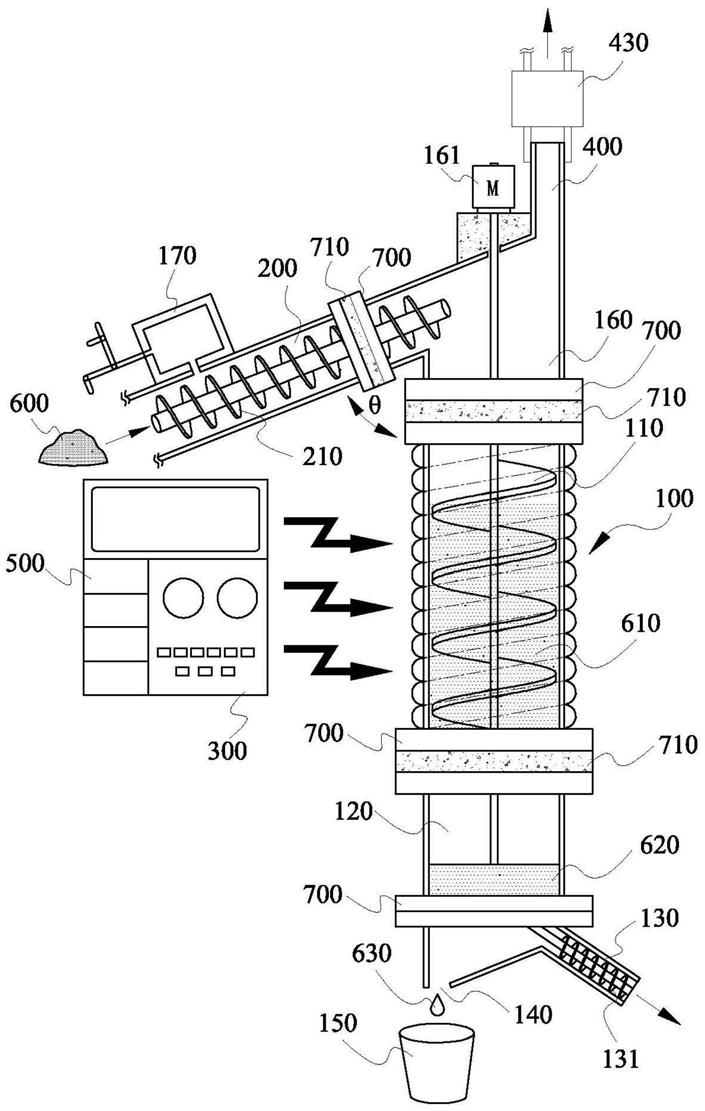
1.本发明有关油泥或废弃物等可再生利用物质的处理系统,尤指设计以高频电磁加热技术,使油泥或废弃物气化为合成气(syngas),即人造瓦斯的再生能源使用目的,促进循环经济。
背景技术:2.对于油泥及废弃物的处理,一直以来都是令各级环保单位及业主或民众头痛不已的问题,目前垃圾废弃物,除了分类回收再利用之外,都直接以掩埋或送往焚化炉焚烧;油泥则正在研究、测试与稻草、麦秆等固形物粉碎后,固化成颗粒状使之成为具备热值的rdf-5(refused-derived fuel),再利用为锅炉等的热源使用。
技术实现要素:3.本发明提供一种新颖的油泥或废弃物处理系统,利用高频加热原理,即诱电加热(dielectric heating)或诱导加热(induction heating)可分别对导体及非导体加热,亦即一般通称的高周波加热方法,其中,可将油泥或废弃物等非导体的物质置于反应炉内以为原料,以高频加热机令反应炉内的原料由反应炉管壁及反应炉中的搅拌器因电场作用产生高温,将高温传导至炉内的原料于极短时间内使原料加热升温,而将反应炉内的原料物质直接裂解气化而成为合成气(syngas)及小部分液态燃料及灰渣。
4.本发明的系统是由反应炉本身所产生的热能传导至被加热的油泥或废弃物,因此除了加热均匀迅速,效率极高外,更可以节省大量能源。
5.根据研究,油泥的成份主要有水分、无机性固体物、碳氢化合物等三大类;国际能源总署统计,举凡由生物产生的有机物质,农畜牧业废弃物,都市垃圾及下水道污泥及沼气等等,均定义为生质能物质,这是仅次于石油、煤及天然气的第四大能源,而且是只要人类文明存在,它就是取之不尽,用之不竭的可循环再生能源,实在是值得人们善加开发利用的宝贵资源。
6.本发明提供一种油泥或废弃物处理系统,包括油泥或废弃物(以下统称为被处理物)的前置处理作业设施,为:至少一个初步处理单元,即;可为洗涤或搅拌或干燥或加工为流体等,做一般性前置处理的设施。在初步前置处理单元之后,可设置有粉碎设施或固化或加工为流体态的设施,使被处理物成为待处理的素原料或rdf-5或浓稠流体,并集中于原料堆置场所、槽或装袋暂置。再设置进料单元,依其固态或流体型态,可分别为:固态,可包括输送设施或铲斗等各种投料设施,将rdf-5或素原料送至原料槽斗;原料槽斗则设置至少一个出料口,接续有至少一个入料管,其中入料管为封闭式,以推杆或以螺旋入料;该至少一个入料管再接续至少一个反应炉,该至少一个反应炉与至少一个入料管以θ角接合,根据热升冷降的物理现象,该θ角以锐角较佳,可减少反应炉的高热进入入料管;但亦可设计套接隔热管及设置散热鳍片或水冷系统,以尽量避免高热影响入料,如此则入料管及反应炉亦可以钝角或直角接合;至少一高频(即高周波)加热机;该至少一个气化反应炉上半部设置
有合成气收集管,可连接集气泵;下半部设置有液态油输出管及灰渣出口;其中,灰渣出口可设置螺旋管将灰渣引出。
7.为营造气化反应炉的控氧环境,在入料管与气化反应炉及灰渣、液态油出口管与裂解氧化反应炉等组构而成的系统,可设置自动控制或手动气密闭锁部件或真空井/泵,令真空井/泵浦辅助抽除大气,以控制氧气等气体进入反应炉参与裂解气化反应;此外,为使气化反应炉维持长时间运作,本发明亦可在反应炉内腔中设置材质为导体的搅拌器如螺杆或旋叶等,除可使该导体搅拌器亦形成涡流成为热源外,亦可搅动原料,进而刮除反应炉内壁的灰渣,除得以维持裂解反应炉的容积外,并可与炉壁热源共同形成“内外均对原料加热”的功效,可大幅提升裂解反应的效率;其中可视需要将该搅拌器设置为自动或手动。
8.为进一步增进效率,本发明的入料、裂解气化及出渣等三大部份,可一体成型或以组合式构造分别设置绝热垫片、法兰、隔热管散热鳍片或水冷等冷却系统等材料或部件,裨免使气化反应炉于运作时将高温传递至入料管及出渣管。
9.本发明亦可设计成移动式的机动型机组,以提供为独立的供电单元。以偏远地区的居家或工寮为例,可以同时解决垃圾及用电问题。甚至,如果自身产出的垃圾或厨余数量不足,可以捡拾枯枝落叶等废弃物充当原料,进而得到电力或人造瓦斯的热源。
10.此外,更可设计将本发明系统装置于载具,将系统所获得的合成气进一步纯化供应予燃气引擎或燃料电池使用,为载具提供更完美的驱动能源。
11.至于在流体态原料方面,如油泥,本发明突破传统观念采取由下而上的入料方法进行油泥或其他废弃物处理。由于油泥为浓稠的流体,可以利用连通管原理或以帮浦推挤油泥或呈流体状的废弃物进入反应炉进行高温裂解,达到将油泥或废弃物气化的目的。即,将油泥或成浓稠流体态的废弃物置于系统的管道内,管道的两端分别设置为入料端及反应炉端,其间为连通管的构造,反应炉端向上延伸,原料则由下而上输入,反应炉末端处可设置滤网,以减少裂解后的灰渣没入原料中,并可形成磁涡流现象,达到如前述相同的内外加热效应;入料端可为槽体或以管路与帮浦相连至原料槽;反应炉端由下而上的配置方式则为管体、冷却段及加热段,加热段顶端的一侧为出渣侧,另一侧则为向上延伸的舱壁;出渣侧接续密闭腔室为灰渣堆积室;如同前述,在灰渣堆积室及出渣侧等,均可设置散热鳍片或水冷设施;灰渣堆积室下部再设置有缓冲室及底部的出渣舱,以出渣口/管与外部相通。如此,本发明方法即可具有控氧条件对油泥及成浓稠流体的废弃物进行高温裂解。因为无论是油泥或成浓稠流体的废弃物,基本上均已具备有一定的气密性;亦即,当上述原料由入料端进入管道,无论是连通管构造或以帮浦推挤入料,均已令系统与外部形成阻绝状态,大气无法进入系统,形成绝佳的密闭控氧环境;此由下而上入料的方式除可巧妙营造密闭控氧条件外,更可连续不绝入料,并节省系统机构的大量动作,实为油泥及废弃物处理技术的一大突破。
12.必须加以说明的是:如采取连通管概念所设置的系统,在逐步进行油泥等原料裂解时,在入料端应依系统对原料裂解的进度配合入料,以维持反应炉端与入料端压力及质量的平衡,如此才能持续将管道中的原料逐步向上推挤至加热区段,进行连续不停的裂解反应程序,使系统维持运作。另外,值得一提的是:在反应炉端的顶部需设置有集气管/口,以将油泥等原料裂解后所得的合成气接往集气槽、净化槽等后续处理设施。
13.在此,另一巧妙的设计可提供油泥等原料裂解反应后的灰渣被自动移入另侧的灰
渣堆积室;即,在顶部集气管/口边再设置一吸气管或自集气管岔出,直接将合成气导入反应区内部,对由下而上逐步完成裂解反应后所向上推挤冒出的灰渣,直接吹向灰渣堆积室,避免其向上累堆至形成集气管/口阻塞的情事;此吸气管可加设耐高温的帮浦,以确保吹灰的效益。经此吸、吹过程的合成气,最终仍能重返,经集气管/口进入集气槽、各净化槽等后续处理设施;如此系统则可不需另外设置其他清理灰渣的机构,免除多余的机械动作,徒增可能增加系统气密度损害的风险。
附图说明
14.图1是本发明的气化炉示意图;
15.图2是本发明的流程示意图;
16.图3是本发明的辐射形配置的实施例示意图;
17.图4是本发明的另一可移动式之实施示意图;
18.图5是本发明由下方向上方进料进行裂解反应处理的结构示意图;以及
19.图6是本发明以输料泵由下方向上方进料进行裂解反应处理的结构示意图。
20.附图标记说明:
21.100:气化反应炉
22.110:加热区
23.111:降温区段
24.120:灰渣区
25.130:出渣管
26.131:出渣螺旋输送杆
27.140:泄油口
28.141:集油管
29.150:集油槽
30.160:搅拌器
31.161:搅拌器马达
32.170:真空井/泵
33.180:灰渣堆积室
34.181:密闭阀
35.182:缓冲室
36.183:出渣室
37.184:出渣口
38.200:进料管
39.210:进料螺旋输送杆
40.220:入料管
41.221:输料泵
42.222:入料管
43.223:出料管
44.230:支座
45.300:高频加热机
46.400:合成气收集管
47.410:集气槽
48.430:控压阀/接头
49.440:安全阀/供气管路单元
50.450:吸气管
51.500:中央控制单元
52.510:净化单元
53.520:燃气引擎
54.530:发电机组
55.540:液态燃料处理单元
56.550:燃烧器
57.600:原料堆
58.610:原料
59.611:被处理物
60.620:灰渣区
61.621:灰渣槽桶
62.630:油料
63.640:原料槽
64.650:油泥槽
65.700:法兰接头
66.710:隔热垫片
67.800:原料槽斗
68.810:输送带
69.811:输送机构
70.820:控制阀
71.900:移动式气化发电机组
72.910:起动电力单元
73.920:粉碎机
74.930:充电单元
75.940:燃料电池
具体实施方式
76.请参阅图1,本实施例为以法兰接头组合在一起的入料、气化反应炉组、出渣等三大部分的系统说明。在中央控制单元500经电源启动后,原料堆600的原料即由进料管200的进料螺旋输送杆210输入气化反应炉100;其中气化反应炉100为中空设计,外覆有石英等绝缘体,再包覆以保温棉(图未绘出)以尽量维持气化反应炉100的高温,节省能源;在原料进入后,即因重力作用,自底部逐渐往上堆积,待堆积一定高度,即填满加热区110后,中央控制单元500即下达加热指令,启动高频加热机300,令加热区110内原料由气化反应炉100传
导高热至其内部产生急速升温,于极短时间内升温至额定温度,产生裂解气化反应,气化反应所获得的合成气(syngas)则可经由合成气收集管400及控压阀/接头430汇入收集槽(本图未绘出)作进一步处理使用。顺便一提的是,本实施例在启动之初,由原料进入气化反应炉100时,堆置于炉内下部灰渣区620的原料,因没有参与裂解气化反应,因此会被下方出渣口连接的出渣管130的出渣螺旋输送杆131在中央控制单元500下达指令后原封不动地连同以裂解气化反应后的灰渣退出,但此仅为初始运作时的情况;另外,在系统对原料作出裂解氧化反应时,会同时产生部分的液态油料630产品,该液态油料630则由炉体下方的泄油口140直接汇入集油槽150,或者,该液态油料630不自行汇集排出,而是与灰渣混合排出,以作进一步的处理或利用。
77.值得一提的是,本实施例的气化炉设置有自动控制或手动气密闭锁部件或真空井/泵170,使本系统可以在控氧的环境进行裂解反应。另外,本实施例所设置有上部进料管200、加热区110、下部灰渣区120及出渣管130,此各区域可以法兰(flang)接头700固合,形成一组合式结构,以方便维护保养或部件更替;该法兰接头700可设置隔热垫片710以控制加热区110的热传导效应,其中上部进料管200及下部灰渣区120的构成亦可以隔热材质制作,亦可加置散热鳍片或水冷系统,其目的均在于控制高温传导。此外,为避免本气化反应炉100的炉壁形成积碳或渣垢,本实施例亦设置有搅拌器160,该搅拌器160可为自动或手动,亦可为中央控制单元500在一定条件下自动启动搅拌器马达161,以适时搅拌原料,同时可清理炉壁积垢,确保气化反应炉100的容积,且由于搅拌器为导体材质,在该高频加热机300启动时,可同时令该搅拌器160产生涡流生热形成气化反应炉100内部的另一热源,使原料受气化反应炉100的炉壁及搅拌器160内外同时加热,可提升裂解气化的效率。
78.请参阅图2,本实施例为流程示意图。在原料堆600内的rdf-5原料610内,由输送带810输往原料槽斗800,设置于原料槽斗800下方的进料管200则将原料610输入气化反应炉100,在系统进行气化反应时即可获得合成气及部分油品以及灰渣,分别由合成气收集管400输往净化单元510,经净化后的合成气则可供应予燃气引擎520以产生机械能驱动发电机组530产出电力,副产品油料630则经由集油管汇集至集油槽150以进一步处理利用,灰渣则经由出渣管130集中于灰渣区620进一步处理使用。
79.请参阅图3,本实施例为较大规模的应用。在大量的被处理物611(即原料)由输送带810送至原料槽斗800,该原料槽斗800设置有多组进料管200。进料管200以适当的角度与气化反应炉100连接。当中央控制单元500下达启动指令后,输送带810即自原料堆600输送被处理物611至原料槽斗800,原料槽斗800内的原料即分别经由呈辐射状配置的进料管200分别将原料注入其所相连接的气化反应炉100,当气化反应炉100获得注入一定量的原料时,中央控制单元500即再令高频加热机300对气化反应炉100加热,以高温将原料原本较大分子的结构裂解为更小的分子形成气化反应,如此即可获得合成气、液态油及灰渣等各相物质,并被分别导入合成气收集管400,集油管141及灰渣槽桶621;其中,合成气收集管400所汇集的合成气可由集气泵浦(图未绘出)输往集气槽410,集气槽410设有压力安全阀(图未绘出),以调节气化反应炉100、合成气收集管400及集气槽410等各气相物质系统的压力,避免发生危险。之后集气槽410的合成气则进一步以管体再输往净化单元510的多个槽体进行各种处理步骤,例如:去除悬浮物、粉尘、脱硫、去酸、冷却、净化、纯化等,最后将净化后的合成气导入燃气引擎520或锅炉及蒸汽引擎以获得机械能驱动发电机组530产生电能。与此
同时,裂解氧化过程所产生的液态油料630则进入集油槽150,或经由集油管141输往中央储油槽以进一步处理利用。本实施例计有八机组作辐射状布设,其他亦可视厂房既有的空间因地制宜,或作多机组平行并列或梅花阵列甚至是上中下等多层布列。
80.请参阅图4,本实施例为一可移动式的设计,适用于各种临时性设施,例如工寮或山林避难小屋,露营区、集会场所,甚至是战地。本实施例较前述各例不同的是,在移动式气化发电机组900于自备有起动电力单元910,起动电力单元910可为蓄电设备或人力或其他发电设施。例如,在一山林工寮内,由某甲先行在操作中央控制单元500设定好操作程序,就地捡拾枯枝或垃圾等废弃物,送入粉碎机920获得较小颗粒的被处理物611后,投入进料管200;然后启动起动电力单元910,本系统即依某甲所设定的程序,下达指令予气化反应炉100,对所投进入料槽并被输入气化反应炉100的被处理物611加热,待气化反应炉100达到一定程度的高温时,随即发生气化现象获得合成气及部分液态油料;该所获得的合成气及液态油即分别经由其管路(图未绘出)进入合成气的净化单元510及液态燃料(油)处理单元540,分别进行净化和处理;其中逐渐堆栈的灰渣,则由出渣管130排出。在经过净化及必要处理后的合成气及油品则再分别进入集气槽410及集油槽150。或者,将系统所获得的合成气进一步纯化供应予燃料电池940使用。
81.集气槽及集油槽亦各设置有安全阀/供气管路单元440以确保维持系统管路及槽体的压力,让合成气得以安全、顺畅地提供予燃烧器550以供应热能或燃气引擎520以获取机械能推动发电机组530产生电能。值得一提的是,所获得的电能除直接供应电器使用之外,更可经由充电单元930,将电能输往起动电力单元910,对其续行充电以补充蓄电池的电能;亦即,在平时小耗电的情况下,蓄电池即可满足该工寮的照明等小功率电用具的需求,并在下次启动本移动式气化发电机组530时,亦可储存、提供充足的备用电力。准此,本实施例的系统规模可依实地需要设计,或大或小,依赖使用的需求而定。
82.请参阅图5,本实施例以油泥等浓稠液态的原料为说明案例。其同样有至少一个气化反应炉100,该气化反应炉100下方连接入料管220,该入料管220呈u型的连通管构造,右侧为入料端,设置有原料槽斗800,以输送带或管体等输送机构811与原料槽640连接,原料槽斗800下方设置有入料控制阀820,可定时定量对固联于下方的入料管220进行供料,该入料管220可以支座230固定,延伸至左侧时向上弯折而起,该气化反应炉100自该入料管220连接端由下而上分别设置有散热鳍片等气冷或水冷设施为降温区段111,降温区段111上方为加热区110,以高频加热机300对该原料施以高温加热进行裂解气化。
83.该加热区110顶部设置有合成气收集管400,该加热区110旁侧则连接有灰渣堆积室180,此合成气收集管400及灰渣堆积室180如同前述实施例,均可设置散热鳍片等气冷或水冷设施(图未绘出)以及该合成气收集管400旁侧另有吸气管450,该吸气管450向下弯折贯穿该灰渣堆积室180,该加热区110的侧壁而朝向该灰渣堆积室180;该原料经气化后即生成合成气及灰渣,该合成气由该合成气收集管400收集引导至另一个集气槽或净化槽等后续处理设施(图未绘出),其中有部分合成气经由该吸气管450以帮浦或加压设施451吸取再重新进入加热区110上方与逐步裂解所向上推挤的灰渣相对应处,将灰渣吹往灰渣堆积室180,令灰渣掉落其间堆积。经堆积后的灰渣达一定量时,灰渣堆积室180底部所设置的密闭阀181可开启,将所堆积的灰渣引导至其下方的缓冲室182,该缓冲室182亦为密闭空间,可设置真空井/泵,作为系统控氧环境的缓冲区,待灰渣进入缓冲室182达一定量时,设于缓冲
室182及灰渣堆积室180中间的密闭阀181则以手动或自动的方式闭合,如此即可保持系统不与外界的大气相通;待缓冲室182的灰渣达一定量时,则可将该灰渣引导至其下方的出渣室183,由出渣口184推出,作进一步的处理或利用。
84.此实施例主要概念为:输入该入料管220这种u型或ㄩ型连通管构造中的浓稠原料因为液态流体,可适当阻绝大气进入反应端及系统。在大气压力及自身的重量作用下,在入料端及反应端该呈流体态的原料均可呈现在同一水平位置;操作时,仅需由控制单元设定部分原料确实被推挤至该加热区110进行反应区段,即可启动高频加热机300对加热区110内的原料加热裂解,由于加热区110下方设置有降温区段111,其高温热能并不会全部传递至该入料管220内的原料,同时,在高温气化后的灰渣因该气化反应炉100顶部可设置有滤网(图未绘出),亦可避免灰渣掉回原料堆中;如此,本系统即可将原料以手动或自动的方式,经由入料控制阀820定时定量送入该入料管220,令左右两端的原料高度因连通管原理均维持在一定的平面,即可持续将原料推挤至加热区110段进行裂解气化处理。
85.本实施例充分利用油泥等原料的浓稠流体的特性,配合大气压力及重力,机械结构及动作甚少,但效益甚大,实为理想的发明创作。
86.请参阅图6,本实施例也是由下方向上方进料进行裂解反应处理的案例。其主要结构与图5的实施例相同,其差异点主要在于用输料泵221向油泥槽650吸取该原料,经由入料管222进入出料管223,该出料管223尾端向上弯折而起连接该气化反应炉100,该气化反应炉100自该出料管223连接端由下而上分段为降温区段111及加热区110;降温区段111以散热鳍片或水冷系统将原料冷却。其余结构与图5的实施例相同,在此不予赘述。
87.综观上述,本发明的油泥或废弃物的处理系统在设计上已迥异于传统的掩埋、焚烧,深具新颖性及进步性。利用本发明的处理系统,废弃物非但不再是废弃物,反而是摇身一变成为新的能源!如前所述,国际能源总署已经将人类文明所产生的废弃物定义为第四大能源;人类如果善加开发、利用此第四大能源,就可以逐渐减缓对自然资源的开发,不须再继续破坏地球及大自然了。发明人经实地打造原型机多次测试,均获得大量合成气,证明确实可行,且其机组的建造成本及操作、维护保养等费用,均远低于欧美、日本等先进国家刻正研发的“电浆气化”技术。高频加热技术问世二十多年来迄今已十分成熟,举凡微波炉、金属焊接、熔炉、表面硬化处理等,均已有广泛使用,且不乏专业书籍或文献,但不见于对废弃物气化处理的研究与实施;在此时空条件下,本发明的系统已足以建造为商业运作规模,实已具实用价值,应已符合国家专利的要件,故依法提出申请,敬请惠予审定核准,裨利尽早投产实施,为日益恶化的地球环境保护及促进循环经济,贡献棉薄之力,是所至盼。