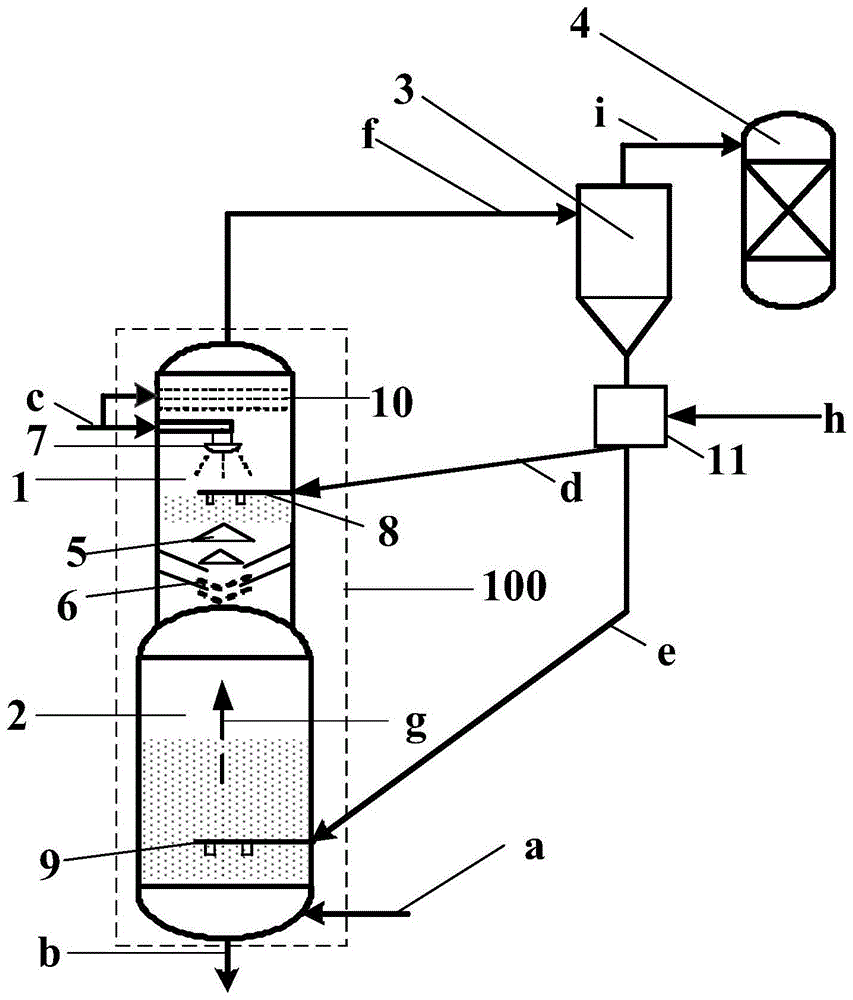
本发明涉及一种重油轻质化与合成气联产的方法和装置,尤其涉及一种将重油原料的轻质化与气化互相耦合处理的方法和装置,属于石油加工
技术领域:
。
背景技术:
:随着原油重质化与劣质化,劣质重油(稠油、超稠油、油砂沥青、减压渣油、油浆、脱油沥青等)产量剧增。劣质重油通常具有h/c比低,硫、氮及重金属含量高,残炭值大等特点,内部富集的残炭与沥青质组分导致重油在加工过程中生焦倾向严重。由于催化剂失活、氢耗高与长周期操作等问题,直接采用催化裂化或催化加氢等手段难以满足大量劣质重油的直接加工处理需求。采用溶剂脱沥青、减粘裂化、催化裂化、加氢处理与延迟焦化等技术组合的方式加工劣质重油,与一步法重油加工技术相比,总体工艺流程较长,投资成本也较高。其中,延迟焦化工艺作为当前广泛应用的劣质重油加工技术,存在炉管结焦、除焦过程环保压力大、液收低等问题。此外,延迟焦化工艺副产大量的固体焦,特别是高硫焦的价值较低,最新出台的环保要求对硫含量>3%的高硫焦采取限制出厂措施。国内部分炼厂将延迟焦化产生的石油焦用于循环流化床燃烧发电或气化多联产工艺,实现焦炭的转化利用。重油先转化为低活性的石油焦,然后通过冷却、研磨并再次加热转化,但总体工艺流程复杂,效率较低。此外,由于劣质重油原料具有较低的h/c原子比,因此必须通过加氢过程才能最大化生产轻质油品,并满足清洁油品的质量要求,故而,炼厂在加工劣质重油过程中氢源缺乏问题更加突出,催化重整等工艺过程产生的氢气不足以满足油品清洁化生产的氢气需求。劣质重油的直接气化虽然可将重油直接转化为合成气等小分子,但没有充分利用重油中赋存的油气分子与氢元素,也在一定程度上造成重油的资源浪费。针对上述一系列问题,许多研究者提出相应的短流程技术方案用于劣质重油加工转化。exxon公司开发的以流化焦粉作为重油裂解反应床料的灵活焦化系列工艺就是其中一种。灵活焦化工艺以焦粉作为重油裂解反应热载体,生成的焦炭附着在焦粉表面,要输送到气化/燃烧反应器中去除,因此反应中焦炭物料要在焦化、燃烧与气化等反应器之间的循环返料,不仅造成焦粉物料在多个反应器之间循环返料难度,更是难以实现焦炭气化与重油焦化反应发生直接物流或热量交换,增加了裂解反应的能耗。技术实现要素:本发明提供一种重油轻质化与合成气联产的方法,该方法通过对重油原料裂解反应中生成的焦炭的循环路径进行优化,不仅提高了焦炭的利用价值,降低了裂解反应的能耗,更是提高了轻质油的品质和收率,同时,降低了工艺操作难度。本发明还提供一种实现上述方法的装置。为实现上述目的,一方面,本发明提供一种重油轻质化与合成气联产的方法,采用内部具有相互导通的裂解段和气化段的裂解/气化耦合反应器作为反应器,所述方法包括以下步骤:使重油原料进入所述裂解/气化耦合反应器上部的所述裂解段与流化焦粉接触发生裂解反应,生成轻质油气和焦炭,焦炭被焦粉携带下行进入所述裂解/气化耦合反应器下部的所述气化段发生气化反应,生成合成气;所述合成气上行进入所述裂解段后,与所述轻质油气合并引出所述裂解/气化耦合反应器进入气固分离系统;所述轻质油气和合成气在所述气固分离系统至少经过第一级气固分离,收取焦粉颗粒并分成两部分,分别返回所述裂解段和气化段,形成所述焦粉颗粒的一级循环和二级循环;对所述气固分离系统输出的净化油气产物实施油气分馏,收取轻质油和合成气产品。进一步地,所述轻质油气和合成气在所述气固分离系统顺序进行第一级气固分离和第二级气固分离,依次分离出一级焦粉颗粒和二级焦粉颗粒,收取净化油气产物;将所述一级焦粉颗粒返回所述裂解段,形成焦粉颗粒一级循环,将所述二级焦粉颗粒则返回所述气化段,形成焦粉颗粒二级循环;其中,所述一级焦粉颗粒的粒径大于所述二级焦粉颗粒的粒径;或者,所述轻质油气和合成气在所述气固分离系统经过第一级气固分离,收取的焦粉颗粒经过焦粉返料分配机构,利用流化气体反吹方式,被分别送回所述裂解段和气化段,形成焦粉颗粒的一级循环和二级循环。进一步地,所述一级焦粉颗粒的粒径大于20μm,所述二级焦粉颗粒的粒径小于50μm。进一步地,所述流化气体的反吹气速为0.2-3.0m/s。进一步地,所述裂解反应的条件为:反应温度450-700℃,反应压力0.1-6.0mpa,反应时间1-20s,表观气速1-20m/s,剂油比4-20。进一步地,所述气化反应的条件为:反应温度850-1200℃,反应压力0.1-6.0mpa,表观气速为0.1-5.0m/s,焦粉颗粒的停留时间为1-20min。进一步地,所述焦炭被焦粉携带下行进入所述裂解/气化耦合反应器下部的气化段发生气化反应之前,还包括对所述焦粉依次进行水蒸气汽提处理和粒径细化处理。进一步地,所述水蒸气汽提处理的条件为:水蒸气与所述重油原料的质量比为0.1-0.3,所述水蒸气的温度为200-400℃,所述水蒸气的表观气速为0.5-5.0m/s。另一方面,本发明还提供一种用于实施上述任一所述方法的重油轻质化与合成气联产的装置,所述装置包括:裂解/气化耦合反应器,包括内部相互导通的裂解段和气化段,以及原料入口、油气出口、一级颗粒入口和二级颗粒入口,所述裂解段位于所述气化段的上部;所述一级颗粒入口以及原料入口位于所述裂解段,所述二级颗粒入口位于所述气化段,所述油气出口位于所述裂解/气化耦合反应器的顶部;气固分离系统,包括气固分离入口、气固分离油气出口和气固分离固相出口;分馏塔,包括分馏塔入口和多个轻质组分出口;所述气固分离系统位于所述裂解/气化耦合反应器外部,所述油气出口与所述气固分离入口连通,所述一级颗粒入口和二级颗粒入口分别与所述气固分离固相出口连通,所述气固分离油气出口与所述分馏塔入口连通。进一步地,所述气固分离系统包括第一气固分离装置和第二气固分离装置;所述第一气固分离装置的入口与所述油气出口连通,所述第一气固分离装置的固相出口与所述一级颗粒入口连通,所述第一气固分离装置的油气出口与所述第二气固分离装置的入口连通,所述第二气固分离装置的固相出口与所述二级颗粒入口连通,所述第二气固分离装置的油气出口与所述分馏塔入口连通。本发明的实施,至少具有以下优势:1、本发明充分发挥重油裂解与焦炭气化两个反应之间的协同作用。一方面,裂解段生成的焦粉颗粒作为气化段的反应原料,在气化段内反应生成高品质的合成气,避免石油焦生成,丰富炼厂氢气来源;另一方面,气化后的合成气上行至裂解段,一方面可以为裂解反应提供热量,同时可以作为重油裂解的反应气氛,特别是在加压条件下通过提供氢自由基等活性组分提升轻油收率与品质,因此本发明的方法通过以上过程实现两个反应之间的物料互供,能量互补,协同反应与油气联产等技术优势;2、本发明提出了重油裂解-焦炭气化一体化工艺及其耦合反应器装置,通过将上段重油裂解段与下段焦炭气化段耦合在同一反应系统内,避免了灵活焦化等工艺过程中多个反应器之间的循环操作困难、工艺复杂、占地面积大与投资高等问题,进一步提高能效,提升该方法的技术经济性。附图说明图1为本发明一实施例中提供的重油轻质化与合成气联产的装置示意图;图2为本发明另一实施例中提供的重油轻质化与合成气联产的装置示意图。具体实施方式为使本发明的目的、技术方案和优点更加清楚,下面将结合本发明的实施例,对本发明实施例中的技术方案进行清楚、完整地描述,显然,所描述的实施例是本发明一部分实施例,而不是全部的实施例。基于本发明中的实施例,本领域普通技术人员在没有做出创造性劳动前提下所获得的所有其他实施例,都属于本发明保护的范围。本发明提供一种重油轻质化与合成气联产的方法,采用内部具有相互导通的裂解段和气化段的裂解/气化耦合反应器作为反应器,所述方法包括以下步骤:使重油原料进入所述裂解/气化耦合反应器上部的所述裂解段与流化焦粉接触发生裂解反应,生成轻质油气和焦炭,焦炭被焦粉携带下行进入所述裂解/气化耦合反应器下部的所述气化段发生气化反应,生成合成气;所述合成气上行进入所述裂解段后,与所述轻质油气合并引出所述裂解/气化耦合反应器进入气固分离系统;所述轻质油气和合成气在所述气固分离系统至少经过第一级气固分离,收取焦粉颗粒并分成两部分,分别返回所述裂解段和气化段,形成所述焦粉颗粒的一级循环和二级循环;对所述气固分离系统输出的净化油气产物实施油气分馏,收取轻质油和合成气产品。本发明的裂解/气化耦合反应器是指能够同时发生裂解反应和气化反应的一体化耦合反应器,且裂解段位于气化段的上部。上述方法中,重油原料通过裂解/气化耦合反应器中的原料入口进入裂解段,与处于裂解段中的流化态焦粉进行接触发生裂解反应生成轻质油气和焦炭,其中,焦炭附着在焦粉颗粒表面而成为焦粉颗粒。为了能够增加重油原料与流化焦粉的接触面积,可以在原料入口处设置雾化装置对重油原料进行雾化处理后再与流化焦粉接触发生裂解反应。在裂解段中,会有部分焦粉颗粒(焦炭被焦粉携带)由于粒径过大而在重力的作用下下行进入气化段,与气化段中的气化剂发生气化反应从而生成含有氢气、一氧化碳等活性小分子的合成气。随着合成气的不断生成,合成气会上行进入裂解段,该合成气一方面会提供裂解反应所需的热量,使裂解-气化两个反应区的热量匹配利用,提高总体能效,另一方面合成气中的氢气能够在一定程度抑制致重油裂解反应的生焦反应,改善重油裂解的产物分布,从而提高油气的品质以及收率。除了上述的裂解段的焦粉颗粒会下行进入气化段外,裂解段中发生裂解反应生成的轻质油气和来自于气化段上行的合成气会发生合并。当向耦合反应器外引出轻质油气和合成气时,也会携带部分裂解段的焦粉颗粒,因此为了避免该部分焦粉颗粒的浪费,可以将轻质油气和合成气先引入至气固分离系统进行气固分离。经气固分离后,净化油气产物从气固分离系统中输出后进行进一步分馏,得到轻质油和合成气产品。而经气固分离得到的焦粉颗粒可以分为两部分进行应用,一部分焦粉颗粒返回裂解段继续作为裂解反应的载体,另一部分进入气化段与气化剂发生气化反应,其中,焦粉颗粒返回裂解段称为焦粉颗粒的一级循环,焦粉颗粒进入气化段称为焦粉颗粒的二级循环。本发明利用上裂解-下气化的耦合反应器进行重质油原料的裂解处理,为焦粉颗粒的往复循环利用提供了更加便捷的路径,使裂解段的焦粉颗粒在重力作用下直接下行至气化段中参与气化反应,简化了工艺流程,避免了焦粉颗粒由于复杂路径所导致的热量散失;同时,携带热量的合成气能够直接上行进入裂解段,不仅为裂解反应提供了反应热量,更为裂解反应提供了氢气气氛,抑制了裂解反应的生焦,从而有利于油气品质以及收率的提高。此外,本发明还通过对气固分离得到的焦粉颗粒进行一级循环和二级循环以提高焦粉颗粒的利用率,从而进一步改善轻质油和合成气的产率,提高重油轻质化和合成气联产的效率。本发明能够在一个反应器中形成裂解与气化两个反应之间的原料互供以及热量互补,实现反应协同耦合与油气联产等技术优势。整个耦合反应器可以在高压下操作,从而大幅提高加工能力,并且在高压下实现高品质合成气对重油裂解过程的提质作用。进一步地,所述焦炭被焦粉携带下行进入耦合反应器下部的气化段发生气化反应之前,还包括对所述焦粉依次进行水蒸气汽提处理和粒径细化处理。具体地,还可以在耦合反应器的裂解段和气化段之间设置水蒸气汽提段和粒径细化段,用于依次对从裂解段下行的焦粉颗粒进行水蒸气汽提和粒径细化。其中,水蒸气汽提能够对下行的焦粉颗粒的表面的油气进行清除,粒径细化能够对经水蒸气汽提后的焦粉颗粒进行粒径切割细化,避免焦粉颗粒之间发生粘结团聚而造成合成气的产率下降。在具体实施过程中,水蒸气汽提段可以包括多层汽提结构,从而通过经汽提水蒸气入口进入的汽提水蒸气的作用清除焦炭颗粒表面的轻质油气。详细地,多层汽提结构可以采用人字形挡板、环形挡板、锥形挡板、格栅性挡板、散装填料或规整填料等汽提结构中的一种或多种的组合。粒径细化段可以包括喷射研磨器,喷射研磨器用于利用从研磨水蒸气入口进入的水蒸气对经水蒸气汽提段处理后的焦炭颗粒进行破碎筛分,从而保证进入气化段的焦炭颗粒与气化剂能够有更大的接触面积,保证气化反应的高效进行。裂解段中大粒径的焦粉颗粒在下行过程中依次经水蒸气汽提处理和粒径细化处理后最终进入气化段,并且与二级循环的焦粉颗粒混合,与通入气化段的气化剂发生气化反应,从而生成合成气。并且,由于在裂解段和气化段之间还设置有水蒸气汽提段和粒径细化段,从而能够保证裂解段和气化段的具有相对独立的反应环境,更避免了裂解段和气化段之间的焦粉颗粒相互粘连团聚,保证了裂解-气化耦合反应的安全性和操作稳定性。本发明对进入气固分离系统的轻质油气和合成气可以包括但不限于以下两种气固分离方式。在一种实施方式中,轻质油气和合成气在气固分离系统顺序进行第一级气固分离和第二级气固分离,依次分离出一级焦粉颗粒和二级焦粉颗粒,收取净化的油气产物;将所述一级焦粉颗粒返回所述裂解段,形成所述一级循环,将所述二级焦粉颗粒则返回所述气化段,形成所述二级循环;其中,所述一级焦粉颗粒的粒径大于所述二级焦粉颗粒的粒径。具体地,气固分离系统可以包括串联设置的第一气固分离装置和第二气固分离装置,其中第一气固分离装置用于接收进入气固分离系统的待分离物流(轻质油气、合成气以及夹杂在其中的焦粉颗粒),并且第一气固分离装置对待分离物流进行第一级气固分离后,将其中的非固态物流输出至第二气固分离中进行第二级气固分离。本发明的轻质油气和合成气进入气固分离系统后,首先在第一气固分离装置中进行第一级气固分离,得到一级非固态物流(被分离出的轻质油气和合成气)和一级焦粉颗粒,该一级焦粉颗粒能够通过管道返回至裂解段从而形成一级循环;一级非固态物流会进入第二气固分离装置中进行第二级气固分离,得到二级非固态物流(净化油气产物,即将进行分馏获得轻质油和合成气产品)和二级焦粉颗粒,该二级焦粉颗粒能够通过管道返回至气化段从而形成二级循环。其中,可以通过对第一气固分离装置和第二气固分离装置的分离参数进行限定,使得第一焦粉颗粒的粒径大于第二焦粉颗粒的粒径。示例性的,一级焦粉颗粒的粒径大于20μm,进一步地,优选一级焦粉颗粒的粒径大于50μm;所述二级焦粉颗粒的粒径小于50μm,进一步地,优选二级焦粉颗粒的粒径小于20μm。本发明通过设置第一级气固分离和第二级气固分离,对进入气固分离系统中的焦粉颗粒进行了分级处理,尽可能保证参与气化反应的焦粉颗粒具有相对较小的粒径,从而能够提高焦粉颗粒在气化反应中的转化率以提高合成气的产气量及其品质,继而当合成气上行至裂解段后既能够保证大量热量被传递至裂解段,又能够使裂解反应在富氢环境下进行提高轻质油气的品质。上述第一气固分离装置可以是一个或多个旋风分离器互相串联或者并联,第二气固分离装置可以是一个或多个旋风分离器互相串联或者并联。在另一种实施方式中,所述轻质油气和合成气在气固分离系统经过第一级气固分离,收取的焦粉颗粒经过焦粉返料分配机构,利用流化气体反吹方式,被分别送回所述裂解段和气化段,形成所述一级循环和二级循环。而收取的非固态物流作为净化油气产物进入后续的分馏处理中,以获得轻质油和合成气产品。其中,可以利用是一个或多个旋风分离器互相串联或者并联的方式进行第一级气固分离,且收集的焦粉颗粒先在焦粉返料分配机构中聚集,然后通过流化气体反吹的方式分别进入裂解段和气化段以形成一级循环和二级循环。上述流化气体可以包括水蒸气和/或氮气等,还可以是本发明中气化部分生成的合成气。若采用本发明的合成气作为流化气体,可以对气固分离系统中输出的合成气进行收集,并且将其中部分合成气作为流化气体进行使用。伴随着一级循环和二级循环的进行,合成气最终还是会进入耦合反应器中被收集,既降低了重质油裂解的成本,又提高了合成气了使用效率,降低了能耗。此外,通过控制流化气体的反吹气速可以控制焦粉颗粒在一级循环和二级循环的比例,进而能够控制裂解段和气化段发生反应的效率。在本发明中,为了保证气化段中生成的合成气对裂解反应的积极影响,可以使流化气体的反吹气速为0.2-3.0m/s。本发明还对耦合反应器中的工艺参数进行了下述限定,从而进一步实现重油加工过程中物流与能流的匹配,确保整个重油加工过程中的稳定性,提高总体能效。在裂解段内,裂解反应的反应温度450-700℃,反应压力0.1-6.0mpa,反应时间1-20s,表观气速1-20m/s,剂油比4-20。一般情况下,将重油预热至150-350℃后再进入裂解段进行反应。其中,表观气速是指用于流化焦粉颗粒的流化气体与上行进入的合成气的集合的表观气速。在气化段内,气化反应的反应温度850-1200℃,反应压力0.1-6.0mpa,表观气速为0.1-5.0m/s,焦粉颗粒的停留时间为1-20min。其中,表观气速是指气化剂与用于流化焦粉颗粒的流化气体的集合的表观气速,焦粉颗粒的停留时间是指焦粉颗粒在气化段中停留的时间。以上反应条件能够保证气化反应的顺利进行,并且有助于对处于裂解段中的焦粉颗粒进行合理分配(少部分细粉颗粒进入气固分离系统,大部分焦粉颗粒留在裂解段继续充当裂解反应载体,少部分大粒径焦粉颗粒下行进入气化段参与气化反应),从而保证整个流程的稳定性。本发明的气化剂可以从耦合反应器外部通入气化段中,具体地,气化剂可以是氧气、水蒸气、富氧空气和空气中的一种或多种。进一步地,水蒸气汽提处理中,水蒸气与重油的质量比为0.1-0.3,所述水蒸气的温度为200-400℃,所述水蒸气的表观气速为0.5-5.0m/s。该处理条件既能够清除从裂解段下行进入气化段中的焦粉颗粒表面的油气,也能够和上行的合成气供同成为待分离物流进入气固分离系统中的动力。此外,还可以在耦合反应器的裂解段上部增设洗涤段,使耦合反应器的待分离物流经过洗涤处理后再进入气固分离系统。具体地,在待分离物流进入气固分离系统之前,可以使待分离物流先经过含有低温液体的洗涤段进行洗涤降温,一方面能够将待分离物流中的部分焦粉颗粒清除,使清除的焦粉颗粒落回至裂解段继续充当裂解载体,另一方面能够对待分离物流进行降温,避免待分离物流在气固分离系统中以高温状态继续生焦,从而进一步提高轻质油气的品质,也避免了生焦过多对气固分离系统造成堵塞。降温洗涤段可以采用内置填料式结构强化混合物流与低温液体的接触,也可以采用塔板类结构强化混合物流与低温液体的接触。内置填料式结构可以包括拉西环、鲍尔环、阶梯环、弧鞍填料、矩鞍填料、金属环矩鞍、球形填料等散装填料,或者格栅填料、波纹填料、脉冲填料等规整填料中的一种多种的组合。塔板类结构包括泡罩塔板、筛孔塔板、浮阀塔板、喷射塔板、穿流塔板中的一种或多种的组合。上述低温液体可以是重油原料。在实际操作过程中,使重油原料分两路进入裂解段中,一路重油原料直接与焦粉接触发生裂解反应,另一路重油原料作为低温液体先经过洗涤段进行换热,随后下行与焦粉发生裂解反应,从而有效降低裂解反应所需能耗。在本发明中,作为低温液体的重油原料为重油原料总质量的5-10%。进一步地,为了提高焦粉颗粒的利用率,可以使气固分离得到的焦粉颗粒分别经过分散装置后再各自进入裂解段和气化段中,从而使焦粉颗粒能够均匀分布在裂解段和气化段中,使更多的焦粉颗粒参与反应,从而提高裂解反应和气化反应的反应效率。本发明的重油原料的康氏残炭值≥8%,具体可以是稠油、超稠油、油砂沥青、常压重油、减压渣油、催化裂化油浆、溶剂脱油沥青中一种或多种任意比例的混合物,也可是煤热解或液化过程的重质焦油与渣油,油页岩干馏产生的重油,生物质中低温热解液体产物等衍生重油的一种或多种任意比例的混合物。本发明的焦粉可选用微球状结构,具有优异流化性能的焦粉颗粒。一般的,焦粉的粒径为10-500μm,进一步为20-200μm。下面结合具体实施例和附图对本发明进行详细阐述。实施例1图1为本发明一实施例提供的重油轻质化与合成气联产的装置示意图,本实施例中提供的重油轻质化与合成气联产的方法使用如图1所示的装置,该装置至少包括:裂解/气化耦合反应器100,该裂解/气化耦合反应器100包括内部相互导通的裂解段1和气化段2,以及原料入口、油气出口、一级颗粒入口和二级颗粒入口,所述裂解段1位于所述气化段2的上部;所述一级颗粒入口以及原料入口位于所述裂解段1,所述二级颗粒入口位于所述气化段2,所述油气出口位于所述裂解/气化耦合反应器100的顶部;具体地,上述裂解/气化耦合反应器具体可以是由本领域常用的裂解反应器和气化反应器经适当改造和组装得到,裂解反应器比如可以是流化床反应器,其底端与气化反应器的顶端相互贯通。裂解反应器与气化反应器最好同轴设置,以方便物料的输运和循环;其中,裂解段1中可以包括流化床,从而通过流化床的作用使焦粉和颗粒处于流化状态,并充当裂解反应的载体;气化段2中可以包括流化床,通过流化床的作用使焦粉颗粒处于流化状态并与气化剂a接触进行气化反应,气化段还设置有用于注入气化剂a的气化剂入口以及用于固体灰渣b等无法反应转化的杂质输出的排渣口。气固分离系统3,包括气固分离入口,气固分离油气出口和气固分离固相出口;分馏塔4,包括分馏塔入口和多个轻质组分出口;所述气固分离系统3位于所述裂解/气化耦合反应器100外部,所述油气出口与所述气固分离入口连通,所述一级颗粒入口和二级颗粒入口分别与所述气固分离固相出口连通,所述气固分离油气出口与所述分馏塔入口连通。在上述基础上,图1中的裂解/气化耦合反应器100的内部还包括:水蒸气汽提段5,水蒸气汽提段5可以包括水蒸气汽提挡板,从而通过喷射水蒸气清除下行过程中的焦粉颗粒表面的油气;粒径细化段6,粒径细化段6可以包括蒸气喷射研磨器,通过喷射蒸汽对汽提后的焦粉颗粒进行细化研磨;雾化装置7,雾化装置7设置于裂解段1,其与原料入口连通,用于对重油原料c进行雾化处理;第一分散装置8,第一分散装置8设置于裂解段1中,与一级颗粒入口连通,用于对一级循环的焦粉颗粒d进行分散处理;第二分散装置9,第二分散装置9设置于气化段2中,与二级颗粒入口连通,用于对二级循环的焦粉颗粒e进行分散处理;洗涤段10,该洗涤段10设置在裂解段1上部且与裂解段1连通,用于对即将进入气固分离系统3的待分离物流f进行洗涤降温;裂解段1包括两个原料入口,其中一个原料入口直接通向流化态焦粉,另一个原料入口通向洗涤段10。图1中的裂解/气化耦合反应器100的外部还包括:焦粉返料分配机构11,设置在气固分离系统3和裂解/气化耦合反应器100之间,气固分离固相出口通过焦粉返料分配机构11分别与一级颗粒入口和二级颗粒入口连通;焦粉返料分配机构11包括焦粉返料入口和焦粉返料出口,焦粉返料入口与气固分离固相出口连通,焦粉返料出口分别与一级颗粒入口和二级颗粒入口连通。使用本实施例提供的装置进行重油轻质化与合成气联产的方法简述如下:重油原料c通过第一原料入口和第二原料入口,分别输入至裂解/气化耦合反应器100中,通过第一原料入口输入裂解段1的重油原料c经过雾化装置7的雾化处理后,直接与流化态的焦粉(包括外部附着有焦炭的焦粉颗粒)接触发生裂解反应,通过第二原料入口输入的重油原料c先经过洗涤段10与即将进入气固分离系统3的待分离物流f发生换热后,再下行进入裂解段1与流化态的焦粉接触发生裂解反应。重油原料c经上述两路发生裂解反应分别得到轻质油气与焦炭,焦炭会附着在焦粉表面形成焦粉颗粒。一部分结焦严重粒径较大的焦粉颗粒会在重力作用下下行,在下行的过程中,首先经过水蒸气汽提段5去除焦粉颗粒表面残余的轻质油气,随后经过粒径细化段6对焦粉颗粒的粒径进行切割细化。最后,焦粉颗粒从粒径细化段6下行至气化段2。在气化段2中,上述被细化的焦粉颗粒与经气化剂入口进入气化段2的气化剂a发生气化反应,获得合成气g。并且,焦粉颗粒气化过程中不能反应的固体灰渣在累积之后可以通过排渣口排出裂解/气化耦合反应器100外,固体灰渣b中的重金属可以通过后续工艺回收利用。合成气g在气化剂a的驱动下会上行(上行过程中会携带部分未气化的小粒径的焦粉颗粒)进入裂解段1,为重油裂解反应提供反应热量以及反应气氛(上行的合成气的气量可以通过调控气化剂类型、气速等控制,从而保证裂解/气化耦合反应器100内部物流与能流的匹配),并且合成气g会和轻质油气合并经油气出口引出裂解/气化耦合反应器100,并经气固分离入口进入气固分离系统3。本实施例中的气固分离为第一级气固分离(即,只进行一次气固分离),分离出的焦粉颗粒经气固分离固相出口输出,经焦粉返料入口进入焦粉返料分配机构11,并且在流化气体h反吹的作用下从焦粉返料分配机构11的焦粉返料出口中分两路分别进入裂解段1和气化段2,其中,经一级颗粒入口进入裂解段1的焦粉颗粒即为一级循环的焦粉颗粒d,经二级颗粒入口进入气化段2的焦粉颗粒即为二级循环的焦粉颗粒e。能够理解的是,一级循环的焦粉颗粒d和裂解段1中的焦粉颗粒混合后,还会继续循环作用(一部分下行入气化段2作为气化剂原料,一部分留在裂解段1作为裂解反应载体,一部分与轻质油气和和合成气混合并进入气固分离系统3);二级循环的焦粉颗粒e会在气化段2中发生气化反应,部分未发生气化反应的焦粉颗粒会被合成气g携带上行进入裂解段1。经气固分离油相出口输出的净化油气产物i会经分馏塔入口进入分馏塔4进行分馏,从而通过分馏塔4的多个轻质组分出口会分别输出轻质油、裂解气(干气、液化气等)和合成气产品。当然,还可以通过设置多个分馏塔进行进一步切割分馏得到不同馏程组分的液体产物,其中,塔底重油(包括部分焦粉颗粒等)可以与重油原料c混合,重新循环进入裂解/气化耦合反应器100中加工。上述裂解反应的条件为:反应温度450-700℃,反应压力0.1-6.0mpa,反应时间1-20s,表观气速1-20m/s,剂油比4-20;上述气化反应的条件为:反应温度850-1200℃,反应压力0.1-6.0mpa,表观气速为0.1-5.0m/s,焦粉颗粒的停留时间为1-20min。上述水蒸气汽提处理的条件为:水蒸气与重油的质量比为0.1-0.3,水蒸气的温度为200-400℃,汽提水蒸气的表观气速为0.5-5.0m/s。焦粉返料分配机构中,流化气体的反吹气速为0.2-3.0m/s。为验证本发明的效果,采用图1所示的装置和工艺流程分别对两种重油(辽河常压重油和辽河减压重油)进行试验。表1所示为重油原料的性质。表2为具体反应参数,同常规重油裂解工艺相比较,采用该本实施例中的方法可以使轻质油收率提高,且液收率提高,干气和焦炭产率明显降低,详细的产品分布可见表3和表4。表1样品名称辽河常压重油辽河减压渣油密度(20℃)/g·cm-30.98171.0271运动粘度(100℃)/mm2·s-1314.83380康氏残炭/wt%13.3920.04c/wt%86.886.05h/wt%11.5810.09s/wt%0.390.48n/wt%0.811.55n(h)/n(c)1.591.41饱和分/wt%31.0816.36芳香分/wt%26.1336.91胶质/wt%40.0641.12沥青质/wt%2.735.61ni/ppm88175v/ppm2.163.6初馏点36041210%39945630%44649850%48254770%54261190%628672终馏点692775vgo比例(350-500℃)56.62%30.98%重油馏分比例(>500℃)43.38%69.02%表2表3样品名称/wt%辽河常压重油辽河减压渣油干气收率3.974.13液化气收率1.011.07汽油馏分2.142.01柴油馏分6.846.43减压馏分油40.7738.33重油馏分33.1831.19焦炭收率12.0916.84由表3可知:1、本实施例的方法和装置能够显著提高轻质油的收率,抑制焦炭产生;2、随着重油原料的劣质化,裂解得到的气体与焦炭收率逐渐提高,液体收率逐渐下降。与原料初始的残炭值相比,焦炭收率与残炭比值约为0.8-0.9,远小于延迟焦化中焦炭/残炭1.4-1.6的比值。随着重油原料性质的变化,液体质量收率保持在70-80%之间,其中含有部分大于500℃的重油馏分,后续可以通过回炼方式进行加工。表4合成气组分h2coco2ch4等其他组分体积含量(vol%)46.634.916.12.4由表4可知:本实施例的得到合成气中h2与co体积分数之和约为80%左右,作为高品质的合成气可用于后续重整制氢或者油品f-t合成等过程,能够显著降低重油原料的裂解生焦。实施例2图2为本发明另一实施例中提供的重油轻质化与合成气联产的装置示意图,本实施例中提供的重油轻质化与合成气联产的方法使用如图2所示的装置。与实施例1中的装置不同的是,本实施例的装置中,气固分离系统3包括第一气固分离装置31和第二气固分离装置32;所述第一气固分离装置31的固相出口与所述一级颗粒入口连通,所述第一气固分离装置的油气出口与所述第二气固分离装置32的入口连通,所述第二气固分离装置32的固相出口与所述二级颗粒入口连通,所述第二气固分离装置32的油气出口与所述分馏塔入口连通。第一气固分离装置31和第二气固分离装置32可为旋风分离器。使用本实施例提供的装置进行的重油轻质化与合成气联产的方法与实施例1中的方法不同之处在于,经洗涤段10处理后的待分离物流f先进入第一气固分离装置31中进行第一级气固分离,得到一级非固态物流j(被分离出的轻质油气和合成气)和一级焦粉颗粒,该一级焦粉颗粒能够通过管道返回至裂解段从而形成一级循环的焦粉颗粒d;一级非固态物流j会进入第二气固分离装置32中进行第二级气固分离,得到二级非固态物流(净化油气产物i,即将进行分馏获得轻质油和合成气产品)和二级焦粉颗粒,该二级焦粉颗粒能够通过管道返回至气化段2从而形成二级循环的焦粉颗粒e。为验证本发明的效果,采用图2所示的装置和工艺流程分别对实施例1中的两种重油(辽河常压重油和辽河减压重油)进行试验。具体反应参数与实施例1相同,同常规重油裂解工艺相比较,采用本实施例中的方法可以使液体质量收率保持在70-80%之间,且得到合成气中h2与co体积分数之和约为80%左右。最后应说明的是:以上各实施例仅用以说明本发明的技术方案,而非对其限制;尽管参照前述各实施例对本发明进行了详细的说明,本领域的普通技术人员应当理解:其依然可以对前述各实施例所记载的技术方案进行修改,或者对其中部分或者全部技术特征进行等同替换;而这些修改或者替换,并不使相应技术方案的本质脱离本发明各实施例技术方案的范围。当前第1页12