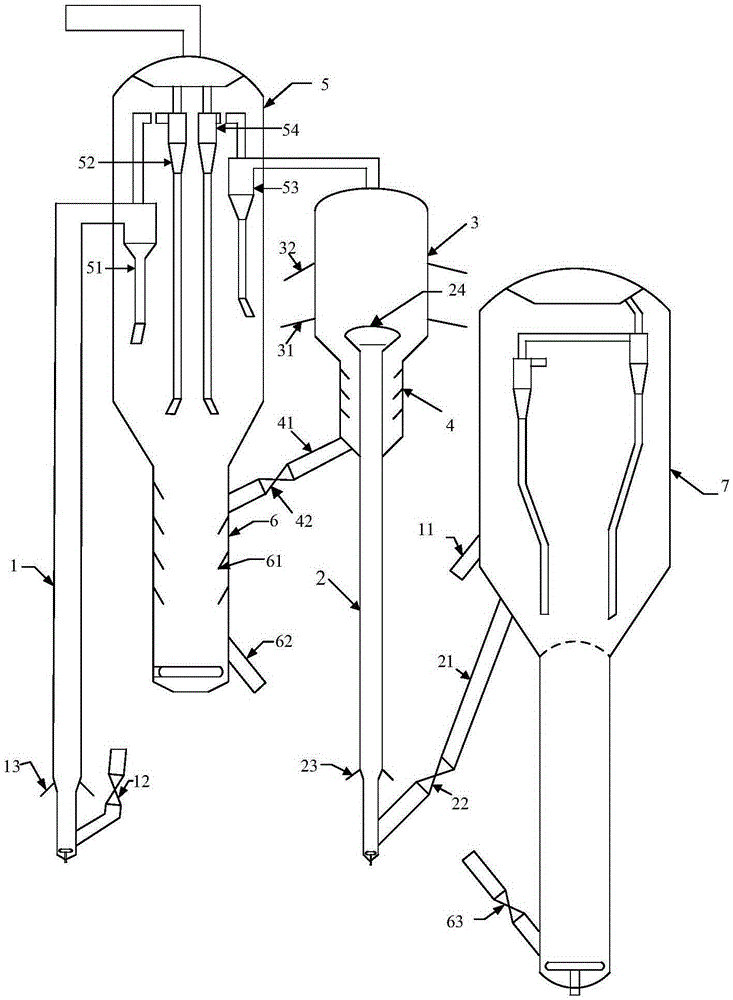
本发明涉及一种多产丁烯和轻芳烃的烃类催化转化方法。
背景技术:
:丁烯和轻芳烃(苯、甲苯和二甲苯,简称BTX)是基本的化工原料,目前丁烯主要来源于MTO、丁烷、LPG、凝析油、石脑油、加氢裂化尾油及粗柴油等蒸汽热裂解和烃油催化裂化,BTX主要来源于轻烃重整工艺和蒸汽热裂解工艺。随着蒸汽裂解采用新的轻质原料,产品分布将会出现变化,如采用乙烷作为蒸汽裂解原料,与以石脑油为原料相比,产物中乙烯比例明显提高,而丁烯和轻芳烃的产率将会降低。在这样的背景下,利用重质烃油催化转化生产丁烯和轻芳烃,将是蒸汽热裂解制乙烯的一条有效补充措施。US5009769中公开的烃类裂化方法采用双提提升管反应器裂化不同性质的烃类原料。蜡油和渣油注入第一根提升管,在剂油比5-10、停留时间1-4秒的条件下裂化;直馏汽油、直馏中间馏分油和催化重汽油注入第二根提升管,在剂油比3-12、停留时间1-5秒的条件下裂化。两根提升管末端进入同一个沉降器中,且共用后续分馏系统。CN1299403A公开了一种由重质烃原料选择性生产C2-C4烯烃的两段催化裂化方法。该方法包括:在常规大孔沸石催化裂化催化剂存在下,在由催化裂化装置组成的第一反应段中将重质原料转化成较低沸点产物。将所生成的较低沸点产物中的石脑油馏分进入由反应区、汽提区、催化剂再生区和分馏区组成的第二反应段中,在500-600℃温度下与含约10-50重量%平均孔径小于约0.7纳米的沸石催化剂接触形成裂化产物。US7323099公开了一种选择性生产低碳烯烃的两段催化裂化方法。在第 一反应区,重质原料在含大孔和中孔分子筛催化剂的催化转化下,生产富含烯烃的汽油组分,第一反应区生成的富含烯烃汽油组分再在第二反应区在含中孔分子筛催化剂的催化转化下,生成低碳烯烃。CN101362961A公开了一种制取芳烃和低碳烯烃的催化转化方法,馏程为160-260℃的原料与催化裂解催化剂接触,在温度450-750℃、重时空速0.1-800h-1、反应压力0.10-1.0MPa、催化裂解催化剂与原料的重量比1-150、水蒸汽与原料的重量比为0.05-1.0的条件下,在流化床反应器内进行裂化反应,分离待生催化剂和反应油气,待生催化剂经再生后返回反应器,分离反应油气经分离得到目的产物低碳烯烃和芳烃。该方法乙烯、丙烯产率和选择性大幅增加,汽油的收率和汽油中芳烃的产率均很高,仅有少量重油生成,并且焦炭产率较低。以上技术虽然在增加催化裂化丙烯产率方面取得了比较明显的进步,然而其增加催化裂化丁烯产率的局限性依然很大,并且未涉及如何提高轻芳烃的产率。技术实现要素:本发明的目的是克服现有的由重质烃类原料催化裂化制低碳烯烃和轻芳烃的工艺过程中存在的丁烯和/或轻芳烃产率不高的缺陷,提供一种多产丁烯和轻芳烃的烃类催化转化方法。为了实现上述目的,本发明提供了一种多产丁烯和轻芳烃的烃类催化转化方法,该方法包括以下步骤:(1)将重质烃类原料与第一裂化催化剂在第一反应器中接触反应,然后分离得到第一积炭催化剂和第一反应产物;(2)将终馏点不超过90℃的轻裂解汽油与第二裂化催化剂在第二反应器中接触反应;(3)将所述第二反应器反应后得到的反应混合物不经分离直接引入第三反应器中与馏程为200-390℃的加氢改质裂解轻油接触反应,然后分离得到第二积炭催化剂和第二反应产物,其中,所述加氢改质裂解轻油由裂解轻油进行加氢处理制得;(4)将所述第一反应产物和所述第二反应产物进行分馏,将所述第一积炭催化剂和所述第二积炭催化剂进行汽提和再生,并将得到的再生催化剂引入所述第一反应器和所述第二反应器中循环利用;其中,所述裂化催化剂为含有改性β沸石的裂化催化剂,所述改性β沸石为磷和过渡金属M改性的β沸石。在本发明提供的所述方法中,在第二反应器中引入轻裂解汽油进行反应,一方面可以使裂化催化剂少量积炭,覆盖部分强酸性中心,另一方面向上的反应物流中含有大量正碳离子。这两个方面可以用来优化加氢改质裂解轻油(特别是富含环烷烃的加氢裂解轻油)的反应,由于裂化催化剂上的强酸性中心被覆盖,同时反应物流中含有大量正碳离子,这样既可以抑制加氢改质裂解轻油的氢转移反应,还可以快速引发加氢改质裂解轻油发生正碳离子裂化反应,生成丁烯和轻芳烃。因此,本发明提供的所述方法能够获得较高的丁烯和轻芳烃产率。而且,本发明中使用的含有改性β沸石的裂化催化剂有助于增产丁烯和轻芳烃。另外,在本发明中,在不同的反应器中,可以使用不同的烃类原料,并对不同烃类的反应进行分区调控,使得本发明的方法的工艺灵活度相对较高。本发明的其它特征和优点将在随后的具体实施方式部分予以详细说明。附图说明附图是用来提供对本发明的进一步理解,并且构成说明书的一部分,与下面的具体实施方式一起用于解释本发明,但并不构成对本发明的限制。在附图中:图1是实施本发明所述的方法的催化裂化装置的一种实施方式的结构示意图。附图标记说明1第一反应器11向第一反应器输送再生的裂化催化剂的输送管12输送管11上的再生催化剂流量控制阀13第一反应器的原料油进料喷嘴2第二反应器21向第二反应器输送再生的裂化催化剂的输送管22输送管21上的再生催化剂流量控制阀23第二反应器的轻裂解汽油进料喷嘴24第二反应器的出口分布器3第三反应器31第三反应器底部加氢裂解轻油喷嘴32第三反应器上部冷却介质喷嘴4汽提器41向汽提器6输送待生催化剂的输送管42输送管41的流量控制阀5沉降器51第一反应器的快速分离器52单级旋风分离器53第三反应器的粗旋54单级旋风分离器6汽提器61汽提器6的挡板62汽提器6的待生催化剂输送管63输送管62上的待生催化剂流量控制阀7再生器具体实施方式以下对本发明的具体实施方式进行详细说明。应当理解的是,此处所描述的具体实施方式仅用于说明和解释本发明,并不用于限制本发明。在本文中,除非有特殊的说明,术语“低碳烯烃”均指C2-C4烯烃,“轻芳烃”均指苯、甲苯和二甲苯。本发明提供的所述多产丁烯和轻芳烃的烃类催化转化方法包括:(1)将重质烃类原料与第一裂化催化剂在第一反应器中接触反应,然后分离得到第一积炭催化剂和第一反应产物;(2)将终馏点不超过90℃的轻裂解汽油与第二裂化催化剂在第二反应器中接触反应;(3)将所述第二反应器反应后得到的反应混合物不经分离直接引入第三反应器中与馏程为200-390℃的加氢改质裂解轻油接触反应,然后分离得到第二积炭催化剂和第二反应产物,其中,所述加氢改质裂解轻油由裂解轻油进行加氢处理制得;(4)将所述第一反应产物和所述第二反应产物进行分馏,将所述第一积炭催化剂和所述第二积炭催化剂进行汽提和再生,并将得到的再生催化剂引入所述第一反应器和所述第二反应器中循环利用;其中,所述裂化催化剂为含有改性β沸石的裂化催化剂,所述改性β沸 石为磷和过渡金属M改性的β沸石。在步骤(1)中,所述第一反应器可以是提升管反应器、流化床反应器、下行式输送线反应器或者由多个上述反应器经过串联和/或并联组成的复合反应器,其中,每个反应器可以根据需要分成两个或两个以上的反应区。优选情况下,所述第一反应器为提升管反应器。所述提升管反应器可以为等直径提升管反应器、等线速提升管反应器和变直径提升管反应器中的一种或多种。在步骤(1)中,当所述第一反应器为提升管反应器时,所述第一反应器的反应条件可以包括:温度为450-540℃(反应器的出口温度),优选为490-530℃;剂油重量比(引入第一反应器的催化剂与重质烃类原料的重量比)为4-15:1;油气停留时间为0.1-5s,优选为1-4s。反应区的绝压可以为0.15-0.30MPa(反应器的出口压力),优选为0.18-0.28MPa。在步骤(1)中,优选向所述第一反应器中注入稀释剂,以降低所述重质烃类原料的分压。该稀释剂可以选自水蒸气、C1-C4低碳烷烃和氮气中的一种或多种,优选为水蒸气。稀释剂与重质烃类原料的用量的重量比可以为0.01-2:1,优选为0.05-0.20:1。在步骤(2)中,所述第二反应器可以是提升管反应器、流化床反应器、下行式输送线反应器或者由多个上述反应器经过串联和/或并联组成的复合反应器,其中,每个反应器可以根据需要分成两个或两个以上的反应区。优选情况下,所述第二反应器为提升管反应器。所述第二反应器可以是一个提升管反应器,也可以是多个提升管反应器并联或串联。所述提升管反应器可以选自等直径提升管反应器、等线速提升管反应器和变直径提升管反应器中的一种或多种。在一种优选实施方式中,所述第二反应器为提升管反应器,且该提升管反应器的反应条件包括:温度为540-620℃(反应器的出口温度),剂油重量 比(引入第二反应器的催化剂与轻裂解汽油的重量比)为15-100:1,油气停留时间为0.1-3s。反应区的绝压为0.15-0.30MPa(反应器的出口压力)。进一步优选地,作为所述第二反应器的提升管反应器从下到上包括预提升段和提升管,并且在所述预提升管的上方且在所述提升管的底部设置有加料喷嘴,所述轻裂解汽油通过该加料喷嘴喷入所述提升管中。在步骤(2)中,优选向所述第二反应器中注入稀释剂,以降低其中烃类原料的分压。该稀释剂可以选自水蒸气、C1-C4低碳烷烃和氮气中的一种或多种,优选为水蒸气。稀释剂与轻裂解汽油的重量比可以为0.01-2:1,优选为0.05-0.20:1。在步骤(2)中,所述轻裂解汽油的终馏点不超过90℃,优选不超过75℃,更优选馏程为35-75℃。所述轻裂解汽油可以含有30-100重量%的烯烃。更进一步优选地,所述轻裂解汽油中的烯烃含量不低于45重量%,更进一步优选不低于55重量%。该轻裂解汽油可以是本发明方法的后续分馏过程中得到的轻汽油馏分,也可以是来自于其它裂化过程,例如可以是催化裂化轻汽油、蒸汽裂解轻汽油、焦化轻汽油等。优选情况下,所述轻裂解汽油中的至少部分来自本发明方法的后续分馏过程得到的轻汽油馏分。在步骤(2)中,为了进一步提高丁烯和轻芳烃的产率,更优选地,所述轻裂解汽油在注入所述第二反应器之前经过选择性加氢处理,以将其中的二烯烃和炔烃转化为单烯烃。该选择性加氢处理的条件可以包括:温度为20-90℃,压力为0.2-1MPa(绝压),氢气和烯烃的摩尔比为1-5:1。所使用的催化剂可以为各种常规的加氢催化剂,如含镍的加氢催化剂,该加氢催化剂可以为各种市售的产品,如中石化长岭催化剂分公司生产的牌号为RDD-1的加氢催化剂。所述选择性加氢处理可以采用常规的方法实施,例如可以采用专利申请CN1035775A中公开的方法实施。在步骤(3)中,所述第三反应器优选为流化床反应器。所述第三反应 器可以是一个或者多个并联或串联的流化床反应器。所述流化床反应器可以选自散式流化床反应器、鼓泡床反应器、湍动床反应器、快速床反应器和密相流化床反应器中的一种或多种。在优选情况下,所述第三反应器为流化床反应器,且该流化床反应器的反应条件可以包括:温度为520-600℃(床层温度),优选为540-580℃;重时空速为0.2-30h-1,优选为2-20h-1;油气空塔线速为0.2-1.5m/s,优选为0.6-1.2m/s;反应区的绝压为0.15-0.30MPa。在步骤(3)中,第三反应器中生成的反应油气离开流化床床层时温度较高,为了抑制目标产物发生二次反应,进一步优选在所述第三反应器的上部稀相空间注入冷却介质以将所述第三反应器的上部温度降至480-540℃。所述冷却介质可以为干气、水蒸气、粗裂解汽油和含油污水中一种或多种,最优选为含油污水。在步骤(3)中,所述加氢改质裂解轻油的馏程优选为240-365℃。所述加氢改质裂解轻油中的链烷烃和环烷烃总含量可以大于70重量%,优选大于75重量%;双环芳烃含量可以小于3重量%,优选小于2重量%;三环芳烃含量可以小于1重量%,优选小于0.5重量%。在步骤(3)中,注入所述第三反应器的加氢改质裂解轻油为裂解轻油经过加氢处理制得,以将其中的芳烃饱和成环烷烃。优选地,该加氢改质裂解轻油的制备过程包括:将裂解轻油在反应温度为200-480℃(优选300-450℃)、氢分压为0.7-21MPa(优选5-16MPa)、体积空速为0.1-6h-1(优选0.3-2h-1)、氢油体积比为100-2600(优选800-1500)的条件下进行加氢处理,其中,体积空速定义为单位时间内通过单位催化剂体积的油的体积。该加氢处理过程所用的催化剂可以含有无机载体(优选为氧化铝或氧化铝-氧化硅)和负载在该无机载体上的至少一种第VIII族金属(可选地与第VI族金属组合)。所述第VIII族和第VI族金属为本领域技术人员公知,在元素周期表中 有明确定义。第VIII族金属的含量优选为3-25重量%,更优选为5-15重量%。优选地,第VIII族金属选自Pt、Co、Ni和Fe,最优选选自Pt、Co和Ni。优选地,第VI族金属为Mo,其含量可以为5-50重量%,优选为10-40重量%,更优选为20-30重量%。为了进一步提高丁烯和轻芳烃的产率,裂解轻油经过加氢改质后得到加氢改质裂解轻油,所述加氢改质裂解轻油中的链烷烃和环烷烃总含量大于70重量%,优选大于75重量%;双环芳烃含量小于3重量%,优选小于2重量%;三环芳烃含量小于1重量%,优选小于0.5重量%。在步骤(3)中,所述裂解轻油可以是本发明方法的后续分馏过程中得到的裂解轻油,也可以是来自于其它裂化过程。优选情况下,所述裂解轻油中的至少部分来自本发明方法的后续分馏过程得到的裂解轻油。在一种优选实施方式中,本发明提供的所述方法还包括:将从所述第一反应产物和所述第二反应产物中分离出的轻裂解汽油和裂解轻油分别返回步骤(2)和步骤(3)中使用,也即使步骤(2)中的轻裂解汽油至少部分源自本发明方法的后续分馏过程得到的轻裂解汽油,且使步骤(3)中的裂解轻油至少部分源自本发明方法的后续分馏过程得到的裂解轻油。在本发明提供的所述方法中,步骤(2)中所用的轻裂解汽油与步骤(1)中所用的重质烃类原料的重量比可以为0.05-0.8:1,优选为0.08-0.5:1;步骤(3)中所用的加氢裂解轻油与步骤(1)中所用的重质烃类原料的重量比可以为0.05-0.9:1,优选为0.08-0.6:1。在本发明中,所述重质烃类原料可以选自凝析油、致密油、减压瓦斯油、常压渣油和减压渣油中一种或多种。在本发明所述的方法中,步骤(1)得到的第一反应产物和步骤(3)得到的第二反应产物优选引入同一分馏装置中进行分馏。分馏得到低碳烯烃、汽油、轻油、重油及其它低分子饱和烃类,其中,所得到的轻汽油馏分可以 部分或全部返回至第二反应器进行催化裂化反应,所述得到的裂解轻油部分或全部经过加氢改质后可以返回至第三反应器中进行反应。在本发明所述的方法中,所述第一反应器和所述第二反应器中加入的裂化催化剂可以相同或不同,优选为相同。所述裂化催化剂为含有改性β沸石的裂化催化剂。优选地,以所述裂化催化剂的总重量为基准,所述裂化催化剂含有1-60重量%的沸石混合物、5-99重量%的耐热无机氧化物和0-70重量%的粘土;更优选地,所述裂化催化剂含有10-50重量%的沸石混合物、10-70重量%的耐热无机氧化物和0-60重量%的粘土。其中,以所述沸石混合物的总重量为基准,所述沸石混合物含有1-75重量%的改性β沸石和25-99重量%的具有MFI结构的沸石;更优选地,所述沸石混合物含有10-70重量%的改性β沸石和30-90重量%的具有MFI结构的沸石。在本发明中,所述改性β沸石为磷和过渡金属M改性的β沸石。该改性β沸石可以采用各种常规方法进行制备,例如,可以在合成β沸石的过程中引入磷和过渡金属M,或者在合成β沸石后采用铵交换、磷改性、过渡金属M改性及焙烧处理等步骤来引入磷和所述过渡金属M。所述的过渡金属M可以选自Fe、Co、Ni和Cu中的一种或多种,优选为Fe和/或Cu。在本发明中,所述具有MFI结构的沸石可以为具有pentasil结构的高硅沸石,选自ZSM-5和ZRP系列沸石中的一种或多种。优选地,具有MFI结构的沸石为含稀土的ZRP沸石(参见CN1052290A、CN1058382A、US5232675)、含磷的ZRP沸石(参见CN1194181A、US5951963)、含磷和稀土的ZRP沸石(参见CN1147420A)、含磷和碱土金属的ZRP沸石(参见CN1211469A、CN1211470A、US6080698)以及含磷和过渡金属的ZRP沸石(参见CN1465527A、CN1611299A)中的一种或多种。所述β沸石和所述具有MFI结构的沸石可以采用市售品,也可以采用本领域公知的各种方法进行制备,在此不再赘述。在本发明中,所述耐热无机氧化物可以选自SiO2和/或Al2O3。在本发明中,所述粘土可以为本领域常规使用的各种粘土,如高岭土和/或多水高岭土。在本发明中,所述烃类催化转化方法还可以包括将所得到的催化裂解的汽油全馏分或将其切割后的馏程在70-180℃之间(优选在80-170℃之间)的汽油馏分(富含芳烃的汽油组分)加氢精制得到精制汽油;然后将精制汽油进行溶剂抽提,得到苯、甲苯、二甲苯的步骤。所述加氢精制可以采用常规的方法实施,通常可以包括将所述汽油馏分与加氢催化剂以及氢气接触,在氢分压为2.0-15.0MPa、温度为200-400℃、氢油体积比为100-1000:1、体积空速为0.5-5h-1的条件下反应,饱和其中的烯烃、二烯烃和炔烃,同时脱除硫氮等杂质,得到精制汽油。所述加氢催化剂可以是负载在氧化铝和/或无定型硅铝上的第VIB和/或VIII族非贵金属催化剂,所述第VIB非贵金属可以选自Mo或/和W,所述第VIII族非贵金属可以选自Co或/和Ni(参见CN1109495A、CN1631529A、CN1631526A、CN1632071A)。优选地,所述加氢催化剂含有0-10重量%的添加剂、1-9重量%的至少一种第VIII族金属、12-39重量%的至少一种第VIB族金属以及氧化铝和/或无定型硅铝载体,其中,所述添加剂可以选自氟、磷等非金属元素和钛等金属元素。所述溶剂抽提可以采用常规的方法实施,例如可以包括将加氢精制得到的精制汽油与溶剂接触,在温度为80-120℃、溶剂与精制汽油之间的体积比为2-6的条件下抽提,得到苯、甲苯、二甲苯(参见专利CN1393507A、CN1258717A)。其中,溶剂抽提的溶剂可以选自环丁砜、N-甲基吡咯烷酮、二乙二醇醚、三乙二醇醚、四乙二醇、二甲基亚砜和N-甲酰基吗啉醚中的一种或多种,溶剂回收后可循环使用。抽余油即非芳烃可以作为蒸汽裂解原料,也可以引入催化裂化反应器进行裂化反应,例如可以引入第一反应器、第二反应器、第三反应器进行裂化反应,还可以用于调和汽油。本发明提供的所述多产低碳烯烃和轻芳烃的烃类催化转化方法可以在图1所示的催化裂化装置中实施,具体地,该催化裂化装置包括第一提升管反应器1(即第一反应器)、第二提升管反应器2(即第二反应器)和流化床反应器3(即第三反应器),所述第二提升管反应器2位于所述流化床反应器3的下方,所述第一提升管反应器1、所述第三流化床反应器3与所述沉降器6三器并列排布。而且,通过在第三反应器的稀相空间喷入冷却介质,可快速将反应油气降温,并快速引出反应器,从而大幅减少反应油气停留时间,避免生成的目标产物(即丁烯烃和轻芳烃)进一步消耗,同时可以明显降低干气产率。在优选情况下,如图1所示,实施本发明的方法的催化裂化装置包括:第一提升管反应器1、第二提升管反应器2、流化床反应器3、沉降器5和汽提器4和6,所述汽提器4位于所述流化床反应器3的下方,所述汽提器6位于沉降器5的下方。第二提升管反应器2的出口24和所述流化床反应器3的下部任意位置连通,且所述流化床反应器3与沉降器5通过一条或多条通道连通。更优选地,汽提器4与流化床反应器3同轴,并位于流化床反应器3的下方,汽提器4和汽提器6通过一条或多条通道连通。其中,第一提升管反应器1和第二提升管反应器2均选自等直径的圆管、锥台形筒体或1-6段直径不同的直筒体通过变径段连接而成的组合体的至少一种;所述流化床反应器3选自等直径的筒体、锥台形筒体或1-6段直径不同的直筒体通过变径段连接而成的组合体的至少一种。所述催化裂化装置还可以包括再生器7,汽提后的积炭催化剂,通过催化剂输送通路62在待生催化剂流量控制阀63的控制下输送至再生器7;再生的裂化催化剂可以通过输送管11在再生催化剂流量控制阀12的控制下输送至第一提升管反应器1,也可以通过输送管21在再生催化剂流量控制阀22的控制下输送至第一提升管反应器2,以对再生的裂化催化剂进行循环利 用。以下结合图1对本发明提供的所述多产丁烯和轻芳烃的烃类催化转化方法进行进一步说明,但并不因此限制本发明。图1中示出了实施本发明方法的催化裂化装置的一种具体实施方式,虽然该示意图为简化流程,但这并不影响本领域技术人员对本发明的理解。具体地,该催化裂化装置包括提升管反应器1(第一反应器)、提升管反应器2(第二反应器)、流化床反应器3(第三反应器)、汽提器4、沉降器5、汽提器6和再生器7。沉降器4与汽提器6同轴,其中汽提器6位于沉降器5的下方。汽提器4、提升管反应器2和流化床反应器3同轴,其中汽提器4位于流化床反应器3的下方,提升管反应器2的出口和流化床反应器3的底部任意位置连通。提升管反应器1的末端与快速分离器51的入口连通,流化床反应器3的末端与快速分离器53的入口连通。汽提器4通过通道41与汽提器6连通。流化床反应器3的催化剂料位通过催化剂流量控制阀42的开度进行调节。重质烃类原料预热至180-340℃后,与水蒸气一起通过喷嘴13喷入提升管反应器1,在温度为450-540℃(优选为490-530℃)、绝压为0.15-0.30MPa(优选为0.18-0.28MPa)、催化剂与重质烃类原料的重量比为4-15、油气停留时间为0.1-5s(优选为1-4s)的条件下,与由来自管线11的热的再生裂化催化剂接触并反应。反应物流和催化剂通过快分装置51和单级旋风分离器52分离,分离的积炭催化剂进入汽提器6,分离得到的反应油气物流引入分馏装置。来自本发明分馏装置的轻裂解汽油在540-620℃、反应区绝压为0.15-0.3MPa、剂油重量比为15-100:1、油气停留时间为0.1-3s的条件下在提升管反应器2的下部与裂化催化剂接触并反应。来自本发明分馏装置的裂解轻油在经过加氢改质后,在520-600℃、快速分离器51的入口连通,反 应区绝压为0.15-0.30MPa、注入流化床反应器3的底部,与来自第二反应器的反应混合物一起在流化床反应器3中继续反应。为了提高丁烯和轻芳烃的产率,本发明优选将分馏装置得到的富含烯烃的轻裂解汽油馏分(终馏点不超过85℃,优选为70-75℃),在反应温度为20-90℃、绝压为0.2-1MPa、氢气和烯烃的摩尔比为1-5:1的条件下,在含镍催化剂上经过选择性加氢反应将二烯烃和炔烃转化为烯烃后,通过喷嘴23喷入提升管反应器2底部,与来自管线21的热的再生裂化催化剂接触并反应。喷嘴23的位置位于提升管反应器2的预提升段的上方。本发明还优选将分馏装置得到的裂解轻油在反应温度为300-450℃、氢分压为5-16MPa、体积空速为0.3-2h-1、氢油体积比为800-1500:1的条件下进行加氢处理,将其中的双环芳烃和三环芳烃饱和,加氢处理后的中质烃类原料通过喷嘴31喷入流化床反应器3的底部,与来自提升管反应器2的反应物流一起在温度为520-600℃(优选为540-590℃)、绝压为0.15-0.30MPa(优选为0.18-0.28MPa)、重时空速为0.2-30h-1(优选为2-20h-1)、油气空塔线速为0.2-1.5m/s(优选为0.6-1.2m/s)的条件下反应。在流化床反应器3内反应后,携带部分催化剂的油气进入快速分离器53和单级旋风分离器54,催化剂与油气分离,催化剂进入汽提器6,分离掉催化剂的油气进入分馏装置。在分馏装置得到气体(包括二氧化碳、一氧化碳、干气和液化气)、轻汽油、富含轻芳烃重汽油、柴油和重油。气体产品通过本领域技术人员熟知的分离技术,得到丙烯、丁烯等低碳烯烃。待生催化剂在汽提器,6(其中设置有挡板61)中汽提出吸附的烃类产物,由管线62送至再生器7进行再生,再生后热的再生裂化催化剂返回到提升管反应器重复使用。反应油气离开流化床床层时温度还很高,为抑制目标产物发生二次反应,通过喷嘴32在流化床的稀相空间喷入冷却介质含油污水,将反应油气温度降至480-540℃。下面的实施例将对本方法予以进一步的说明,但并不因此限制本发明。以下实施例在中型试验装置上进行,其流程如图1所示,其中提升管反应器1的内径(直径)是18毫米,高度6米,提升管反应器2的内径(直径)是12毫米,高度5米,流化床反应器3出口处的内径64毫米,高度0.2米~0.5米,沉降器内径300毫米。实施例1本实施例中使用的裂化催化剂为:以裂化催化剂的总重量为基准,所用裂化催化剂含有10重量%的β沸石、20重量%的ZSM-5沸石(硅铝比为40)、45重量%的高岭土和25重量%的氧化铝粘结剂,其中,β沸石中含以元素计1重量%的铁和1.5重量%的磷。裂化催化剂于800℃、100%水蒸汽气氛下老化10小时,装置中催化剂的装量(系统催化剂藏量)为60千克。将重质烃类原料(其性质如表1所示)引入提升管反应器1,与来自再生器7的热催化剂接触反应后,反应油气与催化剂分离,反应油气离开反应器引入分馏装置,分离得到的积炭催化剂引入汽提器6,经过汽提后输送到再生器7进行再生,反应油气引入分馏系统;轻裂解汽油馏分(组成见表2,该轻汽油馏程为35-75℃)引入提升管反应器2的底部,与来自再生器的热催化剂接触反应;加氢改质的裂解轻油馏分(组成见表3,该裂解轻油馏分馏程为240-365℃)注入床层反应器3的底部,与来自第二反应器的反应油气一起与催化剂接触反应,油气和催化剂经过流化床反应器3的出口,经过沉降,大部分催化剂落入流化床床层。而携带部分催化剂的油气进入快速分离器53和单级旋风分离器54,催化剂与油气分离,积炭催化剂进入汽提器6,分离掉催化剂的油气进入分馏装置。积炭催化剂经过汽提后输送到再生器进行再生。引入提升管反应器2的轻裂解汽油量与引入提升管反应器1的重质烃类原料的重量之比为0.15,引入流化床反应器3的加氢改质裂解轻油 馏分与引入提升管反应器1的重质烃类原料的重量之比为0.15,反应条件以及反应结果见表4。实施例2本实施例的流程和使用的裂化催化剂同实施例1,不同的是,轻裂解汽油(性质见表2)于反应温度40℃、反应压力0.5MPa、氢气和烯烃的摩尔比为4:1下,在加氢催化剂(购自中石化长岭催化剂分公司,牌号为RDD-1)上经过选择性加氢反应,将二烯烃和炔烃转换成单烯烃后引入提升管反应器2,其余反应条件以及反应结果见表4。对比例1该反应装置为传统的DCC反应器型式,即提升管+床层反应器,提升管反应器位于流化床反应器的下方。将重质烃类原料(其性质如表1所示)引入提升管反应器1,与来自再生器的热催化剂接触反应轻汽油馏分(组成见表2,该轻汽油馏程为35-75℃)引入提升管反应器的中部,与来自上游的热催化剂接触反应;加氢改质的裂解轻油馏分(组成见表3,该柴油馏分馏程为240-365℃)引入流化床反应器3的底部,与催化剂接触反应;反应油气和催化剂引入流化床反应器继续反应,油气和催化剂经过流化床反应器的出口,油气进入沉降器,通过两级旋风分离器分离掉其中携带的催化剂,催化剂与油气分离,积炭催化剂进入汽提器,分离掉催化剂的油气进入分馏装置。积炭催化剂经过汽提后输送到再生器进行再生。引入提升管反应器轻裂解汽油总量与引入提升管反应器1的重质烃类原料的重量之比为0.15,引入流化床反应器的加氢裂解馏分与引入提升管反应器1的重质烃类原料的重量之比为0.15,反应条件以及反应结果见表5。实施例3本实施例的流程同实施例1,不同的是,使用的裂化催化剂为:以裂化催化剂的总重量为基准,所用裂化催化剂含有15重量%的β沸石、15重量%的ZSM-5沸石(硅铝比为40)、45重量%的高岭土和25重量%的氧化铝粘结剂,其中,β沸石中含以元素计1重量%的铁和1.5重量%的磷;而且,反应条件以及反应结果见表6。实施例4本实施例的流程同实施例1,不同的是,在流化床反应器3的上部注入冷却介质(水蒸气),将流化床出口反应油气的温度降低至490℃;而且,反应条件以及反应结果见表6。表1表2轻裂解汽油馏分组成重量%烷烃32烯烃61环烷烃3芳烃2二烯烃和炔烃含量2表3加氢改质的裂解轻油馏分组成重量%链烷烃23.5一环烷烃9.5二环烷烃45.7三环烷烃9.7总环烷烃64.9烷基苯4.8茚满或四氢萘3.9茚类1.5总单环芳烃10.2萘0.2萘类0.6苊类0.3苊烯类0.1总双环芳烃1.2三环芳烃0.2总重量100表4表5表6*表4-6中,A指提升管反应器1,B指提升管反应器2,C指流化床反应器3。*表4-6中,剂油比是指催化剂与反应器进料的重量比。物料平衡是以重质烃类原料为基准计算得到的,丁烯产率是以产物中的丁烯重量除以重质烃类原料的重量得到的,轻芳烃产率以产物中的轻芳烃重量除以重质烃类原料的重量得到的。*表4-6中,反应压力是指沉降器出口压力。由表4-6的数据可见,根据本发明所述的方法可以获得较高的丁烯产率和轻芳烃产率。当前第1页1 2 3