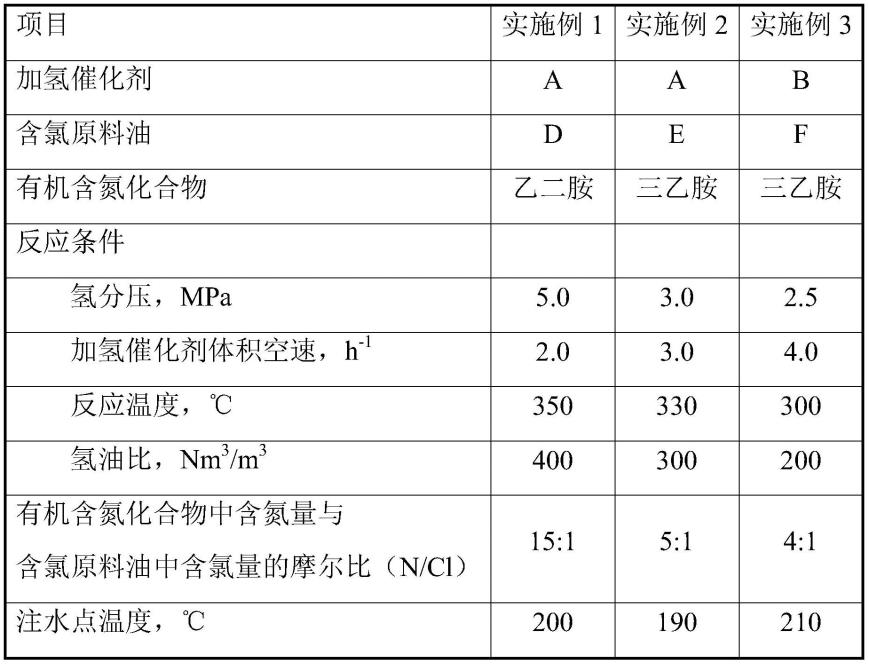
1.本发明涉及含氯原料油处理技术领域,具体涉及一种含氯原料油的脱氯方法。
背景技术:2.随着我国城市化进程的不断发展,城市人口逐年上升,人民的生活水平不断提高,城市生活垃圾的产量也在不断增加,目前城市垃圾处理方法主要包括填埋、焚烧等。无论是焚烧还是填埋都存在一系列后续的环保问题。
3.化学转化方法可将塑料垃圾转化为具有利用价值的工业原料或燃料油,不仅可消除环境污染,且还可实现资源的可持续性发展利用,是治理“白色污染”的有效途径。目前废塑料炼油产业在国内已呈遍地开花局面,已经有一些企业建成规模较小的热解示范装置,但是废塑料热解产品的高值利用问题尚待有效解决。
4.各种工艺转化而来的废塑料油、废轮胎油杂质含量高,尤其是其中氯含量,通过加氢工艺流程可有效能脱除其中的硫、氮、氧、氯等杂质,但加氢脱氯生成的hcl会给装置带来严重的腐蚀问题。
5.以植物油或餐饮废油为原料,通过加氢处理的方法可以得到生物质燃料,但是,餐饮废油中氯离子和氧含量较高,在加氢条件下生成氯化氢及水,氯化氢和水在液相条件下会生成浓度很高的盐酸,对装置造成严重的腐蚀,造成装置运行周期缩短,甚至带来装置运行安全隐患。
6.在一些原油开采过程中,加入了含有cl离子的助剂以增加产油量,导致原油及原油加工的馏分油,即石油类油品中有机氯含量大幅提高,给后续加工带来不便。
7.cn104059689a公开了一种油品脱氯方法,将碱性物质和盐加入去离子水中,制成浓度为4~6.5mol/l、盐的阴离子浓度为1~1.5mol/l的碱性盐溶液,把该碱性盐溶液和油品按和盐的阴离子摩尔数之和与的摩尔数之比为(15.5~5000):1混合,在100℃~180℃下,回流反应2~4h,经冷却、静置、分液得到脱氯后的油品。该方法对高氯含量的废轮胎热解油进行脱氯时,脱氯率未达到55%。
8.cn104726134a公开了一种含氯塑料油生产高品质汽柴油的方法。其特征是以含氯塑料油注入装有活性三氧化二铝的高温脱氯塔进行高温脱氯,高温脱氯塔塔顶喷淋少量naoh水溶液,脱氯后的塑料油进入装有分子筛/氧化铝催化剂的催化蒸馏塔中进行反应和精馏;催化蒸馏后塑料油经加压进入加氢精制塔,加氢精制后的馏分油经常压蒸馏,根据馏出温度切割成汽油和柴油,塔底重油与原料含氯塑料油混合重新反应。该方法经过高温脱氯塔脱氯后,产物氯含量仍大于50μg/g。
9.cn106318462a公开了一种用于将含氯柴油进行加氢脱氯的反应系统,并提供使用该系统对含氯柴油进行加氢脱氯的方法,将含氯柴油和氢气依次引入串联的加氢反应器和脱氯罐,与加氢反应器的加氢精制催化剂床层,以及脱氯罐的加氢脱金属剂床层、脱氯剂床层接触反应;依照含氯柴油和氢气的流向,加氢反应器装填的是加氢精制催化剂;脱氯罐中依次装填的是加氢脱金属剂、脱氯剂ⅰ和脱氯剂ⅱ。该发明采用在脱氯罐中级配装填加氢脱
金属剂、脱氯剂的方式脱除来自于加氢反应器的含铁杂质和氯化铵。
10.cn110079360a公开一种用于含氯油加氢脱氯的方法,所述方法为将含氯原料在临氢状态和加氢脱氯温度下进行低压加氢脱氯的方法,其包括以下步骤:(a)含氯原料进入低压加氢脱氯反应器;(b)反应产物进入脱氯吸附反应器;和(c)产物进入气液分离器得到脱氯净化油和含氢气相。
11.上两种方法均使用固体脱氯剂对加氢后物流进行脱氯,一方面使用固体脱氯剂、脱氯罐(脱氯吸附反应器)会增加装置的成本,另一方面由于固体脱氯剂氯容的限制,在加工高氯原料油时,脱氯剂需要频繁更换,反而影响了装置的运转周期。
技术实现要素:12.本发明是为了解决现有技术对含氯原料油进行脱氯时,脱氯率低、成本高的问题。
13.本发明提供一种含氯原料油的脱氯方法,包括:含氯原料油、有机含氮化合物及氢气混合后,混合物料进入加氢反应器与加氢催化剂接触进行反应,反应流出物经过冷却、注水后进入高压分离器进行气液相分离,分离所得气相为富氢气体进入循环氢系统,分离所得水相为含氯化铵废水进入废水处理系统,分离所得油相为低氯液相产物,其进入后续加工系统或者作为产品直接出装置;含氯原料油的氯含量大于等于5μg/g,所得低氯液相产物的氯含量小于0.5μg/g。
14.所述含氯原料油选自废塑料油、废旧轮胎油、餐饮废油、石油类油品中的一种或几种。
15.在本发明的一个实施方式中,所述废塑料油为废塑料通过热裂化、热裂解、催化裂解、催化裂化、溶解液化中一种或几种转化方法得到的烃类物料;废塑料油的馏程为30~700℃,氯含量小于10000μg/g。废塑料油的组成包括烯烃的体积分数为5~80%,优选5~60%,芳烃的体积分数为小于90%,优选2~60%,链烷烃的体积分数小于90%,优选5~60%。
16.在本发明中,所述废塑料为新鲜生活垃圾中废塑料、工农业生产中废塑料、陈化垃圾中废塑料中的一种或几种,废塑料的种类为选自pe、pp、ps、pvc中的一种或多种。
17.在本发明的一个实施方式中,所述废旧轮胎油为废旧轮胎通过热裂化、热裂解、催化裂解、催化裂化、溶解液化中一种或几种转化方法得到的烃类物料;废旧轮胎油的馏程为30~700℃,氯含量小于10000μg/g。废旧轮胎油的组成包括烯烃的体积分数为5~80%,优选5~60%,芳烃的体积分数为小于90%,优选2~60%,链烷烃的体积分数小于90%,优选5~60%。
18.在本发明中,所述废旧轮胎为天然橡胶和/或合成橡胶制备的各种废弃轮胎。
19.在本发明中,所述热裂化和热裂解反应,是指在高温条件下,烃类分子包括废塑料、废旧轮胎,在隔绝空气条件下分解成较小分子的反应。按照反应温度不同,将小于等于600℃的称为热裂化反应,将大于600℃的称为热裂解反应。
20.在本发明中,所述催化裂化和催化裂解反应,是指在高温条件和催化剂存在下,烃类分子包括废塑料、废旧轮胎,分解成较小分子的反应。按照反应产物不同,将以低碳烯烃(乙烯、丙烯、丁烯)为目的产物的反应称为催化裂解反应,将以车用汽油为目的产物的反应称为催化裂化反应。
21.在本发明中,所述溶解液化反应,是指废塑料、废旧轮胎在溶剂油和/或有机溶剂的存在下,由固态转化为液态的反应。
22.在本发明中,所述石油类油品是指原油和任何来自原油来源的油品,包括但不限于原油、原油加工所得的馏分油、废矿物油等。
23.在本发明的一个实施方式中,所述有机含氮化合物为有机胺类化合物,选自脂肪胺、醇胺、酰胺、脂环胺、芳香胺、萘系胺中一种或几种;优选有机含氮化合物为低级脂肪胺。所述低级脂肪胺是指c7以下的脂肪胺类化合物。
24.在本发明的一个实施方式中,进入加氢反应器的混合物料中,有机含氮化合物中含氮量与含氯原料油中含氯量的摩尔比为1~20:1,优选为3~18:1。
25.在本发明的一个实施方式中,加氢催化剂包括加氢金属活性组分和载体,所述加氢金属活性组分为选自第vib族金属元素、第viii族金属元素中的一种或几种,所述第vib族金属元素为钼和/或钨,所述第viii族金属元素为钴和/或镍;以加氢催化剂的总重量为基准,以氧化物计,所述第vib族金属元素含量为1~50重量%,所述第viii族金属元素含量为1~40重%,所述载体包括氧化铝和/或氧化硅。
26.在本发明的一个实施方式中,加氢反应器的反应条件为:氢分压0.1~10mpa、反应温度60~500℃、体积空速0.1~30h-1
、氢油体积比1~1000nm3/m3;优选加氢反应器的反应条件为:氢分压0.5~6mpa、反应温度100~400℃、体积空速0.2~20h-1
、氢油体积比5~800nm3/m3。
27.在本发明的一个实施方式中,在注水点位置的反应流出物物料温度大于等于150℃,优选为150~250℃。
28.在本发明的一个实施方式中,注水所用的水为选自脱氧水、软化水、脱盐水中的一种或几种。
29.在本发明的一个实施方式中,注水时,水的用量与含氯原料油中氯元素的质量比为10000~100000:1,优选为20000~50000:1。
30.在本发明的一个实施方式中,注水点位置设置1~3个;在注水时,使用至少一个注水点。
31.在本发明的一个实施方式中,在注水点,对反应流出物进行连续注水,监测注水点前和注水点后的反应流出物物流压差,控制压差小于0.1mpa。当压差大于等于0.1mpa时,采用增加注水量,或更换注水点等方式进行调整,直至压差小于0.1mpa。
32.在本发明其中一个实施方式中,所得反应流出物进入高压分离器,经气液分离后,得到气相物料、液相物料和水相物料,高压分离器的操作条件为:温度20~100℃,压力0.1~10mpa,优选的操作条件为:温度20~60℃,压力0.5~6mpa。
33.分离所得气相为富氢气体进入循环氢系统进行循环使用。分离所得水相为含氯化铵废水进入废水处理系统进行处理。分离所得油相为低氯液相产物,其进入后续加工系统如加氢提质、加氢裂化、催化裂化、催化裂解、蒸汽裂解制乙烯等工艺过程进行进一步处理,或者作为产品直接出装置。
34.本发明的特点:
35.1、本发明可以处理含氯原料油,有效解决了由于原料油含氯而造成的装置腐蚀和管道堵塞的问题,同时可以把液体产物的氯含量降至小于0.5μg/g,满足后续装置加工或作
为产品的要求。
36.2、本发明在加氢脱除原料其他杂质的同时,有效进行脱氯,不需要固体脱氯剂,可以大幅降低加工成本,并有效延长含氯原料油整体加工的操作周期。
附图说明
37.图1是本发明提供的含氯原料油的脱氯方法的流程示意图。
具体实施方式
38.下面结合附图对本发明进行进一步的说明,但并不因此而限制本发明。
39.图1是本发明提供的含氯原料油的脱氯方法的流程示意图,如图1所示,来自管线1的含氯原料油经进料泵2升压后与来自管线3的有机含氮化合物混合后进入换热器4进行换热,换热后物料与来自管线5的氢气混合后一起进入加热炉6进行加热,加热后的混合物料经管线7进入加氢反应器8与加氢催化剂接触进行反应,反应流出物经管线9进入换热器4进行冷却,经来自管线10的软化水在注水点注水后,经管线11进入高压分离器12进行气液相分离,分离所得气相为富氢气体,经管线13进入循环氢压缩机16升压后经管线17抽出,与来自管线18的补充氢混合后经管线5循环至加热炉6入口。高压分离器12分离所得水相为含氯化铵废水,经管线15进入废水处理系统。高压分离器12分离所得油相为氯含量小于0.5μg/g的低氯液相产物,经管线14抽出,作为进料进入后续加工系统或者作为产品直接出装置。
40.下面结合实施例对本发明作进一步的说明,但并不因此而使本发明受到任何限制。
41.在实施例中,液体物料中氯含量采用库仑法进行测定,具体方法为《石油化工分析方法》(ripp试验方法)中的《电量法测定原油中总氯含量》(ripp 64-90)的方法进行测定。所用仪器为微库仑分析仪,试样为液体物料。
42.下面的实施例将对本发明提供的方法予以进一步的说明,但并不因此而限制本发明。
43.实施例中所使用的加氢催化剂a,其载体为氧化铝,蝶形,当量直径1.6mm,活性金属组成为:氧化钼26.0重%,氧化镍4.0重%;
44.实施例中所使用的加氢催化剂b,其载体为氧化铝,蝶形,当量直径1.6mm,活性金属组成为:氧化钼12重%,氧化钴3.0重%;
45.实施例中所使用的加氢催化剂c,其载体为氧化铝,蝶形,当量直径1.6mm,活性金属组成为:氧化钨18重%,氧化镍2重%,氧化钴0.04重%;
46.含氯原料油包括:
47.含氯原料油d:废塑料油,氯含量3000μg/g,馏程150~600℃;
48.含氯原料油e:废旧轮胎热解油,氯含量50μg/g,馏程180~550℃;
49.含氯原料油f:餐饮废油,氯含量300μg/g,馏程180~350℃;
50.含氯原料油g:含氯石脑油,氯含量1000μg/g,硫含量300μg/g,氮含量3μg/g,馏程40~180℃;
51.含氯原料油h:含氯柴油,氯含量200μg/g,硫含量3000μg/g,氮含量200μg/g,馏程180~380℃。
52.实施例1
53.含氯原料油d、乙二胺及氢气以一定比例混合后,进入加氢反应器与加氢催化剂a接触进行反应。反应流出物与含氯原料油换热后,在注水点连续注入除盐水,注水点处反应流出物的温度为200℃,除盐水的用量与含氯原料油d中氯含量的质量比为30000:1,注水点前后压差小于0.1mpa。注水后反应流出物进入高压分离器进行气液分离,分离后的气相,作为循环氢进入循环氢系统。高压分离器分离的水相,即高压分离器水包流出的含氯化铵废水进入废水处理系统,高压分离器分离的油相为低氯液相产物,进行后续加工或者作为产品直接出装置。加氢反应器的操作条件为:氢分压2.0mpa,反应温度340℃、体积空速4.0h-1
,氢油体积300nm3/nm3。高压分离器操作条件为:温度30℃,压力2.5mpa。含乙二胺中含氮量与含氯原料油d中含氯量的摩尔比(n/cl)为15:1。具体反应条件和产物性质见表1。
54.由表1可见,加氢装置连续运转93天后,注水点前后压差小于0.1mpa,低氯液相产物氯含量小于0.5μg/g。加氢装置连续运转300天后,注水点前后压差小于0.1mpa,低氯液相产物氯含量小于0.5μg/g。
55.实施例2
56.采用与实施例1相同的工艺流程处理含氯原料油e,区别在于,所用有机含氮化合物为三乙胺。具体反应条件和产物性质见表1。
57.由表1可见,加氢装置连续运转93天后,注水点前后压差小于0.1mpa,低氯液相产物氯含量小于0.5μg/g。加氢装置连续运转300天后,注水点前后压差小于0.1mpa,低氯液相产物氯含量小于0.5μg/g。
58.实施例3
59.采用与实施例1相同的工艺流程处理含氯原料油f,区别在于,所用的加氢催化剂为加氢催化剂b,所用有机含氮化合物为三乙胺。具体反应条件和产物性质见表1。
60.由表1可见,加氢装置连续运转93天后,注水点前后压差小于0.1mpa,低氯液相产物氯含量小于0.5μg/g。加氢装置连续运转300天后,注水点前后压差小于0.1mpa,低氯液相产物氯含量小于0.5μg/g。
61.实施例4
62.采用与实施例1相同的工艺流程处理含氯原料油g,区别在于,所用的加氢催化剂为加氢催化剂b。除盐水的用量与原料中氯元素的质量比为8000:1,在装置运转第18天时,注水点前后的压差上升为0.15mpa,调整注水量,使得除盐水的用量与含氯原料油g中氯元素的质量比调整为20000:1,注水点前后的压差降低至小于0.1mpa。具体反应条件和产物性质见表2。
63.由表2可见,加氢装置连续运转78天后,注水点前后压差小于0.1mpa,低氯液相产物硫、氮、氯含量均小于0.5μg/g。加氢装置连续运转350天后,注水点前后压差小于0.1mpa,低氯液相产物硫、氮、氯含量均小于0.5μg/g。
64.实施例5
65.采用与实施例1相同的工艺流程处理含氯原料油h,区别在于,所用的加氢催化剂为加氢催化剂c。具体反应条件和产物性质见表2。
66.由表2可见,加氢装置连续运转78天后,注水点前后压差小于0.1mpa,低氯液相产物氯含量小于0.5μg/g、硫含量6μg/g、氮含量1μg/g。加氢装置连续运转350天后,注水点前
后压差小于0.1mpa,低氯液相产物氯含量小于0.5μg/g、硫含量7μg/g、氮含量1.2μg/g。
67.表1
[0068][0069][0070]
表2
[0071]
[0072][0073]
需说明的是,以上所述仅为本发明的任意实施例,并不用于限制本发明,对于本领域的技术人员来讲,本发明可以有各种更改和变化。凡在本发明的精神和原则之内,所做的任何修改、等同替换、改进等,均应包含在本发明的保护范围之内。