地增加了传热传质,超细氧化铝经过初级脱酸的第一个旋流器1后进入布袋分离器2,之后依次进入三级气固逆流脱酸模组,进行多级脱酸,加热后的新鲜空气直接随超细氧化铝进入旋流器1中进行高温脱酸,测得第二个旋流器1进口温度约376℃,分离器出口温度约为325℃,第三个旋流器1进口温度约为428℃,分离器出口温度约为388℃,第四个旋流器1进口温度约为490℃,分离器出口温度约为440℃,脱酸后的物料由双蝶阀出料器12排出系统,收集到99.8%的产品;初级脱酸后的气体换热后经引风机、消音器排出,最后脱酸后的热空气则进入第三个旋流器1继续利用,经过第二个旋流器1脱酸后的热空气则进入料斗10下的文丘里输送器11进行循环利用;换热介质循环槽9中的导热油经过循环泵8进入冷却器7换热空气,测得最后排气温度为90℃。最后,将1g超细氧化铝充分分散在24克去离子水中制成质量分数为4%的悬浮液,经过ph计的检测,脱酸后的超细氧化铝的ph约为5.50,符合产品要求。
38.实施例2
‑439.改变多级气固逆流脱酸模组的级数,n分别为1,2和4,其它条件和实施例1相同,进行实验,对超细氧化铝采用一级脱酸时,即n为1时,总旋流板6数为14块,初级脱酸处的旋流器1内部的旋流板6数为6,第二个旋流器1内部的旋流板6数为8,n为1时,初级脱酸的旋流器1出口与布袋分离器2相连,布袋分离器2下方设有星型出料器15和文丘里输送器11,文丘里输送器11通过管路与一级旋流器1入口相连;一级旋流器1出口和旋风分离器3相接,经预热器5和电加热4加热后的新鲜气体进入一级脱酸模组,对超细粉体进行脱酸,脱酸后的热空气由一级旋风分离器3通过管路回收至初级脱酸系统继续利用,初级脱酸排出的废气则进入冷却器7回收热量后排空,而超细粉体从料斗10经关风机进入初级脱酸系统、一级脱酸模组,得到脱酸产品;对超细氧化铝采用二级逆流脱酸时,即n为2时,总旋流板6数为13块,初级脱酸处的旋流器1内部的旋流板6数为3,第二个旋流器1内部的旋流板6数为5,第三个旋
流器1内部的旋流板6数为5,n为2时,初级脱酸系统的布袋分离器2与一级气固逆流脱酸旋流器1相连,一级旋风分离器3下方设有星型出料器15和文丘里输送器11,文丘里输送器11通过管路与二级旋流器1入口相连,二级旋流器1出口和旋风分离器3相接,经预热器5和电加热4加热后的新鲜气体进入二级脱酸模组,对超细粉体进行脱酸,脱酸后的热空气由二级旋风分离器3通过管路回收至一级脱酸模组,一级脱酸后的热空气则进入初级脱酸系统继续利用,初级脱酸排出的废气则进入冷却器7回收热量后排空,而超细粉体从料斗10经关风机进入初级脱酸系统、一级脱酸模组、二级脱酸模组得到脱酸产品;对超细氧化铝采用四级逆流脱酸时,总旋流板6数为10块,初级脱酸处的旋流器1内部的旋流板6数为2,第二个旋流器1内部的旋流板6数为2,第三个旋流器1内部的旋流板6数为2,第四个旋流器1内部的旋流板6数为2,第五个旋流器1内部的旋流板6为2,n为4时,初级脱酸系统的布袋分离器2与一级脱酸模组的旋流器1相连,一级脱酸模组旋风分离器3下的文丘里输送器11与二级脱酸模组的旋流器1相连,二级脱酸模组旋风分离器3下的文丘里输送器11与三级脱酸模组的旋流器1相连,三级气固逆流脱酸旋流器1出口与旋风分离器3相连,旋风分离器3下方设有星型出料器15和文丘里输送器11,文丘里输送器11通过管路与四级旋流器1入口相连,经预热器5和电加热4加热后的新鲜气体进入四级脱酸模组,对超细粉体进行脱酸,脱酸后的热空气由四级旋风分离器3通过管路依次回收至三级脱酸模组、二级脱酸模组、一级脱酸模组,一级脱酸后的热空气则进入初级脱酸系统继续利用,初级脱酸排出的废气则进入冷却器7回收热量后排空,而超细粉体从料斗10经关风机进入初级脱酸系统、一级脱酸模组、二级脱酸模组、三级脱酸模组、四级脱酸模组得到脱酸产品。
40.经过实验得到如图4所示的在不同级数下的ph值,得到如下结论:在实施例1的实验操作条件下,随着多级气固逆流脱酸模组的级数不断增加,脱酸效果先不断增强,随后趋于平稳,也就是说在n为3时,脱酸效果已经达到最佳。
41.实施例5
‑842.改变内旋旋流板的倾斜角度,分别为35
°
、50
°
、65
°
、70
°
,其它条件和实施例1相同,进行实验。
43.经过实验得到如图5所示的在不同内旋旋流板倾斜角度下的ph值,得出以下结论:在35
°
到45
°
的倾斜角度范围内,随着倾斜角度的增加,脱酸效果逐渐增强,在45
°
到70
°
的范围内,随着倾斜角度的增加,脱酸效果逐渐减弱,倾斜角度主要影响气固间的传热传质,倾斜角度在35
°
到45
°
之间时,随着角度的增大,气固在旋流板6上的接触面积增大,停留时间增长,脱酸效果越来越好,当倾斜角度处于45
°
到70
°
时,倾斜角度过大,气固在旋流板6上的接触面积减小,传热传质效果减弱,脱酸效果也有所下降。
44.实施例8
‑
11
45.改变外旋旋流板的倾斜角度,分别为10
°
、20
°
、25
°
、30
°
,其它条件和实施例1相同,进行实验。
46.经过实验得到如图6所示的在不同外旋旋流板倾斜角度下的ph值,得出以下结论:在10
°
到15
°
的倾斜角度范围内,随着倾斜角度的增加,脱酸效果逐渐增强,在15
°
到30
°
的范围内,随着倾斜角度的增加,脱酸效果逐渐减弱,倾斜角度主要影响气固间的传热传质,倾斜角度在10
°
到15
°
之间时,随着角度的增大,气固在旋流板6上的接触面积增大,停留时间增长,脱酸效果越来越好,当倾斜角度处于15
°
到30
°
时,对于内旋旋流板来说,角度增大,影
响了气流的旋转强度,单位气体损耗的能量更多,传热传质效果减弱,脱酸效果也有所下降。
47.实施例12
‑
15
48.改变内旋旋流板的旋流片62的间距,分别为4.5、5.5、6.5、7,通过改变每一块旋流板6中旋流片62的数量,根据公式确定间距,其它条件与实施例1相同,进行实验。
49.经过实验得到如图7所示的在不同内旋旋流板的旋流片62间距的条件下的ph值,得到如下结论:在内旋旋流板的旋流片62之间的间距为4.5~5.0cm的范围内,随着间距的增大,脱酸效果逐渐增加,在内旋旋流板的旋流片62之间的间距为5.0~7.0cm的范围内,随着间距的增大,脱酸效果逐渐减弱。在4.5~5.0cm的范围内,随着间距空隙的增大,气固相经过旋流板6做内旋运动时的阻力更小,气相湍流增加,粉体在旋流板6上的脱酸效果逐渐增强。当旋流片的间距处在5.0~7.0cm时。在相同的操作条件下,随着间距空隙的增大,粉体返混现象加剧,导致传质面积减小,粉体在旋流板6上的脱酸效果逐渐减弱。
50.实施例16
‑
19
51.改变外旋旋流板的旋流片62的间距,使其分别为2.0、2.5、4.0、5.0,通过改变每一块旋流板6中旋流片62的数量,根据公式确定间距,其它条件与实施例1相同,进行实验。
52.经过实验得到如图8所示的在不同外旋旋流板的旋流片62间距的条件下的ph值,得到如下结论:在外旋旋流板的旋流片62之间的间距为2.0~3.0的范围内,随着间距的增大,脱酸效果逐渐增强,在3.0~5.0的范围内,随着间距的增大,脱酸效果逐渐减弱,在2.0~3.0cm的范围内,随着间距空隙的增大,气体在旋流板6做外旋运动时的阻力更小,气流的外旋强度更大,粉体在旋流板6上的脱酸效果逐渐增强,当旋流片62的间距处.3.0~5.0cm时,在相同的操作条件下,随着间距空隙的增大,对于外旋旋流板来说,气体阻力相对变大,粉体返混现象加剧,导致单位体积气体能量损耗更大,粉体在旋流6上的脱酸效果逐渐减弱。