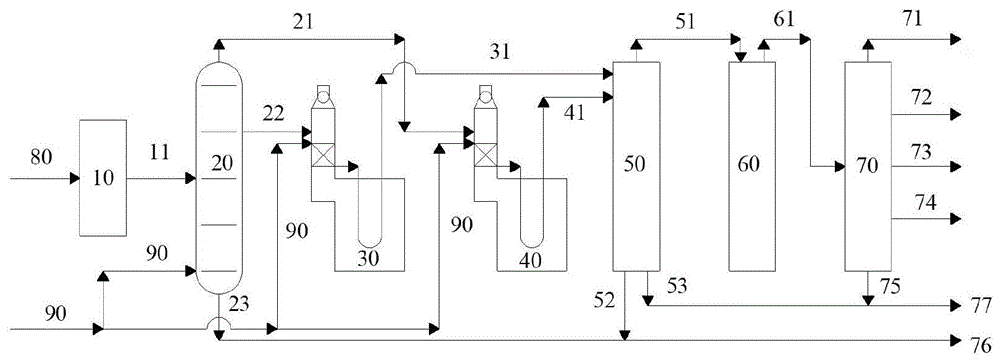
本发明涉及石油化工
技术领域:
,尤其涉及一种降低乙烯联合装置综合能耗的系统及其方法。
背景技术:
:蒸汽热裂解工艺是不需要任何催化剂进行化学反应,广泛应用于生产乙烯、丙烯、丁二烯等烯烃产品和苯、甲苯、二甲苯等芳烃产品“三烯、三苯”的石油化工工艺;并进一步生产合成树脂、合成橡胶、合成纤维三大产品,其中乙烯是石油化工行业标志性的基本有机化工原料,在国民经济中占有十分重要的地位。采用石油烃生产乙烯的裂解原料可以是乙烷、丙烷、丁烷等气相馏分,也可以是石脑油、常压柴油、加氢尾油等液相馏分。现有技术采用工艺流程复杂的油品炼制装置和油品精制装置才能得到这些裂解原料,如:常减压装置“三塔二炉”工艺流程,又如:加氢裂化装置“二炉二反一压一塔”工艺流程,再如:渣油加氢装置“一压一炉一反二塔”工艺流程,而蒸汽热裂解的裂解原料从乙烷到加氢尾油都可以适用,并不需要严格的分离与精制,实际上仅仅进行简单处理宽馏分油的原油,就可以作为裂解原料制备乙烯;因此现有技术存在工艺流程长、综合能耗高的问题。现有技术中的专利申请号200510093276.x一种重质原油直接延迟焦化方法,公开了将常减压蒸馏装置与延迟焦化装置组合为一套装置,使重质原油直接进入到延迟焦化装置的分馏塔,该分馏塔同时具有常减压蒸馏和延迟焦化功能,一塔二用,既分馏焦化反应后的馏分油,又分馏原油的轻组分;由此,油品经过混合、换热、加压、加热、精馏分离之后,馏出气体、汽油、柴油、蜡油馏分,简化了油品的加工流程,降低了生产成本。现有技术中的专利申请号200880021957.7使用常压蒸馏的烃热裂解方法,公开了首先将烃类裂解进料在常压热蒸馏步骤中进行处理来形成轻汽油和常压渣油的混合物,轻汽油/常压渣油组合物在气化步骤中至少部分被气化,再将气化步骤的气化产物进行蒸汽热裂解生产乙烯。现有技术中的专利申请号201610653709.0乙烯裂解炉,公开了该乙烯裂解炉包括辐射段、对流段、急冷锅炉、高压汽包、引风机等等,其中辐射炉管包括多组辐射炉管组,每组辐射炉管组中的出口管和入口管各自集中布置,而且该乙烯裂解炉在辐射段采用双段式供热,其中上部燃烧器布置在入口管二侧或在出口管二侧布置热负荷低的燃烧器,由此可大大降低发生二次反应并结焦的隐患以及进一步缓解辐射炉管外壁过热的问题,可以显著延长清焦的间隔时间并延长辐射炉管的使用寿命。现有技术中的专利申请号200510093276.x一种重质原油直接延迟焦化方法,虽然将重质原油直接进入到延迟焦化装置的分馏塔,使该分馏塔同时具有常减压蒸馏和延迟焦化功能,一塔二用,既分馏焦化反应后的馏分油,又分馏原油的轻组分,但是仅仅用于石油炼制装置,无法生产“三烯、三苯”。现有技术中的专利申请号200880021957.7使用常压蒸馏的烃热裂解方法,仅仅将轻汽油/常压渣油组合物在气化步骤中至少部分被气化,再将气化步骤的占总重量20wt%的气化产物进行蒸汽热裂解生产乙烯,原油利用率较低。现有技术中的专利申请号201610653709.0乙烯裂解炉,包括辐射段、对流段、急冷锅炉、高压汽包、引风机等,辐射段采用双段式供热,上部燃烧器布置在入口管二侧或在出口管二侧布置热负荷低的燃烧器,由此降低发生二次反应并结焦的隐患,进一步缓解辐射炉管外壁过热的现象,但是该乙烯裂解炉仅仅是一台蒸汽热裂解的反应器设备,无法进行裂解原料的优化。综上所述,现有技术存在工艺流程长、原料利用率低、综合能耗高的问题。因此,亟需一种简化工艺流程,对宽馏分原油进行简单处理即可进行热裂解制乙烯的系统。技术实现要素:本发明的目的是针对现有技术中的不足,提供一种降低乙烯联合装置综合能耗的系统及其方法。本发明的第一个目的是,提供一种降低乙烯联合装置综合能耗的系统。一种降低乙烯联合装置综合能耗的系统,用于对宽馏分原油进行热裂解制乙烯,包括:原油预处理工段;油品汽提工段,所述油品汽提工段与所述原油预处理工段通过管道连接;液体裂解工段,所述液体裂解工段与所述油品汽提工段通过管道连接;气体裂解工段,所述气体裂解工段与所述油品汽提工段通过管道连接;急冷工段,所述急冷工段分别与所述液体裂解工段和所述气体裂解工段通过管道连接;压缩工段,所述压缩工段与所述急冷工段通过管道连接;精馏分离工段,所述精馏分离工段与所述压缩工段通过管道连接。优选地,所述原油预处理工段包括:脱盐处理设备、脱水处理设备和预热处理设备;其中,所述脱盐处理设备、所述脱水处理设备和所述预热处理设备顺次通过管道连接。优选地,所述急冷工段包括:急冷油设备和急冷水设备;其中,所述急冷油设备和所述急冷水设备顺次通过管道连接。优选地,所述压缩工段包括:增压处理设备、碱洗处理设备、水洗处理设备、干燥处理设备;其中,所述增压处理设备、所述碱洗处理设备、所述水洗处理设备和所述干燥处理设备顺次通过管道连接。优选地,所述精馏分离工段包括:深冷设备、脱甲烷设备、脱乙烷设备、乙烯精馏设备、脱丙烷设备、丙烯精馏设备和脱丁烷设备;其中,所述深冷设备、所述脱甲烷设备、所述脱乙烷设备、所述乙烯精馏设备、所述脱丙烷设备、所述丙烯精馏设备和所述脱丁烷设备进行组合连接。本发明的另一个目的是,提供一种降低乙烯联合装置综合能耗的方法。一种降低乙烯联合装置综合能耗的方法,应用于如上所述的降低乙烯联合装置综合能耗的系统,包括以下步骤:步骤s1、宽馏分原油经原油预处理工段处理后,得到预处理原油;步骤s2、于过热水蒸汽的作用下,所述步骤s1得到的所述预处理原油经油品汽提工段处理后,分别得到气相馏分、轻液相馏分和重液相馏分;步骤s3、于过热水蒸汽的作用下,所述步骤s2得到的所述轻液相馏分经液体裂解工段处理后,得到第一裂解气;步骤s4、于过热水蒸汽的作用下,所述步骤s2得到的所述气相馏分经气体裂解工段处理后,得到第二裂解气;步骤s5、所述步骤s3得到的所述第一裂解气和所述步骤s4得到的所述第二裂解气经急冷工段处理后,分别得到第三裂解气、裂解燃料油和第一裂解汽油;步骤s6、所述步骤s5得到的所述第三裂解气经压缩工段处理后,得到高压裂解气;步骤s7、所述步骤s6得到的所述高压裂解气经精馏分离工段处理后,得到甲烷氢副产品、乙烯产品、丙烯产品、混合c4副产品和第二裂解汽油。优选地,所述步骤s2得到的所述重液相馏分和所述步骤s5得到的所述裂解燃料油合并得到裂解燃料油副产品。优选地,所述步骤s5得到的所述第一裂解汽油和所述步骤s7得到的所述第二裂解汽油合并得到裂解汽油副产品。优选地,在所述步骤s7中,所述精馏分离工段采用顺序分离工艺、前脱乙烷分离工艺、前脱丙烷分离工艺中的任意一种。优选地,在所述步骤s1中,在所述原油预处理工段内,对所述宽馏分原油依次进行脱盐预处理、脱水预处理和预热预处理。优选地,在所述步骤s5中,对所述第一裂解气和所述第二裂解气依次进行急冷油处理和急冷水处理。优选地,在所述步骤s6中,在所述压缩工段内,对所述第三裂解气依次进行增压处理、碱洗处理、水洗处理和干燥处理。优选地,在所述步骤s7中,在所述精馏分离工段内,对所述高压裂解气按不同组合进行深冷处理、脱甲烷处理、脱乙烷处理、乙烯精馏处理、脱丙烷处理、丙烯精馏处理和脱丁烷处理。优选地,在所述步骤s1中,所述原油预处理工段的工作条件为:入口:操作压力为0.45~0.65mpaa,操作温度为10~70℃;出口:操作压力为0.25~0.45mpaa,操作温度为70~450℃;脱盐率为97.0~99.9%,脱水率为95.0~99.5%。优选地,在所述步骤s2中,所述油品汽提工段的工作条件为:操作压力为0.20~0.40mpaa,顶部操作温度为70~190℃,底部操作温度为370~450℃。优选地,在所述步骤s2中,所述预处理原油与所述过热水蒸汽的质量比为1:0.03~0.27。优选地,在所述步骤s3中,所述液体裂解工段的工作条件为:反应压力为0.15~0.35mpaa,反应温度为800~860℃。优选地,在所述步骤s3中,所述轻液相馏分与所述过热水蒸汽的质量比为1:0.50~1.20。优选地,在所述步骤s4中,所述气体裂解工段的工作条件为:反应压力为0.15~0.35mpaa,反应温度为830~890℃。优选地,在所述步骤s4中,所述气相馏分与所述过热水蒸汽的质量比为1:0.20~0.50。优选地,在所述步骤s5中,所述急冷工段的工作条件为:急冷油处理:操作压力为0.14~0.34mpaa,顶部操作温度为101~121℃,底部操作温度为150~230℃;急冷水处理:操作压力为0.13~0.33mpaa,顶部操作温度为35~55℃,底部操作温度为75~95℃。优选地,在所述步骤s6中,所述压缩工段的工作条件为:入口:操作压力为0.12~0.32mpaa,操作温度为35~55℃;出口:操作压力为3.60~4.90mpaa,操作温度为81~99℃。优选地,在所述步骤s6中,所述压缩工段为多段压缩工段。优选地,在所述步骤s6中,所述压缩工段为五段压缩工段。本发明采用以上技术方案,与现有技术相比,具有如下技术效果:本发明的一种降低乙烯联合装置综合能耗的系统和方法,利用油品汽提工段对预处理原油进行水蒸汽汽提蒸馏,分离得到气相馏分、轻液相馏分和重液相馏分,其中的气相馏分和轻液相馏分分别送至气体裂解工段和液体裂解工段进行裂解反应,不仅缩短了工艺流程,而且大幅度降低了综合能耗;从原油炼制出发,包括炼油、裂解、分离一体化的乙烯联合装置综合能耗从现有技术676~810千克标油/吨乙烯下降到553~663千克标油/吨乙烯。附图说明图1是本发明一个示意性降低乙烯联合装置综合能耗系统的流程图。图2是本发明一个示意性降低乙烯联合装置综合能耗方法的流程图。其中的附图标记为:原油预处理工段10、油品汽提工段20、液体裂解工段30、气体裂解工段40、急冷工段50、压缩工段60、精馏分离工段70、宽馏分原油80、过热水蒸汽90、预处理原油11、气相馏分21、轻液相馏分22、重液相馏分23、第一裂解气31、第二裂解气41、第三裂解气51、裂解燃料油52、第一裂解汽油53、高压裂解气61、甲烷氢副产品71、乙烯产品72、丙烯产品73、混合c4副产品74、第二裂解汽油75、裂解燃料油副产品76、裂解汽油副产品77。具体实施方式下面将结合本发明中的附图,对本发明实施例中的技术方案进行清楚、完整地描述,显然,所描述的实施例仅仅是本发明一部分实施例,而不是全部的实施例。基于本发明中的实施例,本领域普通技术人员在没有作出创造性劳动前提下所获得的所有其他实施例,都属于本发明保护的范围。需要说明的是,在不冲突的情况下,本发明中的实施例及实施例中的特征可以相互组合。下面结合附图和具体实施例对本发明作进一步说明,但不作为本发明的限定。实施例1本实施例为本发明的一个示意性实施例。如图1所示,一种降低乙烯联合装置综合能耗的系统,包括原油预处理工段10、油品汽提工段20、液体裂解工段30、气体裂解工段40、急冷工段50、压缩工段60和精馏分离工段70,原油预处理工段10与油品汽提工段20通过管道连接,液体裂解工段30分别与油品汽提工段20和急冷工段50通过管道连接,气体裂解工段40分别与油品汽提工段20和急冷工段50通过管道连接,急冷工段50、压缩工段60和精馏分离工段70依次通过管道连接。进一步地,原油预处理工段10包括脱盐处理设备、脱水处理设备和预热处理设备,分别用于对宽馏分原油80进行脱盐预处理、脱水预处理和预热预处理。进一步地,脱盐处理设备、脱水处理设备和预热处理设备顺次通过管道连接。进一步地,油品汽提工段20使用的设备为油品汽提塔。进一步地,液体裂解工段30使用的设备为液体裂解炉。进一步地,气体裂解工段40使用的设备为气体裂解炉。进一步地,急冷工段50包括急冷油设备和急冷水设备,分别用于对裂解气进行急冷油处理和急冷水处理。进一步地,急冷油设备和急冷水设备顺次通过管道连接。进一步地,急冷油设备为急冷油塔,急冷水设备为急冷水塔。进一步地,压缩工段60包括增压处理设备、碱洗处理设备、水洗处理设备和干燥处理设备,分别用于对裂解气进行增压处理、碱洗处理、水洗处理和干燥处理。进一步地,增压处理设备、碱洗处理设备、水洗处理设备和干燥处理设备顺次通过管道连接。进一步地,精馏分离工段70包括深冷设备、脱甲烷设备、脱乙烷设备、乙烯精馏设备、脱丙烷设备、丙烯精馏设备和脱丁烷设备,分别用于对裂解气进行深冷处理、脱甲烷处理、脱乙烷处理、乙烯精馏处理、脱丙烷处理、丙烯精馏处理和脱丁烷处理。进一步地,深冷设备、脱甲烷设备、脱乙烷设备、乙烯精馏设备、脱丙烷设备、丙烯精馏设备和脱丁烷设备顺次通过管道连接。进一步地,除上述描述的顺序分离工艺外,在精馏分离工段70内还可以采用前脱乙烷分离工艺或前脱丙烷分离工艺,区别仅仅在于精馏分离工段70内的上述设备的顺序略有不同。如图2所示,应用于上述降低乙烯联合装置综合能耗的系统的方法,包括以下步骤:步骤s1、宽馏分原油80经原油预处理工段10处理后,得到预处理原油11;步骤s2、于过热水蒸汽90的作用下,步骤s1得到的预处理原油11经油品汽提工段20处理后,分别得到气相馏分21、轻液相馏分22和重液相馏分23;步骤s3、于过热水蒸汽90的作用下,步骤s2得到的轻液相馏分22经液体裂解工段30处理后,得到第一裂解气31;步骤s4、于过热水蒸汽90的作用下,步骤s2得到的气相馏分21经气体裂解工段40处理后,得到第二裂解气41;步骤s5、步骤s3得到的第一裂解气31和步骤s4得到的第二裂解气41经急冷工段50处理后,分别得到第三裂解气51、裂解燃料油52和第一裂解汽油53;步骤s6、步骤s5得到的第三裂解气51经压缩工段60处理后,得到高压裂解气61;步骤s7、步骤s6得到的高压裂解气61经精馏分离工段70处理后,得到甲烷氢副产品71、乙烯产品72、丙烯产品73、混合c4副产品74和第二裂解汽油75。进一步地,在步骤s1中,在原油预处理工段10内,对宽馏分原油80依次进行脱盐预处理、脱水预处理和预热预处理。进一步地,在上述步骤中,步骤s3和步骤s4为并列的步骤。进一步地,在步骤s5中,在急冷工段50内,对第一裂解气31和第二裂解气41依次进行急冷油处理和急冷水处理。进一步地,在步骤s6中,在压缩工段60内,对第三裂解气51依次进行增压处理、碱洗处理、水洗处理和干燥处理。进一步地,在步骤s7中,在精馏分离工段70内,对高压裂解气61按不同组合进行深冷处理、脱甲烷处理、脱乙烷处理、乙烯精馏处理、脱丙烷处理、丙烯精馏处理和脱丁烷处理。进一步地,步骤s2得到的重液相馏分23和步骤s5得到的裂解燃料油52合并得到裂解燃料油副产品76。进一步地,步骤s5得到的第一裂解汽油53和步骤s7得到的第二裂解汽油75合并得到裂解汽油副产品77。进一步地,在步骤s1中,在原油预处理工段10内,对宽馏分原油80依次进行脱盐预处理、脱水预处理和预热预处理,从而得到预处理原油11。进一步地,在步骤s1中,原油预处理工段10的工作条件为:入口:操作压力为0.45~0.65mpaa,操作温度为10~70℃;出口:操作压力为0.25~0.45mpaa,操作温度为70~450℃;脱盐率为97.0~99.9%,脱水率为95.0~99.5%。进一步地,在步骤s2中,油品汽提工段20的工作条件为:操作压力为0.20~0.40mpaa,顶部操作温度为70~190℃,底部操作温度为370~450℃。进一步地,在油品汽提工段20内,预处理原油11与过热水蒸汽90的质量比为1:0.03~0.27。进一步地,在步骤s3中,液体裂解工段30的工作条件为:反应压力为0.15~0.35mpaa,反应温度为800~860℃。进一步地,在液体裂解工段30内,轻液相馏分22与过热水蒸汽90的质量比为1:0.50~1.20。进一步地,在步骤s4中,气体裂解工段40的工作条件为:反应压力为0.15~0.35mpaa,反应温度为830~890℃。进一步地,在气体裂解工段40内,气相馏分21与过热水蒸汽90的质量比为1:0.20~0.50。进一步地,在步骤s5中,急冷工段50的工作条件为:急冷油处理:操作压力为0.14~0.34mpaa,顶部操作温度为101~121℃,底部操作温度为150~230℃;急冷水处理:操作压力为0.13~0.33mpaa,顶部操作温度为35~55℃,底部操作温度为75~95℃。进一步地,在步骤s6中,压缩工段60的工作条件为:入口:操作压力为0.12~0.32mpaa,操作温度为35~55℃;出口:操作压力为3.60~4.90mpaa,操作温度为81~99℃。进一步地,压缩工段60为五段压缩工段。进一步地,在步骤s7中,精馏分离工段70采用顺序分离工艺、前脱乙烷分离工艺、前脱丙烷分离工艺中的任意一种。本发明的一个具体实施过程如下:将宽馏分原油80输入至原油预处理工段10进行脱盐、脱水、预热等预处理,预处理得到的预处理原油11输入至油品汽提工段20;分别向油品汽提工段20、液体裂解工段30和气体裂解工段40输入过热水蒸汽90,其中,过热水蒸汽90被分别输入至液体裂解工段30内的液体裂解炉的对流段和气体裂解工段40内的气体裂解炉的对流段;在油品汽提工段20内,过热水蒸汽90与预处理原油11进行气液接触,发生传热传质过程,预处理原油11被分为气相馏分21、轻液相馏分22和重液相馏分23,其中,气相馏分21从油品汽提工段20的顶部(即油品汽提塔的塔顶)流出并输入至气体裂解工段40(输入至气体裂解炉的对流段),轻液相馏分22从油品汽提工段20的中部(即油品汽提塔的塔中部)侧线流出并输入至液体裂解工段30(输入至液体裂解炉的对流段),重液相馏分23从油品汽提工段20的底部(即油品汽提塔的塔底)流出;在液体裂解工段30内,轻液相馏分22在液体裂解炉的对流段与过热水蒸汽90被进一步预热至横跨温度后,进入液体裂解炉的辐射段,发生蒸汽热裂解反应,生成第一裂解气31,其中,第一裂解气31包括三烯、三苯等产品,第一裂解气31从液体裂解炉的辐射段流出,并输入至急冷工段50;在气体裂解工段40内,气相馏分21在气体裂解炉的对流段与热水蒸汽90被进一步预热至横跨温度后,进入气体裂解炉的辐射段,发生蒸汽热裂解反应,生成第二裂解气41,其中,第二裂解气41包括乙烯、丙烯等产品,第二裂解气41从气体裂解炉的辐射段流出,并输入至急冷工段50;在急冷工段50内,第一裂解气31经过急冷油处理和急冷水处理后,变成第一股第三裂解气51和裂解燃料油52,第二裂解气41经过急冷水处理后,变成第二股第三裂解气51和第一裂解汽油53,第一股第三裂解气51和第二股第三裂解气51合并后从急冷工段50的顶部流出,并输入至压缩工段60,裂解燃料油52和第一裂解汽油53从急冷工段50的底部流出,裂解燃料油52和重液相馏分23合并形成裂解燃料油副产品76;在压缩工段60内,第三裂解气51依次进行增压处理、碱洗处理、水洗处理和干燥处理后,变成高压裂解气61,高压裂解气61从压缩工段60流出,并输入至精馏分离工段70;在精馏分离工段70内,高压裂解气61按不同组合进行深冷处理、脱甲烷处理、脱乙烷处理、乙烯精馏处理、脱丙烷处理、丙烯精馏处理和脱丁烷处理后,分别得到甲烷氢副产品71、乙烯产品72、丙烯产品73、混合c4副产品74和第二裂解汽油75,第二裂解汽油75和第一裂解汽油53合并形成裂解汽油副产品77。本发明的优点在于,利用油品汽提工段对预处理原油进行水蒸汽汽提蒸馏,分离得到气相馏分、轻液相馏分和重液相馏分,其中的气相馏分和轻液相馏分分别送至气体裂解工段和液体裂解工段进行裂解反应,不仅缩短了工艺流程,而且大幅度降低了综合能耗;从原油炼制出发,包括炼油、裂解、分离一体化的乙烯联合装置综合能耗从现有技术676~810千克标油/吨乙烯下降到553~663千克标油/吨乙烯。实施例2为验证上述降低乙烯联合装置综合能耗的系统及方法的可靠性,发明人进行了一组对照实验,如下:实验组1一采用本发明的降低乙烯联合装置综合能耗的系统及方法的石油工厂,其乙烯生产规模为150万吨/年,宽馏分原油为沙特阿拉伯轻质原油,该原油的主要性质如下:原油分类高硫中间基初馏点/℃91密度(20℃)/kg·m-3859.8馏出率(v)/%api32.35100℃3.11凝点/℃-17150℃13.02蜡含量/%3.48200℃22.64残碳/%4.25250℃32.07元素分析300℃40.99硫/%2.30350℃48.83氮/%0.05400℃58.03镍/μg·g-15.40450℃64.79钒/μg·g-118.30500℃72.55其热裂解制乙烯方法同实施例1,具体工艺参数如下:原油预处理工段10:入口:操作压力0.49mpaa,操作温度25℃;出口:操作压力0.29mpaa,操作温度355℃;脱盐率99.5%,脱水率98.0%;油品汽提工段20:操作压力0.24mpaa,顶部操作温度85℃,底部操作温度390℃;预处理原油11与过热水蒸汽90的质量比为1:0.05;液体裂解工段30:液体裂解炉辐射段:反应压力0.19mpaa,反应温度819℃;轻液相馏分22与过热水蒸汽90的质量比为1:0.75;气体裂解工段40:气体裂解炉辐射段:反应压力0.19mpaa,反应温度848℃;气相馏分21与过热水蒸汽90的质量比为1:0.28;急冷工段50:急冷油设备:操作压力0.18mpaa,顶部操作温度106℃,底部操作温度179℃;急冷水设备:操作压力0.17mpaa,顶部操作温度39℃,底部操作温度81℃;压缩工段60采用五段压缩工艺,一段入口操作压力0.16mpaa,一段入口操作温度39℃;五段出口操作压力4.11mpaa,五段出口操作温度86℃;精馏分离工段70采用顺序分离工艺流程。该实验组的综合能耗如下表所示:对照组1采用现有工艺,其乙烯生产规模为150万吨/年,综合能耗如下表所示:由实验组1的综合能耗表和对照组1的综合能耗表可知,采用本发明的系统及方法,从沙特阿拉伯轻质原油炼制出发到纯度≥99.95mol%聚合级乙烯、纯度≥99.6mol%聚合级丙烯等主要产品为止,包括炼油、裂解、分离一体化的乙烯联合设备合计能耗为103688千克标油/小时,综合能耗为553千克标油/吨乙烯;采用现有工艺,从沙特阿拉伯轻质原油炼制出发到纯度≥99.95mol%聚合级乙烯、纯度≥99.6mol%聚合级丙烯等主要产品为止,包括炼油、裂解、分离一体化的乙烯联合设备合计能耗为126750千克标油/小时,综合能耗为676千克标油/吨乙烯;两者对比可知,本发明的综合能耗远小于现有技术。实施例3为验证上述降低乙烯联合装置综合能耗的系统及方法的可靠性,发明人进行了一组对照实验,如下:实验组2一采用本发明的降低乙烯联合装置综合能耗的系统及方法的石油工厂,其乙烯生产规模为100万吨/年,宽馏分原油为大庆原油,该原油的主要性质如下:原油分类低硫石蜡基初馏点/℃113密度(20℃)/kg·m-3861.7馏出率(v)/%api32.0100℃0.2凝点/℃33120℃1.3h2o含量/%0.01140℃2.5蜡含量/%26.3160℃3.8沥青质/%0.0180℃5.6胶质/%8.36200℃7.8残碳/%3.10220℃10.0灰分/%0.012240℃12.6元素分析260℃15.6硫/%0.11280℃17.6氮/%0.16300℃20.6镍/μg·g-13.06400℃30.5钒/μg·g-10.04500℃53.7其热裂解制乙烯方法同实施例1,具体工艺参数如下:原油预处理工段10:入口:操作压力0.51mpaa,操作温度30℃;出口:操作压力0.31mpaa,操作温度387℃;脱盐率99.7%,脱水率97.5%;油品汽提工段20:操作压力0.26mpaa,顶部操作温度89℃,底部操作温度399℃;预处理原油11与过热水蒸汽90的质量比为1:0.10;液体裂解工段30:液体裂解炉辐射段:反应压力0.21mpaa,反应温度823℃;轻液相馏分22与过热水蒸汽90的质量比为1:0.80;气体裂解工段40:气体裂解炉辐射段:反应压力0.21mpaa,反应温度853℃;气相馏分21与过热水蒸汽90的质量比为1:0.32;急冷工段50:急冷油设备:操作压力0.20mpaa,顶部操作温度109℃,底部操作温度186℃;急冷水设备:操作压力0.19mpaa,顶部操作温度41℃,底部操作温度82℃;压缩工段60采用五段压缩工艺,一段入口操作压力0.18mpaa,一段入口操作温度41℃;五段出口操作压力4.19mpaa,五段出口操作温度88℃;精馏分离工段70采用顺序分离工艺流程。该实验组的综合能耗如下表所示:对照组2采用现有工艺,其乙烯生产规模为100万吨/年,综合能耗如下表所示:由实验组2的综合能耗表和对照组2的综合能耗表可知,采用本发明的系统及方法,从大庆原油炼制出发到纯度≥99.95mol%聚合级乙烯、纯度≥99.6mol%聚合级丙烯等主要产品为止,包括炼油、裂解、分离一体化的乙烯联合设备合计能耗为73250千克标油/小时,综合能耗为586千克标油/吨乙烯;采用现有工艺,从大庆原油炼制出发到纯度≥99.95mol%聚合级乙烯、纯度≥99.6mol%聚合级丙烯等主要产品为止,包括炼油、裂解、分离一体化的乙烯联合设备合计能耗为89495千克标油/小时,综合能耗为716千克标油/吨乙烯;两者对比可知,本发明的综合能耗远小于现有技术。实施例4为验证上述降低乙烯联合装置综合能耗的系统及方法的可靠性,发明人进行了一组对照实验,如下:实验组3一采用本发明的降低乙烯联合装置综合能耗的系统及方法的石油工厂,其乙烯生产规模为80万吨/年,宽馏分原油为胜利原油,该原油的主要性质如下:其热裂解制乙烯方法同实施例1,具体工艺参数如下:原油预处理工段10:入口:操作压力0.57mpaa,操作温度45℃;出口:操作压力0.37mpaa,操作温度406℃;脱盐率99.0%,脱水率99.0%;油品汽提工段20:操作压力0.32mpaa,顶部操作温度137℃,底部操作温度422℃;预处理原油11与过热水蒸汽90的质量比为1:0.18;液体裂解工段30:液体裂解炉辐射段:反应压力0.27mpaa,反应温度840℃;轻液相馏分22与过热水蒸汽90的质量比为1:0.90;气体裂解工段40:气体裂解炉辐射段:反应压力0.27mpaa,反应温度869℃;气相馏分21与过热水蒸汽90的质量比为1:0.40;急冷工段50:急冷油设备:操作压力0.26mpaa,顶部操作温度116℃,底部操作温度201℃;急冷水设备:操作压力0.25mpaa,顶部操作温度49℃,底部操作温度89℃;压缩工段60采用五段压缩工艺,一段入口操作压力0.24mpaa,一段入口操作温度49℃;五段出口操作压力4.36mpaa,五段出口操作温度93℃;精馏分离工段70采用前脱乙烷分离工艺流程。该实验组的综合能耗如下表所示:对照组3采用现有工艺,其乙烯生产规模为80万吨/年,综合能耗如下表所示:由实验组3的综合能耗表和对照组3的综合能耗表可知,采用本发明的系统及方法,从胜利原油炼制出发到纯度≥99.95mol%聚合级乙烯、纯度≥99.6mol%聚合级丙烯等主要产品为止,包括炼油、裂解、分离一体化的乙烯联合设备合计能耗为64102千克标油/小时,综合能耗为641千克标油/吨乙烯;采用现有工艺,从胜利原油炼制出发到纯度≥99.95mol%聚合级乙烯、纯度≥99.6mol%聚合级丙烯等主要产品为止,包括炼油、裂解、分离一体化的乙烯联合设备合计能耗为78296千克标油/小时,综合能耗为783千克标油/吨乙烯;两者对比可知,本发明的综合能耗远小于现有技术。实施例5为验证上述降低乙烯联合装置综合能耗的系统及方法的可靠性,发明人进行了一组对照实验,如下:实验组4一采用本发明的降低乙烯联合装置综合能耗的系统及方法的石油工厂,其乙烯生产规模为11.5万吨/年,宽馏分原油为中原原油,该原油的主要性质如下:其热裂解制乙烯方法同实施例1,具体工艺参数如下:原油分类含硫石蜡基初馏点/℃62密度(20℃)/kg·m-3854.8馏出率(v)/%api33.3100℃4.27凝点/℃32120℃7.41h2o含量/%0.00140℃10.09蜡含量/%20.5160℃13.01沥青质/%0.17180℃15.50胶质/%10.86200℃17.95残碳/%4.10220℃21.88灰分/%0.015240℃24.81元素分析260℃28.10硫/%0.57280℃30.98氮/%0.17300℃34.16镍/μg·g-13.40400℃46.61钒/μg·g-12.80500℃68.24原油预处理工段10:入口:操作压力0.59mpaa,操作温度49℃;出口:操作压力0.39mpaa,操作温度425℃;脱盐率99.3%,脱水率98.2%;油品汽提工段20:操作压力0.34mpaa,顶部操作温度162℃,底部操作温度437℃;预处理原油11与过热水蒸汽90的质量比为1:0.23;液体裂解工段30:液体裂解炉辐射段:反应压力0.29mpaa,反应温度848℃;轻液相馏分22与过热水蒸汽90的质量比为1:1.00;气体裂解工段40:气体裂解炉辐射段:反应压力0.29mpaa,反应温度881℃;气相馏分21与过热水蒸汽90的质量比为1:0.45;急冷工段50:急冷油设备:操作压力0.28mpaa,顶部操作温度118℃,底部操作温度220℃;急冷水设备:操作压力0.27mpaa,顶部操作温度51℃,底部操作温度92℃;压缩工段60采用五段压缩工艺,一段入口操作压力0.26mpaa,一段入口操作温度51℃;五段出口操作压力4.61mpaa,五段出口操作温度95℃;精馏分离工段70采用前脱乙烷分离工艺流程。该实验组的综合能耗如下表所示:对照组4采用现有工艺,其乙烯生产规模为11.5万吨/年,综合能耗如下表所示:由实验组4的综合能耗表和对照组4的综合能耗表可知,采用本发明的系统及方法,从中原原油炼制出发到纯度≥99.95mol%聚合级乙烯、纯度≥99.6mol%聚合级丙烯等主要产品为止,包括炼油、裂解、分离一体化的乙烯联合设备合计能耗为9530千克标油/小时,综合能耗为663千克标油/吨乙烯;采用现有工艺,从中原原油炼制出发到纯度≥99.95mol%聚合级乙烯、纯度≥99.6mol%聚合级丙烯等主要产品为止,包括炼油、裂解、分离一体化的乙烯联合设备综合能耗合计能耗为11643千克标油/小时,为810千克标油/吨乙烯;两者对比可知,本发明的综合能耗远小于现有技术。实施例6实验组5一采用本发明的降低乙烯联合装置综合能耗的系统及方法的石油工厂,其乙烯生产规模为100万吨/年,宽馏分原油为沙特阿拉伯轻质原油,该原油的主要性质如下:原油分类高硫中间基初馏点/℃91密度(20℃)/kg·m-3859.8馏出率(v)/%api32.35100℃3.11凝点/℃-17150℃13.02蜡含量/%3.48200℃22.64残碳/%4.25250℃32.07元素分析300℃40.99硫/%2.30350℃48.83氮/%0.05400℃58.03镍/μg·g-15.40450℃64.79钒/μg·g-118.30500℃72.55其热裂解制乙烯方法同实施例1,具体工艺参数如下:原油预处理工段10:入口:操作压力0.45mpaa,操作温度10℃;出口:操作压力0.25mpaa,操作温度70℃;脱盐率97.0%,脱水率99.5%;油品汽提工段20:操作压力0.20mpaa,顶部操作温度70℃,底部操作温度370℃;预处理原油11与过热水蒸汽90的质量比为1:0.03;液体裂解工段30:液体裂解炉辐射段:反应压力0.15mpaa,反应温度800℃;轻液相馏分22与过热水蒸汽90的质量比为1:0.50;气体裂解工段40:气体裂解炉辐射段:反应压力0.15mpaa,反应温度830℃;气相馏分21与过热水蒸汽90的质量比为1:0.20;急冷工段50:急冷油设备:操作压力0.14mpaa,顶部操作温度101℃,底部操作温度150℃;急冷水设备:操作压力0.13mpaa,顶部操作温度35℃,底部操作温度75℃;压缩工段60采用五段压缩工艺,一段入口操作压力0.12mpaa,一段入口操作温度35℃;五段出口操作压力3.60mpaa,五段出口操作温度81℃;精馏分离工段70采用前脱丙烷分离工艺流程。该实验组的综合能耗如下表所示:由实验组5的综合能耗表和对照组1的综合能耗表可知,采用本发明的系统及方法,从沙特阿拉伯轻质原油炼制出发到纯度≥99.95mol%聚合级乙烯、纯度≥99.6mol%聚合级丙烯等主要产品为止,包括炼油、裂解、分离一体化的乙烯联合设备合计能耗为77375千克标油/小时,综合能耗为619千克标油/吨乙烯;采用现有工艺,从沙特阿拉伯轻质原油炼制出发到纯度≥99.95mol%聚合级乙烯、纯度≥99.6mol%聚合级丙烯等主要产品为止,包括炼油、裂解、分离一体化的乙烯联合设备合计能耗为84500千克标油/小时,综合能耗为676千克标油/吨乙烯;两者对比可知,本发明的综合能耗远小于现有技术。实施例7实验组6一采用本发明的降低乙烯联合装置综合能耗的系统及方法的石油工厂,其乙烯生产规模为100万吨/年,宽馏分原油为沙特阿拉伯轻质原油,该原油的主要性质如下:原油分类高硫中间基初馏点/℃91密度(20℃)/kg·m-3859.8馏出率(v)/%api32.35100℃3.11凝点/℃-17150℃13.02蜡含量/%3.48200℃22.64残碳/%4.25250℃32.07元素分析300℃40.99硫/%2.30350℃48.83氮/%0.05400℃58.03镍/μg·g-15.40450℃64.79钒/μg·g-118.30500℃72.55其热裂解制乙烯方法同实施例1,具体工艺参数如下:原油预处理工段10:入口:操作压力0.65mpaa,操作温度70℃;出口:操作压力0.45mpaa,操作温度450℃;脱盐率99.9%,脱水率95.0%;油品汽提工段20:操作压力0.40mpaa,顶部操作温度190℃,底部操作温度450℃;预处理原油11与过热水蒸汽90的质量比为1:0.27;液体裂解工段30:液体裂解炉辐射段:反应压力0.35mpaa,反应温度860℃;轻液相馏分22与过热水蒸汽90的质量比为1:1.20;气体裂解工段40:气体裂解炉辐射段:反应压力0.35mpaa,反应温度890℃;气相馏分21与过热水蒸汽90的质量比为1:0.50;急冷工段50:急冷油设备:操作压力0.34mpaa,顶部操作温度121℃,底部操作温度230℃;急冷水设备:操作压力0.33mpaa,顶部操作温度55℃,底部操作温度95℃;压缩工段60采用五段压缩工艺,一段入口操作压力0.32mpaa,一段入口操作温度55℃;五段出口操作压力4.90mpaa,五段出口操作温度99℃;精馏分离工段70采用前脱丙烷分离工艺流程。该实验组的综合能耗如下表所示:由实验组6的综合能耗表和对照组1的综合能耗表可知,采用本发明的系统及方法,从沙特阿拉伯轻质原油炼制出发到纯度≥99.95mol%聚合级乙烯、纯度≥99.6mol%聚合级丙烯等主要产品为止,包括炼油、裂解、分离一体化的乙烯联合设备合计能耗为78745千克标油/小时,综合能耗为630千克标油/吨乙烯;采用现有工艺,从沙特阿拉伯轻质原油炼制出发到纯度≥99.95mol%聚合级乙烯、纯度≥99.6mol%聚合级丙烯等主要产品为止,包括炼油、裂解、分离一体化的乙烯联合设备合计能耗为84500千克标油/小时,综合能耗为676千克标油/吨乙烯;两者对比可知,本发明的综合能耗远小于现有技术。由上述实验组1~6和对照组1~4可知,采用本发明的降低乙烯联合装置综合能耗的系统及方法,利用油品汽提工段对预处理原油进行水蒸汽汽提蒸馏,分离得到气相馏分、轻液相馏分和重液相馏分,其中的气相馏分和轻液相馏分分别送至气体裂解工段和液体裂解工段进行裂解反应,不仅缩短了工艺流程,而且大幅度降低了综合能耗;从原油炼制出发,包括炼油、裂解、分离一体化的乙烯联合装置综合能耗从现有技术676~810千克标油/吨乙烯下降到553~663千克标油/吨乙烯。以上所述仅为本发明较佳的实施例,并非因此限制本发明的实施方式及保护范围,对于本领域技术人员而言,应当能够意识到凡运用本发明说明书及图示内容所作出等同替换和显而易见变化所得到的方案,均应当包含在本发明的保护范围内。当前第1页1 2 3