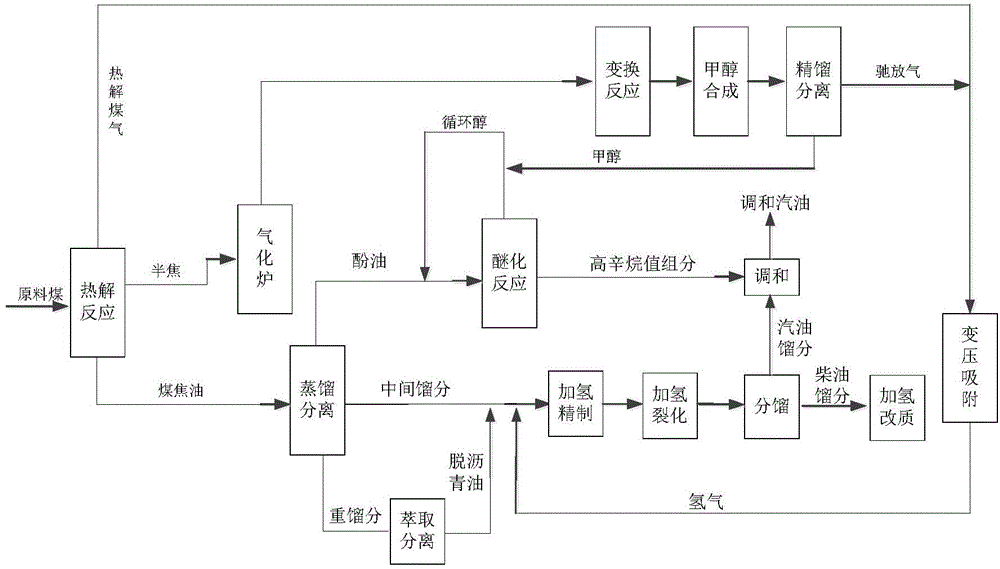
本发明涉及煤炭深加工领域,具体地,涉及一种煤焦油制清洁燃料的方法及一种煤制清洁燃料的方法,以及由所述两种方法制备得到的清洁燃料。
背景技术:
:我国是煤炭资源丰富而石油资源相对短缺的国家,随着国民经济的快速发展我国对油品的需求持续高速增长,因此,为了保障我国国民经济的可持续发展,优化能源结构,降低对石油进口的依赖,充分利用我国丰富的煤炭资源优势,大力发展煤化工高新技术产业,以煤化工产品替代部分石油化工产品,已经成为我国能源战略的必然选择。煤制油(Coal-to-liquids,CTL)是以煤炭为原料,通过化学加工过程生产油品和石油化工产品的一项技术,目前常用的煤制油技术主要有煤直接液化和煤间接液化以及煤焦油加氢处理等方法。煤的直接液化将煤在高温高压条件下,通过催化加氢直接液化合成液态烃类燃料,并脱除硫、氮、氧等原子。这种方法对煤的种类适应性差,反应及操作条件苛刻,产出燃油的芳烃、硫和氮等杂质含量高,十六烷值低的特点,在发动机上直接燃用较为困难,油品不符合国家标准(GB19147—2009);煤的间接液化,首先把煤气化,再通过费托合成转化为烃类燃料,但是煤的间接液化以生产化学品(直链烃)为主,燃料油品为副,燃料油产品选择性较差。煤焦油加氢处理生产附加值较高的燃料油,多采用加氢精制和/或加氢裂化工艺,但是得到的燃料油十六烷值低,油品仍不符合国家标准(GB19147—2009)。例如CN103160305A公开了一种采用煤直接制备燃料油的系统及工艺。首先,原料煤在热解炉中进行热解,生成煤气、煤焦油和半焦;半焦通过气化炉转化为气化粗煤气和煤焦油;粗煤气经分离和洗涤得到合成气,合成气进行费托合成柴油;利用变压吸附将热解煤气中氢气分离出来;气化煤焦油与热解煤焦油混合得到混合煤焦油,利用抽提的氢气对混合煤焦油进行加氢精制处理,得到煤焦油加氢柴油,随后,与费托合成柴油调配得到高品质柴油。CN101580728A公开了一种不粘结性煤或弱粘结性煤的加工工艺。首先,在中低温下将不粘结性煤或弱粘结性煤进行中低温干馏,生成半焦、煤气和煤焦油;然后分别对这三种干馏产物进行处理,第一,将半焦通过气化成合成气,然后将合成气进行费-托合成制备石蜡类烃类,第二,利用变压吸附技术将煤气中的氢气提出,第三,对煤焦油进行分馏,分馏得到含酚油、塔顶油和塔底油,对于含酚油又进行抽提,得到酚类和脱酚油,将塔底重油和脱酚油进行延迟焦化,得到焦化气、焦化石脑油、焦化柴油、焦化蜡油和焦炭;然后,利用抽提的氢气对石蜡烃类和焦化石脑油、焦化柴油、焦化蜡油进行加氢处理;最后,将分别得到的加氢产出进行混合。CN102634369A公开了一种高温煤焦油加氢、后延迟焦化与焦炉煤气制甲醇组合工艺。焦化厂生产焦炭时,副产焦炉煤气和高温煤焦油,焦炉煤气作为生产甲醇的原料,甲醇副产的驰放气经过变压吸附装置制取氢气作为高温煤焦油加氢的原料,高温煤焦油加氢副产的软沥青进入后延迟焦化装置,作为生产针状焦的原料。由于目前煤制油的制备工艺得到的油品无法达到国家标准,因此煤制油制得的油品需要与石化油品混配,才能够使最终油品的十六烷值等指标符合国家标准。因此,迫切需要开发一种能够将煤炭资源转化为符合国标甚至更高标准 要求的燃料的工艺方法。技术实现要素:为了克服上述缺陷,本发明提供一种能够将煤焦油资源和煤炭资源转化为符合国家标准甚至更高标准要求的燃料的工艺方法。本发明的第一方面,提供了一种煤焦油制备清洁燃料的方法,其中,该方法包括:(1)将煤焦油进行蒸馏分离,得到酚油馏分、中间馏分和重馏分,其中,所述酚油馏分为小于220℃馏分,所述中间馏分为220-350℃馏分,所述重馏分为大于350℃馏分;(2)将步骤(1)得到的酚油馏分与甲醇进行醚化反应,得到高辛烷值组分;(3)用萃取剂对步骤(1)得到的重馏分进行萃取分离,得到脱沥青油;(4)将步骤(1)得到的中间馏分与步骤(3)得到的脱沥青油进行加氢精制和加氢裂化后,裂化产物经分馏得到汽油馏分和柴油馏分;(5)将步骤(2)得到的高辛烷值组分加入到步骤(4)得到的汽油馏分中,制得高辛烷值的汽油;(6)将柴油馏分进行加氢改质处理,制得改质柴油。本发明的第二方面,提供了一种煤制备清洁燃料的方法,其中,该方法包括:该方法包括:(1)在450-800℃条件下,将原料煤进行热解,得到煤焦油、半焦和热解煤气;(2)将步骤(1)得到的半焦经气化得到气化粗煤气,经变换后进行甲醇合成反应,得到甲醇和甲醇驰放气;(3)将步骤(1)得到的热解煤气与步骤(2)得到的甲醇驰放气混合,并在提氢条件下,得到氢气;(4)将步骤(1)得到的煤焦油进行蒸馏分离,得到酚油馏分、中间馏分和重馏分,其中,所述酚油馏分为小于220℃馏分,所述中间馏分为220-350℃馏分,所述重馏分为大于350℃馏分;(5)将步骤(4)得到的酚油馏分与步骤(2)得到的甲醇进行醚化反应,得到高辛烷值组分;(6)用萃取剂对步骤(4)得到的重馏分进行萃取分离,得到脱沥青油;(7)将步骤(4)得到的中间馏分与步骤(6)得到的脱沥青油进行加氢精制和加氢裂化后,裂化产物经分馏得到汽油馏分和柴油馏分;(8)将步骤(5)得到的高辛烷值组分加入到步骤(7)得到的汽油馏分中,制得高辛烷值的汽油;(9)将柴油馏分进行加氢改质处理,制得改质柴油;(10)将步骤(3)得到的至少一部分氢气通入步骤(7)的加氢精制和/或加氢裂化反应中。本发明还提供了由上述两种方法制备得到的高辛烷值的汽油和改质柴油。通过上述技术方案,本发明提供的煤焦油制清洁燃料的方法以及煤制清洁燃料的方法实现了对煤焦油和煤碳资源的充分深加工,获得了高辛烷值组分,生产高品质的清洁燃料,同时实现了各个生产工艺之间的系统连通,提高了系统能效使能源的利用最大化,达到了煤炭资源的高效和清洁利用。本发明的其他特征和优点将在随后的具体实施方式部分予以详细说明。附图说明附图是用来提供对本发明的进一步理解,并且构成说明书的一部分,与下面的具体实施方式一起用于解释本发明,但并不构成对本发明的限制。在附图中:图1是本发明实施例1中工艺流程的示意图;图2是本发明实施例2中工艺流程的示意图;图3是本发明实施例4中工艺流程的示意图。具体实施方式以下结合附图对本发明的具体实施方式进行详细说明。应当理解的是,此处所描述的具体实施方式仅用于说明和解释本发明,并不用于限制本发明。本文所述的清洁燃料指高辛烷值的汽油和改质柴油。本发明第一方面,提供了一种煤焦油制备清洁燃料的方法,其中,该方法包括:(1)将煤焦油进行蒸馏分离,得到酚油馏分、中间馏分和重馏分,其中,所述酚油馏分为小于220℃馏分,所述中间馏分为220-350℃馏分,所述重馏分为大于350℃馏分;(2)将步骤(1)得到的酚油馏分与甲醇进行醚化反应,得到高辛烷值组分;(3)用萃取剂对步骤(1)得到的重馏分进行萃取分离,得到脱沥青油;(4)将步骤(1)得到的中间馏分与步骤(3)得到的脱沥青油进行加氢精制和加氢裂化后,裂化产物经分馏得到汽油馏分和柴油馏分;(5)将步骤(2)得到的高辛烷值组分加入到步骤(4)得到的汽油馏分中,制得高辛烷值的汽油;(6)将柴油馏分进行加氢改质处理,制得改质柴油。根据本发明,步骤(2)的醚化反应中,酚油馏分中的酚与醇的摩尔比为1:1-5;优选为1:3-5。所述醚化反应的条件可以在很大范围内改变,优选地,所述醚化反应的条件可以包括温度为350-450℃,酚与醇的摩尔比为1:1-5,平均液体空速为0.5h-1-2h-1。醚化反应的催化剂可以为Al2O3、SiO2、Al2O3-SiO2复合氧化物载体负载的酸催化剂和碱催化剂中的至少一种。更优 选地,醚化反应的催化剂为SiO2负载的Cs2O碱催化剂,并且以固体负载碱催化剂的总量为基准,Cs的含量为10-15重量%。所述醚化反应的条件包括温度为380-420℃,平均液体空速为0.5h-1-1.0h-1。同样优选地,本发明步骤(2)中进行醚化反应后剩余的醇,可以作为循环醇并入外加的甲醇,与步骤(1)得到的酚油馏分进行醚化反应。根据本发明,步骤(3)中,为了有效降低加氢处理原料中沥青质的含量,本发明对重馏分进行萃取分离,分离出沥青质和胶质,由此得到的脱沥青油可以直接进行加氢处理,减少了加氢处理过程中在加氢催化剂表面形成的结焦量,延长了加氢催化剂的使用寿命,使得加氢装置(特别是固定床加氢装置)能够长期稳定运行。优选地,所述萃取分离的条件使得所述脱沥青油中沥青质的含量不高于9重量%。更优选地,所述脱沥青油中沥青质的含量为不高于7重量%。进一步优选地,所述脱沥青油中沥青质的含量为不高于5重量%。所述沥青质的含量可以参照SY/T7550-2004中规定的方法测定。其中,本发明对于萃取分离的条件没有特别限定,可以在很大范围内改变,优选地,所述萃取分离的条件可以包括:温度为50-300℃,压力为0-10MPa(以表压计),在上述萃取分离的条件下,将重馏分与萃取剂混合并使混合物分成萃取相和萃余相,全部或部分沥青质位于萃余相中。萃余相中的沥青质可以用作制备沥青的原料,也可以用作炼焦或延迟焦化的原料。根据本发明的方法,所述萃取分离优选为超临界溶剂萃取分离(即,所述萃取分离在萃取剂超临界状态下进行),这样能够获得更高的萃取分离效率,得到具有更低沥青质和胶质含量的脱沥青油。所述超临界溶剂萃取分离的条件可以根据具体使用的萃取剂进行选择。一般地,所述超临界溶剂萃取分离的条件包括:压力为3-8MPa(以表压计),温度为120-220℃,优选地,所述超临界溶剂萃取分离的条件包括:温度为80-220℃,压力为3-8MPa。其中,萃取分离中使用的萃取剂可以为各种能够将煤焦油中的油分提取出来的液体物质,例如,所述萃取剂可以为选自C3-C5的直链或支链烷烃和各种来源的石脑油中的一种或两种以上的混合物。优选地,所述萃取剂为C3-C5的烷烃中的一种或多种,这样在同等条件下能够获得具有更低沥青质含量的脱沥青油,从而进一步降低加氢催化剂表面的结焦量,进一步延长加氢装置(特别是固定床加氢装置)的连续运转时间。所述C3-C5烷烃包括C3-C5的直链或支链烷烃,其具体实例可以包括但不限于丙烷、丁烷(如正丁烷和异丁烷)和戊烷(如正戊烷、异戊烷和新戊烷)。所述萃取分离的次数以及每次萃取分离使用的萃取剂的量,可以根据煤焦油的种类以及预期的脱沥青油中沥青质和胶质总量进行适当的选择。一般地,相对于100重量份重馏分,每次萃取分离使用的萃取剂的量可以为100-1000重量份,优选为300-800重量份。萃取分离的次数可以为1-3次。根据本发明的方法,步骤(4)中加氢处理中的有效成分来自于步骤(3)萃取分离得到的脱沥青油和步骤(1)分馏切割得到的中间馏分。步骤(3)的萃取分离得到萃取相可以直接作为脱沥青油和中间馏分一起与加氢催化剂接触,也可以将萃取相进行分离,得到萃取物,将萃取物作为脱沥青油和中间馏分一起与加氢催化剂接触。优选从萃取相中分离出至少部分萃取剂,将剩余的富含萃取物的液相作为脱沥青油和中间馏分一起与加氢催化剂接触,这样分离出的萃取剂可以循环使用,同时也能够提高加氢处理的有效加氢原料量。可以采用常用的各种方法从萃取相中分离出至少部分萃取剂,例如蒸馏或者闪蒸。所述蒸馏和闪蒸的条件可以根据萃取剂的种类进行适当的选择,没有特别限定。根据本发明,步骤(4)的分馏过程中,汽油馏分的馏程温度为65-195℃,柴油馏分的馏程温度为220-365℃。本发明提供的煤焦油制清洁燃料的方法获得了高辛烷值组分,通过将这 种高辛烷值组分加入到汽油馏分中,从而实现了以煤焦油为原料来获得符合国家标准的汽油,优选地,本发明步骤(2)得到的高辛烷值组分与步骤(4)中分馏得到的汽油馏分的调合重量比可以为1:0.3-7。根据本发明,步骤(4)中,所述加氢精制的条件包括:反应温度可以为350-400℃,压力可以为8-20MPa,氢油体积比可以为800-2000:1,平均液体空速可以为0.5h-1-3h-1,更优选地,所述加氢精制反应的条件包括:反应温度为360-400℃,压力为8-15MPa,氢油体积比为800-2000:1,平均液体空速为0.2h-1-2h-1。根据本发明,所述加氢精制反应优选在催化剂存在下进行,所述催化剂没有具体限定,可以为本领域的常规选择,所述催化剂为常规的加氢精制催化剂,主要以第VIB族和第VIII族金属为活性组分,第VIB族金属一般为Mo和/或W,第VIII族金属Co和/或Ni,以含硅氧化铝或氧化铝为载体,根据本发明,步骤(4)中,所述加氢裂化的条件包括:裂化温度可以为360-400℃,压力可以为8-15MPa,氢油体积比可以为800-2000:1,平均液体空速可以为0.2h-1-2h-1。根据本发明,所述加氢裂化反应优选在催化剂存在下进行,所述催化剂没有具体限定,可以为本领域的常规选择,加氢裂化过程所用催化剂为常规的加氢裂化催化剂,主要以第VIB族和第VIII族金属为活性组分,以无定型硅铝和分子筛为载体,第VIB族金属一般为Mo和/或W,第VIII族金属Co和/或Ni。本发明中,为了更进一步提高得到的柴油馏分的品质,本发明将步骤(4)得到的柴油馏分进行加氢改质,所述加氢改质的条件可以在很大范围内改变,优选情况下,所述加氢改质的条件包括:反应温度为360-400℃、压力为8-15MPa,氢油体积比为800-2000:1,平均液体空速为0.2h-1-2h-1。更优选地,所述加氢改质的条件包括:反应温度为360-380℃,压力为10-14MPa, 氢油体积比为1000-2000:1,平均液体空速为0.2h-1-1.0h-1。根据本发明,所述加氢改质反应优选在催化剂存在下进行,所述催化剂没有具体限定,可以为本领域的常规选择,所述催化剂为具有较高开环选择性和良好芳烃饱和的催化剂,主要以第VIB族和第VIII族金属为活性组分,第VIB族金属一般为Mo和/或W,第VIII族金属Co和/或Ni,以含氧化铝、含硅氧化铝和分子筛为载体。本发明第二方面提供了一种煤制清洁燃料的方法,其中,该方法包括:(1)在450-800℃条件下,将原料煤进行热解,得到煤焦油、半焦和热解煤气;(2)将步骤(1)得到的半焦经气化得到气化粗煤气,经变换后进行甲醇合成反应,得到甲醇和甲醇驰放气;(3)将步骤(1)得到的热解煤气与步骤(2)得到的甲醇驰放气混合,并在提氢条件下,得到氢气;(4)将步骤(1)得到的煤焦油进行蒸馏分离,得到酚油馏分、中间馏分和重馏分,其中,所述酚油馏分为小于220℃馏分,所述中间馏分为220-350℃馏分,所述重馏分为大于350℃馏分;(5)将步骤(4)得到的酚油馏分与步骤(2)得到的甲醇进行醚化反应,得到高辛烷值组分;(6)用萃取剂对步骤(4)得到的重馏分进行萃取分离,得到脱沥青油;(7)将步骤(4)得到的中间馏分与步骤(6)得到的脱沥青油进行加氢精制和加氢裂化后,裂化产物经分馏得到汽油馏分和柴油馏分;(8)将步骤(5)得到的高辛烷值组分加入到步骤(7)得到的汽油馏分中,制得高辛烷值的汽油;(9)将柴油馏分进行加氢改质处理,制得改质柴油;(10)将步骤(3)得到的至少一部分氢气通入步骤(7)的加氢精制和 /或加氢裂化反应中。根据本发明,步骤(2)中,所述气化的条件可以在很大范围内改变,优选情况下,所述气化的条件包括:气化压力为0.07-3MPa,气化温度为1000-1200℃。更优选地,所述气化的条件包括:气化压力为0.1-3MPa,气化温度为1000-1200℃。根据本发明,步骤(2)中,所述甲醇合成反应的反应器、反应条件以及催化剂可以根据实际需要进行选择和调整,优选情况下,所述甲醇合成反应是在固定床反应器上进行,所述甲醇合成反应的条件包括:温度为220-280℃,压力为5-10MPa,合成气空速为4000-10000h-1。更优选地,所述甲醇合成反应的条件包括:温度为260-280℃,压力为5-7MPa,合成气空速为4000-6000h-1;所述甲醇合成反应的催化剂可以为CuO/ZnO/Al2O3催化剂。本发明中,步骤(3)中,所述提氢的方法可以为本领域公知的各种提氢方法,优选情况下,所述提氢的方法为变压吸附法,变压吸附法的条件包括:压力为0.3-4.0MPa,吸附剂选自氧化铝、硅胶、活性炭和沸石分子筛中的至少一种,如图2所示。可选地,步骤(3)中,所述提氢的方法也可以为膜分离法,如图1所示膜分离法的压力为0.3-2.0MPa,所述膜分离法所用薄膜的种类为本领域技术人员所公知,例如可以由选自聚酰亚胺和聚砜高分子聚合物制成。本发明可以将步骤(3)中得到的至少一部分氢气通入步骤(7)的加氢精制和/或加氢裂化反应中。本发明步骤(4)至步骤(9)涉及煤焦油制备清洁燃料,与前述煤焦油制备清洁燃料方法的步骤(1)至步骤(6)相对应,在此不再赘述,上文中所有有关本发明的第一方面的描述,均由于提及而在此引入。同样优选地,本发明步骤(5)中进行醚化反应后剩余的醇,可以作为 循环醇并入步骤(2)中得到的甲醇,与步骤(4)得到的酚油馏分进行醚化反应。本发明提供的煤制清洁燃料的方法实现了煤热解气、半焦和煤焦油各个生产工艺之间的系统连通,提高了系统能效使能源的利用最大化,达到了煤炭资源的高效和清洁利用。本发明还提供了以上煤焦油制清洁燃料的方法及煤制清洁燃料的方法获得的高辛烷值的汽油和改质柴油。以上结合附图详细描述了本发明的优选实施方式,但是,本发明并不限于上述实施方式中的具体细节,在本发明的技术构思范围内,可以对本发明的技术方案进行多种简单变型,这些简单变型均属于本发明的保护范围。另外需要说明的是,在上述具体实施方式中所描述的各个具体技术特征,在不矛盾的情况下,可以通过任何合适的方式进行组合,为了避免不必要的重复,本发明对各种可能的组合方式不再另行说明。此外,本发明的各种不同的实施方式之间也可以进行任意组合,只要其不违背本发明的思想,其同样应当视为本发明所公开的内容。实施例1如图1所示工艺流程所示:(1)将原料煤(神木煤)粉碎后送进直立干馏炉中进行热解反应,压力为0.05MPa,温度为650℃,得到煤焦油(性质见下表1)、半焦和热解煤气。将半焦送入流化床煤气发生器中,在压力为0.13MPa,温度为1000℃,气固比5:1(体积/体积)的条件下,与水蒸气和氧气(水蒸气与氧气的体积比为4:1)反应,得到气化粗煤气。气化粗煤气经增压至3.0MPa后进入耐硫变换装置,将气体中的成分满足甲醇合成原料气中H2/CO的要求,变换后的气体进入脱硫装置,将气体中总硫含量降低至0.1ppm以下,再经压缩机增 压至5.0MPa,进入甲醇合成装置(固定床反应器)进行甲醇合成反应,所述甲醇合成反应的条件包括:温度为260℃,压力为5.0MPa,合成气空速为5000h-1;所述甲醇合成反应的催化剂为托普索公司的CuO/ZnO/Al2O3;经精馏分离得到甲醇和甲醇驰放气;并将热解反应得到的热解煤气与甲醇驰放气混合,通过膜分离法,得到浓度大于99.8重量%的氢气。(2)将步骤(1)得到的煤焦油经机械预处理脱除杂质和水后,进行蒸馏分离,得到酚油馏分(小于220℃馏分)、中间馏分(220-350℃馏分)和重馏分(大于350℃馏分);其中,所述酚油馏分中酚的总量为60重量%;再将该酚油馏分中酚与甲醇以摩尔比为1:3,在温度为450℃下,平均液体空速1.5h-1,在催化剂Cs2O/SiO2的存在下进行醚化反应,结果得到高辛烷值的汽油添加剂,其辛烷值为112.8。(3)在温度为180℃,压力为5MPa的条件下,将步骤(1)得到的重馏分与正戊烷按1:5的重量比混合进行萃取分离,得到萃取相和萃余相,其中,萃取相为脱沥青油(性质如表12所示)。(4)将步骤(1)中得到的中间馏分与步骤(3)中得到的脱沥青油依次进行加氢精制和加氢裂化,其中,加氢精制的条件包括:反应温度为380℃、压力为10MPa、氢油体积比为1000:1,平均液体空速为0.5h-1;加氢裂化的条件包括:反应温度为400℃、压力为12MPa、氢油体积比为1500:1,平均液体空速为0.8h-1。加氢裂化产物经分馏,获得汽油馏分和柴油馏分;然后,将柴油馏分在反应温度为380℃、压力为10MPa、氢油体积比为1500:1,平均液体空速为0.5h-1下进行加氢改质,获得改质柴油(性质如表3所示);然后,再将经醚化反应得到的产物高辛烷值组分与上述的汽油馏分以1:3.5的重量比进行混合,获得调和汽油终油品(性质如表2所示)。表1煤焦油性质表2调和汽油终油品的性质注:93号国标参数为GB17930-2011《车用汽油V》93号车用汽油标准参数。表3改质柴油的性质注:0号国标参数为GB19147-2009《车用柴油V》0号车用柴油标准参数。实施例2如图2所示工艺流程所示:(1)将原料煤(神木煤)粉碎后送进直立干馏炉中进行热解反应,压力为0.05MPa,温度为650℃,得到煤焦油(性质见上表1)、半焦和热解煤气。将半焦送入流化床煤气发生器中,在压力为0.13MPa,温度为1000℃,气固比5:1(体积/体积)的条件下,与水蒸气和氧气(水蒸气与氧气的体积比为4:1)反应,得到气化粗煤气。气化粗煤气经增压至3.0MPa后进入耐硫变换装置,将气体中的成分满足甲醇合成原料气中H2/CO的要求,变换后的气体进入脱硫装置,将气体中总硫含量降低至0.1ppm以下,再经压缩机增压至6.0MPa,进入甲醇合成装置(固定床反应器)进行甲醇合成反应,所 述甲醇合成反应的条件包括:温度为270℃,压力为6.0MPa,合成气空速为6000h-1;所述甲醇合成反应的催化剂为CuO/ZnO/Al2O3;经精馏分离得到甲醇和甲醇驰放气;并将热解反应得到的热解煤气与甲醇驰放气混合,通过变压吸附提纯氢气法,得到浓度大于99重量%的氢气。(2)将步骤(1)得到的煤焦油经机械预处理脱除杂质和水后,进行蒸馏分离,得到酚油馏分(小于220℃馏分)、中间馏分(260-350℃馏分)和重馏分(大于350℃馏分);其中,所述酚油馏分中酚的总量为60重量%;再将该酚油馏分中酚与甲醇以摩尔比为1:5,在温度为400℃下,平均液体空速0.5h-1条件下,在催化剂Cs2O/SiO2的存在下进行醚化反应,结果得到高辛烷值的汽油添加剂,其辛烷值为120.5。(3)在温度为180℃,压力为6MPa的条件下,将步骤(1)得到的重馏分与丁烷按1:3的重量比混合进行萃取分离,得到萃取相和萃余相,其中,萃取相为脱沥青油(性质如表12所示)。(4)将步骤(1)中得到的中间馏分与步骤(3)中得到的脱沥青油依次进行加氢精制和加氢裂化,其中,加氢精制的条件包括:反应温度为380℃、压力为12MPa、氢油体积比为1500:1,平均液体空速为0.5h-1;加氢裂化的条件包括:反应温度为380℃、压力为12MPa、氢油体积比为1500:1,平均液体空速为1.0h-1。加氢裂化产物经分馏,获得汽油馏分和柴油馏分;然后再将经醚化反应得到的产物高辛烷值组分与上述的汽油馏分以1:2.5的重量比进行混合,获得调和汽油终油品(性质如表4所示)。然后将柴油馏分在反应温度为380℃、压力为12MPa、氢油体积比为1200:1,平均液体空速为1.0h-1下进行加氢改质,获得加氢改质柴油(性质如表5所示)。表4调和汽油终油品的性质注:93号国标参数为GB17930—2011《车用汽油》93号车用汽油V标准参数。表5改质柴油的性质注:0号国标参数为GB19147—2009《车用柴油》0号车用柴油V标准参数。实施例3如图2所示工艺流程所示:(1)将原料煤(通辽煤)粉碎后送进直立干馏炉中进行热解反应,压力为0.03MPa,温度为550℃,得到煤焦油(性质见表6)、半焦和热解煤气。将半焦送入气化炉中,在压力为2.8MPa,温度为1200℃条件下,得到气化粗煤气。气化粗煤气经增压至3.0MPa后进入耐硫变换装置,将气体中的成分满足甲醇合成原料气中H2/CO的要求,变换后的气体进入脱硫装置,将气体中总硫含量降低至0.1ppm以下,再经压缩机增压至5.0MPaMPa,进入甲醇合成装置(固定床反应器)进行甲醇合成反应,所述甲醇合成反应的条件 包括:温度为260℃,压力为5.0MPa,合成气空速为4000h-1;所述甲醇合成反应的催化剂为CuO/ZnO/Al2O3;经精馏分离得到甲醇和甲醇驰放气;并将热解反应得到的热解煤气与甲醇驰放气混合,通过变压吸附提纯氢气法,得到浓度大于99重量%的氢气。(2)将步骤(1)得到的煤焦油经机械预处理脱除杂质和水后,进行蒸馏分离,得到酚油馏分(小于220℃馏分)、中间馏分(220-350℃馏分)和重馏分(大于350℃馏分);其中,所述酚油馏分中酚的总量为64重量%;再将该酚油馏分中酚与步骤(1)得到的甲醇以摩尔比为1:5,在温度为400℃下,平均液体空速0.5h-1条件下,在催化剂SiO2进行醚化反应,得到高辛烷值组分,其辛烷值为115.6。(3)在温度为180℃,压力为5MPa的条件下,将步骤(1)得到的重馏分与正戊烷按1:3的重量比混合进行萃取分离,得到萃取相和萃余相,其中,萃取相为脱沥青油(性质如表12所示)。(4)将步骤(1)中得到的中间馏分与步骤(3)中得到的脱沥青油依次进行加氢精制和加氢裂化,其中,加氢精制的条件包括:反应温度为380℃、压力为12MPa、氢油体积比为1500:1,平均液体空速为0.4h-1;加氢裂化的条件包括:反应温度为400℃、压力为12MPa、氢油体积比为1500:1,平均液体空速为0.5h-1。加氢裂化产物经分馏,获得汽油馏分和柴油馏分;然后再将经醚化反应得到的产物高辛烷值组分与上述的汽油馏分以1:6的重量比进行混合,获得调和汽油终油品(性质如表7所示)。然后将柴油馏分在反应温度为380℃、压力为10MPa、氢油体积比为1500:1,平均液体空速为0.5h-1下进行加氢改质,获得加氢改质柴油(性质如表8所示)。表6煤焦油性质表7调和汽油终油品的性质注:93号国标参数为GB17930—2011《车用汽油》93号车用汽油V标准参数。表8改质柴油的性质注:0号国标参数为GB19147-2013《车用柴油V》0号车用柴油标准参数。实施例4如图3所示工艺流程所示:(1)将呼伦贝尔褐煤煤焦油(性质见表9)经机械预处理脱除杂质和水后,进行蒸馏分离,得到酚油馏分(小于220℃馏分)、中间馏分(220-350℃馏分)和重馏分(大于350℃馏分);其中,所述酚油馏分中酚的总量为66重量%;再将该酚油馏分中酚与甲醇以摩尔比为1:2.5,在温度为400℃,平均液体空速0.5h-1条件下,在催化剂SiO2的存在下进行醚化反应,得到高辛烷值组分,其辛烷值为117.6。(2)在温度为180℃,压力为6MPa的条件下,将步骤(1)得到的重 馏分与正戊烷按1:3的重量比混合进行萃取分离,得到萃取相和萃余相,其中,萃取相为脱沥青油(性质如表12所示)。(3)将步骤(1)中得到的中间馏分与步骤(2)中得到的脱沥青油依次进行加氢精制和加氢裂化,其中,加氢精制的条件包括:反应温度为380℃、压力为12MPa、氢油体积比为1000:1,平均液体空速为0.4h-1;加氢裂化的条件包括:反应温度为400℃、压力为12MPa、氢油体积比为1500:1,平均液体空速为0.5h-1。加氢裂化产物经分馏,获得汽油馏分和柴油馏分;然后再将经醚化反应得到的产物高辛烷值组分与上述的汽油馏分以1:5的重量比进行混合,获得调和汽油终油品(性质如表10所示)。然后将柴油馏分在反应温度为380℃、压力为12MPa、氢油体积比为1200:1,平均液体空速为0.5h-1下进行加氢改质,获得加氢改质柴油(性质如表11所示)。表9煤焦油性质表10调和汽油终油品的性质注:93号国标参数为GB17930—2011《车用汽油》93号车用汽油V标准参数。表11改质柴油的性质注:0号国标参数为GB19147-2009《车用柴油V》0号车用柴油标准参数。实施例5如图1所示工艺流程所示:采用与实施例1相同的煤制清洁燃料的方法,不同在于,步骤(3)中,萃取分离在萃取剂超临界状态下进行,得到萃取相和萃余相,其中,萃取相为脱沥青油(性质如表12所示),超临界萃取分离的条件为:温度为160℃,压力为4MPa。实施例6如图2所示工艺流程所示:采用与实施例3相同的煤制清洁燃料的方法,不同在于,步骤(3)中,萃取分离在萃取剂超临界状态下进行,得到萃取相和萃余相,其中,萃取相为脱沥青油(性质如表12所示),超临界萃取分离的条件为:温度为185℃,压力为5MPa。表12编号密度/kg/m3,20℃残炭/重量%沥青质/重量%实施例10.98352.246.32实施例20.98212.326.37实施例30.98442.426.44实施例40.96821.453.85实施例50.98652.536.85实施例60.98672.566.76从以上实施例在表1-11中的数据可以看出,本发明提供的煤制清洁燃料的方法实现了对煤炭资源的充分深加工,获得了高辛烷值组分,生产高品质的清洁燃料,同时实现了各个生产工艺之间的系统连通,提高了系统能效,使能源的利用最大化,达到了煤炭资源的高效和清洁利用。从实施例1-6在表12中的数据可见,萃取分离在萃取剂超临界状态下进行,得到具有更小密度、更低残炭含量和沥青质含量的脱沥青油,将得到的上述更小密度、更低残炭含量和沥青质含量的脱沥青油进行加氢处理,更有利于减少加氢过程中在加氢催化剂表面形成的结焦量,延长加氢催化剂的使用寿命,使得加氢装置(特别是固定床加氢装置)能够长期稳定运行,另外,根据以上实施例在表1-11中的数据可知,利用上述更小密度、更低残炭含量和沥青质含量的脱沥青油,可以制备得到的高品质的调和汽油终油品和改性柴油。当前第1页1 2 3