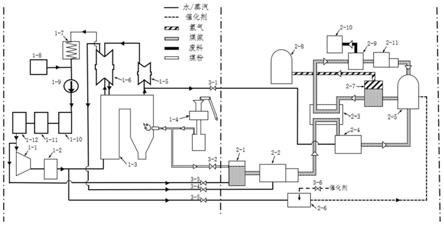
1.本发明属于洁净能源转化领域,特别涉及一种超临界及其以上参数煤电机组耦合超临界水制氢系统及方法。
背景技术:2.氢作为宇宙中分布最广泛的物质,以其单位质量热值高、燃烧等氧化反应最终产物为水的特点被认为是世界上最干净也最具有开发潜力的能源形式。包括我国在内的世界各国在氢能领域开展了大量的研究和应用,如氢燃料电池、大规模弃风弃电制氢、先进煤制氢技术等方面。氢能的大规模应用主要聚焦于制取、储存、利用三个方面,在制取方面,近年来,超临界水气化制氢技术以其近零的污染物排放、较高的制氢效率而得到了广泛的关注,但其相应的设备制造成本和建设成本较为高昂,单独建设超临界水气化制氢机组短时间内不具备很好地经济性。
3.另一方面,我国是一个多煤少油缺气的国家,为适应我国经济快速发展所带来的能源需要,我国建设起一大批煤电机组,随着我国科技实力的不断发展和相关产业的不断成熟,我国煤电机组的运行参数逐步提高,达到了超临界参数,超临界及其以上参数的煤电机组因为其成熟的技术路线和设备技术以及较高的发电效率,从2005年以来在全国各地大规模兴建,装机量不断地提高。然而,由于温室气体排放带来的全球气候变暖等环境问题的加剧,可再生能源,如风电、光伏等发电技术的装机不断攀升,大大挤占了火力发电机组的发电空间,全国煤电机组现阶段很多都处于全年利用小时数极低的状态,低负荷运行状态下的火力发电机组效率较低,而负荷的快速变化也会使机组寿命大幅度衰减,怎样利用好相关技术对煤电机组剩余负荷空间进行有效利用是现阶段的研究难点。
技术实现要素:4.本发明的目的在于提供一种超临界及其以上参数煤电机组耦合超临界水制氢系统及方法,解决了现有技术中存在的上述不足。
5.为了达到上述目的,本发明采用的技术方案是:
6.本发明提供的提供一种超临界及其以上参数煤电机组耦合超临界水制氢系统,包括:
7.超临界及以上参数煤电机组热力系统,用于提供超临界水、煤粉和低压中温水;
8.超临界及耦合制氢系统,用于利用超临界水、煤粉和低压中温水制氢。
9.优选地,所述超临界及以上参数煤电机组热力系统包括供水系统、锅炉和制粉系统,其中,所述供水系统的出水口分为两路,一路连接锅炉的进水口,一路连接超临界及耦合制氢系统;所述制粉系统的出料口分为两路,一路连接锅炉的进料口,另一路连接超临界及耦合制氢系统;
10.所述锅炉的超临界水出口连接超临界及耦合制氢系统。
11.优选地,所述锅炉的高温高压蒸汽出口连接有高压缸,所述高压缸的中温中压出口连接有中低压缸,所述中低压缸的抽汽出口连接超临界及耦合制氢系统。
12.优选地,所述供水系统包括给水泵、高压加热器、补水系统、循环水泵、精处理设备0、低压加热器和除氧器,其中,所述补水系统的出水口依次经过循环水泵、精处理设备0、低压加热器、除氧器、给水泵和高压加热器连接锅炉的进水口;所述除氧器的出水口还连接有超临界及耦合制氢系统。
13.优选地,超临界及耦合制氢系统包括高浓度煤浆混合器、煤浆超临界水混合器、超临界反应器、气固分离装置和氢气收集装置,其中,所述超临界及以上参数煤电机组热力系统的煤粉出口连接高浓度煤浆混合器的进料口;所述超临界及以上参数煤电机组热力系统的低压中温水出口连接高浓度煤浆混合器的进水口;所述高浓度煤浆混合器的出料口连接煤浆超临界水混合器的进浆口;
14.所述煤浆超临界水混合器的超临界水进口连接超临界及以上参数煤电机组热力系统的超临界水出口;
15.所述煤浆超临界水混合器的出浆口连接超临界反应器的进浆口,所述超临界反应器的气固混合物出口连接气固分离装置,所述气固分离装置的氢气出口连接氢气收集装置。
16.优选地,所述高浓度煤浆混合器的出浆口和煤浆超临界水混合器的进浆口之间依次设置有高压汽动煤浆柱塞泵和煤浆回热器,其中,所述高压汽动煤浆柱塞泵的进汽口连接超临界及以上参数煤电机组热力系统的抽汽出口。
17.优选地,所述超临界反应器还连接有高压催化剂混合器,所述高压催化剂混合器的进水口连接超临界及以上参数煤电机组热力系统的高压水出口。
18.一种超临界及其以上参数煤电机组耦合超临界水制氢方法,基于所述的系统,包括以下步骤:
19.将超临界及以上参数煤电机组热力系统中的低压中温水和煤粉送入至超临界及耦合制氢系统进行混合,得到低压高浓度煤浆;
20.将超临界及以上参数煤电机组热力系统中的超临界水送入至超临界及耦合制氢系统中,与低压高浓度煤浆进行混合反应制氢。
21.优选地,当满足下列任一条件时,超临界及耦合制氢系统停止运行:
22.超临界及耦合制氢系统最小工作功率对应的高浓度煤浆混合器最小给煤量小于制粉系统的最大煤粉量与超临界及以上参数煤电机组热力系统运行中锅炉所需的锅炉实时煤粉量之差;
23.超临界及耦合制氢系统最小工作功率对应的高浓度煤浆混合器的最小水流量小于循环水泵最大泵水量与超临界及以上参数煤电机组热力系统运行中锅炉所需的实时水流量之差;
24.超临界及耦合制氢系统最小工作功率对应的煤浆
‑
超临界水混合器的最小超临界水流量小于锅炉最大连续蒸发量与超临界及以上参数煤电机组热力系统运行中高压缸实时功率对应的所需蒸发量之差。
25.与现有技术相比,本发明的有益效果是:
26.本发明提供的一种超临界及其以上参数煤电机组耦合超临界水制氢系统,在现有
超临界及其以上参数煤电机组方案的基础上,通过添加超临界耦合制氢系统,实现电力、氢能的多联产,不需要破坏原有的煤电机组相应设备结构,不需要重复投资多余的煤储存、运输、煤粉制取设备系统,不需要添加过多的泵和热力设备,相应浆液泵尺寸大幅度缩小,有效降低了超临界水制氢的相关成本,例如在百万级机组内,为满足环保要求,仅仅建设封闭式的煤仓、相应运煤路线、磨煤设备,就会产生多达几亿的费用。同时,本发明可以充分利用煤电机组剩余负荷空间,使机组处于高负荷水平的运转状态,提高煤电机组的运行水平和效率,在机组参与调峰时,可在不降低锅炉蒸发量的情况下,将所产生整齐有效利用,降低发电量,实现灵活调峰,延长机组使用寿命。
附图说明
27.图1是超临界及其以上参数煤电机组耦合超临界水制氢系统的总体示意图。
具体实施方式
28.下面结合附图和具体实施方式对本发明进一步详细说明。
29.如图1所示,本发明提供的一种超临界及其以上参数煤电机组耦合超临界水制氢系统,包括超临界及以上参数煤电机组热力系统、超临界耦合制氢系统和阀门控制系统,其中:
30.所述超临界及以上参数煤电机组热力系统为目前全世界主流采用的超临界以上参数(一般指蒸汽循环参数,温度大于374摄氏度、压力大于22.1mpa)煤粉燃烧锅炉,该热力系统包括的主要设备有给水泵1
‑
1、高压加热器1
‑
2、锅炉1
‑
3、制粉系统1
‑
4、高压缸1
‑
5、中低压缸1
‑
6、冷凝系统1
‑
7、补水系统1
‑
8、循环水泵1
‑
9、精处理设备1
‑
10、低压加热器 1
‑
11和除氧器1
‑
12,其中,补水系统1
‑
8、循环水泵1
‑
9、精处理设备1
‑
10、低压加热器 1
‑
11和除氧器1
‑
12组成锅炉1
‑
3的供水系统。
31.所述补水系统1
‑
8的出水口依次连接循环水泵1
‑
9、精处理设备1
‑
10、低压加热器1
‑
11 和除氧器1
‑
12的进水口。
32.所述除氧器1
‑
12的出水口经过给水泵1
‑
1和高压加热器1
‑
2连接锅炉1
‑
3的进水口。
33.所述制粉系统1
‑
4的出料口连接锅炉1
‑
3的进料口。
34.所述锅炉1
‑
3的高温高压蒸汽出口连接高压缸1
‑
5的进汽口,所述高压缸1
‑
5的中温中压蒸汽出口连接中低压缸1
‑
6的中温中压蒸汽入口。
35.所述锅炉1
‑
3的中温中压蒸汽出口连接中低压缸1
‑
6的中温中压蒸汽入口。
36.所述高压缸1
‑
5和中低压缸1
‑
6均连接有发电机。
37.所述中低压缸1
‑
6的乏汽出口连接冷凝系统1
‑
7,其中,所述冷凝系统1
‑
7的出水口连接有循环水泵1
‑
9。
38.所述超临界耦合制氢系统包括高浓度煤浆混合器2
‑
1、高压汽动煤浆柱塞泵2
‑
2、煤浆回热器2
‑
3、煤浆
‑
超临界水混合器2
‑
4、超临界反应器2
‑
5、高压催化剂混合器2
‑
6、气固分离装置2
‑
7、氢气收集装置2
‑
8、固废分离器设备2
‑
9、废物处理装置2
‑
10和回料泵2
‑
11,其中,所述制粉系统1
‑
4的出料口连接高浓度煤浆混合器2
‑
1的进料口;所述除氧器1
‑
12 的出水口还连接高浓度煤浆混合器2
‑
1的进水口,所述高浓度煤浆混合器2
‑
1的出浆口经过高压
汽动煤浆柱塞泵2
‑
2连接煤浆回热器2
‑
3的进浆口;所述中低压缸1
‑
6的抽汽出口连接高压汽动煤浆柱塞泵2
‑
2的进汽口。
39.所述煤浆回热器2
‑
3的高温出浆口连接煤浆
‑
超临界水混合器2
‑
4的进浆口。
40.所述煤浆
‑
超临界水混合器2
‑
4的超临界水进口连接锅炉1
‑
3的超临界水出口。
41.所述煤浆
‑
超临界水混合器2
‑
4的出浆口连接超临界反应器2
‑
5的进浆口;所述超临界反应器2
‑
5的催化剂入口连接高压催化剂混合器2
‑
6的催化剂出口。
42.所述高压催化剂混合器2
‑
6的进水口连接高压加热器1
‑
2的高压水出口。
43.所述超临界反应器2
‑
5的气固混合物出口连接气固分离装置2
‑
7,所述气固分离装置2
‑
7 的氢气出口连接氢气收集装置2
‑
8;所述气固分离装置2
‑
7的杂质出口经过煤浆回热器2
‑
3 连接固废分离器设备2
‑
9。
44.所述固废分离器设备2
‑
9的废料出口连接废物处理装置2
‑
10;所述固废分离器设备2
‑
9 的其余产物出口经过回料泵2
‑
11连接超临界反应器2
‑
5。
45.所述锅炉1
‑
3和煤浆
‑
超临界水混合器2
‑
4之间的超临界水管道上设置有高温高压调节阀组3
‑
1。
46.所述制粉系统1
‑
4和高浓度煤浆混合器2
‑
1之间的连接管道上设置有粉量调节阀3
‑
2。所述煤粉量调节阀3
‑
2内应布置有震打、拨扫等装置防止阀组处煤粉出现堵塞情况。
47.所述除氧器1
‑
12和高浓度煤浆混合器2
‑
1之间的连接管道上设置有中温低压调节阀 3
‑
3。
48.所述中低压缸1
‑
6和高压汽动煤浆柱塞泵2
‑
2之间的连接管道上设置有调节阀3
‑
4。
49.所述高压加热器1
‑
2和高压催化剂混合器2
‑
6之间的连接管道上设置有高压中温调节阀 3
‑
5。
50.所述高压催化剂混合器2
‑
6的进料口处设置有催化剂量控制阀3
‑
6。
51.本发明的工作原理为:
52.所述超临界及以上参数煤电机组热力系统有一最大运行功率p1‑
max
,其对应锅炉1
‑
3有一最大连续蒸发量q
13
‑
max
,超临界及以上参数煤电机组热力系统1在并网运行时其实时会由电网下达一功率为p1,p1所需的锅炉蒸发量为q
13
‑1,锅炉1
‑
3在运行时的实时蒸发量为q
13
,该锅炉蒸发量下对应所需的制粉系统1
‑
4给煤量为m
14
‑
13
,制粉系统1
‑
4的实际给煤量为m
14
,制粉系统最大给煤量为m
14
‑
max
,该锅炉蒸发量下所需的循环水泵1
‑
9流量为q
19
‑
13
,循环水泵有一最大泵水量q
19
‑
max
,循环水泵1
‑
9所泵水的实时流量为q
19
。
53.所述超临界及以上参数煤电机组热力系统的工作流程为:循环水泵1
‑
9所泵出的水,依次进入精处理设备1
‑
10、低压加热器1
‑
11和除氧器1
‑
12,对入锅炉1
‑
3水进行精处理除氧和低温加热,水在离开除氧器1
‑
12后一股流入给水泵1
‑
1,其流量为q
11
,另一股流入高浓度煤浆混合器2
‑
1,其流量为q
21
,因此q
11
和q
21
的流量和应等于q
19
,q
11
和q
21
的相对大小由中温低压调节阀3
‑
3进行调节。循环水泵1
‑
9所泵出的水在离开除氧器1
‑
12后一股流入给水泵1
‑
1升压后进入高压加热器1
‑
2中进行进一步加热,从高压加热器1
‑
2流出来后,一股高压水流入至高压催化剂混合器2
‑
6,流量为q
26
,q
26
的大小主要高压中温调节阀3
‑
5进行调节,由一股高压水输入锅炉1
‑
3中的冷却壁面中进行加热,流量为q
13
,制粉系统1
‑
4制备煤粉量为m
14
,一股流入锅炉1
‑
3中,通过锅炉内的燃烧器引燃后加热锅炉1
‑
3受热壁面中的水,其给
煤量应与锅炉实时蒸发量下对应所需的给煤量相同,为m
14
‑
13
,另一股煤粉由制粉系统1
‑
4 到锅炉1
‑
3间煤粉输送管道至高浓度煤浆混合器2
‑
1,其给煤量为m
21
,考虑煤粉在管道和阀门中的附着和堆积,m
14
‑
13
和m
21
的给煤量和应小于等于m
14
,m
14
‑
13
和m
21
的相对大小由旁路中的煤粉量调节阀3
‑
2进行调节。水流在锅炉1
‑
3中加热到功率为p1所需的参数的高温高压蒸汽后,一股流入高压缸1
‑
5做功,其流量为p1所需的锅炉蒸发量为q
13
‑1,另一股经锅炉1
‑
3到高压缸1
‑
5间超临界水管路输送至煤浆
‑
超临界水混合器2
‑
4,其流量为q
13
‑
24
,因此q
13
‑1和 q
13
‑
24
的流量和应等于输入锅炉1
‑
3的流量q
11
,q
13
‑1和q
24
的相对大小由旁路中的高温高压调节阀组3
‑
1进行调节;高温高压蒸汽在高压缸1
‑
5做功后,中温中压的蒸汽流入中低压缸1
‑
6 进一步做功,一部分抽汽进入锅炉1
‑
3再热,流量为q
16
‑
13
,重新流回中低压缸1
‑
6做功,提高热力系统的做功效率,另一部分抽汽经高温高压辅汽管路输至高压汽动煤浆柱塞泵2
‑
2,其流量q
16
‑
22
由高温高压辅汽管路上的调节阀3
‑
4控制,蒸汽进入中低压缸1
‑
6和高压缸1
‑
5 后做功带动相应电系统进行发电;剩余乏汽从中低压缸1
‑
6排出后进入冷凝系统1
‑
7冷却,其流量为q
17
,后补水系统1
‑
8根据实时的运行状态对系统进行补水,其补水流量为q
18
,实时状态下相应关系应满足下列式子:
54.q
19
=q
17
+q
18
55.相应水流重新流入循环水泵1
‑
9进行升压泵送,热力系统完成相应的循环。
56.所述超临界及耦合制氢系统是同超临界及以上参数煤电机组热力系统进行耦合运行的,安装在制粉系统1
‑
4到锅炉1
‑
3间煤粉输送管道至高浓度煤浆混合器2
‑
1旁路中的煤粉量调节阀3
‑
2调节进入高浓度煤浆混合器2
‑
1的煤粉量,安装在除氧器1
‑
11到给水泵1
‑
1间低压中温水管路间至高浓度煤浆混合器2
‑
1旁路中的中温低压调节阀3
‑
3调节进入高浓度煤浆混合器2
‑
1的低压水量,煤粉在高浓度煤浆混合器2
‑
1内同水混合为低压高浓度煤浆,其煤浆质量分数ω
21
为:
57.ω
21
=m
21
/(q
21
+m
21
)
58.煤浆从高浓度煤浆混合器2
‑
1离开输入高压汽动煤浆柱塞泵2
‑
2,从中低压缸1
‑
6所抽的抽汽经高温高压辅汽管路输至高压汽动煤浆柱塞泵2
‑
2驱动其做动,将高浓度煤浆升压泵送至煤浆回热器2
‑
3进行第一步加热,加热后流入煤浆
‑
超临界水混合器2
‑
4,高浓度煤浆的压力由高压汽动煤浆柱塞泵2
‑
2的功率决定,高压汽动煤浆柱塞泵2
‑
2的功率主要由抽汽量和抽汽参数进行决定;高浓度煤浆进入煤浆
‑
超临界水混合器2
‑
4后同从锅炉1
‑
3到高压缸 1
‑
5间超临界水管路来的超临界水进行混合,混合为进料煤浆,其煤浆质量系数ω
24
为:
59.ω
24
=(m
21
+q
13
‑
24
)/(q
21
+m
21
+q
13
‑
24
)
60.实时条件下,超临界反应器2
‑
5应有一最佳入炉煤浆质量系数ω
best
,若ω
24
与ω
best
相偏离,应调节高温高压调节阀组3
‑
1、调节q
21
,煤粉量调节阀3
‑
2,调节m
21
,中温低压调节阀3
‑
3调节q
13
‑
24
使其达到最佳ω
best
。进料煤浆输送至超临界反应器2
‑
5内进行反应制氢;高压水从高压加热器1
‑
2流入高压催化剂混合器2
‑
6同催化剂进行混合,加入的催化剂的量由催化剂量控制阀3
‑
6进行控制,催化剂量由超临界反应器2
‑
5的实时反应状态进行决定, q
26
的大小主要高压中温调节阀3
‑
5进行调节,在高压催化剂混合器2
‑
6内混合好的高压催化剂溶液输送至超临界反应器2
‑
5同煤浆进行反应。
61.所述的超临界反应器2
‑
5内反应后的气固混合产物输送至气固分离装置2
‑
7进行
气固分离,氢气分离出后进入氢气收集装置2
‑
8、其他产物继续输送至固废分离器设备2
‑
9,中间经过煤浆回热器2
‑
3对其热量进行回收,预热高浓度煤浆,在固废分离器设备2
‑
9中分离后的废料进入废物处理装置2
‑
10进行后续处理,其余产物经回料泵2
‑
11升压送回超临界反应器2
‑
5进行进一步反应。
62.所述氢气收集装置2
‑
8用于本耦合制氢系统生产的氢气的短期储存,并可以对氢气进行外放燃烧,并向其余储氢和运氢设备输送氢气,氢气收集装置的内部监测压力为p
28
,从气固分离装置2
‑
7输入氢气收集装置2
‑
8的流量为q
28
同时,氢气收集装置有一最大氢气容量对应的内部压力p
28
‑
max
,当
63.p
28
≥p
28
‑
max
64.时,阀门3
‑
1、3
‑
2、3
‑
3、3
‑
4、3
‑
5、3
‑
6全部关闭,超临界耦合制氢系统的进料过程停止,但设备余料仍会支持着反应继续进行,氢气收集装置2
‑
8对所储存氢气进行外放燃烧,其燃烧氢气的流量为q
燃烧
,外放燃烧时,q
燃烧
应满足:
65.1.05q
28
≥q
燃烧
≥q
28
66.当从气固分离装置2
‑
7输入氢气收集装置2
‑
8的流量q
28
减小到一定数值(流量q
28
‑
min
),且氢气收集装置2
‑
8压力p
28
小于最大压力时,外放燃烧停止,其满足下列关系式:
67.p
28
<p
28
‑
max
,q
28
<q
28
‑
min
68.其中,q
28
‑
min
应根据实际相应制氢系统的规模进行设置。
69.本超临界及其以上参数煤电机组耦合超临界水制氢系统,主要遵从超临界及以上参数煤电机组热力系统的负荷变化,剩余功率余量用于超临界及耦合制氢,因此,所述超临界及耦合制氢系统有最小工作功率,其分别对应的给煤量为m
21
‑
min
,高压低温水量为q
21
‑
min
,超临界水量为q
13
‑
24
‑
min
,当出现下列情况之一时,超临界及耦合制氢系统停止进料,阀门3
‑
1、3
‑
2、 3
‑
3、3
‑
4、3
‑
5、3
‑
6全部关闭,系统停止制氢,由超临界及以上参数煤电机组热力系统独立运行:
70.超临界及耦合制氢系统最小工作功率对应的高浓度煤浆混合器2
‑
1最小给煤量m
21
‑
min
小于制粉系统1
‑
4的最大煤粉量m
14
‑
max
与超临界及以上参数煤电机组热力系统运行中锅炉1
‑
3 所需的锅炉1
‑
3实时煤粉量m
14
‑
13
之差;
71.超临界及耦合制氢系统最小工作功率对应的高浓度煤浆混合器2
‑
1的最小水流量q
21
‑
min
小于循环水泵1
‑
9最大泵水量q
19
‑
max
与超临界及以上参数煤电机组热力系统运行中锅炉1
‑
3 所需的实时水流量q
19
‑
13
之差;
72.超临界及耦合制氢系统最小工作功率对应的煤浆
‑
超临界水混合器2
‑
4的最小超临界水流量q
13
‑
24
‑
min
小于锅炉1
‑
3最大连续蒸发量q
13
‑
max
与超临界及以上参数煤电机组热力系统运行中高压缸1
‑
5实时功率对应的所需蒸发量q
13
‑1之差。