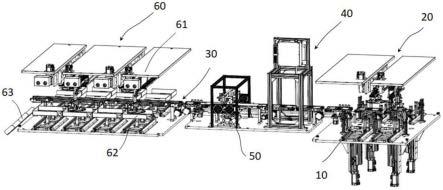
1.本实用新型涉及电池生产领域,尤其涉及一种电池片检测装置。
背景技术:2.电池片在经过栅线丝印、烧结、检测及分选后,实施打包、出货。为了保证电池片的合格率经分选准确度。打包之前,需要对电池片实施再次检测及分选。目前,一般采取人工抽检的方式实施对电池片的复检及分选,人工抽检方式效率低下,且搬运时易损坏电池片。
技术实现要素:3.为了解决传统的人工抽检存在的技术问题,本实用新型提供了一种电池片检测装置,其具体技术方案如下:
4.一种电池片检测装置,包括输送机构、缺陷检测机构、厚度检测机构及分选机构,其中:
5.输送机构被配置为将丝印有栅线的电池片输送至缺陷检测机构和厚度检测机构内,其中,缺陷检测机构用于实施对电池片的缺陷检测,厚度检测机构用于实施对电池片的厚度检测;
6.输送机构还被配置为将完成缺陷检测和厚度检测的电池片输送至分选机构,分选机构被配置与基于缺陷检测和厚度检测结果实施对电池片的分选。
7.通过输送机构、厚度检测机构、缺陷检测机构及分选机构的配合,本实用新型能够根据客户需求选择检测项目及具体标准,对检测数据进行储存、汇总、判断,实现了对电池片的自动检测及自动分选,其可大幅度提升对电池片的复检、分选效率,并提升了检测、分选的准确度。并且,本实用新型可作为划片机的前道工位,使划片机针对不同厚度来调节激光划片的功率及次数,大幅降低因电池片厚度不均匀导致的碎片概率。
8.在一些实施例中,厚度检测机构包括安装支架、第一厚度检测机构、第二厚度检测机构及第三厚度检测机构,其中:安装支架上设有供电池片通过的输送通道;第一厚度检测机构连接在安装支架上并位于安装支架的第一侧,第二厚度检测机构和第三厚度检测机构连接在安装支架上并位于安装支架的与第一侧相对的第二侧;电池片通过输送通道时,第一厚度检测机构检测电池片的中间部的厚度,第二厚度检测机构和第三厚度检测机构分别检测电池片的第一边侧部和第二边侧部的厚度。
9.通过第一厚度检测机构、第二厚度检测机构及第三厚度检测机构的配合,厚度检测机构实现了对电池片的中间位置及两侧位置处的厚度检测。
10.在一些实施例中,第一厚度检测机构、第二厚度检测机构及第三厚度检测机构均包括设置在输送通道两侧的第一激光传感器和第二激光传感器;电池片通过所述输送通道时,第一激光传感器和第二激光传感器同步扫描电池片以实施对电池片的相应部位的厚度检测。
11.将第一厚度检测机构、第二厚度检测机构及第三厚度检测机构设置成包括两个成
对设置的激光器,通过两个激光器同步测量与电池片的两个相对表面的距离并进行计算,即能快速得出电池片的相应部位的厚度数据。
12.在一些实施例中,完成检测的电池片包括合格电池片和不合格电池片,其中,合格电池片按预定规则被区分为若干个类别;分选机构包括:设置在输送机构的上方的搬运机构;若干设置在输送机构的边侧的合格片收料盒,每个合格片收料盒均对应收取一个类别的合格电池片;搬运机构被配置为从输送机构上拾取合格电池片,并将拾取的合格电池片存放至对应的合格片收料盒内。
13.通过设置搬运机构及若干合格片收料盒,实现了对合格电池片的分类收取。
14.在一些实施例中,分选机构还包括设置在输送机构的出料端的不合格片收料盒,不合格电池片经输送机构的出料端落入至不合格片收料盒内。
15.通过在在输送机构的出料端设置不合格片收料盒,实现了对不合格电池片的自动收取。
16.在一些实施例中,搬运机构包括第一安装板、第一平移机构、第一升降机构及第一吸取组件,其中:第一平移机构设置在第一安装板上,第一升降机构连接在第一平移机构的活动部件上,第一吸取组件连接在升降机构的活动部件上;第一吸取组件用于吸取电池片,第一升降机构用于驱动第一吸取组件升降,第一平移机构用于驱动第一吸取组件在输送机构和合格片料盒之间平移。
17.提供了一种结构简单的搬运机构,其通过第一平移机构、第一升降机构的配合驱动,实现第一吸取组件在输送机构和合格片料盒之间移动,从而将合格电池片收取至对应的合格片料盒内。
18.在一些实施例中,电池片检测装置还包括电池片供料机构和电池片上料机构,其中:电池片供料机构被配置为供应待检测的丝印有栅线的电池片;电池片上料机构被配置为从电池片供料机构上拾取电池片,并将拾取的电池片上料至输送机构上。
19.通过设置电池片供料机构,实现了对电池片的供料。而通过设置电池片上料机构,则实现了对电池片的自动上料。
20.在一些实施例中,电池片供料机构包括机台、储料部及顶升部,其中:储料部设置在机台上,储料部用于叠放电池片;顶升部设置在机台的下方,顶升部用于向上顶升叠放在储料部内的电池片。
21.提供了一种电池片供料机构的实现方式,其能够实现对电池片的叠放,并能够将电池片顶升出来,方便了电池片上料机构的取料。
22.在一些实施例中,储料部包括导轨、滑动连接板、承载底板及若干档杆,其中:导轨设置在机台上;滑动连接板滑动连接在导轨上;承载底板固定连接在滑动连接板上,滑动连接板沿导轨滑动时,带动承载底板同步滑动,以实现承载底板在一远离输送机构的补料工位和一靠近输送机构的上料工位之间的位置切换;若干档杆设置在承载底板的周侧,承载底板和若干档杆限定出用于叠放电池片的储料腔,档杆上设置有沿竖直方向延伸的导向皮带;机台对应于上料工位的位置处设置有顶升通道;顶升部设置在顶升通道的下方,承载底板滑动至上料工位处时,顶升部经顶升通道向上穿入至储料腔内以顶升叠放在储料腔内的电池片。
23.通过对储料部进行设置,使得承载底板和档杆限定出的储料腔能够实现在补料工
位和上料工位之间的位置切换,当储料部内的电池片被搬空后,方便了对储料部的补料。而在档杆上设置导向皮带,则实现了对电池片的顶升导向。
24.在一些实施例中,承载底板的底部设置有定位部件,承载底板滑动至上料工位时,定位部件将承载底板定位在上料工位处。
25.通过在承载底板的底部设置定位部件,实现了对承载底板的定位。防止电池片上料机构在取片过程中,承载底板发生意外滑动。
26.在一些实施例中,电池片上料机构包括第二安装板、第二平移机构及第二吸取组件,其中:第二安装板设置在电池片供料机构和输送机构的上方;第二平移机构设置在第二安装板上,第二吸取组件连接在第二平移机构的活动部件上;第二吸取组件用于吸取电池片,第二平移机构用于驱动第二吸取组件在电池片供料机构和输送机构之间平移。
27.提供了一种结构简单的电池片上料机构,其通过第二平移机构驱动第二吸取组件在电池片供料机构和输送机构之间移动,从而将电池片供料机构中的电池片自动上料至输送机构内。
附图说明
28.图1为本实用新型实施例提供的电池片检测装置的结构示意图;
29.图2为本实用新型实施例中的输送机构、缺陷检测机构及厚度检测机构的结构示意图;
30.图3为本实用新型实施例中的厚度检测机构在一个视角下的结构示意图;
31.图4为本实用新型实施例中的厚度检测机构在另一个视角下的结构示意图;
32.图5为本实用新型实施例中的电池片供料机构和电池片上料机构的结构示意图;
33.图6为本发明实施例中的储料部结构示意图;
34.图1至图6中包括:
35.电池片供料机构10:机台11、储料部12、顶升部13、导轨121、滑动连接板122、承载底板123、档杆124、垫板125、导向皮带126;
36.电池片上料机构20:第二安装板21、第二平移机构22、第二吸取组件23;
37.输送机构30;
38.缺陷检测机构40;
39.厚度检测机构50:安装支架51、第一厚度检测机构52、第二厚度检测机构53、第三厚度检测机构54、第一激光传感器521、第二激光传感器522;
40.分选机构60:搬运机构61、合格片收料盒62、不合格电池片收料盒63。
具体实施方式
41.为使本实用新型的上述目的、特征和优点能够更加明显易懂,下面结合附图和具体实施方式对本实用新型作进一步详细的说明。
42.目前,一般采取人工抽检的方式实施对电池片的复检及分选,人工抽检方式不仅效率低下。
43.鉴于此,本实用新型提供了一种电池片检测装置,其实现了对电池片的自动检测及自动分选,其可大幅度提升对电池片的复检、分选效率。
44.如图1和图2所示,本实用新型实施例提供的电池片检测装置包括输送机构30、缺陷检测机构40、厚度检测机构50及分选机构60,其中:
45.输送机构30被配置为将丝印有栅线的电池片输送至缺陷检测机构40和厚度检测机构内50,其中,缺陷检测机构40用于实施对电池片的缺陷检测,厚度检测机构50用于实施对电池片的厚度检测。
46.输送机构30还被配置为将完成缺陷检测和厚度检测的电池片输送至分选机构60,分选机构60基于缺陷检测和厚度检测结果实施对电池片的分选。
47.可见,通过输送机构30、缺陷检测机构40、厚度检测机构50及分选机构60的配合,本实用新型的电池片检测装置实现了对电池片的缺陷检测及厚度检测,并基于检测结果完成对电池片的分选,从而提升复检、分选效率。
48.缺陷检测机构40可采用已知的各种电池片缺陷检测装置,其可实施对电池片的脏污、隐裂、孔洞等缺陷中的一种或多种的检测。可选地,缺陷检测机构采用pl检测装置,能够检出电池片是否具有脏污、划痕、隐裂等问题。
49.可选的,如图3和图4所示,厚度检测机构50包括安装支架51、第一厚度检测机构52、第二厚度检测机构53及第三厚度检测机构54,其中:安装支架51上设有供电池片通过的输送通道。第一厚度检测机构52连接在安装支架51上并位于安装支架51的第一侧,第二厚度检测机构53和第三厚度检测机构54连接在安装支架51上并位于安装支架的与第一侧相对的第二侧。
50.电池片在输送机构30的带动下通过输送通道时,第一厚度检测机构52检测电池片的中间部的厚度,第二厚度检测机构53和第三厚度检测机构54分别检测电池片的第一边侧部和第二边侧部的厚度。
51.可见,通过设置第一厚度检测机构52、第二厚度检测机构53及第三厚度检测机构54的配合,厚度检测机构50实现了对电池片的中间位置及两侧位置处的厚度检测,从而能够实施对电池片的实际厚度及均匀度的准确评估。
52.如本领域一般技术人员所知晓的,非接触式激光侧厚组件包括两个激光传感器,待检测电池片自两个激光传感器之间通过。随着待检测电池片的移动,两个激光传感器通过激光分别测出其与待检测电池片的两个相对表面的距离,以间接实现对待检测电池片的对应位置处的厚度测量。具体到本实用新型中:
53.第一厚度检测机构52、第二厚度检测机构53及第三厚度检测机构54均包括设置在输送通道两侧的第一激光传感器521和第二激光传感器522。
54.电池片在电池片在输送机构30的带动下通过输送通道时,各厚度检测机构的第一激光传感器521和第二激光传感器522同步扫描电池片的相应部位,从而实施对电池片的相应部位的厚度检测。
55.在一些应用例中,根据厚度、缺陷的检测结果,完成检测的电池片按预定标准被认定为合格电池片或不合格电池片,合格电池片又进一步细分为若干个类别。
56.为了实现对不同类别的合格电池片的分类收取,可选的,分选机构60包括:设置在输送机构30的上方的搬运机构61,及若干设置在输送机构30的边侧的合格片收料盒62,每个合格片收料盒62均对应收取一个类别的合格电池片。
57.搬运机构61从输送机构30上拾取合格电池片,并将拾取的合格电池片存放至对应
的合格片收料盒内,从而实现了对合格电池片的分类收取。
58.可选的,搬运机构61包括第一安装板、第一平移机构、第一升降机构及第一吸取组件,其中:第一平移机构设置在第一安装板上,第一升降机构连接在第一平移机构的活动部件上,第一吸取组件连接在升降机构的活动部件上。其中,第一吸取组件用于吸取电池片,第一升降机构用于驱动第一吸取组件升降,第一平移机构用于驱动第一吸取组件在输送机构和合格片料盒之间平移。
59.通过第一平移机构、第一升降机构的配合驱动,第一吸取组件可实现在输送机构30和合格片料盒62之间的自由移动,从而使得第一吸取组件能够从输送机构30上吸取合格电池片,并将吸取的合格电池片放置至对应的合格片料盒62内。
60.此外,为了实施对不合格电池片的自动收取,分选机构60还包括设置在输送机构30的出料端的不合格片收料盒63。由于搬运机构61不会拾取输送机构30上的不合格电池片,因此,不合格电池片最终经输送机构30的出料端落入至不合格片收料盒63内。
61.继续参考图1所示,可选的,本实用新型实施例中的电池片检测装置还包括电池片供料机构10和电池片上料机构20,其中:
62.电池片供料机构10被配置为供应待检测的丝印有栅线的电池片。
63.电池片上料机构20被配置为从电池片供料机构10上拾取电池片,并将拾取的电池片上料至输送机构30上。
64.可选的,如图5所示,电池片供料机构10包括机台11、储料部12及顶升部13,其中:储料部12设置在机台11上,储料部12用于叠放电池片。顶升部13设置在机台11的下方,顶升部13用于向上顶升叠放在储料部12内的电池片。
65.通过顶升部13向上顶升叠放在储料部12内的电池片,可将叠放在最顶部的电池片向上顶升出储料部12,并使得最顶部的电池片靠近电池片上料机构20,从而方便了电池片上料机构20的取片。
66.可选的,如图6所示,储料部12包括导轨121、滑动连接板122、承载底板123及若干档杆124,其中:导轨121设置在机台11上,滑动连接板122滑动连接在导轨121上,承载底板123固定连接在滑动连接板122上,滑动连接板122沿导轨121滑动时,带动承载底板123同步滑动,以实现承载底板123在一远离输送机构30的补料工位和一靠近输送机构30的上料工位之间的位置切换。若干档杆124设置在承载底板123的周侧,承载底板123和若干档杆124限定出用于叠放电池片的储料腔。机台11对应于上料工位的位置处设置有顶升通道,顶升部13设置在顶升通道的下方,承载底板123滑动至上料工位处时,顶升部13经顶升通道向上穿入至储料腔内以顶升叠放在储料腔内的电池片。
67.储料部12配合电池片上料机构20实施电池片上料的具体过程如下:
68.首先,控制承载底板123滑动至补料工位处,将电池片叠放至储料腔内。
69.接着,控制承载底板123滑动至上料工位处,顶升部13经顶升通道向上顶升储料腔内的电池片,位于最顶层的电池片被顶升出储料腔。电池片上料机构20拾取位于最顶层的电池片,并将拾取的电池片上料至输送机构30上。
70.可选的,顶升部13以步进的方式向上顶升电池片,每次步进的距离与一片电池片的厚度相当。
71.待储料腔中的电池片被取空后,控制承载底板123滑动至补料工位处,实施补料。
72.可选的,承载底板123的端部设置有把手,可通过把手人工推拉承载底板123在补料工位和上料工位之间滑动。当然,也可以通过直线驱动模组自动控制承载底板123在补料工位和上料工位之间滑动。
73.可选的,各档杆124上均设置有沿竖直方向延伸的导向皮带126,用于防止电池片边缘和内侧壁发生碰撞导致出现崩边、隐裂、脏污等问题。当电池片边缘接触到某一条或几条导向皮带126时,顶升部13向上顶升电池片,与电池片边缘接触的导向皮带126同步向上传送,从而防止电池片边缘出现问题。
74.可选的,承载底板123的底部设置有定位部件。当承载底板123滑动至上料工位时,定位部件将承载底板123定位在上料工位处,防止电池片上料机构20在取片过程中,承载底板123发生意外滑动。机台11为不锈钢材质,可采用磁铁作为定位部件。
75.为了防止顶升部13直接顶升电池片,造成电池片损坏,可选的,承载底板123上还铺设有垫板125,电池片叠放在垫板125上。顶升部13向上顶升垫板125,从而带动电池片同步上升。
76.可选的,如图5所示。电池片上料机构20包括第二安装板21、第二平移机构22及第二吸取组件23,其中:第二安装板21设置在电池片供料机构10和输送机构30的上方,第二平移机构22设置在第二安装板21上,第二吸取组件23连接在第二平移机构22的活动部件上。
77.第二吸取组件23用于吸取电池片,第二平移机构22用于驱动第二吸取组件23在电池片供料机构10和输送机构30之间平移。
78.通过第二平移机构22的平移驱动,第二吸取组件23能够从电池片供料机构10内吸取电池片,并将吸取的电池片上料至输送机构30上。
79.可选的,第二吸取组件23采用伯努利吸盘,伯努利吸盘取片时无需接触,不会对电池片造成损害。
80.上文对本实用新型进行了足够详细的具有一定特殊性的描述。所属领域内的普通技术人员应该理解,实施例中的描述仅仅是示例性的,在不偏离本实用新型的真实精神和范围的前提下做出所有改变都应该属于本实用新型的保护范围。本实用新型所要求保护的范围是由所述的权利要求书进行限定的,而不是由实施例中的上述描述来限定的。