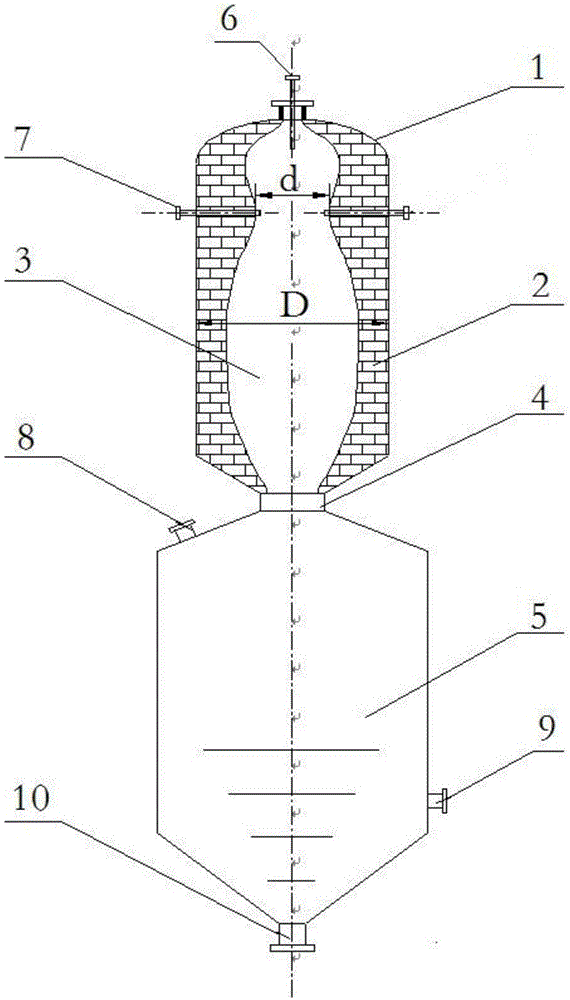
本发明属于能源化工生产
技术领域:
,具体涉及一种碳一化工燃料以多元共轭方式反应制取合成气的方法。
背景技术:
:碳一化学工业是研究含有一个碳原子的物质为原料合成工业产品的化学工艺。一个碳原子的物质主要有co、co2、ch4、ch3oh、hcho,碳一化工燃料是针对碳一化学工业归集出来的含有一个碳原子的原料集,多指煤、天然气、焦炉气、油田气、炼厂气和煤层气等通过化学反应能产生合成气的气液固原料。煤因其藏量丰富、分布广泛、获取和运输容易,永远都是能源化工生产
技术领域:
原料选用的主角,作为不可再生的化石能源,对煤炭资源的扎实利用是当前和今后科学界的一个创新主题,先有技术后有煤是当下煤炭利用的基本原则。根据生产和工艺需要,原煤可以预制成粉体或浆料供生产用,近年来,在环境治理和节能减排政策指引下,经过科研人员的不断技术创新,一些工农业生产产生的有机固(危)废、生物质、城市垃圾以及其它含碳自然资源和生活垃圾等物质也纳入到碳一化工工业生产原料集中,壮大了碳一化工的体量,使发展碳一化工成为能源化工领域的主体。在当下资源日益紧缺的情况下,如何提高资源利用率一直是业界探讨的主流话题。煤油气作为三大不可再生的化石能源对国民经济和国防工业和国防安全都有重大的保障作用,油气资源更以其优秀的理化特性像血液一样流淌在国民经济的机体里,国民经济的这一运行特点导致了油气资源快速高额消耗甚至出现严重短缺,直接影响到国民经济的健康运行,因此近多年来,业界人员提出了煤转气和煤转油这两个创新性的科学命题并付诸了产业化运行,大大缓解了油气资源短缺引发的能源供需矛盾,但煤炭资源因其结构复杂、理化性质迥异等特性,导致煤转气转油过程中有用成分传质效果不好,造成煤炭资源浪费严重,针对引发的这一次生问题,科研人员倾心研究,提出了一个又一个新观点,开发了一个又一个具有针对性的新技术,以期解决煤炭资源最大化有效利用这一技术难题。技术实现要素:本发明所要解决的技术问题在于针对上述现有技术的不足,提供了一种碳一化工燃料以多元共轭方式反应制取合成气的方法。该方法对气化炉的反应腔以及喷嘴进行设计,使气化炉的反应腔的实际反应空间与原料反应的流场匹配,使碳一气态燃料和碳一固态燃料原料在反应腔中高强度混合并充分接触,提高了反应中的传质效果,并引发产物间的多元共轭反应,从而得到高浓度的以co和h2为主要成分的粗合成气,提高了碳一燃料资源的利用效率,降低了制取资源成本。为解决上述技术问题,本发明采用的技术方案是:一种碳一化工燃料以多元共轭方式反应制取合成气的方法,其特征在于,该方法包括以下步骤:步骤一、将烘炉烧嘴内嵌于安装在气化炉顶部的气态燃料喷嘴中,然后进行烘炉,直至气化炉预热至安全投料温度;步骤二、将烘炉烧嘴从气态燃料喷嘴中拆卸取出,将第一氧化剂管道、气态燃料管道和第二氧化剂管道按照套筒方式依次从里向外同轴装配在气态燃料喷嘴中,然后将碳一气态燃料通过气态燃料管道通入气化炉中,同时将碳一固态燃料磨制成的高浓度浆料与氧化剂通过位于气化炉侧上方的浆料喷嘴通入气化炉中,碳一气态燃料和高浓度浆料进入气化炉的气化段后,将氧化剂通过第一氧化剂管道和第二氧化剂管道通入气化炉中,并在反应腔中与碳一气态燃料和高浓度浆料混合,发生多元共轭反应,生成粗合成气;所述气态燃料喷嘴的外壳、第一氧化剂管道、气态燃料管道和第二氧化剂管道相邻之间均形成冷却水通道;所述多元共轭反应的温度为1250℃~1450℃,压力为1.0mpa~9.0mpa;所述粗合成气的主要成分为co和h2;所述反应腔呈扁长葫芦型,其中反应腔细颈部的直径d与反应腔腹部最粗处的直径d之间的关系为:d=0.382d,以细颈部为分界的反应腔上下两段腔室的轴向高度为1:3,所述反应腔细颈部处开设有相对的浆料喷嘴,所述浆料喷嘴的中心连线与气化炉的轴线垂直;步骤三、将步骤二中生成的粗合成气和未反应固体余物形成的气固混合物并行送入气化炉的淬冷段中,在并行送入过程中通过淬冷水切入结构输入带压低温水对气固混合物进行淬冷,气固混合物中的粗合成气携带淬冷过程中换热产生的大量过热蒸汽从排气口排出气化炉并进行收集,气固混合物中的未反应固体余物凝聚成渣团沉降至淬冷段底部积聚的淬冷水中继续进行换热,换热后的淬冷水从排水口排出气化炉并进行热量回收,换热后的未反应固体余物渣团从排渣口排出气化炉。本发明将碳一气态燃料和碳一固态燃料磨制成的高浓度浆料分别通过设置在气化炉顶部的气态燃料喷嘴和设置在气化炉侧方的浆料喷嘴送入气化炉的气化段并在反应腔内进行快速、高密度的分散交汇,然后在氧化剂存在及一定的温度和压力条件下,碳一气态燃料和碳一固态燃料磨制成的高浓度浆料发生高强度元素层级的多元共轭反应,生成以co和h2为主要成分的粗合成气,各反应式如下所示:c+o2→co2(a)c+co2→2co(b)c+h2o→co+h2(c)c+2h2→ch4(d)s+h2→h2s(e)s+co→cos(f)ch4+2o2→co2+2h2o(g)ch4+h2o→co+3h2(h)ch4+co2→2co+2h2(i)co+h2o→co2+h2(j)从上述反应式可以看出,多元共轭反应过程中反应原料中的c、h、o、s间发生氧化合成反应,生成co2、h2o、ch4,由于ch4和h2o分别为多元共轭反应的原料主要成分和辅料,反应过程中生成ch4和h2o的量较小可以忽略不计,因此影响多元共轭反应的唯一关键产物为co2,根据化学平衡反应原理,反应(b)和反应(i)不断消耗co2,促进了生成co2的反应(a)、反应(g)和反应(j)的持续进行,反过来又促进了co和h2的持续生成;另外,由于碳一固态燃料磨制成的高浓度浆料中含有的水可作为原料参与多元共轭反应,促进了反应(c)和反应(h)的持续进行,提高了co和h2的生成量,反应产物co2、co、h2、h2o、ch4之间的多元共轭效应促使碳一固态燃料磨制成的高浓度浆料中有用的c、h等元素和碳一气态燃料中ch4的彻底转化,碳一燃料中的能量几乎全部转载到粗合成气中,从而大大提高了co和h2的产量,使碳一燃料资源的利用率最大化,避免了碳一燃料资源的浪费。由于气化炉的反应腔呈扁长葫芦型,并且反应腔细颈部的直径d与反应腔腹部最粗处的直径d之间存在着数学黄金分割的数值关系,细颈部为分界点的上下两段腔室的轴向高度为1:3,使得反应腔的空间与多元共轭反应流场高度匹配,原料碳一气态燃料和碳一固态燃料磨制成的高浓度浆料进入反应腔后得到更充分分散混合,从而触发元素层级间的反应,引发多元共轭反应链,使主要反应向着生成co和h2的方向进行,原料在气化段短暂的停留时间内进行了高效的传质,并在淬冷段的有效行程中使反应进行的更为彻底,进一步提高了原料的转化率。本发明的碳一燃料经反应后生成高浓度的以co和h2为主要成分的粗合成气,将粗合成气和未反应固体余物形成的气固混合物并行送入气化炉的淬冷段中并采用带压低温水进行淬冷,短暂的淬冷过程迫使气固混合物迅速完全分离,粗合成气被带压低温水淬冷脱灰并大幅降温同时产生大量过热蒸汽,粗合成气被过热蒸汽饱和后从排气口排出气化炉然后送往气体净化工段进一步深度处理,未反应固体余物和粗合成气中夹带的细粒未反应固体余物迅速抱团凝聚成大块渣团落入淬冷段底部积聚的淬冷水中进行充分换热至平衡,从而实现对未反应固体余物的显热的回收,转载了大量未反应固体余物的显热的高温水可沿着整个气化生产系统逐一下行,反哺或填补各个生产系统因热量不足而造成的额外能量消耗,而换热平衡后的未反应固体余物渣团从排渣口排出气化炉送往收集处理场所进行进一步回收利用。本发明所述多元共轭反应的压力为表压(g)。上述的一种碳一化工燃料以多元共轭方式反应制取合成气的方法,其特征在于,步骤一中所述烘炉采用的燃料为步骤二中所述碳一气态燃料中的一种或两种以上,或者为常态甲醇、汽化甲醇、工厂弛放气,和焦碳生产产生的荒煤气中的一种。上述燃料中均含有c、h为主要元素的化合物,具有较高的利用价值,同时也是生产过程中的副产品,可以通过本方法进行二次利用提升其使用价值。上述的一种碳一化工燃料以多元共轭方式反应制取合成气的方法,其特征在于,步骤二中所述碳一气态燃料为天然气、焦炉气、油田气、炼厂气、煤层气、沼气和甲烷中的一种或两种以上。上述的一种碳一化工燃料以多元共轭方式反应制取合成气的方法,其特征在于,步骤二中所述碳一固态燃料为煤或与煤成分近似的有机固废物、农林残渣;所述碳一固态燃料磨制成的高浓度浆料为固相浓度不小于65wt%的水基浆料。采用煤如烟煤、无烟煤等作为碳一固态燃料,使用前需要对煤依次进行干燥、粉碎和研磨等物理处理,然后配制成粒级级配合理且固相浓度不小于65wt%的水基浆料,以便在气化炉中与碳一气态燃料的充分接触,从而发生高强度元素层级的多元共轭反应。与煤同质的有机固废物包括城市垃圾、有机化工生产和食品行业产生的废弃物,如医药化工生产的包装、残次品和下脚料以及并生的一些危废物品,使用前也需要依次经干燥、粉碎、研磨、配制调浆成固相浓度不小于65wt%的水基浆料。农林残渣是农林生产过程中产生的废弃物,如碎枝、木渣、果壳等,经干燥、粉碎、研磨,单独配制成固相浓度不小于65wt%的水基浆料或与煤等混合后经上述处理配制成固相浓度不小于65wt%的水基浆料。上述的一种碳一化工燃料以多元共轭方式反应制取合成气的方法,其特征在于,步骤二中所述氧化剂为含氧体积大于96%的气体。采用该氧化剂可减少合成气中的n2、ar等气体,尽可能提高合成气的有效成分co、h2的纯度。商业空气分离装置制取含氧体积大于96%的氧化剂在经济上也具有可行性。本发明气化炉的反应腔由耐火材料制成的预筑品制成,如氧化铬和氧化铝空心球浇注料、高铬砖等产品。上述的一种碳一化工燃料以多元共轭方式反应制取合成气的方法,其特征在于,步骤二中所述烘炉烧嘴为缩口筒管型烧嘴,且所述烘炉烧嘴的直径与第一氧化剂管道、气态燃料管道和第二氧化剂管道按照套筒方式依次从里向外同轴装配形成的结构的直径相等。烘炉烧嘴设计为缩口筒管型烧嘴,与气态燃料喷嘴的缩口设计相匹配吻合,有利于烘炉过程的高效进行;当烘炉过程结束后,取出烘炉烧嘴,将第一氧化剂管道、气态燃料管道和第二氧化剂管道按照套筒方式依次从里向外同轴装配在燃料喷嘴中,进行碳一气态燃料和氧化剂的进料,烘炉烧嘴的直径与第一氧化剂管道、气态燃料管道和第二氧化剂管道按照套筒方式依次从里向外同轴装配形成的结构的直径相等,保证了烘炉烧嘴与气态燃料管道和氧化剂管道均能够在气化炉上安装。上述的一种碳一化工燃料以多元共轭方式反应制取合成气的方法,其特征在于,步骤三中所述淬冷水切入结构为壁厚δ的环形结构通道,所述环形结构通道的内壁上均匀布设有俯角为α、孔径为ф,孔间距为μ的斜孔,其中ф=δ,μ=5ф,10°≤α≤45°。按照上述俯角、孔径、孔间距布置的淬冷水切入结构的环形结构通道上的水分布均匀,不易堵塞,与合成气、未反应的固体余物能够充分混合进行热量交换,保证对合成气、未反应的固体余物进行有效冷却。上述的一种碳一化工燃料以多元共轭方式反应制取合成气的方法,其特征在于,步骤三中所述粗合成气中的co和h2的干气体积总含量大于93%。本发明的制取合成气的方法大大提高了co和h2的含量,促进了碳一气态燃料和碳一固态燃料的转化,实现了碳一燃料资源的高效利用。上述的一种碳一化工燃料以多元共轭方式反应制取合成气的方法,其特征在于,步骤三中所述排出气化炉的换热后的未反应固体余物渣团的干质中的碳元素含量小于2.50wt%;所述排出气化炉的换热后的淬冷水中携带的未反应固体余物渣团中的碳元素含量小于9.00wt%。本发明方法得到的未反应固体余物渣团中的碳元素含量极低,说明了原料中的有效元素碳元素的转化率较高,原料资源的利用更为彻底。本发明与现有技术相比具有以下优点:1、本发明中以碳一气态燃料和碳一固态燃料为原料,对气化炉的反应腔以及喷嘴进行设计,使气化炉的反应腔的实际反应空间与原料反应的流场匹配,使原料在反应腔中高强度混合并充分接触,提高了反应中的传质效果,并通过关键中间产物co2,引发产物间的多元共轭反应,让反应向着原料中c元素和o、h元素转化生成co和h2的方向进行,从而得到高浓度的以co和h2为主要成分的粗合成气,大大提高了co和h2的产量,并提高了碳一燃料资源的利用效率,避免了碳一燃料资源的浪费,降低了制取资源成本,减缓能源消耗速度,实现了化石资源的可持续发展。2、本发明同时采用碳一气态燃料和碳一固态燃料为原料进行多喷嘴进料,可以根据目标产品的需要,通过调节碳一气态燃料和碳一固态燃料的进料比例,从源头上进行控制,实现合成气中h2/co比值的调节,方便易行,灵活高效。3、本发明的碳一气态燃料和碳一固态燃料的来源广泛,原料易得,既扩大了本发明制取方法的应用范围,又实现了对资源包括废弃物资源的充分利用;由于原料来源广泛,且采用多喷嘴进料,显著提高了本发明方法的制取合成气的生产能力,降低了生产原料、设备和土地成本,特别适用于大型煤化工企业制取合成气的生产。4、本发明制取得到的粗合成气中的co和h2的干气体积总含量大于93%,比单一含碳固体燃料产生的合成气co、h2的体积含量高近10%。5、本发明方法得到的未反应余物中的碳元素含量极低,对原料资源的利用率更高,且未反应余物中的有效元素含量更少,有害元素ca、na、mg、fe、al等固化更好,整体固废排放更少,对环境友好。6、本发明将烘炉烧嘴安装在气态燃料喷嘴中代替第一氧化剂管道、气态燃料管道和第二氧化剂管道按照套筒方式依次从里向外同轴装配在气态燃料喷嘴中进行烘炉操作,大大减轻了烘炉时人财物消耗,避免了烧嘴整体吊装更换,更换烧嘴更便捷、更省时、更安全,且避免了烧嘴回火发生人身安全事故。下面通过附图和实施例对本发明的技术方案作进一步的详细描述。附图说明图1为本发明采用的气化炉的结构示意图。图2为本发明的第一氧化剂管道、气态燃料管道和第二氧化剂管道与气态燃料喷嘴的装配结构示意图。图3为本发明采用的烘炉喷嘴的结构示意图。图4为本发明的烘炉喷嘴与气态燃料喷嘴的装配结构示意图。附图标记说明1—气化炉;2—气化段;3—反应腔;4—淬冷水切入机构;5—淬冷段;6—气态燃料喷嘴;7—浆料喷嘴;8—排气口;9—排水口;10—排渣口;11—烘炉烧嘴;12—气态燃料管道;13—冷却水通道;14-1—第一氧化剂管道;14-2—第二氧化剂管道。具体实施方式如图1所示,本发明采用的气化炉1由气化段2和淬冷段5通过淬冷水切入结构4连通而成,所述气化段2包括反应腔3,所述反应腔3的顶部与气态燃料喷嘴6相连,所述反应腔3的上侧方与浆料喷嘴7相连,所述淬冷段5的上方开设有排气口8,淬冷段5的下侧方开设有排水口9,淬冷段5的正下方开设有排渣口10。如图2所示,当进行碳一气态燃料进料时,将第一氧化剂管道14-1、气态燃料管道12和第二氧化剂管道14-2按照套筒方式依次从里向外同轴装配在气态燃料喷嘴6,所述气态燃料喷嘴6的外壳、第一氧化剂管道14-1、气态燃料管道12和第二氧化剂管道14-2相邻之间均形成冷却水通道13。如图3和图4所示,当进行烘炉操作时,将烘炉烧嘴11安装在气态燃料喷嘴6中。本发明实施例1~实施例4中对原料碳一气态燃料、碳一固态燃料、氧化物、合成气采用的分析方法分别为:煤的工业分析方法gb/t212-2008、煤的发热量测定方法gb/t213-2008、煤中全水分的测定方法gb/t211-2017、煤中碳和氢的测定方法gb/t476-2008、煤灰成分分析方法gb/t1574-2007、煤中全硫的测定方法gb/t214-2007、煤的可磨性指数测定方法哈德格罗夫法gb/t2565-2014、煤中砷的测定方法gb/t3058-2008、煤中氯的测定方法gb/t3558-2014等国标所述的标准方法、天然气采用天然气的组成分析气相色谱法gb/t13610-2014标准方法、氧气采用工业氧gb/t3863-2008标准方法。实施例1本实施例包括以下步骤:步骤一、将烘炉烧嘴11内嵌于安装在气化炉1顶部的气态燃料喷嘴6中,然后采用气态甲醇为燃料进行烘炉,直至气化炉1预热至1000℃以上;步骤二、将烘炉烧嘴11从气态燃料喷嘴6中拆卸取出,将第一氧化剂管道14-1、气态燃料管道12和第二氧化剂管道14-2按照套筒方式依次从里向外同轴装配在气态燃料喷嘴6中,然后将碳一气态燃料通过气态燃料管道12通入气化炉1中,同时将碳一固态燃料与氧化剂通过位于气化炉1侧上方的浆料喷嘴7通入气化炉1中,碳一气态燃料和高浓度浆料进入气化炉1的气化段2后,将氧化剂通过第一氧化剂管道14-1和第二氧化剂管道14-2通入气化炉1中,并在反应腔3中与碳一气态燃料和高浓度浆料混合,发生多元共轭反应,生成粗合成气;所述气态燃料喷嘴6的外壳、第一氧化剂管道14-1、气态燃料管道12和第二氧化剂管道14-2相邻之间均形成冷却水通道13;所述烘炉烧嘴11为缩口筒管型烧嘴,且所述烘炉烧嘴11的直径与第一氧化剂管道14-1、气态燃料管道12和第二氧化剂管道14-2按照套筒方式依次从里向外同轴装配形成的结构的直径相等;所述碳一气态燃料为ch4体积含量为96%的天然气,碳一固态燃料为神府煤,使用前磨制成的浓度为65wt%的水基浆料;所述多元共轭反应的温度为1450℃,压力为6.50mpa,该多元共轭反应的压力为表压(g);所述粗合成气的主要成分为co和h2;所述氧化剂为体积纯度99.6%的氧气;所述反应腔3呈扁长葫芦型,其中反应腔3细颈部的直径d为1222.40mm,反应腔3腹部最粗处的直径d为3200.00mm,以细颈部为分界的反应腔3上下两段腔室的轴向高度为1:3,所述反应腔3细颈部处开设有相对的浆料喷嘴7,所述浆料喷嘴7的中心连线与气化炉1的轴线垂直;步骤二中采用的碳一固态燃料、碳一气态燃料的物性参数如下表1和表2所示,氧化剂的反应分配参数如下表3所示,碳一固态燃料磨制成的水基浆料的入炉参数如下表4所示:表1实施例1的碳一固态燃料的物性参数表2实施例1的碳一气态燃料的物性参数表3实施例1的氧化剂的反应分配参数名称温度(℃)压力(mpa(g))流量(nm3/h)第一氧化剂通道40.007.502550第二氧化剂通道40.007.5014450煤浆氧化剂40.007.5012250表4实施例1的碳一固态燃料磨制成的水基浆料的入炉参数浓度(wt%)流量(kg/h)入喷嘴温度(℃)入喷嘴压力(mpa)6525000.0030.006.65步骤三、将步骤二中生成的粗合成气和未反应固体余物形成的气固混合物并行送入气化炉1的淬冷段5中,在并行送入过程中通过淬冷水切入结构4输入带压低温水对气固混合物进行淬冷,气固混合物中的粗合成气携带淬冷过程中换热产生的大量过热蒸汽从排气口8排出气化炉1并进行收集,气固混合物中的未反应固体余物凝聚成渣团沉降至淬冷段5底部积聚的淬冷水中继续进行换热,换热后的淬冷水从排水口9排出气化炉1并进行热量回收,换热后的未反应固体余物渣团从排渣口10排出气化炉1;所述淬冷水切入结构4为壁厚δ的环形结构通道,所述环形结构通道的内壁上均匀布设有俯角为α、孔径为ф,孔间距为μ的斜孔,其中ф=δ=10.00mm,μ=50.00mm,α为30°;所述排出气化炉的换热后的未反应固体余物渣团的干质中的碳元素含量为1.58wt%;所述排出气化炉的换热后的淬冷水中携带的未反应固体余物渣团中的碳元素含量为7.26wt%。本实施例制取的粗合成气的干气组成如下表5所示。表5实施例1制取的粗合成气的干气组成组分体积含量(%)h253.14co40.93co25.35h2s0.003ch40.046n20.491ar0.040总计100.00从表5可知,本实施例制取的粗合成气的干气组成以co和h2为主,且co和h2的干气体积总含量为94.07%。本实施例烘炉采用的燃料还可为ch4体积含量为96%的天然气,常态甲醇、工厂弛放气,和焦碳生产产生的荒煤气中的一种。所述碳一气态燃料还可为焦炉气、油田气、炼厂气、煤层气、沼气和甲烷中的一种,或者天然气、焦炉气、油田气、炼厂气、煤层气、沼气和甲烷中的一种或两种以上。所述碳一固态燃料还可为与煤成分近似的有机固废物、农林残渣。实施例2本实施例与实施例1的不同之处在于:步骤一中采用天然气为原料进行烘炉;步骤二中采用的碳一固态燃料为内蒙煤,碳一气态燃料为ch4含量96.63%的天然气,碳一固态燃料、碳一气态燃料的物性参数分别如下表6和表7所示,氧化剂为体积纯度99.6%的氧气,氧化剂的反应分配参数如下表8所示,碳一固态燃料磨制成的水基浆料的入炉参数如下表9所示,所述多元共轭反应的温度为1250℃,压力为1.0mpa,该多元共轭反应的压力为表压(g);步骤三中制取的粗合成气的干气体积组成如下表10所示,所述排出气化炉的换热后的未反应固体余物渣团的干质中的碳元素含量为2.15wt%;所述排出气化炉的换热后的淬冷水中携带的未反应固体余物渣团中的碳元素含量为8.32wt%。表6实施例2的碳一固态燃料的物性参数表7实施例2的碳一气态燃料的物性参数表8实施例2的氧化剂的反应分配参数名称温度(℃)压力(mpa(g))流量(nm3/h)第一氧化剂通道40.002.002500第二氧化剂通道40.002.0014500煤浆氧化剂40.002.0012300表9实施例2的碳一固态燃料磨制成的水基浆料的入炉参数浓度(wt%)流量(kg/h)入喷嘴温度(℃)入喷嘴压力(mpa)6525000.0030.001.20表10实施例2制取的粗合成气的干气组成组分体积含量(%)h252.74co40.77co26.01h2s0.003ch40.030n20.407ar0.04总计100.00从表10可知,本实施例制取的粗合成气的干气组成以co和h2为主,且co和h2的干气体积总含量为93.51%。实施例3本实施例与实施例1的不同之处在于:步骤一中采用天然气为原料进行烘炉,步骤二中采用的碳一固态燃料为新疆煤,碳一气态燃料为ch4含量96.63%的天然气,碳一固态燃料、碳一气态燃料的物性参数分别如下表11和表12所示,氧化剂为体积纯度99.6%的氧气,氧化剂的反应分配参数如下表13所示,碳一固态燃料磨制成的水基浆料的入炉参数如下表14所示,所述多元共轭反应的压力为9.0mpa,温度1350℃,该多元共轭反应的压力为表压(g);步骤三中制取的粗合成气的干气体积组成如下表15所示,所述排出气化炉的换热后的未反应固体余物渣团的干质中的碳元素含量为2.37wt%;所述排出气化炉的换热后的淬冷水中携带的未反应固体余物渣团中的碳元素含量为8.03wt%。表11实施例3的碳一固态燃料的物性参数表12实施例3的碳一气态燃料的物性参数表13实施例3的氧化剂的反应分配参数名称温度(℃)压力(mpa(g))流量(nm3/h)第一氧化剂通道40.009.902550第二氧化剂通道40.009.9014380煤浆氧化剂40.009.9012450表14实施例3的碳一固态燃料磨制成的水基浆料的入炉参数浓度(wt%)流量(kg/h)入喷嘴温度(℃)入喷嘴压力(mpa)6525000.0030.009.20表15实施例3制取的粗合成气的干气组成组分体积含量(%)h252.31co40.76co26.25h2s0.004ch40.020n20.612ar0.044总计100.00从表15可知,本实施例制取的粗合成气的干气组成以co和h2为主,且co和h2的干气体积总含量为93.07%。实施例4本实施例与实施例1的不同之处在于:步骤一中采用天然气为原料进行烘炉,步骤二中采用的碳一固态燃料为兴华煤,碳一气态燃料为ch4含量93.63%的天然气,碳一固态燃料、碳一气态燃料的物性参数分别如下表16和表17所示,氧化剂为体积纯度99.6%的氧气,氧化剂的反应分配参数如下表18所示,碳一固态燃料磨制成的水基浆料的入炉参数如下表19所示;步骤二中反应腔3细颈部的直径d为1298.80mm,反应腔3腹部最粗处的直径d为3400.00mm,所述多元共轭反应的温度为1350℃;步骤三中ф=δ=10.00mm,μ=50.00mm,α为10°,步骤三中制取的粗合成气的干气体积组成如下表20所示,所述排出气化炉的换热后的未反应固体余物渣团的干质中的碳元素含量为2.28wt%;所述排出气化炉的换热后的淬冷水中携带的未反应固体余物渣团中的碳元素含量为8.70wt%。表16实施例4的碳一固态燃料的物性参数表17实施例4的碳一气态燃料的物性参数表18实施例4的氧化剂的反应分配参数名称温度(℃)压力(mpa(g))流量(nm3/h)第一氧化剂通道40.007.502550第二氧化剂通道40.007.5014380煤浆氧化剂40.007.5012450表19实施例2的碳一固态燃料磨制成的水基浆料的入炉参数浓度(wt%)流量(kg/h)入喷嘴温度(℃)入喷嘴压力(mpa)6530000.0030.006.65表20实施例4制取的粗合成气的干气组成组分体积含量(%)h248.31co44.90co26.36h2s0.002ch40.020n20.376ar0.032总计100.00从表20可知,本实施例制取的粗合成气的干气组成以co和h2为主,且co和h2的干气体积总含量为93.21%。实施例5本实施例与实施例1的不同之处在于:步骤一中采用气态甲醇为原料进行烘炉,步骤二中采用的碳一固态燃料为核桃壳和陕北煤混合物,碳一气态燃料为ch4含量95.76%的油田气,碳一固态燃料中陕北煤、核桃壳和碳一气态燃料的物性参数分别如下表21、表22和表23所示,氧化剂为体积纯度99.6%的氧气,氧化剂的反应分配参数如下表24所示,碳一固态燃料磨制成的水基浆料的入炉参数如下表25所示;步骤二中反应腔3细颈部的直径d为1298.80mm,反应腔3腹部最粗处的直径d为3400.00mm;步骤三中ф=δ=10.00mm,μ=50.00mm,α为45°,步骤三中制取的粗合成气的干气组成如下表26所示,所述排出气化炉的换热后的未反应固体余物渣团的干质中的碳元素含量为2.09wt%;所述排出气化炉的换热后的淬冷水中携带的未反应固体余物渣团中的碳元素含量为8.90wt%。表21实施例5的碳一固态燃料中的陕北煤的物性参数表22实施例5的碳一固态燃料中的核桃壳的物性参数表23实施例5的碳一气态燃料的物性参数表24实施例5的氧化剂的反应分配参数名称温度(℃)压力(mpa(g))流量(nm3/h)第一氧化剂通道40.007.502550第二氧化剂通道40.007.5014380煤浆氧化剂40.007.5012750表25实施例5的碳一固态燃料磨制成的水基浆料的入炉参数注:表25中的流量分别为单个浆料喷嘴的进料量。表26实施例5制取的粗合成气的干气组成从表26可知,本实施例制取的粗合成气的干气组成以co和h2为主,且co和h2的干气体积总含量为93.21%。实施例6本实施例与实施例1的不同之处在于:步骤一中采用气态甲醇为原料进行烘炉,步骤二中采用的碳一固态燃料为兴华煤和杏壳混合物,碳一气态燃料为ch4含量95.206%的油田气,碳一固态燃料中的兴华煤、杏壳、碳一气态燃料的物性参数分别如下表27、表28和表29所示,氧化剂为体积纯度99.6%的氧气,氧化剂的反应分配参数如下表30所示,碳一固态燃料磨制成的水基浆料的入炉参数如下表31所示;步骤二中反应腔3细颈部的直径d为1375.20mm,反应腔3腹部最粗处的直径d为3600.00mm;步骤三中ф=δ=12.00mm,μ=60.00mm,α为30°,所述排出气化炉的换热后的未反应固体余物渣团的干质中的碳元素含量为2.30wt%;所述排出气化炉的换热后的淬冷水中携带的未反应固体余物渣团中的碳元素含量为8.76wt%。表27实施例6的碳一固态燃料中的兴华煤的物性参数表28实施例6的碳一固态燃料中的杏壳的物性参数表29实施例6的碳一气态燃料的物性参数表30实施例6的氧化剂的反应分配参数名称温度(℃)压力(mpa(g))流量(nm3/h)第一氧化剂通道40.007.502350第二氧化剂通道40.007.5014280煤浆氧化剂40.007.5012050表31实施例6的碳一固态燃料磨制成的水基浆料的入炉参数注:表31中的流量分别为单个浆料喷嘴的进料量。表32实施例6制取的粗合成气的干气组成组分体积含量(%)h249.25co44.58co25.66h2s0.003ch40.031n20.443ar0.03总计100.00从表32可知,本实施例制取的粗合成气的干气组成以co和h2为主,且co和h2的干气体积总含量为93.83%。以上所述,仅是本发明的较佳实施例,并非对本发明作任何限制。凡是根据发明技术实质对以上实施例所作的任何简单修改、变更以及等效变化,均仍属于本发明技术方案的保护范围内。当前第1页12