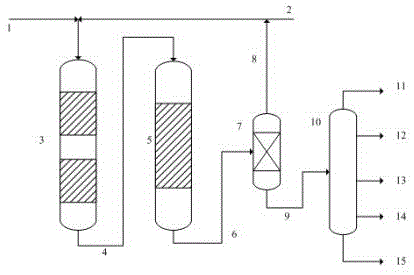
本发明涉及一种高氮高干点原料油的加氢裂化预处理方法,具体地说涉及一种高氮高干点蜡油加氢裂化方法,通过加氢裂化生产优质产品的方法。
背景技术:
:现代炼油技术中,加氢裂化是指通过加氢反应使原料中有10%以上的大分子化合物变为小分子化合物的那些加氢工艺过程,它具有原料适应性强、生产方案灵活性大、产品质量好等特点,因而已成为重油深度加工的重要工艺技术之一。加氢裂化技术的核心是催化剂,包括预处理催化剂和裂化催化剂。其中加氢裂化预处理催化剂的主要作用是:加氢脱除原料中含有的硫、氮、氧和重金属等杂质以及加氢饱和多环芳烃,改善油品的性质。因为原料油中的氮化物尤其是碱性氮化物可以毒害裂化催化剂的酸中心,因此,加氢脱氮性能是衡量加氢裂化预处理催化剂的重要指标。cn201310540358.9公开了一种劣质重质馏分油生产润滑油基础油的加氢方法。劣质重质馏分油与氢气进入第一段反应区进行加氢精制反应,反应流出物进行分离,所得液体进入第二段反应区进行加氢精制反应;第二段反应流出物进入第三段反应区,进行加氢裂化反应;加氢裂化流出物进行分离,至少部分尾油与新氢混合后,进行异构脱蜡和补充精制反应,得到各种润滑油基础油。本发明方法可在较缓和的条件下对劣质原料中的含氮杂质进行加氢处理,使其满足加氢裂化进料要求,从而拓宽了润滑油基础油的原料来源;同时由于加氢精制温度大大降低,从而可以提高装置的运转周期,加工更劣质原料或者在同样运转周期下提高装置的加工能力。但该方法需要三个加氢反应区,装置设备投资高且操作复杂,同时无法有效利用加氢反应的反应热,能耗较高。cn201110326424.3公开了一种高酸高钙重质原油的加氢处理方法,该方法包括,将高酸高钙重质原油和氢气引入串联的低压加氢处理区和高压加氢处理区,并依次与加氢保护催化剂床层、加氢脱金属催化剂床层、加氢脱硫催化剂床层和加氢脱氮催化剂床层接触,其中,所述低压加氢处理区的氢分压为1mpa-6.5mpa,所述高压加氢处理区的氢分压为7mpa-20mpa。本发明通过将整套装置分为低压加氢处理区和高压加氢处理区,既有效的实现了脱酸、脱钙,又可以将高酸高钙重质原油处理为合格的催化裂化原料,同时操作工艺安全,实现了装置的长周期稳定运转,和石油资源的有效利用。但该方法装置设备投资高且操作复杂。cn201110320460.9提供一种重质油品的固定床加氢处理方法,该方法包括,在加氢处理反应条件下,将重质油品和氢气依次引入串联的多个加氢反应器中,并与该多个加氢反应器中依次设置的加氢保护催化剂床层、加氢脱金属催化剂床层、加氢脱硫催化剂床层和加氢脱残炭催化剂床层接触,每个加氢反应器的出料口一端还设置有大孔加氢处理催化剂床层,避免了沥青质的析出和结焦,延长了催化剂的使用寿命。该方法只针对原料中沥青质含量较高劣质渣油,且无法实现原料的深度加氢饱和。cn201510046362.9公开了一种重质油加氢处理催化剂级配装填方法,反应系统包括两个或两个以上串联的加氢反应器,从第二个反应器开始,在同一反应器内,按与反应物流接触顺序,催化剂活性和可几孔径都呈递减趋势;在相邻两个反应器,按与反应物流接触顺序,前一反应器底部催化剂活性低于后一反应器顶部催化剂活性,前一反应器底部催化剂可几孔径不大于后一反应器顶部催化剂可几孔径;同时,前一反应器底部催化剂活性低于后一反应器底部催化剂活性,前一反应器底部催化剂可几孔径大于后一反应器顶部催化剂可几孔径。cn201210171553.4公开了一种最大量生产中间馏分油的加氢方法,将新鲜原料油以并流的方式同时引入加氢精制反应器和加氢裂化反应器;加氢精制反应器依次装填加氢精制催化剂和无定形加氢裂化催化剂;加氢裂化反应器依次装填无定形加氢裂化催化剂和分子筛加氢裂化催化剂;全部或部分尾油馏分进入加氢裂化反应器,加氢裂化反应器的反应流出物与部分原料油一起进入加氢精制反应器。本发明提供的方法,能处理重质馏分油,最大量生产中间馏分油。cn201410108689.x公开了一种铁和钙含量高的烃油原料加氢处理方法,包括在加氢处理反应条件下,将重质原料油依次与包括加氢处理保护催化剂ⅰ、加氢处理催化剂ⅱ和加氢处理催化剂ⅲ的催化剂组合接触,其中,所述加氢处理保护催化剂i含有载体和负载在该载体上的加氢活性金属组分,其中的载体为一种氧化铝成型物,以压汞法表征,所述成型物的孔容为0.3-0.8毫升/克,比表面积为70-220m2/g,其中,直径为6-10nm孔的孔体积占总孔容的8-25%,直径为85-160nm孔的孔体积占总孔容的40-75%。与现有技术相比,本发明具有更好的劣质原料油加氢处理性能。cn200910086744.9公开了一种加氢催化剂的级配组合;反应器自上而下分别装填加氢脱金属和加氢脱硫催化剂;原料物流自上而下,保持沿物流方向,催化剂活性逐渐增大,孔径逐渐减小,粒度逐渐减小,孔隙率逐渐减小;脱金属催化剂、加氢脱硫催化剂由一种或多种脱金属催化剂组成;活性金属组分和酸性助剂浓度分布呈不均匀分布,从催化剂颗粒表面到中心,加氢脱金属催化剂的活性金属组分和酸性助剂浓度梯度增加,加氢脱硫催化剂的活性金属组分和酸性助剂浓度梯度减少;按重量含量计算,脱金属催化剂占15~80%;脱硫催化剂占20~85%;用于重质馏分油和渣油加氢催化,具有更好的脱金属、脱残炭、脱硫活性和稳定性,控制催化剂床层的温升,减缓催化剂的失活速度。上述方法对不同孔径催化剂进行级配,都是催化剂孔径沿着物流方向逐渐降低,该方法可以有效的缓解装置压降升高速度,延长装置运行周期,但不能处理高氮高干点原料油。技术实现要素:针对现有技术的不足,本发明提供一种高氮高干点原料油加氢裂化预处理方法,该方法能够有效处理高氮高干点原料油,具有流程简单、易于操作等优点。本发明一种高氮高干点原料油加氢裂化预处理方法,包括如下内容:(1)在加氢精制工艺条件下,高氮高干点原料油与氢气混合进入加氢精制反应器进行加氢精制反应,所述加氢精制反应器内至少包含两个加氢精制催化剂床层,每个加氢精制催化剂床层上部装填加氢精制催化剂a,下部装填加氢精制催化剂b,所述加氢精制催化剂a是未经焙烧的加氢精制催化剂且在负载活性金属的同时负载了有机化合物,加氢精制催化剂b为经过焙烧的催化剂;所述加氢精制催化剂a的孔径小于加氢精制催化剂b的孔径,加氢精制催化剂a的颗粒度高于加氢精制催化剂b的颗粒度;(2)步骤(1)得到的加氢反应流出物进入加氢裂化反应器进行加氢裂化反应,加氢裂化反应器装填加氢裂化催化剂;(3)步骤(2)得到的加氢裂化反应流出物进入分离系统,经分离得到气体、石脑油、航煤和柴油的一种或几种和尾油。上述方法中,所述高氮高干点原料油初馏点一般为220~450℃,优选为330~390℃;终馏点一般为500~650℃之间,优选550~600℃,氮含量不低于1500ug/g。上述方法中,所述高氮高干点原料油密度不低于0.9g/cm3,c7不溶物不大于300ug/g,fe、ca、ni、v含量之和不超过10.0ug/g。上述方法中,加氢精制催化剂a和b的形状可以为条型或球型,如选用条型催化剂,催化剂a的颗粒度为5~10mm,如选用球型催化剂,催化剂a的颗粒度为3~6mm,催化剂a的颗粒度为加氢精制催化剂b颗粒度的1.3~3倍。上述方法中,所述加氢精制催化剂a的孔径为4~9nm,优选6~8nm,加氢精制催化剂b的孔径为加氢精制催化剂a孔径1.2~4倍。上述方法中,加氢精制反应器操作条件包括:反应压力5.0~35.0mpa,优选6.0~19.0mpa;平均反应温度为200℃~480℃,优选270℃~450℃;体积空速为0.1~15.0h-1,优选0.2~3.0h-1;氢油体积比为100:1~2500:1,优选400:1~2000:1。上述方法中,加氢裂化预处理反应器各床层入口以tn表示,且n≥2,其中,tn≥tn-1,tn-tn-1≤20℃。上述方法中,沿物流方向前一个加氢精制催化剂床层中加氢精制催化剂a同加氢精制催化剂b装填体积比低于下一个加氢精制催化剂床层中加氢精制催化剂a同加氢精制催化剂b装填体积比。上述方法中,第一加氢精制催化剂床层中加氢精制催化剂a装填体积占第一加氢精制催化剂床层的1~80v%,优选10~50v%;第二加氢精制催化剂床层中装填的加氢精制催化剂b相比第一加氢精制催化剂床层中装填的加氢精制催化剂b高5~60%,优选10~50%。上述方法中,步骤(1)所述的加氢精制催化剂可以采用市售催化剂或者按本领域现有方法制备。催化剂采用的载体一般为氧化铝、无定型硅铝、氧化硅、氧化钛等,载体中可以含有其它助剂,如p、si、b、ti、zr等;催化剂中活性组分为w、mo、ni、co中的一种或几种,活性组分是氧化态,以氧化物重量计的含量一般为15%~45%。选用氧化态催化剂在使用之前进行常规的硫化处理,使加氢活性组分转化为硫化态。其中,催化剂a在载体成型后进行高温焙烧,在温度300~750℃下焙烧0.5~20小时,再浸渍活性金属组分和有机助剂,所述有机化合物包括但不限于亚砜中的至少一种,干燥后不经过焙烧得到加氢精制催化剂,干燥温度为70~290℃,干燥时间为0.5~20h;市售的催化剂有抚顺石油化工研究院(fripp)研制开发的ff-46、ff-56,也可以按cn101491766a等所述方法制备;催化剂a在开工过程中不能进行高温干燥,同时在引入开工油前催化剂床层温度不能高于160℃。催化剂b在载体成型后进行高温焙烧,在温度300~750℃下焙烧0.5~20小时,再浸渍活性金属组分和有机助剂,经过焙烧得到加氢精制催化剂,焙烧温度300~750℃,焙烧时间为0.5~20h,市售的催化剂有抚顺石油化工研究院(fripp)研制开发的3926、3936、ch-20、ff-14、ff-18、ff-24、ff-26、ff-36、fh-98、fh-uds、fzc-41等加氢催化剂,ifp公司的hr-416、hr-448等加氢催化剂,clg公司的icr174、icr178、icr179等加氢催化剂,uop公司新开发了hc-p、hc-kuf-210/220,topsor公司的tk-525、tk-555、tk-557等加氢催化剂,akzo公司的kf-752、kf-840、kf-848、kf-901、kf-907等加氢催化剂。本发明方法中,加氢裂化反应器操作条件包括:反应压力5.0~35.0mpa,优选6.0~19.0mpa;平均反应温度为200℃~480℃,优选270℃~450℃;体积空速为0.1~15.0h-1,优选0.2~3.0h-1;氢油体积比为100:1~2500:1,优选400:1~2000:1。本发明方法中,加氢裂化催化剂通常包括裂化组分、加氢组分和粘合剂。如可以是包括现有技术在内任何适用的加氢裂化催化剂。裂化组分通常包括无定形硅铝和/或分子筛,常用分子筛如y型或usy型分子筛。粘合剂通常为氧化铝或氧化硅。加氢组分为ⅵ族、ⅶ族或ⅷ族金属、金属氧化物或金属硫化物,更优选为铁、铬、钼、钨、钴、镍、或其硫化物或氧化物中的一种或几种。以催化剂的重量为基准,加氢组分含量通常为5~40wt%。具体可以选择现有的加氢裂化催化剂,也可以根据需要制备特定的加氢裂化催化剂。商业加氢裂化催化剂主要有:uop公司的hc-12、hc-14、hc-24、hc-39等和fripp研制开发的3905、3955、fc-12、fc-16、fc-24、fc-32、3971、3976、fc-26、fc-28等,以及chevron公司研制开发的icr126、icr210等。现有技术中,针对加氢处理催化剂活性相的结构,人们先后提出了十余种理论模型,其中topsøe等人提出的co-mo-s模型是目前影响最为广泛的一种模型。co-mo-s活性相分为单层(又叫ⅰ型co-mo-s)及多层(又叫ⅱ型co-mo-s)。ⅰ型co-mo-s通过mo-o-al键与载体相连,是低硫配位的co-mo-s活性相,mo与al相互作用较强,因而影响mos2层边、角位co电子状态,导致每个活性中心本征(内在)活性低。ii型co-mo-s与载体相互作用较低,因此更易完全硫化,呈堆积(叠层)mos2结构,为高硫配位的co-mo-s活性相,通常由较大的片堆积(叠层)在一起,不与载体相连,ii型活性相每个活性中心本征活性高。纯al2o3靠mo-o-al连接,mos2单层分散好,为i型活性相,加入p、b、si助剂,可削弱mo-o-al连接,出现i型和ii型混合活性相。其中,ii型活性相催化剂加氢活性更好,具体体现在在较低的平反应温度下,加氢脱氮和芳烃饱和效果更好;但由于催化剂在制备过程中未进行高温焙烧,其高温稳定性较差,因而在加工重质劣质原料时,需要较高的反应温度,这也使这类催化剂在反应器的高温反应区其催化活性不能有效的发挥。同时,加氢精制过程普遍采用相同孔径或催化剂孔径沿物流方向逐渐增大的加氢精制催化剂,而为了使催化剂具有较高的比表面积,加氢精制催化剂平均孔径较小,这样高干点高氮原料油的大分子烃类无法进入催化剂孔道,这部分大分子物质通过调整操作的方式依然无法实现有效的脱除;而采用催化剂孔径递减的级配方式虽然大分子烃类可以进入催化剂孔道,但由于其本身活性较差,且处于反应器的低温区,仍无法对大分子烃类进行有效的脱除。本发明通过在各个催化剂床层上部(即低温反应区)装填ii型活性相加氢催化剂,下部(即高温反应区)装填普通i型活性相加氢催化剂,以及在反应器各床层底部装填大孔径加氢精制催化剂,充分发挥小孔径ii型活性相加氢催化剂低温活性好的特点,在提高加氢饱和效果的同时还能产生较大的反应热,促进普通大孔径i型活性相加氢催化剂在高温区活性的发挥,更好的提高加氢精制反应的芳烃饱和及脱氮深度,有效的脱除重质馏分油中的大分子烃类,改善产品质量。附图说明图1是本发明工艺方法的一种原则流程示意图。高干点高氮原料油1与氢气2混合进入加氢精制反应器3,加氢精制反应流出物4进入加氢裂化反应器5,加氢裂化反应流出物6进入分离器7,分离得到的气相8循环使用,液相9进入分馏塔10分离得到气体11、石脑油12、航煤13、柴油14和尾油15。具体实施方式下面通过实施例来进一步说明本发明的具体情况。采用图1所示的工艺流程,所用加氢裂化催化剂为大连石油化工研究院研制生产的商品催化剂fc-32。表1原料油主要性质原料油名称混合原料密度(20℃)/g·cm-30.9249馏程/℃ibp/10%252.8/390.130%/50%426.1/454.870%/90%485.7/530.195%/ebp549.6/575.2酸值,mg·koh/g0.51残炭,%0.22s,%0.75n/ug·g-12400c,%86.36h,%12.42金属,ppmfe1.7na2.92ni0.07v0.07表2加氢精制和加氢裂化催化剂主要物化性质催化剂催化剂a催化剂bfc-32化学组成mo-nimo-niw-ni物理性质:孔容,ml/g≮0.32≮0.30>0.32比表面,m2/g≮160≮160>240形状齿球型齿球型圆柱条平均孔径,nm811颗粒度3.52.0未经焙烧经过焙烧表3实施例工艺条件和试验结果试验编号实施例1实施例2实施例3精制反应器第一床层装填比例,%催化剂a702090催化剂b308010第二床层装填比例,%催化剂a601080催化剂b409020反应压力/mpa16.016.016.0第一床层入口温度/℃340330340第二床层入口温度/℃345350340体积空速/h-11.01.01.0氢油体积比800800800精制油含氮/ug.g-14.4129.5裂化反应器平均反应温度/℃373378375体积空速/h-11.51.51.5转化率,%767369比较例1采用现有技术,加氢精制反应器全部装填加氢精制催化剂a。比较例2采用现有技术,加氢精制反应器全部装填加氢精制催化剂b。表4实施例工艺条件和试验结果试验编号实施例1比较例1比较例2精制反应器第一床层装填比例,%催化剂a701000催化剂b300100第二床层装填比例,%催化剂a60100100催化剂b4000反应压力/mpa16.016.016.0平均反应温度/℃380380380体积空速/h-11.01.01.0氢油体积比800800800精制油含氮/ug.g-14.43120裂化反应器平均反应温度/℃373382377体积空速/h-11.51.51.5转化率,%767170由实施例可以看出,高氮高干点原料油通过本技术的加氢处理方法,可以有效降低精制油氮含量,提高裂化催化剂的裂解性能。当前第1页12