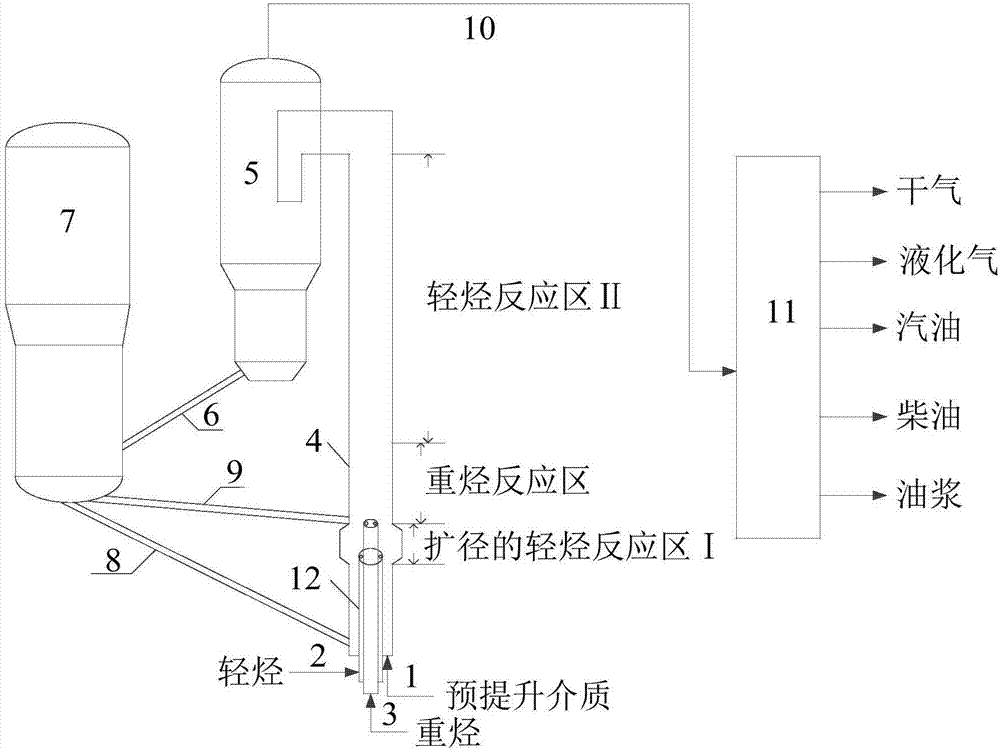
本发明涉及一种石油烃类催化转化方法,更具体的说,涉及一种在不存在氢的情况下,增产汽油和低碳烯烃的重质柴油和劣质重油催化转化方法。
背景技术:
:经济新常态下,中国主要成品油消费仍呈增长趋势,汽油刚性需求增长较快,而柴油需求增速大幅减少,2020年以前,我国汽油需求增速总体快于柴油;同时化工市场对乙烯、丙烯和丁二烯等低碳烯烃的需求越来越旺盛。由于我国原油普遍偏重,沸点小于200℃的石脑油馏分产量较低,只能提供不足50%的蒸汽裂解原料用于低碳烯烃的生产。催化裂化装置作为炼厂生产汽油和副产低碳烯烃的主要手段之一,提供了我国商品汽油池中75%的汽油组分和我国丙烯产品池中32%的丙烯组分,在炼油厂中占有举足轻重的地位。近几年来,随着我国消费柴汽比的逐渐下降,成品油市场发生变化,柴油库存急剧增加,柴油过剩问题凸显,已经影响到炼厂的正常运行,亟需减少柴油库存,增加汽油产量。国内外的历史数据研究表明:经济发展阶段、汽车行业发展水平是影响消费柴汽比趋势的决定性因素。2020年以前,我国汽油需求增速总体将快于柴油;替代能源对汽柴油需求变化趋势影响有限。预计2020年我国消费柴汽比将降至1.0左右。cn1382776公开了一种渣油加氢处理与重油催化裂化联合方法,该专利方法提出将催化裂化装置生产的重循环油和油浆中的澄清油混合在一起作为渣油装置进料的一部分,该物流加氢改质后与其它进料一起再回催化裂化装置加工,可提高催化裂化装置汽油和柴油收率。尽管汽油收率增加了2.8~3个单位,与加氢装置的成本高、氢耗和相应的能耗大相比,汽油收率的增幅并不理想。cn1422327a公布了将催化裂化装置生产的hco进行加氢处理后或与石脑油混合后进外置独立的催化裂化装置加工增产小分子烯烃和汽油的方法,该方法提出在外置的第二提升管催化裂化反应器中再裂化循环油可抑制与其它进料混合在单一提升管反应器反应时发生所不希望的氢转移反应,从而对进一步提高轻烯烃产率有利。虽然一定程度上提高了低碳烯烃的收率,但是该专利采用两根提升管联合加氢工艺处理相对轻质的石脑油,工艺复杂,投资成本高,工艺经济性并不高。cn103540359a公布了一种提高低碳烯烃和汽油收率的劣质重油催化转化工艺,该专利提出将提升管反应器划分为两个反应区,第一反应区为劣质重油与催化剂反应的区域,第二反应区为催化蜡油与柴油与催化剂反应的区域,提升管反应产生的油浆进入减压蒸馏塔,减压蒸馏塔上部出口的较低残炭轻馏分物料与中部出口的较高残炭重馏分物料共同进入加氢装置进行加氢处理;底部超高残炭油浆经过油浆过滤器处理后进入延迟焦化装置;加氢装置出来的低残炭易裂解物料进入提升管第一反应区再次进行反应。该专利利用催化裂化与、减压装置、加氢组合工艺进行联合操作,可以在一定程度上同时提高汽油和低碳烯烃收率,但是工艺较为复杂,需要对现有催化裂化装置进行较大的改造,投资成本高,实施较为困难。cn204981765u公布了一种劣质轻油及重油加工装置,其特征是:在重油进料喷嘴下方设置密相转化反应器,内部设置劣质轻油或/和烯烃气相进料分布器,或在预提升段或器中下部设置劣质轻油或/和烯烃气相进料喷嘴;设置劣质轻油或/和烯烃汽化器,其下部设置液相进口,上部设置气相出口并与密相转化反应器气相进料分布器或气相进料喷嘴连接。该装置用于焦化汽油、石脑油、烯烃等改质增产丙烯,并同时提高重质油裂化反应剂油比、改善产品分布提高经济效率。然而该专利并没有实施例,具体效果不得而知。从催化裂化原理的角度分析,由于该装置采用的轻烃为焦化汽油、石脑油、烯烃,采用密相转化反应器后,高温再生催化剂与这些轻烃在较大的剂油比条件下接触并反应,必然会导致轻烃过度裂化,副产物干气会大大增加。cn102746880a公布了一种轻烃和重油耦合催化裂化汽油、柴油和乙烯、丙烯的方法,该发明通过采用并列式或同轴式复合提升管循环反应-再生装置;预热的轻烃进入内嵌提升管反应器,与催化剂ⅰ接触,生成含低碳烯烃的产品,并形成积炭催化剂ⅱ;预热的重油进入外置提升管反应器,与催化剂ⅰ接触,生成含汽油、柴油的产品,并形成积碳催化剂ⅲ,积炭催化剂ⅱ和ⅲ进入再生器,再生后的催化剂ⅰ返回反应器。该专利采用两个提升管反应器,内嵌式提升管采用混合c4、fcc轻汽油、轻石脑油、轻柴油作为原料,外嵌式提升管采用大庆混合油或大庆减压渣油为原料,汽油收率较低,而且工艺较为复杂,实施难度大。因此,如何利用催化裂化装置将重质柴油和劣质重油更多地转化为汽油和低碳烯烃,成为科研人员关注的焦点和需要解决的关键问题。技术实现要素:本发明的目的是在现有技术的基础上提供一种以重质柴油和劣质重油为原料,同时提高汽油和低碳烯烃收率的催化转化方法。本发明提供一种增产汽油和低碳烯烃的催化转化方法,所述方法包括:所述反应区为沿提升管反应器垂直方向从下至上的扩径的轻烃反应区ⅰ、重烃反应区、轻烃反应区ⅱ;从再生器引入两根再生剂输送管分别将再生催化剂输送到扩径的轻烃反应区ⅰ和重烃反应区,将预热的轻烃和重烃从一体式喷嘴同时分别喷入轻烃反应区ⅰ和重烃反应区,与来自再生器的催化剂接触进行催化裂化反应;所述轻烃是馏程为140~320℃的石油烃馏分,所述重烃为初馏点≥245℃的石油烃类馏分和/或含有碳氢化合物的动植物油脂和/或煤炭液化产物,轻烃与重烃的质量比为0.001:1~0.55:1;所述催化剂为催化裂化催化剂,所述方法包括以下步骤:(1)、预提升介质从提升管反应器底部向上喷出,轻烃从一体式喷嘴中的轻烃喷头喷出,在扩径的轻烃反应区ⅰ与来自再生器的高温再生催化剂接触并反应,生成的反应产物和反应后的积炭催化剂向上运动进入重烃反应区;(2)、重烃从一体式喷嘴中的重烃外喷头喷出,从重烃反应区底部进入反应器,与来自再生器的高温再生催化剂和来自扩径的轻烃反应区ⅰ向上运动的积炭催化剂共同接触并反应,生成的反应产物和反应后的催化剂向上运动进入轻烃反应区ⅱ;(3)、生成的反应产物和催化剂在离开轻烃反应区ⅱ后,进入旋风分离系统;(4)、反应产物分离后,待生催化剂进入汽提器进行汽提,汽提后的催化剂进入再生器,经过再生器烧焦后再进入提升管扩径的轻烃反应区ⅰ或重烃反应区循环使用;反应产物经过油气管线进入分馏塔进行分馏得到相应产品。本发明所述的增产汽油和减少油浆的催化裂化转化方法,所述一体式喷嘴包括轻烃喷嘴、轻烃套管、重烃喷嘴和重烃套管,轻烃喷嘴上设有轻烃喷头,重烃喷嘴上设有重烃外喷头,轻烃喷头和重烃外喷头能够同时分别喷出轻烃和重烃;所述一体式喷嘴中的轻烃套管与重烃外套管同轴,重烃外套管的外管壁与轻烃套管的内管壁构成轻烃环形雾化室;重烃外喷头上均匀地开有1~5个重烃外喷孔,轻烃喷头上均匀地开有4~10个轻烃喷孔,轻烃套管的外径与重烃外套管的外径之比为2.20:1~2.28:1,轻烃喷头上单个轻烃喷孔的孔径与重烃外喷头上单个重烃外喷孔的孔径之比为0.1:1~2.0:1。本发明所述的增产汽油和减少油浆的催化裂化转化方法,所述扩径的轻烃反应区ⅰ的提升管反应器内径与重烃反应区的提升管反应器内径之比为1.1:1~3:1。本发明所述的增产汽油和减少油浆的催化裂化转化方法,扩径的轻烃反应区ⅰ、重烃反应区、轻烃反应区ⅱ的高度分别占提升管反应器总高度的1~15%、1~40%、1~60%。本发明所述的增产汽油和减少油浆的催化裂化转化方法,预提升介质选自氮气、氦气、催化裂化干气、水蒸汽中的一种或两种以上的混合物。本发明所述的增产汽油和减少油浆的催化裂化转化方法,扩径的轻烃反应区ⅰ中的轻烃是沸点范围为140~320℃、硫含量为0.03~0.27重量%、十六烷值为55~65的馏分油,选自常减压装置直馏柴油、减压柴油、加氢柴油、渣油加氢柴油、焦化柴油、催化柴油、催化裂化装置轻/重循环油中的一种或两种以上的混合物。本发明所述的增产汽油和减少油浆的催化裂化转化方法,重烃反应区的重烃为初馏点≥245℃的石油烃类馏分和/或含有碳氢化合物的动植物油脂和/或煤炭液化产物,具体而言是选自常压瓦斯油、减压瓦斯油、减压渣油、常压渣油、劣质柴油、煤焦油、渣油加氢尾油、溶剂脱沥青油、抽余油、焦化蜡油、页岩油、油砂沥青、重质原油、含有碳氢化合物的动植物油脂、煤炭液化产物的一种或两种以上的混合物。本发明所述的增产汽油和减少油浆的催化裂化转化方法,扩径的轻烃反应区ⅰ的轻烃油剂接触温度为450~710℃,优选590~650℃;反应压力为常压至320千帕,优选100~270千帕;停留时间为0.05~3s,优选0.1~0.7s;催化剂与轻烃的剂油比为5:1~160:1,优选15:1~130:1;轻烃与重烃的质量比为0.001:1~0.55:1,优选0.05:1~0.15:1;再生催化剂的温度为570~755℃,优选630~720℃。本发明所述的增产汽油和减少油浆的催化裂化转化方法,重烃反应区内的重烃油剂接触温度为450~640℃,优选500~600℃;催化剂与该段原料的剂油比为5:1~25:1,优选6:1~18:1;油气分子的停留时间为0.05~2.5s,优选0.5~1.5s;反应压力为常压至320千帕,优选100~270千帕。本发明提供的方法可以将常规的催化裂化装置适当改造后进行。本发明提供的方法的理论依据是:由于催化剂中b酸主要是由分子筛提供的,而分子筛的孔道直径小,常规催化裂化反应中,重烃大分子在提升管反应器底部与分子筛接触时很难进入分子筛中与酸性中心接触发生反应,再生催化剂从再生器中循环出来的温度约680℃左右,此时重烃大分子容易瞬间在分子筛孔道外结焦,从而堵塞了分子筛孔道,影响裂化效果。本发明中从再生器循环至提升管反应器的高温再生催化剂首先与轻烃(如直馏柴油)在扩径的轻烃反应区ⅰ接触反应,一方面由于扩径的轻烃反应区ⅰ提升管反应器的内径比重烃反应区的要大,轻烃(如直馏柴油)在扩径的轻烃反应区ⅰ的反应时间延长,使得轻烃(如直馏柴油)在高温下快速裂解生成大量小分子烯烃的时间延长,再生催化剂上的b酸中心与小分子烯烃发生催化反应生成大量的正碳离子,正碳离子向上运动至重烃反应区后引发重烃大分子的链反应,促进重油大分子的迅速裂解,产生更多的正碳离子;另一方面由于从再生器引入一根再生剂输送管将再生催化剂输送到提升管反应器的重烃反应区,使得重烃反应区的催化剂平均活性提高,强化了重烃的高效转化,从而达到增产汽油和低碳烯烃的多重效果。本发明的有益效果是:(1)、由于采用了一体式喷嘴,经过加热的轻烃(如直馏柴油)从轻烃喷头上均匀分布的多个轻烃喷孔中喷出,形成均匀分散的轻烃(如直馏柴油)油滴,保证催化剂与轻烃(如直馏柴油)油滴均匀接触,防止轻烃(如直馏柴油)与催化剂形成沟流;经过加热的重烃从重烃外喷头上均匀分布的多个重烃外喷孔中喷出,形成均匀分散的重烃油滴,保证催化剂与重烃油滴均匀接触;(2)、均分分散的轻烃(如直馏柴油)油滴在扩径的轻烃反应区ⅰ内与催化剂接触反应,由于扩径的轻烃反应区ⅰ提升管反应器的内径比重烃反应区的要大,轻烃(如直馏柴油)在扩径的轻烃反应区ⅰ的反应时间延长,轻烃(如直馏柴油)在高温下快速裂解生成大量小分子烯烃,再生催化剂上的b酸中心与小分子烯烃发生催化反应生成大量的正碳离子,正碳离子向上运动至重烃反应区后引发重烃大分子的链反应,促进重油大分子的迅速裂解,产生更多的正碳离子,加速重烃的裂解;(3)、由于从再生器引入一根再生剂输送管将再生催化剂输送到提升管反应器的重烃反应区,使得重烃反应区的催化剂平均活性提高,强化了重烃的高效转化,从而达到增产汽油和低碳烯烃的多重效果。附图说明图1为本发明的增产汽油和低碳烯烃的催化裂化转化方法所采用的装置流程图;图2是一体式喷嘴的放大示意图;图3为采用常规喷嘴进行试验时的装置流程图;其中:1-预提升介质,2-轻烃,3-重烃,4-提升管反应器,5-汽提器,6-待生剂输送管,7-再生器,8-第一再生剂输送管,9-第二再生剂输送管,10-油气管线,11-分馏塔,12-一体式喷嘴。13-轻烃入口,14-重烃入口,15-轻烃喷嘴,16-轻烃喷头,17-重烃喷嘴,18-重烃外喷头,19-重烃外套管,20-轻烃套管,21-环形雾化室,32-轻烃喷孔,33-重烃外喷孔。22-预提升介质,23-混合原料,24-提升管反应器,25-汽提器,26-待生剂输送管,27-再生器,28-再生剂输送管,29-油气管线,30-分馏塔,31-常规喷嘴。具体实施方式下面结合附图和实施例对本发明所提供的方法予以进一步的说明,但这些实施例不应认为是对本发明的限制。主要分析方法:各实施例中,na2o、al2o3等化学组成用x射线荧光法测定(参见《石油化工分析方法(ripp实验方法)》,杨翠定等编,科学出版社,1990年出版)。物相采用x射线衍射法测定。比表面、孔体积由低温氮吸附-脱附法测定;粒径分布采用激光粒度分析(分析方法gb/t19077.1-2008);磨损指数采用磨损指数的测定(直管法)(分析方法gb/t15458-1995);微反活性(ma)评价:采用astm-d3907方法。催化剂预先在800℃、100%水蒸汽条件下处理17h,以大港轻柴油作为反应原料油。反应温度460℃,进油时间70s,催化剂装量2.5~5g,反应后汽油的产率采用gc7890分析。主要原料及来源:ldo-70新鲜催化剂,兰州石化公司催化剂厂生产,评价前经过800℃、100%水蒸气水热减活处理10h,ldo-70老化后的理化性质见表1。表1催化剂理化性质轻烃取自兰州石化公司500万吨/年常减压装置的常三线柴油(性质见表2);重烃取自兰州石化公司300万吨/年催化裂化装置的新鲜催化原料(性质见表3),新鲜催化原料中减压蜡油与减压渣油混合质量比例为(6:4),减压蜡油是来自兰州石化公司550万吨常减压装置的减压蜡油,减压渣油是来自兰州石化公司550万吨常减压装置的减压渣油。评价装置采用洛阳石化工程公司生产的灵活反应模式型催化裂化提升管试验装置。表2轻烃的性质表3重烃的性质项目测试数据项目测试数据分子量/(g·mol-1)432w(饱和烃)/%61.620℃密度/(kg·m-3)877.9w(芳烃)/%24.9100℃运动黏度/(mm2·s-1)17.08w(胶质+沥青质)/%13.5w(残炭)/%5.04w(重金属)/(μg·g-1)闪点/℃224fe60.50w(元素)/%ni9.14s0.61v22.12n0.29na9.00实施例1采用图1所示的装置和图2所示的一体式喷嘴进行试验。扩径的轻烃反应区ⅰ、重烃反应区、轻烃反应区ⅱ的高度分别占提升管反应器总高度的5%、35%、55%。扩径的轻烃反应区ⅰ的提升管反应器内径与重烃反应区的提升管反应器内径之比为1.5:1。一体式喷嘴12的轻烃套管20的外径与重烃外套管19的外径之比为2.20:1,轻烃喷头16上单个轻烃喷孔的孔径与重烃外喷头18上单个重烃外喷孔的孔径之比为1.429:1。预提升介质为氮气。质量流率为150g/h的500万常三线柴油从一体式喷嘴12的轻烃喷头16上4个轻烃喷孔32喷出,在提升管反应器4内扩径的轻烃反应区ⅰ与经第一再生剂输送管8输送来的再生催化剂接触并反应,在轻烃油剂接触温度620℃、剂油比64.4、停留时间0.2s、500万常三线柴油与300万催料的重量比质量比0.1:1、反应压力为130千帕、再生催化剂温度670℃的条件下,反应后的催化剂继续向上运动;质量流率为1500g/h的300万催料从一体式喷嘴12的重烃外喷头18上4个重烃外喷孔33喷出,在重烃反应区与第二再生剂输送管9输送来的再生催化剂和来自扩径的轻烃反应区ⅰ向上运动的积炭催化剂共同接触并反应,在重烃油剂接触温度530℃、反应器出口温度505℃、剂油比8、反应时间1.9s、反应压力145千帕的条件下,反应后的产物与催化剂继续向上运动,经过轻烃反应区ⅱ后进入汽提器5进行汽提,汽提后的待生催化剂经过待生剂输送管6进入再生器7进行烧焦,烧焦后的催化剂经过第一再生剂输送管8和第二再生剂输送管9进入提升管反应器4。提升管反应器4和汽提器5反应产生的油气经过油气管线10进入分馏塔11,分离成干气、液化气、汽油、柴油和油浆。具体反应条件和反应结果见表4。对比例1对比例1采用的常规喷嘴为专利cn201120267386.4所述的一种催化裂化雾化进料喷嘴,采用图3所示的装置进行试验。质量流率为1650g/h的300万催料与500万常三线柴油的混合原料(500万常三线柴油与300万催料的质量比为0.1:1)从常规喷嘴31喷出,与催化剂接触反应,在油剂接触温度530℃、反应器出口温度505℃、剂油比8、反应时间2.1s、反应压力145千帕的条件下,反应后的产物与催化剂继续向上运动,进入汽提器25进行汽提,汽提后的催化剂经过待生剂输送管26进入再生器27进行烧焦,烧焦后的催化剂经过再生剂输送管28进入提升管反应器24。提升管反应器24和汽提器25反应产生的油气经过油气管线29进入分馏塔30,分离成干气、液化气、汽油、柴油和油浆。具体反应条件和反应结果见表4。表4实施例1与对比例1的反应条件和反应结果实施例2采用图1所示的装置和图2所示的一体式喷嘴进行试验。扩径的轻烃反应区ⅰ、重烃反应区、轻烃反应区ⅱ的高度分别占提升管反应器总高度的5%、35%、55%。扩径的轻烃反应区ⅰ的提升管反应器内径与重烃反应区的提升管反应器内径之比为1.5:1。一体式喷嘴12的轻烃套管20的外径与重烃外套管19的外径之比为2.20:1,轻烃喷头16上单个轻烃喷孔的孔径与重烃外喷头18上单个重烃外喷孔的孔径之比为1.429:1。预提升介质为氮气。质量流率为150g/h的500万常三线柴油从一体式喷嘴12的轻烃喷头16上4个轻烃喷孔32喷出,在提升管反应器4内扩径的轻烃反应区ⅰ与经第一再生剂输送管8输送来的再生催化剂接触反应,在轻烃油剂接触温度590℃、剂油比64.4、停留时间0.2s、500万常三线柴油与300万催料的重量比质量比0.1:1、反应压力为125千帕、再生催化剂温度630℃的条件下,反应后的催化剂继续向上运动,质量流率为1500g/h的300万催料从一体式喷嘴12重烃外喷头18上4个重烃外喷孔33喷出,在重烃反应区与第二再生剂输送管9输送来的再生催化剂和来自扩径的轻烃反应区ⅰ向上运动的积炭催化剂共同接触并反应,在重烃油剂接触温度515℃、反应器出口温度500℃、剂油比8、反应时间1.9s、反应压力140千帕的条件下,反应后的产物与催化剂继续向上运动,经过轻烃反应区ⅱ后进入汽提器5进行汽提,汽提后的待生催化剂经过待生剂输送管6进入再生器7进行烧焦,烧焦后的催化剂经过第一再生剂输送管8和第二再生剂输送管9进入提升管反应器4。提升管反应器4和汽提器5反应产生的油气经过油气管线10进入分馏塔11,分离成干气、液化气、汽油、柴油和油浆。具体反应条件和反应结果见表5。对比例2对比例2采用的常规喷嘴为专利cn201120267386.4所述的一种催化裂化雾化进料喷嘴,采用图3所示的装置进行试验。质量流率为1650g/h的300万催料与500万常三线柴油的混合原料(500万常三线柴油与300万催料的质量比为0.1:1)从常规喷嘴31喷出,与催化剂接触反应,在油剂接触温度515℃、反应器出口温度500℃、剂油比8、反应时间2.1s、反应压力140千帕的条件下,反应后的产物与催化剂继续向上运动,进入汽提器25进行汽提,汽提后的催化剂经过待生剂输送管26进入再生器27进行烧焦,烧焦后的催化剂经过再生剂输送管28进入提升管反应器24。提升管反应器24和汽提器25反应产生的油气经过油气管线29进入分馏塔30,分离成干气、液化气、汽油、柴油和油浆。具体反应条件和反应结果见表5。表5实施例2与对比例2的反应条件和反应结果实施例3采用图1所示的装置和图2所示的一体式喷嘴进行试验。扩径的轻烃反应区ⅰ、重烃反应区、轻烃反应区ⅱ的高度分别占提升管反应器总高度的5%、35%、55%。扩径的轻烃反应区ⅰ的提升管反应器内径与重烃反应区的提升管反应器内径之比为1.5:1。一体式喷嘴12的轻烃套管20的外径与重烃外套管19的外径之比为2.20:1,轻烃喷头16上单个轻烃喷孔的孔径与重烃外喷头18上单个重烃外喷孔的孔径之比为1.429:1。预提升介质为氮气。质量流率为150g/h的500万常三线柴油从一体式喷嘴12的轻烃喷头16上4个轻烃喷孔32喷出,在提升管反应器4内扩径的轻烃反应区ⅰ与经第一再生剂输送管8输送来的再生催化剂接触反应,在轻烃油剂接触温度650℃、剂油比64.4、停留时间0.2s、500万常三线柴油与300万催料的重量比质量比0.1:1、反应压力为135千帕、再生催化剂温度710℃的条件下,反应后的催化剂继续向上运动,质量流率为1500g/h的300万催料从一体式喷嘴12的重烃外喷头18上4个重烃外喷孔33喷出,在重烃反应区与第二再生剂输送管9输送来的再生催化剂和来自扩径的轻烃反应区ⅰ向上运动的积炭催化剂共同接触并反应,在重烃油剂接触温度540℃、反应器出口温度510℃、剂油比8、反应时间1.9s、反应压力145千帕的条件下,反应后的产物与催化剂继续向上运动,经过轻烃反应区ⅱ后进入汽提器5进行汽提,汽提后的待生催化剂经过待生剂输送管6进入再生器7进行烧焦,烧焦后的催化剂经过第一再生剂输送管8和第二再生剂输送管9进入提升管反应器4。提升管反应器4和汽提器5反应产生的油气经过油气管线10进入分馏塔11,分离成干气、液化气、汽油、柴油和油浆。具体反应条件和反应结果见表6。对比例3对比例3采用的常规喷嘴为专利cn201120267386.4所述的一种催化裂化雾化进料喷嘴,采用图3所示的装置进行试验。质量流率为1650g/h的300万催料与500万常三线柴油的混合原料(500万常三线柴油与300万催料的质量比为0.1:1)从常规喷嘴31喷出,与催化剂接触反应,在油剂接触温度540℃、反应器出口温度510℃、剂油比8、反应时间2.1s、反应压力145千帕的条件下,反应后的产物与催化剂继续向上运动,进入汽提器25进行汽提,汽提后的催化剂经过待生剂输送管26进入再生器27进行烧焦,烧焦后的催化剂经过再生剂输送管28进入提升管反应器24。提升管反应器24和汽提器25反应产生的油气经过油气管线29进入分馏塔30,分离成干气、液化气、汽油、柴油和油浆。具体反应条件和反应结果见表6。表6实施例3与对比例3的反应条件和反应结果实施例1与对比例1相比,在进料质量完全相同、进料喷嘴和进料方法不同的反应条件下,反应后汽油收率提高了5.13个百分点,总液收提高了2.61个百分点,转化率提高了12.09个百分点,柴油收率降低了7.91个百分点,重油收率降低了4.18个百分点,丙烯收率提高了1.99个百分点,丁烯收率提高了2.45个百分点。实施例2与对比例2相比,在进料质量完全相同、进料喷嘴和进料方法不同的反应条件下,反应后汽油收率提高了4.99个百分点,总液收提高了2.27个百分点,转化率提高了11.39个百分点,柴油收率降低了7.62个百分点,重油收率降低了3.77个百分点,丙烯收率提高了1.70个百分点,丁烯收率提高了2.13个百分点。实施例3与对比例3相比,在进料质量完全相同、进料喷嘴和进料方法不同的反应条件下,反应后汽油收率提高了4.66个百分点,总液收提高了2.09个百分点,转化率提高了12.93个百分点,柴油收率降低了8.92个百分点,重油收率降低了4.01个百分点,丙烯收率提高了2.35个百分点,丁烯收率提高了2.94个百分点。实施例与对比例的数据表明,本发明具有增产汽油和低碳烯烃的特点。当然,本发明还可有其它多种实施例,在不背离本发明精神及其实质的情况下,熟悉本领域的技术人员可根据本发明作出各种相应的改变和变形,但这些相应的改变和变形都应属于本发明的保护范围。当前第1页12