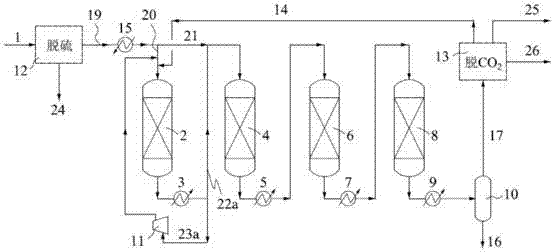
本发明涉及合成天然气
技术领域:
,具体涉及一种合成气制天然气的工艺。
背景技术:
:天然气是一种使用安全、热值高的清洁能源,广泛应用于发电、化工、城市燃气、汽车燃料等行业,是世界上主要的清洁能源之一。目前,在国内天然气供应紧张和天然气价格连续上涨情况下,国内许多公司将目光转向煤制天然气的项目。我国的能源结构是“缺油、少气、富煤”,煤炭资源相对丰富。因此,根据我国的能源结构特点,积极发展煤制合成天然气(SNG),不仅可以满足国内日益增长的市场需求,而且对于保障我国的能源安全,意义重大。德国金属公司申请了用于生产可替代天然气的生产工艺专利US4016189。在该专利申请中,原料气分别在一个高温主甲烷化反应器和一个低温副甲烷化反应器中发生甲烷化反应,通过将主甲烷化反应器出口的部分产品气由气体压缩机加压后循环至高温主甲烷化反应器入口,来控制主甲烷化反应器的温升。德国金属公司申请了合成天然气的生产工艺专利US4205961。在该专利申请中,原料气依次经过两个高温甲烷化反应器和两个低温甲烷化反应器发生甲烷化反应,通过将第一甲烷化反应器或第二甲烷化反应器出口的部分产品气由气体压缩机加压后循环至第一甲烷化反应器入口,来控制第一甲烷化反应器的温升。丹麦托普索公司申请了生产富甲烷气的工艺和装置专利US4298694。在该专利申请中,原料气分别在一个绝热高温甲烷化反应器和一个低温冷却甲烷化反应器中发生甲烷化反应,通过将低温冷却甲烷化反应器出口的部分产品气由气体压缩机加压后循环至绝热高温甲烷化反应器入口,来控制绝热高温甲烷化反应器的温升。为防止低温和高CO浓度下甲烷化催化剂生成羰基镍,该工艺在甲烷化催化剂床层上部增加变换催化剂床层,使进料合成气先发生变换反应,利用变换反应热来预热进入甲烷化催化剂床层的工艺气。通过这一方法,一方面可以降低甲烷化反应器入口处的合成气的进料温度,另一方面可以降低循环气压缩机处理的循环气量,降低压缩机的能耗。五环工程公司申请的专利CN201310434044.0中,净化气依次通过四个甲烷化反应器发生甲烷化反应,用于制取SNG。其中,在第一和第二甲烷化反应器的甲烷化催化剂床层上部分别增加精脱硫催化剂层。第二甲烷化反应器出口的反应物料分成三股,一股送入3#甲烷化反应器,另两股经循环压缩机增压后循环送入第一和第二甲烷化反应器。大唐国际化工研究院申请的专利CN201310000949.7中,原料气经预热后分成四股,其中第一股原料气与蒸汽、第一股循环气混合后进入第一段甲烷化反应器发生反应;第一段产品气、第二股原料气、蒸汽、第二股循环气混合进入第二段甲烷化反应器发生反应;第二段产品气、第三股原料气、蒸汽混合进入第三段甲烷化反应器发生反应;第三段产品气分成两股,循环气和第二股第三段产品气,循环气经循环压缩机升压后分成两股,第一股循环气和第二股循环气;第二股第三段产品气、第四股原料气、蒸汽混合进入第四段甲烷化反应器发生反应,第四段产品气经气液分离后得到产品气。但是,现有的甲烷化工艺,绝大部分采用将第一级甲烷化或第二级甲烷化或后续甲烷化反应器出口的很大一部分产品气,通过压缩机加压后,循环至第一级甲烷化和/或第二级甲烷化反应器入口,通过产品气循环来稀释原料气,以达到控制第一级甲烷化和/或第二级甲烷化反应器反应温升的目的。由于甲烷化反应为强放热反应,为了有效控制第一级甲烷化和/或第二级甲烷化反应器的反应温升,现有的产品气循环工艺存在着循环气量过大,循环气压缩机能耗较大的问题。技术实现要素:本发明的目的就是为了克服上述现有技术存在的缺陷而提供一种循环气量小、能耗小的合成气制天然气的工艺。本发明的目的可以通过以下技术方案来实现:一种合成气制天然气的工艺,包括以下几个步骤:(1)原料合成气经脱硫装置脱硫,得到脱硫气;(2)步骤(1)所得脱硫气经过预热器换热后分成两股,第一股脱硫气通入第一甲烷化反应器的顶部,第二股脱硫气通入第二甲烷化反应器的顶部;(3)第一甲烷化反应器到第N甲烷化反应器依次连接,前一甲烷化反应器的底部产品气经余热回收器换热后进入后一甲烷化反应器的顶部,其中第M甲烷化反应器底部产品气经余热回收器换热后分成两股,第一股产品气通入第M+1甲烷化反应器的顶部,第二股产品气经循环气压缩机压缩后通入第一甲烷化反应器的顶部;N>M;(4)第N甲烷化反应器底部的产品气经余热回收器换热后进入气液分离罐中,气液分离罐底部得到的工艺凝液送至界外,气液分离罐顶部得到的粗SNG产品气通入脱CO2装置中;(5)脱CO2装置将粗SNG产品气分离得到SNG产品气、CO2和甲烷解吸气,所述甲烷解吸气返回至第一甲烷化反应器的顶部或者返回至步骤(2)中所述预热器的入口。优选的,N≥3,所述的甲烷化反应器为固定床绝热甲烷化反应器。优选的,所述的第一股脱硫气和步骤(1)中所述的脱硫气的流量比为(0.2~1):1。优选的,步骤(3)中所述的第二股产品气流量与第一股产品气和第二股产品气流量之和的比率为(0.05~0.8):1。优选的,所述的脱硫装置和脱CO2装置采用的净化方式包括物理吸收和/或化学吸收。更优选的,所述的脱硫装置和脱CO2装置采用的净化方式为物理吸收,吸收剂为低温甲醇。低温甲醇是指温度在-50℃以下的甲醇,此时的甲醇具有对酸性气体溶解度极大的优良特性,可以脱除原料气中的酸性气体,如CO2、H2S、COS等。优选的,每一个所述的甲烷化反应器后连有一台或多台余热回收器。回收的余热可用于公用工程,实现热集成,减少总能耗。所述的甲烷解吸气中包括甲烷、氢气、一氧化碳和二氧化碳,来自于脱CO2装置,在脱除CO2的过程中,为提高甲烷、氢气和一氧化碳等有效组分的回收率,通过闪蒸、气提、加热、压缩等方法从吸收剂富液或/和吸附剂中回收的气相物料,其气体组成包含但不限于甲烷、氢气、一氧化碳、二氧化碳等组分,其中甲烷的浓度为5%~40%,氢气的浓度为1%~15%,一氧化碳的浓度为0.1%~10%,二氧化碳的浓度为35%~85%。优选的,N个甲烷化反应器的物料进口温度为190~350℃。本发明通过对原料合成气先脱除含硫气体,先不脱除CO2,使含CO2的脱硫气经预热器预热后分为两股,一股与循环气压缩机出口的循环气以及与来自脱CO2装置的甲烷解吸气混合后,进入第一甲烷化反应器发生甲烷化反应,反应生成物进入第一余热回收器进行冷却;另一股与第一余热回收器出口的反应物料混合后,进入第二甲烷化反应器发生甲烷化反应。本发明采用含CO2的脱硫气,来自脱CO2装置的甲烷解吸气,循环气压缩机出口的循环气,三者混合后进入第一甲烷化反应器共同参与甲烷化反应,以达到控制甲烷化反应器反应温升的目的,最后再脱除粗SNG中的CO2,获得合格的SNG产品气。通过这一工艺,大大降低了循环气压缩机处理的循环气量,降低了循环气压缩机的过程能耗和设备投资。与现有技术相比,本发明的有益效果体现在以下几方面:(1)本发明大大降低了循环气压缩机处理的循环气量,降低了循环气压缩机的过程能耗和设备投资;(2)在CO2脱除过程中得到的甲烷解吸气返回至甲烷化反应器,能有效的控制甲烷化反应器的反应温升。每一个甲烷化反应器后面均设有余热回收器,回收的余热用于公用工程,实现热集成,降低总能耗。附图说明图1为现有的合成气制天然气的流程示意图一;图2位本发明的流程示意图一;图3为现有的合成气制天然气的流程示意图二;图4为本发明的流程示意图二;图5为本发明的流程示意图三。其中,1为原料合成气,2为第一主甲烷化反应器,3为第一余热回收器,4为第二主甲烷化反应器,5为第二余热回收器,6为第一副甲烷化反应器,7为第三余热回收器,8为第二副甲烷化反应器,9为第四余热回收器,10为气液分离罐,11为循环气压缩机,12为脱硫装置,13为脱CO2装置,14为甲烷解吸气,15为预热器,16为工艺凝液,17为粗SNG产品气,18为脱H2S和CO2装置,19为脱硫气,20为第一股脱硫气,21为第二股脱硫气,22为第一股产品气,23为第二股产品气,24为含硫气体,25为SNG产品气,26为CO2,27为净化气。具体实施方式下面对本发明的实施例作详细说明,本实施例在以本发明技术方案为前提下进行实施,给出了详细的实施方式和具体的操作过程,但本发明的保护范围不限于下述的实施例。实施例1当采用四级甲烷化反应,即N=4,M=1时,一种合成气制天然气的工艺,其流程如图2所示,包括以下步骤:原料合成气1进料量449kNm3/h,温度40℃,压力3.4MPaG,体积百分比组成:H2:46.22,CO:14.28,CO2:38.40,CH4:0.00,N2:0.23,H2S:0.87。原料合成气1经脱硫装置12脱除H2S等含硫组分,得到总硫含量<0.1ppm的脱硫气19,脱除的含硫气体24送至界区外;得到的脱硫气19进入预热器15进行预热,预热后的气体分为两股,第一股脱硫气20与循环气压缩机11出口的循环气以及与来自脱CO2装置13的甲烷解吸气14混合后,混合气体的温度达到320℃,进入第一甲烷化反应器2发生甲烷化反应,第一甲烷化反应器2出口温度约620℃,反应生成物进入第一余热回收器3进行冷却,冷却后的反应物料分为两股,第二股产品气23a进入循环气压缩机11,经升压后循环至第一甲烷化反应器2入口,第一股产品气22a与第二股脱硫气21混合后,混合气体的温度达到320℃,进入第二甲烷化反应器4发生甲烷化反应,第二甲烷化反应器4出口温度约620℃,反应生成物进入第二余热回收器5进行冷却,冷却后的反应物料温度250℃,进入第三甲烷化反应器6发生进一步甲烷化反应,第三甲烷化反应器6出口温度约451℃,反应生成物进入第三余热回收器7进行冷却,冷却后的反应物料,温度240℃,进入第四甲烷化反应器8发生进一步甲烷化反应,第四甲烷化反应器8出口温度273℃,反应生成物进入第四余热回收器9进行冷却,冷却后的反应生成物进入气液分离罐10,底部得到工艺凝液16,送至界区外,顶部得到粗SNG产品气17;得到的粗SNG产品气17进入脱CO2装置13脱除CO2,得到SNG产品气25,脱除的CO226送至界区外;得到SNG产品气25流量约70kNm3/h,温度40℃,压力2.2MPaG,体积百分比组成:H2:0.64,CO:0.03,CO2:0.00,CH4:97.89,N2:1.44,H2S:0.00;脱CO2过程中产生的甲烷解吸气14循环至第一甲烷化反应器2入口。脱硫装置12选用物理吸收的方法脱除H2S等含硫组分,选用低温甲醇作为吸收剂。脱CO2装置13选用物理吸收的方法脱除CO2,选用低温甲醇作为吸收剂。第一甲烷化反应器2、第二甲烷化反应器4、第三甲烷化反应器6和第四甲烷化反应器8为固定床绝热甲烷化反应器。在实施例1中,第一股脱硫气20和脱硫气19的流量比为0.55,第二股产品气23a流量与第一股产品气22a和第二股产品气23a流量之和的比率为0.50。循环气压缩机11的循环气量约213kNm3/h,所需压缩功约1045kW。对比例1采用如图1所示的现有的合成气制天然气的工艺,包括以下步骤:原料合成气1的进料量449kNm3/h,温度40℃,压力3.4MPaG,体积百分比组成:H2:46.22,CO:14.28,CO2:38.40,CH4:0.00,N2:0.23,H2S:0.87。原料合成气1经脱硫和CO2装置18脱除H2S和CO2后,得到总硫含量<0.1ppm的净化气27,脱除的含硫气体24和CO226送至界区外;得到的净化气27进入预热器15进行预热,预热后的气体分为两股,第一股净化气28与循环气压缩机11出口的循环气混合后,混合气体的温度达到320℃,进入第一甲烷化反应器2发生甲烷化反应,第一甲烷化反应器2出口温度约620℃,反应生成物进入第一余热回收器3进行冷却,冷却后分为两股,其中一股反应物料进入循环气压缩机11,经升压后循环至第一甲烷化反应器2入口,另一股反应物料与第二股净化气29混合,混合后气体的温度达到320℃,进入第二甲烷化反应器4发生甲烷化反应,第二甲烷化反应器4出口温度约620℃,反应生成物进入第二余热回收器5进行冷却,冷却后的反应物料温度250℃,进入第三甲烷化反应器6发生进一步甲烷化反应,第三甲烷化反应器6出口温度约436℃,反应生成物进入第三余热回收器7进行冷却,冷却后的反应物料,温度240℃,进入第四甲烷化反应器8发生进一步甲烷化反应,第四甲烷化反应器8出口温度318℃,反应生成物进入第四余热回收器9进行冷却,冷却后的反应生成物进入气液分离罐10,底部得到工艺凝液16,送至界区外,顶部得到SNG产品气25;SNG产品气25流量约70kNm3/h,温度40℃,压力2.2MPaG,体积百分比组成:H2:1.24,CO:0.00,CO2:0.00,CH4:97.28,N2:1.48,H2S:0.00。脱硫和CO2装置18选用物理吸收的方法脱除H2S和CO2等组分,选用低温甲醇作为吸收剂。在对比例1中,循环气压缩机11的循环气量约663kNm3/h,所需压缩功约3316kW。将实施例1和对比例1的能耗及产品进行对比,结果如表1所示:表1实施例1和对比例1的能耗及产品对比项目循环气量(kNm3/h)压缩功(kW)CH4含量实施例1213104597.89对比例1663331697.28减少/节省百分率(%)67.968.5——根据表1中的对比结果,可见,采用本发明的实施例1中的循环气压缩机的循环气量比采用现有技术的对比例1中的循环气量减少约67.9%,循环气压缩机的压缩功节省约68.5%,另外,采用本发明工艺所得的SNG产品气中CH4的含量更高。实施例2当采用四级甲烷化反应,即N=4,M=2时,一种合成气制天然气的工艺,其流程如图4所示,包括以下步骤:原料合成气1进料量315kNm3/h,温度40℃,压力3.65MPaG,体积百分比组成:H2:40.31,CO:12.06,CO2:33.92,CH4:12.69,N2:0.23,H2S:0.78。原料合成气1经脱硫装置12脱除H2S等含硫组分,得到总硫含量<0.1ppm的脱硫气19,脱除的含硫气体24送至界区外。得到的脱硫气19与来自脱CO2装置13的甲烷解吸气14混合后,进入预热器15进行预热,预热后的气体分为两股,第一股脱硫气20与循环气压缩机11出口的循环气混合后,混合气体的温度达到320℃,进入第一甲烷化反应器2发生甲烷化反应,第一甲烷化反应器2出口温度约620℃,反应生成物进入第一余热回收器3进行冷却,第二股脱硫气21与第一余热回收器3出口的反应物料混合后,混合气体的温度达到320℃,进入第二甲烷化反应器4发生甲烷化反应,第二甲烷化反应器4出口温度约620℃,反应生成物进入第二余热回收器5进行冷却,冷却后的反应物料分为两股,第二股产品气23b进入循环气压缩机11,经升压后循环至第一甲烷化反应器2入口,第一股产品气22b以温度240℃进入第三甲烷化反应器6发生进一步甲烷化反应,第三甲烷化反应器6出口温度约453℃,反应生成物进入第三余热回收器7进行冷却,冷却后的反应物料,温度230℃,进入第四甲烷化反应器8发生进一步甲烷化反应,第四甲烷化反应器8出口温度265℃,反应生成物进入第四余热回收器9进行冷却,冷却后的反应生成物进入气液分离罐10,底部得到工艺凝液16,送至界区外,顶部得到粗SNG产品气17。得到的粗SNG产品气17进入脱CO2装置13脱除CO2,得到SNG产品气25,脱除的CO226送至界区外;得到SNG产品气25量约83kNm3/h,温度40℃,压力2.4MPaG,体积百分比组成:H2:0.44,CO:0.02,CO2:0.00,CH4:98.67,N2:0.87,H2S:0.00;脱CO2过程中产生的甲烷解吸气14循环至预热器15的入口。脱硫装置12选用物理吸收的方法脱除H2S等含硫组分,选用低温甲醇作为吸收剂。脱CO2装置13选用物理吸收的方法脱除CO2,选用低温甲醇作为吸收剂。第一甲烷化反应器2、第二甲烷化反应器4、第三甲烷化反应器6和第四甲烷化反应器8为固定床绝热甲烷化反应器。在实施例2中,第一股脱硫气20和脱硫气19的流量比为0.25,第二股产品气23b流量与第一股产品气22b和第二股产品气23b流量之和的比率为0.12。循环气压缩机11的循环气量约37.3kNm3/h,所需压缩功约259kW。对比例2采用如图3所示的现有的合成气制天然气的工艺,包括以下步骤:原料合成气1的进料量315kNm3/h,温度40℃,压力3.65MPaG,体积百分比组成:H2:40.31,CO:12.06,CO2:33.92,CH4:12.69,N2:0.23,H2S:0.78。原料合成气1经脱H2S和CO2装置18脱除H2S和CO2后,得到总硫含量<0.1ppm的净化气27,脱除的含硫气体24和CO226送至界区外。得到的净化气27进入预热器15进行预热,预热后的气体分为两股,第一股净化气28与循环气压缩机11出口的循环气混合后,混合气体的温度达到320℃,进入第一甲烷化反应器2发生甲烷化反应,第一甲烷化反应器2出口温度约620℃,反应生成物进入第一余热回收器3进行冷却,第二股净化气29与第一余热回收器3出口的反应物料混合后,混合气体的温度达到320℃,进入第二甲烷化反应器4发生甲烷化反应,第二甲烷化反应器4出口温度约620℃,反应生成物进入第二余热回收器5进行冷却,冷却后的反应物料分为两股,一股反应物料进入循环气压缩机11,经升压后循环至第一甲烷化反应器2入口,另一股反应物料,温度250℃,进入第三甲烷化反应器6发生进一步甲烷化反应,第三甲烷化反应器6出口温度约430℃,反应生成物进入第三余热回收器7进行冷却,冷却后的反应物料,温度240℃,进入第四甲烷化反应器8发生进一步甲烷化反应,第四甲烷化反应器8出口温度310℃,反应生成物进入第四余热回收器9进行冷却,冷却后的反应生成物进入气液分离罐10,底部得到工艺凝液16,送至界区外,顶部得到SNG产品气25;SNG产品气25量约83kNm3/h,温度40℃,压力2.4MPaG,体积百分比组成:H2:1.28,CO:0.00,CO2:0.00,CH4:97.84,N2:0.88,H2S:0.00。脱硫和CO2装置18选用物理吸收的方法脱除H2S和CO2等组分,选用低温甲醇作为吸收剂。在对比例2中,循环气压缩机11的循环气量约153.4kNm3/h,所需压缩功约1073kW。将实施例2和对比例2的能耗及产品进行对比,结果如表2所示:表2实施例2和对比例2的能耗及产品对比项目循环气量(kNm3/h)压缩功(kW)CH4含量实施例237.325998.67对比例2153.4107397.84减少/节省百分率(%)75.775.9——根据表2中的对比结果,可见,采用本发明的实施例2中的循环气压缩机的循环气量比采用现有技术的对比例2中的循环气量减少约75.7%,循环气压缩机的压缩功节省约75.9%,另外,采用本发明工艺所得的SNG产品气中CH4的含量更高。实施例3采用与实施例1相同的工艺装置及原料气,其流程如图2所示,不同之处在于:(1)第一股脱硫气20和脱硫气19的流量比为0.2;(2)第二股产品气23a流量与第一股产品气22a和第二股产品气23a流量之和的比率为0.1;(3)第一甲烷化反应器的物料入口温度为250℃,第二甲烷化反应器的物料入口温度为190℃,第三甲烷化反应器的物料入口温度为200℃,第四甲烷化反应器的物料入口温度为190℃。经测试,循环气压缩机11的循环气量约10.6kNm3/h,所需压缩功约52kW。实施例4采用与实施例2类似的工艺装置及原料气,其流程如图5所示,不同之处在于:(1)实施例2中甲烷解吸气14返回至预热器15的入口,与脱硫气19混合后再进入预热器,而本实施例中甲烷解吸气14返回第一甲烷化反应器顶部入口;(2)第一股脱硫气20和脱硫气19的流量比为1;(3)第二股产品气23b流量与第一股产品气22b和第二股产品气23b流量之和的比率为0.05;(4)第一甲烷化反应器的物料入口温度为190℃,第二甲烷化反应器的物料入口温度为320℃,第三甲烷化反应器的物料入口温度为350℃,第四甲烷化反应器的物料入口温度为250℃。经测试,循环气压缩机11的循环气量约13.4kNm3/h,所需压缩功约92kW。实施例5采用与实施例1相同的原料气,不同之处在于:(1)本实施例采用三级甲烷化反应,即N=3,M=1;(2)第一股脱硫气20和脱硫气19的流量比为0.8;(3)第二股产品气23a流量与第一股产品气22a和第二股产品气23a流量之和的比率为0.8;(4)第一甲烷化反应器的物料入口温度为250℃,第二甲烷化反应器的物料入口温度为250℃,第三甲烷化反应器的物料入口温度为210℃。经测试,循环气压缩机11的循环气量约1099kNm3/h,所需压缩功约3925kW。本发明提出的一种利用合成气制天然气的节能工艺,已通过较佳的实施例子进行了描述,相关技术人员明显能在不脱离本
发明内容、精神和范围内对本文所述的工艺方法进行改动或适当变更与组合,来实现本发明技术。特别需要指出的是,所有相类似的替换和改动对本领域的技术人员是显而易见的,它们都会被视为包含在本发明精神、范围和内容中。当前第1页1 2 3