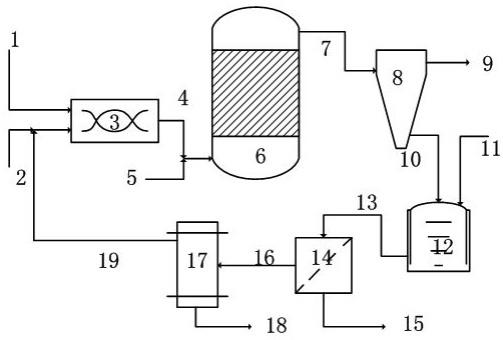
1.本发明涉及含硫原料油加工利用领域,具体地,涉及一种生产燃料油的方法和系统及其应用以及燃料油及其应用。
背景技术:2.随着全球环保法规日趋严格,在清洁汽柴油完成质量升级换代后,清洁的低硫船用燃料油将成为未来几年重点关注的油品之一。国际海事组织《国际防止船舶造成污染公约》规定,自2020年1月起在海上一般区域航行所用的船用燃料油的硫质量分数由现在的不超过3.5%降至不超过0.5%;在排放控制区域航行时,船用燃料油的硫质量不应超过0.1%。通常船用燃料油主要分为两大类,即馏分型燃料油和残渣型燃料油。馏分型燃料油主要适用于中速船舶发动机;而残渣型燃料油一般由重油和轻质馏分混合而成,它发热量大、燃烧性能好、贮存稳定、腐蚀小,是用途广泛的优良燃料,尤其是大马力中低速船舶发动机如大型远洋船舶的最经济理想燃料。高硫残渣型船用燃料油以价格优势占整个市场约70%的份额,馏分型船用燃料油约占25%,其余为低硫燃料油和少量液化天然气。
3.cn109705909a公开了一种由煤焦油生产船用燃料油的方法,具体包括:脱水和机械除杂后的煤焦油全馏分原料引入浆态床加氢反应器中进行加氢处理;将所述加氢处理后得到的浆态床加氢反应器流出物依次进行分离、常压分馏和减压分馏,得到常顶油、常一线油、减一线油和减底油;将常一线油和部分减底油形成的混合物作为船用轻燃料油产品,以及将减一线油和剩余的减底油形成的混合物作为船用重燃料油产品。采用本方法虽然可以获得低硫船用燃料油产品,实际上是将好的品质油品进行勾兑,不能达到物尽其用的目的。
4.cn103695031a公开了一种由煤焦油原料生产柴油兼产船用燃料油调和组分的方法:煤焦油全馏分原料与氢气混合后进入预加氢浆态床反应器进行反应,预加氢产物经气液分离和分馏后,分出轻组分和重组分,其中部分重组分作为船用燃料油,其余重组分和轻组分进一步进行加氢提质以生产清洁柴油。该方法氢气消耗量巨大,副产柴油组分的润滑性不好,不能满足国v/国vi柴油标准。
5.cn106811242b公开了一种环保低碳高热值船用燃料油,其配方组成以重量份计算,包括船用燃料油的主要原料600~750kg,软水250~350kg,乳化液80~120kg十六烷值提高剂1~3kg,联苯0.05~0.15kg,聚异丁烯胺0.15~0.3kg,苯骈三氮唑0.005~0.015kg,二茂铁0.3kg~0.5kg。经500khz高频率、25kw大功率超声波微乳化机和均质高速剪切机混合成船用燃料油,船用馏分燃料油是清亮透明的,三年不变色,油水不分层。该发明产品适合船用柴油机主机和发电机使用,具有环保、低碳、节能、高热值、低成本、防锈、防腐蚀等优点,但实际上是将好的品质油品,添加部分化学添加剂,达到满足船用燃料油标准要求,不能适应广泛原料生产低硫船用燃料油的目的。
6.碱金属与杂原子和/或一种或多种重金属中的一部分反应即碱金属脱硫法能够改善原料品质,但目前该方法反应过程效率低,特别是碱金属的利用率不高,产物中含有未反应的碱金属,后续需要进一步处理产品中未反应的碱金属,以满足低硫船用燃料油的要求。
碱金属脱硫技术在生产低硫船燃领域如何实现高效的应用,是炼油领域亟需攻克的难题。
7.
技术实现要素:8.针对现有技术的不足,本发明提供一种生产燃料油的方法,该方法可将劣质廉价的重质渣油等含硫原料油转化为低硫船用燃料油,碱金属利用效率高,过程安全可靠。
9.碱金属是一种强还原剂,但是采用碱金属代替传统加氢催化剂还原原料油中的金属、硫、氮、氧等杂质却鲜有研究,其主要是因为原料油中的金属、硫、氮、氧等杂质同碳原子结合,被有机物包裹存在于有机相中,碱金属作为无机相难于同原料油中的金属、硫、氮、氧等杂质进行有效的接触无法进行反应。采用间歇式或连续式的搅拌釜反应器,强化碱金属进行分散的同时进行加氢脱金属、加氢脱硫、加氢脱氧反应被本领域技术人员认为是最有效的方式,但是同样存在如下问题导致无法工业应用:(1)间歇式搅拌釜反应器不能连续操作,效率低;(2)连续搅拌釜反应器存在物料停留时间无法精准控制的问题,例如有些没有反应的原料油和碱金属会流出反应器或者某些物料始终停留在反应器中。
10.发明人经过深入研究发现,虽然碱金属同原料油由于极性的不同导致碱金属很难分散在原料油中,即使强制分散,放置后很快会导致碱金属无机相聚集同原料油有机相分离,但是碱金属同原料油预反应后的碱金属硫化物相比碱金属更易分散在原料油中,碱金属硫化物类似两性表面活性剂具有极性和非极性,极大地促进了碱金属在原料油中的分散,并且保持稳定的分散状态。
11.鉴于发明人在研究中的重大发现,本发明提出将含硫原料油和碱金属混合原料经过混合器后特别是在较高的温度下混合,会有部分碱金属与原料中硫发生反应,生成无机化合物碱金属硫化物,促使混合物料介导能力发生变化,生成的碱金属离子与有机化合物形成稳定的cation-π作用,促进了无机化合物碱金属在有机化合物原料油中的分散。
12.同时,本发明还设计了连续反应系统,解决常规的由于间歇式搅拌釜反应器不能连续操作,效率低;连续搅拌釜反应器存在物料停留时间无法精准控制的问题,例如有些没有反应的原料油和碱金属会流出反应器或者某些物料始终停留在反应器中的技术问题。
13.根据本发明的第一方面,提供一种生产燃料油的方法,该方法包括:(1)将含硫原料油与碱金属接触进行预反应得到预反物料,所述预反应在非临氢条件下进行,优选预反应温度为200℃~400℃,更优选为300℃~380℃;(2)将所述预反物料与供氢剂接触进行加氢反应;(3)将步骤(2)获得的物料经过分离后获得液相产品燃料油和固体混合物。
14.优选地,步骤(1)中,所述非临氢条件是指预反应过程加入少量或不加入供氢剂,优选供氢剂与碱金属摩尔比小于0.5。
15.优选地,步骤(1)中,碱金属以熔融碱金属形式提供。
16.优选地,步骤(1)中,碱金属为锂、钠、钾、铷、铯和钫中的一种或多种。
17.步骤(1)中,碱金属与所述含硫原料油中硫的质量比为0.8~3.0:1,优选为1.2~2.5:1,更优选为1.1~1.4:1。
18.优选地,所述含硫原料油包含碳原子、杂原子和重金属中的一种或多种。
19.优选地,所述杂原子包括硫和/或氮。
20.优选地,所述含硫原料油硫含量为1.0wt%以上,优选为1.8~8.0wt%,更优选为2~3wt%。
21.优选地,优选所述含硫原料油密度为980-1000 kg/m3,和/或重金属含量为110-150wppm,和/或残炭含量为7-10wt%,和/或粘度为800-20000cst。
22.更优选,所述原料油为重质渣油、页岩油、油砂油中的一种或多种。
23.进一步优选,所述重质渣油为原油加工过程中的,常压渣油、减压渣油、裂化渣油、渣油裂化柴油和催化柴油中的一种或多种。
24.优选地,步骤(1)中,所述接触在混合器内进行。
25.优选地,所述的混合器为管道混合器、液液搅拌混合器、漩涡混合器和静态混合器中的一种或多种。
26.优选所述混合器包括密闭进料斗、混合机身、驱动轴组件、带轮机构、电机;所述的混合机身包括固定在混合机身内部的定磨盘以及用于与定磨盘配合的动磨盘;动磨盘与所述驱动轴组件、带轮机构、电机连接,提供动力源;设定定磨盘与动磨盘一一对应为一组,优选在驱动轴组件纵向上依次设置1~7组,优选设置2~4组。
27.更优选混合器内的混合过程包括:含硫原料油与熔融状态下的碱金属源从混合器顶部进入密闭进料斗,然后进入到混合机身,定磨盘被固定在混合机身上而处于相对静止状态;电机提供动力,通过带轮机构进行动力传动,使得驱动轴组件开始运行,此时动磨盘带动相对应的定磨盘发生旋转,反应物料由上至下的流动过程中被充分混合。
28.优选地,步骤(2)所述供氢剂为至少含一个氢原子的物质,优选为氢气和/或包含至少一个碳原子和至少一个氢原子的物质。
29.优选地,所述供氢剂为氢气和/或c1-c5的低碳烃,更优选所述低碳烃为甲烷、乙烷、丙烷、丁烷、戊烷、乙烯、丙烯、丁烯、戊烯和二烯中的一种或多种,优选所述供氢剂为氢气和/或乙烷。
30.优选地,步骤(2)所述的供氢剂用量以氢气计,为1.0~3.0摩尔氢气/摩尔硫,优选为1.5~2.5摩尔氢气/摩尔硫。
31.优选地,步骤(2)所述的加氢反应的条件包括:操作压力为4.0~10.0mpa,优选为6.0~8.0mpa;和/或反应温度为200℃~430℃,优选为300℃~380℃,更优选为365℃~380℃。
32.优选地,步骤(2)在反应器中进行,所述的反应器为悬浮床反应器、沸腾床反应器、固定床反应器和cstr反应器中的一种或多种。
33.优选所述反应器为悬浮床反应器,操作条件包括:反应压力为4.0~10.0mpa,优选为6.0~8.0mpa;反应温度为200℃~430℃,优选为300℃~380℃,更优选为365℃~380℃。
34.优选地,步骤(2)在催化剂存在下发生,所述催化剂的活性金属元素包括钼、镍和钴中的一种或多种,优选所述催化剂为金属钼、金属镍、金属钴、钼合金、镍合金、钴合金、氧化钼、氧化镍和氧化钴中的一种或多种;优选所述钼合金为含镍和/或钴的钼合金,优选所述镍合金为含钴和/或钼的镍合金。
35.优选地,步骤(3)中所述的分离采用旋流分离、离心分离、萃取分离、过滤分离和沉降分离中的一种或多种;优选采用旋流分离,更优选所述的旋流分离的操作温度为150℃~380℃,优选为200℃~330℃,更优选为280~290℃。
36.优选地,进行步骤(3)所述分离前,该方法包括:将步骤(2)获得的物料于加氢反应条件下进行稳定处理,稳定时间为1h~6h,优选为2~3h。
37.优选地,该方法还包括:步骤(4),将步骤(3)获得的固体混合物与能够溶解碱金属硫化物的极性溶剂混合,固体混合物中的碱金属硫化物溶解于极性溶剂,从而实现包括金属硫化物和胶质沥青质的固体的分离。
38.优选地,步骤(4)中所述的极性溶剂选自n, n-二甲基苯胺、喹啉、2-甲基四氢呋喃、苯、四氢呋喃、环己烷、氟苯、三氟苯、甲苯、二甲苯、四乙二醇二甲醚、二甘醇二甲醚、异丙醇、乙基丙醛、碳酸二甲酯、二甲氧基醚、二甲基亚丙基脲、乙醇、乙酸乙酯、碳酸亚丙酯、碳酸亚乙酯和碳酸二乙酯中的一种或多种。
39.优选地,该方法还包括:步骤(5),将所述步骤(4)中获得的含碱金属硫化物的极性溶剂引入电解单元,将碱金属硫化物电解生成碱金属和硫磺,碱金属循环返回作为原料使用。
40.优选地,该方法包括:(1)含硫原料油与碱金属在混合器内进行预反应得到预反物料,所述预反应在非临氢条件下进行,预反应温度为200℃~400℃,优选为300℃~380℃;(2)将所述预反物料与供氢剂接触进行加氢反应;(3)将步骤(2)获得的物料经过分离后获得液相产品燃料油和固体混合物;(4)将步骤(3)获得的固体混合物与能够溶解碱金属硫化物的极性溶剂混合,碱金属硫化物溶解于极性溶剂,从而实现包括金属硫化物和胶质沥青质的固体的分离;(5)将步骤(4)中获得的含碱金属硫化物的极性溶剂引入电解单元,将碱金属硫化物电解生成碱金属和硫磺,碱金属循环作为原料使用。
41.根据本发明的第二方面,本发明提供本发明所述的方法得到的燃料油。
42.根据本发明的第三方面,本发明提供本发明所述的方法在生产低硫船用燃料油中的应用。
43.根据本发明的第四方面,本发明提供本发明所述的燃料油作为船用燃料油的应用。
44.根据本发明的第五方面,本发明提供一种生产燃料油的系统,该系统包括:(1)预反应单元,所述预反应单元用于含硫原料油与碱金属接触进行预反应得到预反物料;(2)加氢反应单元,用于预反物料与供氢剂接触进行加氢反应;(3)分离单元,用于分离加氢反应物料。
45.优选地,所述的预反应单元包括混合器,优选为管道混合器、液液搅拌混合器、漩涡混合器和静态混合器中的一种或多种。
46.更优选所述混合器包括密闭进料斗、混合机身、驱动轴组件、带轮机构、电机;所述的混合机身包括固定在混合机身内部的定磨盘以及用于与定磨盘配合的动磨盘;动磨盘与所述驱动轴组件、带轮机构、电机连接,提供动力源;设定定磨盘与动磨盘一一对应为一组,优选在驱动轴组件纵向上依次设置1~7组,优选设置2~4组。
47.优选地,所述的反应单元包括:悬浮床反应器、沸腾床反应器、固定床反应器和cstr反应器中的一种或多种,优选为悬浮床反应器。
48.优选地,所述分离单元包括旋流分离器、离心分离器、萃取分离器、过滤分离器和沉降分离器中的一种或多种,优选为旋流分离器。
49.优选地,该系统还包括:溶解单元,用于分离单元获得的固体混合物与能够溶解碱金属硫化物的极性溶剂混合,从而碱金属硫化物溶解于极性溶剂;电解单元,用于电解溶解单元获得的含碱金属硫化物的极性溶剂中的碱金属硫化物生成碱金属和硫磺;优选各个单元依据需要设置多个进料管线和出料管线;更优选地,所述系统包括:含硫原料油进料管线、碱金属进料管线、混合器出料管线、生成油出反应器管线、液体产品管线、固体混合物出料管线、极性溶剂进料管线、溶解罐、溶解后的混合物料出料管线、金属等其他固体组分出料管线、含碱金属硫化物的极性溶剂出料管线、硫磺出料管线、循环碱金属进料管线。
50.本发明提供本发明所述的系统在生产燃料油中的应用。
51.本发明在不使用催化剂的条件下,即可达到大于90%的硫和金属的去除率,实现超低硫船用燃料油的生产。整个工艺流程简单,二氧化碳排放比较低,硫氧化物零排放,经济与环境效益显著。
52.附图说明
53.图1为本发明的一种生产燃料油的方法的流程图。
54.图2为本发明的一种生产燃料油的方法中使用的密闭混合器的示意图。
55.附图标记说明图1中:1为含硫原料油进料管线、2为碱金属进料管线、3为混合器、4为混合器出料管线、5为供氢剂进料管线、6为加氢反应器、7为生成油出反应器管线、8为分离器、9为液体产品管线、10为分离后的固体混合物出料管线、11为极性溶剂进料管线、12为溶解罐、13为溶解后的混合物料出料管线、14为过滤器、15为金属等其他固体组分出料管线、16为含碱金属硫化物的极性溶剂出料管线、17为电解单元、18为硫磺出料管线、19为循环碱金属进料管线。
56.图2中:1为含硫原料油进料管线、2为碱金属进料管线、3为密闭进料斗、4为混合机身、5为第一动磨盘、6为第一定磨盘、7为第二动磨盘、8为第二定磨盘、9为第三动磨盘、10为第三定磨盘、11为混合物料出料管线、12为驱动轴组件、13为带轮机构、14为电机。
57.具体实施方式
58.在本文中所披露的范围的端点和任何值都不限于该精确的范围或值,这些范围或值应当理解为包含接近这些范围或值的值。对于数值范围来说,各个范围的端点值之间、各个范围的端点值和单独的点值之间,以及单独的点值之间可以彼此组合而得到一个或多个新的数值范围,这些数值范围应被视为在本文中具体公开。
200wppm。本发明中油的重金属含量以重金属元素计,采用icp-aes电感耦合等离子体原子发射光谱法测量。
70.根据本发明的一种优选实施方式,优选所述含硫原料油残炭含量为5-15%(m/m)。本发明中油的残炭的含量以油品分析结果为准,采用石油产品残炭测定法(微量法)(gbt17144)测量。
71.根据本发明的一种优选实施方式,优选所述含硫原料油粘度为800-20000cst。本发明中,油的粘度采用石油产品运动粘度测定法(gbt11137-50)测量。
72.根据本发明的一种优选实施方式,优选所述含硫原料油密度为950-1000 kg/m3,重金属含量为110-200 wppm,残炭含量为5-15wt%,粘度为800-20000cst,硫含量为1.0wt%以上,优选为1.8~8.0wt%。
73.根据本发明的一种优选实施方式,更优选,所述原料油为重质渣油、页岩油、油砂油中的一种或多种。
74.根据本发明的一种优选实施方式,进一步优选,所述重质渣油为原油加工过程中的,常压渣油、减压渣油、裂化渣油、渣油裂化柴油和催化柴油中的一种或多种。
75.本发明对步骤(1)使用的设备或装置或器皿无特殊要求,常用种类均可以用于本发明,根据本发明的一种优选实施方式,优选地,步骤(1)中,所述接触在混合器内进行。由此能够实现反应物料的高度均匀混合,有效提高反应效率。同时会有部分碱金属与原料中硫发生反应,生成无机化合物碱金属硫化物,促进无机化合物碱金属在有机化合物原料油中的分散。
76.根据本发明的一种优选实施方式,优选地,所述的混合器为管道混合器、液液搅拌混合器、漩涡混合器和静态混合器中的一种或多种。
77.根据本发明的一种优选实施方式,优选地,所述混合器包括密闭进料斗、混合机身、驱动轴组件、带轮机构、电机;所述的混合机身包括固定在混合机身内部的定磨盘以及用于与定磨盘配合的动磨盘;动磨盘与所述驱动轴组件、带轮机构、电机连接,提供动力源;设定定磨盘与动磨盘一一对应为一组,优选在驱动轴组件纵向上依次设置1~7组,优选设置2~4组。由此能够实现反应物料的高度均匀混合。
78.根据本发明的一种优选实施方式,更优选混合器内的混合过程包括:含硫原料油与熔融状态下的碱金属源从混合器顶部进入密闭进料斗,然后进入到混合机身,定磨盘被固定在混合机身上而处于相对静止状态;电机提供动力,通过带轮机构进行动力传动,使得驱动轴组件开始运行,此时动磨盘带动相对应的定磨盘发生旋转,反应物料由上至下的流动过程中被充分混合。由此能够实现碱金属和原料中硫的强化碰撞接触,有效提高反应效率。
79.本发明对供氢剂无特殊要求,常用种类均可以用于本发明,根据本发明的一种优选实施方式。
80.根据本发明的一种优选实施方式,优选地,步骤(2)所述供氢剂为至少含一个氢原子的物质,优选为氢气和/或包含至少一个碳原子和至少一个氢原子的物质。
81.根据本发明的一种优选实施方式,优选地,所述供氢剂为氢气和/或c1-5的低碳烃,更优选所述低碳烃为甲烷、乙烷、丙烷、丁烷、戊烷、乙烯、丙烯、丁烯、戊烯和二烯中的一种或多种。根据本发明,在本发明的实施例中以氢气、乙烷作为示例性说明本发明的优势,
但不因此限制本发明的保护范围。
82.根据本发明的一种优选实施方式,优选地,步骤(2)所述的供氢剂用量以氢气计,为1.0~3.0摩尔氢气/摩尔硫,优选为1.5~2.5摩尔氢气/摩尔硫。由此能够抑制稠环化合物等生焦。
83.根据本发明的一种优选实施方式,优选地,步骤(2)所述的加氢反应的条件包括:操作压力为4.0~10.0mpa,优选为6.0~8.0mpa。
84.根据本发明的一种优选实施方式,优选地,步骤(2)所述的加氢反应的条件包括:反应温度为200℃~430℃,优选为300℃~380℃,更优选为365℃~380℃。由此能够实现提高反应过程速率。
85.根据本发明的一种优选实施方式,优选地,步骤(2)在反应器中进行,更优选所述的反应器为悬浮床反应器、沸腾床反应器、固定床反应器和cstr反应器中的一种或多种。
86.根据本发明的一种优选实施方式,优选所述反应器为悬浮床反应器,优选操作条件包括:反应压力为4.0~10.0mpa,优选为6.0~8.0mpa;反应温度为200℃~430℃,优选为300℃~380℃,更优选为365℃~380℃。由此能够实现反应物料的高度均匀混合,加快反应速率,提高过程反应效率。
87.根据本发明的一种优选实施方式,优选地,步骤(2)在催化剂存在下发生,所述催化剂的活性金属元素包括钼、镍和钴中的一种或多种,优选所述催化剂为金属钼、金属镍、金属钴、钼合金、镍合金、钴合金、氧化钼、氧化镍和氧化钴中的一种或多种。
88.根据本发明,优选所述钼合金为含镍和/或钴的钼合金,优选所述镍合金为含钴和/或钼的镍合金。
89.根据本发明的一种优选实施方式,优选地,步骤(3)中所述的分离采用旋流分离、离心分离、萃取分离、过滤分离和沉降分离中的一种或多种;更优选采用旋流分离,更优选所述的旋流分离的操作温度为150℃~380℃,优选为200℃~330℃,更优选为280~290℃。由此能够实现生成油与硫化钠等其他固体杂质的清晰分离。
90.根据本发明的一种优选实施方式,优选地,进行步骤(3)所述分离前,该方法包括:将步骤(2)获得的物料于加氢反应条件下进行稳定处理,稳定时间为1h~6h,优选为2~3h。由此能够实现硫化钠等固体的聚合结晶,便于后续操作单元分离。
91.根据本发明的一种优选实施方式,优选地,该方法还包括:步骤(4),将步骤(3)获得的固体混合物与能够溶解碱金属硫化物的极性溶剂混合,固体混合物中的碱金属硫化物溶解于极性溶剂,从而实现包括金属硫化物和胶质沥青质的固体的分离,提高碱金属硫化物纯度,为后续碱金属回收单元提供高纯原料。
92.本发明中,所述极性溶剂只要满足前述要求即可实现本发明的目的,根据本发明的一种优选实施方式,优选地,步骤(4)中所述的极性溶剂选自n, n-二甲基苯胺、喹啉、2-甲基四氢呋喃、苯、四氢呋喃、环己烷、氟苯、三氟苯、甲苯、二甲苯、四乙二醇二甲醚、二甘醇二甲醚、异丙醇、乙基丙醛、碳酸二甲酯、二甲氧基醚、二甲基亚丙基脲、乙醇、乙酸乙酯、碳酸亚丙酯、碳酸亚乙酯和碳酸二乙酯中的一种或多种。
93.根据本发明的一种优选实施方式,优选地,该方法还包括:步骤(5),将所述步骤(4)中获得的含碱金属硫化物的极性溶剂引入电解单元,将碱金属硫化物电解生成碱金属和硫磺,碱金属循环返回作为原料使用。
94.根据本发明的一种优选实施方式,优选地,该方法包括:(1)含硫原料油与碱金属在混合器内进行预反应得到预反物料,所述预反应在非临氢条件下进行,预反应温度为200℃~400℃,优选为300℃~380℃;(2)将所述预反物料与供氢剂接触进行加氢反应;(3)将步骤(2)获得的物料经过分离后获得液相产品燃料油和固体混合物;(4)将步骤(3)获得的固体混合物与能够溶解碱金属硫化物的极性溶剂混合,碱金属硫化物溶解于极性溶剂,从而实现包括金属硫化物和胶质沥青质的固体的分离;(5)将步骤(4)中获得的含碱金属硫化物的极性溶剂引入电解单元,将碱金属硫化物电解生成碱金属和硫磺,碱金属循环作为原料使用。
95.本发明提供本发明所述的方法得到的燃料油。本发明的燃料油具有低硫、低粘度、低金属杂质含量的性质,本发明的方法具有工艺流程简单、生产成本低、二氧化碳排放比较低、硫氧化物零排放的优势。
96.本发明提供本发明所述的方法在生产低硫船用燃料油中的应用。本发明的方法具有工艺流程简单、生产成本低、二氧化碳排放比较低、硫氧化物零排放的优势,使得特别适合于作为生产低硫船用燃料油。
97.本发明提供本发明所述的燃料油作为船用燃料油的应用。本发明的燃料油具有产品硫含量低,金属杂质含量低、粘度低的性质,使得特别适合于作为生产低硫船用燃料油。
98.本发明只要按照上述方法进行操作即可实现本发明的目的,对其使用的设备、装置无特殊要求,针对本发明,根据本发明的优选实施方式,本发明还设计了连续反应系统,解决常规的由于间歇式搅拌釜反应器不能连续操作,效率低;连续搅拌釜反应器存在物料停留时间无法精准控制的问题,例如有些没有反应的原料油和碱金属会流出反应器或者某些物料始终停留在反应器中的技术问题。
99.本发明提供一种生产燃料油的系统,该系统包括:(1)预反应单元,所述预反应单元用于含硫原料油与碱金属接触进行预反应得到预反物料;(2)加氢反应单元,用于预反物料与供氢剂接触进行加氢反应;(3)分离单元,用于分离加氢反应物料。
100.根据本发明,优选所述预反应单元不包括供氢管线或供氢进料口。
101.根据本发明,优选地,所述的预反应单元包括混合器,优选为管道混合器、液液搅拌混合器、漩涡混合器和静态混合器中的一种或多种。采用混合器,反应物料混合均匀,为高效反应提供基础。
102.根据本发明,更优选所述混合器包括密闭进料斗、混合机身、驱动轴组件、带轮机构、电机;所述的混合机身包括固定在混合机身内部的定磨盘以及用于与定磨盘配合的动磨盘;动磨盘与所述驱动轴组件、带轮机构、电机连接,提供动力源;设定定磨盘与动磨盘一一对应为一组,优选在驱动轴组件纵向上依次设置1~7组,优选设置2~4组。采用前述混合器,反应物料可以实现高度均匀混合,强化碱金属和原料中硫的碰撞接触,有效提高反应效率。
103.根据本发明,反应单元的反应器无特殊要求,优选地,所述的反应单元包括:悬浮床反应器、沸腾床反应器、固定床反应器和cstr反应器中的一种或多种,优选为悬浮床反应
器。
104.根据本发明,分离单元的分离器无特殊要求,根据本发明,优选地,所述分离单元包括旋流分离器、离心分离器、萃取分离器、过滤分离器和沉降分离器中的一种或多种,优选为旋流分离器。
105.根据本发明,优选地,该系统还包括:溶解单元,用于分离单元获得的固体混合物与能够溶解碱金属硫化物的极性溶剂混合,从而碱金属硫化物溶解于极性溶剂;电解单元,用于电解溶解单元获得的含碱金属硫化物的极性溶剂中的碱金属硫化物生成碱金属和硫磺。
106.优选各个单元依据需要设置多个进料管线和出料管线;更优选地,所述系统包括:含硫原料油进料管线、碱金属进料管线、混合器出料管线、生成油出反应器管线、液体产品管线、固体混合物出料管线、极性溶剂进料管线、溶解罐、溶解后的混合物料出料管线、金属等其他固体组分出料管线、含碱金属硫化物的极性溶剂出料管线、硫磺出料管线、循环碱金属进料管线。
107.如图1所示:根据本发明的一种优选的实施方式,预反应单元包括:混合器3,含硫原料油进料管线1、碱金属进料管线2、混合器出料管线4。
108.根据本发明的一种优选的实施方式,反应单元包括:加氢反应器6、供氢剂进料管线5、生成油出反应器管线7。
109.根据本发明的一种优选的实施方式,分离单元包括:分离器8、液体产品管线9、分离后的固体混合物出料管线10。
110.根据本发明的一种优选的实施方式,溶解单元包括:溶解罐12、极性溶剂进料管线11、溶解后的混合物料出料管线13。
111.根据本发明的一种优选的实施方式,系统包括:过滤器14、金属等其他固体组分出料管线15、含碱金属硫化物的极性溶剂出料管线16。
112.根据本发明的一种优选的实施方式,电解单元17包括:为硫磺出料管线18、循环碱金属进料管线19。
113.本发明的生产低硫船用燃料油的方法,包括如下内容:(1)原料油与碱金属在混合器内进行预反应,所述反应在非临氢条件下进行,预反应温度为200℃~400℃,优选为300℃~380℃,进一步优选为335℃~365℃;(2)步骤(1)反应后的物料进入反应器,在供氢剂的作用下进行深度脱硫反应;(3)步骤(2)获得的物料经过分离后获得液相产品低硫船用燃料油和固体混合物。
114.本发明方法中,步骤(1)原料油与熔融状态下的碱金属在混合器内进行预反应。
115.本发明方法中,步骤(1)所述原料油包含至少一个碳原子和杂原子和/或一种或多种重金属。
116.本发明方法中,步骤(1)所述原料油为重质渣油、页岩油、油砂油等中的一种或几种,其硫含量一般为1.0wt%以上,优选为1.8~8.0wt%。所述重质渣油原料为原油加工过程中的常压渣油、减压渣油、裂化渣油、渣油裂化柴油或催化柴油中的一种或几种。
117.本发明方法中,步骤(1)中所述非临氢条件是指预反应过程不加入供氢剂,例如不通入氢气。
118.本发明方法中,步骤(1)所述碱金属为锂(li)、钠(na)、钾(k)、铷(rb)、铯(cs)、钫
(fr)中的一种或几种。
119.本发明方法中,步骤(1)原料油与碱金属的比例根据原料油中硫含量确定,碱金属添加量同原料油中硫含量的质量比为0.8~3.0:1,优选为1.2~2.5:1。
120.本发明方法中,步骤(1)预反应操作压力可以为常压,也可以是后续操作单元的操作压力,优选为常压。
121.本发明方法中,步骤(1)所述的混合器为管道混合器、液液搅拌混合器、漩涡混合器、静态混合器等中的一种或几种。
122.本发明方法中,在一些实施方式中,依据需要在混合器中加入碱金属盐,所述碱金属盐为硫化锂、硫化钠、硫化钾、硫化铷、硫化铯、硫化钫中的一种或几种,碱金属盐的加入量一般为原料的1wt%~20 wt%,优选为原料的5wt%~8wt%。碱金属盐的加入能够提高碱金属在原料油中的分散性能,并保持稳定的分散状态。
123.本发明实施例中采用的混合器具有如下结构:所述混合器主要包括密闭进料斗、混合机身、驱动轴组件、带轮机构、电机等组成;所述的混合机身包括固定在混合机身内部的定磨盘以及用于与定磨盘配合的动磨盘;动磨盘与驱动轴组件、带轮机构、电机连接,提供动力源;定磨盘与动磨盘一一对应为一组,根据需要可以在驱动轴组件纵向上依次设置,一般为1~7组,优先为2~4组。
124.本发明实施例中采用的混合器的混合过程如下:重质渣油与熔融状态下的碱金属从密闭混合器顶部进入密闭进料斗,然后进入到混合机身,定磨盘被固定在混合机身上而处于相对静止状态;电机提供动力,通过带轮机构进行动力传动,使得驱动轴组件开始运行,此时动磨盘带动相对应的定磨盘发生旋转,反应物料由上至下的流动过程中被充分混合。本发明的密闭混合器通过定磨盘和动磨盘的高速咬合、研磨实现了反应物料的高度均匀混合,强化了碱金属和原料中硫的碰撞接触,有效提高了反应效率。
125.本发明方法中,步骤(2)所述供氢剂为至少含一个氢原子的物质,优选为氢气或者为包含至少一个碳原子和至少一个氢原子的物质。
126.本发明方法中,步骤(2)所述供氢剂为氢气或者低碳烃,所述低碳烃为甲烷、乙烷、丙烷、丁烷、戊烷、乙烯、丙烯、丁烯、戊烯、二烯、前述物质的异构体和/或它们的混合物。
127.本发明方法中,步骤(2)所述的供氢剂用量根据重质渣油中硫含量确定,以氢气计,一般为1.0~3.0摩尔氢气/摩尔硫,优选为1.5~2.5摩尔氢气/摩尔硫。
128.本发明方法中,步骤(2)中所述的反应器的操作压力一般为4.0~10.0mpa,优选为6.0~8.0mpa;反应温度一般为200℃~430℃,优选为300℃~380℃。
129.本发明方法中,步骤(2)中所述的反应器为悬浮床反应器、沸腾床反应器、固定床反应器、cstr反应器等中的一种或几种。
130.本发明方法中,在一些实施方式中,步骤(2)反应过程可以在催化剂存在下发生,以帮助促进化学反应。作为非限制性例子,所述催化剂可包括钼、镍、钴,或者钼合金、镍合金、钴合金、含镍和/或钴的钼合金、含钴和/或钼的镍合金,氧化钼、氧化镍或氧化钴,以及它们的组合。
131.本发明一个或多个实施例中采用的反应器为悬浮床反应器,操作条件如下:反应压力一般为4.0~10.0mpa,优选为6.0~8.0mpa;反应温度一般为200℃~430℃,优选为300℃~380℃。采用悬浮床反应器,充分利用其高度反混的特性,保持反应过程中氢气与反应
混合原料的混合均匀,强化传质,提高反应效率,同时降低重质渣油原料结焦几率。采用密闭混合器结合悬浮床反应器的组合方式实现了重质渣油原料与熔融状态下的碱金属的高度混合,提高了碱金属的利用率,在相同处理量的条件下,降低了碱金属的用量,进而降低了后续产品处理未充分反应的金属的难度;由于悬浮床反应器中无催化剂床层,反应器中内环流可以强化氢气与高度混合的重质渣油原料和碱金属混合原料均匀接触,达到强化气液传质的目的,提高脱硫、脱金属的效率,并抑制生焦,可以实现产品产率和质量的双提升。
132.本发明方法中,步骤(3)中所述的分离可以采用旋流分离、离心分离、萃取分离、过滤分离、沉降分离中的一种或几种。
133.本发明方法中,步骤(2)获得的反应物料优选经过稳定处理后进行分离,所述稳定操作条件与步骤(2)所述的悬浮床操作条件一致,稳定时间一般为1h~6h,优选为2~3h。
134.本发明一个或多个实施例中采用旋流分离,所述的旋流分离器为熟知的具有旋流及分离功能的旋流分离器,所述的旋流分离器的操作温度一般为150℃~380℃,优选为200℃~330℃。
135.本发明方法中,可进一步含有步骤(4),所述步骤(4)中将步骤(3)获得的固体混合物与碱金属硫化物可溶解的极性溶剂混合,碱金属硫化物可以溶解于极性溶剂,从而实现与金属等其他固体的分离。
136.本发明方法中,步骤(4)中所述的极性溶剂可以有效溶解反应生成的碱金属硫化物。所述的极性溶剂包含:n, n-二甲基苯胺、喹啉、2-甲基四氢呋喃、苯、四氢呋喃、环己烷、氟苯、三氟苯、甲苯、二甲苯、四乙二醇二甲醚、二甘醇二甲醚、异丙醇、乙基丙醛、碳酸二甲酯、二甲氧基醚、二甲基亚丙基脲、乙醇、乙酸乙酯、碳酸亚丙酯、碳酸亚乙酯、碳酸二乙酯等。所述的极性溶剂可以为一种溶剂,也可以为上述溶剂中的多种溶剂混合液。
137.本发明方法中,步骤(4)中所述的分离操作为本领域人员熟知的过滤操作,简单将溶解碱金属硫化物的溶液和金属等固体物质分开。
138.本发明方法中,可更进一步含有步骤(5),所述步骤(4)中将获得的含碱金属硫化物的溶剂引入电解单元,将碱金属硫化物电解生成碱金属和硫磺,碱金属循环使用。
139.本发明方法中,步骤(5)中所述的电解单元具有配置成选择性运输碱离子的碱离子导电膜,该膜将配置有阳极的阳极液室与配置有阴极的阴极液室分开。步骤(4)包含碱金属硫化物和/或多硫化物以及部分地溶解元素硫和碱金属硫化物和多硫化物的极性溶剂作为阳极溶液,将阳极液溶液引入阳极液室中。将阴极液溶液引入阴极液室中。该阴极液溶液包含碱金属离子和阴极液溶剂。阴极液溶剂可包括多种非水性溶剂中的一种,例如四乙二醇二甲醚、二甘醇二甲醚、碳酸二甲酯、二甲氧基醚、碳酸亚丙酯、碳酸亚乙酯、碳酸二乙酯。将电流施用到电解单元的氧化阳极液室中的硫化物和/或多硫化物以形成更高价态的多硫化物并使高价态多硫化物氧化成元素硫。电流进一步使碱金属离子通过碱金属导电膜从阳极液室到阴极液室,并使阴极液室中的碱金属离子还原以形成元素碱金属。元素碱金属循环使用。
140.本发明方法中,步骤(5)中所述的电解单元操作温度根据选用电解池种类一般为100℃~600℃,优选操作温度低的电解池,优选后的电解池操作温度为为100℃~200℃。
141.一种生产低硫船用燃料油的方法,包括如下内容:((1)原料油与碱金属在混合器内进行预反应,所述反应在非临氢条件下进行,预
反应温度为200℃~400℃,优选为300℃~380℃,进一步优选为335℃~365℃;(2)步骤(1)反应后的物料进入反应器,在供氢剂的作用下进行深度脱硫反应;(3)步骤(1)获得的物料经过分离后获得液相产品低硫船用燃料油和固体混合物;(4)将步骤(3)获得的固体混合物与碱金属硫化物可溶解的极性溶剂混合,碱金属硫化物可以溶解于极性溶剂,从而实现与金属等其他固体的分离;(5)将步骤(4)中获得的含碱金属硫化物的溶剂引入电解单元,将碱金属硫化物电解生成碱金属和硫磺,碱金属循环使用。
142.下面结合附图对本发明的方法进行详细说明。
143.根据本发明的一种优选实施方式,以下结合附图详细说明本发明:原料油为重质渣油、碱金属为熔融状态下的碱金属、反应器为悬浮床反应器,分离器为旋流分离器/离心分离器,溶解单元包括溶解罐。
144.如图1所示,该方法包括:重质渣油与熔融状态下的碱金属首先经过密闭混合器3充分混合进行预反应,预返物料经加压与供氢剂如氢气一起进入悬浮床反应器6,在悬浮床反应器6中进行充分的加氢脱硫、加氢脱金属反应;获得的反应后的物料包括液相的生成油和固相的碱金属硫化物固体和金属等,经过稳定后,引入旋流分离器8进行分离,获得液相产品低硫船用燃料油和固体混合物;获得的固体混合物与碱金属硫化物可溶解的极性溶剂在溶解罐12中混合溶解,溶解后的混合物料引至过滤单元14,分离得到含碱金属硫化物的极性溶剂和金属等其他固体组分;含碱金属硫化物的溶剂引入电解单元17,将碱金属硫化物电解生成碱金属和硫磺,电解生成碱金属循环使用。
145.如图2所示,混合器中发生的预反应步骤包括:重质渣油原料从原料油管线1进入、熔融状态下的碱金属从碱金属进料管线2从密闭混合器顶部进入密闭进料斗3,然后进入到混合机身4,第一定磨盘6、第二定磨盘8、第三定磨盘10被固定在混合机身4上而处于相对静止状态;电机14提供动力,通过带轮机构13进行动力传动,使得驱动轴组件12开始运行,此时第一动磨盘5、第二动磨盘7和第二动磨盘9带动相对应的第一定磨盘、第二定磨盘和第三定磨盘发生旋转,反应物料由上至下的流动过程中被充分混合,从混合物料出料管线11出料。
146.接下来通过具体实施例对本发明的一种生产低硫船用燃料油的方法作进一步的说明。实施例只是对本发明方法的具体实施方式的举例说明,并不构成本发明保护范围的限制。
147.实施例1按照图1所示流程进行(以下实施例相同),1000g/h重质渣油1(性质见表1,以下同)与22.60g/h熔融状态下的金属钠首先经过密闭混合器(图2所示,以下实施例相同)充分混合进行预反后,预反物料经加压与1.28mol/h氢气一起进入悬浮床反应器,进行充分的加氢脱硫、加氢脱金属反应;获得的反应物料经过稳定后,引入旋流分离器进行分离,获得液相产品低硫船用燃料油和固体混合物。
148.实施例21000g/h重质渣油1与22.60g/h熔融状态下的金属钠首先经过密闭混合器充分混合进行预反后,预反物料经加压与1.28mol/h氢气一起进入悬浮床反应器,进行充分的加氢脱硫、加氢脱金属反应;获得的反应物料经过稳定后,引入离心分离器进行分离,获得液相
产品低硫船用燃料油和固体混合物。
149.实施例31000g/h重质渣油1与24.60g/h熔融状态下的金属钠首先经过密闭混合器充分混合进行预反后,预反物料经加压与1.28mol/h氢气一起进入沸腾床反应器,进行充分的加氢脱硫、加氢脱金属反应;获得的反应物料经过稳定后,引入旋流分离器进行分离,获得液相产品低硫船用燃料油和固体混合物。
150.实施例41000g/h重质渣油1与24.60g/h熔融状态下的金属钠首先经过密闭混合器充分混合进行预反后,预反物料经加压与1.28mol/h氢气一起进入搅拌釜反应器,进行充分的加氢脱硫、加氢脱金属反应;获得的反应物料经过稳定后,引入旋流分离器进行分离,获得液相产品低硫船用燃料油和固体混合物。
151.实施例51000g/h重质渣油1,22.60g/h熔融状态下的金属钠与10g/h硫化钠首先经过密闭混合器充分混合进行预反后,预反物料经加压与1.28mol/h氢气一起进入悬浮床反应器,进行充分的加氢脱硫、加氢脱金属反应;获得的反应物料经过稳定后,引入旋流分离器进行分离,获得液相产品低硫船用燃料油和固体混合物。
152.实施例61000g/h重质渣油1与24.60g/h熔融状态下的金属钠首先经过密闭混合器充分混合进行预反后,预反物料经加压与1.28mol/h乙烷一起进入悬浮床反应器,进行充分的加氢脱硫、加氢脱金属反应;获得的反应物料经过稳定后,引入旋流分离器进行分离,获得液相产品低硫船用燃料油和固体混合物。
153.实施例71000g/h重质渣油2与41.60g/h熔融状态下的金属钠首先经过密闭混合器充分混合进行预反后,预反物料经加压与1.625mol/h氢气一起进入悬浮床反应器,进行充分的加氢脱硫、加氢脱金属反应;获得的反应物料经过稳定后,引入旋流分离器进行分离,获得液相产品低硫船用燃料油和固体混合物;经极性溶剂二甲苯溶解后的混合物料引至过滤单元,分离得到含碱金属硫化物的极性溶剂和金属等其他固体组分;含碱金属硫化物的溶剂引入电解单元,将碱金属硫化物电解生成碱金属和硫磺,电解生成碱金属循环使用。
154.实施例8按照实施例1的方法,不同的是,密闭混合器采用常规的混合器代替,常规混合器为带有搅拌桨的混合器,搅拌速率为70rpm。
155.实施例9按照实施例1的方法,不同的是,在密闭混合器中,预反的温度为200℃。
156.实施例10按照实施例1的方法,不同的是,在密闭混合器中,预反的温度为400℃。
157.实施例11按照实施例1的方法,不同的是,在密闭混合器中,预反的温度为350℃,供氢剂为乙烯。
158.实施例12
按照实施例1的方法,不同的是,在密闭混合器中,预反的温度为370℃,供氢剂为丁烯。
159.实施例13按照实施例1的方法,不同的是,加氢反应后在加氢温度370℃下稳定3h再进行所述旋转分离,其余条件均相同。
160.实施例14按照实施例1的方法,不同的是,碱金属钠与所述含硫原料油中硫的质量比为2.5:1。
161.实施例15按照实施例1的方法,不同的是,碱金属钠与所述含硫原料油中硫的质量比为0.8:1。
162.实施例16按照实施例1的方法,不同的是,步骤(2)在金属钼存在下进行,催化剂的用量为45ml。
163.对比实施例16和实施例1发现,本发明的方法在催化剂或不在催化剂下进行步骤(2)的加氢反应,均能获得性能优异的船用燃料油。
164.对比例11000g/h重质渣油1与26.70g/h熔融状态下的金属钠混合物料和1.28mol/h氢气一起进入搅拌釜反应器,进行加氢脱硫、加氢脱金属反应;获得的反应物料经过稳定后,引入离心分离器进行分离,获得液相产品低硫船用燃料油和固体混合物。
165.对比例21000g/h重质渣油2与41.60g/h熔融状态下的金属钠混合物料和1.28mol/h氢气一起进入搅拌釜反应器,进行加氢脱硫、加氢脱金属反应;获得的反应物料经过稳定后,引入离心分离器进行分离,获得液相产品低硫船用燃料油和固体混合物;经极性溶剂溶解后的混合物料引至过滤单元,分离得到含碱金属硫化物的极性溶剂和金属等其他固体组分;含碱金属硫化物的溶剂引入电解单元,将碱金属硫化物电解生成碱金属和硫磺,电解生成碱金属循环使用。
166.实施例1~7和对比例1~2采用的原料油性质见表1,实施例1~6和对比例1操作条件见表2,实施例1~6和对比例1产品性质见表3,实施例7和对比例2操作条件见表4,实施例7和对比例2产品性质见表5。实施例8-16的结果见表6。
167.表1 原料油性质
ꢀ
表2 实施例1~6和对比例1的操作条件表3 实施例1~6和对比例1的结果
由表3结果看出本发明方法获得产品的api度提高幅度明显,可以有效降低生成油的硫含量,金属含量,粘度和残碳值,可以直接生产满足iso 8217 2010 rmg 380标准的低硫船用燃料油。
168.表4实施例7与对比例2的操作条件表5实施例7与对比例2的结果
由表5结果看出本发明方法在碱金属回收后,依然可以保持高的提质效果,生成油的硫含量,金属含量,粘度和残碳值低。
169.表6以上详细描述了本发明的优选实施方式,但是,本发明并不限于此。在本发明的技术构思范围内,可以对本发明的技术方案进行多种简单变型,包括各个技术特征以任何其它的合适方式进行组合,这些简单变型和组合同样应当视为本发明所公开的内容,均属于本发明的保护范围。