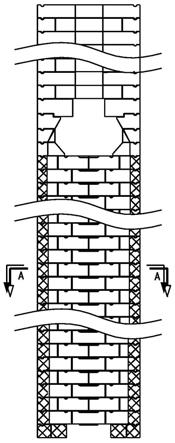
[0001]
本发明涉及一种焦炉燃烧室结构,尤其涉及一种炉墙厚度沿高向变化的焦炉燃烧室结构。
背景技术:[0002]
焦炉本体按部位划分,可分为蓄热室、斜道、燃烧室和炭化室、炉顶这4个主要部位。其中燃烧室一般由沿机侧-焦侧(即长向)分隔的14~18对立火道组成。燃烧室和炭化室间隔设置,燃烧室与炭化室通过炉墙(又称燃烧室炉墙或炭化室炉墙)隔开。加热煤气在立火道内燃烧,产生的热量通过辐射传热及对流传热的方式经炉墙传递给炭化室内的入炉煤,使入炉煤在隔绝空气的条件下干馏,最终生成焦炭。
[0003]
焦炉高向加热的均匀性直接影响焦炭质量的好坏、炼焦耗热量的高低以及推焦操作的难易等。而加热煤气在立火道内燃烧所产生的热量经过炉墙才能传给煤料。因此,炉墙的传热与焦炉的高向加热均匀性有密切关系。
[0004]
传统的焦炉燃烧室结构,炉墙沿高向由厚度均匀一致的炉墙砖砌筑而成。这种形式的炉墙结构简单,但是焦炉的高向加热均匀性不佳,尤其在使用焦炉煤气加热的情况下,因火焰较短,上部焦炭成熟度较差。为解决上述问题,焦炉结构也在不断改进完善,如采用废气循环、高低灯头、分段加热等方式。
[0005]
公开号为cn104449768a的中国专利申请公开了“一种下调式焦炉燃烧室立火道燃烧调节方法及其加热系统”,燃烧室下成对设置的蓄热室中的一个与燃烧室立火道底部直接连通,另一个通过立火道隔墙内沿高度方向设置的数个助燃气体出口与立火道连通,两个蓄热室分别设置助燃空气流量调节装置。采用该技术方案,成对的两个蓄热室内的助燃空气分别通过各自独立的通道进入立火道,其中一个蓄热室内的助燃空气进入立火道底部,另一个蓄热室内的助燃空气沿不同高度位置进入立火道,两个通道中的助燃空气流量可独立调节,从而改善了立火道高向加热均匀性。但是,其对立火道隔墙进行改造,使立火道隔墙的结构较为复杂,用于砌筑立火道隔墙的砖型增多,故只适用于大型焦炉。
技术实现要素:[0006]
本发明提供了一种炉墙厚度沿高向变化的焦炉燃烧室结构,对燃烧室两侧的炉墙进行改进,即根据焦炉生产时燃烧室高向温度场设置不同厚度的炉墙砖,从而有效改善焦炉高向加热均匀性,提高焦炭质量;并且有利于降低焦炉炼焦耗热量及立火道温度,减少氮氧化物的生成量,实现节能环保的目的。
[0007]
为了达到上述目的,本发明采用以下技术方案实现:
[0008]
一种炉墙厚度沿高向变化的焦炉燃烧室结构,所述燃烧室由炉墙围成,并由立火道隔分隔为多个立火道;所述炉墙由炉墙砖砌筑而成,所述立火道隔墙由隔墙砖砌筑而成;所述炉墙自下至上分为3个部分,即下部炉墙、中部炉墙及上部炉墙;其中,中部炉墙的厚度沿高向自下至上由厚变薄。
[0009]
所述中部炉墙沿高向分为多段,且各段炉墙的厚度自下至上依次递减。
[0010]
所述炉墙朝向炭化室一侧的墙面为平面。
[0011]
所述中部炉墙的厚度变化范围为90~110mm。
[0012]
相邻2层炉墙砖之间采用砖沟砖舌形式连接。
[0013]
所述炉墙砖与隔墙砖之间采用咬合缝方式连接。
[0014]
所述下部炉墙是自燃烧室底部至废气循环孔顶部的区域,且自燃烧室底部向上数至少包括4层炉墙砖。
[0015]
所述上部炉墙是自跨越孔底部至过顶砖之间的区域,且至少包括10层炉墙砖。
[0016]
与现有技术相比,本发明的有益效果是:
[0017]
1)根据焦炉生产时燃烧室高向温度场设置不同厚度的炉墙砖,厚度薄的炉墙砖热阻小,传热效率高;可以在不改变立火道隔墙结构的情况下,有效改善焦炉高向加热均匀性,提高焦炭质量。
[0018]
2)降低焦炉生产时所需的加热煤气量,降低炼焦耗热量,降低立火道温度,减少氮氧化物的生成量,具有良好的节能环保效果。
[0019]
3)与采用分段加热立火道隔墙的方式相比,结构更加简单,不仅适用于大型焦炉,也适用于中小型焦炉。
附图说明
[0020]
图1是本发明所述焦炉燃烧室的主视图。
[0021]
图2是图1中的a-a视图。
[0022]
图中:1.炉墙
ꢀꢀ
2.炉墙砖
ꢀꢀ
3.立火道
ꢀꢀ
4.立火道隔墙
ꢀꢀ
5.隔墙砖
具体实施方式
[0023]
下面结合附图对本发明的具体实施方式作进一步说明:
[0024]
如图1、图2所示,本发明所述一种炉墙厚度沿高向变化的焦炉燃烧室结构,所述燃烧室由炉墙1围成,并由立火道隔4分隔为多个立火道3;所述炉墙1由炉墙砖2砌筑而成,所述立火道隔墙4由隔墙砖5砌筑而成;所述炉墙1自下至上分为3个部分,即下部炉墙、中部炉墙及上部炉墙;其中,中部炉墙的厚度沿高向自下至上由厚变薄。
[0025]
所述中部炉墙沿高向分为多段,且各段炉墙的厚度自下至上依次递减。
[0026]
所述炉墙1朝向炭化室一侧的墙面为平面。
[0027]
所述中部炉墙的厚度变化范围为90~110mm。
[0028]
相邻2层炉墙砖之间采用砖沟砖舌形式连接。
[0029]
所述炉墙砖与隔墙砖之间采用咬合缝方式连接。
[0030]
所述下部炉墙是自燃烧室底部至废气循环孔顶部的区域,且自燃烧室底部向上数至少包括4层炉墙砖。
[0031]
所述上部炉墙是自跨越孔底部至过顶砖之间的区域,且至少包括10层炉墙砖。
[0032]
以下实施例在以本发明技术方案为前提下进行实施,给出了详细的实施方式和具体的操作过程,但本发明的保护范围不限于下述的实施例。下述实施例中所用方法如无特别说明均为常规方法。
[0033]
【实施例】
[0034]
如图1、图2所示,本实施例中,某焦炉燃烧室的炉墙共由54层炉墙砖砌筑而成,自机侧至焦侧共设18对立火道,各立火道自机侧至焦侧分别标记为1#~36#立火道;其中,3#立火道至34#立火道这一区域内的燃烧室炉墙采用变厚度炉墙结构。
[0035]
自燃烧室底部向上数第2层炉墙砖至第5层炉墙砖之间的区域为下部炉墙,下部炉墙由厚度为95mm的炉墙砖砌筑而成。
[0036]
第6层炉墙砖至第42层炉墙砖之间的区域为中部炉墙,其中:第6层炉墙砖至第11层炉墙砖均为厚度110mm的炉墙砖。第12层炉墙砖至第17层炉墙砖均为厚度105mm的炉墙砖。第18层炉墙砖至第23层炉墙砖均为厚度为100mm的炉墙砖。第24层炉墙砖至第33层炉墙砖均为厚度为95mm的炉墙砖。第34层炉墙砖至第42层炉墙砖均为厚度为90mm的炉墙砖。
[0037]
第43层炉墙砖至第54层炉墙砖之间的区域为上部炉墙,其由不同厚度的炉墙砖组成跨越孔、看火孔等燃烧室顶部结构。
[0038]
组成焦炉燃烧室的炉墙砖与隔墙砖采用咬合缝方式连接,相邻2层炉墙砖之间采用砖沟砖舌方式连接。
[0039]
采用变厚度炉墙后,燃烧室两侧的中部炉墙对应不同高度的传热系数不同,能够有效改善焦饼沿高向加热不均匀的状况,尤其在使用焦炉煤气加热的情况下,能够有效提高焦炭质量,并有利于降低焦炉炼焦耗热量和氮氧化物生成量。
[0040]
以上所述,仅为本发明较佳的具体实施方式,但本发明的保护范围并不局限于此,任何熟悉本技术领域的技术人员在本发明揭露的技术范围内,根据本发明的技术方案及其发明构思加以等同替换或改变,都应涵盖在本发明的保护范围之内。