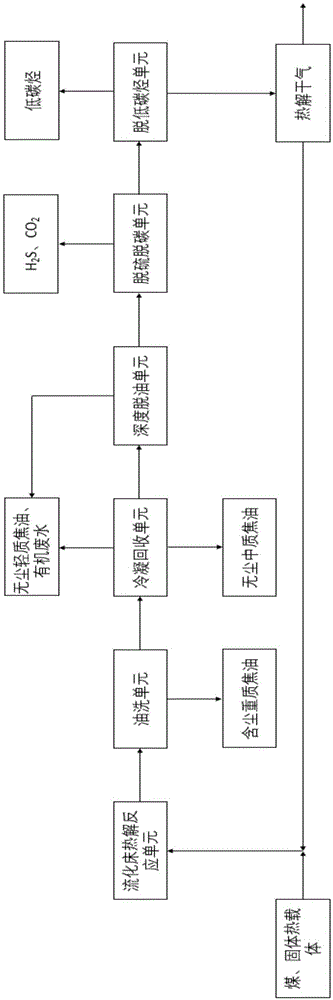
本发明涉及一种固体碳质物料热解领域,具体涉及一种碳质原料流化床热解产物分级回收系统及其回收方法。
背景技术:
:近年来,我国的石油对外依存度逐渐逼近70%,这严重制约我国国民经济的快速增长。因此将我国储量比较丰富的煤炭等固体燃料资源转化为油气资源是解决石油对外依存度较高的重要途径之一。煤炭等固体物料转化为油气资源的方法主要是煤热解及煤气化。但传统煤热解工艺在产物净化方面普遍存在着如耗能高、环保性能差、产品结构单一等问题。这不符合资源的梯级利用、合理化转化以及节能环保的目标。目前,热解油气净化主要方法是采用水洗-冷凝-脱硫-脱氨-洗苯等步骤,或对其进行简单的优化。回收产品后的净化气中仍然存在部分低碳烃类,大多数工艺将这部分净化气作为燃料直接燃烧,这对于附加值较高的低碳烃而言,造成了极大的浪费。此外,采用传统水洗工艺处理热解油气时,不仅消耗大量的水资源,而且大量的焦油、粉尘被一次性捕捉,导致了焦油品质较差、加工难度大的问题。因此,通过对热解油气进行合理的分离回收,可获得不同品质的煤焦油、低碳烃以及热解干气,产品的收益率高;选择合适的焦油回收方式可以减少水资源的使用量,同时降低排污水量,是有效的节水减排方案;此外,合理的热解干气作为流化气,与水蒸气气氛热解相比,也降低了水的用量,同时可以提高焦油产率,进一步提高产物附加值。技术实现要素:本发明的目的是提供一种碳质原料流化床热解产物分级回收系统及其回收方法,本发明提供一种碳质原料流化床热解产物分级回收系统,包括:流化床热解反应单元、油洗单元、冷凝回收单元、深度脱油单元、脱硫脱碳单元和脱低碳烃单元;流化床热解反应单元的热解油气出口与油洗单元的入口连通,所述油洗单元设置含尘重质焦油出口和热解油气出口;油洗单元的热解油气出口与冷凝回收单元的入口连通,所述冷凝回收单元设置无尘中质焦油出口、无尘轻质焦油出口、废水出口和热解油气出口;冷凝回收单元的热解油气出口与深度脱油单元的入口连通,所述深度脱油单元设置含水轻质焦油出口和热解气出口;深度脱油单元的热解气出口与脱硫脱碳单元的入口连通,所述脱硫脱碳单元设置co2、h2s出口和热解气出口,脱硫脱碳单元的热解气出口与脱低碳烃单元的入口连通,所述脱低碳烃单元设置低碳烃出口和热解干气出口。在优选的情况下,所述油洗单元中设置油洗塔,油洗塔顶部设置洗油入口,油洗塔底部设置热解油气入口和含尘重质焦油出口。在本发明其中一种优选的实施方式中,油洗塔的含尘重质焦油出口与油尘分离单元的入口连通,所述油尘分离单元设置粉尘出口和重质焦油出口,所述的重质焦油出口与油洗塔顶部的洗油入口连通。在本发明其中一种优选的实施方式中,所述冷凝回收单元中包括换热冷凝单元和稳定平衡单元,所述稳定平衡单元设置用于油水分离的平衡罐,所述平衡罐设置热解油气入口、含水轻质焦油入口、有机废水出口、无尘轻质焦油出口和热解油气出口,所述深度脱油单元的含水轻质焦油出口与平衡罐的含水轻质焦油入口连通;在本发明其中一种优选的实施方式中,所述冷凝回收单元中设置多级串联的换热器,前一级换热器底部与无尘中质焦油储罐相连,后一级换热器底部与平衡罐相连。所述平衡罐内有水相,具有脱除微量氨功能。优选,深度脱油单元选自电捕焦油脱焦油、热解油气压缩后冷凝、超低温直接冷凝单元中的一种或几种。优选,脱硫脱碳单元选自一级或多级的化学溶剂法、物理溶剂法、化学物理溶剂法、膜分离法、变压吸附法单元中的一种或几种。优选,脱低碳烃单元选自为一级或多级的深冷分离法、油吸收精馏分离法、变温变压吸附法单元中的一种或几种。优选,脱低碳烃单元的热解干气出口与热解干气缓冲罐入口连通,热解干气缓冲罐的出口与流化床热解反应单元的流化气入口连通。优选,所述流化床热解反应单元内,流化床热解反应器与气化反应器或燃烧器耦合,并与固体热载体制备单元一起构成固体热载体循环体系。在本发明优选的一种实施方式中,油尘分离单元的粉尘出口与固体热载体制备单元连通。本发明还提供一种碳质原料流化床热解产物分级回收方法,包括:(1)碳质原料进入流化床热解反应单元进行热解反应,流化床热解反应器采用固体热载体的方式加热,无需外部供热,(2)流化床热解反应单元所得的高温热解油尘气进入油洗单元,经过油洗捕集热解油尘气中的重质焦油和粉尘,(3)脱除粉尘后的热解油气经冷凝回收单元,回收热解油气中的中质焦油、轻质焦油和水分,(4)经脱焦油的热解油气进入深度脱油单元,回收剩余的轻质焦油和水分,(5)经脱焦油处理的热解气进入脱硫脱碳单元脱除其中的co2和h2s,(6)脱硫脱碳后的热解气经压缩冷凝后进入脱低碳烃单元,将热解气分离为低碳烃和热解干气。在优选的情况下,步骤(6)所得热解干气返回步骤(1)流化床热解反应器,作为流化气。优选,步骤(1)中流化床热解反应器内热解温度为500~650℃,热解压力为0.1~1mpa。整个反应设备均有保温层,防止焦油冷凝粘附而导致管道堵塞。优选,步骤(2)油洗单元选自一级、多级串联的油洗塔中的一种或几种,油洗单元的气体入口温度为480~630℃,气体出口温度为300~450℃,洗油入口温度为150~300℃,进一步优选为200~300℃。所用洗油为油洗塔底部的重质焦油,进一步优选为经冷凝、脱粉尘后重质焦油。即油洗塔底部回收的重质焦油经降温后,进行脱粉尘处理,脱粉尘后的重质焦油一部分泵入油洗塔顶部作为洗油,剩余部分进一步降温后作为产品外输。油洗塔热解油气入口位于塔底部,在塔内热解油气与洗油呈逆流接触。优选,步骤(3)的冷凝回收单元内设置多级串联的换热器,热解油气的温度逐步由300~450℃冷凝至30~80℃。在其中一种优选的实施方式中,热解油气首先经一级或多级换热器将300~450℃的热解油气冷却至120~180℃,然后再经一级或多级换热器将热解油气由120~180℃换热冷却至30~80℃。在其中一种优选的实施方式中,所述换热器内热解油气走壳程,冷凝介质走管程。所述的第一级换热器采用低温循环油做冷却介质,将出油洗塔的高温热解油气由350~450℃冷却至120~180℃,冷凝下来的无尘中质焦油进入中质焦油储罐。后续换热器采用冷水做冷却介质,将120~180℃的热解油气继续冷却至30~80℃,所述换热器冷却后的气液混合物进入平衡罐。进一步优选,换热器壳程顶部设置有脉冲式高温焦油喷嘴,用于清洗换热器,防止焦油粘附所致的换热效率降低。所述的与换热器相连的平衡罐的热解油气入口管线插入平衡罐的底部水相中,利用平衡罐底部废水吸收热解油气内的nh3。平衡罐内液体物料平均停留时间超过30min,以保证水油两相的有效分离,操作过程中保证平衡罐内同时存在水相、油相和气相。平衡罐的有机废水出口位于平衡罐的底部,排出的有机废水进入后续工段处理;轻质焦油出口位于平衡罐的中部,引出物料进一步冷凝脱水后为轻质焦油产品;热解油气出口位于平衡罐的顶部,出平衡罐的热解油气经压缩后进入深度脱油单元。优选,步骤(4)深度脱油单元选自电捕脱焦油、热解油气压缩后冷凝、超低温直接冷凝方法中的一种或几种。所述电捕焦油器操作温度在0℃以上。所述的电捕脱焦油系统无需在气体入口前加装除水装置。电捕焦油器采取切向进气,为防止气流过大、电晕线晃动带来的电场不匀。所述热解油气压缩后冷凝、超低温直接冷凝操作温度均在0℃以下,热解油气进冷凝器前需要添加干燥脱水装置。防止水分在系统中结冰,堵塞管路。所述的深度脱油单元收集的轻质焦油及少量水均返回至平衡罐中静置分层后外排。优选,步骤(5)脱硫脱碳单元选自一级或多级的化学溶剂法、物理溶剂法、化学物理溶剂法、膜分离法、变压吸附法中的一种或几种。所述的化学溶剂法可以是mea法、dea法、dipa法、mdea法等中的一种或几种。所述的物理溶剂法可以是多乙二醇二甲醚法、碳酸丙烯酯法、低温甲醇洗法等中的一种或几种。所述的化学物理溶剂法可以是乙醇胺-环丁砜法、二异丙醇胺-环丁砜法、甲基二异丙醇胺-环丁砜法等中的一种或几种。优选,步骤(6)脱低碳烃单元选自一级或多级的深冷分离法、油吸收精馏分离法、变温变压吸附法中的一种或几种。所述的深冷分离法可以是低压、中压、高压法中的一种或几种,操作压力为0.5~4.5mpa,再热釜操作温度为-30~-60℃,塔顶温度为-90~-150℃。所述的油吸收精馏分离法可以是一级或多级串联的吸收塔、精馏塔。所选吸收剂为汽油或柴油中的一种或几种。所述的变温变压吸附法为一级或多级串联或并联的吸附塔,采取多塔循环、交替吸附的操作模式。回收的多组分低碳烃移出系统。脱低碳烃单元分离出的热解干气进入气体缓冲罐,所述的热解干气一部分经调压、预热后进入流化床热解反应器,作为流化床热解反应器的流化气;另一部分热解干气作为产品外输。与现有工艺技术相比,本发明具有以下优势:(1)本发明采用脱低碳烃后的热解干气为流化气,不以水蒸气为流化气,降低了水的用量。(2)通过多段焦油回收操作,分别回收了重质焦油、中质焦油和轻质焦油,实现了焦油的梯级回收利用,焦油产品质量高,利于加工。(3)焦油回收过程不采用荒煤气水洗工艺,减少了有机废水排放量,降低了废水处理成本,且有利于环保。(4)回收了热解气中的低碳烃产物,避免了直接燃烧,提高了产品的附加值。附图说明图1是本发明提供的碳质原料流化床热解产物分级回收系统示意图图2是本发明提供的碳质原料流化床热解产物分级回收方法的工艺流程示意图1-流化床热解反应器,2-油洗塔,3-焦油脱粉尘装置,4-横管式换热器,5-气液分离罐,6-横管式换热器,7-平衡罐,8-电捕焦油器,9-脱硫脱碳塔,10-冷箱,11-脱甲烷塔,12-热解干气储罐。a-原料入口,b-固体热载体入口,c-流化气入口,d-热解半焦出口,e-粉尘出口,f-重质焦油出口,g-冷却介质出口,h-冷却介质入口,i-中质焦油出口,j-冷却介质出口,k-冷却介质入口,l-有机废水出口,m-轻质焦油出口,n-吸收h2s和co2后的nhd富液出口,o-nhd溶剂入口,p-液态低碳烃出口,q-热解干气出口。具体实施方式下面结合附图对本发明进行进一步的说明,但并不因此而限制本发明。图1是本发明提供的碳质原料流化床热解产物分级回收系统示意图,如图1所示,本发明提供一种碳质原料流化床热解产物分级回收系统,包括:流化床热解反应单元、油洗单元、冷凝回收单元、深度脱油单元、脱硫脱碳单元和脱低碳烃单元;流化床热解反应单元的热解油气出口与油洗单元的入口连通,所述油洗单元设置重质焦油出口和热解油气出口;油洗单元的热解油气出口与冷凝回收单元的入口连通,所述冷凝回收单元设置中质焦油出口、轻质焦油出口、废水出口和热解油气出口;冷凝回收单元的热解油气出口与深度脱油单元的入口连通,所述深度脱油单元设置含水轻质焦油出口和热解气出口;深度脱油单元的热解气出口与脱硫脱碳单元的入口连通,所述脱硫脱碳单元设置co2、h2s出口和热解气出口,脱硫脱碳单元的热解气出口与脱低碳烃单元的入口连通,所述脱低碳烃单元设置低碳烃出口和热解干气出口。下面结合实施例对本发明作进一步的说明,但并不因此而使本发明受到任何限制。实施例1本实施例的碳质原料流化床热解产物分级回收方法的工艺流程示意图如图2所示。原料、固体热载体以及流化气分别由原料入口a、固体热载体入口b以及流化气入口c进入流化床热解反应器1。在流化床热解反应器1内进行热解反应,热解反应为常压操作。热解半焦由位于流化床热解反应器1中上部的热解半焦出口d排出,热解油气由流化床热解反应器1顶部排出后由油洗塔2底部的气体入口进入油洗塔2,油洗塔2用冷焦油逆流洗涤热解油气,回收重质焦油的同时除去粉尘。油洗塔2底部重质焦油出口温度为350℃。油洗塔洗涤下来的含尘重质焦油进入油尘分离单元3,脱除的粉尘由粉尘出口e排出后与热解半焦一并进入固体热载体制备单元。经脱粉尘后的重质焦油一部分由重质焦油出口f外输为重质焦油产品,另一部分经冷却后泵入油洗塔塔顶作为洗油。洗油的油洗塔入口温度为250℃。油洗塔2排出的热解油气进入第一级换热器4,第一级换热器4所选冷却介质为循环冷却油,冷却介质经入口h进入第一级换热器4并由出口g排出,第一级换热器4的热解油气入口温度为360℃,热解油气出口温度180℃。冷却后的热解油气进入气液分离罐5,其中中质焦油由气液分离罐5底部的中质焦油出口i排出,分离所得的热解油气进入第二级换热器6。第二级换热器6所用冷却介质为循环冷却水,冷却介质经入口k进入第二级换热器6并由出口j排出。第二级换热器6热解油气入口温度为180℃,热解油气出口温度为30℃。冷却后的气液混合物经平衡罐7的热解油气入口和管线通入平衡罐7底部水相中脱除部分nh3,油水混合物在平衡罐7内静置分层,有机酚水由底部有机废水出口l排出,无尘轻质焦油在平衡罐7中部的轻质焦油出口m排出,气体物流则在顶部的热解油气出口排出并经压缩后进入电捕焦油器8。电捕焦油器8所用直流电压根据进气口油水浓度而定,捕集的焦油和少量水分一起再进入平衡罐7内进行油水分离。脱油后的热解气经进一步压缩换热后进入脱硫脱碳单元。所述的脱硫脱碳单元采用多乙二醇二甲醚法,具体为nhd法,热解气由底部入口进入脱硫脱碳塔9进行脱co2和h2s过程。吸收co2和h2s后的nhd富液由塔底部富液出口n排出后进入闪蒸槽和再生塔,回收co2和h2s。nhd溶剂由脱硫脱碳塔9上部的nhd溶剂入口o进入脱硫脱碳塔9,所述的脱硫脱碳塔9操作温度为12℃。脱co2和h2s后的热解气经压缩换热后进入脱甲烷塔11进行脱低碳烃过程。脱甲烷塔11所选脱甲烷工艺为高压法,操作压力为4.1mpa,再沸器温度为-50℃,塔顶温度为-96℃。低碳烃由脱甲烷塔11底部出口p输出后进入脱乙烷塔、脱丙烷塔等精分离装置。脱低碳烃后的热解干气由脱甲烷塔11顶部排出后进入热解干气储罐12。一部分热解干气经调压、预热后进入流化床热解反应器1做流化气,另一部分经热解干气储罐12的热解干气出口q外输为产品。实施例2实施例2是在实施例1所述工艺流程中完成的,所用煤样a干燥粉碎为40~80目的粉煤样品,样品的工业分析和元素分析如表1所示。表1煤样的工业分析和元素分析煤样a煤样b工业分析mad0.655.83ad11.0311.47vdaf33.4538.40fcdaf66.5561.60元素分析/dafc79.8671.47h4.474.29n1.071.10s1.331.39o13.2721.75所述的流化床热解反应器热解温度为600℃,所选流化速度为0.8m/s。粉煤原料a的进料量为100t/h。油洗塔回收含尘重质焦油4.7t/h。第一级换热器回收无尘中质焦油3.6t/h;第二级换热器回收无尘轻质焦油0.64t/h,同时外排有机废水2.2t/h。脱硫脱碳单元回收co2和h2s分别为2238nm3/h和63.36nm3/h。脱低碳烃单元回收低碳烃为1.5t/h,热解干气为6248nm3/h。实施例3实施例3所用煤样b干燥粉碎为40~80目的粉煤样品,样品的工业分析和元素分析如表1所示。所述的流化床热解反应器热解温度为550℃,流化速度为0.8m/s。粉煤原料b的进料量为100t/h。油洗塔回收含尘重质焦油6.2t/h。第一级换热器回收无尘中质焦油5.3t/h;第二级换热器回收无尘轻质焦油1.1t/h,同时外排有机废水6.2t/h。脱硫脱碳单元回收co2和h2s分别为2916nm3/h和93nm3/h。脱低碳烃单元回收低碳烃为1.61t/h,热解干气为7700nm3/h。实施例4实施例4所用煤样与实施例3相同,所述的流化床热解反应器热解温度为600℃。油洗塔回收含尘重质焦油5.4t/h。第一级换热器回收无尘中质焦油4.3t/h;第二级换热器回收无尘轻质焦油0.8t/h,同时外排有机废水6.7t/h。脱硫脱碳单元回收co2和h2s分别为4370nm3/h和87nm3/h。脱低碳烃单元回收低碳烃为1.91t/h,热解干气为13125nm3/h。以上所述仅为本发明的优选实施例,并不用于限制本发明,对于本领域的技术人员来讲,本发明可以有各种更改和变化。凡在本发明的精神和原则之内,所做的任何修改、等同替换、改进等,均应包含在本发明的保护范围之内。当前第1页12