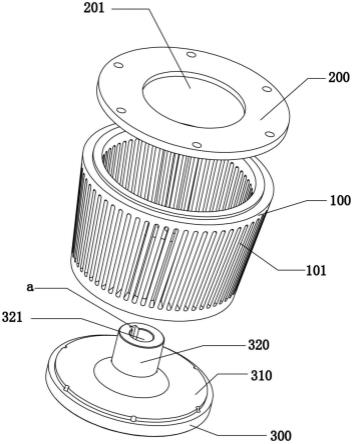
1.本实用新型涉及气流磨分选轮技术领域,具体为一种用于高一致性钕铁硼粉体的分选轮结构。
背景技术:2.由稀土元素r与铁、硼组成的金属间化合物。r主要是钕或钕与其他稀土元素的组合,有时也用钴、铝、钒等元素取代部分铁。钕铁硼磁体有很强的磁晶各向异性和很高的饱和磁化强度。在永磁材料中,烧结nd-fe-b磁体性能最高,但该磁体的居里温度较低,温度稳定性和耐蚀性较差,限制了在较高温度下使用,而且在多数情况下需采用保护涂层。钕铁硼磁体的制造工艺有粉末冶金法和熔体快淬法。因磁性能优异,nd-fe-b型磁体获得了广泛的应用,主要用于电动机、发电机、声波换能器、各种传感器、医疗器械和磁力机械等。
3.当前烧结钕铁硼的粉体制备大多采用流化床型式,即用超音速气流对粉体进行加速对撞,从而实现粉体颗粒的细化,再通过高速旋转的分级轮将磨至一定尺寸的粉体筛选出研磨室进入下道工序。
4.经过长期的调查研究分析发现气流在整个分选轮轴向上的分布并不一致,而当前分级轮型式无论国内外均采用标准圆筒形,这就导致了粉体在接近分级轮叶片时入射速度并不相同,即便是相同大小颗粒,也会出现因入射速度不同,而使远离出料口部位的粉体被弹回进行反复研磨,形成超细粉,既降低了研磨效率,降低了粉料收得率,也恶化了粉体的粒度分布一致性,进而恶化最终磁体的综合磁性能。
技术实现要素:5.为了解决现有技术中存在的上述问题,本实用新型提供了一种高一致性钕铁硼粉体的分选轮结构。
6.一种用于高一致性钕铁硼粉体的分选轮结构,包括叶轮本体,所述叶轮本体的两端分别连接有前挡板和驱动挡板,所述驱动挡板上设有连接孔,用于和驱动部件连接,驱使叶轮本体转动;所述叶轮本体为两端开口的圆台型壳体,所述叶轮本体的周面上排布设置有若干轮槽。
7.上述技术方案的进一步设置为:所述轮槽为沿着圆台的母线方向设置的直槽,并且相对母线倾斜。
8.上述技术方案的进一步设置为:所述轮槽和所述叶轮本体的母线之间呈3
°
的夹角。
9.上述技术方案的进一步设置为:所述轮槽下端的倾斜方向和所述叶轮本体的旋转方向一致。
10.上述技术方案的进一步设置为:所述叶轮本体的上下两个开口分别为驱动口和挡板口,所述驱动挡板连接在所述驱动口处,前挡板连接在所述挡板口处;所述前挡板的中心设有开口,使叶轮本体的内腔能够与装粉体的罐筒连通。
11.上述技术方案的进一步设置为:所述叶轮本体的挡板口端面上设有凸起的内连接环,所述前挡板的下端面上设有与所述连接环配合的连接槽。
12.上述技术方案的进一步设置为:所述叶轮本体的驱动口端面上从外缘延伸设有凸起的外连接环,所述驱动板的连接端面上设有与所述外连接环的内径一致的连接台。
13.上述技术方案的进一步设置为:所述驱动板的连接台上朝向所述叶轮本体的内腔延伸设置有连接套,所述连接孔贯穿所述驱动板和连接套;所述连接孔的侧部设有定位槽。
14.上述技术方案的进一步设置为:所述前挡板的直径大于所述驱动挡板的直径。
15.本实用新型的有益效果在于:与现有技术相比,本实用新型采用新的叶轮结构,使叶轮本体的外径和齿长连续变化,从而使叶轮本体在轴向各位置的分选能力相同,减少粉体的反复研磨,使力度分布峰宽指数得到极大的改善,加工成型的磁体内禀矫顽力亦得到很大的提升。
附图说明
16.图1为本实用新型的分解结构示意图。
17.图2为本实用新型的侧视图。
18.图3为本实用新型的半剖视图。
19.附图上标注:100、叶轮本体;200、前挡板;300、驱动挡板;101、轮槽;201、开口;110、内连接环;120、外连接环;310、连接台;320、连接套;321、连接孔;a、定位槽。
具体实施方式
20.为更进一步阐述本实用新型为实现预定实用新型目的所采取的技术手段及功效,以下结合附图及较佳实施例,对依据本实用新型的具体实施方式、结构、特征及其功效,详细说明如后。
21.参照图1所示,本实施例公开了一种用于高一致性钕铁硼粉体的分选轮结构,包括叶轮本体100,所述叶轮本体100的两端分别连接有前挡板200和驱动挡板300,所述驱动挡板300上设有连接孔321,用于和驱动部件连接,驱使叶轮本体100转动;为了实现叶轮本体100外径的连续变化,所述叶轮本体100为两端开口201的圆台型壳体,所述叶轮本体100的周面上排布设置有若干轮槽101。
22.将叶轮本体100设置成圆台型的壳体,使叶轮本体100的外径连续变化,配合了不同入射速度的粉体在不同的位置被筛选,保证了粉料的收得率和粉体的粒度分布一致性。
23.具体的,所述叶轮本体100的上下两个开口201分别为驱动口和挡板口,所述驱动挡板300连接在所述驱动口处,前挡板200连接在所述挡板口处;所述前挡板200的中心设有开口201,使叶轮本体100的内腔能够与装粉体的罐筒连通。
24.驱动部件连接到驱动挡板300上,通过驱动挡板300带动叶轮本体100转动;同时,装有粉体的罐筒和前挡板200连接,将粉体送入到叶轮本体100内,叶轮本体100在转动时对射入的粉体进行筛选,筛选出的粉体从轮槽101射出送入到下一道工序。
25.优选的,为了配合叶轮本体100的圆台形状,所述前挡板200的直径大于所述驱动挡板300的直径。
26.优选的,本实施例中的前挡板200和驱动挡板300和叶轮本体100之间螺钉固定。
27.参照图2所示,为了保证粉体能够顺利被筛选,所述轮槽101为沿着圆台的母线方向设置的直槽,并且相对母线倾斜。
28.优选的,所述轮槽101和所述叶轮本体100的母线之间呈3
°
的夹角。
29.优选的,所述轮槽101下端的倾斜方向和所述叶轮本体100的旋转方向一致。
30.粉体在射入到叶轮本体100内部后,在叶轮本体100的作用下,沿着叶轮本体100在转动方向具有一定的旋转速度,在筛选过程中从轮槽101射出时,由于这个旋转速度,会打到叶轮本体100上而无法顺利筛选,将轮槽101设置成倾斜方向并且和叶轮本体100的旋转方向一致,使粉体能够顺利射出,避免了粉体在叶轮本体100内进行再次研磨的问题。
31.参照图3所示,为了使前挡板200能够稳定安装到叶轮本体100上,所述叶轮本体100的挡板口端面上设有凸起的内连接环110,所述前挡板200的下端面上设有与所述连接环配合的连接槽。
32.将前挡板200的连接槽套设到内连接环110的外部进行定位,并且通过螺钉将内连接环110和前挡板200固定,保证了叶轮本体100和前挡板200之间连接稳定,不会在使用中产生偏移。
33.为了将叶轮本体100连接到驱动部件,使其能够在驱动部件的带动下转动,所述叶轮本体100的驱动口端面上从外缘延伸设有凸起的外连接环120,所述驱动板的连接端面上设有与所述外连接环120的内径一致的连接台310。
34.外连接环120套设到连接台310上进行定位,并且通过螺钉将连接台310和驱动板进行固定,保证了叶轮本体100和前挡板200之间连接稳定。
35.为了保证驱动部件在驱动板上的连接稳定,所述驱动板的连接台310上朝向所述叶轮本体100的内腔延伸设置有连接套320,所述连接孔321贯穿所述驱动板和连接套320;所述连接孔321的侧部设有定位槽a。
36.在驱动板上设置连接套320,使驱动部件的输出轴大部分插入到连接套320内,减少输出轴在转动过程中的晃动。
37.优选的本实施例中所述的驱动部件为驱动电机。
38.本实施例的使用方式与现有技术中用于粉体筛选的分选轮一致,在此不做赘述。
39.以上所述,仅是本实用新型的较佳实施例而已,并非对本实用新型作任何形式上的限制,虽然本实用新型已以较佳实施例揭示如上,然而并非用以限定本实用新型,任何本领域技术人员,在不脱离本实用新型技术方案范围内,当可利用上述揭示的技术内容做出些许更动或修饰为等同变化的等效实施例,但凡是未脱离本实用新型技术方案内容,依据本实用新型的技术实质对以上实施例所作的任何简介修改、等同变化与修饰,均仍属于本实用新型技术方案的范围内。