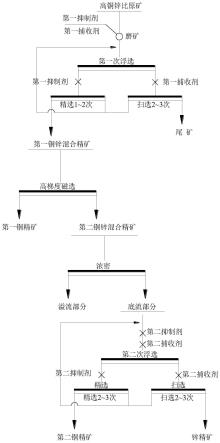
1.本发明涉及矿物加工领域,具体提供了一种高铜锌比硫化铜锌矿选矿分离方法。
背景技术:2.铜锌混合精矿多产自含铜锌硫化矿选矿处理过程中,即含铜锌硫化矿通过铜锌混合浮选获得一个混合精矿产品,再对该混合精矿进行分离处理得到达冶炼标准的铜精矿和锌精矿。由于铜锌矿石在磨矿解离过程中,铜矿物晶格中有游离态的铜离子进入矿浆中,导致铜锌混合精矿中锌矿物可浮性大幅提高,所以当前铜锌混合精矿分离过程中普遍存在着分离难度大,分离效果差,分离后的产品金属互含高等症结。
3.目前很多铜锌硫化矿选矿针对的是铜含量低而锌含量高的低铜锌比原矿,但是在实际原矿中存在大量的铜含量高于锌含量高铜锌比原矿,铜含量高的原矿在磨矿解离过程中会有更多的铜离子进入矿浆中,分离难度更大。在当前铜锌分离工艺为了克服或消除铜离子活化作用对铜锌分离的不利影响,多采用分离前浓密脱药或强化抑制等手段降低混合精矿中闪锌矿的浮游活性,再采用浮铜抑锌的方式进行铜锌分离,但均存在着分离流程长,药剂种类多及药剂成本高等缺陷,尤其是为了降低部分被游离cu
2+
活化的闪锌矿可浮性,常采用大剂量的亚硫酸钠+硫酸锌在矿浆中形成胶体态氢氧化锌对闪锌矿表面实现罩覆,继而达到增大铜锌混合精矿分离效率的目的。
4.近年来,采用高分子抑制剂对闪锌矿表面进行选择性抑制是提高铜锌分离过程中铜锌回收率的重要途径,专利cn201910277352.4提供了一种使用高分子抑制剂为木质素磺酸钙或羧甲基淀粉作为易浮闪锌矿的表面抑制剂,该抑制剂在使用氧化剂和络合剂氧化调控下,可促进其在闪锌矿表面的吸附作用,继而解决了铜锌分离精度不高的问题。此外,采用磁选-浮选联合工艺也是提高铜锌混合精矿分离效率的方法之一,专利cn201610913241.4提供了一种用于铜锌硫化矿分离的磁浮联合选矿工艺,该联合工艺以使用硫酸铜活化后的铜锌混合精矿为对象,经再磨-强磁粗选、精选处理后分别得到铜精矿和锌精矿,该发明专利虽部分解决了铜锌分离困难的难点,但是对于高铜锌比的铜锌硫化矿选矿,由于铜含量高且铜的形态复杂,各形态的铜磁化系数分布很广,磁选工艺难度大,不可避免的会存在铜精矿中锌损失率过高和锌精矿铜含量过高的缺陷。
5.为了解决当前部分铜锌比高的铜锌矿石浮选分离效率低、分离工艺复杂、药剂成本高昂、对环境影响大等问题,开发新的适用于高铜锌比铜锌硫化矿矿石的选矿分离的方法十分必要。
技术实现要素:6.为解决现有技术存在的不足,本发明目的在于提供一种针对高铜锌比原矿的分离方法,实现对于高铜锌比硫化铜锌矿的高效分离,使得分离出的铜精矿中锌互含低、锌精矿中铜互含低,锌回收率提高,分离方法简单稳定,降低药剂的实用量。
7.为实现上述目的,本发明提供了一种高铜锌比硫化铜锌矿选矿分离方法,该方法
以高铜锌比硫化铜锌原矿为原料,其特征在于,包括以下步骤:
8.s1、混合:将高铜锌比铜锌硫化矿原矿矿石与第一抑制剂、第一捕收剂后和水混合进行搅拌、磨矿,形成原矿矿浆,所述第一抑制剂由熟石灰和苯胺黑按重量比8~10:3混合而成,所述第一捕收剂由酯类捕收剂和黄药类捕收剂按重量比2~5:1混合而成;
9.s2、第一次浮选:将原矿矿浆进行第一次浮选得到第一铜锌混合精矿及混合尾矿,混合尾矿抛弃,第一铜锌混合精矿备用;
10.s3、磁选:将第一铜锌混合精矿进行磁选得到磁精矿和磁尾矿,磁精矿即为第一铜精矿,磁尾矿即为第二铜锌混合精矿,所述磁选强度为1.3t,;
11.s4、浓密:将第二铜锌混合精矿进行浓密,浓密底流部分备用,浓密溢流部分抛弃;
12.s5、第二次浮选:将s4中的浓密底流加入第二抑制剂、第二捕收剂后进行第二次浮选,得到第二铜精矿和锌精矿。
13.作为优选,所述步骤s1中原矿矿浆颗粒粒径≤74μm占85%~90%,ph为10~11.5。
14.作为优选,所述步骤s1中第一抑制剂的添加量为500g/t~1000g/t,所述第一捕收剂的添加量为50g/t~70g/t。
15.作为优选,所述步骤s1中所述酯类捕收剂为乙二醚黄原酸甲酸乙酯、乙硫氨酯中的一种或两种,所述黄药类捕收剂为乙基黄药、丁基黄药、异丙基黄药中的一种或两种。
16.作为优选,所述步骤s2中第一次浮选方法包括:将原矿矿浆输送至浮选机中进行充气粗选,得到粗选粗精矿和粗选尾矿,粗选粗精矿加入与第一抑制剂混合进行1~2次精选,粗选尾矿加入第一捕收剂进行2~3次扫选作业,精选尾矿和扫选精矿作为中矿进行顺序返回至上一级浮选作业当中,最后一次扫选的尾矿为可抛弃的尾矿,最后一次精选的精矿为第一铜锌混合精矿。
17.作为优选,所述精选每次加入的第一抑制剂的用量为300g/t~500g/t,所述扫选每次加入的第一捕收剂用量为10g/t~30g/t。
18.作为优选,所述步骤s3中的磁选设备为高梯度磁选机。
19.作为优选,所述步骤s5中第二抑制剂为硫酸锌和焦磷酸钠按质量比5:1混合而成,第二次浮选的粗选作业第二抑制剂用量为200g/t~300g/t,第二捕收剂为乙二醚黄原酸甲酸乙酯、乙硫氨酯中的一种或两种,第二次浮选的粗选作业第二捕收剂用量为10g/t~25g/t。
20.作为优选,所述步骤s5中在第二次浮选过程包括:将浓密底流加入第二抑制剂和第二捕收剂并充分搅拌后的第二混合精矿输送至浮选机中进行充气粗选,得到粗选粗精矿和粗选尾矿,粗选粗精矿加入第二抑制剂进行2~3次精选,粗选尾矿加入第二捕收剂进行2~3次扫选,精选尾矿和扫选精矿作为中矿进行顺序返回至上一级浮选作业当中,最后一次扫选的尾矿为锌精矿,最后一次精选的精矿为第二铜精矿。
21.作为优选,所述精选作业每次加入的第二抑制剂的用量为80g/t~150g/t,所述扫选作业每次加入的第二捕收剂用量为5g/t~10g/t。
22.作为优选,所述高铜锌比硫化铜锌原矿中铜元素的含量在1%~3%,锌元素的含量在0.6%~1%,铜和锌元素含量比为1.6~3:1,同时含有矿物相对含量在8%~20%之间的黄铁矿或磁黄铁矿,其它矿物为常规的硅酸盐或碳酸盐类脉石矿物
23.本发明的主要技术原理为:
24.本发明的选矿分离方法在处理高铜锌比的铜锌硫化矿过程中,在形成原矿矿浆后加入第一抑制剂,可以在第一次浮选过程中使得大部分的黄铁矿和磁黄铁矿被抑制,在多次精选和扫选条件下,矿浆中黄铁矿及磁黄铁矿最终进入混合尾矿之中,矿石中大部分的原生硫化铜矿物(黄铜矿)、次生硫化铜(斑铜矿、辉铜矿、蓝铜矿、黝铜矿)、闪锌矿进入至第一浮选作业浮选精矿中形成了第一铜锌混合精矿,在使用第一捕收剂条件下,通过酯类捕收剂和巯基捕收剂的组合作用可尽可能的提高第一铜锌混合精矿中cu、zn金属回收率,减少金属损失,同时使得铜锌混合精矿的含铁量降到很低。在第一铜锌混合精矿中,铜矿物(包括原生硫化铜和次生硫化铜)为顺磁性矿物,锌矿物(基本为闪锌矿)在含fe量较低时可视为逆磁性矿物,为第一铜锌混合精矿进行磁选奠定基础。
25.在高铜锌比的硫化铜锌矿矿石中,铜矿物种类往往兼具了原生硫化铜和次生硫化铜矿物,而不同种类的硫化铜矿物的比磁化系数差异性较大,如黄铜矿的比磁化系数波动较大,平均比磁化系数为67.53
×
10-9
m3/kg,辉铜矿的比磁化系数为8.5
×
10-9
m3/kg,蓝铜矿的比磁化系数为17
×
10-9
m3/kg。由于不同种类的铜矿物之间的磁性不同,本发明采用1.3t的背景磁场强度条件下进行高梯度强磁选过程,仅回收部分比磁化系数高的铜矿物,得到一个含cu16%~18%、zn 2%~3%的第一铜精矿;而磁选尾矿为第二铜锌混合精矿,在第二铜锌混合精矿中铜矿物的含量和比例得到有效降低,铜锌比从1.1~1.3下降至0.25~0.65,锌品位得以富集,在后续进行第二次浮选时可实现浮少抑多,即抑制矿物量多的锌矿物、浮选矿物量少的铜矿物,降低了浮选难度,在铜上浮过程中通过调控铜精矿中的产率进一步降低铜精矿中不计价锌金属的损失率,锌精矿中铜品位也可以进一步降低。另一方面,在磁选过程中,第一铜锌混合精矿会在磁场产生的脉冲作用下,可进一步分散矿浆,脱附吸附于铜、锌矿物表面的第一捕收剂,在第二铜锌混合精矿浓密脱水时,对分散于矿浆中的第一捕收剂和游离的铜离子(原矿磨矿过程中矿物晶格断裂产生)起到了脱除作用,这极大降低了第二铜锌混合精矿进行铜锌分离的难度,所以在第二次浮选过程中不需要加入活性炭进行吸附处理,加入的第二抑制剂用量较常规的铜锌分离抑制剂用量可大幅度的降低,分离效果更好。
26.与现有技术相比,本发明具有如下有益效果:
27.1.本发明提供的高铜锌比硫化铜锌矿选矿分离方法,工艺流程简单,锌的回收率可以达到70%以上,分离得到的铜精矿中锌互含低、锌精矿中铜互含低,在提高回收率的同时还能提升产品品质,提高矿山整体经济效益,具有广泛的应用前景。
28.2.本发明提供的分离方法,通过将进过浮选后的原矿进行磁选,磁选一方面可以分离出部分磁化系数高的铜矿物形成磁选铜精矿,显著降低高铜锌比原矿中的铜含量,为后续的铜锌进一步分离富集创造条件;另一方面通过磁场脉冲脱附吸附于铜、锌矿物表面的第一捕收剂,经过浓密后脱除第一捕收剂和铜离子,在第二次浮选过程中不需要加入活性炭进行吸附处理,加入的第二抑制剂用量较常规的铜锌分离抑制剂用量可大幅度的降低,这进一步简化了后续的分离工艺流程,并且使得所需的药剂种类和和用量都得以大幅降低,降低生产成本,另外也可以减少添加药剂对于环境的影响,符合绿色经济发展理念。
附图说明
29.图1为本发明的高铜锌比硫化铜锌矿选矿分离方法工艺流程图。
30.图2为常规铜锌混浮-铜锌分离方法工艺流程图。
具体实施方式
31.以下将结合实施例来详细说明本发明。需要说明的是,在不冲突的情况下,本发明中的实施例及实施例中的特征可以相互组合,在不背离本发明精神和实质的情况下,对本发明方法、步骤或条件所作的修改或替换,均属于本发明的范围。
32.实施例1
33.青海某高铜锌比硫化铜锌矿选矿分离
34.青海某含铜锌硫化矿矿山产出的原矿矿石含cu 1.25%、zn 0.86%,原矿铜锌元素含量比1.45,通过铜锌物相及扫描电镜分析可知,矿石中的主要金属矿物和硫化矿,包括黄铁矿、黄铜矿、闪锌矿、磁黄铁矿、砷黝铜矿、辉铜矿、蓝铜矿、赤铁矿等,脉石矿物主要为石英,同时含有部分云母、方解石、斜黝帘石、长石等硅铝酸盐脉石矿物,原矿中的铜以原生硫化矿赋存的铜分布率达到了79.22%,其次为次生硫化铜,分布率为15.42%,锌主要以原生硫化锌(硫化锌)形式赋存,分布率为94.32%,经能谱分析,该矿石中的锌矿物fe含量极低,平均为0.22%~0.68%,矿石中各主要矿物的种类及相对含量如表1所示。
35.表1矿石中各矿物种类及相对含量/%
[0036][0037]
根据附图1所示的工艺流程分离该高铜锌比的铜锌硫化矿矿石,包括以下步骤:
[0038]
(1)将青海某含铜锌硫化矿原矿矿石经原矿粗碎-中碎-细碎至-3mm后,输送至球磨机进行磨矿分级处理,同时在球磨机入口加入熟石灰和苯胺黑按重量比8:3的混合物,添加的用量为800g/t,并加入50g/t乙硫氨酯及10g/t丁基钠黄药并混合,同时加入清水混合至质量浓度为30%~35%的药剂-水-矿石混合体,再进行磨矿,使得磨矿分级溢流产物为
颗粒粒径≤74μm占86%的原矿矿浆,矿浆ph为11.2。
[0039]
(2)矿浆输送至浮选机中进行充气浮选,经过一次粗选、两次扫选和一次精选,精选尾矿和扫选精矿作为中矿进行顺序返回至上一级浮选作业当中,最后一次扫选的尾矿为可抛弃的尾矿,最后一次精选的精矿为第一铜锌混合精矿,其中两次扫选分别加入10g/t乙硫氨酯和5g/t丁基钠黄药,精选加入200g/t的熟石灰和苯胺黑按重量比8:3的混合物,铜锌混合精矿1含cu 15.05%、zn 9.24%,铜锌比为1.63。
[0040]
(3)将步骤(2)所得第一铜锌混合精矿输送至高梯度磁选机中,控制背景磁场强度为1.3t进行磁选,得到第一铜精矿和第二铜锌混合精矿,其中铜精矿1含cu 18.26%、zn 2.33%,第二铜锌混合精矿含cu 11.02%、zn 17.94%,第二铜锌混合精矿的铜锌比为0.61。
[0041]
(4)将步骤(3)所得的第二铜锌混合精矿进行浓密脱水,浓密底流为40%,将该浓密底流输送至浮选机中,同时加入硫酸锌和焦磷酸钠按5:1质量比混合配制的混合物,混合物用量为300g/t,再加入15g/t的乙二醚黄原酸甲酸乙酯,加入药剂调浆搅拌后进行充气浮选,通过一次粗选两次扫选和两次精选得到第二铜精矿和锌精矿,其中两次扫选加入5g/t乙二醚黄原酸甲酸乙酯,两次精选分别加入100g/t的硫酸锌和焦磷酸钠按5:1质量比混合配制的混合物。
[0042]
对比例1
[0043]
青海某高铜锌比矿石常规铜锌混浮-铜锌分离
[0044]
按附图2所示的常规铜锌混浮-铜锌分离的工艺分离青海某含铜锌硫化矿矿山(产地同实施例1)产出的高铜锌比矿石,需要说明的是,对比例1中所采用的常规药剂的种类及使用量为通过相关的条件对比及优化对比试验所得,常规铜锌混浮-铜锌分离的工艺包括以下步骤:
[0045]
(1)将青海某含铜锌硫化矿原矿矿石经原矿粗碎-中碎-细碎至-3mm后,输送至球磨机进行磨矿分级处理,同时在球磨机入口加入熟石灰,添加的用量为2000g/t矿石,并加入60g/t乙硫氨酯及20g/t丁基钠黄药并混合,同时加入清水混合至质量浓度为30%~35%的药剂-水-矿石混合体,再进行磨矿,使得磨矿分级溢流产物为颗粒粒径≤74μm占86%的矿浆,矿浆ph为12.5。
[0046]
(2)矿浆输送至浮选机中进行充气浮选,经过一次粗选两次扫选和一次精选后得到铜锌混合精矿和可弃尾矿,其中两次扫选分别加入20g/t乙硫氨酯和10g/t丁基钠黄药,精选加入1200g/t的熟石灰,铜锌混合精矿含cu 17.89%、zn11.02%,cu/zn比为1.62。
[0047]
(3)将步骤2所得的铜锌混合精矿矿浆依次分别加入450g/t的活性炭,2500g/t硫酸锌、1000g/t亚硫酸钠、50g/t的乙硫氨酯后输送至浮选机中进行充气浮选,经过一次粗选三次扫选和两次精选后得到铜精矿和锌精矿,其中各扫选作业分别加入10g/t的乙硫氨酯,各精选作业加入1000g/t的硫酸锌。最后一次精选泡沫产品为铜精矿,最后一次扫选底流为锌精矿。
[0048]
对比例2
[0049]
青海某高铜锌比矿石铜锌混浮-铜锌分离的工艺
[0050]
本分离步骤取消高梯度磁选,其余药剂种类、用量和工艺步骤均同实施例1。
[0051]
对比例3
[0052]
青海某高铜锌比矿石铜锌混浮-铜锌分离的工艺
[0053]
本分离步骤高梯度磁选磁场强度为1.5t,其余药剂种类、用量和工艺步骤均同实施例1。
[0054]
对比例4
[0055]
青海某高铜锌比矿石铜锌混浮-铜锌分离的工艺
[0056]
本分离步骤高梯度磁选磁场强度为1.1t,其余药剂种类、用量和工艺步骤均同实施例1。
[0057]
实施例1和对比例1~4的高铜锌比矿石分离所添加的试剂种类和用量如表1所示,分离所得到的精矿指标如表2所示。
[0058]
实施例1和对比例1、对比例2各作业所使用的的药剂种类和用量如表2所示。
[0059]
表1实施例1和对比例1~2的各步骤药剂使用种类和用量
[0060][0061]
表1实施例1和对比例1~4的分离产品指标
[0062][0063]
从表1可知,各药剂种类及用量结果可看出,由于实施例1的分离方法降低铜锌分离的难度,其使用的药剂种类和药剂用量相对于对比例1均得到大幅度降低,使成本得到有效降低,且更加环保,具有推广优势。
[0064]
从表2结果可知:
[0065]
1)通过实施例1与对比例1、对比例2的分离得到产品指标结果可看出,采用本技术
提供的分离方法处理青海高铜锌比铜锌硫化矿原矿矿石,有利于铜锌精矿的互含降低。实施例1中的铜精矿1、铜精矿2含zn均低于2.5%,损失于铜精矿中的锌回收率仅为13.68%;对比例1中铜精矿含zn 4.33%,损失于铜精矿中的锌回收率为27.98%;对比例2中铜精矿含zn 3.13%,损失于铜精矿中的锌回收率为20.43%;实施例1中锌精矿含cu 0.67%,对比例1中锌精矿含cu 1.37%,对比例2中锌精矿含cu 1.05%。
[0066]
2)比较实施例1和对比例1、对比例2的分离得到产品指标结果可看出,采用本技术提供的分离方法处理青海高铜锌比铜锌硫化矿原矿矿石,有利于锌精矿的回收率,实施例1中锌精矿中锌回收率70.34%,对比例1中锌精矿中锌回收率57.72%,对比例2中锌精矿中锌回收率64.30%。
[0067]
3)比较实施例1和对比例3、对比例4的分离得到产品指标结果可看出,本发明提供的分离方法采用1.3t的磁场强度,能有效磁选出部分高比磁化系数的铜矿物,磁选出的铜矿物既能保证较低的含锌百分比,锌损失少,且铜的精矿品质较高,又能适当降低高铜锌比硫化矿原矿石中的铜含量,降低铜锌比,更加有利于后续的分离流程。对比例3采用较高强度的磁场强度进行磁选,会将大部分的铜矿物磁选出来,同时也会造成磁选出的铜精矿中锌富含高,造成铜精矿品质降低和锌的大量损失;对比例4采用较低的磁场强度进行磁选,磁选出的铜矿物较少,后续铜锌的分离仍旧难以进行,或者需要大量的药剂使用才能有效分离。
[0068]
以上所述是本发明的优选实施方式,应当指出,对于本技术领域的普通技术人员来说,在不脱离本发明所述原理的前提下,还可以作出若干改进和润饰,这些改进和润饰也应视为本发明的保护范围。