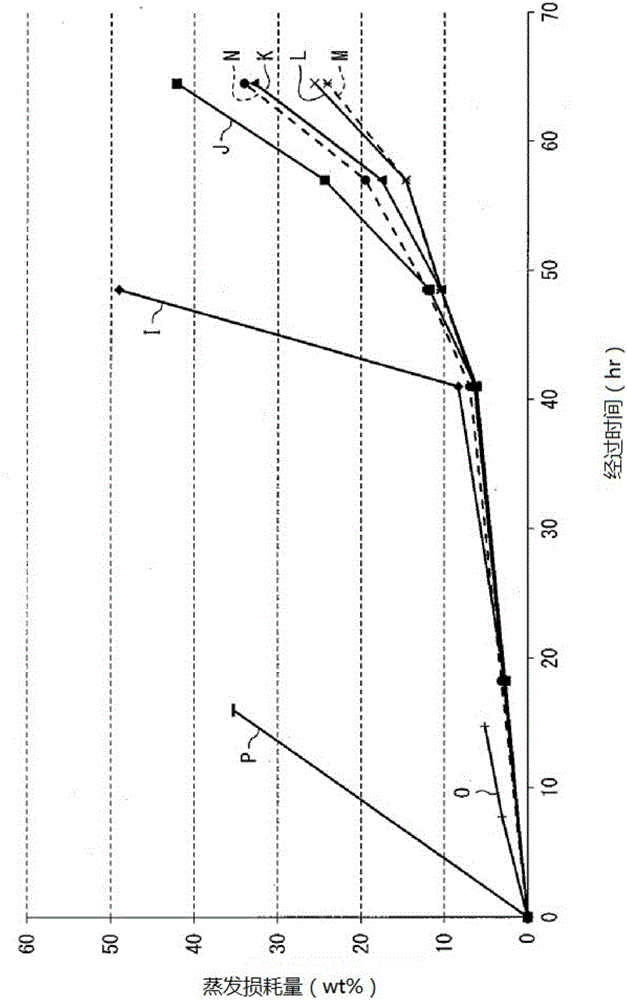
本发明是关于一种润滑剂组合物及其利用、以及脂肪族醚化合物,特别是关于一种具有较高耐湿性、且具有低粘度、低蒸发性、低温流动性及高粘度指数等的物理特性的润滑剂组合物及其利用、以及一种能够较佳地应用于所述润滑剂组合物的脂肪族醚化合物。
背景技术:
:使用高粘度的润滑剂组合物时,会产生由粘性引起的能量损耗的增大、润滑剂组合物的搅拌损失的增大等的不利情况。近年来,在润滑油领域中,为了消除所述不利情况、达到节能的目的,行业中一直在谋求润滑剂组合物的低粘度化。但是,低粘度化的润滑剂组合物,特别是在高温环境下被使用时,会发生润滑剂组合物蒸发损耗的问题。为了解决相关问题,行业中对于能够满足低蒸发性要求的低粘度原油的需求性越来越高。作为低粘度且蒸发量较少的润滑油原油,酯系原油被广泛悉知。但是,酯系原油具有耐湿性差的问题。也就是说,酯系原油在长时间的使用后,由于空气中的水分被加水分解而形成酸,生成的酸成为使金属腐蚀的因素。并且,酯系原油由于其极性较高,会对橡胶、塑料等的有机材料带来坏的影响。此外,近年来,影像设备、音响设备、个人电脑等电子装置的小型轻量化、大容量化以及信息处理的高速化取得了显著的进步。与此同时,针对用来驱动应用于这些电子装置的FD、MO、迷你磁盘、紧凑磁盘、DVD、硬盘等的磁碟或光碟的旋转装置,业界正在开发液体轴承并实用化之。由于没有滚珠轴承,由通过润滑剂对向设置的套筒部件和旋转轴构成的液体轴承,不仅有利于电子装置的小型·轻量化,低噪音性、经济性等的性能也较佳。对应用于这样的液体轴承的润滑油来说,要求其具有在低温区域具有较低的粘度、低温流动性良好的同时,在高温区域也较少发生粘度低下的粘度特性以及低蒸发性。如此,在润滑油领域,针对具有高耐湿性、并且具有低粘度、低蒸发性、低温流动性及高粘度指数等物理特性的润滑油原油或润滑剂组合物的需求越来越强烈。此外,为了提高润滑油的性能,一般会在润滑油中添加抗氧化剂等的添加剂。例如,专利文献1揭示:为了提高润滑剂的热稳定性和抗氧化性、抗酸碱性、润滑性、长寿命性以及水隔离性,使原油中含有苯-α-萘胺、p,p’-二烷基酯-二苯胺及磷酸盐酯。并且,专利文献2揭示了一种钟表用润滑油,其可在-30℃-80℃的范围内工作、长时间也不会变质,可以长期保持电池的寿命,且含有适合作为钟表用润滑油的润滑剂组合物、作为原油的乙醚油、耐磨剂以及抗氧化剂。引用列表专利文献【专利文献1】日本公开专利公报「特開2010-150562号公報(2010年7月8日公開)」【专利文献2】WO2001/059043号公報(2001年8月16日公開)技术实现要素:发明所要解决的技术问题但是,现有的润滑剂组合物在高耐湿性、低粘度、低蒸发性、低温流动性及高粘度指数等的物理特性方面不够充分。鉴于上述问题,本发明的目的在于提供一种具有高耐湿性、且具有低粘度、低蒸发性、低温流动性及高粘度指数等的物理特性的润滑剂组合物及其利用技术、以及能很好地应用于所述润滑剂组合物的脂肪族醚化合物。解决问题所采用的手段为了解决上述课题,本发明提供的润滑剂组合物,其以脂肪族醚化合物为原油且含有抗氧化剂,该抗氧化剂至少由烷基化苯萘胺和亚磷酸酯构成,所述润滑剂组合物中所含有的所述烷基化苯萘胺和所述亚磷酸酯的合计量相对于所述原油的总量为3~8重量%;相对于所述烷基化苯萘胺和所述亚磷酸酯,所述烷基化苯萘胺和所述亚磷酸酯的含有比例分别是烷基化苯萘胺为85~95重量%、亚磷酸酯为5~15重量%。此外,本发明提供的润滑剂组合物中,所述脂肪族醚化合物为单分子中的碳原子数为8~300、单分子中的氧原子数为1~150的脂肪族醚化合物。此外,本发明提供的润滑剂组合物中,所述脂肪族醚化合物为2-(2-乙基己基氧基)乙基醚化合物。此外,本发明提供的润滑剂组合物中,所述脂肪族醚化合物为从具有下述化学式(1)~(10)所表示的结构的化合物构成的群中选择的至少一种。【化学式1】【化学式2】【化学式3】【化学式4】【化学式5】【化学式6】【化学式7】【化学式8】【化学式9】【化学式10】此外,本发明提供的润滑剂组合物中,所述烷基化苯萘胺为N-苯基-十二烷基萘-1-胺或者N-苯基-辛基萘-1-胺。此外,本发明提供的润滑剂组合物中,所述亚磷酸酯为1,1,3-三(2-甲基-4-二十三烷基苯酯亚磷酸酯-5-t-丁基苯基)丁烷。本发明还提供一种轴承润滑油,其使用了本发明上述的润滑剂组合物。本发明还提供一种轴承,其使用本发明上述的润滑剂组合物被润滑。本发明还提供一种轴承,所述轴承为液体轴承或者浸渍轴承。本发明还提供一种发动机,其具有本发明上述的轴承。本发明还提供一种轴承的润滑方法,其采用本发明上述的润滑剂组合物对轴承进行润滑。本发明还提供一种润滑剂组合物的使用,其是关于为了制造润滑脂的使用。本发明还提供一种润滑脂,其含有本发明上述的润滑剂组合物。本发明还提供一种冷冻机油,其含有本发明上述的润滑剂组合物。本发明还提供一种脂肪族醚化合物,其具有用下述化学式(1)~(9)的任意一项所表示的结构。【化学式11】【化学式12】【化学式13】【化学式14】【化学式15】【化学式16】【化学式17】【化学式18】【化学式19】发明的效果根据本发明的技术方案,可以实现具有高耐湿性,并且具有低粘度、低蒸发性、低温流动性以及高粘度指数等的物理特性的润滑剂组合物。图式的简单说明图1是本发明的参考例1-3以及比较例1-5中调制的润滑剂组合物的蒸发损耗量的测定结果的示意图。图2是本发明的实施例1-2以及比较例6-10中调制的润滑剂组合物的蒸发损耗量的测定结果的示意图。图3是本发明的实施例3-8以及比较例15-16中调制的润滑剂组合物的蒸发损耗量的测定结果的示意图。图4是本发明的实施例9-14中调制的润滑剂组合物的蒸发损耗量的测定结果的示意图。图5是本发明的实施例15-17以及比较例17-21中调制的润滑剂组合物的蒸发损耗量的测定结果的示意图。图6是本发明的实施例18-19中调制的润滑剂组合物的蒸发损耗量的测定结果的示意图。图7是本发明的实施例18、20-22以及比较例22-24中调制的润滑剂组合物的蒸发损耗量的测定结果的示意图。图8是本发明的制造例1所获得的化合物1的1H-NMR表的示意图。图9是本发明的制造例3所获得的化合物3的1H-NMR表的示意图。图10是本发明的制造例5所获得的化合物5的1H-NMR表的示意图。图11是本发明的制造例6所获得的化合物6的1H-NMR表的示意图。图12是本发明的制造例10所获得的化合物10的1H-NMR表的示意图。具体实施方式以下,对本发明的实施方式进行详细说明,但本发明不限于该实施方式,本发明可以在该实施方式记载的范围内进行各种各样的变形并得以实施。此外,本说明书中记载的所有学术文献以及专利文献仅作为参考而引用。此外,本说明书中除特别记载之外,表示数值范围的「A~B」意思是「A以上、B以下」。以下,按照(1)本发明的润滑剂组合物、(2)本发明的润滑剂组合物的利用、(3)本发明的脂肪族醚化合物的顺序对本发明进行说明。(1)本发明涉及的润滑剂组合物本发明的发明人鉴于上述课题,锐意研究,结果获得了以脂肪族醚化合物为原油,至少将由烷基化苯萘胺和亚磷酸酯构成的抗氧化剂,所述烷基化苯萘胺和亚磷酸酯的合计量相对于所述原油总量为规定的量,所述烷基化苯萘胺和亚磷酸酯的含有比例以规定的比率含有的润滑剂组合物。本发明的发明人发现,根据该润滑剂组合物,可以提供具有高耐湿性、且具有低粘度、低蒸发性、低温流动性及高粘度指数等物理特性的润滑剂组合物,从而完成了本发明。在各种各样的原油中,所述烷基化苯萘胺和亚磷酸酯的高结合效应为在脂肪族醚化合物中所能看到的特有的效果。〔原油〕本发明的润滑剂组合物以脂肪族醚化合物为原油而使用。本发明的发明人,同时使用烷基化苯萘胺和亚磷酸酯作为抗氧化剂时,发现可以显著地降低蒸发损耗量。并且,发现所述高结合效应是在各种各样的原油中,脂肪族醚化合物所特有的效果。也就是说,将脂肪族醚化合物作为原油使用时,在带来显著的低蒸发性的基础上,可以得到烷基化苯萘胺和亚磷酸酯的高结合效应。此外,由于脂肪族醚化合物被空气中的水分水解,而不会生成酸,因此具有优越的耐湿性。进一步地,由于脂肪族醚化合物与酯系原油相比,极性较低,因此不会对橡胶、塑料等的有机材料造成不良影响。本发明中作为原油被使用的脂肪族醚,并没有被特别限制,可以适当地利用作为润滑剂的原油被常用的脂肪族醚。优选地,所述脂肪族醚为单分子中的碳原子数为8~300,单分子中的氧原子数为1~150的脂肪族醚。单分子中的碳原子数以及单分子中的氧原子数在所述范围内的话,粘性、低蒸发性以及低温流动性间的平衡较为良好,可以达到满意的效果。并且,更优选地,所述脂肪族醚的单分子中的碳原子数在8~80、氧原子数在1~40的范围内。特别优选地,所述脂肪族醚的单分子中的碳原子数在8~60、氧原子数在1~30的范围内。最优选地,所述脂肪族醚的单分子中的碳原子数在8~40、氧原子数在1~20的范围内。其中,较佳地是,所述脂肪族醚为具有下述通式(11)表示的结构的2-(2-乙基己基氧基)乙醚化合物。【化学式20】通式(11)中,R1表示碳原子数为1~18的烷基,R2表示碳原子数为2~18的烯基,n表示平均值为1~6的整数。在此,(R2-O)的每个构成单位可以相同也可以不同。R1和R2可以是直链状也可以是分支状。如果R1的碳原子数在1以上,也就是说该醚化合物中,分子结构的末端不是羟基,而是烷氧基的话,隔水性变好,因此令人满意。如果R1的碳原子数在18以下,不会严重地损坏低温流动性,因此令人满意。此外,如果R2的碳原子数在2以上,由于成为不包含缩醛结构的醚,耐湿性和耐路易斯酸性优异,因此令人满意。如果R2的碳原子数在18以下,不会严重地损坏低温流动性,因此令人满意。优选地,R1的碳原子数为1~12。更优选地,R1的碳原子数为2~8。此外,优选地,R2的碳原子数为2~12。更优选地,R2的碳原子数为2~8。n的平均值为1~6的话,粘性、低蒸发性、低温流动性间的平衡性较佳,因此令人满意。优选地,n的平均值为1~4。更优选地,n的平均值为1~2。作为更具体的一个例子,优选地,所述脂肪族醚为从具有用所述化学式(1)~(10)所表示结构的化合物所构成的群中选择的至少一种。并且,本说明书,将具有用化学式(1)表示结构的化合物称为化合物1,将具有用化学式(2)表示结构的化合物称为化合物2,将具有用化学式(3)表示结构的化合物称为化合物3,将具有用化学式(4)表示结构的化合物称为化合物4,将具有用化学式(5)表示结构的化合物称为化合物5,将具有用化学式(6)表示结构的化合物称为化合物6,将具有用化学式(7)表示结构的化合物称为化合物7,将具有用化学式(8)表示结构的化合物称为化合物8,将具有用化学式(9)表示结构的化合物称为化合物9,将具有用化学式(10)表示结构的化合物称为化合物10。本发明中作为原油,可以单独使用上述脂肪族醚,也可以使用上述脂肪族醚的两种以上的组合。并且,本发明相关的润滑剂组合物以脂肪族醚化合物为原油而使用,只要在不对本发明的效果造成不利影响的前提下,也可以少量含有脂肪族醚化合物以外的原油。优选地,所述脂肪族醚化合物以外的原油的含量相对于原油总量在10重量%以下。更优选地,所述脂肪族醚化合物以外的原油的含量相对于原油总量在5重量%以下。所述脂肪族醚的制造方法没有被特别限定,可以通过任何的制造方法来获得脂肪族醚。例如,所述脂肪族醚可以通过使乙烯氧化物和环氧丙烷等的烯化氧聚合而制造得到。并且,所述脂肪族醚通过由上述方法得到的聚亚烷基氧化物和烷基氯的置换反应,将该聚亚烷基氧化物的末端羟基乙醚化而制造得到。或者,所述脂肪族醚可以利用市售商品。例如,可以适当地使用ADEKA股份有限公司(ADEKACorporation)的ADEKACARPOLM系列、第一工业制药股份有限公司(Dai-ichiKogyoSeiyakuCo.,Ltd.)的NOIGENXL-40等的NOIGENXL系列、NOIGENTDS-30等的NOIGENTDS系列、NOIGENTDX-50等的NOIGENTDX系列、NOIGENSD-60等的NOIGENSD系列、NOIGENLP-100等的NOIGENLP系列以及ANTI-FROTHF-233等。并且,所述化合物1-10的制造方法也没有被特别限定,例如,作为其中的一个例子,可以通过WO2006/025253号公报等记载的现有的合成方法来制造。更具体地,例如,化合物1可以通过2-乙基己基氧基乙基乙醇和1,6-二氯己烷的醚化反应来得到。并且,例如,化合物3可以通过2-(2-乙基己基氧基)乙基乙醇和1,6-二氯己烷的醚化反应,从而合成6-[2-(2-乙基己基氧基)乙氧基]-己基氯化物,利用减压蒸馏将其作为中间体来分离提纯,通过该中间体与2-丁基辛醇的醚化反应而制得。并且,例如,化合物4、化合物5以及化合物6可以通过与化合物3的合成方法相同的手法,代替2-丁基辛醇,分别采用对应的乙醇,进行醚化反应而合成得到。并且,例如,化合物2、化合物7、化合物8以及化合物9可以通过与化合物3的合成方法相同的手法,替代1,6-二氯己烷,使用1,4-二氯己烷,合成4-[2-(2-乙基己基氧基)乙氧基]-丁基氯化物,利用减压蒸馏将其作为中间体来分离提纯,分别采用与该中间体对应的乙醇进行醚化反应而合成得到。但是,化合物1-10的合成方法并不限定于上述方法。在充分地进行了上述醚化反应后,通过采用公知的方法(例如,利用减压蒸馏或硅胶柱层析法的分离等)对生成物进行适当地提炼,可以将化合物1-10作为润滑剂的原油使用。〔抗氧化剂〕本发明的润滑剂组合物中,以脂肪族醚化合物为原油,抗氧化剂至少含有烷基化苯萘胺和亚磷酸酯,所述烷基化苯萘胺和所述亚磷酸酯的合计量相对于所述原油总量为规定的量,并且所述烷基化苯萘胺和所述亚磷酸酯的含有比例为规定的比例。作为抗氧化剂,通过合用烷基化苯萘胺和亚磷酸酯,可以使两者起到协同性的作用,从而达到促进低蒸发性的效果。并且,通过合用烷基化苯萘胺和亚磷酸酯,也可以达到使抗氧化效果的持续时间更长的效果。<烷基化苯萘胺>本发明所使用的烷基化苯萘胺,换句话说,如果被置换了烷的苯萘基胺是苯萘基胺的苯基以及萘基的至少任意一个用烷基被置换的化合物的话即可,没有被特别地限制,例如可以适当地使用具有下述通式(12)表示的结构的烷基化苯α萘基胺:【化学式21】或者具有用下述通式(13)表示的结构的烷基化苯β萘基胺:【化学式22】通式(12)以及通式(13)中,R3以及R4各自独立,表示直链状或者分支状的碳原子数为1~18的烷基。l为0~5的整数,m为0~7的整数,l+m在1以上。如果R3和R4为碳原子数为4~18的烷基的话,对脂肪族醚化合物的溶解性增高,并且由于烷基化苯萘胺自身不易蒸发,因此比较理想。更具体地来说,例如,R3可以列举甲基、乙基、丙基、丁基、戊基、己基、庚基、辛基、壬基、癸基、十一烷基、十二烷基、十三烷基、十四烷基、十五烷基、十六烷基、十七烷基、十八烷基等的烷基。该些烷基可以是直链状,也可以是分支状。优选地,R3为碳原子数为4~18的烷基。特别优选地是,R3为碳原子数为4~12的烷基。置换基数l为2以上时,2以上的R3可以各自相同,也可以不同。并且,R3的置换位置也没有被特别限定。l可以是0~5的整数。优选地,l为0~2。更优选地,l为0~1。此外,作为R4来说,例如,也可以列举甲基、乙基、丙基、丁基、戊基、己基、庚基、辛基、壬基、癸基、十一烷基、十二烷基、十三烷基、十四烷基、十五烷基、十六烷基、十七烷基、十八烷基等的烷基。该写烷基可以是直链状,也可以是分支状。优选地,R4为碳原子数为4~18的烷基。特别优选地是,R4为碳原子数为4~12的烷基。置换基数m为2以上时,2以上的R4可以各自相同,也可以不同。并且,R4的置换位置也没有被特别限定。m可以是0~7的整数。优选地,m为0~2。更优选地,m为0~1。所述通式(12)或者通式(13)表示的化合物中,特别是可以适当地利用R3是碳原子数为4~12的烷基,l是0~1的整数,R4是碳原子数为4~12的烷基,m为0~1的整数,l+m为1以上的烷基化苯萘胺。关于所述烷基化苯萘胺的具体例,例如,可以列举N-苯基-十二烷基萘-1-胺、N-苯基-辛萘基-1-胺、N-苯基-丁萘基-1-胺、N-十二烷基苯-十二烷基萘-1-胺、N-辛苯基-辛萘基-1-胺、N-十二烷基苯-萘基-1-胺、N-辛基苯-萘基-1-胺等。所述烷基化苯萘胺可以利用市售商品。例如,可以适当地使用BASF公司的IRGANOXL06;Chemtura公司的NaugalubeAPAN。<亚磷酸酯>本发明中使用的亚磷酸酯只要是亚磷酸的酯类即可,没有被特别地限定,例如,可以适当地使用具有下述通式(14)表示的结构的第三级亚磷酸酯:【化学式23】或者具有下述通式(16)表示的结构的亚磷酸酯:【化学式24】通式(14)中,R5、R6以及R7各自独立,表示碳原子数为1~18的脂肪族碳化氢基或者碳原子数为4~30的芳香族碳化氢基。此外,通式(16)中,R10、R11、R12、R13、R14、R15、R16、R17以及R18各自独立,表示碳原子数为1~18的脂肪族碳化氢基或者碳原子数为4~30的芳香族碳化氢基,X表示碳原子数为1~18的2价、3价或者4价的脂肪族碳化氢基,n为0、1或者2。R5、R6、R7、R10、R11、R14、R15、R17以及R18为脂肪族碳化氢基的情况下,作为所述脂肪族碳化氢基,例如可以列举甲基、乙基、丙基、丁基、戊基、己基、庚基、辛基、壬基、癸基、十一烷基、十二烷基、十三烷基、十四烷基、十五烷基、十六烷基、十七烷基、十八烷基等的烷基。该些烷基可以是直链状,也可以是分支状。或者,所述脂肪族碳化氢基不限定于所述烷基,也可以是不饱和的脂肪族碳化氢基。R12、R13以及R16为脂肪族碳化氢基的情况下,作为所述脂肪族碳化氢基,例如,可以列举碳原子数为1~18的烯基,该些烯基可以是直链状,也可以是分支状。或者,所述脂肪族碳化氢基不限定于所述烯基,也可以是不饱和的脂肪族碳化氢基。R5、R6、R7、R10、R11、R14、R15、R17以及R18为芳香族碳化氢基的情况下,作为所述芳香族碳化氢基,例如,可以列举苯基、烷基化苯基等。所述烷基化苯基是直链状或者分支状的碳原子数为1~18的烷基,且苯环的至少1~5个氢原子被置换的苯基即可。被置换烷基的苯环的位置也没有被特别限定。并且,置换基数在2以上时,2以上的烷基可以分别是同一东西,也可以不同。R12、R13以及R16为芳香族碳化氢基的情况下,所述芳香族碳化氢基可以列举苯基、烷基化苯基等。所述烷基化苯基是直链状或分支状的碳原子数为1~18的烷基,且苯环的至少1~4个氢原子被置换的苯基即可,被置换烷基的苯环的位置也没有被特别地限定。并且,置换基数在2以上时,2以上的烷基可以分别是同一东西,也可以不同。X是2价、3价或者4价的碳原子数为1~18的脂肪族碳化氢基即可,并不受特别限制,可以是饱和脂肪族碳化氢基也可以是不饱和脂肪族碳化氢基,且可以是直链状也可以是分支状。优选地,该脂肪族碳化氢基是碳原子数为1~6的分支状或者直链状的饱和脂肪族碳化氢基。并且,R12、R13以及R16可以结合于该脂肪族碳化氢基的任意的碳原子。作为具有用通式(14)表示结构的亚磷酸酯的更为具体一个例子,可以列举亚磷酸三苯酯、三壬基苯基亚磷酸酯、磷酸三甲酯、亚磷酸三乙酯、三(2-乙基己基)亚磷酸酯、十三烷基亚磷酸酯、三月桂亚磷酸酯、三(十三)亚磷酸酯、三油亚磷酸酯、联苯单(2-乙基己基)亚磷酸酯、联苯单癸亚磷酸酯、联苯单(十三)亚磷酸酯、三硬脂酰亚磷酸酯、三(2,4-二-tert-丁基苯基)亚磷酸酯等。作为具有用通式(16)表示结构的亚磷酸酯的更为具体一个例子,可以列举1,1,3-三(2-甲基-4-二十三烷基苯酯亚磷酸酯-5-t-丁基苯基)丁烷(来自ADEKA股份有限公司的ADKSTAB522A)、四苯基(四十三)季戊四醇-四亚磷酸酯和双(2-乙基己基)邻苯二甲酸酯的混合物、四(C12~C15烷基)-4,4,-异亚丙基二苯基磷酸酯等。进一步地,除了所述通式(14)以及(16)所表示的亚磷酸酯以外,本发明中,三月桂三硫代亚磷酸酯、四苯基二丙二醇磷酸酯、双(十三烷基)季戊四醇二亚磷酸酯和双(壬基苯基)季戊四醇二亚磷酸酯的混合物、双(癸基)季戊四醇二亚磷酸酯、双(十三烷基)季戊四醇二亚磷酸酯、二硬脂酰季戊四醇二亚磷酸酯、氢化双酚A季戊四醇亚磷酸酯聚合物、氢化双酚A磷酸酯聚合物等也可以作为亚磷酸酯被适宜地使用。所述亚磷酸酯可以利用市售商品,例如,可以适当地使用城北化学工业股份有限公司的JP-360、JP-351、JP-3CP、JP-302、JP-308E、JP-310、JP-312L、JP-333E、JP-318-O、JPM-308、JPM-311、JPM-313、JPS-312、JP-202、JPE-208、JP-212、JP-213D、JP-218-OR、JP-260、JPP-100、JPP-613M、JA-805、JPP-88、JPE-10、JPE-13R、JP-318E、JPP-2000T、JP-650、JPH-3800、HBP;ADEKA股份有限公司的ADKSTAB522A等。优选地,所述亚磷酸酯为分子量在300以上的低蒸发性的亚磷酸酯。如果亚磷酸酯的分子量在上述范围的话,由于亚磷酸酯自身不易蒸发,所以可以达到满意的效果。并且,更优选地,所述亚磷酸酯为分子量在400~1000的范围内的亚磷酸酯。特别优选地,所述亚磷酸酯为分子量在500~800的范围内的亚磷酸酯。〔抗氧化剂的添加量〕优选地,本发明的所述润滑剂组合物所含有的烷基化苯萘胺和亚磷酸酯的合计量相对于所述原油总量为3~8重量%。通过将所述烷基化苯萘胺和亚磷酸酯的合计量相对于所述原油的总量设定为3~8重量%,可以达到润滑剂组合物的蒸发损耗量较小,并且截止蒸发损耗量的上升突然出现坡度的时间较长的效果。此外,通过将所述烷基化苯萘胺和亚磷酸酯的合计量相对于所述原油的总量设定为8重量%以下,可以抑制粘度的上升,并且可以获得热稳定性优良的润滑剂组合物。此外,优选地,所述烷基化苯萘胺和所述亚磷酸酯各自的含有比例相对于烷基化苯萘胺和亚磷酸酯的合计量,烷基化苯萘胺为85~95重量%,亚磷酸酯为5~15重量%。所述烷基化苯萘胺和所述亚磷酸酯的含有比例在上述范围内的话,在减小润滑剂组合物的蒸发损耗量方面和延长抗氧化效果的持续时间方面,可以取得显著的效果。此外,本发明的润滑剂组合物中,抗氧化剂使用烷基化苯萘胺和亚磷酸酯,但是只要在不对本发明的效果造成不利的影响的前提下,也可以少量含有烷基化苯萘胺和亚磷酸酯以外的抗氧化剂。所述烷基化苯萘胺和亚磷酸酯以外的抗氧化剂相对于抗氧化剂总量在10重量%以下时较为理想,在5重量%以下的话更为理想。〔其他的添加剂〕本发明的润滑剂组合物,在所述原油和所述抗氧化剂的基础上,为了进一步提高实用性能,可以混合各种添加剂。所述添加剂可以例举金属钝化剂、防腐剂、导电性赋予剂等。所述金属钝化剂,可以适当地使用苯并三唑、5-甲基-1H-苯并三唑、1-二辛基氨基甲基苯并三唑、1-二辛基氨基甲基-5-甲基苯并三唑、2-(5’-甲基-2’-羟基苯氧)苯并三唑、2-[2’-羟基-3’,5’-二(α、α-二甲基苄基)苯基]-2H-苯并三唑、2-(3’,5’-二-t-丁基-2’-羟基苯基)苯并三唑、2-(3’-t-丁基-5’-甲基-2’-羟基苯基)-5-氯苯并三唑、2-(3’,5’-二-t-丁基-2’-羟基苯基)-5-氯苯并三唑、2-(3’,5’-二-t-戊基-2’-羟基苯基)氯苯并三唑、2-(5’-t-丁基-2’-羟基苯基)-苯并三唑、2-(2’-羟基-5’-甲基苯基)苯并三唑、2-(2’-羟基-5’-t-辛基苯基)苯并三唑、2-[2’-羟基-3’-(3",4",5",6"-四氢苯乙)-5’-甲基苯氧]苯并三唑等。此外,所述防腐剂可以适当地使用烯基琥珀酸半酯、十八烷基琥珀酸酐、烯基琥珀酰胺等的烷基或烯基琥珀酸衍生物;脱水山梨醇单油酸酯、甘油单油酸酯、季戊四醇单油酸酯等的多元醇部分酯;Ca-石油磺酸钙、Ca-烷基苯磺酸盐、Ba-烷基苯磺酸盐、Mg-烷基苯磺酸盐、Na-烷基苯磺酸盐、Zn-烷基苯磺酸盐、Ca-烷基萘磺酸盐等的金属磺酸盐;松香胺、N-油酰肌氨酸等的胺类等。此外,所述导电性赋予剂可以适当地使用烷基磺酸酯、山梨醇酐脂肪酸酯、聚氧乙烯脱水山梨醇脂肪酸酯、聚氧乙烯烷基醚、聚氧乙烯烯基醚等。本发明通过将从上述添加剂中所选择的一种或者两种以上,分别相对于润滑剂组合物的总量以0.01重量%~1重量%的范围混合,可以进一步地提高润滑剂组合物的实用性。〔润滑剂组合物〕通过上述组成,本发明的润滑剂组合物具有低粘度、低蒸发性、低温流动性以及高粘度指数等的物理特性的基础上,可以抑制由于水解造成的金属腐蚀,且针对有机材料的不良影响较少。并且,在抗氧化剂效果的持续时间较长这方面也特别突出。优选地,本发明的润滑剂组合物的40℃的运动粘度(以下,也称40℃运动粘度)在4cSt~10004cSt的范围内。更优选地,所述40℃运动粘度在6cSt~30cSt的范围内。40℃运动粘度在上述范围的话,作为轴承润滑油,可以获得特别优异的润滑性和节能性。此外,优选地,本发明的润滑剂组合物的粘度指数在80以上。更优选地,本发明的润滑剂组合物的粘度指数在110以上。并且,优选地,本发明的润滑剂组合物的流动点在-5℃以下。更优选地,本发明的润滑剂组合物的流动点在-40℃以下。在这种情况下,作为轴承用润滑剂,低温下的粘度特性可以变得特别优异。此外,本说明书的「40℃的运动粘度」、「粘度指数」以及「流动点」可以根据后述实施例所示的方法被测定。(2)本发明的润滑剂组合物的利用〔轴承润滑油〕本发明的润滑剂组合物,可以作为所有通过润滑剂被润滑的轴承的润滑油被使用。因此,本发明也包含使用了本发明的润滑剂组合物的轴承润滑油。例如,本发明的润滑剂组合物可以作为所有具有轴部件和轴承部件(套筒件),该轴部件与该轴承部件通过微小间隙可旋转地装配,为了在该微小间隙中形成润滑膜而在该微小间隙内容纳工作液(轴承润滑油),上述轴部件和轴承部件通过上述润滑膜相对滑动运动的所有轴承的润滑油被适宜地使用。此类轴承一般被称作「滑动轴承」。进一步地,本发明的润滑剂组合物还可以作为液体轴承(液体动压轴承或静压轴承)用的轴承润滑油或者浸渍轴承(「也叫做含油轴承」)用的润滑油被适当地使用。〔轴承〕本发明的轴承使用上述本发明的润滑剂组合物被润滑。本发明的轴承如果是采用上述本发明的润滑剂组合物被润滑的轴承的话,其构成不被特别限定。此外,上述「使用本发明的润滑剂被润滑」的意思是指借由本发明的润滑剂使对向设置的部件之间相对滑动运动。此类轴承可以例举液体轴承、浸渍轴承等。在这里,上述「液体轴承」不具备滚珠轴承等的结构,而具有轴部件(或推力板)和套筒件,该轴部件(或推力板)与该套筒件通过微小间隙可旋转地装配,为了形成润滑膜而在该微小间隙内容纳工作液(润滑剂组合物),上述轴部件(或推力板)与上述套筒件通过上述润滑膜被保持在相互不直接接触的状态。如果是现有公知的液体轴承的话,其构成没有被特别限定。液体动压轴承当中,在轴部件以及套筒件的任何一方或者双方上设置动压产生槽,该轴部件通过动压被支撑的液体轴承以及为了相对于轴部件的旋转轴在垂直方向产生动压而设置有推力板的液体轴承等尤其应当被称作液体动压轴承。本发明的轴承包括所述的液体动压轴承。上述液体动压轴承中,轴部件(或推力板)不旋转的时候不产生动压。因此,轴部件(或推力板)不旋转的时候,套筒件和轴部件(或推力板)部分接触或者全面接触。与此相对,轴部件(或推力板)旋转的时候,通过其旋转而产生动压。基于这个原因,套筒件和轴部件(或推力板)呈现非接触状态。也就是说,液体动压轴承中,套筒件和轴部件(或推力板)始终重复接触或者非接触状态。从而,传统的液体动压轴承中,套筒件与轴部件(或推力板)之间会发生金属磨损,旋转时由于套筒件与轴部件(或推力板)瞬时接触而出现烧溶附着的情况。进一步地,由于轴承上容易蓄积静电,会对磁盘等重要的电子元件产生静电破坏。但是,本发明的液体动压轴承由于使用本发明的润滑剂组合物被润滑,因此很难产生这样的金属磨损或烧溶附着,并且套筒件与轴部件(或推力板)之间不易蓄积静电。此外,上述「浸渍轴承」是通过在烧结金属、合成树脂等的多孔质的轴部件上含浸本发明的润滑剂组合物而形成。如果是现有公知的浸渍轴承(含油轴承)的话,其构成没有被特别限定。传统的浸渍轴承中,轴承部件与轴部件之间会发生金属磨损,轴部件旋转的时候,由于轴承部件与轴部件的瞬时接触会出现烧溶附着的现象。而且,由于轴承上容易蓄积静电,会出现对磁盘等重要的电子元件产生静电破坏的情况。但是,本发明的浸渍轴承由于使用本发明的润滑剂组合物被润滑,因此很难发生此类金属磨损或烧溶附着,并且轴承部件与轴部件之间不易蓄积静电。如上所述,本发明的润滑剂组合物相较于现有的轴承用润滑剂,具有高耐湿性且可以满足低粘度、低蒸发性、低温流动性以及高粘度指数等的物理特性,且该些性能之间的平衡性较佳。因此,将本发明的润滑剂组合物作为工作液来使用的本发明的轴承可以长期保持高速旋转时的稳定性及持久性等,且可以成为节能性优异的轴承。因此,本发明的轴承可以作为用于影像·音响设备、个人电脑等的要求小型·轻量化、大容量化以及信息的高速处理化的电子产品的旋转装置等的轴承被有效地利用。〔发动机〕本发明的发动机具备本发明的轴承。本发明的发动机如果配备本发明的轴承,其他的构造没有特别限定。关于本发明的轴承,如上面[轴承]的项所说明的那样,在此不再赘述。本发明的发动机可以例举个人电脑、音响设备、影音设备、汽车导航等的公知的电子装置所具备的发动机。由于本发明的发动机具备采用本发明的润滑剂组合物被润滑的轴承,因此本发明的发动机相较于现有的发动机不易产生金属磨损及烧溶附着,并且轴承部件与轴部件之间不易蓄积静电。因此,可以长期保持使轴承高速旋转时的稳定性及持久性。其结果是,可以实现发动机的长寿命化。进一步地,本发明的发动机与现有的发动机相比,轴承高速旋转时的节能性特别优异。〔轴承的润滑方法〕本发明的轴承的润滑方法以采用本发明的润滑剂组合物对本发明的轴承进行润滑为特征。关于本发明的润滑剂组合物以及本发明的轴承,分别如上述「(1).本发明的润滑剂组合物」的项以及所述[轴承]的项所说明的那样,因此在此不再赘述。如上所述,本发明的润滑剂组合物,相较于现有的轴承用润滑剂,具有高耐湿性,且能够较平衡地满足低粘度、低蒸发性、低温流动性以及高粘度指数等的物理特性。因此,通过将本发明的润滑剂组合物作为用于润滑轴承的工作液而填充于轴承(特别是液体轴承或浸渍轴承),可以长期保持轴承高速旋转时的稳定性及持久性。其结果是,可以实现轴承的长寿命化。进一步地,还可以提高轴承的节能性。〔润滑酯〕本发明的润滑脂含有本发明的润滑剂组合物。并且,本发明也包括为了制造润滑脂的润滑剂组合物的使用。此外,本发明的润滑剂组合物如上述「(1)本发明的润滑剂组合物」的项所说明的那样,在此不再赘述。本发明的润滑剂组合物相对于润滑脂的总重量的含量优选为50重量%以上,更优选为95重量%以上。本发明的润滑脂在常温下可以是固体,也可以是半固体。并且,通常,为了获得具有期望稠度的润滑脂,本发明的润滑脂中含有所需量的增稠剂。例如,一般情况下,相对于润滑脂的总重量,含有10重量%~40重量%的增稠剂。上述「增稠剂」可以使用润滑脂中通常被使用的增稠剂。例如,可以列举锂皂、钙皂、钠皂、铝皂等,但不限定于该些物质。根据需要,也可以向本发明的润滑脂中混合抗氧化剂、极压剂、防腐剂等的添加剂。通过将该些添加剂分别相对于润滑脂的总重量以0.1重量%~5重量%的比例范围来混合、调配,可以进一步提高润滑脂的实用性。本发明的润滑脂的用途没有被特别限定。本发明的润滑脂可以作为轴承用润滑脂,特别是液体轴承用润滑脂或者浸渍轴承用润滑脂被适当地使用。本发明的润滑脂的制造方法没有被特别限定,可以按照一般的润滑脂的制造方法来制造。本发明的润滑脂作为原油,由于其含有本发明的润滑剂组合物,因此相较于现有的润滑脂,可以成为更切实地且平衡性较佳地满足节能性、高耐湿性、低蒸发性以及低温时的粘度特性等性能的润滑脂。〔冷冻机油〕本发明的冷冻机油含有本发明的润滑剂组合物。此外,关于本发明的润滑剂组合物,如上述「(1)本发明的润滑剂组合物」的项所说明的那样,因此在此不再赘述。本发明的冷冻机油相对于冷冻机油的总重量,优选含有80重量%以上的本发明的润滑剂组合物,更优选含有90重量%以上的本发明的润滑剂组合物。根据需要,可以进一步向本发明的冷冻机油中混合金属钝化剂、防腐剂、导电性赋予剂等的添加剂。该些添加剂分别相对于冷冻机油的总重量以0.01重量%~5重量%的范围来混合。通过这样,可以进一步提高冷冻机油的实用性。本发明的冷冻机油的制造方法没有被特别限定,可以按照一般的冷冻机油的制造方法来制造。由于本发明的冷冻机油作为原油含有本发明的润滑剂组合物,因此相较于现有的冷冻机油,可以更切实地且平衡性较佳地满足节能性、高耐湿性、低蒸发性以及低温时的粘度特性等的性能。(3)本发明的脂肪族醚化合物应用于本发明的润滑剂组合物的脂肪族醚化合物即使作为化合物也含有新颖的物质。因此,所述新颖的化合物也包含于本发明。作为本发明的脂肪族醚化合物,例如,可以例举具有所述化学式(1)~(9)的任意一个所示结构的脂肪族醚化合物。所述脂肪族醚化合物具有高耐湿性,且具有低粘度、低温流动性以及高粘度指数等的物理特性,因此可以作为润滑剂组合物的原油被适当地利用。此外,特别是抗氧化剂使用烷基化苯萘胺和亚磷酸酯的情况下,在各种各样的原油中,可以看到脂肪族醚化合物所特有的低蒸发性的显著效果。优选地,本发明的脂肪族醚化合物的40℃的运动粘度(以下、也称为「40℃运动粘度」)在4cSt~1000cSt的范围内。更优选地,本发明的脂肪族醚化合物的40℃的运动粘度在4cSt~80cSt的范围内。如果40℃运动粘度在上述范围内的话,本发明的以脂肪族醚化合物为原油的润滑剂组合物以及含有该润滑剂组合物的轴承润滑油、润滑脂、冷冻机油的润滑性以及节能性可以变得特别优异。此外,优选地,本发明的脂肪族醚化合物的粘度指数在80以上,更优选地在110以上。并且,优选地,本发明的脂肪族醚化合物的流动点在-5℃以下,更优选地在-40℃以下。在此种情况下,本发明的以脂肪族醚化合物为原油的润滑剂组合物以及含有该润滑剂组合物的轴承润滑油、润滑脂、冷冻机油的低温时的粘度特性变得特别优异。本发明并不限定于以上各个实施方式,本领域技术人员可以在本发明权利要求所示的范围之内进行各种各样的变更、等同替换或者改进,而所有这些改变与变形均应包含在本发明保护的范围之内。此外,将不同的实施方式分别揭示的技术手段进行适当的组合而得到的实施方式也应包含在本发明的技术范围之内。实施例以下,通过实施例对本发明进行更具体的说明,但本发明不限定于各实施例。此外,图中,为了简便,将「重量%」标记为「wt%」,仅标示润滑剂组合物的序号及符号。〔润滑剂组合物的各性能的测定〕润滑剂组合物的各个性能通过以下的方法来测定。<蒸发损耗量>通过180℃下的蒸发性试验,测定蒸发损耗量。具体来说,向材质为SUS304、内径为20mm、高度为35mm的圆筒形试验容器内装入2g的润滑剂组合物,将该圆筒形试验容器放在180℃的带有旋转盘的恒温槽中静置指定时间后,测定润滑剂组合物的重量。通过以下的公式求得蒸发损耗量。并且,将两次测定的平均值作为测定结果。蒸发损耗量(重量%)=(2(g)-静置指定时间后的润滑剂组合物的重量(g))×100/2(g)<原油的65小时后的分解率>将样品10g、水1g、4g的铜系烧结轴承用金属粉末(铜含量为88重量%、锡含量为重量%、铅含量为2重量%)密封入SUS制的耐压容器中,以160℃加热65小时的同时进行搅拌。用气体色层分离法对试验前后的样品进行分析,通过以下的公式,从原油的残存率中求得原油的65小时后的分解率。原油的65小时后的分解率(%)=100-原油的残存率(GC%)<4O℃运动粘度>根据JISK2283,使用Cannon-Fenske粘度计对40℃时的运动粘度进行测定。<10O℃运动粘度>根据JISK2283,使用Cannon-Fenske粘度计对100℃时的运动粘度进行测定。<粘度指数>根据JISK2283算出粘度指数。<绝对粘度>使用布鲁克菲尔德阿美特克公司(BrookfieldAMETEK,Inc.)制造的数码粘度计(DV-II+Pro)测定绝对粘度。<流动点>根据JISK2269,测定流动点。〔原油的合成〕〔制造例1:化合物1的制造〕向2升的玻璃烧瓶内装入1046g的2-乙基己基氧基乙基乙醇、230g的1,6-二氯己烷、219g的氢氧化钾,在180℃下搅拌1小时,使之发生反应。之后,将反应液冷却至室温,为了中和过剩的碱,加入盐酸,使之成为中性。用2升的水对该反应液进行水洗后,使用分液漏斗分离取出有机层,通过减压蒸馏法从有机层中分离出化合物1。所得到的化合物1的1H-NMR表如图8所示。〔制造例2:化合物2的制造〕向10升的玻璃烧瓶内装入1310g的2-(2-乙基己基氧基)乙基乙醇、3048g的1,4-二氯丁烷、438g的氢氧化钾,在90℃下搅拌16小时,使之发生反应。之后,将反应液冷却至室温,为了中和过剩的碱,加入盐酸,使之成为中性。用3升的水对该反应液进行水洗后,使用分液漏斗分离取出有机层,通过减压蒸馏法从有机层中分离4-[2-(2-乙基己基氧基)乙氧基]-丁基氯化物。接着,向5升的玻璃烧瓶内装入2158g的2-丁基辛醇、1185g的4-[2-(2-乙基己基氧基)乙氧基]-丁基氯化物、282g的氢氧化钾,在180℃下搅拌5小时,使之发生反应。之后,将反应液冷却至室温,为了中和过剩的碱,加入盐酸,使之成为中性。用3升的水对该反应液进行水洗后,使用分液漏斗分离取出有机层,通过减压蒸馏法从有机层中分离出化合物2。〔制造例3:化合物3的制造〕向10升的玻璃烧瓶内装入1310g的2-(2-乙基己基氧基)乙基乙醇、3673g的1,6-二氯己烷、438g的氢氧化钾,在90℃下搅拌16小时,使之发生反应。之后,将反应液冷却至室温,为了中和过剩的碱,加入盐酸,使之成为中性。用3升的水对该反应液进行水洗后,使用分液漏斗分离取出有机层,通过减压蒸馏法从有机层中分离6-[2-(2-乙基己基氧基)乙氧基]-己基氯化物。接着,向5升的玻璃烧瓶内装入2158g的2-丁基辛醇、1293g的6-[2-(2-乙基己基氧基)乙氧基]-己基氯化物、282g的氢氧化钾,在180℃下搅拌5小时,使之发生反应。之后,将反应液冷却至室温,为了中和过剩的碱,加入盐酸,使之成为中性。用3升的水对该反应液进行水洗后,使用分液漏斗分离取出有机层,通过减压蒸馏法从有机层中分离出化合物3。所得到的化合物3的1H-NMR表如图9所示。〔制造例4:化合物4的制造〕向10升的玻璃烧瓶内装入1310g的2-(2-乙基己基氧基)乙基乙醇、3673g的1,6-二氯己烷、438g的氢氧化钾,在90℃下搅拌16小时,使之发生反应。之后,将反应液冷却至室温,为了中和过剩的碱,加入盐酸,使之成为中性。用3升的水对该反应液进行水洗后,使用分液漏斗分离取出有机层,通过减压蒸馏法从有机层中分离6-[2-(2-乙基己基氧基)乙氧基]-己基氯化物。接着,向5升的玻璃烧瓶内装入1508g的1-辛醇、1293g的6-[2-(2-乙基己基氧基)乙氧基]-己基氯化物、282g的氢氧化钾,在180℃下搅拌5小时,使之发生反应。之后,将反应液冷却至室温,为了中和过剩的碱,加入盐酸,使之成为中性。用3升的水对该反应液进行水洗后,使用分液漏斗分离取出有机层,通过减压蒸馏法从有机层中分离出化合物4。〔制造例5:化合物5的制造〕向10升的玻璃烧瓶内装入1310g的2-(2-乙基己基氧基)乙基乙醇、3673g的1,6-二氯己烷、438g的氢氧化钾,在90℃下搅拌16小时,使之发生反应。之后,将反应液冷却至室温,为了中和过剩的碱,加入盐酸,使之成为中性。用3升的水对该反应液进行水洗后,使用分液漏斗分离取出有机层,通过减压蒸馏法从有机层中分离6-[2-(2-乙基己基氧基)乙氧基]-己基氯化物。接着,向5升的玻璃烧瓶内装入1832g的1-癸醇、1293g的6-[2-(2-乙基己基氧基)乙氧基]-己基氯化物、282g的氢氧化钾,在180℃下搅拌5小时,使之发生反应。之后,将反应液冷却至室温,为了中和过剩的碱,加入盐酸,使之成为中性。用3升的水对该反应液进行水洗后,使用分液漏斗分离取出有机层,通过减压蒸馏法从有机层中分离出化合物5。所得到化合物5的1H-NMR表如图10所示。〔制造例6:化合物6的制造〕向10升的玻璃烧瓶内装入1310g的2-(2-乙基己基氧基)乙基乙醇、3673g的1,6-二氯己烷、438g的氢氧化钾,在90℃下搅拌16小时,使之发生反应。之后,将反应液冷却至室温,为了中和过剩的碱,加入盐酸,使之成为中性。用3升的水对该反应液进行水洗后,使用分液漏斗分离取出有机层,通过减压蒸馏法从有机层中分离6-[2-(2-乙基己基氧基)乙氧基]-己基氯化物。接着,向5升的玻璃烧瓶内装入2158g的1-十二烷醇、1293g的6-[2-(2-乙基己基氧基)乙氧基]-己基氯化物、282g的氢氧化钾,在180℃下搅拌5小时,使之发生反应。之后,将反应液冷却至室温,为了中和过剩的碱,加入盐酸,使之成为中性。用3升的水对该反应液进行水洗后,使用分液漏斗分离取出有机层,通过减压蒸馏法从有机层中分离出化合物6。所得到化合物6的1H-NMR表如图11所示。〔制造例7:化合物7的制造〕向10升的玻璃烧瓶内装入1310g的2-(2-乙基己基氧基)乙基乙醇、3048g的1,4-二氯丁烷、438g的氢氧化钾,在90℃下搅拌16小时,使之发生反应。之后,将反应液冷却至室温,为了中和过剩的碱,加入盐酸,使之成为中性。用3升的水对该反应液进行水洗后,使用分液漏斗分离取出有机层,通过减压蒸馏法从有机层中分离4-[2-(2-乙基己基氧基)乙氧基]-丁基氯化物。接着,向5升的玻璃烧瓶内装入1508g的1-辛醇、1185g的4-[2-(2-乙基己基氧基)乙氧基]-丁基氯化物、282g的氢氧化钾,在180℃下搅拌5小时,使之发生反应。之后,将反应液冷却至室温,为了中和过剩的碱,加入盐酸,使之成为中性。用3升的水对该反应液进行水洗后,使用分液漏斗分离取出有机层,通过减压蒸馏法从有机层中分离出化合物7。〔制造例8:化合物8的制造〕向10升的玻璃烧瓶内装入1310g的2-(2-乙基己基氧基)乙基乙醇、3048g的1,4-二氯丁烷、438g的氢氧化钾,在90℃下搅拌16小时,使之发生反应。之后,将反应液冷却至室温,为了中和过剩的碱,加入盐酸,使之成为中性。用3升的水对该反应液进行水洗后,使用分液漏斗分离取出有机层,通过减压蒸馏法从有机层中分离4-[2-(2-乙基己基氧基)乙氧基]-丁基氯化物。接着,向5升的玻璃烧瓶内装入1832g的1-癸醇、1185g的4-[2-(2-乙基己基氧基)乙氧基]-丁基氯化物、282g的氢氧化钾,在180℃下搅拌5小时,使之发生反应。之后,将反应液冷却至室温,为了中和过剩的碱,加入盐酸,使之成为中性。用3升的水对该反应液进行水洗后,使用分液漏斗分离取出有机层,通过减压蒸馏法从有机层中分离出化合物8。〔制造例9:化合物9的制造〕向10升的玻璃烧瓶内装入1310g的2-(2-乙基己基氧基)乙基乙醇、3048g的1,4-二氯丁烷、438g的氢氧化钾,在90℃下搅拌16小时,使之发生反应。之后,将反应液冷却至室温,为了中和过剩的碱,加入盐酸,使之成为中性。用3升的水对该反应液进行水洗后,使用分液漏斗分离取出有机层,通过减压蒸馏法从有机层中分离4-[2-(2-乙基己基氧基)乙氧基]-丁基氯化物。接着,向5升的玻璃烧瓶内装入2158g的1-十二烷醇、1185g的4-[2-(2-乙基己基氧基)乙氧基]-丁基氯化物、282g的氢氧化钾,在180℃下搅拌5小时,使之发生反应。之后,将反应液冷却至室温,为了中和过剩的碱,加入盐酸,使之成为中性。用3升的水对该反应液进行水洗后,使用分液漏斗分离取出有机层,通过减压蒸馏法从有机层中分离出化合物9。〔制造例10:化合物10的制造〕向2升的玻璃烧瓶内装入1117g的2-丁基辛醇、191g的1,4-二氯丁烷、219g的氢氧化钾,在180℃下搅拌16小时,使之发生反应。之后,将反应液冷却至室温,为了中和过剩的碱,加入盐酸,使之成为中性。用2升的水对该反应液进行水洗后,使用分液漏斗分离取出有机层,通过减压蒸馏法从有机层中分离出化合物10。所得到的化合物10的1H-NMR表如图12所示。〔原油以及添加物〕以下的实施例、参考例、比较例中,使用通过所述合成例得到的原油以及如下所示的原油以及添加物。<原油>·葵二酸二辛脂(以下、本说明书中称为DOS)·MORESCOWHITEP-70(MORESCOCorporation;液状石蜡)·MORESCO-HILUBELB-15(MORESCOCorporation;烷基二苯醚)·H334R(日油股份有限公司;来源于三羟甲基丙烷的三酯)·ADEKACARPOLM-60(ADEKACorporation;聚亚烷基二醇)·MPDC9(3-甲基-1,5-戊二醇二醇酯;用日本专利第4466850号记载的方法合成)·MPDC11(3-甲基-1,5-戊二醇双十一酸酯;用日本专利第4466850号记载的方法合成)<烷基化苯萘胺系抗氧化剂>·IRGANOXL06(BASFCorporation;N-苯基-1,1,3,3-四甲基丁基萘-1-胺;表中标记为「L06」)·NaugalubeAPAN(ChemturaCorporation;N-苯基-2,4,6,8-四甲基辛基萘-1-胺;表中标记为「APAN」)<二苯胺系抗氧化剂>·IRGANOXL57(BASFCorporation;2,4,4-三甲基戊二苯胺)<苯酚系抗氧化剂>·AO-50F(ADEKACorporation;3-(4,-羟基-3,-5,-二-t-丁基苯基)丙烯酸-n-十八烷基)<亚磷酸酯系抗氧化剂>·ADKSTAB522A(ADEKACorporation;1,1,3-三(2-甲基-4-双十三烷基磷酸酯-5-t-丁基苯基)丁烷)<金属钝化剂>·IRGAMET39(BASFCorporation;N,N-双(2-乙基己基)-(4或者5)-甲基-1H-苯并三唑-1-甲胺)<防腐剂>·IRGACORL12(BASFCorporation;四丙烯基琥珀酸和1,2-丙二醇/矿物油/四丙烯基琥珀酸的混合物)〔参考例1-3、比较例1-5〕原油使用化合物6,调制具有表1所示组成的润滑剂组合物I-P,在180℃的带有旋转盘的恒温槽内多次变化静置时间,测定蒸发损耗量。[表1]结果如图1所示。图1-7中,纵轴表示蒸发损耗量(单位:重量%),横轴表示静置时间(图中以「经过时间」表示,单位为时间)。如图1所示,参考例1中,抗氧化剂使用烷基化苯萘胺和亚磷酸酯,其中烷基化苯萘胺的含有比例为95重量%,亚磷酸酯的含有比例为5重量%,显示蒸发损耗量较小,且截止蒸发损耗量的上升出现坡度的时间较长。并且,烷基化苯萘胺的含有比例为90重量%、亚磷酸酯的含有比例为10重量%的参考例2以及烷基化苯萘胺的含有比例为85重量%、亚磷酸酯的含有比例为15重量%的参考例3中,显示蒸发损耗量更小,且截止蒸发损耗量的上升出现坡度的时间更长。可以认为这是由于抗氧化剂按照上述比例使用烷基化苯萘胺和亚磷酸酯,从而抗氧化效果变得更大的同时,抗氧化效果的持续时间也变得更长。与此相对,抗氧化剂仅使用烷基化苯萘胺,而不使用亚磷酸酯的比较例1与抗氧化剂并用烷基化苯萘胺和亚磷酸酯的情况相比,蒸发损耗量在较早的时间点大幅上升。此外,抗氧化剂仅使用亚磷酸酯而不使用烷基化苯萘胺的比较例4与抗氧化剂并用烷基化苯萘胺和亚磷酸酯的情况相比,蒸发损耗量在较早的时间点变大。此外,烷基化苯萘胺的含有比例为97重量%、亚磷酸酯的含有比例为3重量%的比较2以及烷基化苯萘胺的含有比例为80重量%、亚磷酸酯的含有比例为20重量%的比较例3与烷基化苯萘胺的含有比例为85重量%~95重量%、亚磷酸酯的含有比例为15重量%~5重量%的参考例1-3相比,蒸发损耗量显著变大。进一步地,抗氧化剂既不使用亚磷酸酯也不使用烷基化苯萘胺,而使用了苯酚系抗氧化剂的比较例5与抗氧化剂并用烷基化苯萘胺和亚磷酸酯的情况相比,蒸发损耗量变大。〔实施例1-2、比较例6-10〕原油使用化合物6,调制具有表2所示组成的润滑剂组合物Q-W,在180℃的带有旋转槽的恒温槽内多次变化静置时间,测定蒸发损耗量。[表2]结果如图2所示。并且,低蒸发性的评价如表2所示。表2中,低蒸发性较佳的情况用◎表示,低蒸发性不充分的情况用△表示,低蒸发性较差的情况用×表示。比较例6中,抗氧化剂仅使用相对于润滑剂组合物总量为3.00重量%的烷基化苯萘胺。与此相对,比较例7中,抗氧化剂仅使用烷基化苯萘胺,且与比较例6相比,相对于润滑剂组合物的总量多使用0.50重量%,也就是说使用3.50重量%的烷基化苯萘胺。一方面,实施例2中,作为抗氧化剂,相对于比较例6,不是像比较例7一样仅多使用0.50重量%的烷基化苯萘胺,而是追加使用了0.50重量%的亚磷酸酯。其结果如图2所示,发现相对于烷基化苯萘胺的含有量为润滑剂组合物总量的3.00重量%的比较例6来说,亚磷酸酯多使用0.50重量%的实施例2比起多使用0.50重量%的烷基化苯萘胺的比较例7,蒸发损耗量显著变小。根据所述结果,可以判断通过并用烷基化苯萘胺和亚磷酸酯,超出了抗氧化剂的总量变多所带来的效果,获得了促进低蒸发性的协同性的效果。进一步地,发现相对于烷基化苯萘胺的含有量为润滑剂组合物总量的3.00重量%的比较例6来说,亚磷酸酯稍微多含有0.20重量%的实施例1也获得了促进低蒸发性的显著效果。此外,如图2所示,作为抗氧化剂,以与实施例2的烷基化苯萘胺和亚磷酸酯的比例相同的比例以及相对于原油与实施例2相同的含有量,使用了由苯酚系抗氧化剂和亚磷酸酯构成的抗氧化剂的比较例10中,蒸发损耗量相较于实施例2的蒸发损耗量变大,且蒸发损耗量的上升在较早时间点出现坡度。根据所属结果,可以判断即使并用苯酚系抗氧化剂和亚磷酸酯,也无法达成并用烷基化苯萘胺和亚磷酸酯时的低蒸发性。此外,有关烷基化苯萘胺和亚磷酸酯的比例,烷基化苯萘胺的含有量为81.08重量%、亚磷酸酯的含有量为18.92重量%的比较例8和烷基化苯萘胺的含有量为75重量%、亚磷酸酯的含有量为25重量%的比较例9与烷基化苯萘胺的含有量在85~95重量%、亚磷酸酯的含有量在15~5重量%的范围内的实施例1-2相比,蒸发损耗量变大。〔参考例4-5、比较例11-14〕调制具有表3所示组成的润滑剂组合物1-12。如表3所示,关于各种原油,分别调制仅将烷基化苯萘胺作为抗氧化剂单独使用的润滑剂组合物(表3中记载有「单独」)和抗氧化剂并用烷基化苯萘胺和亚磷酸酯的润滑剂组合物(表3中记载有「并用」)。将两种润滑剂组合物放置在180℃的带有旋转盘的恒温槽内静置16.5小时后,分别测定其蒸发损耗量,求得通过并用烷基化苯萘胺和亚磷酸酯所带来的蒸发损耗量的降低率。通过并用烷基化苯萘胺和亚磷酸酯所带来的蒸发损耗量的降低率(以下、简称「由并用带来的蒸发损耗量降低率」)根据以下公式算出。由并用带来的蒸发损耗量降低率(%)=100-100×(含有烷基化苯萘胺和亚磷酸酯构成的抗氧化剂的润滑剂组合物的16.5小时后的蒸发损耗量/仅将烷基化苯萘胺作为抗氧化剂而含有的润滑剂组合物的16.5小时后的蒸发损耗量)[表3][表4]结果如表4所示。原油使用了上述化学式(6)所表示的脂肪族醚化合物(化合物6)的参考例4中的并用带来的蒸发损耗量降低率(%)为76重量%,原油使用了作为脂肪族聚醚化合物的聚亚烷基二醇的参考例5中的并用带来的蒸发损耗量降低率(%)为54重量%。与此相对,原油使用了作为二酯的葵二酸二辛基的比较例11中的并用带来的蒸发损耗量降低率(%)为1.5重量%,原油使用了液状石蜡的比较例12中的并用带来的蒸发损耗量降低率(%)为3.6重量%,原油使用了作为芳香族醚化合物的烷基二苯醚的比较例13中的并用带来的蒸发损耗量降低率(%)为1.0重量%,原油使用了作为三酯化合物的受阻酯的比较例14中的并用带来的蒸发损耗量降低率(%)为4.7重量%。根据参考例4-5以及比较例11-14的结果,发现由烷基化苯萘胺和亚磷酸酯的组合带来的高结合效应是在各种各样的原油中,脂肪族醚化合物所特有能看到的效果。〔实施例3-14、比较例15-16〕原油使用化合物6,调制具有表5所示组成的润滑剂组合物L、M以及13-24,在180℃的带有旋转盘的恒温槽内多次变化静置时间,测定蒸发损耗量。[表5]结果如图3及图4所示。图3及图4显示:实施例3、4、9以及10中,相对于润滑剂组合物的总体,润滑剂组合物含有的所述烷基化苯萘胺和亚磷酸酯的合计量为4重量%;实施例5、6、11以及12中,相对于润滑剂组合物的总体,润滑剂组合物含有的所述烷基化苯萘胺和亚磷酸酯的合计量为6重量%;实施例7、8、13以及14中,相对于润滑剂组合物的总体,润滑剂组合物含有的所述烷基化苯萘胺和亚磷酸酯的合计量为8重量%;上述各实施例的蒸发损耗量较小,且截止蒸发损耗量的上升出现坡度的时间较长。与此相对,除了将润滑剂组合物所含有的烷基化苯萘胺和亚磷酸酯的合计量相对于润滑剂组合物总体设定为2重量%以外,采用与实施例3-8同样的方法调制润滑剂组合物,进而测定蒸发损耗量的比较例15及16中,蒸发损耗量与实施例3-8的蒸发损耗量相比显著变大,且蒸发损耗量的上升在较早的时间点出现坡度。〔实施例15-17、比较例17-21〕原油使用化合物5,调制具有表6所示组成的润滑剂组合物A-H,在180℃的带有旋转盘的恒温槽内,多次变化静置时间,测定蒸发损耗量。[表6]结果如图5所示。如表6所示,比较例17-21以及实施例15-17中,将脂肪族醚化合物作为原油,抗氧化剂并用烷基化苯萘胺系抗氧化剂以及/或者烷基化二苯胺系抗氧化剂和亚磷酸酯系抗氧化剂。该些比较例和实施例中,将烷基化苯萘胺系抗氧化剂以及/或者烷基化二苯胺系抗氧化剂的使用量相对于润滑剂组合物总量固定为5.5重量%,亚磷酸酯系抗氧化剂的使用量相对于润滑剂组合物总量固定为0.5重量%,另一方面变化烷基化苯萘胺系抗氧化剂和烷基化二苯胺系抗氧化剂的比例。如图5所示,烷基化苯萘胺系抗氧化剂的使用量以及烷基化二苯胺系抗氧化剂的使用量分别为0及5.5重量%的比较例17中,蒸发损耗量相较于实施例15-17、比较例18-21的蒸发损耗量变大,且蒸发损耗量的上升在较早时间点出现坡度。比较例18、比较例19、比较例20、比较例21、实施例15、实施例16中,按照此种记载顺序,蒸发损耗量逐渐减小且逐渐在较晚的时间点出现上升。烷基化苯萘胺系抗氧化剂的使用量以及烷基化二苯胺系抗氧化剂的使用量分别为5.5重量%以及0的实施例17中,蒸发损耗量减少最多且在较晚时间点上升。根据所述结果,可以判断烷基化二苯胺系抗氧化剂和亚磷酸酯系抗氧化剂的组合难以得到本发明的实现低蒸发量的效果。与此相对,发现如果抗氧化剂并用烷基化苯萘胺和亚磷酸酯的话,可以获得显著地降低蒸发量的效果。〔实施例18-19、23-26〕调制具有表7所示组成的润滑剂组合物25-26以及33-36,在180℃的带有旋转盘的恒温槽内,多次变化静置时间,测定蒸发损耗量。并且,测定润滑剂组合物的40℃运动粘度以及100℃运动粘度,求得粘度指数。[表7]结果如表7及图6所示。如表7所示,所得到的润滑剂组合物的40℃运动粘度、100℃运动粘度以及粘度指数与本
技术领域:
的现有润滑油相等或者更出色。并且,确认所得到的润滑剂组合物显示出与本
技术领域:
的现有润滑油具有同等或者更出色的低蒸发性。〔实施例20-22、比较例22-24〕调制具有表8及表9所示组成的润滑剂组合物27-32,在180℃的带有旋转盘的恒温槽内,多次变化静置时间,测定蒸发损耗量。表8所示的组成为本
技术领域:
现存的润滑剂组合物的组成。并且,针对得到的润滑剂组合物,测定原油的65小时后的分解率。并且,针对通过实施例18得到的润滑剂组合物25以及通过实施例24得到的润滑剂组合物34,测定原油的65小时后的分解率。[表8][表9]蒸发损耗量的测定结果与实施例18的结果一起如图7所示。并且,原油的65小时后的分解率的测定结果如表10所示。[表10]如图7所示,以作为二酯的MPDC9以及DOS为原油的现有的润滑剂组合物27及28与通过实施例20-22、24以及实施例18得到的润滑剂组合物相比,蒸发损耗量较大。并且,如表10所示,判断原油的65小时后的分解率超过60%,耐湿性较差。此外,判断以作为二酯的MPDC11为原油的现有的润滑剂组合物的蒸发损耗量较小,但是如表10所示,原油的65小时后的分解率超过60%,耐湿性较差。与此相对,判断实施例20-22、24以及实施例18所得到的润滑剂组合物具有优异的低蒸发性和耐湿性。〔本发明的脂肪族醚化合物的物理性质的评价〕针对通过上述合成例得到的脂肪族醚化合物以及现有润滑油,进行粘性以及低温流动性的评价。结果如表11-13所示。[表11][表12][表13]化合物1化合物3化合物5化合物6DOSMPDC9MPDC11流动点(℃)<-40<-40-15-5<-40-25-5如表11所示,通过所述合成例得到的化合物1、3、5、6与现有的作为二酯的MPDC9、MPDC11以及DOS相比,可以说化合物1、3、5、6的分子量的粘度比较低。并且,确认化合物1、3、5、6的粘度指数也比现有的二酯高或者等同于现有的二酯。此外,如表12所示,确认通过所述合成例得到的化合物3、5、6与现有的作为二酯的DOS相比,化合物3、5、6的分子量的粘度较低。此外,如表13所示,确认通过所述合成例得到的化合物1、3、5、6与现有的作为二酯的MPDC9、MPDC11以及DOS相比,化合物1、3、5、6的流动点较低或者与MPDC9、MPDC11以及DOS相同。产业上的可利用性本发明的润滑剂组合物在具有低粘度、低蒸发性、低温流动性以及高粘度指数等的物理特性的基础上,可以抑制由于水解造成的金属腐蚀,且针对有机材料的不良影响较少。因此,作为轴承用的润滑油自然不用说,也可以作为液体轴承用的润滑油、浸渍轴承用的润滑油、润滑脂用的原料、冷冻机油用的原料等被适当地利用。因此,本发明在使用润滑剂组合物的所有的
技术领域:
中,产业上的利用价值极高。当前第1页1 2 3