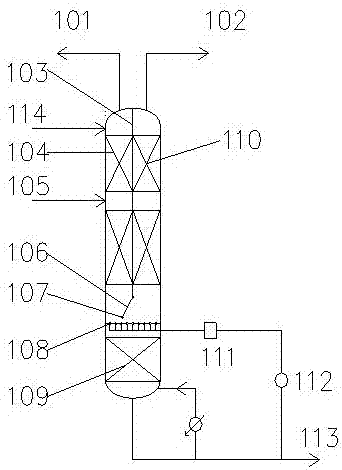
本发明涉及石油炼制工业,特别是催化裂化、延迟焦化等装置吸收稳定工艺与系统。
背景技术:
:吸收稳定系统是石油炼制工业中催化裂化装置和延迟焦化装置的后处理过程,其目的是利用吸收和精馏原理将分馏塔塔顶油气分离罐中的富气和粗汽油分割成干气(c2以下)、液化气(c3、c4)和蒸汽压合格的稳定汽油。吸收稳定系统的装置和工艺流程优化对催化裂化和延迟焦化装置的节能增效起着十分重要的作用。目前大多数炼厂吸收-稳定工艺流程是:分馏塔塔顶富气经富气压缩机升压后与吸收塔底油、解吸塔顶油气混合,经冷却器冷却后进入气液平衡罐进行气液分离。分离出来的气体进入吸收塔下部;分离出来的凝缩油进入解吸塔顶部。分馏塔塔顶分离罐液相粗汽油作为吸收塔的吸收剂。吸收塔顶部出来的贫气进入再吸收塔,用分馏塔柴油作为吸收剂进行再次吸收,以回收吸收塔顶携带出来的汽油组分。再吸收塔塔底富吸收油返回分馏塔。塔顶干气送出装置。解吸塔塔底脱乙烷汽油送至稳定塔。稳定塔塔顶气经塔顶冷却器冷凝冷却后,分离出来的液化石油气。稳定塔塔底油分两路,一路作为产品送出装置;另一路送到吸收塔作为补充吸收剂。在系统中为提高吸收塔吸收效率,吸收塔一般设置中段冷却器。近年来随着低碳化工的快速发展和民用液化气需求量逐渐扩大,提高干气和液化气的分离精度,提高液化气产量,已经成为炼厂提升经济效益的一个重要手段,另外随着节能减排压力的日益增加,如何降低生产能耗也成为关注的焦点。目前炼厂吸收稳定系统普遍存在的问题主要表现为:干气不干,干气中夹带大量的液化气,液化气含量在3%(v)以上,导致大量高附加值的液化气被当作燃料直接燃烧从而造成资源的巨大浪费;吸收塔吸收效果不理想,为了降低干气中的液化气浓度,必须靠加大补充吸收剂(稳定汽油)循环量来提高吸收效果,稳定汽油内循环的存在导致了系统能耗的大幅增加和处理能力的降低。技术实现要素:目前我国柴油馏程范围在180℃~360℃,汽油终馏点为205℃,因此存在柴油中夹带一定量汽油的问题,由于柴油价值较低,而汽油价值较高,因此低价值的柴油中夹带部分高质量的汽油无疑会造成一定的经济损失。现有的催化装置中,柴油通过分馏塔的侧线采出,粗汽油从分馏塔顶部采出,这种分离流程不可能实现汽油和柴油的清晰切割,如何实现柴油和汽油的清晰切割,更大量的得到汽油馏分也是目前需要解决的一个问题。现有的吸收稳定工艺及系统都设置有补充稳定汽油内循环,为了保证干气的干度,还需要利用柴油补充吸收,柴油富吸收油再返回分馏塔中部,利用分馏塔的热量实现柴油与轻烃的分离。由于受分馏塔热平衡的限制,柴油吸收剂的量又不能太大,所以无法通过加大柴油吸收剂量以取消稳定汽油内循环。申请人研究后还发现,造成吸收稳定系统能耗较高的原因主要在于系统内循环物流量较大,增加了吸收和精馏负荷造成系统能耗高。一方面是大量解吸气在解吸塔和吸收塔间循环。目前的流程中解吸气与富气、吸收塔塔底富吸收油混合进入平衡分离罐,大量的解吸气主要是c1、c2组分,降低了平衡罐富气中c3、c4组分及富吸收油中轻烃的分压,使平衡罐气相组成中c3、c4的含量增加,从而加大了平衡罐气相进入吸收塔的量,加大了吸收塔负荷。不仅影响了吸收塔吸收效果,而且增加了吸收塔能耗;另一方面吸收塔气相负荷大,为了降低富气中液化气含量就需要更大量的稳定汽油补充吸收剂。造成大量的稳定汽油在吸收塔、解吸塔和稳定塔间循环,导致系统能耗显著增大。另外目前吸收稳定工艺流程中,解吸塔和稳定塔为独立的两座塔,从富气平衡罐出来的液相首先进入解吸塔进行分离,塔顶得到解吸轻烃,塔底产物再进入稳定塔进行分离,分别得到液化气和稳定汽油产品。采用双塔分离过程存在物料的返混,因而导致分离能耗的增大。本发明针对现有工艺存在的不足,提供一种吸收稳定工艺方法及系统,在使干气中液化气浓度大幅降低的同时,可以提高催化汽油及液化气的收率,并大幅降低系统能耗。本发明提供一种吸收稳定系统,所述吸收稳定系统包括气液平衡罐、富气压缩机、富气平衡罐、吸收塔、解吸-稳定分壁塔、再吸收塔、再生罐、解吸气平衡罐和真空泵;所述气液平衡罐入口与来自分馏塔塔顶的进料管线连接,气液平衡罐气相出口与富气压缩机入口经管线连接,气液平衡罐液相出口与吸收塔吸收剂入口经管线连接,富气压缩机出口与富气平衡罐入口经管线连接,富气平衡罐气相出口与吸收塔气相入口经管线连接,富气平衡罐液相出口与解吸-稳定分壁塔解吸区进料口经管线连接,解吸-稳定分壁塔解吸侧塔顶气相出口经解吸气平衡罐冷却器后与解吸气平衡罐入口经管线连接,解吸气平衡罐液相出口经管线与解吸-稳定分壁塔解吸区循环物料入口连接,解吸气平衡罐气相出口与吸收塔气相入口连接,吸收塔塔底出料口分两路,其中一路经解吸气平衡罐冷却器后与解吸气平衡罐入口连接,另一路经管线与富气平衡罐入口连接,吸收塔塔顶气相出口经管线与再吸收塔入口连接,再吸收塔塔底液相出料口与再生罐入口经管线连接,再生罐气相出口经真空泵与富气压缩机入口连接,再生罐液相出口分两路,其中一路经管线与再吸收塔吸收剂入口连接,另一路出装置。本发明所述吸收稳定系统中,所述富气压缩机出口与富气平衡罐入口的连接管线上设置富气冷却器,所述富气平衡罐液相出口与解吸-稳定分壁塔解吸区进料口的连接管线上设置有换热器,再吸收塔塔底液相出料口与再生罐入口连接管线上设置再生罐换热器,所述再生罐液相出口与再吸收塔吸收剂入口连接管线上设置有进料换热器。本发明所述吸收稳定系统中,所述的解吸-稳定分壁塔为上隔壁式分壁塔,所述解吸-稳定分壁塔中部沿纵向设置一块隔板,将解吸-稳定分壁塔的内部分为解吸区、稳定区和提馏区,所述隔板从分壁塔塔顶部直接延伸下来,但不与分壁塔底部接触,所述解吸-稳定分壁塔还包括气体分配控制系统;气体分配控制系统包括气体分配器和气体分配电脑控制系统;气体分配器由安装有磁铁的气体导向板和电磁吸铁栅板组成。所述的解吸-稳定分壁塔中,气体导向板为下半圆形,下半圆顶部通过与隔板底部设置的转动轴连接,气体导向板转动角度为-90~90°,优选-45~45°,半圆直径为0.8~1d(d为分壁塔的塔内径),优选0.85~0.95d,气体导向板内底部镶嵌一块弓形磁铁。气体导向板位于电磁吸铁栅板上部,气体导向板底部磁铁距离下方电磁吸铁栅板中心位置的垂直距离为1~200mm,优选10~50mm。所述的解吸-稳定分壁塔中,所述的电磁吸铁栅板为一组水平放置的格栅,每个格栅中空设计且贯穿塔壁,格栅采用密封焊的形式固定于塔壁上,格栅内部填装电磁吸铁条,格栅间距10~200mm,优选30~100mm,电磁吸铁栅板采用不锈钢材质,防止被磁化。电磁吸铁栅板位于隔板下部,格栅与隔板顶部平行。所述的解吸-稳定分壁塔中,气体导向板的转动角度是由电脑控制系统控制电磁吸铁栅板上的不同位置格栅的电磁吸铁条和导向板上磁铁之间产生吸引力进行转动,将要转动角度对应的位置的电磁吸铁条通电即可。本发明所述吸收稳定系统中,所述解吸-稳定分壁塔解吸区设置有解吸区进料口、解吸区循环物料入口和解吸气出口,所述解吸-稳定分壁塔稳定区顶部设置有液化气出口,解吸-稳定分壁塔解吸区循环物料入口位于解吸-稳定分壁塔解吸区进料口上方,解吸-稳定分壁塔解吸区循环物料入口与解吸-稳定分壁塔解吸区进料口之间设置3~5块理论板,解吸气出口位于解吸区顶部。本发明提供一种吸收稳定工艺,所述吸收稳定工艺包括如下内容:(1)油气原料进入气液分离罐,分离后得到富气和粗汽油;(2)步骤(1)得到的富气经压缩冷却后进入富气平衡罐,分离后得到气相的第1料流和液相的第2料流;(3)步骤(2)得到的液相的第2料流经换热后经解吸-稳定分壁塔解吸区进料口进入该塔解吸侧,处理后解吸侧塔顶得到解吸气、稳定侧塔顶得到液化石油气、塔底得到稳定汽油;(4)步骤(2)得到的第1料流与步骤(1)得到的粗汽油进入吸收塔,处理后得到贫气和液相的第3料流,液相的第3料流分为第31子料流和第32子料流,第31子料流进入富气平衡罐;(5)步骤(3)得到的解吸气与步骤(4)得到的第32子料流混合并冷却后进入解吸气平衡罐,分离后得到气相的第4料流与液相的第5料流,气相的第4料流进入吸收塔,液相的第5料流经解吸-稳定分壁塔解吸区循环物料入口进入解吸-稳定分壁塔解吸侧塔顶;(6)步骤(4)得到的贫气进入再吸收塔与吸收剂接触反应,反应后得到干气与富吸收油;(7)步骤(6)得到的富吸收油经换热后进入再生罐进行再生,再生后得到气相的第6料流和液相的第7料流,气相的第6料流经真空泵进入富气压缩机与富气混合后一起处理,液相的第7料流全部循环回再生罐,或者部分循环进入再吸收塔作为吸收剂重复利用,部分排出装置。本发明工艺中,步骤(1)得到的富气经压缩冷却至30℃~40℃后进入富气平衡罐。本发明工艺中,步骤(4)中所述第31子料流占第3料流的比例为10wt%~90wt%,优选为30wt%~70wt%。本发明工艺中,步骤(2)得到的第2料流经换热至40℃~90℃,优选为55℃~80℃后进入解吸-稳定分壁塔。本发明工艺中,所述解吸气平衡罐的压力比富气压缩后压力高1%~20%,优选高5%~15%。本发明工艺中,步骤(3)中所述的稳定汽油经冷却后温度为30℃~40℃。本发明工艺中,再吸收塔用的吸收剂可以为复合吸收剂或柴油,所述柴油可以是从分馏塔侧线采出的柴油,所述复合吸收剂为离子液体和有机酸盐的混合物,其中有机酸盐浓度为1wt%~10wt%,优选为1wt%~5wt%。所述复合吸收剂中的离子液体的阳离子为咪唑阳离子或烷基咪唑阳离子,如1-丁基-3-甲基咪唑阳离子或1-戊基-3-甲基咪唑阳离子,阴离子为四氟硼酸根阴离子、六氟磷酸根阴离子、氯离子或溴离子等;具体可以为1-丁基-3-甲基咪唑四氟硼酸盐和/或1-丁基-3-甲基咪唑六氟硼酸盐。所述复合吸收剂中的有机酸盐可以为醋酸钠、丙酸钠、醋酸钾等中的一种或几种。本发明工艺中,步骤(6)得到的富吸收油经换热至60~100℃,优选为70~80℃后进入再生罐进行再生,再生过程为真空操作,再生罐操作压力为5~50kpa,优选为15~20kpa。本发明工艺中,当再吸收塔采用柴油作为吸收剂时,再生后的吸收剂为去除了轻烃及柴油轻端的柴油,其初馏点大于200℃,优选大于205℃。本发明工艺中,所述的解吸-稳定分壁塔为上隔壁式分壁塔,所述解吸-稳定分壁塔中部沿纵向设置一块隔板,将解吸-稳定分壁塔的内部分为解吸区、稳定区和提馏区,所述隔板从分壁塔塔顶部直接延伸下来,但不与分壁塔底部接触,所述解吸-稳定分壁塔还包括气体分配控制系统;气体分配控制系统包括气体分配器和气体分配电脑控制系统;气体分配器由安装有磁铁的气体导向板和电磁吸铁栅板组成。所述的解吸-稳定分壁塔中,气体导向板为下半圆形,下半圆顶部通过与隔板底部设置的转动轴连接,气体导向板转动角度为-90~90°,优选-45~45°,半圆直径为0.8~1d(d为分壁塔的塔内径),优选0.85~0.95d,气体导向板内底部镶嵌一块弓形磁铁。气体导向板位于电磁吸铁栅板上部,气体导向板底部磁铁距离下方电磁吸铁栅板中心位置的垂直距离为1~200mm,优选10~50mm。所述的解吸-稳定分壁塔中,所述的电磁吸铁栅板为一组水平放置的格栅,每个格栅中空设计且贯穿塔壁,格栅采用密封焊的形式固定于塔壁上,格栅内部填装电磁吸铁条,格栅间距10~200mm,优选30~100mm,电磁吸铁栅板采用不锈钢材质,防止被磁化。电磁吸铁栅板位于隔板下部,格栅与隔板顶部平行。所述的解吸-稳定分壁塔中,气体导向板的转动角度是由电脑控制系统控制电磁吸铁栅板上的不同位置格栅的电磁吸铁条和导向板上磁铁之间产生吸引力进行转动,将要转动角度对应的位置的电磁吸铁条通电即可。本发明工艺中,所述解吸-稳定分壁塔解吸区设置有解吸区进料口、解吸区循环物料入口和解吸气出口,所述解吸-稳定分壁塔稳定区顶部设置有液化气出口,解吸-稳定分壁塔解吸区循环物料入口位于解吸-稳定分壁塔解吸区进料口上方,解吸-稳定分壁塔解吸区循环物料入口与解吸-稳定分壁塔解吸区进料口之间设置3~5块理论板,解吸气出口位于解吸区顶部。与现有技术相比,本发明吸收稳定工艺具有如下优势:本发明所述吸收稳定系统通过设置解吸气平衡罐,避免了解吸气对富含液化石油气的富气在冷凝后平衡的干扰,有利于强化富气平衡效果,减少平衡后进入吸收塔的气相量,降低吸收塔负荷,降低了对吸收剂的需求量,为取消稳定汽油内循环创造了条件,大幅降低了能耗。本发明通过解吸气平衡罐对解吸气单独地吸收冷凝平衡,有利于将解吸-稳定分壁塔中过解吸的液化石油气充分吸收冷凝下来,可以大幅降低进入吸收塔气相量,降低吸收塔负荷,进而降低在解吸-稳定分壁塔和吸收塔间的循环量,从而大幅降低过程能耗。本发明吸收稳定工艺中,由于解吸气平衡罐得到的第2料流和富气平衡罐液得到的第5料流相中所含轻组分的不同,分别通过不同进料口进入解吸-稳定分壁塔,并设置富气平衡罐液相加热器,有利于强化解吸效果,降低塔底供热负荷。本发明吸收稳定工艺中,通过采用上隔壁式分壁塔实现了解吸塔和稳定塔的功能,降低了分离过程的物料返混,大幅降低了分离过程能耗,另外本发明提供了灵活可控的分壁塔气相分配控制系统,可对分壁塔隔板两侧气相进行灵活调节,进一步降低了系统能耗、提高了操作可靠性,解决了以往分壁塔无法对隔板两侧气相流率进行灵活分配的难题。本发明吸收稳定工艺及系统建立了专有再吸收循环系统,取消了原吸收稳定系统的补充稳定汽油吸收剂这一内循环,使得系统的能耗大幅降低,而且再吸收循环系统吸收剂循环量可以灵活控制,可使得气产品中液化气夹带率降低到1%(v)以下,大大提高了装置的经济效益,解决了传统工艺受因分馏塔热平衡限制而无法通过增大柴油吸收剂量大幅降低干气中的c3+组分浓度的问题。另外对于老装置而言,还可以大幅提高装置处理能力。当以柴油作为二级循环吸收剂,柴油吸收剂能显著提高从吸收塔出来的贫气中轻烃组分的吸收效果,并且柴油吸收剂循环量可灵活控制,能够使得干气中的c3+组分浓度低于1%(v)以下,从而实现了增产液化气的目的,解决了传统工艺受因分馏塔热平衡限制而无法通过增大柴油吸收剂量大幅降低干气中的c3+组分浓度的问题。尤其当使用将分馏塔产的柴油连续补入再吸收循环系统,保证了吸收剂的效果,通过真空闪蒸方式既实现了富柴油的再生又去除了柴油吸收剂中的汽油馏分,实现了柴油和汽油的清晰切割,达到了增产催化汽油的目的,显著增加了装置经济效益。当采用咪唑类离子液体与有机酸盐的混合物作为吸收剂,其中咪唑类离子液体对c3+组分具有良好的吸收效果,并且对c1和c2吸收效果较差,因此具有良好的选择性;通过加入有机酸盐与离子液体复配使用,大大提高了有机基团的浓度,大幅提高了溶剂对c3、c4组分的吸收效果;有机酸盐的加入大大提高了吸收剂粘度,增强了吸收效果,同时显著加速了c3+组分在溶剂中的解吸速率与解吸深度,大大简化了吸收剂再生系统,提高了再生吸收剂的质量;离子液体与有机酸盐的复配大大降低了降低了吸收剂在系统中的循环量;有机酸盐的加入进一步降低了离子液体的挥发性,减少价格昂贵的离子液体的损失,降低了运行费用。另外咪唑类离子液体与有机酸盐组成的复合溶剂具有熔点低、饱和蒸汽压低的优点,这使得吸收剂再生过程变得非常容易,因此再生能耗大幅降低。本发明吸收稳定系统虽然增加了冷凝器、解吸气平衡罐及相应真空再生措施,但工艺流程清晰、工艺先进合理、装置能耗低、产品质量可靠等优点,尤其是实现了取消稳定期油内循环的目的,这大大降低了现有设备的负荷,在总的设计预算中并没有增加投资量。对于新设计或新建装置具有装置能耗先进,产品指标优质等特点;对于旧装置改造具有改造费用低,降低装置能耗,增加装置效益等特点。附图说明图1为本发明吸收稳定系统工艺流程图。图2是本发明解吸-稳定分壁塔结构示意图。图3是本发明电磁吸铁栅板结构示意图。图4是本发明气体导向板结构示意图。图5为对比例2中吸收稳定工艺流程图。具体实施方式本发明提供一种吸收稳定系统,所述吸收稳定系统包括气液平衡罐1、富气压缩机2、富气平衡罐3、吸收塔4、解吸-稳定分壁塔5、再吸收塔6、再生罐7、解吸气平衡罐8和真空泵10;所述气液平衡罐1入口与来自分馏塔塔顶的进料管线16连接,气液平衡罐1气相出口与富气压缩机2入口连接,气液平衡罐1液相出口与吸收塔4吸收剂入口经管线连接,富气压缩机2出口经富气冷却器后与富气平衡罐3入口经管线连接,富气平衡罐3气相出口与吸收塔4气相入口连接,富气平衡罐3液相出口经换热器12后与解-吸稳定分壁塔5进料口经管线连接,分壁塔5解吸侧塔顶气相出口经解吸气平衡罐冷却器13后与解吸气平衡罐8入口经管线连接,解吸气平衡罐8液相出口经管线与分壁塔5循环物料入口连接,解吸气平衡罐8气相出口与吸收塔4气相入口连接,吸收塔塔底出料口分两路,其中一路28经解吸气平衡罐冷却器13后与解吸气平衡罐8入口连接,另一路27经管线与富气平衡罐3入口连接,吸收塔4塔顶气相出口经管线与再吸收塔6入口连接,再吸收塔6塔底液相出料口经再生罐换热器后与再生罐7入口经管线连接,再生罐7气相出口经真空泵10与富气压缩机2入口连接,再生罐液相出口分两路,其中一路35作为产品出装置,另一路36经进料换热器15后与再吸收塔6吸收剂入口连接。本发明吸收稳定工艺及系统中所用的解吸-稳定分壁塔具体结构由图2、图3、图4做进一步说明,所述的解吸-稳定分壁塔为上隔壁式分壁塔,所述解吸-稳定分壁塔中部沿纵向设置一块隔板103,将解吸-稳定分壁塔的内部分为解吸区104、稳定区110和提馏区109,所述隔板103从分壁塔塔顶部直接延伸下来,但不与分壁塔底部接触,所述解吸-稳定分壁塔还包括气体分配控制系统,气体分配控制系统包括气体分配器和气体分配电脑控制系统111;气体分配器由安装有磁铁的气体导向板106和电磁吸铁栅板108组成。所述气体导向板106为下半圆形,下半圆顶部通过与隔板103底部设置的转动轴401连接,气体导向板转动角度为-90~90°,优选-45~45°,半圆直径为0.8~1d,优选0.85~0.95d,气体导向板106内底部镶嵌一块弓形磁铁107。气体导向板106位于电磁吸铁栅板108上部,气体导向板106底部磁铁107距离下方电磁吸铁栅板108中心位置的垂直距离为1~200mm,优选10~50mm。所述的电磁吸铁栅板108为一组水平放置的格栅,每个格栅中空设计且贯穿塔壁202,格栅采用密封焊的形式固定于塔壁上,格栅内部填装电磁吸铁条,各电磁吸铁条通过电缆201与气体分配电脑控制系统111连接,格栅间距10~200mm,优选30~100mm,电磁吸铁栅板采用不锈钢材质,防止被磁化。电磁吸铁栅板108位于隔板103下部,格栅与隔板顶部平行。气体导向板的转动角度是由气体分配电脑控制系统111控制电磁吸铁栅板上的不同位置格栅的电磁吸铁条和导向板上磁铁之间产生吸引力进行转动,将要转动角度对应的位置的电磁吸铁条通电即可。所述解吸-稳定分壁塔解吸区设置有解吸区进料口105、解吸区循环物料入口114和解吸气出口101,所述解吸-稳定分壁塔稳定区顶部设置有液化气出口102,解吸-稳定分壁塔解吸区循环物料入口114位于解吸-稳定分壁塔解吸区进料口105上方,解吸气101出口位于解吸区顶部。正常工况下,从富气平衡罐出来的液相经加热后通过进料口105进入分壁塔进行分离,分壁塔提馏段上升的气相通过气体分配器分配后分别进入解吸侧和稳定侧,塔顶分别得到解吸气和液化石油气,塔底得到稳定汽油113,由于进入解吸侧和稳定侧的气体量存在一个最佳的比例,可通过气体分配电脑控制系统111控制电磁吸铁栅板108的通电电磁条进而控制气体导向板的转动角度,气体分配电脑控制系统111可以与塔底产物组成信号112及控制电磁吸铁栅板108连接建立闭环控制回路,实现对解吸侧和稳定侧上升气量比进行自动控制,使塔釜再沸器热负荷处于最低,从而达到节能的目的。结合图1,对本发明吸收稳定工艺流程进一步说明,来自催化裂化/焦化分馏塔顶的油气原料经进料管线16进入气液平衡罐1,分离得到富气17和粗汽油18,经富气压缩机2增压并经富气冷却器11冷却后的富气19进入富气平衡罐3平衡后得到的气相第1料流20进入吸收塔7,与来自气液平衡罐1的粗汽油18逆流接触进行吸收反应,反应后得到贫气31和液相第3料流,所述第3料流分为第31子料流和第32子料流,其中第31子料流27与富气压缩机增压后的富气19混合后进入富气平衡罐3一起处理,富气平衡罐3得到液相第2料流21经换热器12加热后进入解吸-稳定分壁塔5,处理后得到解吸气25、液化石油气23及稳定汽油24。解吸气25与吸收塔塔底得到的液相第32子料流混合并经解吸气平衡罐冷却器13冷却后进入解吸气平衡罐8,平衡后得到的气相第4料流29进入吸收塔7与来自富气平衡罐的气相第1料流20一起进行处理,平衡后得到的液相第5料流30通过解吸-稳定分壁塔5循环物料入口进入分壁塔5解吸侧顶部。吸收塔4塔顶得到的贫气31进入再吸收塔6与吸收剂26逆流接触进行反应,反应后塔顶得到干气32,塔底得到的富吸收油33经解吸换热器14换热升温后进入再生罐7进行再生,再生后得到气相的第6料流34和液相的第7料流,其中气相第6料流34经真空泵10返回富气压缩机2入口,液相的第7料流可以分两路,其中一路35作为产品出装置,另一路36经进料换热器15冷却后返回再吸收塔6重复使用。下面的实施例将对本发明提供的方法予以进一步说明,但本发明并不因此而受任何限制。实施例1以国内某100万吨/年,fcc型催化裂化装置的吸收稳定系统为例,采用aspenplus流程模拟软件对本发明工艺进行模拟,采用催化柴油作为吸收剂,关键工艺参数如下:富气压缩机出口压力1.4mpa,解吸气平衡罐操作温度40℃,进入解吸气平衡罐的吸收塔底液占总的吸收塔底液相出料的40wt%,富气平衡罐操作温度40℃,富气平衡罐液相换热至80℃进分壁塔,吸收塔设置一个中间冷却器返塔温度35℃,新鲜催化柴油补入量30t/h(初馏点180℃,终馏点360℃),柴油内循环量20t/h,再生柴油初馏点205℃,再生罐真空度15kpa,干气产量5t/h,液化气产量29t/h,稳定汽油产量57t/h,设备能耗见表1。实施例2与实施例1相同,不同之处在于采用1-丁基-3-甲基咪唑六氟硼酸盐与乙酸钠的混合物(其中乙酸钠为5wt%)作为吸收剂,工艺参数如下:富气压缩机出口压力1.4mpa,解吸气平衡罐操作温度40℃,进入解吸气平衡罐的吸收塔底液占总的吸收塔底液相出料的40wt%,富气平衡罐操作温度40℃,富气平衡罐液相换热至80℃进解吸塔,吸收塔设置一个中间冷却器返塔温度35℃,吸收剂内循环量40t/h,再生罐真空度15kpa,干气产量5t/h,液化气产量29t/h,稳定汽油产量57t/h,设备能耗见表1。比较例1与实施例1相比,不同之处在于取消解吸气平衡罐,解吸塔顶的解吸气全部进入富气平衡罐,其余流程与实施例1完全相同,设备能耗见表1。比较例2:采用如图5所示的传统吸收稳定工艺流程,来自催化裂化/焦化分馏塔顶的油气原料经进料管线16进入气液平衡罐1,分离得到富气17和粗汽油18。富气17经压缩机2压缩后与来自吸收塔4塔底的吸收油27以及解吸塔顶出来的解吸气25混合并经冷却器11冷却后进入富气平衡罐3,分离得到的液相21进入解吸塔5的顶部,解吸塔5塔底脱乙烷汽油22先与稳定汽油换热后再进入稳定塔9的中部,经稳定塔分离出稳定汽油和液化气23;稳定塔塔底得到的稳定汽油部分作为产品24出装置,部分作为补充吸收剂37(稳定汽油)进入吸收塔4的顶部,粗汽油18作为吸收剂进入吸收塔4的第四块板,与来自富气平衡罐3的气相20进行逆流接触反应,吸收塔顶部引出的贫气直接进入再吸收塔6的下部,与从分馏塔来的柴油26在再吸收塔发生反应,进一步吸收贫气中夹带的重组分,富吸收油33返回主分馏塔,干气32从再吸收塔顶排出并入瓦斯管网。工艺参数如下:富气压缩机出口压力1.4mpa,富气平衡罐操作温度40℃,解吸塔液相进料温度40℃,吸收塔设置一个中间冷却器返塔温度35℃,解吸塔塔底脱乙烷汽油中乙烷含量0.1wt%,仍然存在稳定汽油内循环和柴油再吸收过程,稳定汽油内循环量60t/h,再吸收塔柴油进料量25t/h,设备能耗见表1。表1能耗项目实施例1实施例2比较例1比较例2解吸塔再沸器热负荷,kw---5233稳定塔再沸器热负荷,kw---8826解吸-稳定分壁塔热负荷,kw815382068328-补充汽油吸收剂循环量,t/h00060柴油吸收剂流量,t/h505025离子液体复合吸收剂流量,t/h40--真空泵能耗,kw增加210增加190增加220-富气压缩机能耗,kw增加160增加147增加170-干气中c3+含量(v%)0.7%0.6%1%2.8%汽油收率增加,t/h0.790.78-当前第1页12