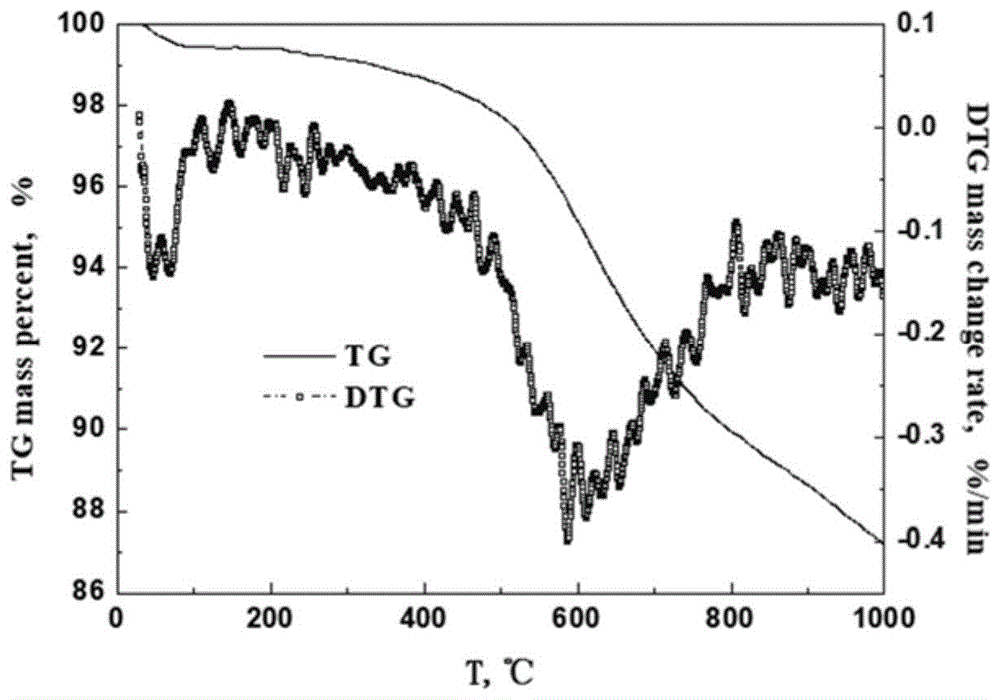
本发明属于煤层气分离处理
技术领域:
,具体涉及一种产出气或抽采煤层气co2分离提纯工艺。
背景技术:
:煤炭是我国的主体能源,在我国一次能源消费结构中占比59%左右。我国煤层气资源丰富,但利用程度较低,尤其是井下抽采的低浓度煤层气,大部分被直接排放到大气中。煤层气中甲烷是高热值碳能源,排空直接造成了巨大的能源浪费,并且由于甲烷也是一种温室效应显著的温室气体,其对臭氧层的破坏是二氧化碳的21倍,煤层气中大量甲烷若不能回收利用,直接排空将加速全球变暖,严重污染环境。自2011年以来,国家鼓励开发煤层气利用技术,要求煤矿企业势必提高煤层气抽采率和利用率。目前,煤矿企业煤层气利用率较低的原因主要在于煤层气中甲烷浓度较低,很难满足工业应用要求,亟需煤层气浓缩技术来实现低浓煤层气中甲烷的提取浓度。co2的捕集、利用与封存是一项新兴的具有大规模减排潜力的技术,可有效降低co2排放并提高其利用率,被认为是进行温室气体深度减排的重要技术路径之一。在co2资源化利用技术中,注co2驱替煤层气技术(co2-enhancedcoalbedmethanerecovery,co2-ecbm)被认为是一种具有较好发展前景的煤层气增产技术,通过向低渗透、压力衰竭或废弃深矿等煤系地层中注入co2,不仅可以提高煤层气采收率,还可实现co2的地下封存从而减少温室气体co2排放量。目前,co2-ecbm技术在世界各国还处于可行性和示范性研究阶段,中国、美国、加拿大、日本、欧盟等纷纷展开研究,并先后进行了不同规模的现场试验,同时也开展了大量基础试验研究。在国内的工程试验研究中发现,受不同地质条件影响,co2注入煤层后,有的需要很长时间co2才能穿透,有的则在短时间内就穿透并随着ch4一同析出。在煤层气排采过程中,若co2随着ch4一起排出,会影响煤层气的质量,势必需要经过脱co2处理后才可以输送至下游用户。目前,为了从产出气或抽采煤层气中分离co2,进而获得较高纯度的ch4,学者们已经研究了很多种ch4/co2分离方法,包括:多级洗涤法、化学吸收法、膜分离法和变压吸附法。其中,多级洗涤法、化学吸收法和膜分离法都是针对大规模抽采且二氧化碳含量低(<1%)的煤层气更为有效、更具有经济性,而变压吸附法则更具灵活性可处理不同规模的煤层气的脱碳分离,是最为合适的co2分离方法。但是,变压吸附分离煤层气中co2多以单一浓度为主,并且受原料气co2浓度波动影响很大,导致co2分离效率低,ch4回收率不高,尤其是吸附材料的性能更是ch4/co2混合气变压吸附分离技术的核心,即对高选择性吸附剂的选择至关重要,也是如何提高煤层气利用量和利用率的关键。目前,已知ch4/co2混合气体的分离用吸附材料包括金属有机骨架材料(mof)、5a/13x、zsm-5、活性炭和分子筛等;其中,沸石分子筛对ch4/co2的分离性能较低,mof材料展现出优越的二氧化碳吸附性能,吸附能力远高于传统吸附材料,但还处于实验室阶段,存在水热和化学稳定性不易控制等问题,5a/13x及其改性物对ch4/co2的分离性能较好,但实际应用较少。活性炭是一种炭质吸附剂,常被用作催化剂、催化剂载体、水处理和气相分离应用中。很多学者采用活性炭作为吸附剂进行ch4/co2分离研究,如李通等《活性炭改性及其对ch4/co2吸附性能的研究》中对煤质活性炭吸附剂进行酸碱改性和氧化改性,研究其对ch4/co2分离性能的影响,以nh3·h2o和h2o2改性后的活性炭吸附剂对co2吸附量分别增加了166%和137%,对co2/ch4的分离因子分别增加至6.3和5.87;ning等《adsorptionequilibriumofmethaneandcarbondioxideonmicrowave-activatedcarbon》通过金属浸渍微波椰壳活性炭的方法制得k2co3/mac吸附剂,提高了对co2的吸附能力,且分离因子达到7.42。可见,与5a/13x沸石分子筛相比,活性炭虽然分离选择性较低,但其具有吸附容量大、价格低廉,制备原料广泛等优点,具有巨大的开发应用潜力。技术实现要素:为此,本发明所要解决的技术问题在于提供一种产出气或抽采煤层气co2分离提纯工艺,以解决现有技术中产出气co2分离效率不理想的问题,进而高效、经济的将co2脱除得到纯度符合质量要求的煤层气,供给下游用户使用。为解决上述技术问题,本发明所述的一种产出气co2分离提纯工艺,包括如下步骤:(a)将产出气进行压缩,并将增压后的产出气进行净化,得到净化后的产出气;(b)将净化后的产出气进行变压吸附处理,以koh改性吸附剂进行脱除co2和ch4提纯,分别得到产品气和尾气。具体的,所述步骤(b)中,所述koh改性吸附剂按照如下方法制备:(1)取koh固体为改性剂加水配制得到koh水溶液,备用;另取椰壳炭化料粉碎,加入粘结剂以及所述koh水溶液混匀,并进行捏合成型,得到吸附剂料条,经风干后备用;(2)将步骤(1)处理后的所述吸附剂料条在保护气氛下进行炭化处理;(3)将步骤(2)处理后的吸附剂料条进行水蒸汽物理活化处理,冷却即得所需koh改性吸附剂。具体的,所述步骤(1)中,控制所述椰壳炭化料、粘结剂、koh改性剂和水的质量比为100:35-45:2-10:15-25,更优选质量比例为100:40:10:20。具体的,所述步骤(1)中,所述粘结剂包括高温煤焦油。具体的,所述步骤(1)中,还包括将所述椰壳炭化料粉碎至粒径150μm以下的步骤,优选为球磨机研磨处理。具体的,所述步骤(1)中,所述捏合成型步骤为在15-25mpa压力下、通过直径为3-5mm的模具进行挤压成型。具体的,所述步骤(2)中,控制所述炭化步骤的炭化温度为500-700℃,升温速率为3-8℃/min,炭化时间为5-15min,更优选升温速率为5℃/min,炭化温度为600℃,炭化10min。具体的,所述步骤(3)中,所述水蒸汽物理活化处理步骤中,控制水蒸气的体积流量为8-12ml/min,控制活化温度为750-900℃,活化时间为20-55min;优选的,控制水蒸气的体积流量为10ml/min,控制活化温度为800℃,活化时间为30min。具体的,所述步骤(b)中,控制所述变压吸附步骤温度为20-30℃,吸附时间90-210s,吸附压力0.4-0.7mpa。优选的,所述步骤(b)中,所述变压吸附步骤为两级变压吸附处理,即包括分离co2的一级变压吸附步骤,以及,提纯ch4的二级变压吸附步骤;所述一级变压吸附步骤中,控制吸附温度为20-30℃,吸附时间150-210s,吸附压力0.5-0.7mpa;优选吸附温度为20℃,吸附时间180s,吸附压力0.6mpa;所述二级变压吸附步骤中,控制吸附温度为20-30℃,吸附时间90-150s,吸附压力0.4-0.6mpa;优选吸附温度为20℃,吸附时间120s,吸附压力0.5mpa。具体的,所述步骤(b)中,所述变压吸附步骤中,控制所述koh改性吸附剂的堆比重为350-450g/l,优选400g/l。具体的,所述步骤(a)中,所述产出气中co2的体积百分含量为15-20%,并控制压缩后产出气的压力为0.5-0.7mpa。具体的,所述步骤(a)中,所述净化步骤包括经过滤器、冷干机和活性炭罐净化。本发明所述产出气co2分离提纯工艺,以产出气为原料,先进行压缩和净化处理,再根据气源co2浓度进行两级变压吸附处理,利用koh改性吸附剂对产出气中的co2进行分离,并使得ch4得到浓缩。该工艺中,仅使用一种koh改性吸附剂即可实现co2分离及ch4的浓缩,且分离效率更优,在co2驱煤层气利用中具有实际的应用指导意义。本发明所述koh改性吸附剂,以椰壳炭化料为基体原料,通过在捏合成型过程中以koh水溶液为改性剂,并进一步通过二次炭化及水蒸气活化处理工艺,制得改性ch4/co2分离用活性炭吸附剂对ch4和co2的饱和吸附量分别达到为2.34mmol/g和3.23mmol/g,平衡分离系数可达到10.27,较不改性条件下平衡分离系数提高了190%,可用于煤层气的分离处理,具有较高的应用价值和意义。附图说明为了使本发明的内容更容易被清楚的理解,下面根据本发明的具体实施例并结合附图,对本发明作进一步详细的说明,其中,图1为椰壳炭化料在n2气氛下热解(tg/dtg)曲线;图2为本发明产出气co2分离ch4提纯工艺的流程图。具体实施方式制备例本发明下述制备例中,所述椰壳炭化料为市售产品,也可以选用椰壳按照常规炭化方式进行处理。本发明下述制备例中,所述椰壳炭化料来源于东南亚,由天津光华晶科环保科技有限公司提供。所述椰壳炭化料和所述高温煤焦油的工业分析、元素分析或性质分析分别见表1-2所示。表1椰壳炭化料工业分析和元素分析注:d--干基;ad--空气干燥基;daf--干燥无灰基;氧含量通过差减法得到表2高温煤焦油性质分析制备例1本制备例所述用于分离甲烷/二氧化碳的改性椰壳基吸附剂,按照如下步骤制备:(1)按照10:20的质量比取koh固体加水配制得到koh水溶液作为改性剂,备用;另取所述椰壳炭化料通过球磨机研磨至150μm以下,并按照椰壳炭化料:高温煤焦油:koh固体:水=100:40:10:20的比例加入至捏合机中混合搅拌25min,之后将混合料加入四柱液压机,通过直径为4mm的模具在20mpa压力下进行挤压成型,将制备出的活性炭吸附剂料条在空气中自然风干2-3天,备用;(2)将晾晒后的活性炭吸附剂料条进行炭化工序,炭化设备为管式电加热炉,控制炭化升温速率为5℃/min,终温为600℃,恒温时间为10min,n2作为炭化过程中的保护气,流量为200ml/min;(3)将炭化后的活性炭吸附剂料条通过水蒸气物理活化法进行,活化设备为管式电加热炉,水蒸气体积流量为10ml/min,炭化料加入量为200g,活化恒温时间为30min,活化温度为800℃,活化之后经自然冷却,即得所需高性能co2/ch4分离专用椰壳基活性炭吸附剂样品。制备例2本制备例所述用于分离甲烷/二氧化碳的改性椰壳基吸附剂,按照如下步骤制备:(1)按照10:20的质量比取koh固体加水配制得到koh水溶液作为改性剂,备用;另取所述椰壳炭化料通过球磨机研磨至150μm以下,并按照椰壳炭化料:高温煤焦油:koh固体:水=100:40:10:20的比例加入至捏合机中混合搅拌25min,之后将混合料加入四柱液压机,通过直径为4mm的模具在20mpa压力下进行挤压成型,将制备出的活性炭吸附剂料条在空气中自然风干2-3天,备用;(2)将晾晒后的活性炭吸附剂料条进行炭化工序,炭化设备为管式电加热炉,控制炭化升温速率为5℃/min,终温为600℃,恒温时间为10min,n2作为炭化过程中的保护气,流量为200ml/min;(3)将炭化后的活性炭吸附剂料条通过水蒸气物理活化法进行,活化设备为管式电加热炉,水蒸气体积流量为10ml/min,炭化料加入量为200g,活化恒温时间为30min,活化温度为750℃,活化之后经自然冷却,即得所需高性能co2/ch4分离专用椰壳基活性炭吸附剂样品。制备例3本制备例所述用于分离甲烷/二氧化碳的改性椰壳基吸附剂,按照如下步骤制备:(1)按照10:20的质量比取koh固体加水配制得到koh水溶液作为改性剂,备用;另取所述椰壳炭化料通过球磨机研磨至150μm以下,并按照椰壳炭化料:高温煤焦油:koh固体:水=100:40:10:20的比例加入至捏合机中混合搅拌25min,之后将混合料加入四柱液压机,通过直径为4mm的模具在20mpa压力下进行挤压成型,将制备出的活性炭吸附剂料条在空气中自然风干2-3天,备用;(2)将晾晒后的活性炭吸附剂料条进行炭化工序,炭化设备为管式电加热炉,控制炭化升温速率为5℃/min,终温为600℃,恒温时间为10min,n2作为炭化过程中的保护气,流量为200ml/min;(3)将炭化后的活性炭吸附剂料条通过水蒸气物理活化法进行,活化设备为管式电加热炉,水蒸气体积流量为10ml/min,炭化料加入量为200g,活化恒温时间为30min,活化温度为850℃,活化之后经自然冷却,即得所需高性能co2/ch4分离专用椰壳基活性炭吸附剂样品。制备例4本制备例所述用于分离甲烷/二氧化碳的改性椰壳基吸附剂,按照如下步骤制备:(1)按照10:20的质量比取koh固体加水配制得到koh水溶液作为改性剂,备用;另取所述椰壳炭化料通过球磨机研磨至150μm以下,并按照椰壳炭化料:高温煤焦油:koh固体:水=100:40:10:20的比例加入至捏合机中混合搅拌25min,之后将混合料加入四柱液压机,通过直径为4mm的模具在20mpa压力下进行挤压成型,将制备出的活性炭吸附剂料条在空气中自然风干2-3天,备用;(2)将晾晒后的活性炭吸附剂料条进行炭化工序,炭化设备为管式电加热炉,控制炭化升温速率为5℃/min,终温为600℃,恒温时间为10min,n2作为炭化过程中的保护气,流量为200ml/min;(3)将炭化后的活性炭吸附剂料条通过水蒸气物理活化法进行,活化设备为管式电加热炉,水蒸气体积流量为10ml/min,炭化料加入量为200g,活化恒温时间为35min,活化温度为800℃,活化之后经自然冷却,即得所需高性能co2/ch4分离专用椰壳基活性炭吸附剂样品。制备例5本制备例所述用于分离甲烷/二氧化碳的改性椰壳基吸附剂,按照如下步骤制备:(1)按照10:20的质量比取koh固体加水配制得到koh水溶液作为改性剂,备用;另取所述椰壳炭化料通过球磨机研磨至150μm以下,并按照椰壳炭化料:高温煤焦油:koh固体:水=100:40:10:20的比例加入至捏合机中混合搅拌25min,之后将混合料加入四柱液压机,通过直径为4mm的模具在20mpa压力下进行挤压成型,将制备出的活性炭吸附剂料条在空气中自然风干2-3天,备用;(2)将晾晒后的活性炭吸附剂料条进行炭化工序,炭化设备为管式电加热炉,控制炭化升温速率为5℃/min,终温为600℃,恒温时间为10min,n2作为炭化过程中的保护气,流量为200ml/min;(3)将炭化后的活性炭吸附剂料条通过水蒸气物理活化法进行,活化设备为管式电加热炉,水蒸气体积流量为10ml/min,炭化料加入量为200g,活化恒温时间为40min,活化温度为800℃,活化之后经自然冷却,即得所需高性能co2/ch4分离专用椰壳基活性炭吸附剂样品。对比制备例1本对比制备例所述椰壳基吸附剂的制备方法同实施例1,其区别仅在于,在进行捏合成型步骤中,不添加所述koh溶液。对比制备例2本对比制备例为采用现有技术中国专利cn108057420a方案实施例1中方法制得的吸附剂。对比制备例3本对比制备例为采用现有技术中国专利cn105293491a方案实施例3中方法制得的吸附剂。对比制备例4本对比制备例所述椰壳基吸附剂的制备方法同实施例1,其区别仅在于,在进行捏合成型步骤中,不添加所述koh,而是在炭化步骤后将所得吸附剂料条置于10wt%koh溶液中浸渍6h,并于120℃进行烘干后再进行相应的活化处理。对比制备例5本对比制备例所述椰壳基吸附剂的制备方法同实施例1,其区别仅在于,所述koh以固体形态经快速研磨后与所述椰壳炭化料混合均匀,并置于n2氛围中于900℃活化60min,经洗涤、烘干后,加入相同量的高温煤焦油混匀并进行捏合成型,随后进行相应的炭化及活化处理。实验例1、热重对本制备例选取的椰壳炭化料的热重分析通过热重分析仪(sta409pg,netzsch)进行,测试气氛为n2,n2流速为60ml/min,升温范围为室温至1000℃,升温速率为5℃/min,样品用量为20mg。椰壳炭化料在n2气氛下热解(tg/dtg)曲线如图1所示。从图1中dtg可看出:椰壳炭化料热解在90℃左右出现失重峰,这主要是椰壳炭化料中水的存在引起的;椰壳炭化料在600℃时失重最明显,这主要是分解缩聚反应引起的。由图1所示tg曲线可知,椰壳炭化料500℃时失重开始明显,600℃时炭化料的质量分数为95%,由此可知椰壳炭化料炭化较为充分,挥发分大部分已热解析出。因此,为保证焦油和挥发气体的析出,本发明方案的炭化温度设定为500-700℃。本发明制备例1-5中方案,经炭化处理后计算所得炭化料得率为69.5-70.5%。2、吸附剂得率和碘值吸附剂得率的高低不仅与原料中挥发分的含量有关,同时也跟碳烧失率有很大关系,因此,吸附剂得率直接反映生产活性炭吸附剂产品原料的适宜性。碘值是展示活性炭吸附剂吸附能力的指标之一,碘值高低与活性炭吸附剂中微孔的多少有很大的关联性,碘值越高,则吸附性能越强。表3为制备例1-5及对比制备例1-5中方案对吸附剂得率及碘值的影响。可见,本发明方案下制得吸附剂的吸附剂得率和碘值均较优。表3吸附剂得率和碘值结果编号活化温度/℃添加剂量/%活化时间/min得率/%碘值/mg.g-1制备例1800103055.5894制备例2750103064839制备例3850103045.2838制备例4800103549.9968制备例5800104039.11000对比制备例180003076.53830对比制备例2800/3057.5800对比制备例3800/6056.8815对比制备例4800/3058.2789对比制备例5800/3057.58023、平衡分离系数分别测定制备例1-5及对比制备例1-5中方案下制备的吸附剂在298k和0-0.1mpa时co2/ch4两种单组份气体在活性炭吸附剂上的吸附等温线,以表征对ch4和co2变压吸附的影响。结果显示,本发明方案下制得吸附剂,根据iupac的定义,吸附等温线属于典型ⅰ型吸附等温线,可以采用langmuir方程对吸附等温线进行拟合。吸附剂的分离性能一般可考虑从两个方面进行评价:对不同气体组分的分离选择性和对气体的吸附量。平衡分离系数是一种评价吸附剂分离性能的重要指标,对吸附剂选择和评价有非常重要的意义,分离系数的大小可表征吸附剂分离混合气体组分的能力,系数越大,则分离性能越好。本实验中主要通过平衡分离系数来表征及评价吸附剂的吸附分离性能。co2和ch4在活性炭吸附剂样品上的吸附平衡等温线的测定采用美国康塔公司生产的全自动物理/化学吸附分析仪(autosorb-1c),该吸附基于体积法进行测量。采用langmuir方程,通过origin软件对吸附等温线数据进行拟合计算,可分别得到co2和ch4的qm(单层饱和吸附量)和k(langmuir吸附平衡常数),并通过式(1)可计算得到活性炭吸附剂对co2/ch4的平衡分离系数α,α计算公式如下:式中,qm为单层饱和吸附量,mol/kg;k为langmuir吸附平衡常数;ɑ为平衡分离系数。采用langmuir方程分别对上述各等温变压吸附线进行拟合,拟合数据结果及co2/ch4平衡分离系数计算结果见下表4所示。由表3可看出,ch4和co2线性相关系数r均大于0.97,拟合度较高,说明拟合理论模型选择正确。表4制备的吸附剂的吸附等温线拟合数据及co2/ch4平衡分离系数由表4中数据可看出,本发明方案下制得吸附剂的co2/ch4平衡分离系数较优。综上,本发明以椰壳炭化料为原料,采用水蒸气活化工艺,通过改性制备ch4/co2分离用活性炭吸附剂,其平衡分离系数可达到10.27,较不改性条件下平衡分离系数提高了190%。实施例本发明下述实施例中,所述净化步骤包括经过滤器、冷干机和活性炭罐净化。所述过滤器、冷干机为通用设备,可从公开商业途径购买得到,上述设备可根据实际气体处理量进行选择,所述活性炭罐装填的活性炭,其堆比重为400-500g/l,可从公开商业途径购买得到,该活性炭的处理气体量可根据实际的气体处理量进行选择,该步骤是为了除去气体中含有的尘、水和油,以达到净化煤层气的目的。本发明下述实施例中,所述co2分离和ch4提纯处理步骤均是在常规六塔真空吸附塔中进行。本发明下述实施例中,采用红外分析方法测定二氧化碳和甲烷含量,甲烷的回收率按照如下公式进行计算:甲烷回收率=(回收的甲烷量/原料气中甲烷的量)×100%。实施例1如图2所示的工艺流程图,本实施例所述产出气co2分离提纯工艺,对co2含量为15%的产出气进行分离提纯,所述原料气各组分的名称及体积百分含量分别如下所示:co215.0%、ch485.0%,气体压力0.2mpa;具体包括如下步骤:(a)将作为原料气的产出气进行压缩,得到压缩后的产出气,控制该压缩后的产出气的压力为0.65mpa;并将所得压缩后的产出气经过滤器除尘,冷干机除水,最后经活性炭罐除油,得到净化后的产出气;其中,活性炭罐中的活性炭堆比重为500g/l;(b)将得到的净化后的产出气通入六塔真空吸附塔进行变压吸附处理,所述吸附塔的内径为100mm,co2分离中所用吸附剂为前述制备例4中所得椰壳活性炭,控制吸附温度为20℃,吸附时间为180s,吸附压力为0.6mpa;分别得到co2分离浓缩气和co2分离尾气;经检测,co2分离尾气各组分的名称及体积百分含量分别如下所示:co236.0%、ch464.0%,气体压力0.05mpa;(c)将得到的co2分离尾气进行再次压缩,得到压缩后的co2分离尾气,该压缩后的co2分离尾气的压力为0.55mpa;并将所得压缩后的co2分离尾气经过滤器除尘,冷干机除水,最后经活性炭罐除油,得到净化后的产出气;其中,活性炭罐中的活性炭堆比重为500g/l;(d)将得到的净化后的产出气通入六塔真空吸附塔进行变压吸附处理,所述吸附塔的内径为100mm,co2分离中所用吸附剂为前述制备例4中所得椰壳活性炭,控制吸附温度为20℃,吸附时间为120s,吸附压力为0.5mpa;分别得到ch4提纯浓缩气和ch4提纯尾气;(e)将步骤(b)得到的co2分离浓缩气和步骤(d)得到的ch4提纯浓缩气进行混合处理得到最终产品气,而变压吸附ch4提纯产生的尾气则排空处理。利用红外分析方法对产品气中的二氧化碳和甲烷含量进行测定,其中,各组分名称及体积百分含量分别为:ch499.5%、co20.5%,计算甲烷回收率为92.5%。实施例2如图2所示的工艺流程图,本实施例所述产出气co2分离提纯工艺,对co2含量为20%的产出气进行分离提纯,所述原料气各组分的名称及体积百分含量分别如下所示:co220.0%、ch480.0%,气体压力0.2mpa;具体包括如下步骤:(a)将作为原料气的产出气进行压缩,得到压缩后的产出气,控制该压缩后的产出气的压力为0.65mpa;并所得压缩后的产出气经过滤器除尘,冷干机除水,最后经活性炭罐除油,得到净化后的产出气;其中,活性炭罐中的活性炭堆比重为500g/l;(b)将得到的净化后的产出气通入六塔真空吸附塔进行变压吸附处理,所述吸附塔的内径为100mm,co2分离中所用吸附剂为前述制备例4中所得椰壳活性炭,控制吸附温度为20℃,吸附时间为180s,吸附压力为0.6mpa;分别得到co2分离浓缩气和co2分离尾气;经检测,co2分离尾气各组分的名称及体积百分含量分别如下所示:co248.0%、ch452.0%,气体压力0.05mpa;(c)将得到的co2分离尾气进行再次压缩,得到压缩后的co2分离尾气,该压缩后的co2分离尾气的压力为0.55mpa;并将所得压缩后的co2分离尾气经过滤器除尘,冷干机除水,最后经活性炭罐除油,得到净化后的产出气;其中,活性炭罐中的活性炭堆比重为500g/l;(d)将得到的净化后的产出气通入六塔真空吸附塔进行变压吸附处理,所述吸附塔的内径为100mm,co2分离中所用吸附剂为前述制备例4中所得椰壳活性炭,控制吸附温度为20℃,吸附时间为120s,吸附压力为0.5mpa;分别得到ch4提纯浓缩气和ch4提纯尾气;(e)将步骤(b)得到的co2分离浓缩气和步骤(d)得到的ch4提纯浓缩气进行混合处理得到最终产品气,而变压吸附ch4提纯产生的尾气则排空处理。利用红外分析方法对产品气中的二氧化碳和甲烷含量进行测定,其中,各组分名称及体积百分含量分别为:ch499.0%、co21.0%,计算甲烷回收率为90.2%。显然,上述实施例仅仅是为清楚地说明所作的举例,而并非对实施方式的限定。对于所属领域的普通技术人员来说,在上述说明的基础上还可以做出其它不同形式的变化或变动。这里无需也无法对所有的实施方式予以穷举。而由此所引伸出的显而易见的变化或变动仍处于本发明创造的保护范围之中。当前第1页12