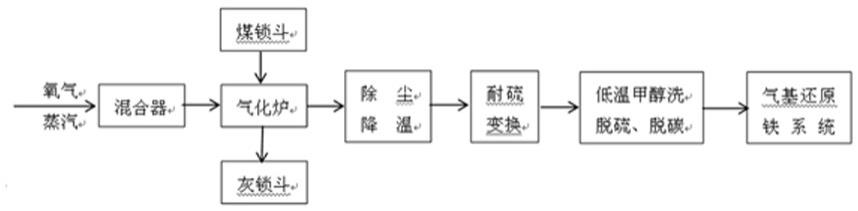
[0001]
本发明属于气基直接还原铁系统所用还原气的制备技术领域,具体涉及一种利用无烟煤为气基直接还原铁系统制还原气的方法。
背景技术:[0002]
气基直接还原铁系统是采用气体作还原剂进行炼铁的工艺,还原气主要成分为h2和co,co+h2>90%、氢碳比1.5~2.0。由于气基直接还原法炼铁具有低碳、环保、产品质量高等优点,是当今世界最先进和最有前景的炼铁工艺技术之一。目前,世界上气基还原炼铁采用最多的还原气为天然气。中国“富煤、贫油、少气”的资源特点,决定了不可能大力发展以天然气为气源的直接还原铁技术,这也是限制该炼铁工艺在中国发展的主要原因之一。因此,经济、有效的还原气制备方法是气基直接还原法炼铁的主要研究内容之一。
技术实现要素:[0003]
本发明针对由于天然气资源紧缺而限制了气基直接还原法炼铁工艺发展的问题,提供一种以无烟煤为原料、以加压移动床为气化工艺制备还原气的方法,具有原料丰富、单炉产气量适中、占地少、环保性好、气体氢碳比可调等优势,可替代天然气为气基直接还原铁系统提供还原气,具有广阔的前景。
[0004]
本发明采用如下技术方案:一种利用无烟煤为气基直接还原铁系统制还原气的方法,加压移动床气化装置运行时,将无烟煤原料从气化炉顶经煤仓加入,原料自上而下移动,依次经历干燥层、干馏层、还原层、氧化层和灰层,与气化炉底通入的气化剂逆向接触并发生反应,具体包括如下步骤:第一步,加压移动床气化装置运行时,将无烟煤原料从气化炉顶经煤仓加入,原料自上而下移动,依次经历干燥层、干馏层、还原层、氧化层和灰层,与气化炉底通入的气化剂逆向接触并发生反应;第二步,加压移动床气化工艺所用气化剂由纯氧和蒸汽管网的中压蒸汽混合组成,由气化炉底部通入,首先与灰层交换热量,然后进入氧化层与炽热煤层接触发生氧化燃烧反应,生成二氧化碳,在此气体温度升至1200℃;反应后的气体向上进入还原层,co2和水蒸汽与无烟煤发生还原反应,生成co和h2,此反应为吸热反应,使气体温度由1200℃迅速下降到800℃;气体再向上进入干馏层和干燥层,与气化炉顶加入的无烟煤接触并进行热量交换,然后携带没有反应的水蒸汽、燃料中干馏逸出的挥发分、蒸发的水分一起到达气化炉顶部的出口,此时气体温度约500~600℃;第三步,从气化炉顶部出口的气体为粗还原气,经旋风分离器除尘后,通过文丘里和洗涤塔进行进一步的降温除尘,温度降至200-300℃;第四步,经除尘降温的粗还原气与外加饱和蒸汽混合后,通过耐硫变换装置调节氢碳比至1.5~2.0;第五步,变换后的气体通过低温甲醇洗吸收塔,脱出粗还原气中的有害组分h2s以及大
部分的co2气体,即得到最终的还原气,将其送往气基还原铁系统。
[0005]
第一步中所述无烟煤的粒径为6-50mm,收到基灰分含量为12-14%,收到基固定碳含量为71-74%,收到基挥发分含量为6-8%,收到基水分含量为6%,收到基全硫含量小于0.5%、软化温度大于1500 ℃、抗碎强度大于90%、热稳定性大于90%。
[0006]
第一步中所述加压移动床气化装置由具有内件和夹套的气化炉组成,加煤用煤锁,排灰用灰锁,煤锁和灰锁均直接与气化炉连接,气化炉压力为0.5-4mpa。
[0007]
第二步中所述纯氧浓度大于99%,蒸汽由夹套自产饱和蒸汽和蒸汽管网送来的过热蒸汽两部分混合组成。
[0008]
第三步中所述粗还原气包括如下体积百分比的组份:co:29~32%、h2:40~42%、ch4:1.5~8%、co2:14~23%、n2:0.1~0.2%、h2s:0.1~0.2%和o
2 :0.1~0.2%。
[0009]
第五步中所述最终的还原气的组份包括co、h2和h2s,其中co+h2>90%,氢碳比1.5-2,h2s含量小于1ppm。
[0010]
本发明的有益效果如下:1. 将煤气化和炼铁工艺结合起来,可促进国内气基直接还原铁工艺的发展。
[0011]
世界上一般以天然气为原料制还原气,国内由于天然气的紧缺限制了气基直接还原法炼铁工艺的发展,该工艺以国内先进的煤气化工艺为基础,以国内丰富的煤炭资源为原料生产还原气,有利于促进气基直接还原铁工艺在国内的发展。
[0012]
2. 该工艺投资小,制还原气成本低。
[0013]
与天然气和电解水制还原气相比,加压移动床气化工艺制取还原气的成本较低;与新型气流床气化工艺相比,该工艺规模较小,投资较低,更适合与规模不太大的主流的气基还原铁系统匹配。
[0014]
3. 废水处理难度大幅降低,更加节能环保。
[0015]
加压移动床系统制备还原气,由于气化温度相对较低,水洗单元相对复杂,但若以无烟煤为原料,由于其煤化程度最高,气体组分中夹带的杂质很少,污水处理单元设计规模大幅降低,更加节能、环保。
附图说明
[0016]
图1为本发明的方法流程图。
具体实施方式
[0017]
一种利用无烟煤为气基直接还原铁系统制还原气的方法,加压移动床气化装置运行时,将无烟煤原料从气化炉顶经煤仓加入,原料自上而下移动,依次经历干燥层、干馏层、还原层、氧化层和灰层,与气化炉底通入的气化剂逆向接触并发生反应,具体包括如下步骤:第一步,加压移动床气化装置运行时,将无烟煤原料从气化炉顶经煤仓加入,原料自上而下移动,依次经历干燥层、干馏层、还原层、氧化层和灰层,与气化炉底通入的气化剂逆向接触并发生反应;第二步,加压移动床气化工艺所用气化剂由纯氧和蒸汽管网的中压蒸汽混合组成,由气化炉底部通入,首先与灰层交换热量,然后进入氧化层与炽热煤层接触发生氧化燃烧反
应,生成二氧化碳,在此气体温度升至1200℃;反应后的气体向上进入还原层,co2和水蒸汽与无烟煤发生还原反应,生成co和h2,此反应为吸热反应,使气体温度由1200℃迅速下降到800℃;气体再向上进入干馏层和干燥层,与气化炉顶加入的无烟煤接触并进行热量交换,然后携带没有反应的水蒸汽、燃料中干馏逸出的挥发分、蒸发的水分一起到达气化炉顶部的出口,此时气体温度约500~600℃;第三步,从气化炉顶部出口的气体为粗还原气,经旋风分离器除尘后,通过文丘里和洗涤塔进行进一步的降温除尘,温度降至200-300℃;第四步,经除尘降温的粗还原气与外加饱和蒸汽混合后,通过耐硫变换装置调节氢碳比至1.5~2.0;第五步,变换后的气体通过低温甲醇洗吸收塔,脱出粗还原气中的有害组分h2s以及大部分的co2气体,即得到最终的还原气,将其送往气基还原铁系统。
实施例
[0018]
将粒径6~50 mm、收到基灰分含量12~14%、收到基固定碳含量71~74%、收到基挥发分含量6~8%、收到基水分含量6%、收到基全硫含量小于0.5%、软化温度(t2)大于1500 ℃、抗碎强度大于90%、热稳定性大于90%的无烟煤通过常压煤仓、煤锁加压后进入气化炉,气化炉压力2.5 mpa,单炉投煤量15 t/h。
[0019]
气化剂氧气6900 nm3/h(99.6%,2.6 mpa)和蒸汽25.5t/h(270 ℃,2.6 mpa),经过混合后从底部进入气化炉,与煤逆向接触发生氧化还原反应。粗还原气从气化炉上部排出,单炉产气量为35000nm3/h,压力2.3 mpa,温度520 ℃,各组分的体积百分比为:co 31%、h
2 42%、ch
4 5%、co
2 21%、n
2 0.14%、h2s 0.16%、其他 0.7%,粗还原气经旋风分离器进行除尘后,通过文丘里和洗涤塔进行进一步的降温除尘,温度降至260℃左右。
[0020]
经除尘降温的粗还原气与外加饱和蒸汽(2.3 mpa、21000 nm3/h)混合后,在耐硫变换炉中发生变换反应,将氢碳比调节为2:1,即:co 23.6%、h
2 45.3%、ch
4 4.7%、co
2 25.5%、n
2 0.13%、h2s 0.15%、其他 0.62%。
[0021]
变换后的气体通过低温甲醇洗吸收塔,吸收其中的h2s和co2气体,将h2s含量降至1 ppm以下后,即得到最终的还原气(各组分的体积百分比为:co30.5%、h
2 58.5%、ch
4 5%、co
2 <3%、h2s <1ppm、其他 3%),送往气基还原铁系统。