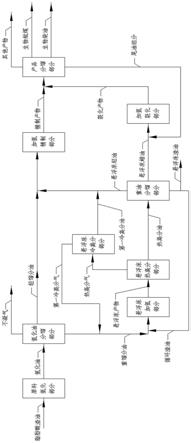
1.本发明涉及一种脂肪酸渣油组合氢化方法;特别的讲本发明涉及一种脂肪酸渣油组合氢化制取生物质液体燃料的方法。
背景技术:2.生物质液体燃料是一种可再生燃料资源,它与矿物燃料相比,具有可再生性、优良的生物可降解性、低含硫量和低污染物排放等特点,是一种真正的绿色能源,将成为石油燃料的理想替代能源。
3.油酸提取过程中剩余的重组分渣油,含有脂肪酸和植物沥青等组分,目前有些工艺是采用直接蒸馏的方法提取出一部分脂肪酸,由于不饱和脂肪酸热稳定性差,直接加热蒸馏会导致不饱和脂肪酸受热缩合,为后续生产生物柴油的过程带来困难。
技术实现要素:4.为了克服现有技术中存在的缺点和不足,本发明的目的在于提供一种脂肪酸渣油组合氢化方法。
5.本发明的目的通过下述技术方案实现:一种脂肪酸渣油组合氢化方法,包括如下步骤:
6.(1)在原料氢化反应部分,将脂肪酸渣油在催化剂存在条件下,与氢气在压力为0.001~3.0mpa、温度为80~250℃、氢气/油体积比为50~1000:1、催化剂/油质量比为0.001%~2.0%的条件下,完成不饱和脂肪酸氢化反应,生成一个由氢气、杂质组分和氢化油组成的氢化反应产物;
7.(2)在氢化油分离部分,所述氢化反应产物分离为气相和氢化油,所述气相经冷却并分水后返回氢化反应部分作为循环气使用;
8.(3)在氢化油分馏部分,所述氢化油在压力为
‑
0.1~0.5mpa、温度为180~380℃条件下,分馏为塔顶不凝气、轻馏分油和重馏分油,所述不凝气从塔顶排出作为装置燃料气,所述轻馏分油送至固定床加氢精制部分,所述重馏分油送至悬浮床加氢部分;
9.(4)在悬浮床加氢部分,所述重馏分油在催化剂存在条件下,在温度为200~500℃、压力为3.0~25.0mpa、氢气/油体积比为50~2000:1、催化剂/油质量比为0.001%~5.0%的条件下,完成加氢反应,生成一个由氢气、水、常规气体烃和常规液体烃组成的悬浮床产物;
10.(5)在悬浮床热高压分离部分,所述悬浮床产物被分离为热高分气和热高分油,热高分气送至加氢精制部分,热高分油送至重油分离部分;
11.(6)在悬浮床冷高压分离部分,所述热高分气冷却并分离为:一个主要由氢气组成的第一冷高分气气体,一个主要由常规气体烃、杂质组分、常规液体烃组成的第一冷高分油液体,所述第一冷高分油液体送至加氢精制反应部分;
12.(7)在重油分离部分,所述热高分油经过精馏工艺分离出悬浮床轻油、悬浮床蜡油
和悬浮床渣油;悬浮床轻油送至加氢精制部分,悬浮床蜡油送至加氢裂化部分,悬浮床渣油大部分返回悬浮反应部分,少量外排;
13.(8)在加氢精制部分,所述轻馏分油、第一冷高分油和悬浮床轻油汇合,在加氢精制催化剂存在条件下,与氢气在温度为170~420℃、压力为3.0~20.0mpa、氢气/原料油体积比为50~3000:1、催化剂体积空速为0.05
‑
5h
‑
1的条件下,完成加氢精制反应,生成一个由氢气、杂质组分、常规气体烃、常规液体烃组成的加氢精制反应产物;
14.(9)在加氢精制冷高压分离部分,所述加氢精制反应产物冷却并分离为:一个主要由氢气组成的第二冷高分气气体,一个主要由常规气体烃、杂质组分、常规液体烃组成的第二冷高分油液体;
15.(10)在加氢裂化部分,在加氢裂化催化剂存在条件下,所述悬浮床蜡油与氢气在温度为300~500℃、压力为3.0~20.0mpa、氢气/蜡油体积比为50~3000:1、催化剂体积空速为0.05
‑
5h
‑
1的条件下,完成加氢裂化反应,生成一个由氢气、杂质组分、常规气体烃、常规液体烃组成的裂化反应产物;
16.(11)在加氢裂化冷高压分离部分,所述裂化反应产物冷却并分离为:一个主要由氢气组成的第三冷高分气气体,一个主要由常规气体烃、杂质组分、常规液体烃组成的第三冷高分油液体;
17.(12)在产品分离部分,所述第二冷高分油液体和第三冷高分油液体汇合,经过精馏工艺分离出气体、生物轻油、生物航煤、生物柴油和尾油组分,气体作为装置燃料气使用,至少一部分尾油组分返回加氢裂化反应部分循环裂化。
18.优选的,所述步骤(6)中,至少一部分所述第一冷高分气体返回悬浮床反应部分形成循环氢气;所述步骤(9)中,至少一部分第二冷高分气气体返回加氢精制反应部分形成循环氢气;所述步骤(11)中,至少一部分第三冷高分气气体返回加氢裂化反应部分形成循环氢气。
19.优选的,所述步骤(1)中,氢化反应部分的操作条件为:温度为150~200℃,压力为0.01~1.0mpa,氢气/油体积比为100~500:1,催化剂/油质量比为0.01%~1.0%;所述步骤(3)中,氢化油分馏部分的操作条件为:压力为
‑
0.09~
‑
0.05mpa,温度为220~350℃。
20.优选的,所述步骤(4)中,悬浮床加氢反应部分的操作条件为:温度320~450℃,压力8.0~20.0mpa,氢气/原料油体积比为300~1500:1,催化剂/油质量比为0.01%~3.0%。
21.优选的,所述步骤(6)中,在悬浮床冷高压分离部分,在热高分气进入冷高压分离器之前,向热高分气中注入洗涤水,热高分气先降低温度至200℃以下,再与洗涤水混合成注水后热高分气;所述悬浮床冷高压分离部分包含注水后热高分气的冷却、分离步骤,注水后热高分气先降温至30~70℃,在此降温过程中,注水后热高分气在冷高压分离器中分离为:一个主要由氢气组成的第一冷高分气气体,一个主要由常规气体烃、常规液体烃和溶解氢组成的第一冷高分油液体和一个主要由水组成的溶解有硫化氢、氨的第一冷高分水液体。
22.优选的,所述步骤(8)中,加氢精制反应部分的操作条件为:温度为260~380℃,压力为5.0~15.0mpa,氢气/原料油体积比为500~2000:1,加氢精制催化剂空速为0.1~1.0hr
‑
1;所述步骤(10)中,加氢裂化反应部分的操作条为:温度为320~450℃,压力为5.0~15.0mpa,氢气/原料油体积比为300~1500:1,催化剂空速为0.2~2.0hr
‑
1。
23.优选的,所述步骤(9)中,在加氢精制冷高压分离部分,在加氢精制反应产物进入冷高压分离器之前,向反应产物注入洗涤水,加氢精制反应产物先降低温度至200℃以下,再与洗涤水混合成注水后加氢精制反应产物;所述加氢精制冷高压分离部分包含注水后加氢精制反应产物的冷却、分离步骤,注水后加氢精制反应产物先降温至30~70℃,在此降温过程中,注水后加氢精制反应产物在冷高压分离器中分离为:一个主要由氢气组成的第二冷高分气气体,一个主要由常规气体烃、常规液体烃和溶解氢组成的第二冷高分油液体和一个主要由水组成的溶解有硫化氢、氨的第二冷高分水液体。
24.优选的,所述步骤(11)中,在加氢裂化冷高压分离部分,在加氢裂化反应产物进入冷高压分离器之前,向反应产物注入洗涤水,加氢裂化反应产物先降低温度至200℃以下,再与洗涤水混合成注水后加氢裂化反应产物;所述加氢裂化冷高压分离部分包含注水后加氢裂化反应产物的冷却、分离步骤,注水后加氢裂化反应产物先降温至30~70℃,在此降温过程中,注水后加氢裂化反应产物在冷高压分离器中分离为:一个主要由氢气组成的第三冷高分气气体,一个主要由常规气体烃、常规液体烃和溶解氢组成的第三冷高分油液体和一个主要由水组成的溶解有硫化氢、氨的第三冷高分水液体。
25.优选的,所述步骤(9)和所述步骤(11)中,加氢精制反应产物和加氢裂化反应产物共用冷高压分离部分。
26.优选的,所述步骤(9)和所述步骤(11)中,在冷高压分离步骤之前,增设一个热高压分离步骤,加氢精制反应产物和加氢裂化反应产物先进入操作温度为180~300℃的热高压分离步骤并分离为:一个由氢气组成的第二热高分气气体,一个由常规液体烃和溶解氢组成的第二热高分油液体;第二热高分气气体进入冷高压分离部分,第二热高分油液体在热高分油液体分离部分分离出生物航煤和生物柴油产品。
27.本发明的有益效果在于:本发明的方法先将不饱和脂肪酸在低压下氢化,再经分馏—分路高压加氢工艺,将脂肪酸渣油转化为高附加值的生产生物柴油和生物航煤等生物质液体燃料,具有现实的经济意义和环保意义。
28.本发明可以解决脂肪酸渣油在加工过程中存在的缩合问题,为脂肪酸渣油的加工利用提供可靠的技术保证,可以提高产品收率,有利于增加企业的经济效益和环境效益,更可以推动再生能源的使用,促进低碳经济、循环经济和新能源的开发利用,降低二氧化碳等温室气体的排放,响应国际碳中和策略,为减缓全球变暖做出巨大贡献。
附图说明
29.图1是本发明的工艺流程见图。
具体实施方式
30.为了便于本领域技术人员的理解,下面结合实施例及附图1对本发明作进一步的说明,实施方式提及的内容并非对本发明的限定。
31.本发明所述常规沸点指的是物质在一个大气压下的气液平衡温度。
32.本发明所述的常规气体烃指的是常规条件下呈气态的烃类,包括甲烷、乙烷、丙烷、丁烷。
33.本发明所述的常规液体烃指的是常规条件下呈液态的烃类,包括戊烷及沸点更高
的烃类。
34.本发明所述的比重,除非特别说明,指的是常压、15.6℃条件下液体密度与常压、15.6℃条件下水密度的比值。
35.本发明所述的生物轻油指的是常规沸点为<180℃的烃类。
36.本发明所述的生物航煤指的是常规沸点为180~300℃的烃类。
37.本发明所述的生物柴油指的是常规沸点为180~370℃的烃类。
38.本发明所述的杂质组分指的是原料中非烃组分的转化物如水、氨、硫化氢等。
39.本发明所述的组分的组成或浓度或含量或收率,除非特别说明,均为重量基准值。
40.本发明所述脂肪酸渣油,是指油酸提取过程中剩余的重组分渣油,以及其他生物油脂提取过程剩余的重组分渣油,一般含有脂肪酸和植物沥青等组分。
41.见图1,一种脂肪酸渣油组合氢化方法,包括如下步骤:
42.(1)在原料氢化反应部分,将脂肪酸渣油在催化剂存在条件下,与氢气在压力为0.001~3.0mpa、温度为80~250℃、氢气/油体积比为50~500:1、催化剂/油质量比为0.001%~2.0%的条件下,完成不饱和脂肪酸氢化反应,生成一个由氢气、杂质组分和氢化油组成的氢化反应产物。
43.本发明所述的氢化一词,指的是在氢气和合适的催化剂存在条件下,所述脂肪酸渣油发生的耗氢的反应过程,一般该过程将完成大部分不饱和脂肪酸的饱和。
44.氢化反应部分的操作条件最好为:温度为150~200℃,压力为0.01~1.0mpa,氢气/油体积比为100~500:1,催化剂/油质量比为0.01%~1.0%。
45.(2)在氢化油分离部分,在氢化油反应产物进入分离器之前,通常先降温至150℃,再经分离器分离为气相和氢化油液相。所述气相通常冷却至30~50℃,分离出气体中的水相得到脱水气体,所述脱水气体返回氢化反应部分循环使用。
46.(3)在氢化油分馏部分,所述氢化油在压力为
‑
0.1~0.5mpa、温度为180~380℃条件下,分馏为塔顶不凝气、轻馏分油和重馏分油,所述不凝气从塔顶排出作为装置燃料气,所述轻馏分油送至固定床加氢精制部分,所述重馏分油送至悬浮床加氢部分。
47.氢化油分馏部分的操作条件做好为:压力为
‑
0.09~
‑
0.05mpa,温度为220~350℃。
48.(4)在悬浮床加氢部分,所述重馏分油在催化剂存在条件下,在温度为200~500℃、压力为3.0~25.0mpa、氢气/油体积比为50~2000:1、催化剂/油质量比为0.001%~5.0%的条件下,完成加氢反应,生成一个由氢气、水、常规气体烃和常规液体烃组成的悬浮床产物。
49.(5)在悬浮床热高压分离部分,所述悬浮床产物被分离为热高分气和热高分油。
50.(6)在悬浮床冷高压分离部分,所述热高分气冷却并分离为:一个主要由氢气组成的第一冷高分气气体,一个主要由常规气体烃、杂质组分、常规液体烃组成的第一冷高分油液体。
51.在所述热高分气进入冷高压分离器之前,通常向热高分气中注入洗涤水。所述热高分气通常先降低温度至200℃以下,再与洗涤水混合。
52.所述悬浮床冷高压分离部分包含注水后热高分气的冷却、分离步骤。在此,所述的注水后热高分气通常先降温至30~70℃,在此降温过程中,所述注水后热高分气在冷高压
分离器中分离为:一个主要由氢气组成的第一冷高分气气体,一个主要由常规气体烃、常规液体烃和溶解氢组成的第一冷高分油液体和一个主要由水组成的溶解有硫化氢、氨的第一冷高分水液体。
53.如前所述,至少一部分(通常为80~100%)所述第一冷高分气气体返回悬浮床加氢反应部分形成循环氢气,以提供反应部分必须的氢气量和氢浓度。
54.本发明所述的悬浮床加氢一词,指的是在氢气和催化剂存在条件下,在合适的温度下,所述重馏分油发生的耗氢的反应过程,其最低的反应深度应具备最低限度的工业意义:即为加氢精制和加氢裂化部分提供合适的加氢原料,一般该过程将完成大分子烃类的加氢裂解反应,一般该过程将完成大部分含氧化合物的脱氧反应。
55.悬浮床加氢反应部分的操作条件最好为:温度为320~450℃、压力为8.0~20.0mpa、氢气/原料油体积比为300~1500:1,催化剂/油质量比为0.01%~3.0%。
56.(7)在重油分离部分,所述热高分油经过精馏工艺分离出悬浮床轻油、悬浮床蜡油和悬浮床渣油;悬浮床轻油送至加氢精制部分,悬浮床蜡油送至加氢裂化部分,悬浮床渣油大部分返回悬浮床进料,少量外排。
57.本发明所述悬浮床轻油通常指沸点低于350℃的馏分,所述悬浮床蜡油通常指沸点在350~480℃的馏分,所述悬浮床渣油通常指沸点高于480℃的馏分。
58.(8)在加氢精制部分,所述轻馏分油、第一冷高分油、悬浮床轻油汇合,在加氢精制催化剂存在条件下,与氢气在温度为170~420℃、压力为3.0~20.0mpa、氢气/原料油体积比为50~3000:1、催化剂体积空速为0.05
‑
5h
‑1的条件下,完成加氢精制反应,生成一个由氢气、杂质组分、常规气体烃、常规液体烃组成的加氢精制反应产物。
59.本发明所述的加氢精制一词,指的是在氢气和合适的催化剂存在条件下,所述轻馏分油、第一冷高分油、悬浮床轻油混合后发生的耗氢的反应过程,其最低的反应深度应具备最低限度的工业意义:即生产出合格的生物柴油和生物航煤,一般该过程将完成对原料油中所有不饱和键的饱和;一般该过程将脱除原料油中全部的氧、硫和氮。
60.加氢精制反应部分的操作条件最好为:温度为260~380℃、压力为5.0~15.0mpa、加氢精制催化剂空速为0.1~1.0hr
‑1、氢气/原料油体积比为500~2000:1。
61.所述加氢精制反应部分,使用的加氢精制催化剂可以是一种或两种或多种催化剂的串联组合或和混装。
62.(9)在加氢精制冷高压分离部分,在加氢精制反应产物进入冷高压分离器之前,通常向反应产物注入洗涤水。所述加氢精制反应产物通常先降低温度至200℃以下,再与洗涤水混合成注水后加氢精制反应产物。
63.所述加氢精制冷高压分离部分包含注水后加氢精制反应产物的冷却、分离步骤。在此,所述的注水后加氢精制反应产物通常先降温至30~70℃,在此降温过程中,所述注水后加氢精制反应产物在冷高压分离器中分离为:一个主要由氢气组成的第二冷高分气气体,一个主要由常规气体烃、常规液体烃和溶解氢组成的第二冷高分油液体和一个主要由水组成的溶解有硫化氢、氨的第二冷高分水液体。
64.如前所述,至少一部分(通常为80~100%)所述第二冷高分气气体返回加氢精制反应部分和或悬浮床反应部分形成循环氢气,以提供反应部分必须的氢气量和氢浓度。
65.(10)在加氢裂化部分,在加氢裂化催化剂存在条件下,所述悬浮床蜡油与氢气在
温度为300~500℃、压力为3.0~20.0mpa、氢气/蜡油体积比为50~3000:1、催化剂体积空速为0.05
‑
5h
‑1的条件下,完成加氢裂化反应,生成一个由氢气、杂质组分、常规气体烃、常规液体烃组成的裂化反应产物。
66.加氢裂化反应部分的操作条件最好为:温度为320~450℃、压力为5.0~15.0mpa、催化剂空速为0.2~2.0hr
‑1、氢气/原料油体积比为300~1500:1。
67.所述加氢裂化反应部分,其原料蜡油性质的不同和加氢深度不同,其操作条件的变化范围很宽,应根据具体的过程条件确定。
68.所述加氢裂化反应部分,使用的加氢裂化催化剂可以是一种或两种或多种催化剂的串联组合或和混装;
69.所述加氢裂化反应部分,其催化剂空速应控制在一个合理的范围内,将单程转化率控制在合理的范围(一般单程转化率为40~70%,最好单程转化率为50~60%),尽可能减少过度裂化反应产生低碳数烃类,以提高生物柴油和生物航煤收率。
70.(11)在加氢裂化冷高压分离部分,在加氢裂化反应产物进入冷高压分离器之前,通常向反应产物注入洗涤水。所述加氢裂化反应产物通常先降低温度至200℃以下,再与洗涤水混合成注水后加氢裂化反应产物。
71.所述加氢裂化冷高压分离部分包含注水后加氢裂化反应产物的冷却、分离步骤。在此,所述的注水后加氢裂化反应产物通常先降温至30~70℃,在此降温过程中,所述注水后加氢裂化反应产物在冷高压分离器中分离为:一个主要由氢气组成的第三冷高分气气体,一个主要由常规气体烃、常规液体烃和溶解氢组成的第三冷高分油液体和一个主要由水组成的溶解有硫化氢、氨的第三冷高分水液体。
72.如前所述,至少一部分(通常为80~100%)所述第三冷高分气气体返回加氢裂化反应部分形成循环氢气,以提供反应部分必须的氢气量和氢浓度。
73.(12)产品分离部分,是自第二冷高分油液体和第三冷高分油液体中分离出生物柴油产品、生物航煤产品和尾油组分的步骤。在此,所述第二冷高分油液体和第三冷高分油液体先分别降低压力后再混合,通常压力降至0.5~4.0mpa形成气、液混相物流,然后经过分离和或分馏等过程完成分离,通常分离为气体、生物轻油、生物航煤、生物柴油和尾油组分等,至少一部分尾油组分返回加氢裂化反应部分循环裂化。
74.本发明所述的加氢裂化反应部分的加氢裂化反应一词,指的是在氢气和合适的裂化催化剂存在条件下,蜡油发生的耗氢的裂化过程,其最低的反应深度应具备最低限度的工业意义:达到一定的裂化转化率(一般单程转化率为40~70%,最好单程转化率为50~60%),其裂化催化剂应具有较高的裂化选择性,以期获得更高的柴油和航煤收率收率。
75.为了实施本发明,加氢精制反应产物和加氢裂化反应产物可以共用冷高压分离部分,该流程仍在本发明的权利范围之内,它只是将加氢精制和加氢裂化的冷高压分离步骤合并,具有节省能耗的优点。
76.为了实施本发明,在冷高压分离步骤之前,可以增设一个热高压分离步骤,在该流程中,加氢精制反应产物和加氢裂化反应产物先进入操作温度通常为180~300℃,最好为200~250℃的热高压分离步骤并分离为:一个由氢气组成的第二热高分气气体,一个由常规液体烃和溶解氢组成的第二热高分油液体。第二热高分气气体进入冷高压分离部分,第二热高分油液体在热高分油液体分离部分(包含分离和或分馏过程)分离出生物航煤和生
物柴油产品。第二热高分油液体分离部分与前述产品分离部分,可以部分共用也可以全部共用。该流程仍在本发明的权利范围之内,它只是增加了一个分离步骤,具有节省能耗的优点。
77.上述实施例为本发明较佳的实现方案,除此之外,本发明还可以其它方式实现,在不脱离本发明构思的前提下任何显而易见的替换均在本发明的保护范围之内。