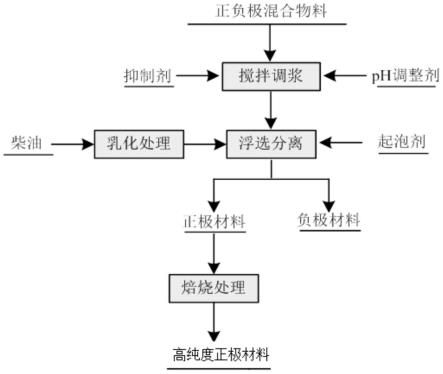
1.本发明属于废旧电池的回收利用领域,尤其涉及一种废旧磷酸铁锂正负极材料的分离回收方法。
背景技术:2.随着科技的发展以及环保要求的日益严格,锂离子电池由于具有高能量密度、高放电电压、长循环性能、低自放电以及环境友好等优点而逐渐成为研究热点并广泛应用于航空航天、电脑、手机、数码相机以及新能源汽车等领域。近年来,随着新能源汽车以及储能技术的快速发展,锂离子电池的需求以及产量得到迅猛发展。因此,锂离子电池的使用必将带来大量电池的报废,若废旧锂离子电池无法得到妥善处置,必然会给资源供应及环境保护带来双重压力。
3.锂离子电池主要包括磷酸铁锂电池和三元电池。若废旧磷酸铁锂电池无法处理回收,不仅造成金属锂等高价成分的资源浪费,其所含有的电解液还会造成环境污染,危害人体健康,因此,开展废旧磷酸铁锂电池回收研究具有重要意义。
4.目前,电池回收主要先通过预处理过程将电池材料拆解,然后采用一定方法对不同有价成分进行分离以便得到铜箔、铝箔以及正负极混合物料等,之后进一步将得到的正负极混合物料进行分离富集,从而得到纯度较高的电极材料以便对其进行再生修复以实现经济价值最大化。然而,目前常用的正负极物料分离手段如磁选、重选等均对处理物料粒度较高,分离效率有限,不仅造成资源损失,也会影响后续再生修复效果,浮选由于其分离效果好、适用性强、成本低廉等优势越来越受到科研工作者的重视,因此,开发一种高效的正负极物料浮选分离方法具有重要意义。
技术实现要素:5.本发明所要解决的技术问题是,克服以上背景技术中提到的不足和缺陷,提供一种废旧磷酸铁锂正负极材料的分离回收方法。
6.为解决上述技术问题,本发明提出的技术方案为:
7.一种废旧磷酸铁锂正负极材料的分离回收方法,包括以下步骤:
8.(1)将废旧磷酸铁锂正负极材料与水混合,加入ph调整剂调整ph至9-10;
9.(2)向步骤(1)后的混合浆料中添加抑制剂并进行搅拌调浆;
10.(3)向步骤(2)后的混合浆料中加入乳化柴油并进行搅拌调浆;
11.(4)向步骤(3)后的混合浆料中加入起泡剂并进行浮选分离,得到精矿石墨负极材料和尾矿磷酸铁锂正极材料;
12.(5)将尾矿磷酸铁锂正极材料进行焙烧处理,得到高纯度的磷酸铁锂正极材料。
13.上述的分离回收方法,优选的,步骤(1)中,ph调整剂为硫酸、盐酸、氢氧化钠、碳酸钠中的一种或几种。
14.上述的分离回收方法,优选的,步骤(2)中,抑制剂为淀粉、木质素磺酸钠、柠檬酸、
单宁酸、草酸中的一种或几种,抑制剂的用量为10~800g/t。
15.上述的分离回收方法,优选的,步骤(2)中,搅拌的速率为1500~2500r/min,搅拌时间为2~5min。
16.上述的分离回收方法,优选的,步骤(3)中,乳化柴油用量为20~1000g/t;搅拌的速率为1500~2500r/min,搅拌时间为2~5min。
17.上述的分离回收方法,优选的,步骤(3)中,乳化柴油是将乳化剂、助乳剂和柴油进行乳化获得的,其中,乳化时间为3~30min,乳化强度为1000~5000r/min。
18.上述的分离回收方法,优选的,所述乳化剂为op-10、吐温80、司盘80、磺酸、np-10 中的一种或几种,乳化剂的加入量占柴油的0.5%~6%;
19.所述助乳剂为乙醇、正丙醇、正丁醇、正戊醇、正己醇中的一种或几种,助乳剂的加入量占柴油的0.2%~5%。
20.上述的分离回收方法,优选的,乳化过程的水油比为1:1~1:6。
21.上述的分离回收方法,优选的,步骤(4)中,所述起泡剂为桉树油、樟脑油、mibc、 2#油中的一种或几种,起泡剂的加入量为10~100g/t;浮选过程中浮选机转速为1500~2500 r/min,充气量为0.2~0.8m3/min。
22.上述的分离回收方法,优选的,步骤(5)中,焙烧温度为200~1000℃,焙烧时间为1~ 10h。
23.与现有技术相比,本发明的优点在于:
24.(1)本发明对废旧磷酸铁锂正负极材料进行浮选分离,浮选过程中引入乳化柴油作为捕收剂,乳化柴油具有非常强的捕收能力和选择性,可以使废旧磷酸铁锂正负极材料分离充分、彻底。
25.(2)本发明在对废旧磷酸铁锂正负极物料充分分离的基础上,对浮选得到的正极物料进行焙烧处理,可以将正极物料中含有的少许石墨去除,相比于磁选可更高纯度的电极材料。
26.(3)本发明的废旧磷酸铁锂正负极材料的分离回收方法工艺简单、操作方便、清洁高效、生产成本低、便于工业化生产。
附图说明
27.图1是本发明废旧磷酸铁锂正负极材料的分离回收流程图。
具体实施方式
28.为了便于理解本发明,下文将结合说明书附图和较佳的实施例对本文发明做更全面、细致地描述,但本发明的保护范围并不限于以下具体实施例。
29.除非另有定义,下文中所使用的所有专业术语与本领域技术人员通常理解含义相同。本文中所使用的专业术语只是为了描述具体实施例的目的,并不是旨在限制本发明的保护范围。
30.除非另有特别说明,本发明中用到的各种原材料、试剂、仪器和设备等均可通过市场购买得到或者可通过现有方法制备得到。
31.实施例1:
32.一种本发明的废旧磷酸铁锂正负极材料的分离回收方法,其工艺流程图如图1所示,包括以下步骤:
33.(1)将500g废旧磷酸铁锂正负极混合物料置于浮选槽中,加入水至1.5l,然后加入氢氧化钠调节浆料的ph至10,并在搅拌速率为2000r/min的转速下调浆3min;
34.(2)向步骤(1)后的浮选槽中按照100g/t的用量添加抑制剂淀粉,在搅拌速率为2000 r/min的转速下调浆3min;
35.(3)将柴油按照水油比1:2(水和柴油)进行配比,并加入占柴油质量2%的乳化剂op-10、占柴油质量0.5%的助乳剂正丙醇进行乳化,其中乳化强度为2000r/min,乳化10min,获得乳化柴油;
36.(4)将乳化柴油作为捕收剂,按照100g/t用量添加至步骤(2)后的浮选槽中,在搅拌速率为2000r/min的转速下调浆3min,并按照20g/t的用量加入起泡剂桉树油进行浮选,浮选过程中浮选机转速为2000r/min,充气量为0.5m3/min,得到的精矿为石墨负极材料,石墨负极材料的品位和回收率分别为96.38%和97.16%,尾矿为磷酸铁锂正极材料;
37.(5)将浮选得到的尾矿磷酸铁锂正极材料进一步转移至马弗炉中,在700℃下焙烧5h,得到高纯度的磷酸铁锂正极材料,磷酸铁锂正极材料的品位和回收率分别为99.92%和 97.38%。
38.实施例2:
39.一种本发明的废旧磷酸铁锂正负极材料的分离回收方法,其工艺流程图如图1所示,包括以下步骤:
40.(1)将500g废旧磷酸铁锂正负极混合物料置于浮选槽中,加入水至1.5l,然后加入氢氧化钠调节浆料的ph至9.5,在搅拌速率为2000r/min的转速下调浆3min;
41.(2)向步骤(1)后的浮选槽中按照150g/t用量添加抑制剂柠檬酸,在搅拌速率为2000 r/min的转速下调浆3min;
42.(3)将柴油按照水油比1:3(水和柴油)进行配比,并添加占柴油质量2%的乳化剂吐温 80、占柴油质量0.5%的助乳剂正丁醇进行乳化,其中乳化强度为2500r/min,乳化8min,获得乳化柴油;
43.(4)将乳化柴油作为捕收剂,按照90g/t用量添加至步骤(2)后的浮选槽中,在搅拌速率为2000r/min的转速下调浆3min,并按照30g/t的用量加入起泡剂2#油进行浮选,浮选过程中浮选机转速为2000r/min,充气量为0.5m3/min,得到的精矿为石墨负极材料,石墨负极材料的品位和回收率分别为96.29%和97.49%,尾矿为磷酸铁锂正极材料;
44.(5)将浮选得到的磷酸铁锂正极材料转移至马弗炉中,在800℃下焙烧4h,得到高纯度的磷酸铁锂正极材料,磷酸铁锂正极材料的品位和回收率分别为99.93%和97.45%。
45.实施例3:
46.一种本发明的废旧磷酸铁锂正负极材料的分离回收方法,其工艺流程图如图1所示,包括以下步骤:
47.(1)将500g废旧磷酸铁锂正负极混合物料置于浮选槽中,加入水至1.5l,然后加入氢氧化钠调节浆料的ph至9,在搅拌速率为2000r/min的转速下调浆3min;
48.(2)向步骤(1)后的浮选槽中按照140g/t用量添加单宁酸,在搅拌速率为2000r/min 的转速下调浆3min;
49.(3)将柴油按照水油比1:1(水和柴油)进行配比,并添加占柴油质量3%的乳化剂司盘 80、占柴油质量00.4%的助乳剂正戊醇进行乳化,其中乳化强度为2500r/min,乳化10min,获得乳化柴油;
50.(4)将乳化柴油作为捕收剂,按照120g/t用量添加至步骤(2)后的浮选槽中,在搅拌速率为2000r/min的转速下调浆3min,并按照50g/t的用量加入起泡剂2#油进行浮选,浮选过程中浮选机转速为2000r/min,充气量为0.5m3/min,得到的精矿为石墨负极材料,石墨负极材料的品位和回收率分别为96.56%和97.18%,尾矿为磷酸铁锂正极材料;
51.(5)将浮选得到的尾矿磷酸铁锂正极材料转移至马弗炉中,在850℃下焙烧4.5h,得到高纯度的磷酸铁锂正极材料,磷酸铁锂正极材料的品位和回收率分别为99.95%和97.29%。