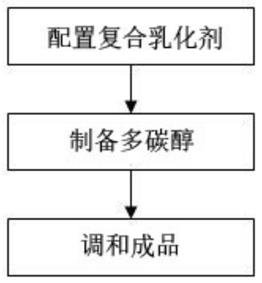
1.本发明涉及一种醇基醚液体燃料及其制备方法,属新能源及燃料技术领域。
背景技术:2.随着我国经济的快速发展,石油的需求量持续增长。而石油作为一种不可再生资源,决定了它是确保国家安全,保证国民经济持续发展和人民生活水平不断提高不可缺少的战略资源。我国是富煤炭、缺油气的国家,这样的国情决定了我国的石油来源将主要依赖于进口。另外,我国的汽车尾气排放已成为大气环境的一个主要污染源。因此,针对我国自然条件和能源资源特色,逐渐改变汽车能源结构,发展汽车清洁替代燃料,在发动机上实现高效,低污染的燃烧,控制汽车发动机尾气有害气体的排放对大气质量带来的日趋严重的影响,已经成为我国能源与环境研究中的一个十分重大和紧迫的课题。能够替代石油的产品,首先要满足原料充足,生产工艺成熟,生产量要成规模。从这一基本条件以及我们国家的能源国情来衡量,最符合条件的就是甲醇(醇醚)燃料。
3.醇醚燃料作为替代能源具有很多优点:一是甲醇的来源广泛,生产工艺成熟,生产规模较大。二是甲醇本身含氧量高,达到50%,燃烧充分,能有效降低和减少有害气体排放,有利于环境保护。三是甲醇燃烧性好,作为一种极性溶剂能够有效消除发动机系统各部位积碳,避免了因积碳的形成而引起动力下降,燃烧不充分而造成的燃料损耗。既增加了燃料的利用率,又可以保证发动机动力延长使用寿命。四是醇醚燃料在使用过程中无需对发动机进行改动即可正常使用。
4.现有技术中的甲醇汽油种类很多,但普遍存在遇水乳化、低温分层、高温气阻、对金属有腐蚀、密封部件溶胀等弊端。
5.因此针对这一问题,迫切需要开发一种全新的液体燃料及制备方法,以满足实际使用的需要。
技术实现要素:6.为了解决现有技术上的不足,本发明提供醇基醚液体燃料及其制备方法。
7.一种醇基醚液体燃料,由以下重量份数组组分构成:二甲苯15%—25%、稳定轻烃30%—55%、异辛烷20%—35%、复合乳化剂1%—3%,余量为甲醇。
8.进一步的,所述的复合乳化剂由正丁醇,油酸,二茂铁,二异丙基醚,硝酸异辛酯,异丙醇,丁醇及甲基叔丁基醚中的至少六种以任意比例混合。
9.优选的,所述的复合乳化剂由以下重量份数组组分构成:正丁醇1%—3%,二茂铁0.5%—2.1%,二异丙基醚10%—21%,硝酸异辛酯3.5%—5.8%,甲基叔丁基醚8%—19%,余量为油酸。
10.优选的,所述的复合乳化剂由以下重量份数组组分构成:丁醇3%—5.1%,二茂铁1.3%—41%,油酸7%%—21%,硝酸异辛酯3.5%—5.8%,,异丙醇8%—19%,余量为甲基叔丁基醚。
11.优选的,所述的复合乳化剂由正丁醇,油酸,二茂铁,二异丙基醚,硝酸异辛酯,异丙醇,丁醇及甲基叔丁基醚间以1:1比例混合。
12.进一步的,所述的二甲苯为煤基混合二甲苯,甲醇的纯度不低于99%。
13.一种醇基醚液体燃料的制备方法:包括如下步骤:s1,配置复合乳化剂,首先在氧气含量不大于3%的环境下对复合乳化剂原料在混合设备中以常温常压搅拌混合,并保持搅拌状态保存备用;s2, 制备多碳醇,首先将反应混合器中的氧气含量下降至1%以下,同时向反应混合器内通入低温惰性气体,并使反应混合器内气压为标准气压的至少3倍,且温度为-20℃—5℃;然后将甲醇添加到反应混合器中,并待反应混合器中温度及气压稳定后将s1步骤制备的复合乳化剂匀速添加到甲醇中与甲醇混合,使复合乳化剂的添加量为当前反应混合器中甲醇总体积的2%—5%,最后在完成复合乳化剂添加后,对混合液进行超声波均质10—30分钟,并静置得到多碳醇;s3,调和成品,在保持反应混合器中气压、温度及氧气含量不变条件下,依次将二甲苯、稳定轻烃、异辛烷添加到s2步骤得到多碳醇中,并在完成添加后对混合液进行超声波乳化30—60分钟,即可得到成品醇基醚液体燃料。
14.进一步的,所述的s2步骤向甲醇中添加原料及s3步骤向多碳醇中添加原料时,物料均沿竖直方向从下向上添加至反应混合器中。
15.进一步的,所述的反应混合器包括承载机架、混合罐、曝气管、上料头、气体分馏机构、惰性气体储气罐、负压泵、增压泵、气压传感器、温度传感器、气体传感器及驱动电路,其中所述承载机架为轴向截面呈矩形的框架结构,所述混合罐、气体分馏机构及惰性气体储气罐均嵌于承载机架内,其中所述气体分馏机构共一个并与承载机架同轴分布,所述混合罐至少两个,环绕承载机架轴线均布,且混合罐轴线与承载机架轴线平行分布,所述惰性气体储气罐位于混合罐、气体分馏机构下方,且其轴线与水平面平行分布,所述混合罐为密闭腔体结构,其上端面设一个排气口,下端面设一个进气口、一个进液口和一个排液口,其中所述排气口通过负压泵与气体分馏机构上端面连接,所述气体分馏机构下端面通过增压泵分别与混合罐的进液口连通,上端面另通过增压泵分别与惰性气体储气罐及混合罐进气口连通,所述气压传感器、温度传感器、气体传感器分别嵌于混合罐内,并与混合罐顶部连接,所述曝气管至少两条,嵌于混合罐内并与进气口连通,且各曝气管与混合罐内侧面连接并环绕混合罐轴线均布,且各曝气管间相互并联,其轴线与混合罐轴线呈0
°
—60
°
夹角,且曝气管的出气口轴线与混合罐底部呈0
°
—90
°
夹角,所述上料头嵌于混合罐内,并与混合罐同轴分布,且上料头与进液口连通,所述驱动电路与承载机架外表面连接,并分别与混合罐、气体分馏机构、负压泵、增压泵、气压传感器、温度传感器、气体传感器电气连接。
16.进一步的,所述的混合罐包括罐体、密封盖、超声波振荡机构、承载托盘,所述罐体为轴向截面呈“凵”字形腔体结构,其上端面与密封盖连接并构成闭合腔体结构,所述罐体包括保温承载外套、密封环、承载内衬、导流板、射流头,其中所述承载内衬嵌于保温承载外套内并与保温承载外套同轴分布,且所述承载内衬上端面与保温承载外套上端面间通过至少一条密封环连接,且所述保温承载外套和承载内衬间设宽度不小于5毫米的换热腔,所述换热腔对应的保温承载外套内侧面及承载内衬外侧面均设一条环绕承载内衬轴线呈螺旋结构分布的导流板,且保温承载外套内侧面及承载内衬外侧面的导流板间间隔分布,所述
射流头至少两个,嵌于换热腔内并环绕承载内衬轴线均布,所述射流头与密封环下端面连接,且射流头轴线与导流板板面平行分布,其对应的保温承载外套外侧面设一个导流口,所述超声波振荡机构至少两个,环绕承载内衬轴线嵌于承载内衬外侧面,且超声波振荡机构的振动方向与罐体轴线相交并呈30
°
—120
°
夹角,所述承载托盘至少一个,嵌于罐体的承载内衬内并与承载内衬同轴分布,所述承载托盘为轴向截面呈“h”字形槽状结构,承载托盘侧表面与承载内衬侧壁间滑动连接,且其下端面位于曝气管上端面至少5毫米处,承载托盘槽底均布孔径不大于5毫米的透气孔,且透孔总面积为承载托盘槽底面积的80%—95%,所述上料头与承载托盘下端面槽体内并于槽体侧壁间通过连接弹簧连接,且上料头上端面与槽底间间距为0—50毫米,所述超声波振荡机构间相互并联,并分别与驱动电路电气连接。
17.进一步的,所述的气体分馏机构包括分馏罐、换热器、调压泵、曝气盘、温度传感器及多通阀,其中所述分馏罐为轴线与水平面垂直分布的闭合腔体结构,其上端面设一个回流口和一个回气口,下端面设一个回液口,其中所述回流口通过负压泵与混合罐的排气口连通,所述回气口与多通阀连通,所述多通阀通过增压泵分别与混合罐的进气口和惰性气体储气罐连通,所述曝气盘至少一个,嵌于分馏罐内并与分馏罐底部连接,且曝气盘与回流口连通,所述换热器嵌于分馏罐内,与分馏罐顶部连接并同轴分布,且换热器与曝气盘间间距不大于分馏罐高度的20%,换热器和曝气盘外径为分馏罐内径的20%—90%,所述调压泵嵌于分馏罐内,与分馏罐顶部连接并与回气口连通,所述温度传感器共两个,分别与换热器及曝气盘外表面连接,且所述调压泵、温度传感器及多通阀均与驱动电路电气连接。
18.本发明一方面原料成本来源广泛、毒副作用小,环境友好性好,同时具有良好的可再生能力,且生成工艺简单,产品品质稳定,从而有效的降低生产及使用成本;另一方面较传统的汽油产品,存储转运稳定性好,极大的提高了燃料的燃性和动力能力,并同时有效的降低了燃料燃烧时的污染物排放量,从而有效的克服了传统汽油燃料的缺陷,提高了燃料使用的安全性及可靠性。
附图说明
19.下面结合附图和具体实施方式来详细说明本发明;图1为本发明制备方法流程示意图;图2为反应混合器结构示意图;图3为混合罐局部结构示意图;图4为气体分馏机构局部结构示意图。
具体实施方式
20.为使本发明实现的技术手段、创作特征、达成目的与功效易于施工,下面结合具体实施方式,进一步阐述本发明。
21.实施例1如图1所示,一种醇基醚液体燃料,由以下重量份数组组分构成:二甲苯15%、稳定轻烃30%、异辛烷20%、复合乳化剂1%,余量为甲醇。
22.优选的,所述的复合乳化剂由以下重量份数组组分构成:正丁醇1%—3%,二茂铁0.5%—2.1%,二异丙基醚10%—21%,硝酸异辛酯3.5%—5.8%,甲基叔丁基醚8%—19%,余量为
油酸。
23.同时,所述的二甲苯为煤基混合二甲苯,甲醇的纯度不低于99%。
24.一种醇基醚液体燃料的制备方法:包括如下步骤:s1,配置复合乳化剂,首先在氧气含量不大于3%的环境下对复合乳化剂原料在混合设备中以常温常压搅拌混合,并保持搅拌状态保存备用;s2, 制备多碳醇,首先将反应混合器中的氧气含量下降至1%以下,同时向反应混合器内通入低温惰性气体,并使反应混合器内气压为标准气压的3倍,且温度为-20℃;然后将甲醇添加到反应混合器中,并待反应混合器中温度及气压稳定后将s1步骤制备的复合乳化剂匀速添加到甲醇中与甲醇混合,使复合乳化剂的添加量为当前反应混合器中甲醇总体积的2%,最后在完成复合乳化剂添加后,对混合液进行超声波均质10—30分钟,并静置得到多碳醇;s3,调和成品,在保持反应混合器中气压、温度及氧气含量不变条件下,依次将二甲苯、稳定轻烃、异辛烷添加到s2步骤得到多碳醇中,并在完成添加后对混合液进行超声波乳化30分钟,即可得到成品醇基醚液体燃料。
25.本实施例中,所述的s2步骤向甲醇中添加原料及s3步骤向多碳醇中添加原料时,物料均沿竖直方向从下向上添加至反应混合器中。
26.实施例2如图1所示,一种醇基醚液体燃料,由以下重量份数组组分构成:二甲苯25%、稳定轻烃40%、异辛烷25%、复合乳化剂3%,余量为甲醇。
27.优选的,所述的复合乳化剂由正丁醇,油酸,二茂铁,二异丙基醚,硝酸异辛酯,异丙醇,丁醇及甲基叔丁基醚间以1:1比例混合。
28.进一步的,所述的二甲苯为煤基混合二甲苯,甲醇的纯度不低于99%。
29.一种醇基醚液体燃料的制备方法:包括如下步骤:s1,配置复合乳化剂,首先在氧气含量不大于3%的环境下对复合乳化剂原料在混合设备中以常温常压搅拌混合,并保持搅拌状态保存备用;s2, 制备多碳醇,首先将反应混合器中的氧气含量下降至1%以下,同时向反应混合器内通入低温惰性气体,并使反应混合器内气压为标准气压的10倍,且温度为5℃;然后将甲醇添加到反应混合器中,并待反应混合器中温度及气压稳定后将s1步骤制备的复合乳化剂匀速添加到甲醇中与甲醇混合,使复合乳化剂的添加量为当前反应混合器中甲醇总体积的5%,最后在完成复合乳化剂添加后,对混合液进行超声波均质30分钟,并静置得到多碳醇;s3,调和成品,在保持反应混合器中气压、温度及氧气含量不变条件下,依次将二甲苯、稳定轻烃、异辛烷添加到s2步骤得到多碳醇中,并在完成添加后对混合液进行超声波乳化60分钟,即可得到成品醇基醚液体燃料。
30.本实施例中,所述的s2步骤向甲醇中添加原料及s3步骤向多碳醇中添加原料时,物料均沿竖直方向从下向上添加至反应混合器中。
31.实施例3如图1所示,一种醇基醚液体燃料,由以下重量份数组组分构成:二甲苯20%、稳定轻烃55%、异辛烷21%、复合乳化剂1.5%,余量为甲醇。
32.优选的,所述的复合乳化剂由正丁醇,油酸,二茂铁,二异丙基醚,硝酸异辛酯,异丙醇,丁醇及甲基叔丁基醚中的至少六种以任意比例混合。
33.优选的,所述的复合乳化剂由正丁醇,油酸,二茂铁,二异丙基醚,硝酸异辛酯,异丙醇,丁醇及甲基叔丁基醚间以1:1比例混合。
34.本实施例中,所述的二甲苯为煤基混合二甲苯,甲醇的纯度不低于99%。
35.一种醇基醚液体燃料的制备方法:包括如下步骤:s1,配置复合乳化剂,首先在氧气含量不大于3%的环境下对复合乳化剂原料在混合设备中以常温常压搅拌混合,并保持搅拌状态保存备用;s2, 制备多碳醇,首先将反应混合器中的氧气含量下降至1%以下,同时向反应混合器内通入低温惰性气体,并使反应混合器内气压为标准气压的至少5倍,且温度为0℃;然后将甲醇添加到反应混合器中,并待反应混合器中温度及气压稳定后将s1步骤制备的复合乳化剂匀速添加到甲醇中与甲醇混合,使复合乳化剂的添加量为当前反应混合器中甲醇总体积的3%,最后在完成复合乳化剂添加后,对混合液进行超声波均质20分钟,并静置得到多碳醇;s3,调和成品,在保持反应混合器中气压、温度及氧气含量不变条件下,依次将二甲苯、稳定轻烃、异辛烷添加到s2步骤得到多碳醇中,并在完成添加后对混合液进行超声波乳化40分钟,即可得到成品醇基醚液体燃料。
36.本实施例中,所述的s2步骤向甲醇中添加原料及s3步骤向多碳醇中添加原料时,物料均沿竖直方向从下向上添加至反应混合器中。
37.实施例4如图1所示,一种醇基醚液体燃料,由以下重量份数组组分构成:二甲苯15%、稳定轻烃30%、异辛烷35%、复合乳化剂2.3%,余量为甲醇。
38.本实施例中,所述的复合乳化剂由正丁醇,油酸,二茂铁,二异丙基醚,硝酸异辛酯,异丙醇,丁醇及甲基叔丁基醚中的至少六种以任意比例混合。
39.优选的,所述的复合乳化剂由以下重量份数组组分构成:丁醇3%—5.1%,二茂铁1.3%—41%,油酸7%%—21%,硝酸异辛酯3.5%—5.8%,,异丙醇8%—19%,余量为甲基叔丁基醚。
40.此外,所述的二甲苯为煤基混合二甲苯,甲醇的纯度不低于99%。
41.一种醇基醚液体燃料的制备方法:包括如下步骤:s1,配置复合乳化剂,首先在氧气含量为0的环境下对复合乳化剂原料在混合设备中以常温常压搅拌混合,并保持搅拌状态保存备用;s2, 制备多碳醇,首先将反应混合器中的氧气含量下降至1%以下,同时向反应混合器内通入低温惰性气体,并使反应混合器内气压为标准气压的至少6.5倍,且温度为-5℃;然后将甲醇添加到反应混合器中,并待反应混合器中温度及气压稳定后将s1步骤制备的复合乳化剂匀速添加到甲醇中与甲醇混合,使复合乳化剂的添加量为当前反应混合器中甲醇总体积的4%,最后在完成复合乳化剂添加后,对混合液进行超声波均质15分钟,并静置得到多碳醇;s3,调和成品,在保持反应混合器中气压、温度及氧气含量不变条件下,依次将二甲苯、稳定轻烃、异辛烷添加到s2步骤得到多碳醇中,并在完成添加后对混合液进行超声波
乳化30—60分钟,即可得到成品醇基醚液体燃料。
42.本实施例中,所述的s2步骤向甲醇中添加原料及s3步骤向多碳醇中添加原料时,物料均沿竖直方向从下向上添加至反应混合器中。
43.需要说明的,本发明所采用的原料中:甲醇,可通过植物发酵等工艺制备得到,来源广泛,具有良好的资源再生能力,并可有效的提高诸如秸秆等农业废弃物的综合回收效率及气附加值,环境友好性好,且甲醇燃烧时燃烧充分,能有效降低和减少有害气体排放,有利于环境保护;并可能够有效消除发动机系统各部位积碳,避免了因积碳的形成而引起动力下降,燃烧不充分而造成的燃料损耗,从而既增加了燃料的利用率,又可以保证发动机动力延长使用寿命;二甲苯、稳定轻烃、异辛烷:具有碳链结构短、含碳量低且化学性能稳定,可有效降低然后时二氧化碳、一氧化碳产生量,减少车辆发动机积碳及提高燃油运输存储的安全性和可靠性的特点。
44.同时,本发明燃烧特性较传统的汽油,具有馏程长、低硫、无杂质、燃烧充分、排放达到环保最佳数值的优势,从而达到有效减少发动机积碳,减少二氧化碳排放量,并有效提高车辆动力的优势。
45.如图2—4所示,重点说明的,本发明在具体实施中,所述的反应混合器包括承载机架1、混合罐2、曝气管3、上料头4、气体分馏机构5、惰性气体储气罐6、负压泵7、增压泵8、气压传感器9、温度传感器10、气体传感器11及驱动电路12,其中所述承载机架1为轴向截面呈矩形的框架结构,所述混合罐2、气体分馏机构5及惰性气体储气罐6均嵌于承载机架1内,其中所述气体分馏机构5共一个并与承载机架1同轴分布,所述混合罐2至少两个,环绕承载机架1轴线均布,且混合罐2轴线与承载机架1轴线平行分布,所述惰性气体储气罐6位于混合罐2、气体分馏机构5下方,且其轴线与水平面平行分布,所述混合罐2为密闭腔体结构,其上端面设一个排气口21,下端面设一个进气口22、一个进液口23和一个排液口24,其中所述排气口21通过负压泵7与气体分馏机构5上端面连接,所述气体分馏机构5下端面通过增压泵8分别与混合罐2的进液口23连通,上端面另通过增压泵8分别与惰性气体储气罐6及混合罐2进气口22连通,所述气压传感器9、温度传感器10、气体传感器11分别嵌于混合罐2内,并与混合罐2顶部连接,所述曝气管3至少两条,嵌于混合罐2内并与进气口22连通,且各曝气管3与混合罐2内侧面连接并环绕混合罐2轴线均布,且各曝气管3间相互并联,其轴线与混合罐2轴线呈0
°
—60
°
夹角,且曝气管3的出气口轴线与混合罐2底部呈0
°
—90
°
夹角,所述上料头4嵌于混合罐2内,并与混合罐2同轴分布,且上料头4与进液口23连通,所述驱动电路12与承载机架1外表面连接,并分别与混合罐2、气体分馏机构5、负压泵7、增压泵8、气压传感器9、温度传感器10、气体传感器11电气连接。
46.本实施例中,所述负压泵7、增压泵8均与承载机架1上端面连接,且负压泵7、增压泵8与混合罐2、气体分馏机构5、惰性气体储气罐6间均设控制阀13。
47.需要注意的,所述的混合罐2包括罐体21、密封盖22、超声波振荡机构23、承载托盘24,所述罐体21为轴向截面呈“凵”字形腔体结构,其上端面与密封盖22连接并构成闭合腔体结构,所述罐体21包括保温承载外套211、密封环212、承载内衬213、导流板214、射流头215,其中所述承载内衬213嵌于保温承载外套211内并与保温承载外套211同轴分布,且所述承载内衬213上端面与保温承载外套211上端面间通过至少一条密封环212连接,且所述
保温承载外套211和承载内衬213间设宽度不小于5毫米的换热腔216,所述换热腔216对应的保温承载外套211内侧面及承载内衬213外侧面均设一条环绕承载内衬213轴线呈螺旋结构分布的导流板214,且保温承载外套211内侧面及承载内衬213外侧面的导流板214间间隔分布,所述射流头215至少两个,嵌于换热腔216内并环绕承载内衬213轴线均布,所述射流头215与密封环212下端面连接,且射流头215轴线与导流板214板面平行分布,其对应的保温承载外套211外侧面设一个导流口217,所述超声波振荡机构23至少两个,环绕承载内衬213轴线嵌于承载内衬213外侧面,且超声波振荡机构23的振动方向与罐体211轴线相交并呈30
°
—120
°
夹角,所述承载托盘24至少一个,嵌于罐体21的承载内衬213内并与承载内衬213同轴分布,所述承载托盘24为轴向截面呈“h”字形槽状结构,承载托盘24侧表面与承载内衬213侧壁间滑动连接,且其下端面位于曝气管3上端面至少5毫米处,承载托盘24槽底均布孔径不大于5毫米的透气孔218,且透孔218总面积为承载托盘24槽底面积的80%—95%,所述上料头4与承载托盘24下端面槽体21内并于槽体21侧壁间通过连接弹簧219连接,且上料头4上端面与槽底21间间距为0—50毫米,所述超声波振荡机构23间相互并联,并分别与驱动电路12电气连接。
48.与此同时,所述的气体分馏机构5包括分馏罐51、换热器52、调压泵53、曝气盘54、温度传感器10及多通阀55,其中所述分馏罐51为轴线与水平面垂直分布的闭合腔体结构,其上端面设一个回流口56和一个回气口57,下端面设一个回液口58,其中所述回流口56通过负压泵7与混合罐2的排气口21连通,所述回气口57与多通阀55连通,所述多通阀55通过增压泵8分别与混合罐2的进气口22和惰性气体储气罐6连通,所述曝气盘54至少一个,嵌于分馏罐51内并与分馏罐51底部连接,且曝气盘54与回流口56连通,所述换热器52嵌于分馏罐51内,与分馏罐51顶部连接并同轴分布,且换热器52与曝气盘54间间距不大于分馏罐51高度的20%,换热器52和曝气盘54外径为分馏罐51内径的20%—90%,所述调压泵53嵌于分馏罐51内,与分馏罐51顶部连接并与回气口57连通,所述温度传感器10共两个,分别与换热器52及曝气盘54外表面连接,且所述调压泵53、温度传感器10及多通阀55均与驱动电路10电气连接。
49.本发明所使用的反应混合器较传统的混合设备在混合反应时,可有效的抑制挥发性气体、原料高温蒸发及搅拌时飞溅等造成的物料损耗及环境污染,一方面有效克服了传统搅拌设备运行时易因可燃性及有毒有害气体散溢而引发的火灾、爆炸、中毒等安全事故;另一方面可有效的提高物料的综合回收利用率,降低了生产成本。
50.经过检测,本发明具体技术指标为:
51.本发明一方面原料成本来源广泛、毒副作用小,环境友好性好,同时具有良好的可再生能力,且生成工艺简单,产品品质稳定,从而有效的降低生产及使用成本;另一方面较传统的汽油产品,存储转运稳定性好,极大的提高了燃料的燃性和动力能力,并同时有效的降低了燃料燃烧时的污染物排放量,从而有效的克服了传统汽油燃料的缺陷,提高了燃料使用的安全性及可靠性。
79.以上显示和描述了本发明的基本原理和主要特征和本发明的优点。本行业的技术人员应该了解,本发明不受上述实施例的限制,上述实施例和说明书中描述的只是说明本发明的原理,在不脱离本发明精神和范围的前提下,本发明还会有各种变化和改进,这些变化和改进都落入要求保护的本发明范围内。本发明要求保护范围由所附的权利要求书及其等效物界定。