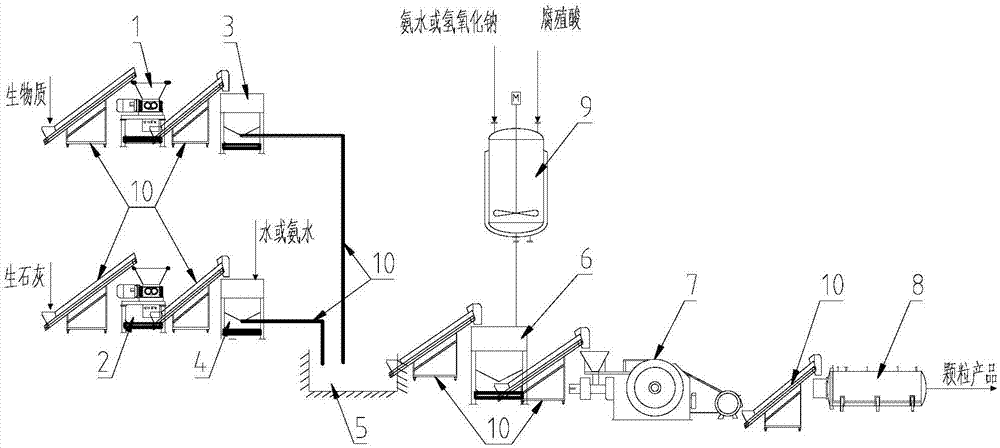
本发明涉及一种生物质成型原料,特别是指一种生物质气化用补钙型生物质成型原料及其生产方法与系统。
背景技术:
:随着社会的进步,人类对各种能源的需求不断增加,供求矛盾日益突出。石油、煤、天然气是目前人类使用的最主要的不可再生资源,其大量开采利用带来了严重的环境污染问题,不利于人类的可持续发展。生物质能是一种总量大、清洁、可再生的能源,我国每年产生的秸秆量约7亿吨,目前,各地政府已禁止田间直接焚烧秸秆,因此,急需一种生物质高效资源化利用技术。生物质成型颗粒气化生产合成气是一种生物质能大规模高效利用技术,生产的合成气可用于生产甲醇、费托合成油品等。然而,现有以生物质为原料生产的成型颗粒多用于锅炉直接燃烧,其热稳定性和机械强度不能满足生物质气化生产的要求。如果直接用于生物质气化生产合成气,在水蒸汽气化时,容易发生热爆粉化问题。技术实现要素:本发明的目的在于提供一种气化时不易发生热爆粉化的生物质气化用补钙型生物质成型原料及其生产方法与系统。为实现上述目的,本发明所提供的生物质气化用补钙型生物质成型原料,主要由如下原料制得:生物质原料,100质量份;熟石灰,按氧化钙计1~12质量份,优选为3.5~5质量份;腐殖酸盐,1~10质量份,优选为4.3~5.9质量份;以上各原料的用量均为扣除水分后的用量,熟石灰和腐殖酸盐的含水量以方便配置使用和节省干燥成本为宜。优选地,所述腐殖酸盐为腐殖酸的可溶盐,例如腐殖酸铵、腐殖酸钠、腐殖酸钾等。优选地,所述腐殖酸盐按重量百分数计由如下原料制得:腐殖酸,75~90%;氨水以NH3计,0~25%;氢氧化钠,0~15%;以上各原料的用量均为扣除水分后的用量,总量为100%,氨水和氢氧化钠的加入量总和应保证腐殖酸完全反应(可以稍过量)。以R-COOH代表腐殖酸,在腐殖酸盐制备过程中发生的化学反应如下:添加氢氧化钠时:R-COOH+NaOH=R-COONa+H2O;添加氨水时:R-COOH+NH3.H2O=R-COONH4+H2O。优选地,该生物质气化用补钙型生物质成型原料为棒状,直径6~40mm,长15~60mm;热稳定性BTS+6≥80%,落下强度≥85%。优选地,所述生物质原料为玉米秸秆、玉米芯、花生壳、油菜秸秆、棉花杆、木屑、竹屑、草本类或其它含纤维物料中的一种或多种混合物。所述生物质原料也可以是返工的不合格生物质成型原料。本发明同时提供了一种生物质气化用补钙型生物质成型原料的生产方法,包括如下步骤:1)将生物质原料、熟石灰、腐殖酸盐溶液充分混合反应,得到待压制混合料;2)进行挤压成型,得到成型混合料;3)将成型混合料与CO2反应进行碳化,并进行干燥,即得生物质气化用补钙型生物质成型原料产品。碳化过程中发生的主要反应为:Ca(OH)2+CO2=CaCO3+H2O。优选地,该方法还包括生物质原料预处理步骤和熟石灰制备步骤;所述生物质原料预处理步骤是将生物质原料经粉碎和过筛,使其粒径≤6mm;所述熟石灰制备步骤是将生石灰粉碎,再过80~100目筛后,加入水或稀氨水,混合熟化,制得含水量为15~17%的熟石灰。优选地,该方法还包括腐殖酸盐溶液的制备步骤,即将腐殖酸与氢氧化钠溶液和/或氨水混合反应,制得质量分数≥12%、pH=11~13.5的腐殖酸盐溶液;所述氢氧化钠溶液中NaOH的质量分数为15%~45%,所述氨水中NH3的质量分数为10%~28%。优选地,步骤1)中,先将生物质原料与熟石灰混匀,再与腐殖酸盐溶液进行混合。其目的是保证腐殖酸盐与生物质原料更好地混合,如果熟石灰与生物质未提前混合均匀,可能造成熟石灰直接接触腐殖酸时结块,混合效果较差。本发明还提供了前述生物质气化用补钙型生物质成型原料的生产系统,包括生物质粉碎机、生石灰粉碎机、生物质仓、石灰仓、混合仓、成型机和碳化罐;所述生物质粉碎机设置有生物质入口和生物质出口,所述生石灰粉碎机设置有生石灰入口和生石灰出口,所述混合仓设置有生物质入口、熟石灰入口和腐殖酸盐入口;所述生物质粉碎机的生物质出口与生物质仓的生物质入口相连,所述生物质仓的生物质出口与混合仓的生物质入口相连;所述生石灰粉碎机的生石灰出口与石灰仓的生石灰入口相连,所述石灰仓的熟石灰出口与混合仓的熟石灰入口相连;所述混合仓的混合料出口与成型机的混合料入口相连;所述碳化罐设置有二氧化碳入口、成型原料入口和产品颗粒出口,所述成型机的成型原料出口与碳化罐的成型原料入口相连。关于出入口的说明:本发明中,只要某装置可加入某物质,即认为存在该物质的入口,而不必确实的存在一个接口;相应地,只要某装置可输出某物质,即认为存在该物质的出口,而不必确实的存在一个接口。优选地,该系统中,固体物料通过输送机进行输送,液体物料通过管道进行输送。所述输送机可采用皮带输送机、螺旋输送机、斗式提升机等各种类型的用于输送固体物料的输送机。优选地,该系统还包括用于制备腐殖酸盐的反应釜,所述反应釜设置有氨水入口、氢氧化钠入口、腐殖酸入口和腐殖酸盐出口;所述反应釜的腐殖酸盐出口与混合仓的腐殖酸盐入口相连。优选地,所述混合仓前还设置有受料坑,所述受料坑的生物质入口与所述生物质仓的生物质出口相连,所述受料坑的熟石灰入口与所述石灰仓的熟石灰出口相连;所述受料坑的混合料出口与混合仓的混合料入口相连。该方案将生物质与熟石灰在受料坑中混合后,再在混合仓中与腐殖酸盐进行混合。优选地,该系统中,固体物料通过皮带输送机进行输送,液体物料通过管道进行输送。与现有技术相比,本发明的有益效果如下:1)熟石灰可形成成型颗粒的碳酸钙骨架,调整生物质气化反应,稳定气化床层;并可调整气化熔渣的硅钙比,在熔渣气化时,可保证合理的熔渣酸碱性。2)腐殖酸是动植物遗骸,主要是植物的遗骸,经过微生物的分解和转化,以及地球化学的一系列过程造成和积累起来的一类有机物质。腐殖酸组成主要以C、H、O元素为主,与生物质元素组成类似,对原料无污染,对生物质气化工艺不会造成不利影响;腐殖酸在自然界中广泛存在,储量丰富,适宜大规模使用。3)腐殖酸盐具有很强的粘结性和热稳定性,可显著提高生物质气化原料的机械强度和热稳定性,还可均化气化炉内成型颗粒破裂程度,稳定蒸汽和氧气利用率。4)原料氨水可来自气化工厂副产物氨水,实现氨水环保循环利用;碳化、干燥生产工艺用CO2可来自锅炉烟道气或低压放空气,实现CO2循环利用,可实现CO2和氨水的环保循环利用,节能减排。5)本发明生产的生物质成型原料热稳定性好,机械强度高,生产成本低,气化时不易发生热爆粉化,可满足生物质气化对颗粒原料的要求。附图说明图1、图2为本发明实施例所设计的两种补钙型生物质成型原料生产系统的结构示意图。图3为本发明实施例所提供的采用图2所示系统生产生物质气化用补钙型生物质成型原料的生产工艺示意图。其中,生物质粉碎机1、生石灰粉碎机2、生物质仓3、石灰仓4、受料坑5、混合仓6、成型机7、碳化罐8、反应釜9、输送机10具体实施方式下面结合附图和具体实施例对本发明作进一步的详细说明。如图1、2所示,本发明所设计的生物质气化用补钙型生物质成型原料的生产系统,包括生物质粉碎机1、生石灰粉碎机2、生物质仓3、石灰仓4、混合仓6、成型机7、碳化罐8和反应釜9。图2在图1基础上作了优化,增加了受料坑5和反应釜9,以下对图2中系统作具体说明(图1可参照理解)。生物质粉碎机1设置有生物质入口,生石灰粉碎机2设置有生石灰入口,石灰仓4设置有加水口,混合仓6设置有腐殖酸盐入口,反应釜9设置有氨水入口、氢氧化钠入口和腐殖酸入口,碳化罐8设置有二氧化碳入口(以上仅列举从外部加入原料的入口,内部出入口未一一列出)。生物质粉碎机1的生物质出口与生物质仓3的生物质入口相连,生物质仓3的生物质出口与受料坑5的生物质入口相连。生石灰粉碎机2的生石灰出口与石灰仓4的生石灰入口相连,石灰仓4的熟石灰出口与受料坑5的熟石灰入口相连。受料坑5的混合料出口与混合仓6的混合料入口相连。混合仓6的腐殖酸盐入口与反应釜9的腐殖酸盐出口相连,混合仓6的混合料出口与成型机7的混合料入口相连。成型机7的成型原料出口与碳化罐8的成型原料入口相连,碳化罐8还设置有颗粒产品出口。该系统中,固体物料通过皮带输送机10进行输送,液体物料通过管道进行输送。如图3所示,本发明同时提供了一种生产生物质气化用补钙型生物质成型原料的方法,具体步骤如下:1)粉碎:取生物质和生石灰,分别通过生物质粉碎机1、生石灰粉碎机2进行粉碎过筛,再分别储存至生物质仓3和石灰仓4中备用。2)配制熟石灰:将水或稀氨水计量加入至石灰仓4中,搅拌熟化,制得含水量15~17%的熟石灰。3)制备腐殖酸盐:将腐殖酸、氢氧化钠和/或氨水加入至反应釜9中,生产以腐殖酸钠和/或腐殖酸铵为主的具有强粘结性的腐殖酸盐。加氨水的目的一方面是消耗化工企业产生的低质量氨水,另一方面提供碱性环境,减少后续氢氧化钠使用量。4)混合:将熟石灰、粉碎后的生物质原料分别送入受料坑5,在搅拌机作用下混合均匀,然后输送至混合仓6,在混合仓6中与制备的腐殖酸盐充分搅拌,制备待压制混合料。5)成型:将待压制混合料输送至成型机7挤压成型,得到成型混合料。6)碳化、干燥:将成型混合料送入碳化罐8与CO2循环气进行碳化反应,同时烘干,CO2可采用来自锅炉烟道气或低压放空气,即得补钙型生物质成型颗粒原料产品。实施例1~4各实施例采用图2中生产系统和图3中生产工艺,并按照下表给出的原料及配比生产补钙型生物质成型原料。表1各实施例采用的原料组成注:生物质原料干重系生物质干燥后的质量,腐殖酸盐溶液干重指溶质腐殖酸盐的质量;腐殖酸盐制备原料中,腐殖酸、NaOH、NH3均为扣除水分后计算的百分数,三者之和为100%;对比例为现有的玉米秸秆生物质原料。对各实施例制得的补钙型生物质成型原料的理化性质进行检测,检测结果见表2。因生物质成型颗粒热稳定性、落下强度及冷抗压强度测试没有国家及行业标准,因此分别参考《工业型煤煤热稳定性测试方法MT/T924-2004》、《工业型煤落下强度测试方法MT/T925-2004》和《工业型煤冷压强度测定方法MT/T748-2007》进行检验,分析测试条件与各标准保持一致,但在处理热稳定性测试数据时,因生物质成型颗粒本身直径小于13mm,故取测得的粒径在6mm以上的生物质成型颗粒的比例,记为BTS+6,其它分析测试数据处理方法与标准相同。表2各实施例成型后的生物质颗粒检测指标项目实施例1实施例2实施例3实施例4对比例外观棒状棒状棒状棒状棒状颗粒直径12mm12mm12mm12mm12mm颗粒长度(平均值)30mm28mm25mm24mm25mm水分4.40%4.60%3.50%4.56%4.91%灰分7.80%11.50%5.40%8.23%7.50%挥发分70.30%65.70%74.30%71.45%71.37%固定碳17.50%18.20%16.80%15.76%16.22%热稳定性BTS+682.20%87.60%82.90%91.25%55.41%落下强度86.50%89.20%89.40%85.16%68.45%冷抗压强度420N/个440N/个457N/个427N/个280N/个从表2可以看出,与对比例相比,本发明大大提高了生物质成型原料的热稳定性、落下强度和冷抗压强度。实施例4较实施例2有更强的热稳定性,但腐殖酸盐添加量过多,使生产成本急速上升。当前第1页1 2 3