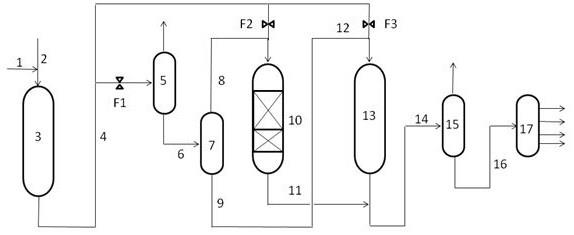
1.本发明涉及一种加氢装置,所述加氢装置能够灵活加工多种原料;此外本发明还涉及一种加氢方法,具体地说涉及一种有利于提高液收,增产柴油产品并提高柴油产品低温流动性加氢方法。
背景技术:2.随着炼化企业的规模扩大,加氢裂化装置逐渐大型化,加氢裂化装置处理的原料越来越复杂和多样化。随着油品市场需求的变化,柴油的需求量逐步降低,而航煤的需求量增长较快,加氢裂化掺炼柴油增产航煤越来越常见。
3.美国专利us4172815公开了一种同时生产喷气燃料和柴油的单段循环加氢裂化方法,其工艺流程为:重质原料油经过加氢裂化后,其产品经过分馏,得到喷气燃料馏分、柴油馏分和尾油;喷气燃料馏分全部或部分与尾油混合,送回加氢裂化反应器。此工艺流程明显的缺点是喷气燃料再进行加氢裂化,虽然提高了喷气燃料的质量,但喷气燃料收率降低、总氢耗和投资增加较多。
4.cn200610008416.3公开了一种并列式加氢裂化方法,该方法将重质馏分油和劣质催化裂化柴油分别加氢裂化,所得的裂化产物混合后进行气液分离,所得的液相经分馏得到轻石脑油、重石脑油、航煤、柴油和尾油,该方法有效转化催化柴油,但需要两套加氢预处理及加氢裂化反应器,设备投资较高,操作难度大。
5.us4789457、us4919789将重质原料进行催化裂化,以催化裂化轻循环油为原料,采用中压加氢裂化直接生产汽油。us4426276将原油重质馏分进行催化裂化处理,催化裂化轻循环油和重循环油与直馏中间馏分油(直馏柴油)混合进行加氢裂化。这些技术的主要不足在于加氢裂化的原料仅为中间馏分,重质馏分全部进行催化裂化处理,从而没有充分发挥加氢裂化的加氢性能优势。重质馏分全部进行催化裂化处理,必然有较多不能利用的油浆外排,不能充分利用石油资源。
6.cn201710304435.9公开了一种掺炼柴油的加氢裂化方法,柴油和减压蜡油与氢气混合进入加氢裂化反应器在加氢裂化催化剂的作用下进行加氢裂化反应,所述加氢裂化催化剂中所含的y分子筛的孔径按物流方向呈降低趋势,该方法能大幅度的提高重石脑油收率,改善中间馏分油性质。但该方法减压蜡油与柴油的比例范围较窄,柴油存在过度裂化。
7.现有技术中,加氢裂化装置同时处理vgo与柴油的过程中,由于vgo与柴油组成不同,同时处理会造成能耗增加,液收较低,柴油过度裂化等问题。
技术实现要素:8.针对现有技术的不足,本发明提供一种加氢装置,所述加氢装置能够处理多种原料。此外本发明还提供一种提高液收及产品质量的不同原料的加氢方法。该方法充分利用不同原料的特点,选择性进行加氢裂化和/或临氢降凝,提高装置液收与柴油收率,提高柴油产品低温流动性,加工原料中蜡油与柴油的比例范围更大。
9.一种加氢装置,所述加氢装置包括加氢预处理反应器,临氢降凝反应器、加氢裂化反应器、高温高压分离器、高温低压分离器,所述加氢预处理反应器的塔底出口同高温高压分离器的入口通过管线相连通,所述高温高压分离器的液相出口同高温低压分离的入口通过管线相连通,所述高温低压分离器的液相出口同加氢裂化反应器的塔顶入口通过管线相连通,所所述高温低压分离器的气相出口同临氢降凝反应器的塔顶入口通过管线相连通,所述临氢降凝反应器、加氢裂化反应器的塔底出口通过管线同分离系统相连通。
10.本发明上下文中,所述的连通包括含有阀门的情形,也就是说管线上设置阀门,阀门控制物流的流通也视为连通。
11.上述加氢装置中,所述加氢预处理反应器的塔底出口同高温高压分离器的入口通过管线相连通,所述管线上设置阀门f1控制物流是否进入高温高压分离器。
12.上述加氢装置中,所述加氢预处理反应器的塔底出口也可以同临氢降凝反应器或者加氢裂化反应器的塔顶入口通过管线直接相连通,管线上设置阀门f2、f3控制物流是否进入临氢降凝反应器或者加氢裂化反应器。所述阀门的位置本领域技术人员可以根据实际情况进行设置,所述阀门之间不能不能互相影响,最好是处于并联状态。
13.上述加氢装置中,所述临氢降凝反应器、加氢裂化反应器的塔底出口通过管线气液分离单元的入口相连通,所述气液分离单元的液相出口同分馏单元相连通。
14.一种加氢方法,所述方法采用上述的加氢装置,以蜡油和/或柴油为原料,当采用蜡油和柴油混合原料时,加氢方法包括如下过程:
15.(1)阀门f1打开,f2及f3关闭,混合原料油与氢气混合后,在加氢裂化预处理条件下进入加氢裂化预处理反应器,通过加氢裂化预处理催化剂床层,反应流出物不经换热直接进入高温高压分离器进行分离,得到气相和液相,气相包括氢气、轻烃组分、硫化氢和少量氨气,液相为加氢裂化预精制油;
16.(2)步骤(1)得到的加氢裂化预精制油进入高温常压分离器,得到气相和液相,气相为柴油及石脑油组成的轻馏分,液相为重馏分,气相经分离后得到的富氢气体循环使用;
17.(3)步骤(2)得到的轻馏分进入柴油临氢降凝反应器,经过临氢降凝催化剂床层,得到临氢降凝流出物i;
18.(4)步骤(2)得到的重馏分在蜡油加氢裂化条件下进入蜡油加氢裂化反应器,经过加氢裂化催化剂床层,得到裂化流出物ii;
19.(5)步骤(3)得到的临氢降凝流出物i与步骤(4)得到的裂化流出物ii混合后依次进入分离和分馏系统得到石脑油、航煤、柴油、尾油等产品。
20.当采用柴油为原料时,加氢方法包括如下过程:f1及f3关闭,f2打开,原料油与氢气混合后,在加氢裂化预处理条件下进入加氢裂化预处理反应器,通过加氢裂化预处理催化剂床层,反应流出物在柴油加氢裂化条件下进入临氢降凝反应器,得到临氢降凝流出物依次进入分离和分馏系统得到石脑油、航煤、柴油等产品;
21.当采用蜡油为原料时,加氢方法包括如下过程:f1及f2关闭,f3打开,原料油与氢气混合后,在加氢裂化预处理条件下进入加氢裂化预处理反应器,通过加氢裂化预处理催化剂床层,反应流出物在蜡油加氢裂化条件下进入蜡油加氢裂化反应器,通过加氢裂化催化剂床层,得到裂化流出物依次进入分离和分馏系统得到石脑油、航煤、柴油、尾油等产品。
22.上述方法中,所述的蜡油为减压蜡油,所述的柴油为直馏柴油,所述的混合原料为
减压蜡油如伊朗vgo、沙特vgo、科威特vgo等中的一种或者几种与直馏柴油的混合原料,混合原料中减压蜡油质量含量为10%~90%,优选20~80%,进一步优选32~65%。所述的直馏柴油原料为各种类型原油经常规常压塔而获得的柴油馏分,是初馏点220℃、干点380℃范围内的任意馏分,其初馏点一般为290~340℃,干点一般为330~380℃,氮含量一般<100μg/g,硫含量》2000μg/g,直馏柴油原料的链烷烃质量含量一般为30%~60%,优选为35%~55%。直馏柴油原料的芳烃质量含量一般10%~35%,优选为15%~30%,所述减压蜡油的性质如下:馏程350~550℃,优选360~520℃,密度:0.85~1.02g/cm3,硫含量:0.1~0.5wt%,氮含量:500~5000ppm。
23.上述方法中,所述的加氢裂化预处理条件为,反应压力5.0~20.0mpa,优选为7.0mpa~16.0mpa;平均反应温度为300℃~450℃,优选为330℃~400℃;体积空速0.1~6.0h-1,优选为0.5~3.0h-1;氢油体积比200∶1~2000∶1,优选为300∶1~1500∶1。
24.上述方法中,所述的加氢裂化预处理催化剂为常规加氢处理催化剂,可以是各商业催化剂,如大连(抚顺)石油化工研究院(fripp)研制生产的3996、ff-14、ff-16、ff-18、ff-26、ff-36、ff-46、ff-56、ff-56等裂化预处理催化剂,法国石油公司(ifp)的hr-416、hr-448等催化剂,托普索公司(topsor)的tk-525、tk-557催化剂,阿克佐(akzo)的kf-752、kf-840、kf-901、kf-907等。上述加氢裂化预处理催化剂也可以按本领域知识进行制备,普通加氢处理催化剂(负载型催化剂,活性金属含量相对较低,一般以氧化物计为20%~45%)一般先制备催化剂载体,然后用浸渍法负载活性金属组分。
25.上述方法中,所述的高温高压分离器控制条件如下:温度为320℃~400℃,优选340℃~370℃,压力为3.0~16.0mpa,优选为6.0mpa~12.0mpa。
26.上述方法中,所述的高温常压分离器控制条件如下:温度为320℃~400℃,优选340℃~370℃,压力为常压。
27.上述方法中,所述临氢降凝反应器操作条件如下:反应压力6.0~20.0mpa,氢油体积比200:1~1500:1,体积空速为0.1~10.0h-1
,反应温度260℃~455℃;优选操作条件为反应压力7.0~15.0mpa,氢油体积比300:1~1000:1,体积空速0.3~8.0h-1
,反应温度310℃~410℃。
28.上述方法中,所述述临氢降凝反应器装填的临氢降凝催化剂,含有zsm-5分子筛20~80%,优选为30~70%,含有以氧化物计的第viii族金属5~20%,优选8~15%,所述第viii族金属为钴和/或镍。
29.上述方法中,所述临氢降凝反应器装填的临氢降凝催化剂中所含有的zsm-5分子筛沿物流方向其总酸含量呈增加趋势、非骨架铝占比呈降低趋势。
30.上述方法中,所述临氢降凝反应器装填的临氢降凝催化剂中所含有的zsm-5分子筛沿物流方向其比表面积呈降低趋势。
31.上述方法中,所述临氢降凝反应器装填的临氢降凝催化剂中所含有的zsm-5分子筛沿物流方向其孔体积呈降低趋势。
32.上述临氢降凝方法中,所述临氢降凝反应区依次装填临氢降凝催化剂a、临氢降凝催化剂b,所述临氢降凝催化剂a中含有的zsm-5分子筛记为a1,所述a1的比表面积为350~500m2/g,350~500m2/g,优选400~450m2/g,孔体积为0.38~0.50cm3/g,优选0.40~0.45cm3/g,总酸含量1.6~2.7mmol/g,优选2.0~2.5mmol/g,弱酸含量0.8~1.4mmol/g,优
选1.0~1.2mmol/g,非骨架铝占比6%~12%,优选8%~10%,负载氧化硅的含量为0.02~0.7wt%,优选0.04~0.06wt%。所述临氢降凝催化剂b中含有的zsm-5分子筛记为b1,所述b1的比表面积为250~340m2/g,优选为280~330m2/g,孔体积为0.25~0.37cm3/g,优选为0.30~0.35cm3/g,总酸含量2.8~3.6mmol/g,优选为3.2~3.5mmol/g,弱酸含量为1.5~2.2mmol/g,优选1.7~2.0mmol/g,非骨架铝占比2%~5%,优选为2%~3%,负载氧化硅的含量为0.08~0.3wt%,优选0.1~0.2wt%。
33.上述临氢降凝方法中,所述临氢降凝催化剂a、临氢降凝催化剂b的装填体积比为1:9~9:1,优选4:6~6:4。
34.上述临氢降凝方法中,所述记为a1的zsm-5分子筛的制备方法,包括如下步骤:
35.(1)对zsm-5分子筛进行溶硅处理;
36.(2)对步骤(1)的物料进行脱铝处理;
37.(3)采用酸性缓冲溶液浸渍处理步骤(2)的物料;
38.(4)步骤(3)的物料负载氨基硅油,经干燥、焙烧后得到最终用于临氢降凝的改性zsm-5分子筛。
39.本发明方法中,步骤(1)中所述zsm-5分子筛可以采用市售商品或者按照现有技术制备。例如采用如下方法制备:将一定量的氧氧化钠、去离子水、偏铝酸钠、硅胶、模板剂(tpa2o)混合,各物料摩尔比为:(25~300)sio2:1al2o3:tpa2o:(0.01~10)na2o:(100~1100)h2o;将混合好的物料转入不锈钢晶化釜内,在一定温度下晶化;晶化结束后,将混合物产物以去离子水洗涤至ph值为7-8;将所得样品110℃烘干,研磨。
40.本发明方法中,步骤(1)中所述脱硅处理可以采用naoh、季铵盐以及季铵盐保护下的naoh处理的一种或几种。
41.本发明方法中,步骤(1)中所述脱硅处理采用碱处理,碱处理过程如下:zsm-5分子筛置于oh-含量为0.1~1.0mol/l的碱溶液中搅拌0.5h~2h,液固体积比以ml/g计为(6~10):1,处理后进行过滤,并重复此过程2~4次;然后换用去离子水洗涤1~5次至碱金属离子含量低于0.1wt%,干燥后得到碱改性后的zsm-5分子筛。所述碱为naoh、koh等的一种或几种。所述处理温度为40℃~70℃。所述水洗温度为40℃~70℃。所述处理过程液固比以ml/g计为(8~12):1,水洗过程液固比以ml/g计为(8~12):1。
42.本发明方法中,步骤(2)中所述脱铝处理采用酸处理,酸处理过程如下:zsm-5分子筛于h
+
含量为0.1~1.0mol/l的酸溶液中浸渍处理0.5h~2h,处理后进行过滤,重复此过程2~4次;然后换用去离子水洗涤1~5次至酸根离子含量低于0.1wt%,干燥后得到酸处理后的zsm-5分子筛。所述酸为盐酸、硫酸、硝酸、磷酸、草酸等的一种或几种。所述浸渍处理温度为40℃~70℃。所述水洗温度为40℃~70℃。所述浸渍处理过程液固比以ml/g计为(8~12):1,水洗过程液固比以ml/g计为(8~12):1。
43.本发明方法中,步骤(2)中所述脱铝处理采用水热处理,水热处理过程如下:zsm-5分子筛于水蒸气压力0.05mpa~0.5mpa下,400℃~700℃条件下水热处理0.5~5h,得到水热处理后的zsm-5分子筛。
44.本发明实施例中,所述zsm-5分子筛依次采用碱处理、酸处理、水热处理来进行脱硅和脱铝,在扩孔的同时调变分子筛的酸性及非骨架铝。
45.本发明方法中,步骤(3)中所述酸性缓冲溶液的ph为5.7~6.4,优选5.9~6.2,具
体过程如下:将经过处理的分子筛置于缓冲溶液中浸渍处理0.5h~2h,液固体积比以ml/g计为(8~12):1,处理温度为40℃~70℃,处理后进行过滤,并重复此过程2~4次;然后直接干燥或者洗涤后干燥获得酸性缓冲溶液处理后的zsm-5分子筛。
46.本发明方法中,步骤(3)中所述酸性缓冲溶液为ph符合要求的任一缓冲溶液,出于后续处理过程的简化,实施例中采用草酸-草酸铵缓冲溶液,选用含有不易焙烧的组分的缓冲溶液处理后,需用去离子水洗涤2-3次。
47.本发明方法中,步骤(4)中所述的负载氨基硅油采用浸渍法,等体积浸渍或者过体积浸渍均可,优选等体积浸渍。
48.本发明方法中,步骤(4)中所述的氨基硅油氨值为0.6~1.0。本发明实施例中采用含氨基硅油0.02~0.10wt%,优选0.04~0.06wt%的乳化液等体积浸渍步骤(3)制得的物料,所述溶剂为去离子水,等体积浸渍时间为5~10h。
49.本发明方法中,步骤(3)中所述干燥温度为100℃~150℃,干燥时间为2~4h;焙烧温度为550℃;焙烧时间为3~5h。
50.上述临氢降凝方法中,所述记为b1的zsm-5分子筛的制备方法,包括如下步骤:
51.(1)对zsm-5分子筛进行扩孔处理;
52.(2)采用酸性缓冲溶液浸渍处理步骤(1)的物料;
53.(3)步骤(2)的物料负载氨基硅油,经干燥、焙烧后得到最终改性zsm-5分子筛。
54.上述方法步骤(1)中,所述zsm-5分子筛可以采用市售商品或者按照现有技术制备。例如采用如下方法制备:将一定量的氧氧化钠、去离子水、偏铝酸钠、硅胶、模板剂(tpa2o)混合,各物料摩尔比为:(25~300)sio2:1al2o3:tpa2o:(0.01~10)na2o:(100~1100)h2o;将混合好的物料转入不锈钢晶化釜内,在一定温度下晶化;晶化结束后,将混合物产物以去离子水洗涤至ph值为7-8;将所得样品110℃烘干,研磨。
55.上述方法步骤(1)中,所述扩孔处理可以采用酸处理、水热处理中的一种或几种。
56.上述方法步骤(1)中,本发明方法中,步骤(5)中所述扩孔处理采用酸处理,酸处理过程如下:zsm-5分子筛于h
+
含量为0.1~1.0mol/l的酸溶液中浸渍处理0.5h~2h,处理后进行过滤,重复此过程2~4次;然后换用去离子水洗涤1~5次至酸根离子含量低于0.1wt%,干燥后得到酸处理后的zsm-5分子筛。所述酸为盐酸、硫酸、硝酸、磷酸、草酸等的一种或几种。所述浸渍处理温度为40℃~70℃。所述水洗温度为40℃~70℃。所述浸渍处理过程液固比以ml/g计为(8~12):1,水洗过程液固比以ml/g计为(8~12):1。
57.上述方法步骤(1)中,所述扩孔处理采用水热处理,水热处理过程如下:zsm-5分子筛于水蒸气压力0.05mpa~0.5mpa下,400℃~700℃条件下水热处理0.5~5h,得到水热处理后的zsm-5分子筛。
58.本发明实施例中,所述zsm-5分子筛依次采用酸处理、水热处理来进行扩孔处理,所述过程并不构成对本发明的限制。
59.上述方法步骤(2)中,所述酸性缓冲溶液的ph为4.9~5.5,优选5.0~5.3,具体过程如下:将经过扩孔处理的分子筛置于缓冲溶液中浸渍处理0.5h~2h,液固体积比以ml/g计为(8~12):1,处理温度为40℃~70℃,处理后进行过滤,并重复此过程2~4次;然后直接干燥或者洗涤后干燥获得酸性缓冲溶液处理后的zsm-5分子筛。
60.上述方法步骤(2)中,所述酸性缓冲溶液为ph符合要求的任一缓冲溶液,出于后续
处理过程的简化,实施例中采用草酸-草酸铵缓冲溶液,选用含有不易焙烧的组分的缓冲溶液处理后,需用去离子水洗涤2-3次。
61.上述方法步骤(3)中,所述的负载氨基硅油采用浸渍法,等体积浸渍或者过体积浸渍均可,优选等体积浸渍。
62.上述方法步骤(3)中,所述的氨基硅油氨值为0.6~1.0。本发明实施例中采用含氨基硅油0.08~0.15wt%,优选0.12~0.13wt%的乳化液等体积浸渍步骤(2)制得的物料,所述溶剂为去离子水,等体积浸渍时间为5~10h。
63.上述方法步骤(8)中,所述干燥温度为100℃~150℃,干燥时间为2~4h;焙烧温度为550℃;焙烧时间为3~5h。
64.上述临氢降凝方法中,分别将制备的记为a1的zsm-5分子筛、记为b1的zsm-5分子筛粘结剂混捏成型,经干燥、焙烧后制备出载体;在载体上引入第viii族金属活性金属,经干燥、焙烧后制备出临氢降凝催化剂a、b。
65.上述方法中,所述蜡油加氢裂化的典型的操作条件为:反应压力8.0~16.0mpa,氢油体积比600∶1~1500∶1,体积空速为0.1h-1
~5.0h-1
,反应温度260℃~455℃;优选的操作条件为:反应压力8.0~15.5mpa,氢油体积比800∶1~1300∶1,体积空速0.3h-1
~2.0h-1
,反应温度310℃~430℃。
66.上述方法中,所述分离系统及分馏系统操作条件均为常规操作条件,无任何特殊要求。
67.同现有技术相比,本发明的装置及加氢方法能够灵活加工不同的原料,操作简单、产品质量好。
附图说明
68.图1是一种加氢装置示意图
69.其中1为原料油,2为氢气,3为精制反应器,4为精制后的物流,5为高温高压分离器,6为分离出的液相物流,7为高温常压分离器,8为分离出的气相物流,9为分离出的液相物流,10为临氢降凝反应器,11为临氢降凝产物,13为加氢裂化反应器,14为临氢降凝与加氢裂化产物的混合物,15为低温高压分离器,16为分离出的液相物流,17为分馏塔。
具体实施方式
70.下面结合实施例及比较例进一步说明本发明方法的作用及效果,但以下实施例不构成对本发明方法的限制。
71.实施例1
72.100g zsm-5原粉在1000ml浓度为0.3mol/l的盐酸溶液于60℃下处理1h并重复两次,抽滤;所得滤饼置于1000ml去离子水中于50℃下洗涤三次后,抽滤;滤饼置于1000ml浓度为0.3mol/l的naoh溶液中于50℃下处理1h并重复两次,抽滤;所得滤饼置于1000ml去离子水中于50℃下洗涤三次后,抽滤;滤饼在120℃下干燥6h后,置于水热处理釜中,于500℃、0.1mpa压力下进行水热处理2h,取出后置于1000ml ph值为6.1的草酸-草酸铵缓冲溶液中于50℃下处理1.5h并重复两次,抽滤;所得滤饼置于1000ml去离子水中于50℃下洗涤三次后,抽滤;滤饼在120℃下干燥6h后,量取64ml浓度为0.05g/l的氨基硅油水溶液等体积浸渍
24h,在120℃下干燥6h,取出后置于马弗炉中程序升温至550℃焙烧3h后得到zsm-5ga分子筛。对zsm-5ga进行表征,其性质如表1所示。
73.表1 zsm-5ga分子筛表征结果
[0074][0075]
实施例2:
[0076]
按照本发明提供的方法,100g zsm-5原粉在1000ml浓度为0.5mol/l的盐酸溶液于60℃下处理1h并重复两次,抽滤;所得滤饼置于1000ml去离子水中于50℃下洗涤三次后,抽滤;滤饼在120℃下干燥6h后,置于水热处理釜中,于500℃、0.1mpa压力下进行水热处理2h,取出后置于1000ml ph值为5.3的缓冲溶液中于50℃下处理1.5h并重复两次,抽滤;所得滤饼置于1000ml去离子水中于50℃下洗涤三次后,抽滤;滤饼在120℃下干燥6h后,量取64ml浓度为0.11g/l的氨基硅油水溶液等体积浸渍24h,在120℃下干燥6h,取出后置于马弗炉中程序升温至550℃焙烧3h后得到zsm-5gb分子筛。对zsm-5gb进行表征,其性质如表3所示。
[0077]
表3 zsm-5gb分子筛表征结果
[0078][0079]
实施例3:
[0080]
以实施例1和实施例2得到的分子筛制备催化剂,并分别命名为cata和catb其制备过程为分子筛与大孔氧化铝、粘结剂混捏、挤条、成型后,经干燥和焙烧,得到载体;用硝酸镍的浸渍液浸渍到的载体,然后经干燥和焙烧,得到催化剂;其中分子筛质量百分数为30wt%,大孔氧化铝质量百分数为50wt%,nio质量百分数为10wt%,其余为粘结剂。
[0081]
实施例4:
[0082]
将cata和catb按照体积比为1:9装填在临氢降凝反应器中,加氢裂化预精制反应器和加氢裂化反应器分别装填市售加氢裂化预精制催化剂ff-66和市售加氢裂化催化剂fc-14。加氢裂化预处理反应器的反应条件为,反应压力8.0mpa;平均反应温度为350℃;体积空速1.0h-1;氢油体积比500∶1。临氢降凝反应器的反应条件为:反应压力8.0mpa,氢油体积比500:1,体积空速为4.0h-1
,反应温度350℃。加氢裂化反应器的操作条件为:反应压力8.0mpa,氢油体积比1000∶1,体积空速为1.0h-1
,反应温度360℃。
[0083]
实施例5~13
[0084]
以直馏柴油和减压蜡油混合油为原料,分别按照不同的配比,按照本方法进行加氢裂化反应,原料油性质如表4所示,所得产品收率及性质如表5~13所示。
[0085]
表4实施例1~9原料油性质
[0086][0087][0088]
表5实施例5产品收率及性质
[0089]
[0090]
表6实施例6产品收率及性质
[0091][0092][0093]
表7实施例7产品收率及性质
[0094][0095]
表8实施例8产品收率及性质
[0096][0097][0098]
表9实施例9产品收率及性质
[0099][0100]
表10实施例10产品收率及性质
[0101][0102][0103]
表11实施例11产品收率及性质
[0104][0105]
表12实施例12产品收率及性质
[0106][0107][0108]
表13实施例13产品收率及性质
[0109][0110]
比较例:
[0111]
以柴油和蜡油1:1混合油为原料,原料油性质如表14所示,采用传统加氢裂化装置,即原料经加氢裂化预精制反应器后不经分离直接进入加氢裂化反应器,所采用催化剂为市售加氢裂化预精制催化剂ff-66和市售加氢裂化催化剂fc-14。加氢裂化预处理反应器的反应条件为,反应压力8.0mpa;平均反应温度为350℃;体积空速1.0h-1;氢油体积比500∶1。加氢裂化反应器的操作条件为:反应压力8.0mpa,氢油体积比1000∶1,体积空速为1.0h-1
,反应温度360℃。所得产品收率及性质如表15所示。
[0112]
表14比较例原料油性质
[0113]
[0114][0115]
表15比较例产品收率及性质
[0116]