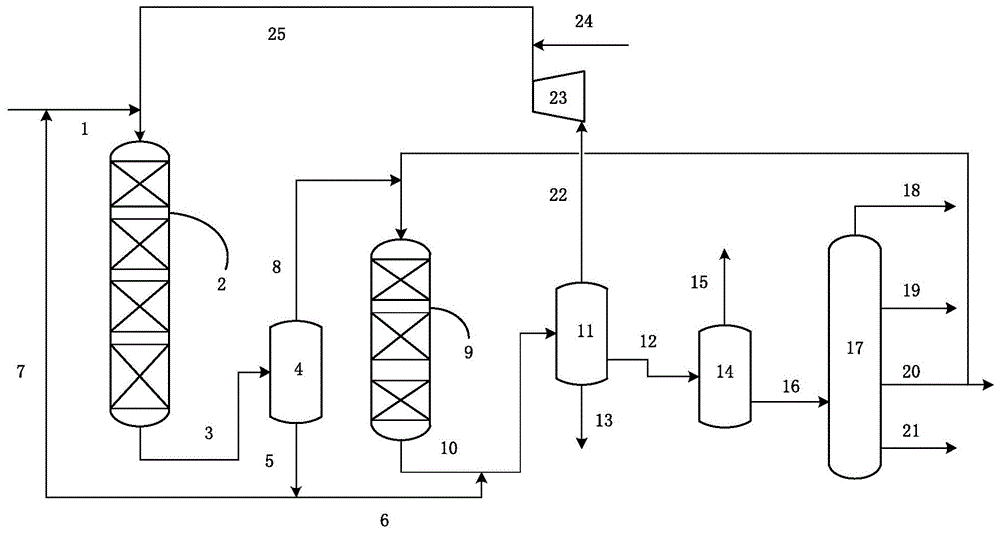
本发明涉及一种在存在氢的情况下为获得低沸点馏分的烃油裂解方法,更具体地说,是一种由混合原料生产化工料的加氢方法和系统。
背景技术:
:随着原油重质化、劣质化进程的加剧,催化裂化柴油的质量日益变差、产量逐年增加,这部分催化裂化柴油约占我国商品柴油份额的三分之一。目前,炼厂为了从原油中提取更多的轻质油品,不断提高催化裂化装置的加工能力和加工深度,导致催化裂化柴油的质量进一步变差,主要表现在芳烃含量高、硫和氮等杂质含量高,十六烷值低。与此同时,随着环保立法的日趋严格,国vi车用柴油标准要求十六烷值不小于51,硫含量不大于10μg/g,多环芳烃质量含量不大于7%。近些年柴油消费量进入峰值平台区,柴汽比逐年降低已成为大趋势,压减柴油,尤其是劣质柴油的需求更为迫切。全世界丙烯的需求量预计在未来的20年内将持续增长,中国丙烯需求增长超过世界平均值。丙烯是仅次于乙烯的重要石油化工原料。蒸汽裂解和催化裂解是我国丙烯的主要工艺过程,原料性质是影响丙烯产率的主要影响因素,随原料重质劣质化趋势的加剧,改善裂解原料性质是提高丙烯收率的关键。催化柴油加工手段主要包括加氢精制和加氢裂化两类。采用常规的加氢精制工艺处理催化柴油,虽然可以有效地脱除柴油中的硫、氮等杂质,但柴油产品十六烷值提高幅度有限。按照油品质量升级的趋势,车用柴油标准主要由降低硫转移到对油品结构组成的控制,尤其是多环芳烃。因此,芳烃含量在80%以上,多环芳烃占比在60%以上的催化柴油越来越难以通过常规手段加入到柴油池当中。加氢裂化手段可以将催化柴油馏分转化为轻质的重石脑油或汽油馏分,但目前催化柴油转化为汽油馏分的工业装置普遍存在技术水平高、运行周期短、装置运行苛刻等问题。cn103805245b公开了一种加氢裂化和加氢脱芳组合的加氢方法。该发明将劣质催柴与氢气以气液逆流方式进行加氢精制;精制生成油在贵金属催化剂存在下进行加氢脱芳反应;蜡油与氢气进行加氢裂化预处理反应,加氢裂化预处理流出物与加氢脱芳流出物混合后,进行加氢裂化反应;加氢裂化流出物经分离和分馏,得到不同馏分产品;其中裂化尾油循环至加氢脱芳反应器。该方法采用贵金属催化剂充分饱和催化柴油中的芳烃,提高中间馏分油的收率和产品质量。cn102994147b公开了一种重质油中压加氢裂化生产中间馏分油的方法。该方法以减压蜡油或减压蜡油添加部分催化柴油为原料加氢生产柴油,采用固定床两段加氢裂化工艺,在一段反应器中装填特有的加氢精制催化剂、二段反应器中装填特有的加氢裂化催化剂。cn1955257b公开了一种生产化工原料的加氢裂化方法,将劣质催化裂化柴油与重质加氢裂化原料按比例混合,然后进行加氢处理和加氢裂化,得到重石脑油和尾油等化工各原料。技术实现要素:本发明的目的是在现有技术的基础上提供一种由混合原料生产化工料的加氢方法和系统。具体地说,是要解决现有技术加工富含芳烃柴油馏分大比例掺入的混合原料时,产品中重石脑油馏分收率和芳烃潜含量偏低,以及尾油质量下降的问题。本发明提供一种生产化工料的加氢方法,包括:富含芳烃柴油馏分和蜡油馏分的混合原料进入第一加氢反应区,依次与加氢精制催化剂和加氢裂化催化剂i接触进行反应,第一加氢反应区的反应流出物进入第一高压分离器进行分离,分离所得第一气相物流进入第二加氢反应区,与加氢裂化催化剂ii接触进行反应,第一高压分离器分离所得第一液相物流分与第二加氢反应区的反应流出物一起依次进入第二高压分离器、分馏区,经分离后得到轻石脑油馏分、重石脑油馏分、柴油馏分和尾油馏分,柴油馏分循环回第二加氢反应区。在本发明中,所述的混合原料由富含芳烃柴油馏分和蜡油馏分组成,以混合原料整体为基准,富含芳烃柴油馏分的质量分数为30%~80%。在优选的情况下,富含芳烃柴油馏分的密度为0.90g/cm3~0.99g/cm3,馏程范围为165~400℃,芳烃含量至少为60重量%;进一步优选富含芳烃柴油馏分为催化裂化柴油。在优选的情况下,蜡油馏分选自减压蜡油、焦化蜡油、脱沥青油中一种或几种,蜡油馏分的密度为0.88g/cm3~0.97g/cm3,馏程范围为300~600℃。本发明中,混合原料与氢气混合后进入第一加氢反应区,与加氢精制催化剂接触后进行加氢脱硫、加氢脱氮、烯烃饱和、部分芳烃饱和等反应。经过加氢精制后的混合原料直接接触加氢裂化催化剂i,在优选的情况下,所述加氢裂化催化剂i为含有无定形硅铝的加氢裂化催化剂,主要发生选择性开环反应,在最大限度减少断链反应,保留精制蜡油馏分的同时,改善其烃类结构,因此,第一加氢反应区的液相物流具有链烷烃、一环烷烃、二环烷烃含量高以及氢含量高的特点。此外,混合原料中的富含芳烃柴油馏分中芳烃含量较高,芳烃含量通常在60%以上,而双环以上芳烃含量在40%以上。富含芳烃柴油馏分原料中300℃以上馏分以双环和三环芳烃为主,这些多环芳烃进行加氢饱和后,根据加氢饱和深度的不同,其沸点降低范围为20~50℃。在优选的情况下,为保证下游含分子筛的加氢裂化催化剂ii的活性及稳定性,以第一加氢反应区的液体流出物为基准,其中有机氮含量小于20μg/g。本发明中,第一加氢反应区的反应流出物进入第一高压分离器,在第一高压分离器内闪蒸,较轻的烃油、富氢气体等气体以气态形式作为第一气相物流从第一高压分离器的气相出口排出,较重的烃油以液态形式作为第一液相物流从第一高压分离器的液相出口排出。在优选的情况下,第一高压分离器的温度为300~370℃,进一步优选为320~350℃。在第一高压分离器的操作温度下,加氢后的富含芳烃柴油馏分几乎均以气相形式从第一高压分离器的气相出口排出,加氢后的蜡油馏分几乎均以液相形式从第一高压分离器的液相出口排出。在优选的情况下,第一加氢反应区的反应条件为:氢分压6.0~20.0mpa,反应温度300~450℃,氢油体积比400~2000nm3/m3,以混合原料作为新鲜原料,以新鲜原料计,液时体积空速为0.2~3.0h-1。在本发明中,分离所得第一气相物流进入第二加氢反应区,与加氢裂化催化剂ii接触进行加氢裂化反应。第一气相物流主要为加氢后的石脑油馏分和柴油馏分,其干点在300℃~370℃以内,因此第二加氢反应区优选在适宜柴油馏分转化为重石脑油馏分的工艺条件内操作。此外,由于第一加氢反应区反应流出物中的气体组分也直接进入了第二加氢反应区,因此第二加氢反应区的反应气氛中含有第一加氢反应区中经加氢脱硫和加氢脱氮反应脱除后,生成的全部硫化氢和氨。第二加氢反应区内较高的氨浓度具有抑制过度二次裂化的作用,将进一步有益于柴油馏分高选择性地转化为重石脑油馏分,减少干气、液化气及轻石脑油馏分的收率,并能够最大限度的保留重石脑油馏分中的环状结构,得到高芳烃潜含量的重石脑油馏分,该重石脑油馏分是优质的催化重整原料。在优选的情况下,第二加氢反应区的反应条件为:氢分压6.0~20.0mpa,反应温度300~420℃,氢油体积比300~1200nm3/m3,液时体积空速为0.5~8.0h-1。在本发明其中一种优选的实施方式中,第一高压分离器分离所得第一液相物流分为两路,一路循环回第一加氢反应区,以质量计,循环第一液相物流为混合原料的1%~80%。另一路与第二加氢反应区的反应流出物进行混合进入第二高压分离器。在第二高压分离器内进行气液分离,得到第二气相物流和第二液相物流。优选,第二高压分离器的温度为150~300℃,进一步优选为220~260℃。所得第二液相物流进入分馏区,经分离后得到轻石脑油馏分、重石脑油馏分、柴油馏分和尾油馏分,柴油馏分循环回第二加氢反应区。在优选的情况下,本发明监控尾油馏分的产品质量情况,并通过第一液相物流循环回第一加氢反应区来改善尾油馏分的产品质量。在其中一种优选的实施方式中,当尾油馏分的氢含量小于等于13.5重%时,至少部分第一液相物流循环回第一加氢反应区,以质量计,循环的第一液相物流为混合原料的1%~50%。在优选的情况下,第二高压分离器分离所得第二气相物流经脱除硫化氢和氨后,作为循环氢循环回第一加氢反应区。在本发明中,第一加氢反应区上游装填加氢精制催化剂,下游装填加氢裂化催化剂i,第二加氢反应区装填加氢裂化催化剂ii;在优选的情况下,加氢裂化催化剂i与加氢裂化催化剂ii的体积比为2:1~1:5;加氢精制催化剂的体积与加氢裂化催化剂i和加氢裂化催化剂ii的体积和之比为5:1~1:10。在优选的情况下,加氢精制催化剂是负载在载体上的至少一种第viii族金属组分和至少一种第vib族金属组分的催化剂。进一步优选,所述加氢精制催化剂,以氧化物计并以加氢精制催化剂为基准,所述第viii族金属组分的含量为1~10重量%,所述第vib族金属组分的含量为10~45重量%;所述第viii族金属组分为钴和/或镍,第vib族金属组分为钼和/或钨。在优选的情况下,加氢裂化催化剂i包括载体和负载在该载体上的加氢金属活性组分,所述载体由氧化铝和无定形氧化硅-氧化铝组成;所述加氢金属活性组分选自至少一种第viii族金属组分和至少一种第vib族金属组分。进一步优选,以加氢裂化催化剂i整体为基准,以氧化物计,加氢裂化催化剂i组成为:氧化铝20重量%~70重量%,无定形氧化铝-氧化硅20重量%~70重量%,第vib族金属组分10重量%~35重量%,第viii族金属1重量%~15重量%;所述第viii族金属组分为钴和/或镍,第vib族金属组分为钼和/或钨。在优选的情况下,加氢裂化催化剂ii包括载体和负载在该载体上的加氢金属活性组分,所述载体由氧化铝和分子筛组成;所述分子筛为y型分子筛或β型分子筛中的一种或几种;所述加氢金属活性组分选自至少一种第viii族金属组分和至少一种第vib族金属组分。进一步优选分子筛为y型分子筛。进一步优选,以加氢裂化催化剂ii整体为基准,以氧化物计,加氢裂化催化剂ii组成为:氧化铝30重量%~72重量%,分子筛1重量%~30重量%,第vib族金属组分15重量%~35重量%,第viii族金属组分2重量%~8重量%,所述第viii族金属组分为钴和/或镍,第vib族金属组分为钼和/或钨。本发明还提供用于上述加氢方法的生产化工料的加氢系统,包括第一加氢反应区、第二加氢反应区、第一高压分离器、第二高压分离器和分馏区;蜡油馏分进料管线、富含芳烃柴油馏分的进料管线与氢气进料管线连通,并与第一加氢反应区的入口连通,第一加氢反应区内上游装填加氢精制催化剂,下游装填加氢裂化催化剂i,第一加氢反应区的出口管线与第一高压分离器入口连通;第一高压分离器设置液相出口和气相出口,其液相出口与第一液相物流出料管线连通,其气相出口与第一气相物流出料管线连通;第一气相物流出料管线与第二加氢反应区的入口连通,第二加氢反应区装填加氢裂化催化剂ii,第二加氢反应区的出口管线与第二高压分离器的入口连通;第一液相物流出料管线与第二高压分离器的入口连通;第二高压分离器的液相出口经管线与分馏区入口连通,分馏区设置轻石脑油馏分出口、重石脑油馏分出口、柴油馏分出口、尾油馏分出口,并与相应的出料管线连通,其中,柴油馏分出料管线与第二加氢反应区入口连通。在其中一种优选的实施方式中,第一液相物流出料管线分为两路,一路管线与第一加氢反应区入口连通,另一路管线与第二高压分离器的入口连通。在其中一种优选的实施方式中,第二高压分离器设置气相出口和液相出口,气相出口经管线与循环氢净化系统连通,循环氢净化系统的循环氢出口与循环氢压缩机入口连通,循环氢压缩机出口与第一加氢反应区的入口连通。本发明的特点:本发明优选的加氢裂化催化剂i为无定形硅铝的加氢裂化催化剂,具有耐氮、裂化活性低和改善重馏分烃组成的特点。在第一加氢反应区内级配装填加氢精制催化剂和加氢裂化催化剂i,可在较为缓和条件下实现混合原料脱硫、脱氮并改善加氢蜡油馏分质量的目的,不仅所得的加氢蜡油馏分收率高,并且加氢蜡油馏分具有氢含量高的特点,适宜作为生产低碳烯烃原料,是优质的化工料。本发明采用高压分离器的方式进行分离,将馏程和烃类构成相差较大的加氢柴油馏分和加氢蜡油馏分进行有效分离。馏程较轻,富含环状结构的加氢柴油馏分在第二加氢反应区内,与含分子筛的加氢裂化催化剂ii接触进行反应,在富氨环境下高选择性地转化为高芳烃潜含量重石脑油馏分。进一步优选的加氢裂化催化剂ii中含有y型分子筛,可最大限度的保留进料中的环状结构,使得产品中重石脑油馏分芳烃潜含量高,为优质的催化重整的原料。本发明提供的方法和系统,可以大比例地处理催化裂化柴油,利用其富含芳烃的特点生产优质的催化重整原料,进行催化重整得到芳烃产品同时副产的氢气,一方面为炼厂提供廉价的氢气降低生产成本,另一方面为炼厂走芳烃路线提供基础。此外,本发明所得的尾油馏分氢含量高,是优质的制备低碳烯烃的原料。本发明的产品中不含有中间馏分油,可最大量的生产化工料,可促进以燃料油为主的炼厂向油化结合型发展,改善企业经济效益。附图说明图1是本发明提供的生产化工料的加氢方法流程示意图。具体实施方式下面结合附图对本发明所提供的方法进行进一步的说明,但并不因此而限制本发明。图中省略了许多设备,如泵、换热器、压缩机等,但这对本领域普通技术人员是公知的。如图1所示,来自管线1的富含芳烃柴油馏分和蜡油馏分的混合原料与来自管线25的富氢气体混合进入第一加氢反应区2,依次与加氢精制催化剂和加氢裂化催化剂i接触,进行加氢脱硫、加氢脱氮、芳烃加氢饱和反应以及缓和的加氢裂化反应。第一加氢反应区2的反应流出物经管线3进入第一高压分离器4进行闪蒸分离,分离得到第一气相物流和第一液相物流。第一液相物流经管线5抽出后分为两路,一路经管线7循环回第一加氢处理反应区2,另一路经管线6进入第二高压分离器11。第一气相物流经管线8进入到第二加氢反应区9与加氢裂化催化剂ii接触进行反应,加氢柴油馏分加氢裂化为石脑油等轻质产品,第二加氢反应区9的反应流出物经管线10进入第二高压分离器11进行气液分离。第二高压分离器11分离得到的酸性水由管线13抽出。第二高压分离器11分离得到的第二气相物流为富氢气体经管线22进入循环氢压缩机23,加压后与来自管线24的新氢混合,经管线25送至第一加氢反应区2入口。第二高压分离器11得到的第二液相物流经管线12进入到低压分离器14进一步进行气液分离,分离所得低分气体经管线15出装置,所得的液体产物经管线16进入分馏塔17进行组分分离。分离得到轻石脑油馏分经管线18抽出;分离所得的重石脑油馏分经管线19抽出;分离得到柴油馏分经管线20抽出并返回至第二加氢反应区入口进行回炼;分离所得的尾油馏分经管线21抽出。下面的实施例将对本发明予以进一步的说明,但并不因此而限制本发明。实施例和对比例中加氢精制催化剂a的商品牌号为rn-410,加氢精制催化剂b的商品牌号为rs-2000。加氢裂化催化剂c的商品牌号为rhc-140,是含有无定形硅铝的加氢裂化催化剂。加氢裂化催化剂d的商品牌号为rhc-5,是含有分子筛的加氢裂化催化剂。以上催化剂由中国石油化工股份有限公司催化剂长岭分公司生产。实施例中所用的原料油e和原料油f来自采用催化裂化装置,原料油g为减压蜡油,其性质列于表1。从表1可以看出,催化柴油原料e和f的总芳烃含量高达78质量%以上,双环以上芳烃的含量在56质量%以上,十六烷值不高于20,两种原料均为高芳烃含量的劣质的富含芳烃的柴油馏分;减压蜡油g密度为0.9347g/cm3,氮质量分数为1800μg/g,是较为劣质的减压蜡油馏分。实施例1原料油e与原料油g的混合原料与氢气一起进入第一加氢反应区,依次与加氢精制催化剂a和加氢裂化催化剂c接触反应,其反应流出物进入到第一高压分离器进行气液分离,第一液相物流部分循环回第一加氢反应区,以混合原料作为新鲜原料,循环的第一液相物流为新鲜原料的10重量%,剩余部分的第一液相物流进入第二高压分离器。分离所得第一气相物流进入装有加氢裂化催化剂d的第二加氢反应区,其反应流出物进入第二高压分离器进行气液分离,分离所得第二液相物流进入分馏塔,经分馏得到轻石脑油馏分、重石脑油馏分、柴油馏分和尾油馏分,柴油馏分返回到第二加氢反应区进行循环转化,循环的柴油馏分是第二加氢反应区的新鲜原料的7重量%。反应条件如表2所示,产品收率和性质如表3所示。对比例1在常规的单段串联一次通过流程下,原料油e与原料油g的混合原料与氢气混合进入反应区,依次经过加氢精制反应器和加氢裂化反应器,加氢精制反应器内装填加氢精制催化剂a,加氢裂化反应器内装填加氢裂化催化剂d。加氢裂化反应器的反应流出物经过气液分离和液相分馏,得到轻石脑油馏分、重石脑油馏分、柴油馏分和尾油馏分。所得柴油馏分和部分尾油馏分作为循环油循环回加氢裂化反应器,循环油是新鲜混合原料的17重量%。反应条件如表2所示,产品收率和性质如表3所示。实施例2原料油f与原料油g的混合原料与氢气一起进入第一加氢反应区,依次与加氢精制催化剂b和加氢裂化催化剂c接触反应,其反应流出物进入到第一高压分离器进行气液分离,分离所得的全部第一液相物流进入第二高压分离器。分离所得第一气相物流进入装有加氢裂化催化剂d的第二加氢反应区,其反应流出物进入第二高压分离器进行气液分离,分离所得第二液相物流进入分馏塔,经分馏得到轻石脑油馏分、重石脑油馏分、柴油馏分和尾油馏分,柴油馏分返回到第二加氢反应区进行循环转化,循环的柴油馏分是第二加氢反应区的新鲜原料的13重量%。反应条件如表2所示,产品收率和性质如表3所示。由实施例和对比例可以看出,采用本发明提供的方法加工催化柴油和蜡油混合原料,可以低氢耗、高收率的得到重石脑油馏分和尾油馏分,重石脑油馏分具有较高的芳烃潜含量,尾油馏分具有收率高、氢含量高的特点,并且不产柴油。而对比例的化学氢耗高、重石脑油收率低,芳烃潜含量也较低。表1原料油efg密度(20℃),g/cm30.94320.95760.9347硫,%0.150.260.35氮,μg/g70013001800氢,%9.99.712.16十六烷值19.317.4/烃组成,质量%链烷烃9.813.67.8环烷烃6.28.356.3总芳烃84.078.135.9双环以上芳烃含量60.556.521.4馏程(astmd-86),℃astmd-1160初馏点19520731410%22623538830%25526643150%27029045370%29832246690%331349500终馏点343366514表2表3当前第1页12