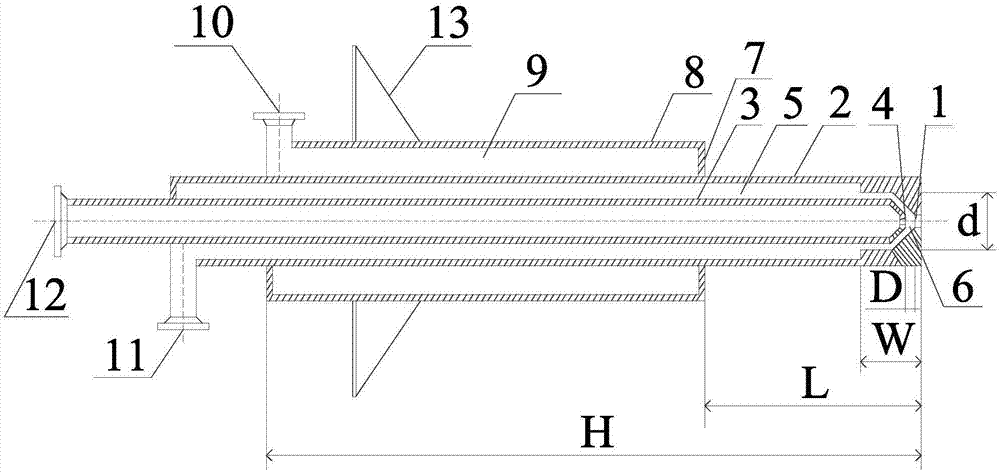
本发明涉及一种石油烃类的催化裂化转化装置,更具体的说,涉及一种催化裂化提升管进料喷嘴及应用。
背景技术:
:催化裂化作为炼油工业主要的轻质油品生产工艺,因其适用性广、加工成本相对低廉而受到了国内外主要研发机构的广泛关注。催化裂化提供了我国商品汽油池中75%的汽油组分,在炼油厂中占有举足轻重的地位。在催化裂化工艺和催化剂研发过程中,催化裂化提升管试验装置在催化裂化催化剂配方筛选、催化原料裂化性能及产品性质考察、催化裂化催化剂评价、工业装置反应工艺条件的优化与模拟、催化裂化催化剂放大试生产验证等方面发挥了重要作用。在催化裂化提升管试验装置运转过程中,喷嘴作为催化原料雾化的重要部件,直接影响催化裂化试验研究的结果。喷嘴的形式也直接关系着催化裂化工艺的开发。目前,国内外使用的催化裂化进料喷嘴大致分为两种,第一种是内部结构采用收缩与扩张形式,利用气液两相的速度差,达到强化原料的目的,如中国专利cn1304979a;第二种是采用蒸汽注入到原料油中,利用喷嘴内的压力高于反应器内部的压力,使原料中的气泡在差压作用下膨胀并发生爆裂,达到原料雾化的目的,如中国专利cn1282777y、cn2754736y等。然而,所有的催化裂化进料喷嘴都只能喷出一种原料,只能用于催化裂化试验装置一种原料油的评价与试验,不能在一个喷嘴上喷出两种原料。随着工业催化裂化装置加工的原料越来越复杂多变,催化裂化试验装置需要模拟工业催化裂化装置的方面也越来越多。近年来,随着我国消费柴汽比的逐渐下降,成品油市场发生变化,柴油库存急剧增加,柴油过剩问题凸显,已经影响到炼厂的正常运行,亟需减少柴油库存,增加汽油产量。国内部分炼厂已经开始将一部分重质柴油掺炼到工业催化裂化装置中,以减少柴油的产量。重质柴油在提升管反应器的什么反应区与催化剂进行反应可以最大限度地减少柴油产量,成为科研人员关注的焦点。催化裂化提升管试验装置在模拟工业催化裂化装置掺炼重质柴油时,由于现有的进料喷嘴只能喷出一种催化裂化原料,无法模拟重质柴油喷出与催化剂接触并反应。因此,如何开发出能够同时喷出两种原料的进料喷嘴尤为重要。技术实现要素:本发明的目的是针对现有进料喷嘴存在的问题,在现有技术的基础上提供一种催化裂化提升管喷嘴及应用,该喷嘴能够同时喷出两种原料,并且能够保证油气得到充分雾化,与催化剂接触更加均匀,不仅结构简单,使用方便,而且操作弹性好。本发明提供一种催化裂化提升管喷嘴及应用,采用的技术方案是:一种催化裂化提升管喷嘴,包括:烃油ⅰ外喷头1,烃油ⅰ外套管2,烃油ⅰ内套管3,烃油ⅰ内喷头4,蒸汽腔5,烃油ⅰ与蒸汽混合室6,烃油ⅱ喷头7,烃油ⅱ套管8,烃油ⅱ环形雾化室9,烃油ⅱ进料入口10,蒸汽进料入口11,烃油ⅰ进料入口12,卡套式接头13,,烃油ⅰ外喷孔35,烃油ⅰ内喷孔36,烃油ⅱ喷孔37,所述烃油ⅰ内套管3设置在烃油ⅰ外套管2的内部且与其同轴,烃油ⅰ内套管3的顶端与烃油ⅰ内喷头4相连通,烃油ⅰ内套管3的底端与烃油ⅰ进料入口12相连通;烃油ⅰ外套管2与烃油ⅱ套管8同轴,烃油ⅱ套管8的外径大于烃油ⅰ外套管2的外径,烃油ⅰ外套管2的顶端与烃油ⅰ外喷头1相连通,烃油ⅰ外套管2的底端与蒸汽进料入口11相连通,烃油ⅱ套管8的顶端与烃油ⅱ喷头7相连通,烃油ⅱ套管8的底端与烃油ⅱ进料入口10相连通;烃油ⅱ套管8与烃油ⅰ外套管2通过密封面或焊接方式密封连接;烃油ⅰ内套管3的外管壁与烃油ⅰ外套管2的内管壁形成的环形空腔构成蒸汽腔5,蒸气腔5的顶端与烃油ⅰ外喷头1相连通,蒸气腔5的底端与蒸汽进料入口11相连通;烃油ⅰ内喷头4与烃油ⅰ外喷头1之间的腔室构成烃油ⅰ与蒸汽混合室6,烃油ⅰ与蒸汽混合室6与烃油ⅰ外喷头1相连通;烃油ⅰ外套管2的外管壁与烃油ⅱ套管8的内管壁形成的环形空腔构成烃油ⅱ环形雾化室9,烃油ⅱ环形雾化室9的顶端与烃油ⅱ喷头7相连通,烃油ⅱ环形雾化室9的底端与烃油ⅱ进料入口10相连通;烃油ⅰ外喷孔35位于烃油ⅰ外喷头1上,烃油ⅰ内喷孔36位于烃油ⅰ内喷头4上,烃油ⅱ喷孔37位于烃油ⅱ喷头7上;卡套式接头13安装在烃油ⅱ套管8,催化裂化提升管喷嘴通过卡套式接头13与催化裂化提升管试验装置提升管反应器底部相连通。本发明所述的催化裂化提升管喷嘴,所述烃油ⅰ外套管2顶端设有烃油ⅰ外喷头1,烃油ⅰ外喷头1上的烃油ⅰ外喷孔35设置1-5个,所述烃油ⅰ外喷孔35在烃油ⅰ外喷头1上均匀排列,每个喷孔孔径为0.6~2.0mm。本发明所述的催化裂化提升管喷嘴,所述烃油ⅰ内喷头4上设有1个烃油ⅰ内喷孔36,所述烃油ⅰ内喷孔36位于烃油ⅰ内喷头4上,喷孔孔径为1.1~1.5mm。本发明所述的催化裂化提升管喷嘴,所述烃油ⅱ套管8顶端的环形截面设有烃油ⅱ喷头7,烃油ⅱ喷头7上的烃油ⅱ喷孔37设置4-10个,所述烃油ⅱ喷孔37在烃油ⅱ喷头7上均匀排列,每个喷孔孔径为0.6~1.1mm。本发明所述的催化裂化提升管喷嘴,烃油ⅰ内喷头4与烃油ⅰ外喷头1的间距d为3~5mm。本发明所述的催化裂化提升管喷嘴,蒸汽腔5缩径后的直径d为4.5~5.0mm。本发明所述的催化裂化提升管喷嘴,烃油ⅱ喷头7和烃油ⅰ外喷头1的间距l与烃油ⅱ进料入口10和烃油ⅰ外喷头1的间距h之比为0.50:1~0.67:1。本发明所述的催化裂化提升管喷嘴,蒸汽腔5缩径段长度w与烃油ⅱ进料入口10和烃油ⅰ外喷头1的间距h之比为0.018:1~0.048:1。本发明所述的催化裂化提升管喷嘴,蒸汽腔5缩径后的直径d与烃油ⅰ内套管3的外径之比为1.667:1~1.800:1。本发明所述的催化裂化提升管喷嘴,烃油ⅱ套管8的外径与烃油ⅰ外套管2的外径之比为2.20:1~2.28:1。本发明所述的催化裂化试验用喷嘴,烃油ⅰ外套管2的内径与烃油ⅰ内套管3的内径之比为4.000:1~5.333:1。本发明所述的催化裂化试验用喷嘴,烃油ⅱ喷头7上单个烃油ⅱ喷孔37的孔径与烃油ⅰ外喷头1上单个烃油ⅰ外喷孔35的孔径之比为0.1:1~2.0:1。本发明所述的催化裂化提升管喷嘴,所述烃油ⅱ喷头7喷出的原料为轻烃,轻烃是馏程为180~380℃的石油烃馏分;所述烃油ⅰ外喷头(1)喷出的原料为重烃,重烃为馏程为≥245℃的石油烃馏分,轻烃与重烃的质量比为0.001:1~0.55:1。本发明所述催化裂化提升管喷嘴应用于配套的催化裂化提升管工艺,包括将预热的轻烃和重烃从催化裂化提升管喷嘴同时分别喷入提升管反应器内不同的反应区,与来自再生器的催化剂接触进行催化裂化反应;所述反应区为沿反应器垂直方向从下至上的轻烃反应区ⅰ、重烃反应区、轻烃反应区ⅱ;所述应用包括下列步骤:(1)、预提升介质从提升管底部向上喷出,轻烃从催化裂化提升管喷嘴上的烃油ⅱ喷头7喷出,进入轻烃反应区ⅰ与再生催化剂接触进行催化裂化反应,生成的反应产物和反应后的含积炭催化剂向上流动进入重烃反应区;(2)、重烃从催化裂化提升管喷嘴上的烃油ⅰ外喷头1喷出,单独从重烃反应区底部进入反应器,与来自轻烃反应区ⅰ的反应产物和催化剂接触进行催化裂化反应,生成的反应产物和反应后的催化剂向上运动进入轻烃反应区ⅱ;(3)、在轻烃反应区ⅱ的反应产物和催化剂接触进行催化裂化反应后,反应产物与含积炭的催化剂由顶部出口流出反应器,进入旋风分离系统进行分离;(4)、分离出的含积炭的催化剂进入汽提器进行汽提后进入再生器烧焦再生,再生催化剂返回反应器底部循环使用;反应产物经过油气管线进入分馏塔进行分馏得到相应产品。本发明所述的一种催化裂化提升管喷嘴的应用,所述轻烃反应区ⅰ、重烃反应区、轻烃反应区ⅱ的高度分别占提升管反应器总高度的1~15%、1~40%、1~60%。本发明所述的一种催化裂化提升管喷嘴的应用,所述催化剂为催化裂化催化剂。该喷嘴应用时,将其装配到催化裂化提升管试验装置的提升管反应器底部,按照事先设定好的试验条件进行试验。本发明与现有技术相比具有以下优点和有益效果:1、由于在催化裂化提升管喷嘴上设置了烃油ⅱ环形雾化室,使得本发明所述的喷嘴能够同时喷出两种原料,可以用于催化裂化提升管试验装置进行不同催化原料同时与催化剂接触并反应的试验研究。2、由于喷出两种原料的喷头上都设置了一个以上的圆形喷孔,可以形成更加均匀分散的烃油油滴,保证催化剂与烃油油滴均匀接触,防止烃油油滴与催化剂形成沟流。3、由于烃油ⅱ喷头7喷出的轻烃优先与催化剂接触反应,产生大量的正碳离子,加速了重烃的高效转化,使得本发明具有降低催化裂化柴汽比的特点。4、本发明所述的一种催化裂化提升管喷嘴及应用,不仅结构简单,使用方便,而且操作弹性好。上述说明仅仅是本发明技术方案的概述,为了能够更加清楚了解本发明的技术手段,并且为了让本发明的特征和优点能够更明显易懂,以下特举较佳的实施例,并配合催化裂化提升管试验装置的流程示意图,进行详细说明。附图说明图1为本发明所述的催化裂化提升管喷嘴的结构示意图。图2为本发明所述的烃油ⅰ外喷头的俯视图。图3为本发明所述的烃油ⅰ内喷头的俯视图。图4为本发明所述的烃油ⅱ喷头的俯视图。图5为本发明实施例采用的催化裂化提升管试验装置的流程示意图。图6为对比例所采用的催化裂化提升管试验装置的流程示意图。其中:1-烃油ⅰ外喷头,2-烃油ⅰ外套管,3-烃油ⅰ内套管,4-烃油ⅰ内喷头,5-蒸汽腔,6-烃油ⅰ与蒸汽混合室,7-烃油ⅱ喷头,8-烃油ⅱ套管,9-烃油ⅱ环形雾化室,10-烃油ⅱ进料入口,11-蒸汽进料入口,12-烃油ⅰ进料入口,13-卡套式接头;14-预提升介质,15-烃油ⅱ,16-烃油ⅰ,17-提升管反应器,18-汽提器,19-待生剂输送管,20-再生器,21-再生剂输送管,22-油气管线,23-分馏塔,24-催化裂化提升管喷嘴;25-预提升介质,26-混合原料,27-提升管反应器,28-汽提器,29-待生剂输送管,30-再生器,31-再生剂输送管,32-油气管线,33-分馏塔,34-常规喷嘴;35-烃油ⅰ外喷孔,36-烃油ⅰ内喷孔,37-烃油ⅱ喷孔。具体实施方式下面结合附图对本发明进行进一步详细说明。附图和具体实施方式并不限制本发明要求保护的范围。催化裂化提升管喷嘴的工作过程:这种催化裂化提升管喷嘴的工作过程为:如图1、图2、图3和图4所示,经过预热的烃油ⅰ从烃油ⅰ进料入口12进入,从烃油ⅰ内喷头4上的烃油ⅰ内喷孔36喷出;经过预热的蒸汽(或干气)从蒸汽进料入口11进入蒸汽腔5,蒸汽经过缩径后产生强大的压力并与从烃油ⅰ内喷头4喷出的烃油ⅰ油滴在烃油ⅰ与蒸汽混合室6内进行混合,混合后从烃油ⅰ外喷头1的多个烃油ⅰ外喷孔35高速喷出雾化成60μm左右的小液滴,与催化剂接触发生反应;经过预热的烃油ⅱ从烃油ⅱ进料入口10进入,在烃油ⅱ环形雾化室9内进行雾化,从烃油ⅱ喷头7的多个烃油ⅱ喷孔37高速喷出雾化成60μm左右的小液滴,与催化剂接触发生反应。这种催化裂化提升管喷嘴与图4所示的催化裂化提升管装置反应器采用卡套式接头13和卡帽连接,保证密封良好,以利于试验的正常进行。主要分析方法:各实施例中,na2o、al2o3等化学组成用x射线荧光法测定(参见《石油化工分析方法(ripp实验方法)》,杨翠定等编,科学出版社,1990年出版)。物相采用x射线衍射法测定。比表面、孔体积由低温氮吸附-脱附法测定;粒径分布采用激光粒度分析(分析方法gb/t19077.1-2008);磨损指数采用磨损指数的测定(直管法)(分析方法gb/t15458-1995);微反活性(ma)评价:采用astm-d3907方法。催化剂预先在800℃、100%水蒸汽条件下处理17h,以大港轻柴油作为反应原料油。反应温度460℃,进油时间70s,催化剂装量2.5~5g,反应后汽油的产率采用gc7890分析。主要原料及来源:ldo-70新鲜催化剂,兰州石化公司催化剂厂生产,评价前经过800℃、100%水蒸气水热减活处理10h,ldo-70老化后的理化性质见表1。表1催化剂理化性质烃油ⅰ取自兰州石化公司300万吨/年催化裂化装置的新鲜催化原料(性质见表2),减压蜡油与减压渣油混合质量比例为(6:4),减压蜡油是来自兰州石化公司550万吨常减压装置的减压蜡油,减压渣油是来自兰州石化公司550万吨常减压装置的减压渣油。烃油ⅱ取自兰州石化公司550万吨/年常减压装置的减一线柴油(性质见表3)。评价装置采用洛阳石化工程公司生产的灵活反应模式型催化裂化提升管试验装置。表2烃油ⅰ的性质项目测试数据项目测试数据分子量/(g·mol-1)432w(饱和烃)/%51.320℃密度/(kg·m-3)877.9w(芳烃)/%42.2100℃运动黏度/(mm2·s-1)17.08w(胶质+沥青质)/%6.5w(残炭)/%4.62w(重金属)/(μg·g-1)闪点/℃224fe6.44w(元素)/%ni9.68s0.61v14.39n0.14ca17.88表3烃油ⅱ的性质实施例1实施例1所述的烃油ⅰ外喷头1上的烃油ⅰ外喷孔35设置4个,在烃油ⅰ外喷头1上均匀排列,每个喷孔孔径为0.7mm。实施例1所述的烃油ⅰ内喷头4上的烃油ⅰ内喷孔36设置1个,在烃油ⅰ内喷头4上,喷孔孔径为1.1mm。实施例1所述的烃油ⅱ喷头7上的烃油ⅱ喷孔37设置4个,在烃油ⅱ喷头7上均匀排列,每个喷孔孔径为1.0mm。实施例1所述的烃油ⅰ内喷头4与烃油ⅰ外喷头1的间距d为3mm。实施例1所述的蒸汽腔5缩径后的直径d为4.5mm。实施例1所述的烃油ⅱ喷头7和烃油ⅰ外喷头1的间距l与烃油ⅱ进料入口10和烃油ⅰ外喷头1的间距h之比为0.50:1。实施例1所述的蒸汽腔5缩径段长度w与烃油ⅱ进料入口10和烃油ⅰ外喷头1的间距h之比为0.018:1。实施例1所述的蒸汽腔5缩径后的直径d与烃油ⅰ内套管3的外径之比为1.800:1。实施例1所述的烃油ⅱ套管8的外径与烃油ⅰ外套管2的外径之比为2.20:1。实施例1所述的烃油ⅰ外套管2的内径与烃油ⅰ内套管3的内径之比为5.333:1。实施例1所述的烃油ⅱ喷头7上单个烃油ⅱ喷孔37的孔径与烃油ⅰ外喷头1上单个烃油ⅰ外喷孔35的孔径之比为1.429:1。实施例1所述的烃油ⅰ为沸点≥300℃的催化裂化新鲜原料。实施例1所述的烃油ⅱ为沸程为180~380℃的柴油馏分。按照图1、图2、图3、图4所示的催化裂化提升管喷嘴和图5所示的装置,催化裂化提升管喷嘴24与提升管反应器17采用卡套式接头和卡帽连接密封后开始试验。轻烃反应区ⅰ、重烃反应区、轻烃反应区ⅱ的高度分别占提升管反应器总高度的5%,35%,55%。质量流率为150g/h的550万常减压装置减一线柴油从催化裂化提升管喷嘴24的烃油ⅱ喷头7上的4个烃油ⅱ喷孔37喷出,在提升管反应器17内的轻烃反应区ⅰ与再生催化剂接触反应,在轻烃油剂接触温度620℃、剂油比64.4、停留时间0.1s、550万常减压装置减一线柴油与300万催料的重量比0.1:1、反应压力为130千帕、再生催化剂温度670℃的条件下,反应后的催化剂继续向上运动,质量流率为1500g/h的300万催料从催化裂化提升管喷嘴24的烃油ⅰ外喷头1上的4个烃油ⅰ外喷孔35喷出,在重烃反应区与上述催化剂接触反应,在重烃油剂接触温度535℃、反应器出口温度505℃、剂油比6.44、反应时间2.0s、反应压力140千帕的条件下,反应后的产物与催化剂继续向上运动,经过轻烃反应区ⅱ后进入汽提器18进行汽提,经过汽提的待生催化剂经过待生剂输送管19进入再生器20进行烧焦,烧焦后的催化剂经过再生剂输送管21进入提升管反应器17。提升管反应器17和汽提器18反应产生的油气经过油气管线22进入分馏塔23,分离成干气、液化气、汽油、柴油和油浆。具体反应条件和反应结果见表4。实施例2实施例2所述的烃油ⅰ外喷头1上的烃油ⅰ外喷孔35设置2个,在烃油ⅰ外喷头1上均匀排列,每个喷孔孔径为1.1mm。实施例2所述的烃油ⅰ内喷头4上的烃油ⅰ内喷孔36设置1个,在烃油ⅰ内喷头4上,喷孔孔径为1.2mm。实施例2所述的烃油ⅱ喷头7上的烃油ⅱ喷孔37设置4个,在烃油ⅱ喷头7上均匀排列,每个喷孔孔径为1.1mm。实施例2所述的烃油ⅰ内喷头4与烃油ⅰ外喷头1的间距d为3.5mm。实施例2所述的蒸汽腔5缩径后的直径d为4.6mm。实施例2所述的烃油ⅱ喷头7和烃油ⅰ外喷头1的间距l与烃油ⅱ进料入口10和烃油ⅰ外喷头1的间距h之比为0.54:1。实施例2所述的蒸汽腔5缩径段长度w与烃油ⅱ进料入口10和烃油ⅰ外喷头1的间距h之比为0.025:1。实施例2所述的蒸汽腔5缩径后的直径d与烃油ⅰ内套管3的外径之比为1.769:1。实施例2所述的烃油ⅱ套管8的外径与烃油ⅰ外套管2的外径之比为2.22:1。实施例2所述的烃油ⅰ外套管2的内径与烃油ⅰ内套管3的内径之比为5.000:1。实施例2所述的烃油ⅱ喷头7上单个烃油ⅱ喷孔37的孔径与烃油ⅰ外喷头1上单个烃油ⅰ外喷孔35的孔径之比为1:1。实施例2所述的烃油ⅰ为沸点≥300℃的催化裂化新鲜原料。实施例2所述的烃油ⅱ为沸程为180~380℃的柴油馏分。按照图1、图2、图3、图4所示的催化裂化提升管喷嘴和图5所示的装置,催化裂化提升管喷嘴24与提升管反应器17采用卡套式接头和卡帽连接密封后开始试验。轻烃反应区ⅰ、重烃反应区、轻烃反应区ⅱ的高度分别占提升管反应器总高度的5%,35%,55%。质量流率为150g/h的550万常减压装置减一线柴油从催化裂化提升管喷嘴24的烃油ⅱ喷头7上的4个烃油ⅱ喷孔37喷出,在提升管反应器17内的轻烃反应区ⅰ与再生催化剂接触反应,在轻烃油剂接触温度620℃、剂油比64.4、停留时间0.1s、550万常减压装置减一线柴油与300万催料的重量比0.1:1、反应压力为130千帕、再生催化剂温度670℃的条件下,反应后的催化剂继续向上运动,质量流率为1500g/h的300万催料从催化裂化提升管喷嘴24的烃油ⅰ外喷头1上的2个烃油ⅰ外喷孔35喷出,在重烃反应区与上述催化剂接触反应,在重烃油剂接触温度535℃、反应器出口温度505℃、剂油比6.44、反应时间2.0s、反应压力140千帕的条件下,反应后的产物与催化剂继续向上运动,经过轻烃反应区ⅱ后进入汽提器18进行汽提,经过汽提的待生催化剂经过待生剂输送管19进入再生器20进行烧焦,烧焦后的催化剂经过再生剂输送管21进入提升管反应器17。提升管反应器17和汽提器18反应产生的油气经过油气管线22进入分馏塔23,分离成干气、液化气、汽油、柴油和油浆。具体反应条件和反应结果见表4。实施例3实施例3所述的烃油ⅰ外喷头1上的烃油ⅰ外喷孔35设置1个,在烃油ⅰ外喷头1上均匀排列,每个喷孔孔径为2mm。实施例3所述的烃油ⅰ内喷头4上的烃油ⅰ内喷孔36设置1个,在烃油ⅰ内喷头4上,喷孔孔径为1.3mm。实施例3所述的烃油ⅱ喷头7上的烃油ⅱ喷孔37设置6个,在烃油ⅱ喷头7上均匀排列,每个喷孔孔径为0.9mm。实施例3所述的烃油ⅰ内喷头4与烃油ⅰ外喷头1的间距d为4mm。实施例3所述的蒸汽腔5缩径后的直径d为4.7mm。实施例3所述的烃油ⅱ喷头7和烃油ⅰ外喷头1的间距l与烃油ⅱ进料入口10和烃油ⅰ外喷头1的间距h之比为0.58:1。实施例3所述的蒸汽腔5缩径段长度w与烃油ⅱ进料入口10和烃油ⅰ外喷头1的间距h之比为0.032:1。实施例3所述的蒸汽腔5缩径后的直径d与烃油ⅰ内套管3的外径之比为1.741:1。实施例3所述的烃油ⅱ套管8的外径与烃油ⅰ外套管2的外径之比为2.24:1。实施例3所述的烃油ⅰ外套管2的内径与烃油ⅰ内套管3的内径之比为4.706:1。实施例3所述的烃油ⅱ喷头7上单个烃油ⅱ喷孔37的孔径与烃油ⅰ外喷头1上单个烃油ⅰ外喷孔35的孔径之比为0.45:1。实施例3所述的烃油ⅰ为沸点≥300℃的催化裂化新鲜原料。实施例3所述的烃油ⅱ为沸程为180~380℃的柴油馏分。按照图1、图2、图3、图4所示的催化裂化提升管喷嘴和图5所示的装置,催化裂化提升管喷嘴24与提升管反应器17采用卡套式接头和卡帽连接密封后开始试验。轻烃反应区ⅰ、重烃反应区、轻烃反应区ⅱ的高度分别占提升管反应器总高度的5%,35%,55%。质量流率为150g/h的550万常减压装置减一线柴油从催化裂化提升管喷嘴24的烃油ⅱ喷头7上的6个烃油ⅱ喷孔37喷出,在提升管反应器17内的轻烃反应区ⅰ与再生催化剂接触反应,在轻烃油剂接触温度620℃、剂油比64.4、停留时间0.1s、550万常减压装置减一线柴油与300万催料的重量比0.1:1、反应压力为130千帕、再生催化剂温度670℃的条件下,反应后的催化剂继续向上运动,质量流率为1500g/h的300万催料从催化裂化提升管喷嘴24的烃油ⅰ外喷头1上的1个烃油ⅰ外喷孔35喷出,在重烃反应区与上述催化剂接触反应,在重烃油剂接触温度535℃、反应器出口温度505℃、剂油比6.44、反应时间2.0s、反应压力140千帕的条件下,反应后的产物与催化剂继续向上运动,经过轻烃反应区ⅱ后进入汽提器18进行汽提,经过汽提的待生催化剂经过待生剂输送管19进入再生器20进行烧焦,烧焦后的催化剂经过再生剂输送管21进入提升管反应器17。提升管反应器17和汽提器18反应产生的油气经过油气管线22进入分馏塔23,分离成干气、液化气、汽油、柴油和油浆。具体反应条件和反应结果见表4。实施例4实施例4所述的烃油ⅰ外喷头1上的烃油ⅰ外喷孔35设置3个,在烃油ⅰ外喷头1上均匀排列,每个喷孔孔径为0.8mm。实施例4所述的烃油ⅰ内喷头4上的烃油ⅰ内喷孔36设置1个,在烃油ⅰ内喷头4上,喷孔孔径为1.4mm。实施例4所述的烃油ⅱ喷头7上的烃油ⅱ喷孔37设置8个,在烃油ⅱ喷头7上均匀排列,每个喷孔孔径为0.7mm。实施例4所述的烃油ⅰ内喷头4与烃油ⅰ外喷头1的间距d为4.5mm。实施例4所述的蒸汽腔5缩径后的直径d为4.8mm。实施例4所述的烃油ⅱ喷头7和烃油ⅰ外喷头1的间距l与烃油ⅱ进料入口10和烃油ⅰ外喷头1的间距h之比为0.62:1。实施例4所述的蒸汽腔5缩径段长度w与烃油ⅱ进料入口10和烃油ⅰ外喷头1的间距h之比为0.040:1。实施例4所述的蒸汽腔5缩径后的直径d与烃油ⅰ内套管3的外径之比为1.714:1。实施例4所述的烃油ⅱ套管8的外径与烃油ⅰ外套管2的外径之比为2.26:1。实施例4所述的烃油ⅰ外套管2的内径与烃油ⅰ内套管3的内径之比为4.444:1。实施例4所述的烃油ⅱ喷头7上单个烃油ⅱ喷孔37的孔径与烃油ⅰ外喷头1上单个烃油ⅰ外喷孔35的孔径之比为0.875:1。实施例4所述的烃油ⅰ为沸点≥300℃的催化裂化新鲜原料。实施例4所述的烃油ⅱ为沸程为180~380℃的柴油馏分。按照图1、图2、图3、图4所示的催化裂化提升管喷嘴和图5所示的装置,催化裂化提升管喷嘴24与提升管反应器17采用卡套式接头和卡帽连接密封后开始试验。轻烃反应区ⅰ、重烃反应区、轻烃反应区ⅱ的高度分别占提升管反应器总高度的5%,35%,55%。质量流率为150g/h的550万常减压装置减一线柴油从催化裂化提升管喷嘴24的烃油ⅱ喷头7上的8个烃油ⅱ喷孔37喷出,在提升管反应器17内的轻烃反应区ⅰ与再生催化剂接触反应,在轻烃油剂接触温度620℃、剂油比64.4、停留时间0.1s、550万常减压装置减一线柴油与300万催料的重量比0.1:1、反应压力为130千帕、再生催化剂温度670℃的条件下,反应后的催化剂继续向上运动,质量流率为1500g/h的300万催料从催化裂化提升管喷嘴24的烃油ⅰ外喷头1上的3个烃油ⅰ外喷孔35喷出,在重烃反应区与上述催化剂接触反应,在重烃油剂接触温度535℃、反应器出口温度505℃、剂油比6.44、反应时间2.0s、反应压力140千帕的条件下,反应后的产物与催化剂继续向上运动,经过轻烃反应区ⅱ后进入汽提器18进行汽提,经过汽提的待生催化剂经过待生剂输送管19进入再生器20进行烧焦,烧焦后的催化剂经过再生剂输送管21进入提升管反应器17。提升管反应器17和汽提器18反应产生的油气经过油气管线22进入分馏塔23,分离成干气、液化气、汽油、柴油和油浆。具体反应条件和反应结果见表4。实施例5实施例5所述的烃油ⅰ外喷头1上的烃油ⅰ外喷孔35设置5个,在烃油ⅰ外喷头1上均匀排列,每个喷孔孔径为0.6mm。实施例5所述的烃油ⅰ内喷头4上的烃油ⅰ内喷孔36设置1个,在烃油ⅰ内喷头4上,喷孔孔径为1.5mm。实施例5所述的烃油ⅱ喷头7上的烃油ⅱ喷孔37设置10个,在烃油ⅱ喷头7上均匀排列,每个喷孔孔径为0.6mm。实施例5所述的烃油ⅰ内喷头4与烃油ⅰ外喷头1的间距d为5mm。实施例5所述的蒸汽腔5缩径后的直径d为5mm。实施例5所述的烃油ⅱ喷头7和烃油ⅰ外喷头1的间距l与烃油ⅱ进料入口10和烃油ⅰ外喷头1的间距h之比为0.67:1。实施例5所述的蒸汽腔5缩径段长度w与烃油ⅱ进料入口10和烃油ⅰ外喷头1的间距h之比为0.048:1。实施例5所述的蒸汽腔5缩径后的直径d与烃油ⅰ内套管3的外径之比为1.667:1。实施例5所述的烃油ⅱ套管8的外径与烃油ⅰ外套管2的外径之比为2.28:1。实施例5所述的烃油ⅰ外套管2的内径与烃油ⅰ内套管3的内径之比为4.000:1。实施例5所述的烃油ⅱ喷头7上单个烃油ⅱ喷孔37的孔径与烃油ⅰ外喷头1上单个烃油ⅰ外喷孔35的孔径之比为1:1。实施例5所述的烃油ⅰ为沸点≥300℃的催化裂化新鲜原料。实施例5所述的烃油ⅱ为沸程为180~380℃的柴油馏分。按照图1、图2、图3、图4所示的催化裂化提升管喷嘴和图5所示的装置,催化裂化提升管喷嘴24与提升管反应器17采用卡套式接头和卡帽连接密封后开始试验。轻烃反应区ⅰ、重烃反应区、轻烃反应区ⅱ的高度分别占提升管反应器总高度的5%,35%,55%。质量流率为150g/h的550万常减压装置减一线柴油从催化裂化提升管喷嘴24的烃油ⅱ喷头7上的10个烃油ⅱ喷孔37喷出,在提升管反应器17内的轻烃反应区ⅰ与再生催化剂接触反应,在轻烃油剂接触温度620℃、剂油比64.4、停留时间0.1s、550万常减压装置减一线柴油与300万催料的重量比0.1:1、反应压力为130千帕、再生催化剂温度670℃的条件下,反应后的催化剂继续向上运动,质量流率为1500g/h的300万催料从催化裂化提升管喷嘴24的烃油ⅰ外喷头1上的5个烃油ⅰ外喷孔35喷出,在重烃反应区与上述催化剂接触反应,在重烃油剂接触温度535℃、反应器出口温度505℃、剂油比6.44、反应时间2.0s、反应压力140千帕的条件下,反应后的产物与催化剂继续向上运动,经过轻烃反应区ⅱ后进入汽提器18进行汽提,经过汽提的待生催化剂经过待生剂输送管19进入再生器20进行烧焦,烧焦后的催化剂经过再生剂输送管21进入提升管反应器17。提升管反应器17和汽提器18反应产生的油气经过油气管线22进入分馏塔23,分离成干气、液化气、汽油、柴油和油浆。具体反应条件和反应结果见表4。对比例1按照图6所示的装置,对比例1采用的常规喷嘴为专利cn201120267386.4所述的一种催化裂化雾化进料喷嘴,常规喷嘴34与提升管反应器27连接密封后开始试验。质量流率为1650g/h的300万催料与550万常减压装置减一线柴油的混合原料(550万常减压装置减一线柴油与300万催料的质量比为0.1:1)从常规喷嘴34喷出,与再生催化剂接触反应,在油剂接触温度535℃、反应器出口温度505℃、剂油比6.44、反应时间2.0s、反应压力140千帕的条件下,反应后的产物与催化剂继续向上运动,进入汽提器28进行汽提,汽提后的催化剂经过待生剂输送管29进入再生器30进行烧焦,烧焦后的催化剂经过再生剂输送管31进入提升管反应器27。提升管反应器27和汽提器28反应产生的油气经过油气管线32进入分馏塔33,分离成干气、液化气、汽油、柴油和油浆。具体反应条件和反应结果见表5。表4实施例1、实施例2、实施例4、实施例4、实施例5的反应条件和反应结果表5对比例1的反应条件和反应结果实施例1与对比例1相比,在进料质量完全相同、进料位置不同的反应条件下,反应后汽油收率提高了2.25个百分点,总液收提高了0.51个百分点,转化率提高了5.62个百分点,柴油收率降低了4.02个百分点,重油收率降低了1.61个百分点,柴汽比降低了0.089。数据显示本发明具有降低催化裂化柴汽比的特点。实施例2与对比例1相比,在进料质量完全相同、进料位置不同的反应条件下,反应后汽油收率提高了2.33个百分点,总液收提高了0.52个百分点,转化率提高了5.74个百分点,柴油收率降低了4.06个百分点,重油收率降低了1.69个百分点,柴汽比降低了0.091。数据显示本发明具有降低催化裂化柴汽比的特点。实施例3与对比例1相比,在进料质量完全相同、进料位置不同的反应条件下,反应后汽油收率提高了2.29个百分点,总液收提高了0.51个百分点,转化率提高了5.67个百分点,柴油收率降低了4.09个百分点,重油收率降低了1.59个百分点,柴汽比降低了0.091。数据显示本发明具有降低催化裂化柴汽比的特点。实施例4与对比例1相比,在进料质量完全相同、进料位置不同的反应条件下,反应后汽油收率提高了2.36个百分点,总液收提高了0.55个百分点,转化率提高了5.85个百分点,柴油收率降低了4.15个百分点,重油收率降低了1.71个百分点,柴汽比降低了0.093。数据显示本发明具有降低催化裂化柴汽比的特点。实施例5与对比例1相比,在进料质量完全相同、进料位置不同的反应条件下,反应后汽油收率提高了2.38个百分点,总液收提高了0.50个百分点,转化率提高了5.96个百分点,柴油收率降低了4.23个百分点,重油收率降低了1.74个百分点,柴汽比降低了0.095。数据显示本发明具有降低催化裂化柴汽比、增产汽油、提高总液收和转化率、降低重油收率的特点。当然,本发明还可有其它多种实施例,在不背离本发明精神及其实质的情况下,熟悉本领域的技术人员可根据本发明作出各种相应的改变和变形,但这些相应的改变和变形都应属于本发明的保护范围。当前第1页12