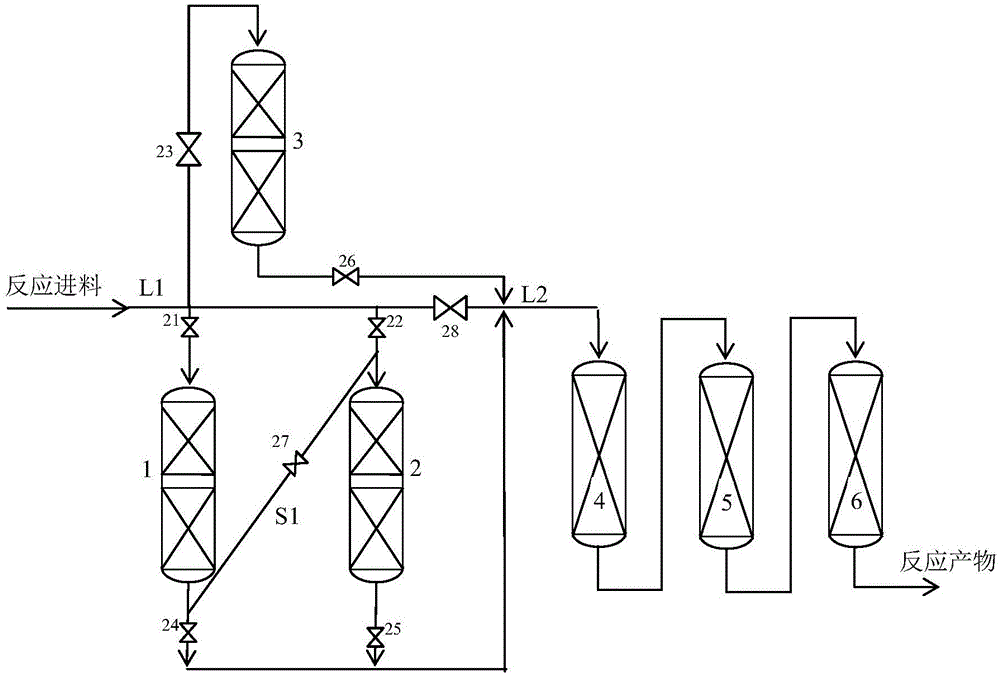
本发明涉及一种固定床渣油加氢处理方法及系统,尤其涉及一种可轮换的固定床渣油加氢处理方法及系统。
背景技术:
:随着原油日益变重、变劣,越来越多的重油、渣油需要加工处理。渣油加氢处理工艺的主要目的是通过加氢处理,使渣油原料中的硫、氮、金属等杂质含量大幅降低,稠环芳烃、胶质、沥青质等非理想组分加氢转化,提高氢碳比,降低残炭含量,使其裂化性能得到明显改善。固定床渣油加氢技术是一种重油深度加工技术,在高温高压的临氢条件下,对常压或减压渣油进行脱硫、脱氮、脱金属等,以最大限度地获取轻质产品,是渣油轻质化的重要手段之一。固定床渣油加氢技术以其液体产品收率高,产品质量好,生产灵活性强,废物少,环境友好,投资回报率高等优点,得到越来越广泛的应用。虽然固定床渣油加氢技术具有诸多优点,但在加工劣质油时,渣油原料中大量的金属杂质、不饱和组分以及垢物容易沉积在催化剂的表面、催化剂颗粒之间的空隙,导致保护和脱金属反应器床层堵塞、压降上升过快,或者加氢保护催化剂和加氢脱金属催化剂的活性先于加氢脱硫主催化剂失活,从而造成装置运行周期缩短、主催化剂利用效率低等问题。cn103059928a本发明提供一种加氢处理装置,该装置包括依次串联的加氢保护单元和主加氢处理单元,所述加氢保护单元包括并联的主加氢保护反应器和备用加氢保护反应器,所述主加氢保护反应器的体积大于备用加氢保护反应器的体积。cn102676218a公开了一种固定床渣油加氢工艺。该工艺设置了备用固定床反应器,备用固定床反应器可与主固定床反应器进行串联操作和切出操作。但上述工艺和装置在需要换剂时,所消耗较长,一般至少需要20天。在换剂期间,由于在线催化剂总量减少,会使在线催化剂处理负荷增大,在保持原操作条件的情况下,会影响主催化剂的催化活性,此催化活性损失是不可逆的。为了保证主催化剂的催化活性,就需要进一步提高前部反应苛刻度,更大幅度地提高反应温度,这样会加重加热炉的负荷,有的可能会存在原设计负荷太小,无法满足提温要求。cn106701172a公开了一种渣油加氢处理方法,所述方法包括以下内容:渣油原料与氢气混合后依次经过串联设置的加氢预处理反应区和加氢处理反应区,所述加氢预处理反应区包括二台以上并联设置的加氢预处理反应器,当所述加氢预处理反应区中任一台加氢预处理反应器的压降达到设计上限的50%~80%,优选60%~70%时,将该加氢预处理反应器从加氢预处理反应区中切出,同时将该切出的加氢预处理反应器与加氢预处理反应区和加氢处理反应区以串联的方式连接起来。该渣油加氢方法将各个加氢预处理反应器从并联切换为串联,从而解决了反应器压降快速增长的难题。但该方法在并联、串联操作后,需要停止并更换各个加氢预处理反应器的催化剂,而且需要较长停工时间,不能长期连续进行渣油加氢,从而影响炼厂的经济效率;还有,各个加氢预处理反应器在运行后期,压降处于最高位,而且还采用串联形式进行操作,使得加氢预处理的总压降非常高,若保持原操作条件的情况下,会影响主催化剂的催化活性,此催化活性损失是不可逆的。为了保证主催化剂的催化活性,就需要进一步提高前部加氢预处理的反应苛刻度,更大幅度地提高反应温度,这样会加重加热炉的负荷,有时可能会存在原设计负荷太小,无法满足提温要求。上述渣油加氢工艺中,当固定床同时装填有加氢保护剂和加氢脱金属催化剂时,若采用较低比例的加氢脱金属剂,整个催化剂体系的加氢脱金属性能不足,尤其是进入运行尾期,容金属能力低,导致主反应区催化剂失活快,不利于装置长周期运行;若采用较高比例的加氢脱金属剂,相对应的保护剂比例低,那么整个体系的容垢容杂质能力不足,导致加氢预处理反应器压降上升快,缩短正常运转的时间,很快进入运行尾期,导致停工,同样不利于装置长周期运行。技术实现要素:针对上述现有技术中存在的不足之处,本发明提供一种可轮换的固定床渣油加氢处理方法及系统。该方法可实现加氢预处理工艺的长期运转而不停工,又有利于主催化剂整体催化活性的稳定发挥,提高主催化剂利用效率和装置操作的稳定性,大幅延长加氢处理反应器的运行时间。本发明提供了一种可轮换的固定床渣油加氢处理方法,所述渣油加氢处理设置有串联的加氢预处理反应区和加氢处理反应区,所述加氢预处理反应区包括第一加氢预处理反应器、第二加氢预处理反应器、第三加氢预处理反应器;渣油原料与氢气混合进入加氢预处理反应区,依次经过串联连接的第一加氢预处理反应器与第二加氢预处理反应器,并进行加氢预处理反应;然后再进入加氢处理反应区;其中第三加氢预处理反应器作为非在线加氢预处理反应器;当第一加氢预处理反应器内的压降上升到压降设计上限或催化剂活性低于要求时,切换出第一加氢预处理反应器并作为非在线加氢预处理反应器,而第二加氢预处理反应器与第三加氢预处理反应器并联,并进行加氢预处理反应;当第二加氢预处理反应器内的压降上升到压降设计上限或催化剂活性低于要求时,切换出第二加氢预处理反应器并作为非在线加氢预处理反应器,而第三加氢预处理反应器与第一加氢预处理反应器并联,并进行加氢预处理反应;当第三加氢预处理反应器内的压降上升到压降设计上限或催化剂活性低于要求时,切换出第三加氢预处理反应器并作为非在线加氢预处理反应器,而第一加氢预处理反应器与第二加氢预处理反应器串联,并进行加氢预处理反应;当第一加氢预处理反应器内的压降上升到压降设计上限或催化剂活性低于要求时,按上述方式进行循环轮换,实现不间断地进行加氢预处理反应。本发明渣油加氢处理方法中,渣油加氢技术采用固定床渣油加氢处理技术,加氢预处理反应区的各个加氢预处理反应器中可以装填加氢保护剂、加氢脱金属催化剂中的一种或几种。优选地,所述第一加氢预处理反应器、第二加氢预处理反应器、第三加氢预处理反应器均设置有加氢保护剂床层和加氢脱金属催化剂床层,所述加氢保护剂床层填装有加氢保护剂,所述加氢脱金属催化剂床层填装有加氢脱金属催化剂。上述加氢保护剂、加氢脱金属催化剂一般以多孔耐熔无机氧化物如氧化铝为载体,以第vib族和/或第viii族金属如w、mo、co、ni等的氧化物中的至少一种为活性组分,选择性地加入其它各种助剂如p、si、f、b等元素中的至少一种。本发明渣油加氢处理方法中,每个加氢预处理反应器中,加氢脱金属催化剂与加氢保护剂的重量比例为(0.05~20):1;优选为(0.2~10):1。本发明渣油加氢处理方法中,在开工之后且第一次轮换加氢预处理反应器前,所述第一、第二、第三加氢预处理反应器内的加氢脱金属催化剂与加氢保护剂的重量比例逐渐增加。优选地,在开工之后且第一次轮换加氢预处理反应器前,所述第一加氢预处理反应器内的加氢脱金属催化剂与加氢保护剂的重量比例为(0.05~2):1;以加氢脱金属催化剂与加氢保护剂的总重量为100%计,与第一加氢预处理反应器相比,所述第二加氢预处理反应器内的加氢脱金属催化剂的重量分数增加3~30个百分点,优选为3~20个百分点;与第二加氢预处理反应器相比,所述第三加氢预处理反应器内的加氢脱金属催化剂的重量分数增加3~30个百分点,优选为3~20个百分点。本发明渣油加氢处理方法中,加氢预处理反应器作为非在线加氢预处理反应器时,更换新的催化剂或进行催化剂的再生。本发明渣油加氢处理方法中,每切换一次加氢预处理反应器,以前一次切换接入的加氢预处理反应器为基准,增加一次非在线加氢预处理反应器的加氢脱金属催化剂的比例,直至加氢脱金属催化剂与加氢保护剂的重量比例增加至(4~20):1,优选为(4~10):1。本发明渣油加氢处理方法中,每切换一次加氢预处理反应器,以前一次切换接入的加氢预处理反应器为基准,增加一次非在线加氢预处理反应器的加氢脱金属催化剂与加氢保护剂的比例,以加氢脱金属催化剂与加氢保护剂的总重量为100%计,加氢脱金属催化剂的重量分数增加3~30个百分点,优选为3~20个百分点,直至加氢脱金属催化剂与加氢保护剂的重量比例增加至(4~20):1,优选为(4~10):1。本发明渣油加氢处理方法中,可以当压降上升到压降设计上限时,进行轮换。压降设计上限可以为0.6~1.0mpa。本发明渣油加氢处理方法中,所述的加氢预处理反应区的操作条件可以为:反应温度为350~420℃,反应压力为10mpa~25mpa,氢油体积比为300~1500,原料油液时体积空速为0.15h-1~2.0h-1;优选地,反应温度为360~400℃,反应压力为15mpa~25mpa,氢油体积比为500~800,原料油液时体积空速为0.3h-1~1.0h-1。当加氢预处理反应器并联操作时,各反应器的进料空速可以根据需要进行调配,一般可以根据反应器内催化剂的装填量进行调配。本发明渣油加氢处理方法中,在开工之后且未切换加氢预处理反应器前,所述第一加氢预处理反应器的反应温度为350~385℃,所述第二加氢预处理反应器的反应温度比所述第一加氢预处理反应器高1~10℃,优选为1~5℃。本发明渣油加氢处理方法中,可以根据催化剂活性确定是否进行轮换。根据加氢预处理产物的金属含量(ni+v),确定第一、第二、第三加氢预处理反应器中两个加氢预处理反应器在线时的反应温度,以使加氢预处理产物的金属(以ni+v计)含量控制在50μg/g以下,优选为30μg/g以下,若通过调节反应温度不能将金属含量控制在50μg/g以下,优选为30μg/g以下,即催化剂活性低于要求,需要进行轮换。可根据加氢预处理产物的金属含量在350~420℃范围内调整加氢预处理反应区的反应温度,可逐渐增加反应温度,催化剂的活性逐渐提高,使预处理产物中的金属含量不大于50μg/g。在开工阶段后至第一次轮换前,根据加氢预处理产物的金属含量,分别升高第一、第二加氢预处理反应器的反应温度,反应温度的升幅为5~30℃,优选为10~20℃。在每次轮换后至下一次轮换前,根据加氢预处理产物的金属含量,分别升高第一、第二、第三加氢预处理反应器中两个加氢预处理反应器在线时的反应温度,反应温度的升幅为1~10℃,优选为2~10℃。本发明渣油加氢处理方法中,在切换加氢预处理反应器后,第一、第二、第三加氢预处理反应器中两个加氢预处理反应器在线的反应温度高于加氢处理反应区的反应温度,优选地高于1~25℃。本发明渣油加氢处理方法中,在每次轮换时,未切换的加氢预处理反应器先进行降温操作,温度降低1~10℃,优选1~5℃。本发明渣油加氢处理方法中,所述的加氢处理反应区包括1~5台串联设置的加氢处理反应器,优选包括2~3台串联设置的加氢处理反应器。本发明渣油加氢处理方法中,所述的加氢处理反应区的操作条件为:反应温度为345~420℃,反应压力为10mpa~25mpa,氢油体积比为300~1500,原料油液时体积空速为0.15h-1~0.80h-1;优选地,反应温度为355~400℃,反应压力为15mpa~25mpa,氢油体积比为400~800,原料油液时体积空速为0.2h-1~0.6h-1。本发明渣油加氢处理方法中,加氢处理反应区中可以装填本领域常规使用加氢处理催化剂,可以选用加氢脱硫催化剂、加氢脱氮催化剂和脱残炭转化催化剂中的一种或几种。本发明渣油加氢处理方法中,所述的渣油原料为常压渣油和/或减压渣油,不含有或含有直馏蜡油、减压蜡油、二次加工蜡油和催化回炼油中的一种或几种。所述渣油原料的性质为硫含量不大于4wt%,氮含量不大于0.7wt%,金属含量(ni+v)不大于120μg/g,残炭值不大于17wt%,沥青质含量不大于5wt%。本发明还提供一种可轮换的固定床渣油加氢处理系统,所述系统包括设置有串联的加氢预处理反应区和加氢处理反应区,所述加氢预处理反应区包括第一加氢预处理反应器、第二加氢预处理反应器、第三加氢预处理反应器;反应进料总管路分别通过3条入口管路与第一加氢预处理反应器、第二加氢预处理反应器、第三加氢预处理反应器的入口分别相连,每条入口管路均设置有入口阀体,反应出料总管路通过3条出口管路与第一加氢预处理反应器、第二加氢预处理反应器、第三加氢预处理反应器的出口分别相连,每条出口管路均设置有出口阀体;第一加氢预处理反应器、第二加氢预处理反应器通过串联管路相连,串联管路的一端连接于第一加氢预处理反应器的出口与第一加氢预处理反应器的出口阀体之间的管路,而另一端连接于第二加氢预处理反应器的进口与第二加氢预处理反应器的进口阀体之间的管路,并且串联管路上设置有串联阀体。所述反应出料总管路串联有1~5台加氢处理反应器,优选2~3台加氢处理反应器。与现有技术相比,本发明具有如下优点:(1)本发明采用3个加氢预处理反应器,渣油原料先进入第一加氢预处理反应器,然后经过串联的第二加氢预处理反应器,实现加氢预处理反应。第一、第二、第三、第一、……依次循环切出并作为非在线加氢预处理反应器,在更换催化剂或催化剂再生后,第三、第一、第二、第三、……的循环顺序依次上线;在线状态时,第一加氢预处理反应器与第二加氢预处理反应器串联,第一或第二与第三加氢预处理反应器处于并联。通过上述切出、轮动和上线等操作,不但始终保持两个串联或并联的加氢预处理反应器处于在线状态,一个非在线加氢预处理反应器处于切出状态。通过多次轮换操作,可实现三个加氢预处理反应器反复循环切出、轮动、上线,进而实现加氢预处理工艺的长期运转而不停工。通过上述切出、轮动和上线等动作,不管切换成串联状态,还是并联状态,均新增加一个加氢预处理反应器,在线催化剂处理负荷变化非常小,同时新增加氢预处理反应器具有很高容金属能力和容垢容杂质能力,这样既不会使各加氢预处理反应器的压降过快上升,又有利于主催化剂整体催化活性的稳定发挥,主催化剂的失活速率下降平缓,可提高主催化剂利用效率和装置操作的稳定性,大幅延长加氢处理反应器的运行时间。由于在线催化剂处理负荷变化非常小,从而可稳定地控制加氢预处理的温度、压力和流速等参数,有利于加热炉等装置稳定地运行,无需大幅度地调节运行参数,加氢预处理后的物料性质也很稳定,进而有利于加氢处理反应器的稳定操作、运行。(2)本发明在开工至开始第一次轮换反应器的时期,第一、第二、第三加氢预处理反应器内的加氢脱金属催化剂比例处于最低水平,此时体系以容垢容杂质为主,可避免各加氢预处理反应器的压降快速上升,而且由于催化剂活性高,反应性能过剩,加氢脱金属催化剂活性高,不会影响主反应区催化剂的反应性能。优选地,每切换一次加氢预处理反应器,增加一次非在线加氢预处理反应器的加氢脱金属催化剂与加氢保护剂的比例,随着轮换反应器换剂次数的增加,第一、第二、第三加氢预处理反应器内的催化剂活性各自稳定在一定范围内,但随着长时间的运行,主反应区催化剂反应性能开始缓慢下降,在轮换时逐步增加轮换反应器内脱金属剂比例,在保证装置平稳操作的情况下,兼顾加氢预处理反应区和加氢处理反应区,使各催化剂的活性得到充分发挥,又可以减慢加氢处理反应区中催化剂整体活性的失活速率,保证最终产品的性质处于优良水平。(3)在开工至开始第一次轮换反应器的时期,第一、第二加氢预处理反应器中的各级温度均处于最低水平,此时体系以容垢容杂质为主,较低反应温度可以避免第一、第二加氢预处理反应器的压降快速上升,而且在开工阶段加氢预处理催化剂活性高,反应性能过剩,加氢脱金属催化剂活性高,这样可使加氢预处理后的物流不会影响主反应区催化剂的反应性能;优选地,加氢预处理反应区的反应温度根据加氢预处理产物的金属(ni+v)含量在350-420℃范围内进行调整,可以逐渐增加反应温度,提高加氢预处理反应器内催化剂活性,使金属(ni+v)含量不大于50μg/g,有利于保证主反应区催化剂整体的活性,同时并且加氢预处理反应器的反应温度高于加氢处理反应区的反应温度,保证最终产品处于优良水平。(4)本发明优选地,在开工初期,限定特定的第一、第二、第三的加氢脱金属催化剂与加氢保护剂的比例,以及每轮换一次,增加一次加氢脱金属催化剂的比例,同时加氢预处理反应器的加氢脱金属催化剂比例,在每次轮换前后根据金属含量调整预处理反应温度,而且反应温度高于加氢处理反应区的反应温度,这样通过催化剂级配、反应温度操控等多种操作,产生配合、协同作用,能够避免加氢预处理反应器的压降快速上升,并使所提供的加氢处理反应区的进料更有利于主反应区催化剂整体活性的稳定发挥,减慢主催化剂的失活速率,保证最终加氢处理产品处于优良水平,大幅度地延长加氢处理的运行时间。(5)本发明固定床渣油加氢处理系统,反应进料总管路分别通过3条入口管路与3个加氢预处理反应器入口相连,通过3条出口管路与3个加氢预处理反应器出口相连,加氢预处理反应器均设置有进口阀体、出口阀体,同时,第一加氢预处理反应器、第二加氢预处理反应器通过串联管路相连,串联管路两端连接于特定位置,从而能够实现3个加氢预处理反应器的切出、轮动和上线等动作,同时管线与阀体规律地排布,从而便于操作,避免轮换出错。附图说明图1为本发明的一固定床加氢的反应系统的示意图;附图标记:1-第一加氢预处理反应器;2-第二加氢预处理反应器;3-第三加氢预处理反应器;4、5、6-加氢处理反应器;21-28为阀门;l1-反应进料总管路;l2-反应出料总管路;s1-管路。具体实施方式下面通过实施例来进一步说明本发明的技术方案,但不应认为本发明仅局限于以下的实施方式中,其中wt%为质量分数。本发明实施例所述的第一加氢预处理反应器1、第二加氢预处理反应器2、第三加氢预处理反应器3为样式、大小相同的反应器;加氢处理反应器4、加氢处理反应器5、加氢处理反应器6为样式、大小相同的反应器;所述对比例1和2中的反应器①、反应器②、反应器③为样式、大小相同的加氢预处理反应器,并且与本发明实施例相同,反应器④、反应器⑤、反应器⑥为加氢处理反应器,并且与本发明实施例相同。本发明实施例和对比例所用渣油原料的性质见表1。表1原料性质分析项目渣油a渣油b分析方法硫含量,wt%3.202.71sh/t0689-2000氮含量,μg/g29502856sh/t0704-2001残炭(ccr),wt%12.4910.38gb/t17144-1997重金属含量fe,μg/g8.626.74icp-frippni,μg/g24.421.75icp-frippv,μg/g74.239.49icp-fripp凝点,℃2228gb/t510-1983粘度,(100℃)mm/s122.662.85gb/t11137密度(20℃),g/cm30.98390.9777gb/t13377-1992实施例1本实施例采用如图1所示的反应系统,包括第一加氢预处理反应器1、第二加氢预处理反应器2、第三加氢预处理反应器3、加氢处理反应器5、加氢处理反应器6、加氢处理反应器7。反应进料总管路l1分别通过3条入口管路与第一加氢预处理反应器1、第二加氢预处理反应器2、第三加氢预处理反应器3的入口分别相连,每条入口管路均设置有入口阀体,即反应进料总管路l1经过阀体21、阀体22、阀体23分别与第一加氢预处理反应器1、第二加氢预处理反应器2、第三加氢预处理反应器3的入口相连;反应出料总管路l2通过3条出口管路与第一加氢预处理反应器1、第二加氢预处理反应器2、第三加氢预处理反应器3的出口分别相连,每条出口管路均设置有出口阀体;即第一加氢预处理反应器1、第二加氢预处理反应器2、第三加氢预处理反应器3的出口经过阀体24、阀体25、阀体26后分别与反应出料总管路l2相连;第一加氢预处理反应器1、第二加氢预处理反应器2通过串联管路s1相连,串联管路s1的一端连接于第一加氢预处理反应器1的出口与阀体24之间的管路,而另一端连接于第二加氢预处理反应器2的进口与阀体22之间的管路,并且串联管路s1上设置有阀体27。反应进料总管路l1通过跨线直接与反应出料总管路l2连接,跨线上设置有阀体28。本实施例采用渣油原料a,其工艺流程如下:(1)装填反应器,第一加氢预处理反应器1内催化剂级配重量比例为脱金属剂:保护剂=1:2,第二加氢预处理反应器2内催化剂级配重量比例均为脱金属剂:保护剂=3:4,第三加氢预处理反应器3内的催化剂级配重量比例为脱金属剂:保护剂=5:4。开工后,打开阀体21、25和27,其余阀门关闭,第一加氢预处理反应器1和第二加氢预处理反应器2串联,并作为在线加氢预处理反应器,而第三加氢预处理反应器3处于切出状态。反应进料首先进入第一加氢预处理反应器1和第二加氢预处理反应器2,再依次进入加氢处理反应器4、5、6,进一步进行加氢处理反应后得到反应产物。1→2→4-6(2)装置运行一段时间后,当第一加氢预处理反应器1的压降达到设计上限时,关闭阀体21和27,打开阀22、23、25和26,其余阀门关闭;第二加氢预处理反应器2与第三加氢预处理反应器3并联,并作为在线加氢预处理反应器,而第一加氢预处理反应器1处于切出状态,完成第1次切换。此时,反应进料同时进入并联的第二加氢预处理反应器2与第三加氢预处理反应器3,再依次进入加氢处理反应器4、5、6,进一步进行加氢处理反应后得到反应产物。在第一加氢预处理反应器1作为切出状态(非在线加氢预处理反应器)期间,进行更换新鲜催化剂,第一加氢预处理反应器1内催化剂级配重量比例为脱金属剂:保护剂=2:1。(3)装置运行一段时间后,当第二加氢预处理反应器2的压降达到设计上限时,开阀21、23、24和26,其余阀门关闭;第一加氢预处理反应器1与第三加氢预处理反应器3并联,并作为在线加氢预处理反应器,而第二加氢预处理反应器2处于切出状态,完成第2次切换。此时,反应进料同时进入并联的第一加氢预处理反应器1与第三加氢预处理反应器3,再依次进入加氢处理反应器4、5、6,进一步进行加氢处理反应后得到反应产物。在第二加氢预处理反应器2作为切出状态(非在线加氢预处理反应器)期间,进行更换新鲜催化剂,第二加氢预处理反应器2内催化剂级配重量比例为脱金属剂:保护剂=3:1。(4)装置运行一段时间后,当第三加氢预处理反应器3的压降达到设计上限时,打开阀21、25和27,其余阀门关闭,第一加氢预处理反应器1与第二加氢预处理反应器2串联,并作为在线加氢预处理反应器,而第三加氢预处理反应器3处于切出状态,完成第3次切换。此时,反应进料依次经过第一加氢预处理反应器1与第二加氢预处理反应器2,再依次进入加氢处理反应器4、5、6,进一步进行加氢处理反应后得到反应产物。在第三加氢预处理反应器3作为切出状态(非在线加氢预处理反应器)期间,进行更换新鲜催化剂,第二加氢预处理反应器2内催化剂级配重量比例为脱金属剂:保护剂=5:1。1→2→4-6(5)按照上述方式,三个加氢预处理反应器依次循环切出、轮动、上线,进而实现加氢预处理工艺不间断运行,直到主反应器停工(第4次轮换后),而且三个加氢预处理反应器内的催化剂级配重量比例调整至脱金属剂:保护剂=5:1。表2实施例1中加氢预处理反应区的反应条件表3实施例1中加氢预处理反应区的切换条件和切换时间切换条件第一次切换第二次切换第三次切换第四次切换第一反应器压降,mpa0.6--0.6第二反应器压降,mpa-0.6--第三反应器压降,mpa--0.6-切换的时间,h550081001000011820本实施例中三个加氢预处理反应器开工初期反应温度较低时,正常运行时反应温度根据加氢预处理产物的金属(ni+v)含量在350~420℃范围内进行调整,可以逐渐增加反应温度,使金属(ni+v)含量不大于20μg/g。具体操作方式如下:在开工阶段后至第一次轮换前,根据加氢预处理产物的金属含量,分别升高第一、第二加氢预处理反应器的反应温度,例如,在步骤(1)中,第一加氢预处理反应器1在开工后100时的温度365℃,在第一次轮换前100时的温度383℃,上升18℃。在每次轮换后至下一次轮换前,根据加氢预处理产物的金属(ni+v)含量,分别升高第一、第二、第三加氢预处理反应器中两个加氢预处理反应器在线时的反应温度,例如,在步骤(2)中,第二加氢预处理反应器2在第一次轮换后100时的温度383℃,在第二次轮换前100时的温度390℃,上升7℃。在每次轮换时,未切换(不需切换)的加氢预处理反应器先进行降温操作,例如第二加氢预处理反应器2,在第一次轮换前100时反应温度为385℃,在第一次轮换后100时反应温度383℃,即在第1次轮换时,温度降低了2℃。加氢处理反应器4装填催化剂为fzc-33b:fzc-34b=1:1;加氢处理反应器5装填催化剂为fzc-34b:fzc-41b=1:1;加氢处理反应器6全部装填催化剂fzc-41b。加氢处理反应器的反应温度根据加氢生成油的硫含量进行调整,使加氢生成油的硫含量保持在0.40重量%。例如,开工后100h时,第一加氢预处理反应器1的反应温度为365℃,第二加氢预处理反应器2为368℃,加氢处理反应器4、5、6的反应温度分别为353℃、355℃、357℃,之后运转过程中各反应器反应温度根据上述控制原则进行调节。实施例2本实施例与实施例1基本相同,不同点于,原料采用渣油b,具体原料性质见表1,加氢预反应器的反应温度和切换时间见表4和表5,渣油加氢生成油性质见表6。表4实施例2中加氢预处理反应区的反应条件表5实施例2中加氢预处理反应器的切换时间第一次切换第二次切换第三次切换第四次切换切换的时间,h650094001190013750实施例3本实施例采用实施例1的反应系统、反应原料和反应器的轮换方法,不同点在于:第一加氢预处理反应器1、第二加氢预处理反应器2、第三加氢预处理反应器3内脱金属剂与保护剂的比例均为1:1,而且每次轮换保持不变,其中加氢预处理反应器的切换时间见表6。实施例3中,最终因加氢处理催化剂失活并且主反应区反应器压降达到设计值被迫停工,运转周期见表7。表6实施例3中加氢预处理反应器的切换时间第一次切换第二次切换第三次切换第四次切换切换时间,h50007300900010500对比例1对比例1所用原料a性质见表1,两个加氢预处理反应器内的脱金属催化剂与保护剂重量比例均为常规使用比例,为1:1,而且每次轮换保持不变;在同一时间段,加氢预处理反应器①、加氢预处理反应器②的反应温度相同;同时根据加氢预处理产物的金属(ni+v)含量,在350~420℃范围内调整不同时间段的加氢预处理反应器①和/或加氢预处理反应器②内的反应温度,使金属(ni+v)含量不大于20μg/g。加氢处理反应器④、加氢处理反应器⑤、加氢处理反应器⑥分别与实施例1中的加氢处理反应器4、加氢处理反应器5、加氢处理反应器6相同,而且所装填的催化剂也相同,加氢处理反应器的反应温度根据加氢生成油的硫含量进行调整,使加氢生成油的硫含量保持在0.40重量%。具体轮换方式如下:(1)开工时,反应器操作顺序为①→②→④-⑥(2)运行至5000h时,加氢预处理反应器①床层压降增大至0.6mpa,切出换剂,反应器操作顺序为:②→④-⑥(3)运行至5500h时,加氢预处理反应器①处理后反应器操作顺序为:②→①→④-⑥(4)运行至7600h时,加氢预处理反应器②床层压降增大至0.6mpa,切出换剂,反应器操作顺序为①→④-⑥(5)运行至8100h时,渣油预处理加氢反应器②处理后反应器操作顺序为①→②→④-⑥(6)按照上述方式,两个加氢预处理反应器依次循环切出换剂。当装置运行至11000h时,加氢处理催化剂失活并且主反应区反应器压降达到设计值被迫停工。对比例2对比例2的所用原料a性质见表1,三个加氢预处理反应器内的脱金属催化剂与保护剂比例均为常规使用比例,为1:1,而且每次轮换保持不变;在同一时间段,加氢预处理反应器①、加氢预处理反应器②、加氢预处理反应器③的反应温度相同;同时根据加氢预处理产物的金属(ni+v)含量,在350~420℃范围内调整不同时间段的加氢预处理反应器①、加氢预处理反应器②、加氢预处理反应器③内的反应温度,使金属(ni+v)含量不大于20μg/g。加氢处理反应器④、加氢处理反应器⑤、加氢处理反应器⑥分别与实施例1中的加氢处理反应器5、加氢处理反应器6、加氢处理反应器7相同,而且所装填的催化剂也相同,加氢处理反应器的反应温度根据加氢生成油的硫含量进行调整,使加氢生成油的硫含量保持在0.40重量%。具体轮换方式如下:(1)开工时,反应器操作顺序为(2)运行至6000h时,加氢预处理反应器③的压降达到0.6mpa,调整流程完成一次由并联到串联的切换操作。此时,反应器操作顺序为(3)运行至8500h时,加氢预处理反应器②的压降达到0.6mpa,调整流程完成第二次由并联到串联的切换操作。此时,反应器操作顺序为①→②→③→④-⑥(4)运行至9700h时,加氢预处理反应器①的压降达到临界值,整个反应系统停工。本发明实施例1-3和对比例1-2运行9000小时时,加氢处理反应区所得渣油加氢生成油的性质见表7。表7加氢处理反应区所得渣油加氢生成油性质和运行周期实施例1实施例2实施例3对比例1对比例2加氢处理生成油的性质密度(20℃),g/cm30.93010.92410.93060.93070.9346硫含量,wt%0.400.390.400.400.40n,μg/g12701121128212871302ccr,wt%5.34.465.45.45.6(ni+v),μg/g12.39.2912.512.613.1加氢处理反应器的运行周期,h127101500011810110009700需要说明的是,在上述具体实施方式中所描述的各个具体技术特征,可以通过任何合适的方式进行任意组合,其同样落入本发明所公开的范围之内。另外,本发明的各种不同的实施方式之间也可以进行任意组合,只要其不违背本发明的思想,其同样应当视为本发明所公开的内容。以上结合附图详细描述了本发明的优选实施方式,但是,本发明并不限于上述实施方式中的具体细节,在本发明的技术构思范围内,可以对本发明的技术方案进行多种简单变型,这些简单变型均属于本发明的保护范围。当前第1页12